80吨年催化裂化设计书.docx
《80吨年催化裂化设计书.docx》由会员分享,可在线阅读,更多相关《80吨年催化裂化设计书.docx(54页珍藏版)》请在冰豆网上搜索。
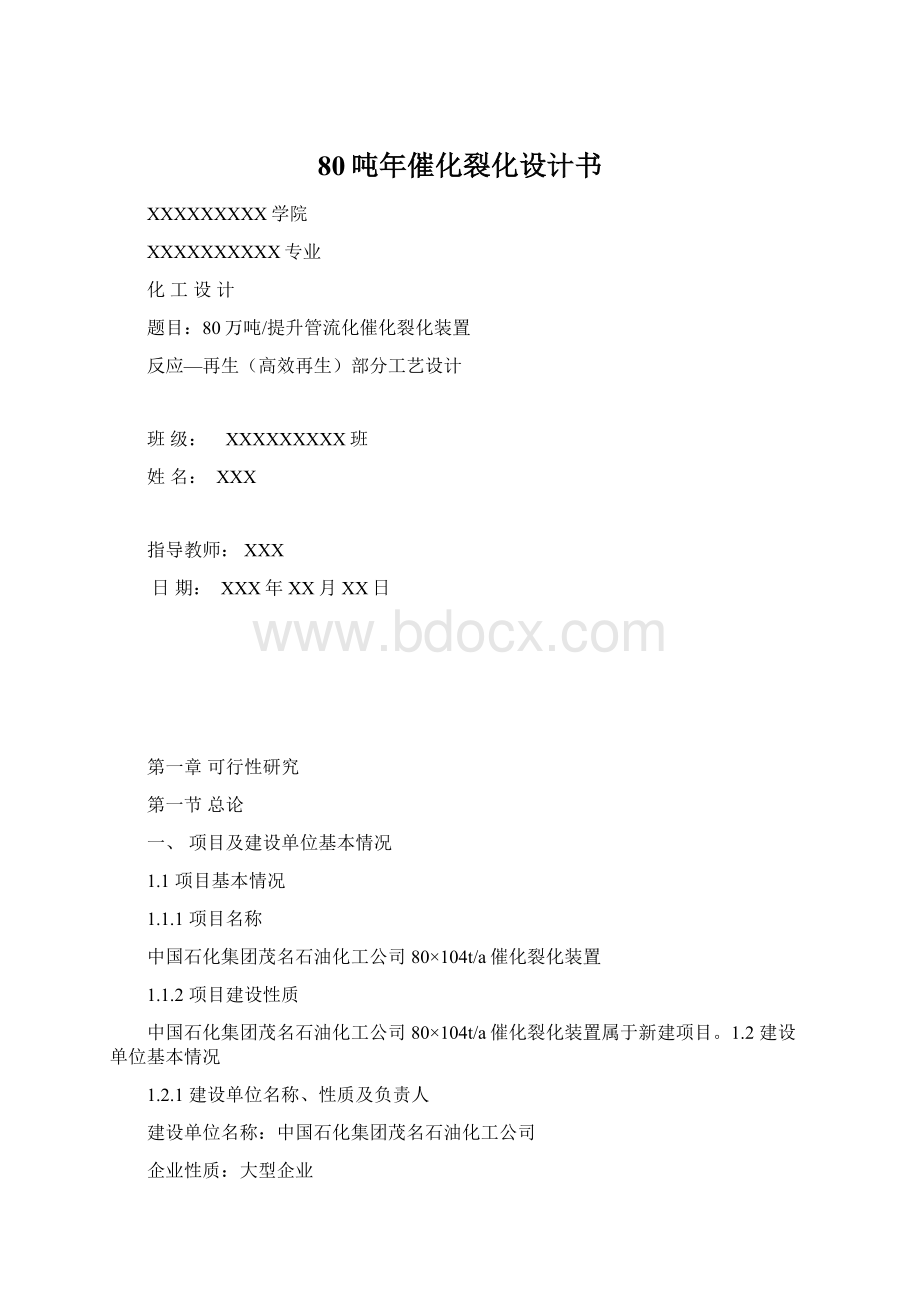
80吨年催化裂化设计书
XXXXXXXXX学院
XXXXXXXXXX专业
化工设计
题目:
80万吨/提升管流化催化裂化装置
反应—再生(高效再生)部分工艺设计
班级:
XXXXXXXXX班
姓名:
XXX
指导教师:
XXX
日期:
XXX年XX月XX日
第一章可行性研究
第一节总论
一、项目及建设单位基本情况
1.1项目基本情况
1.1.1项目名称
中国石化集团茂名石油化工公司80×104t/a催化裂化装置
1.1.2项目建设性质
中国石化集团茂名石油化工公司80×104t/a催化裂化装置属于新建项目。
1.2建设单位基本情况
1.2.1建设单位名称、性质及负责人
建设单位名称:
中国石化集团茂名石油化工公司
企业性质:
大型企业
负责人:
XXX
二、编制依据
2.1编制依据
1、中国石化集团茂名石油化工公司新建80×104t/a催化裂化装置可行性研究委托书;
2、《80×104t/a催化裂化装置可研报告的数据》(中国石化集团茂名石油化工公司公司)。
三、主要研究结果
3.1项目概况
本项目为中国石化集团茂名石油化工公司80×104t/a催化裂化装置属新建项目。
3.2装置组成
80×104t/a催化裂化装置包括:
反应一再生、分馏、吸收稳定(含气压机)、主风机—烟机系统、余热锅炉、产汽系统。
3.3装置加工能力
装置设计规模80×104t/a
年开工时数8000小时
3.4原料来源
大庆原料油。
3.5产品
主要产品:
汽油、液化石油气、轻柴油
副产品:
干气、油浆
3.6主要研究结论
中国石化集团茂名石油化工公司80×104t/a催化裂化装置工程经过技术方案论证,所选的技术方案先进可行,经济效益好,为改善全厂产品结构和质量、提高经济效益创造了良好的条件。
各项指标均好于行业基准值,因此建设本项目在经济上是可行的。
综上所述,充分利用我国石化行业成熟、可靠且先进的工艺技术,新建中国石化集团茂名石油化工公司80×104t/a催化裂化装置,对促进中国石化集团茂名石油化工公司的发展具有重要作用。
四、存在问题及建议
4.1装置加工方案
厂方可根据市场情况或实际生产情况适当调整装置的加工方案,达到装置适时、适应总流程要求的需要。
4.2装置能耗
本次设计应厂方委托,采用的设计数据为多产汽煤柴方案,由反应部分带至后部系统的低温位热量增多,装置的低温余热增加,虽然优化换热流程,仍提高了装置能耗1~2kg标油/t原料。
由于石科院MIP工艺技术要求反应部分较低的油气分压,反应部分采用的蒸汽量较多,使装置能耗有所提高。
4.3装置低温余热回收系统
装置低温余热回收系统采用的热能回收介质为系统提供的热媒水,所回收的低温热能也由全厂统一考虑利用。
第二节市场
一、产品市场分析与预测
根据市场分析,利用液化石油气中富含的低碳烯烃,其中碳四组分被利用做汽油的高辛烷值调合组分,丙烯、正丁烯等组分可用以生产市场需求旺盛的高附加值聚丙烯和顺酐产品,降低液化石油气的产品比例。
1.1聚丙烯
新建80×104t/a重油催化裂化装置投产后,可生产11×104t/a的聚丙烯原料,为中国石化集团茂名石油化工公司向高附加值的化工领域延伸夯实基础。
1.2成品油
新建80×104t/a重油催化裂化装置投产后,生产催化汽油的辛烷值~90.5,烯烃含量~25%v,可作为高标号清洁汽油的优质调合组分。
这将提高全厂高标号成品汽油的比例、优化全厂成品油的结构,使”建设单位”化工公司成品油的市场竞争力提高。
第三节建设规模、产品方案
一、建设规模
中国石化集团茂名石油化工公司,新建催化裂化装置规模:
80×104t/a。
二、产品方案
2.1确定产品方案的依据
新建80×104t/a催化裂化装置的产品方案:
以产低烯烃含量的清洁汽油调合组分和低碳烯烃为主,增产碳三、碳四组分。
第四节工艺技术方案
一、石科院MIP工艺技术方案
石油化工科学研究院(以下简称石科院)开发了多产异构烷烃的催化裂化工艺(MIP工艺),该工艺技术采用新型提升管反应器和适宜的工艺条件,在不同的反应区实现裂化、氢转移和异构化反应以达到降低汽油烯烃含量、提高异构烷烃含量的目的。
在降低催化汽油烯烃含量的同时,其研究法辛烷值(RON)基本不变(或略有降低),马达法辛烷值(MON)有所提高,抗爆指数基本不变,汽油的安定性得到改善,产品分布也有所改善。
该技术是具有生产满足欧III排放标准汽油组分同时多产丙烯的催化裂化工艺技术。
2002年~2004年,上海高桥石化公司140×104t/a催化裂化(3#催化)、安庆120×104t/a重油催化裂化、镇海180×104t/a催化裂化、九江100×104t/a重油催化裂化等8套装置应用MIP工艺技术均获得成功,取得了令人满意的工业试验和应用结果。
采用MIP工艺技术的催化裂化装置与常规催化裂化装置相比,操作难度基本相当,能耗相当或略有增加。
第五节原料、辅助材料及燃料供应
本次新建80×104t/a催化裂化装置设计,为全厂扩能改造的一部分,原料、辅助材料及燃料供应由厂方统一考虑。
第六节公用工程及辅助生产设施
一、新水
水源取自中国石化集团茂名石油化工公司内DN300供水干线,新鲜水水质达到《生活饮用水卫生标准》GB5749-85要求,可以直接作为生产和生活用水。
新建80×104t/a催化装置消耗新鲜水13t/h,可以满足要求。
二、循环水系统
2.1循环水系统现状
中国石化集团茂名石油化工公司原一循环水场,2004年改建后供水能力为4000m3/h。
循环水3#冷却塔为逆流冷却塔,供水能力为4000m3/h。
4#冷却塔为横流塔,处理能力为4000m3/h,3#、4#冷却塔及相关设施合并简称为二循,供水能力为8000m3/h。
5#冷却塔为逆流冷却塔,总处理量8000m3/h,简称三循。
一循、二循、三循合计供水能力为20000m3/h。
目前已建生产装置循环水实际用量为17100m3/h。
2.2新建80万吨/年催化装置消耗循环水:
1200m3/h(未计余热回收站的用水量),实际很多低温余热不能利用,实际循环水用量增加约1800~2000m3/h。
考虑全厂其它系统的配套改造,实际循环水总增量为4000~6000m3/h,需要新建循环水厂。
三、净化风、非净化风系统
3.1目前净化风、非净化风负荷情况
公司平均连续用量为:
250m3n/min;最低用风量为:
220m3n/min;最高用风量为:
270m3n/min,其中总供风量的40%为净化风,其余为非净化风。
净化风、非净化风系统可以满足新建80×104t/a催化裂化装置的要求。
四、氮气系统
4.1现有供氮设备:
新空分制氮产量为:
1000m3n/h(氮气);合计用电量为600kW左右
空分制氮产量为:
600m3n/h(氮气);合计用电量为300kW左右
分子筛制氮产量为:
200m3n/h(氮气);用电量为100kW左右
氮气总产量为:
1800m3n/h
氮气储存能力:
球罐2个400m3(可补压至2.4MPa,满罐储量为9600m3n/罐)
卧罐4个50m3(可补压至2.4MPa,满罐储量为1200m3n/罐)
钢瓶6个20m3(可补压至14.0MPa,满罐储量为2800m3n/罐)
氮气总储备能力:
38400m3n
4.2氮气外供分布情况:
公司正常生产总用氮量为:
900m3n/h,总氮气生产能力是1800m3n/h,富裕生产量900m3n/h
供氮系统可以满足新建80×104t/a催化裂化装置的要求。
五、排水系统
中国石化集团茂名石油化工公司工业污水处理场建成于1998年10月,由中国市政东北设计研究院设计,总投资7200万元(包括外排管线及污水库部分),处理能力为600m3/h,目前实际最大处理量约390m3/h,处理工艺采用国内外比较成熟的“老三套”处理法。
可以满足新建80×104t/a催化裂化装置的要求。
六、蒸汽系统
目前全厂共有3台100t/h的中压蒸汽炉,正常均投用。
特别是天气到零下20℃后,总负荷达到约300t/h,几乎没有富余。
且1.0MPa的蒸汽供应能力已经超过设计负荷。
新建80×104t/a催化裂化装置考虑在开工过程中蒸汽的消耗,全厂蒸汽锅炉需要扩建。
第七节环境保护
一、环保标准
1、《环境空气质量标准》GB3095-1996(二级);
2、《城市区域环境噪声标准》GB3096-93(二类);
3、《地下水质量标准》GB/T14848-93(Ⅴ类标准);
4、《污水综合排放标准》GB8978-1996(新扩改二级);
5、《大气污染物综合排放标准》GB16297-1996(二级);
6、《工业企业厂界噪声标准》GB12348-90(Ⅲ类);
7、《一般工业固体废物贮存、处置场污染控制标准》GB18599-2001。
二、环境保护治理措施
2.1废水治理措施
装置内废水遵循“清污分流,分类处理”的原则进行处理。
含油污水、生产废水和生活污水分别经各自的管网送到现有的污水处理场进行处理。
2.2废气治理措施
本装置排放的再生烟气经三级旋风除尘器除尘,蒸汽过热炉的燃料为脱硫的燃料气等措施,烟气经各自的烟囱排放,废气污染源达标情况见下表2.2-1。
表2.2-1废气污染源达标情况
序
号
排放点
废气
类型
排放
规律
排放量
m3n/h
污染物kg/h(mg/m3)
烟囱
高度
m
排放去向
SO2
NOx
TSP
1
再生器
烟气
连续
1.48×105
25.5(172)
29.6(200)
14.8(100)
100
大气
GB16297-1996二级标准
200(550)
61(240)
277.8(120)
100
达标
2
蒸汽过热炉
烟气
连续
0.25×105
0.65
(26)
5.38
(215)
0.50
(20)
43
GB16297-1996二级标准
29.2(550)
8.85(240)
45.3(120)
43
-达标
由表9.3-6可知,本装置排放再生烟气再生烟气和蒸汽过热炉烟气分别经100m和43m高的烟囱排放,其废气污染物均能够满足《大气污染物综合排放标准》GB16297-1996(二级新扩改)的要求。
可以做到达标排放。
2.3固体废物治理措施
本装置产生废催化剂600t/a,送克拉玛依石化公司工业固体废渣池堆存。
待“新疆维吾尔自治区乌鲁木齐市危险废物处理中心”投入运行后,送“该危险废物处理中心”处理。
三、主要环境保护项目
工艺上对再生烟气采取旋风分离除尘措施。
既回收了催化剂,又减少的再生烟气中污染物的排放量。
本项目采取三级旋风除尘器除尘后,烟气中粉尘的浓度有350mg/m3降低到100mg/m3。
第八节项目实施计划
1、可行性研究报告编制:
2009年3月;
2、可行性研究报告批复:
2009年6月;
3、基础设计:
2009年6月~2009年11月;
4、基础设计审查及批复:
2009年11月~2009年12月;
5、详细设计:
2009年12月~2010年9月;
6、工程建设:
2010年10月~2011年10月;
7、工程投产2011年11月。
第九节投资估算及资金筹措
一、建设投资估算
1.1投资估算编制的依据
1、中国石油天然气总公司《石油建设安装工程费用定额、石油建设工程其他费用定额》([95]中油基字第79号)
2、中国石油天然气集团公司《中国石油天然气集团公司建设项目可行性研究报告内容和深度的规定》(中油计字[2000]第499号)
3、中国石油天然气股份有限公司《中国石油天然气股份有限公司石油建设工程其他费用补充规定》(石油计字[2003]71号)
4、中国石油天然气股份有限公司《中国石油天然气股份有限公司建设项目经济评价参数(2004)》(石油计字[2004]86号)
1.2投资估算范围
建设投资估算范围包括:
80万吨/年催化裂化装置界区内的固定资产投资、无形资产投资、递延资产投资和预备费。
1.3建设投资估算办法
1.3.1工程费用估算
1、采用工程量法及相关系数法进行估算。
2、设备材料价格及施工费达到2005年价格水平。
3、设备运杂费按设备原价的9%计算,主要材料费运杂费按5.5%计算。
1.3.2固定资产其他费估算
1、建设单位管理费(含工程建设监理费):
按中油(95)中油基字第79号和石油计字(2003)71号文有关规定,按工程费用乘以相应费率并乘以调整系数2.4估算。
2、场地准备及临时设施费:
按石油计字(2003)71号文有关规定,按新建工程的工程费用乘以0.4%估算。
3、工程勘察和设计费:
根据中国石油天然气股份有限公司《中国石油天然气股份有限公司石油建设工程其他费用补充规定》(石油计字[2003]71号)和国家计委、建设部“关于发布《工程勘察设计收费管理规定》的通知”(计价格[2002]10号)有关规定计算,内容包括:
勘察费、可行性研究费、工程设计收费和非标设备设计费。
4、环境影响评价费:
根据中国石油天然气股份有限公司《中国石油天然气股份有限公司石油建设工程其他费用补充规定》(石油计字[2003]71号)估算。
5、劳动安全卫生评价费:
根据中国石油天然气股份有限公司《中国石油天然气股份有限公司石油建设工程其他费用补充规定》(石油计字[2003]71号)估算。
6、工程保险费:
根据中国石油天然气股份有限公司《中国石油天然气股份有限公司石油建设工程其他费用补充规定》(石油计字[2003]71号)估算。
7、压力容器检验费:
按实际情况估列。
1.3.3无形资产投资估算
专利及专有技术使用费:
按有关报价资料估算。
1.3.4递延资产投资
1、办公及生活家具购置费:
根据中国石油天然气总公司《石油建设工程其它费用规定》((95)中油基字第79号文件)估算。
2、生产准备费:
:
根据中国石油天然气总公司《石油建设工程其它费用规定》((95)中油基字第79号文件)估算。
1.4预备费估算
1、基本预备费:
以固定资产投资、无形资产投资和递延资产投资之和的10%计算。
2、价差预备费:
根据国家发展计划委员会会计投资(1999)1340号文精神,本工程暂不考虑。
二、资金筹措及资金使用计划
2.1资金筹措
本项目资本金65%由企业自有资金投入,其余部分为银行借款。
借款年利率为5.022%。
流动资金中30%为自有资金,70%为银行借款,借款年利率为4.536%。
第十节财务评价
一、财务评价依据及基础数据与参数
1.1财务评价依据
本项目可行性研究报告经济评价的编制执行石油计字[2002]234号《炼油化工建设项目可行性研究报告编制规定》有关规定,按照新建项目进行经济评价。
评价范围仅包括催化裂化装置。
1)本项目生产期各年生产负荷均为100%。
2)本项目计算期17年,其中建设期2年,生产期15年。
3)原材料、辅助材料、燃料动力价格
原料价格(含税)依据石油计字[2004]86号文有关规定确定。
混合原料油:
1309元/吨
辅助材料价格按现行市场价格确定。
燃料动力价格:
参照厂方提供的价格确定(含税)。
新鲜水
2
元/吨
循环水
0.29
元/吨
中压除氧水
17.55
元/吨
除盐水
9.36
元/吨
电
0.48
元/度
1.0Mpa蒸汽
59.89
元/吨
3.5Mpa蒸汽
79.10
元/吨
0.5Mpa蒸汽
59.89
元/吨
净化压缩空气
0.05
元/标立
非净化压缩空气
0.05
元/标立
氮气
2.34
元/标立
4)装置定员为36人,工资及附加费按35000元/人.年计算。
5)固定资产折旧年限按14年考虑,残值率为5%,修理费按固定资产原值(扣除建设期利息)的3%计算。
6)无形资产和递延资产分别按10年和5年摊销。
7)其他制造费按固定资产原值(扣除建设期利息)的1%计算,其他管理费按35000元/年.人计算。
8)产品价格(含税):
依据石油计字[2004]86号文有关规定确定。
干气
1021
元/吨
液化石油气
1393
元/吨
汽油
2152
元/吨
轻柴油
1912
元/吨
油浆
1041
元/吨
9)销售费用按销售收入的0.5%计取。
10)本项目财务基准收益率为12%。
11)财务费用
建设投资借款及流动资金借款利息计入当年财务费用中。
第二章工艺流程设计
第一节生产方法
一、原料、产品、催化剂
1.1原料
v催化裂化的原料来源十分广泛,重质馏分油、蜡油、焦化馏分油、减粘裂化油灯都可做它的原料油。
为充分利用资源,现在一般采用渣油催化裂化。
v渣油按含金属、残炭的高低、可分为三大类:
v1、渣油金属<10PPM残炭<5%。
这类加工难度较少,过剩热量可用降低进料温度,多取油浆来解决,利用低转化率操作来减少剂油接触时间。
用钝化剂可减少焦炭产率。
v2、渣油金属10~30PPM,残炭5~10%。
这类加工难度较大,过剩热量采用在再生器内或再生器外设取热措施除掉。
v3、渣油金属>30PPM,残炭>10%。
此类难加工,需预处理。
1.2产品
主要产品:
汽油、液化石油气、轻柴油
副产品:
干气、油浆
1.3催化剂
根据一些厂的使用证明:
Y-15剂具有活性高、稳定性好、耐高温、耐水汽化、耐金属性能也好、而且炼渣油也有较好的选择性。
股本设计选用Y-15催化剂。
催化剂性质表1-3
名称
项目
长岭
Y-15新鲜剂
平衡剂
CRC—催化剂
下喷嘴上喷嘴
筛分组成(重%)
0—20µ
2.6
0.66
12.6
11.3
20—40µ
12.4
11.64
32.1
33.9
40—80µ
47.5
71.2
47.7
48.6
80—110µ
23.2
12.2
7.1
5.8
>110µ
14.3
4.8
0.5
0.4
比表面积(㎡/g)
392.5
126.6
76
64
孔体积
0.65
0.43
0.164
0.17
微反活性(%)
80.4
72
87
80
充气密度(g/ml)
0.43
0.57
0.85
0.87
沉降密度(g/ml)
0.45
0.61
0.91
0.91
压紧密度(g/ml)
0.52
0.71
1.17
1.11
骨架密度(g/ml)
0.27
2.38
2.68
2.73
重Fe
金Ni
属V
300
6002
6306
1400
1465
1938
66
83
110
第二节化学原理
一、催化裂化条件下各族烃类的主要反应:
1、烷烃裂化为较小分子的烯烃和烷烃,如:
C16H34 ?
?
C8H16 + C8H18
2、烯烃裂化为较小分子的烯烃。
3、异构化反应
4、氢转移反应
5、芳构化反应
6、环烷烃裂化为烯烃
7、烷基芳烃脱烷基反应
8、缩合反应 单环芳烃可缩合成稠环芳烃,最后缩合成焦炭,并放出氢气,使烯烃饱和。
由以上反应可见,在烃类的催化裂化反应过程中,裂化反应的进行
使大分子分解为小分子的烃类,这是 催化裂化工艺成为重质油轻质化重要手段的根本依据。
而氢转移反应使催化汽油饱和度提高,安定性好。
异构 化、芳构化反应是催化汽油辛烷值提高的重要原因。
催化裂化得到的石油馏分仍然是许多种烃类组成的复杂混合物。
催化裂化并不是各族烃类单独反应的综合 结果,在反应条件下,任何一种烃类的反应都将受到同时存在的其它烃类的影响,并且还需要考虑催化剂存在 对过程的影响。
石油馏分的催化裂化反应是属于气-固非均相催化反应。
反应物首先是从油气流扩散到催化剂孔隙内,并且 被吸附在催化剂的表面上,在催化剂的作用下进行反应,生成的产物再从催化剂表面上脱附,然后扩散到油气 流中,导出反应器。
因此烃类进行催化裂化反应的先决条件是在催化剂表面上的吸附。
实验证明,碳原子相同 的各种烃类,吸附能力的大小顺序是:
稠环芳烃 > 稠环、多环环烷烃 > 烯烃 > 烷基芳烃 > 单环环烷烃 > 烷烃
而按烃类的化学反应速度顺序排列,大致情况如下:
烯烃 > 大分子单烷侧链的单环芳烃 > 异构烷烃和环烷烃 > 小分子单烷侧链的单环芳烃> 正构烷烃 > 稠环芳烃
综合上述两个排列顺序可知,石油馏分中芳烃虽然吸附性能强,但反应能力弱,吸附在催化剂表面上占据 了大部分表面积,阻碍了其它烃类的吸附和反应,使整个石油馏分的反应速度变慢。
烷烃虽然反应速度快,但 吸附能力弱,对原料反应的总效应不利。
而环烷烃既有一定的吸附能力又具适宜的反应速度。
因此认为,富含 环烷烃的石油馏分应是催化裂化的理想原料。
但实际生产中,这类原料并不多见。
石油馏分催化裂化的另一特点就是该过程是一个复杂反应过程。
反应可同时向几个方向进行,中间产物又 可继续反应,这种反应属于平行-顺序反应。
平行-顺序反应的一个重要特点是反应深度对产品产率分配有重大影响。
随着反应时间的增 长,转化率提高,气体和焦炭产率一直增加。
汽油产率开始时增加,经过一最高点后又下降。
这是因为到一定 反应深度后,汽油分解成气体的反应速度超过汽油的生成速度,即二次反应速度超过了一次反应速度。
因此要 根据原料的特点选择合适的转化率,这一转化率应选择在汽油产率最高点附近。
第三节装置组成
本次设计范围只含盖80×104t/a催化裂化装置边界区内部分,主要组成:
反应-再生部分、分馏部分、吸收稳定部分、机组部分、烟气能量回收部分、余热锅炉及产汽部分。
1.1反应-再生系统
反应再生系统形式(同轴、高低并列)
原料油进入本装置原料油缓冲罐,换热后进入提升管反应器的第一反应区进行裂化反应,反应后的油气和催化剂通过大孔分布板进入提升管的第二反应区进行氢转移和异构化反应。
生成汽油、轻柴油、液化石油气、干气、油浆等气相产物,同时生成焦炭。
反应油气与待生催化剂经提升管反应器出口快分设施迅速分离,油气经单级旋风分离器分离催化剂后,离开沉降器进入分馏塔。
为保证MIP工艺对第二反应区催化剂空速的要求,由汽提段底部设待生催化剂外循环抽出系统及外循环管和循环滑阀,向第二反应区补充待生催化剂。
待生催化剂经汽提段、待生斜管、待生滑阀进入再生器的烧焦罐底部,在富氧、CO助燃剂的条件下进行完全再生。
再生过程的过剩热量由外取热器取走。
1.2分馏系统
由沉降器来的反应油气进入分馏塔底部,通过人字型挡板与循环油浆逆流接触,洗涤反应油气中的催化剂并脱除过热,使油气呈饱和状态进入分馏塔上部进行分馏。
分馏塔顶油气冷却至40℃,进入分馏塔顶油气分离器进行气液相分离,分离出的粗汽油经粗汽油泵打入吸收塔作吸收剂,富气进入气压机。
轻柴油自分馏塔自流至轻柴油汽提塔,汽提后的轻柴油由轻柴油泵抽出,冷却至60℃,分为二路,一路作为产品出装置,一路再冷却至40℃,送至再吸收塔作吸收剂。
分馏塔多余的热量分别由顶循环回流,一中段循环回流、二中段循环回流和油浆循环回流取走。
1.3吸收-稳定系统