道路水泥论文.docx
《道路水泥论文.docx》由会员分享,可在线阅读,更多相关《道路水泥论文.docx(14页珍藏版)》请在冰豆网上搜索。
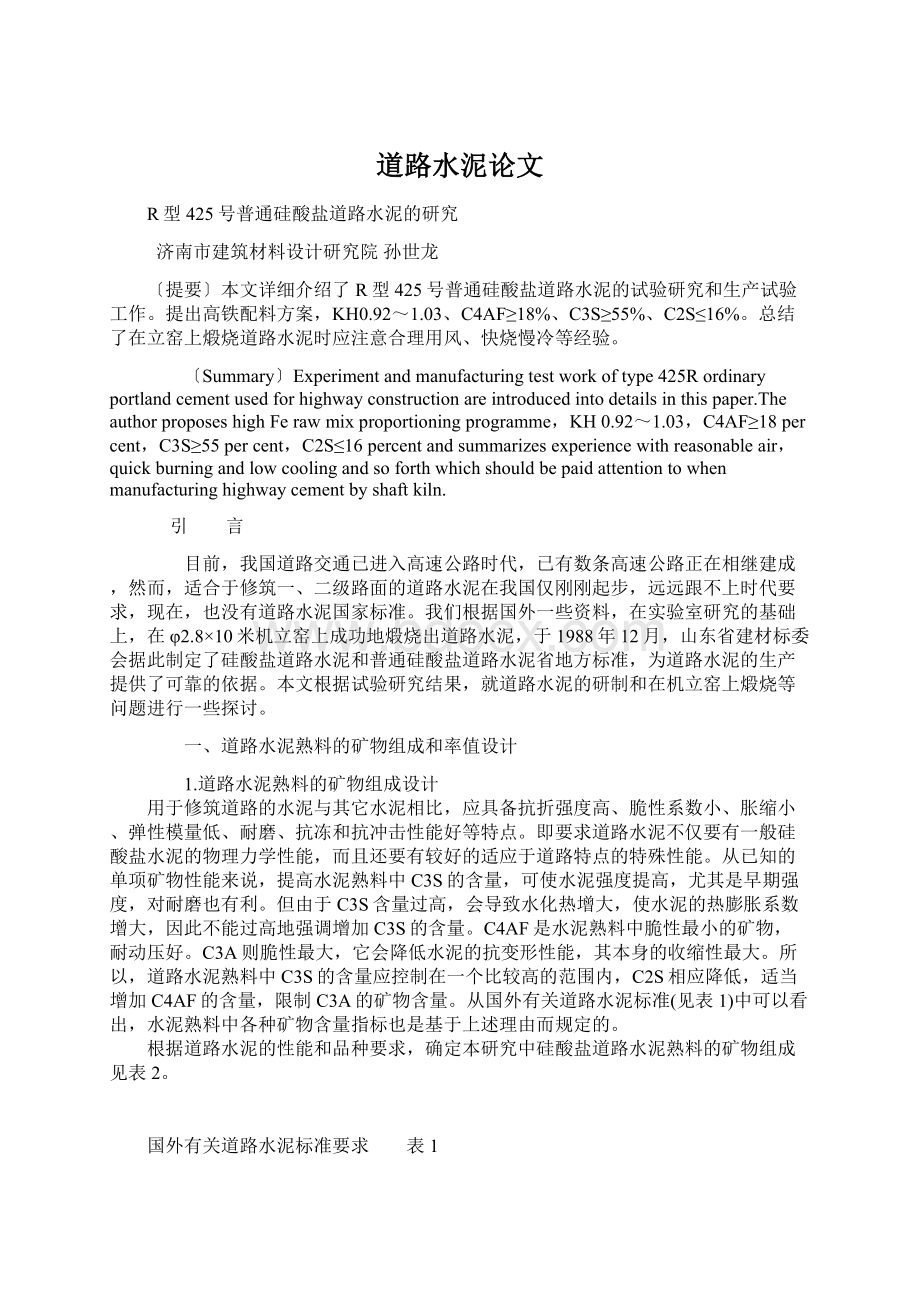
道路水泥论文
R型425号普通硅酸盐道路水泥的研究
济南市建筑材料设计研究院孙世龙
〔提要〕本文详细介绍了R型425号普通硅酸盐道路水泥的试验研究和生产试验工作。
提出高铁配料方案,KH0.92~1.03、C4AF≥18%、C3S≥55%、C2S≤16%。
总结了在立窑上煅烧道路水泥时应注意合理用风、快烧慢冷等经验。
〔Summary〕Experimentandmanufacturingtestworkoftype425Rordinaryportlandcementusedforhighwayconstructionareintroducedintodetailsinthispaper.TheauthorproposeshighFerawmixproportioningprogramme,KH0.92~1.03,C4AF≥18percent,C3S≥55percent,C2S≤16percentandsummarizesexperiencewithreasonableair,quickburningandlowcoolingandsoforthwhichshouldbepaidattentiontowhenmanufacturinghighwaycementbyshaftkiln.
引 言
目前,我国道路交通已进入高速公路时代,已有数条高速公路正在相继建成,然而,适合于修筑一、二级路面的道路水泥在我国仅刚刚起步,远远跟不上时代要求,现在,也没有道路水泥国家标准。
我们根据国外一些资料,在实验室研究的基础上,在φ2.8×10米机立窑上成功地煅烧出道路水泥,于1988年12月,山东省建材标委会据此制定了硅酸盐道路水泥和普通硅酸盐道路水泥省地方标准,为道路水泥的生产提供了可靠的依据。
本文根据试验研究结果,就道路水泥的研制和在机立窑上煅烧等问题进行一些探讨。
一、道路水泥熟料的矿物组成和率值设计
1.道路水泥熟料的矿物组成设计
用于修筑道路的水泥与其它水泥相比,应具备抗折强度高、脆性系数小、胀缩小、弹性模量低、耐磨、抗冻和抗冲击性能好等特点。
即要求道路水泥不仅要有一般硅酸盐水泥的物理力学性能,而且还要有较好的适应于道路特点的特殊性能。
从已知的单项矿物性能来说,提高水泥熟料中C3S的含量,可使水泥强度提高,尤其是早期强度,对耐磨也有利。
但由于C3S含量过高,会导致水化热增大,使水泥的热膨胀系数增大,因此不能过高地强调增加C3S的含量。
C4AF是水泥熟料中脆性最小的矿物,耐动压好。
C3A则脆性最大,它会降低水泥的抗变形性能,其本身的收缩性最大。
所以,道路水泥熟料中C3S的含量应控制在一个比较高的范围内,C2S相应降低,适当增加C4AF的含量,限制C3A的矿物含量。
从国外有关道路水泥标准(见表1)中可以看出,水泥熟料中各种矿物含量指标也是基于上述理由而规定的。
根据道路水泥的性能和品种要求,确定本研究中硅酸盐道路水泥熟料的矿物组成见表2。
国外有关道路水泥标准要求 表1
国家
矿物组成(%)
初凝时间
(时∶分)
抗折强度(MPa)
抗压强度(MPa)
C3A
MgO
SO3
C3S
3天
7天
28天
3天
7天
28天
日本
苏联
罗马尼亚
<6.0
≤8.0
≤6.0
≤2.5
≤2.5
2~3
3.5
≤3.0
>50
≥2∶00
≥2∶00
≥2∶00
3.5
(2天)
5.0
5.9
6.5
15
(2天)
26
51.5
40
道路水泥熟料矿物组成设计要求 表2
矿 物
C3S
C2S
C3A
C4AF
MgO
SO3
fCaO
含 量(%)
≥55
≤16
<5.0
≥18
<3.5
<3.5
<1.5
2.硅酸盐道路水泥熟料的率值设计
(1)熟料饱和系数KH的设计
为了降低道路水泥的脆性系数和水化热,必需限制水泥熟料中C3A的含量,因而使水泥的早期强度下降,为使水泥获得较好的早期强度,就必须取较高的饱和系数以获得较多的C3S来弥补由于C3A的降低而引起的强度损失。
按照预定的率值,配KH=0.92~1.03的饱和系数,以确定硅酸盐道路水泥熟料的最佳饱和系数。
(2)硅酸率n值的设计
由于KH值取值较高,在Al2O3+Fe2O3总量不变的情况下,n值应取得低些,这样在熟料煅烧过程中的液相量能相应增加,以促使C3S生成和fCaO的溶解及Ca2+和
离子的扩散,有利于A矿的形成。
否则,致使熟料烧成困难,且易于粉化,故在研究中取n值为1.6±0.1。
(3)铝氧率P值的确定
铝氧率表示熟料熔剂矿物中铝酸三钙与铁铝酸四钙的比例。
铝氧率高,则熟料中C3A多,相应C4AF减少,液相粘度增大,导致A矿形成反应速度减慢,影响熟料的质量;铝氧率过低,虽然使粘度较小,易于溶液中的质点扩散,对硅酸三钙形成也有利,但由于物料对温度变化比较敏感,不利于操作控制,使烧成范围变窄。
根据国外学者建议,道路水泥中C3S/C2S>5,C3A/C4AF<0.3,并限制C3A的含量,本研究试验中,道路水泥熟料取较低的P值,即P=0.8±0.1。
二、试验方法与内容
1.原、燃材料
小试硅酸盐道路水泥所用原、燃材料和某厂现用生产普通硅酸盐水泥所用的相同。
各种原、燃材料化学成分见表3,燃料工业分析见表4。
原料化学成分(%) 表3
原 料
SiO2
Fe2O3
Al2O3
CaO
MgO
SO3
烧失量
结晶水
CaF2
石灰石
粘 土
铁 渣
萤 石
石 膏
煤 灰
0.88
67.87
7.60
1.80
55.43
0.12
4.77
71.63
0.08
4.25
0.25
13.95
5.81
0.50
32.66
53.22
1.77
1.17
33.66
2.15
1.35
2.35
0.23
0.06
0.49
40.98
2.76
43.23
4.21
8.29
25.50
17.41
32.11
燃料工业分析 表4(略)
2.生料制备
按率值和矿物组成要求进行计算、配料入磨,小试生料化学成分见表5。
3.熟料煅烧
(1)熟料煅烧要求
生料化学成分和率值 表5
编 号
成 分(%)
细 度
(%)
率 值
SiO2
Fe2O3
Al2O3
CaO
MgO
烧失量
KH
n
P
S1
S2
S3
S4
S5
S6
S7
S8
S9
S10
S11
S12
11.92
11.46
11.45
11.23
11.10
11.00
10.84
11.67
11.27
11.32
10.90
11.40
3.70
3.52
3.60
3.45
3.73
3.57
3.50
3.75
3.84
3.46
3.59
3.86
3.17
3.09
3.13
3.04
2.78
2.95
2.93
3.24
3.17
3.28
3.16
3.22
38.09
38.31
38.34
38.37
38.52
38.40
38.47
37.67
37.42
37.58
37.72
37.81
1.41
1.54
1.25
1.22
1.23
1.38
1.33
1.73
1.83
2.08
2.32
1.70
38.05
38.53
39.20
39.34
39.33
39.42
39.73
38.88
39.35
39.27
40.16
38.77
1.4
2.2
2.1
1.9
2.2
2.8
1.4
2.2
0.946
0.997
0.995
1.022
1.050
1.048
1.068
0.949
0.977
0.967
1.000
0.968
1.74
1.73
1.70
1.73
1.71
1.69
1.69
1.67
1.61
1.68
1.61
1.62
0.86
0.88
0.87
0.88
0.75
0.83
0.84
0.86
0.83
0.95
0.88
0.83
实验室硅酸盐道路水泥熟料需在箱式高温电炉内烧成,根据实验条件和设备,制定硅酸盐道路水泥熟料的煅烧要求:
(a)相同的升温速率
(b)相同的煅烧温度
(c)相同的恒温时间
(d)相同的冷却方式
(2)熟料煅烧
将制备好的生料制成具有一定粒度、含水率和强度的生料球,在箱式高温电炉内煅烧,自然升温到1350℃恒温50分钟后,打开炉门,待炉膛温度冷至600~800℃时将熟料取出,再自然冷却至室温,经化学分析,所煅烧的硅酸盐道路水泥熟料的化学成分见表6。
岩相鉴定结果见表7和图1。
熟料化学成分和率值 表6
编号
成 分(%)
率 值
SiO2
Fe2O3
Al2O3
CaO
MgO
烧失量
fCaO
CaF2
SO3
KH
n
P
S1
19.74
6.34
5.32
61.73
2.33
0.66
0.24
0.918
1.69
0.84
S2
19.59
6.14
5.09
62.70
2.24
0.85
0.70
0.948
1.74
0.83
S3
19.37
6.05
5.04
62.79
2.03
0.28
0.17
1.03
2.09
0.965
1.75
0.83
S4
19.34
5.79
5.14
63.82
1.23
0.39
0.73
0.92
2.07
0.980
1.77
0.89
S5
18.79
6.13
5.24
63.76
2.10
0.39
0.94
1.04
2.13
1.006
1.65
0.85
S6
18.42
6.05
5.50
63.75
2.47
0.74
1.50
1.04
2.03
1.020
1.59
0.91
S7
18.16
6.07
5.07
63.67
2.17
0.89
1.046
1.63
0.84
S8
19.36
4.49
5.46
61.49
3.16
0.24
0.926
1.62
0.84
S9
19.11
6.72
5.22
61.54
3.19
0.22
0.59
0.945
1.60
0.78
S10
19.21
6.28
5.41
62.48
3.25
0.06
0.955
1.64
0.86
S11
18.84
6.63
5.75
63.24
3.35
0.64
0.975
1.52
0.87
S12
19.47
6.34
5.15
62.59
2.91
0.38
0.951
1.69
0.81
硅酸盐道路水泥熟料岩相鉴定结果 表7
编号
名 称
矿物组成(%)
C3S
C2S
C3A
C4AF
MgO
S12
硅酸盐道路
水泥熟料
65
5~8
少量
22
3
图1 黑色致密块状道路水泥熟料(反光×250)(略)
由鉴定结果看出矿物结构特征:
C3S呈板柱状,晶体较完整,尺寸欠均齐,一般25~45微米,大者80微米,小者5微米;C2S圆形麻面状较多,极少表面有双晶纹;C3A小片状;MgO多呈矩形均匀分布。
道路水泥熟料XRD分析结果见图2。
从XRD分析结果可以看出,这与岩相鉴定结果是一致的。
图2 道路水泥熟料的XRD图(略)
V—C3S;△—C4AF;φ—C2S(少);无fCaO
(3)硅酸盐道路水泥熟料物理力学性能
在硅酸盐道路水泥熟料中,加入4.0%天然二水石膏一起磨至一定细度,进行物理力学性能测试,结果见表8。
硅酸盐道路水泥熟料物理力学性能 表8
编号
细度
(%)
稠度
(%)
初凝
(时∶分)
终凝
(时∶分)
安定性
强 度(MPa)
SO3
(%)
烧失量(%)
抗折
抗压
3天
7天
28天
3天
7天
28天
S2
4.9
25.75
2∶00
5∶00
合格
7.0
7.4
8.9
45.1
54.6
68.9
3.44
0.85
S3
6.1
25.50
3∶40
5∶47
合格
6.2
6.9
8.3
38.3
44.4
57.7
3.63
0.75
S4
5.9
26.00
4∶44
7∶18
合格
6.7
7.7
8.9
42.9
53.3
64.5
3.37
3.00
S5
4.3
25.75
3∶42
6∶36
合格
6.5
7.3
8.2
38.7
47.7
58.0
1.79
2.05
S6
5.3
26.00
2∶45
3∶55
合格
6.7
7.6
8.1
42.7
50.4
55.8
S7
7.5
25.00
4∶10
5∶55
合格
6.2
7.3
7.8
43.0
48.0
54.7
S8
8.5
25.75
4∶55
7∶20
合格
6.4
7.3
8.4
36.0
44.0
56.7
S9
11.1
25.50
3∶50
4∶50
合格
6.9
7.6
8.6
42.3
51.8
58.7
S10
6.9
25.50
3∶05
4∶05
合格
6.9
7.3
7.6
36.9
42.1
51.5
S11
3.1
25.50
1∶27
2∶22
合格
6.9
7.0
8.2
35.7
40.0
48.3
S12
4.8
23.00
2∶28
4∶02
合格
6.5
6.9
8.8
43.1
39.9
62.4
从表8测试结果看,合理的率值可以烧成理想物理性能的道路水泥熟料,如S2和S4两种熟料质量较好,以此率值来调整确定最佳配比,即取KH=0.95±0.2,n=1.6±0.1,P=0.8±0.1。
另外,细度过低会影响28天的抗压强度和凝结时间,使强度下降,凝结时间提前,控制细度在6%左右比较合适。
(4)不同煅烧温度和恒温时间对熟料质量的影响
煅烧制度直接影响着水泥熟料质量。
将S4生料样置于不同的温度下以相同恒温时间煅烧和在相同煅烧温度下以不同恒温时间煅烧,熟料质量情况见表9。
不同煅烧温度和恒温时间对熟料质量的影响 表9
项目
编号
温度
(℃)
恒时
(分)
熟料化学成分(%)
率值
fCaO
(%)
熟料矿物组成(%)
SiO2
Fe2O3
Al2O3
CaO
MgO
KH
KH-
n
P
C3S
C2S
C3A
C4AF
S10-1
1300
40
19.06
6.59
5.57
62.50
3.25
0.955
0.921
1.57
0.85
1.87
55.26
12.95
3.58
20.03
S10-1
1350
40
19.06
6.59
5.57
62.50
3.25
0.955
0.949
1.57
0.85
0.38
61.35
8.36
3.58
20.23
S10-1
1400
40
19.06
6.59
5.57
62.50
3.25
0.955
0.950
1.57
0.85
0.33
61.56
8.20
3.58
20.03
S10-1
1350
20
19.09
6.53
5.39
62.58
3.11
0.962
0.953
1.60
0.83
0.48
62.31
7.22
3.21
19.85
S10-1
1350
30
19.14
6.45
5.47
62.90
3.34
0.963
0.954
1.61
0.84
0.48
62.70
7.53
3.56
19.61
S10-1
1350
40
19.06
6.59
5.57
62.50
3.25
0.955
0.955
1.55
0.82
0.38
61.35
8.36
3.58
20.03
S10-1
1350
50
19.06
6.74
5.56
62.91
3.00
0.954
0.954
1.55
0.82
0.44
62.43
7.45
3.30
20.49
从表9可知,温度过低不利于A矿形成,致使fCaO增高,熟料质量降低。
随温度升高,液相粘度减小,液相量增加,促进了C2S和CaO的固溶,提高了Ca2+和
离子的扩散,降低了fCaO,促进了A矿的形成,同时,A矿固溶程度随温度升高而提高,从而提高了A矿的水化活性,使熟料质量得以提高。
但温度过高,不仅浪费热源,熟料强度也会因C3S析晶完整粗大而降低。
因而道路水泥熟料烧成范围控制在1320~1420℃比较适宜。
恒温时间则是在温度和液相量一定的情况下,物料各组分互相作用发生化学物理反应所用的时间,不同煅烧恒温时间中fCaO含量和煅烧程度不同,这对熟料的质量就有不同的影响。
从表9编号S4~S7样中看出,fCaO随着温度的升高和恒温时间的增加而减少。
选用适当的煅烧范围和恒温时间,就能保障熟料的煅烧质量。
根据以上分析,道路水泥的煅烧恒温时间为30~40分钟。
(5)复合矿化剂在道路水泥熟料煅烧中的影响
研究和实践证明,在水泥生料中掺入适量的萤石和石膏作为复合矿化剂,可以改善水泥熟料的矿物组成和易烧性,也有利于C3S的形成和熟料质量的提高。
在道路水泥的研制中,掺入0.8%的萤石和1.5%石膏作复合矿化剂(S10)与不掺复合矿化剂(S11)的料样做比较,试验结果见表10。
从表10看出,掺矿化剂要比不掺矿化剂好,强度有所提高,凝结时间也好,SO3含量降低,脆性系数提高。
在熟料煅烧时可使烧成范围扩大,有利于操作控制。
4.硅酸盐道路水泥特性试验
硅酸盐道路水泥的特性作为重点研究目标。
由于对道路水泥的特殊要求,本研究试验就道路水泥的磨耗率、抗干缩、抗冷冻与普通硅酸盐水泥进行了对比试验,特性测试结果见表11—a和表11—b。
从表11—a可以看出,道路水泥的磨耗率比普通硅酸盐水泥的磨耗率低,而掺入6.5%钢渣的普通硅酸盐道路水泥的又大大低于普通硅酸盐道路水泥的磨耗率。
由此可知,在磨制道路水泥时,掺入耐磨性较好的工业废料钢渣,不仅可降低道路水泥的磨耗率,提高其耐磨性,并可降低生产成本。
复合矿化剂对道路水泥熟料物理性能的影响 表10
编号
细度
(%)
稠度
(%)
凝结时间(时:
分)
安定
性
抗折强度(MPa)
抗压强度(MPa)
SO3
脆性
系数
初凝
终凝
3天
7天
28天
3天
7天
28天
S10
6.9
25.50
3:
05
4:
05
合格
6.9
7.3
7.6
36.9
42.1
51.5
3.20
6.7
S11
3.1
25.50
1:
27
2:
22
合格
6.9
7.0
8.2
35.7
40.0
48.3
3.39
5.8
注:
S10和S11为同一配比。
道路水泥特性测试结果 表11-a
编号
磨耗率(%)
水泥砂浆干缩率(%)
7天
14天
28天
2个月
3个月
A组
1.65
-0.0267
-0.0275
-0.0269
-0.0267
-0.0272
B组
1.79
-0.0288
-0.0295
-0.0283
-0.0282
-0.0285
C组
1.09
注:
A组为普通硅酸盐道路水泥;
B组为普通硅酸盐水泥;
C组为掺入6.5%钢渣的普通硅酸盐道路水泥。
道路水泥特性测试结果 表11-b
编号
混凝土标号
28天抗压强度
(MPa)
对比强度
(MPa)
冻融后强度
(MPa)
强度损失
(%)
重量损失
(%)
冷冻次数
M
A组
B组
300号
300号
53.6
41.5
57.0
47.2
57.0
45.5
0
3.53
0.08
-0.04
50
50
从表11—b可以看出,道路水泥在50次冷冻后的强度损失为零,而普通硅酸盐水泥的强度损失达3.53%,道路水泥的抗冻性明显好于普通硅酸盐水泥。
从上述试验分析研究结果可知,道路水泥的实验室研究完全符合原设计要求。
三、R型425号普通硅酸盐道路水泥生产中试
根据实验室研究结果,于1988年8月在机立窑上进行了R型425号普通硅酸盐道路水泥生产中试。
1.原材料的要求
根据实验室研究,对各种原材料的质量控制见表12。
2.中试R型425号普通硅酸盐道路水泥内控指标
(1)熟料中C3S不得低于55%;C2S<20%。
(2)熟料中C3A不得超过6.0%。
(3)熟料中C4AF不得低于16%。
(4)熟料中MgO不得超过4.0%。
(5)水泥中烧失量不得超过5.0%。
(6)强度:
3天抗折强度大于4.2兆帕,3天抗压强度大于12.0兆帕;28天抗折强度大于6.9兆帕,28天抗压强度大于49.0兆帕。
进厂原料、燃料的质量要求 表12
名 称
主 要 质 量 指 标
石灰石
CaO>52%