推荐万向节滑动叉加工艺及铣床夹具设计说明书 精品.docx
《推荐万向节滑动叉加工艺及铣床夹具设计说明书 精品.docx》由会员分享,可在线阅读,更多相关《推荐万向节滑动叉加工艺及铣床夹具设计说明书 精品.docx(41页珍藏版)》请在冰豆网上搜索。
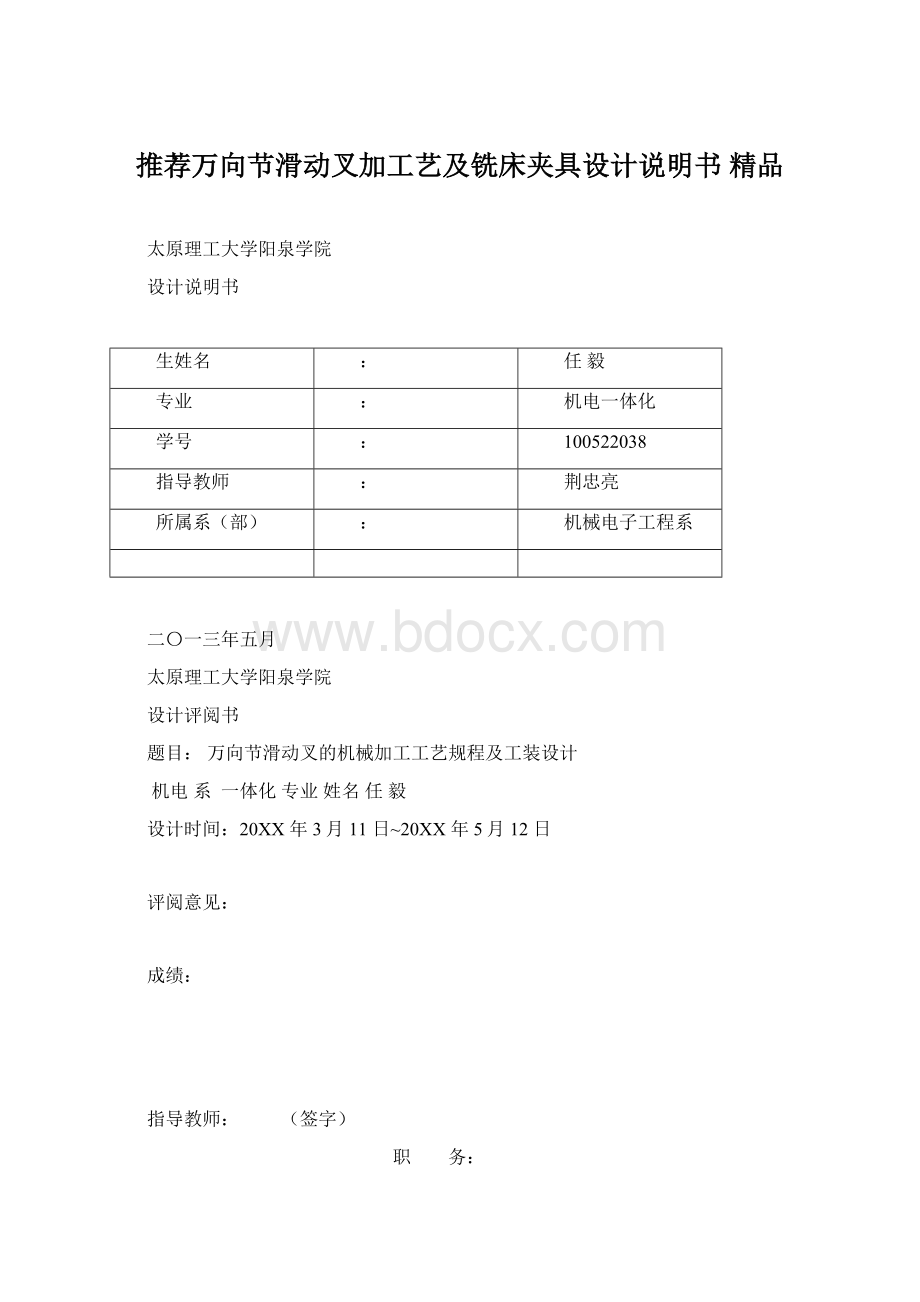
推荐万向节滑动叉加工艺及铣床夹具设计说明书精品
太原理工大学阳泉学院
设计说明书
生姓名
:
任毅
专业
:
机电一体化
学号
:
100522038
指导教师
:
荆忠亮
所属系(部)
:
机械电子工程系
二〇一三年五月
太原理工大学阳泉学院
设计评阅书
题目:
万向节滑动叉的机械加工工艺规程及工装设计
机电系一体化专业姓名任毅
设计时间:
20XX年3月11日~20XX年5月12日
评阅意见:
成绩:
指导教师:
(签字)
职 务:
201年 月 日
太原理工大学阳泉学院
设计答辩记录卡
机电系 一体化 专业姓名任毅
答辩内容
问题摘要
评议情况
记录员:
(签名)
成绩评定
指导教师评定成绩
答辩组评定成绩
综合成绩
注:
评定成绩为100分制,指导教师为30%,答辩组为70%。
专业答辩组组长:
(签名)
201年 月 日
摘要
汽车底盘传动轴上的万向节滑动叉它位于传动轴的端部。
主要作用一是传递扭矩,使汽车获得前进的动力;二是当汽车后桥钢板弹簧处在不同的状态时,由本零件可以调整传动轴的长短及其位置。
零件的两个叉头部位上有两个孔,是用来安装滚针轴承并且与十字轴相连,起万向节轴节的作用。
而零件外圆内的花键孔与传动轴端部的花键轴相配合,用于传递动力之用。
而这次的夹具也是用于装夹此零件,而夹具的作用也是为了提高零件的劳动生产率、保证加工质量、降低劳动强度。
而夹具的另一个目的也是为了固定零件位置,使其得到最高的效率。
关键字:
万向节滑动叉;传递扭矩;调整位置;夹具;提高效率
第一章概述
本次设计的课题名称是万向节滑动叉机加工艺及工装设计。
万向节滑动叉位于传动轴的端部,主要作用之一是传递扭矩,使汽车获得前进的动力;二是当汽车后桥钢板弹簧处在不同状态时,由本零件可以调整传动轴的长短及其位置。
万向节滑动叉就是将万向节叉和滑动花键副的一部分组合起来,使其成为一个零件,其特征是该万向节滑动叉为采用管材制作的万向节叉与滑动套为一体的整体式结构,其端部呈叉形结构,并设有两个十字销孔,用于安装十字万向节;在管内设有内花键,这种呈整体式结构的滑动叉,不仅加工容易、成本低,而且强度高,故其使用寿命与传统的万向节叉滑动套合件相比,有了成倍的提高。
它的研究和使用可以简化万向传动装置的结构,也满足功能要求,因此对万向节滑动叉的研究有极大的实际意义。
本课题的研究及论文的撰写是在荆老师的悉心指导下完成的。
荆老师在百忙中给我们讲解论文中的细节以及论文中所涉及的工艺分析,还有他严谨的治学态度也是我学习的榜样。
通过本次设计,使我对本专业有了更加深刻的了解,在以后的工作中也具有重要意义。
第二章零件的分析
2.1零件的作用
题目所给定的零件是解放牌汽车底盘传动轴上的万向节滑动叉,它位于传动轴的端部。
主要作用一是传递扭矩,使汽车获得前进的动力;二是当汽车后桥钢板弹簧处在不同的状态时,由本零件可以调整传动轴的长短及其位置。
零件的两个叉头部位上有两个Φ
mm的孔,用以安装滚针轴承并与十字轴相连,起万向联轴节的作用。
零件Φ65mm外圆内为Φ50mm花键孔与传动轴端部的花键轴相配合,用于传递动力之用。
2.2零件的材料
万向节滑动叉的材料选用45钢,属于优等碳素结构钢,经调质处理后有良好的综合机械性能和加工工艺性能,零件材料的选择主要是考虑到满足使用要求,同时兼顾材料的工艺性和经济性,45钢满足以上要求,所以选用45钢。
45钢调质后机械性能
屈服强度
抗拉强度
延伸率
布氏硬度
σ
=550MN/m
σb=750MN/m
δs=20%
HB=235
2.3零件的工艺分析
2.3.1结构分析
零件的结构分析主要包括以下三方面:
(1)零件表面的组成和基本类型
尽管组成零件的结构多种多样,但从形体上加以分析,都是由一些基本表面和特形表面组成的。
基本表面有内外圆柱表面、圆锥表面和平面等;特形表面主要有螺旋面、渐开线齿形表面、圆弧面(如球面)等。
在零件结构分析时,根据机械零件不同表面的组合形成零件结构上的特点,就可选择与其相适应的加工方法和加工路线,例如外圆表面通常由车削或磨削加工;内孔表面则通过钻、扩、铰、镗和磨削等加工方法获得。
机械零件不同表面的组合形成零件结构上的特点。
在机械制造中,通常按零件结构和工艺过程的相似性,将各类零件大致分为轴类零件、套类零件、箱体类零件、齿轮类零件和叉架类零件等。
(2)主要表面与次要表面区分
根据零件各加工表面要求的不同,可以将零件的加工表面划分为主要加工表面和次要加工表面;这样,就能在工艺路线拟定时,做到主次分开以保证主要表面的加工精度。
(3)零件的结构工艺性
所谓零件的结构工艺性是指零件在满足使用要求的前提下,制造该零件的可行性和经济性。
功能相同的零件,其结构工艺性可以有很大差异。
所谓结构工艺性好,是指在现有工艺条件下,既能方便制造又有较低的制造成本。
2.3.2零件的技术要求分析
零件图样上的技术要求,既要满足设计要求,又要便于加工,而且齐全和合理。
其技术要求包括下列几个方面:
(1)加工表面的尺寸精度、形状精度和表面质量;
(2)各加工表面之间的相互位置精度;
(3)工件的热处理和其它要求,如动平衡、镀铬处理、去磁等。
零件的尺寸精度、形状精度、位置精度和表面粗糙度的要求,对确定机械加工工艺方案和生产成本影响很大。
因此,必须认真审查,以避免过高的要求使加工工艺复杂化和增加不必要的费用。
在认真分析了零件的技术要求后,结合零件的结构特点,对零件的加工工艺过程便有一个初步的轮廓。
加工表面的尺寸精度、表面粗糙度和有无热处理要求,决定了该表面的最终加工方法,进而得出中间工序和粗加工工序所采用的加工方法。
如,轴类零件上IT7级精度、表面粗糙度Ra1.6μm的轴颈表面,若不淬火,可用粗车、半精车、精车最终完成;若淬火,则最终加工方法选磨削,磨削前可采用粗车、半精车(或精车)等加工方法加工。
表面间的相互位置精度,基本上决定了各表面的加工顺序。
2.3.3毛坯的选择
毛坯的确定,不仅影响毛坯制造的经济性,而且影响机械加工的经济性。
所以在确定毛坯时,既要考虑热加工方面的因素,也要兼顾冷加工方面的要求,以便从确定毛坯这一环节中,降低零件的制造成本。
机械加工中常用毛坯的种类
毛坯的种类很多,同一种毛坯又有多种制造方法,机械制造中常用的毛坯有以下几种:
(1)铸件
形状复杂的零件毛坯,宜采用铸造方法制造。
目前铸件大多用砂型铸造,它又分为木模手工造型和金属模机器造型。
木模手工造型铸件精度低,加工表面余量大,生产率低,适用于单件小批生产或大型零件的铸造。
金属模机器造型生产率高,铸件精度高,但设备费用高,铸件的重量也受到限制,适用于大批量生产的中小铸件。
其次,少量质量要求较高的小型铸件可采用特种铸造(如压力铸造、离心制造和熔模铸造等)。
(2)锻件
机械强度要求高的钢制件,一般要用锻件毛坯。
锻件有自由锻造锻件和模锻件两种。
自由锻造锻件可用手工锻打(小型毛坯)、机械锤锻(中型毛坯)或压力机压锻(大型毛坯)等方法获得。
这种锻件的精度低,生产率不高,加工余量较大,而且零件的结构必须简单;适用于单件和小批生产,以及制造大型锻件。
模锻件的精度和表面质量都比自由锻件好,而且锻件的形状也可较为复杂,因而能减少机械加工余量。
模锻的生产率比自由锻高得多,但需要特殊的设备和锻模,故适用于批量较大的中小型锻件。
(3)型材
型材按截面形状可分为:
圆钢、方钢、六角钢、扁钢、角钢、槽钢及其它特殊截面的型材。
型材有热轧和冷拉两类。
热轧的型材精度低,但价格便宜,用于一般零件的毛坯;冷拉的型材尺寸较小、精度高,易于实现自动送料,但价格较高,多用于批量较大的生产,适用于自动机床加工。
(4)焊接件
焊接件是用焊接方法而获得的结合件,焊接件的优点是制造简单、周期短、节省材料,缺点是抗振性差,变形大,需经时效处理后才能进行机械加工。
除此之外,还有冲压件、冷挤压件、粉末冶金等其它毛坯。
毛坯种类选择中应注意的问题
(1)零件材料及其力学性能
零件的材料大致确定了毛坯的种类。
例如材料为铸铁和青铜的零件应选择铸件毛
坯;钢质零件形状不复杂,力学性能要求不太高时可选型材;重要的钢质零件,为保证其力学性能,应选择锻件毛坯。
(2)零件的结构形状与外形尺寸
形状复杂的毛坯,一般用铸造方法制造。
薄壁零件不宜用砂型铸造;中小型零件可考虑用先进的铸造方法;大型零件可用砂型铸造。
一般用途的阶梯轴,如各阶梯直径相差不大,可用圆棒料;如各阶梯直径相差较大,为减少材料消耗和机械加工的劳动量,则宜选择锻件毛坯。
尺寸大的零件一般选择自由锻造;中小型零件可选择模锻件;一些小型零件可做成整体毛坯。
(3)生产类型
大量生产的零件应选择精度和生产率都比较高的毛坯制造方法,如铸件采用金属模机器造型或精密铸造;锻件采用模锻、精锻;型材采用冷轧或冷拉型材;零件产量较小时应选择精度和生产率较低的毛坯制造方法。
(4)现有生产条件
确定毛坯的种类及制造方法,必须考虑具体的生产条件,如毛坯制造的工艺水平,设备状况以及对外协作的可能性等。
(5)充分考虑利用新工艺、新技术和新材料
随着机械制造技术的发展,毛坯制造方面的新工艺、新技术和新材料的应用也发展很快。
如精铸、精锻、冷挤压、粉末冶金和工程塑料等在机械中的应用日益增加。
采用这些方法大大减少了机械加工量,有时甚至可以不再进行机械加工就能达到加工要求,其经济效益非常显著。
我们在选择毛坯时应给予充分考虑,在可能的条件下,尽量采用。
毛坯形状和尺寸的确定
毛坯形状和尺寸,基本上取决于零件形状和尺寸。
零件和毛坯的主要差别,在于在零件需要加工的表面上,加上一定的机械加工余量,即毛坯加工余量。
毛坯制造时,同样会产生误差,毛坯制造的尺寸公差称为毛坯公差。
毛坯加工余量和公差的大小,直接影响机械加工的劳动量和原材料的消耗,从而影响产品的制造成本。
所以现代机械制造的发展趋势之一,便是通过毛坯精化,使毛坯的形状和尺寸尽量和零件一致,力求作到少、无切削加工。
毛坯加工余量和公差的大小,与毛坯的制造方法有关,生产中可参考有关工艺手册或有关企业、行业标准来确定。
在确定了毛坯加工余量以后,毛坯的形状和尺寸,除了将毛坯加工余量附加在零件相应的加工表面上外,还要考虑毛坯制造、机械加工和热处理等多方面工艺因素的影响。
下面仅从机械加工工艺的角度,分析确定毛坯的形状和尺寸时应考虑的问题。
(1)工艺搭子的设置
有些零件,由于结构的原因,加工时不易装夹稳定,为了装夹方便迅速,可在毛坯上制出凸台,即所谓的工艺搭子。
工艺搭子只在装夹工件时用,零件加工完成后,一般都要切掉,但如果不影响零件的使用性能和外观质量时,可以保留。
(2)整体毛坯的采用
在机械加工中,有时会遇到如磨床主轴部件中的三瓦轴承、发动机的连杆和车床的开合螺母等类零件。
为了保证这类零件的加工质量和加工时方便,常做成整体毛坯,加工到一定阶段后再切开。
(3)合件毛坯的采用
为了便于加工过程中的装夹,对于一些形状比较规则的小形零件,如T形键、扁螺母、小隔套等,应将多件合成一个毛坯,待加工到一定阶段后或者大多数表面加工完毕后,再加工成单件。
图5.3a为T815汽车上的一个扁螺母。
毛坯取一长六方钢,图5.3b表示在车床上先车槽、倒角;图5.3c表示在车槽及倒角后,用?
24.5mm的钻头钻孔。
钻孔的同时也就切成若干个单件。
合件毛坯,在确定其长度尺寸时,既要考虑切割刀具的宽度和零件的个数,还应考虑切成单件后,切割的端面是否需要进一步加工,若要加工,还应留有一定的加工余量。
在确定了毛坯种类、形状和尺寸后,还应绘制一张毛坯图,作为毛坯生产单位的产品图样。
绘制毛坯图,是在零件图的基础上,在相应的加工表面上加上毛坯余量。
但绘制时还要考虑毛坯的具体制造条件,如铸件上的孔、锻件上的孔和空档、法兰等的最小铸出和锻出条件;铸件和锻件表面的起模斜度(拔模斜度)和圆角;分型面和分模面的位置等。
并用双点划线在毛坯图中表示出零件的表面,以区别加工表面和非加工表面。
2.3.4加工表面的技术要求分析
万向节滑动叉共有两组加工表面,他们相互间有一定的位置要求。
现分述如下:
a.以Φ39mm孔为中心的加工表面
这一组加工表面包括:
两个Φ
mm的孔及其倒角,尺寸为
的与两个孔Φ
mm相垂直的平面,还有在平面上的四个M8螺孔。
其中,主要加工表面为Φ
mm的两个孔。
b.以Φ50mm花键孔为中心的加工表面
这一组加工表面包括:
Φ
mm十六齿方齿花键孔,Φ55mm阶梯孔,以及Φ65mm的外圆表面和M60×1mm的外螺纹表面。
这两组加工表面之间有着一定的位置要求,主要是:
(1)Φ
mm花键孔与Φ
mm二孔中心联线的垂直度公差为100:
0.2;
(2)Φ39mm二孔外端面对Φ39mm孔垂直度公差为0.1mm;
(3)Φ
mm花键槽宽中心线与Φ39mm中心线偏转角度公差为2°。
由以上分析可知,对于这两组加工表面而言,可以先加工其中一组表面,然后借助于专用夹具加工另一组表面,并且保证它们之间的位置精确要求。
2.3.5表面处理内容及作用
由于零件受正反向冲击性载荷,容易疲劳破坏,所以采用表面喷砂处理,提高表面硬度,还可以在零件表面造成残余压应力,以抵消部分工作时产生的拉应力,从而提高疲劳极限。
第三章工艺规程设计
将工件在各个机加工工序中所采用的加工方法、应达到的加工要求、所需要的工装设备、具体的操作规范等用文件的形式详细地规定下来,即形成了零件机加工工艺规程。
它既是指导零件生产的技术文件,也是新建或扩建零件机加工厂房的主要依据,同时也是现有生产方法和技术的总结。
加工工艺规程是机械制造厂的最主要的技术文件之一。
将工艺规程内容填入一定格式的卡片即成为生产准备和施工依据的工艺文件。
常用的有机械加工工艺过程卡片、机械加工工艺卡片、机械加工工序卡片。
3.1生产过程与工艺过程
3.1.1生产过程
生产过程是指把原材料(半成品)转变为成品的全过程。
机械产品的生产过程,一般包括:
①生产与技术的准备,如工艺设计和专用工艺装备的设计和制造、生产计划的编制,生产资料的准备;②毛坯的制造,如铸造、锻造、冲压等;③零件的加工,如切削加工、热处理、表面处理等;④产品的装配,如总装,部装、调试检验和油漆等;⑤生产的服务,如原材料、外购件和工具的供应、运输、保管等。
机械产品的生产过程一般比较复杂,目前很多产品往往不是在一个工厂内单独生产,而是由许多专业工厂共同完成的。
例如:
飞机制造工厂就需要用到许多其他工厂的产品(如发动机、电器设备、仪表等),相互协作共同完成一架飞机的生产过程。
因此,生产过程即可以指整台机器的制造过程,也可以是某一零部件的制造过程。
3.1.2工艺过程
工艺过程是指在生产过程中改变生产对象的形状、尺寸、相对位置和性质等,使其成为成品或半成品的过程。
如毛坯的制造,机械加工、热处理、装配等均为工艺过程。
在工艺过程中,若用机械加工的方法直接改变生产对象的形状、尺寸和表面质量,使之成为合格零件的工艺过程,称为机械加工工艺过程。
同样,将加工好的零件装配成机器使之达到所要求的装配精度并获得预定技术性能的工艺过程,称为装配工艺过程。
机械加工工艺过程和装配工艺过程是机械制造工艺学研究的两项主要内容。
3.2机械加工工艺过程的组成
机械加工工艺过程是由一个或若干个顺序排列的工序组成的,而工序又可分为若干个安装、工位、工步和走刀,毛坯就是依次通过这些工序的加工而变成为成品的。
3.2.1工序
工序是指一个或一组工人,在一个工作地点对一个或同时对几个工件所连续完成的那一部分工艺过程。
区分工序的主要依据,是工作地点(或设备)是否变动和完成的那部分工艺内容是否连续。
如图4.1所示的零件,孔1需要进行钻孔和铰孔,如果一批工件中,每个工件都是在一台机床上依次地先钻孔,而后铰孔,则钻孔和铰孔就构成一个工序。
如果将整批工件都是先进行钻孔,然后整批工件再进行铰孔,这样钻孔和铰孔就分成两个工序了。
工序不仅是组成工艺过程的基本单元,也是制订工时定额,配备工人,安排作业和进行质量检验的依据。
通常把仅列出主要工序名称的简略工艺过程称为工艺路线。
3.2.2安装与工位
工件在加工前,在机床或夹具上先占据一正确位置(定位),然后再夹紧的过程称为装夹。
工件(或装配单元)经一次装夹后所完成的那一部分工艺内容称为安装。
在一道工序中可以有一个或多个安装。
工件加工中应尽量减少装夹次数,因为多一次装夹就多一次装夹误差,而且增加了辅助时间。
因此生产中常用各种回转工作台、回转夹具或移动夹具等,以便在工件一次装夹后,可使其处于不同的位置加工。
为完成—定的工序内容,一次装夹工件后,工件(或装配单元)与夹具或设备的可动部分一起相对刀具或设备固定部分所占据的每一个位置,称为工位。
图4.2所示为一种利用回转工作台在—次装夹后顺序完成装卸工件、钻孔,扩孔和铰孔四个工位加工的实例。
3.2.3工步与走刀
(1)工步工步是指被加工表面(或装配时的连接表面)和切削(或装配)工具不变的情况下所连续完成的那一部分工序。
一个工序可以包括几个工步,也可以只有一个工步。
一般来说,构成工步的任一要素(加工表面、刀具及加工连续性)改变后,即成为一个新工步。
但下面指出的情况应视为一个工步。
①对于那些一次装夹中连续进行的若干相同的工步应视为一个工步。
如图4.1所示,两孔1的加工,可以作为一个工步。
②为了提高生产率,有时用几把刀具同时加工一个或几个表面,此时也应视为一个工步。
称为复合工步.
(2)走刀在一个工步内,若被加工表面切去的金属层很厚,需分几次切削,则每进行一次切削就是一次走刀。
一个工步可以包括一次走刀或几次走刀。
3.3制定零件工艺规程的原则和技术要求
3.3.1工艺规程的设计原则
工艺规程设计必须遵循以下原则:
(1)所设计的工艺规程必须保证机器零件的加工质量和机器的装配质量,达到设计图样上规定的各项技术要求。
(2)工艺过程应具有较高的生产效率,使产品能尽快投放市场。
(3)尽量降低制造成本。
(4)注意减轻工人的劳动强度,保证生产安全。
3.3.2工艺规程的作用
(1)工艺规程是工厂进行生产准备工作的主要依据。
(2)工艺规程是企业组织生产的指导性文件。
(3)工艺规程是创建和扩建机械制造厂(或车间)的重要技术文件。
3.3.3工艺规程设计所需原始材料
设计工艺规程必须具备以下原始材料:
(1)产品装配图、零件图。
(2)产品验收质量标准。
(3)产品的年生产纲领。
(4)毛坯材料与毛坯生产条件。
(5)制造厂的生产条件,包括机床设备和工艺设备的规格、性能和当前的技术状态,工人的技术水平,工厂自制工艺装备的能力以及工厂供电、供气的能力等有关资料。
(6)工艺规程的设计、工艺装备设计所用设计手册和相关标准。
3.3.4工艺规程设计的步骤及内容
(1)分析零件图和产品装配图。
设计工艺规程时,首先应分析零件图所在部件所在零件在部件或总成的装配图。
(2)对零件图和装配图进行工艺审查。
(3)由产品的年生产纲领和产品自身特性研究确定零件生产类型。
(4)确定毛坯。
提高毛坯制造质量,可以减少机械加工劳动量,降低机械加工成本。
(5)拟定工艺路线。
(6)确定各工序所用机床设备和工艺设备(含刀具、夹具、量具、辅助等),对需要改装或重新设计的专用工艺装备要提出设计任务书。
(7)确定各工序的加工余量,计算工序尺寸及公差。
(8)确定各工序的技术要求及检验方法。
(9)确定各工序的切削用量和工时定额。
(10)编制工艺文件。
3.3.5工艺要求
制定零件机械加工工艺过程是生产技术准备工作的一个重要组成部分。
一个零件可以采用不同的工艺过程制造出来,但正确与合理的工艺过程应满足以下基本要求:
(1)保证产品的质量符合图纸和技术要求条件所规定的要求;
(2)保证提高生产率和改善劳动条件;
(3)保证经济性的合理。
3.3.6技术依据
(1).产品零件图和装配图,技术条件;
(2).毛坯生产和供应条件;
(3).年生产纲领
(4).本车间生产条件(包括设备,工人技术等级,劳动场合条件等);
(5).工艺技术条件,手册等。
3.4生产类型的确定
计算零件生产纲领的公式:
N=Q*n(1+&%)(1+β%)
其中:
Q=5000辆/年(产品的年产量)
n=1件/辆(每辆汽车该零件的数量)
&=4(零件的备品率)
β=1(零件的废品率)
则N=5000x1x(1+4%)x(1+1%)=5252(件)
根据生产纲领确定该零件为成批生产。
3.5确定毛坯的制造形式
零件材料为45钢。
考虑到汽车在运行中要经常加速及正、反向行驶,零件在工作过程中则经常承受交变载荷及冲击性载荷,因此应该选用锻件,以使金属纤维不被切断,保证零件工作可靠。
由于零件年产量为5252件,已达大批生产的水平,而且零件的轮廓尺寸不大,故可采用模锻成型。
这对提高生产率、保证加工质量也是有利的。
模锻毛坯具有以下特点:
1.其轮廓尺寸接近零件的外形尺寸,加工余量及材料消耗均大量减少;
2.其制造周期短,生产率高,保证产品质量。
3.6制定工艺路线及方法
3.6.1加工方法的选择
零件各表面加工方法的选择,不但影响加工质量,而且也要影响生产率和成本。
同一表面的加工可以有不同的加工方法,这取决于表面形状,尺寸,精度,粗糙度及零件的整体构型等因素。
主要加工面的加工方法选择:
(1)两个Φ
mm孔及其倒角可选用加工方案如下:
a)该零件的批量不是很大,考虑到经济性,不适用于钻-拉方案
b)该零件除上述因素外,尺寸公差及粗糙度要求均不是很高,因此只需采用钻-镗方案。
(2)尺寸为
mm的两个与孔Φ
mm相垂直的平面根据零件外形及尺寸的要求,选用粗铣-磨得方案
(3)Φ50mm花键孔因孔径不大,所以不采用先车后拉,而采用钻-扩-拉方案。
(4)Φ65mm外圆和M60x1外螺纹表面均采用车削即可达到零件图纸的要求
3.6.2基准的选择
基面选择是工艺规程设计中的重要工作之一。
基面选择得正确与合理,可以使加工质量得到保证,生产率得以提高。
否则,加工工艺过程中会问题百出,更有甚者,还会造成零件大批报废,使生产无法正常进行。
粗基准的选择
对于一般的轴类零件而言,以外圆作为粗基准是完全合理的。
但对本零件来说,
如果以Φ65mm外圆(或Φ62mm外圆)表面作基准(四点定位),则可能造成这一组内外圆柱表面与零件的叉部外形不对称。
按照有关粗基准的选择原则(即当零件有不加工表面时,应以这些不加工表面作粗基准;若零件有若干个不加工表面时,则应以与加工表面要求相对位置精度较高的不加工表面作为粗基准),现选择叉部两个Φ
mm孔的不加工外轮廓表面作为粗基准,利用一组共两个短V形块支承这两个Φ
mm的外轮廓作主要定位面,以消除
四个自由度,再用一对自动