推荐CA6140车床后托架加工工艺及夹具设计a 精品.docx
《推荐CA6140车床后托架加工工艺及夹具设计a 精品.docx》由会员分享,可在线阅读,更多相关《推荐CA6140车床后托架加工工艺及夹具设计a 精品.docx(25页珍藏版)》请在冰豆网上搜索。
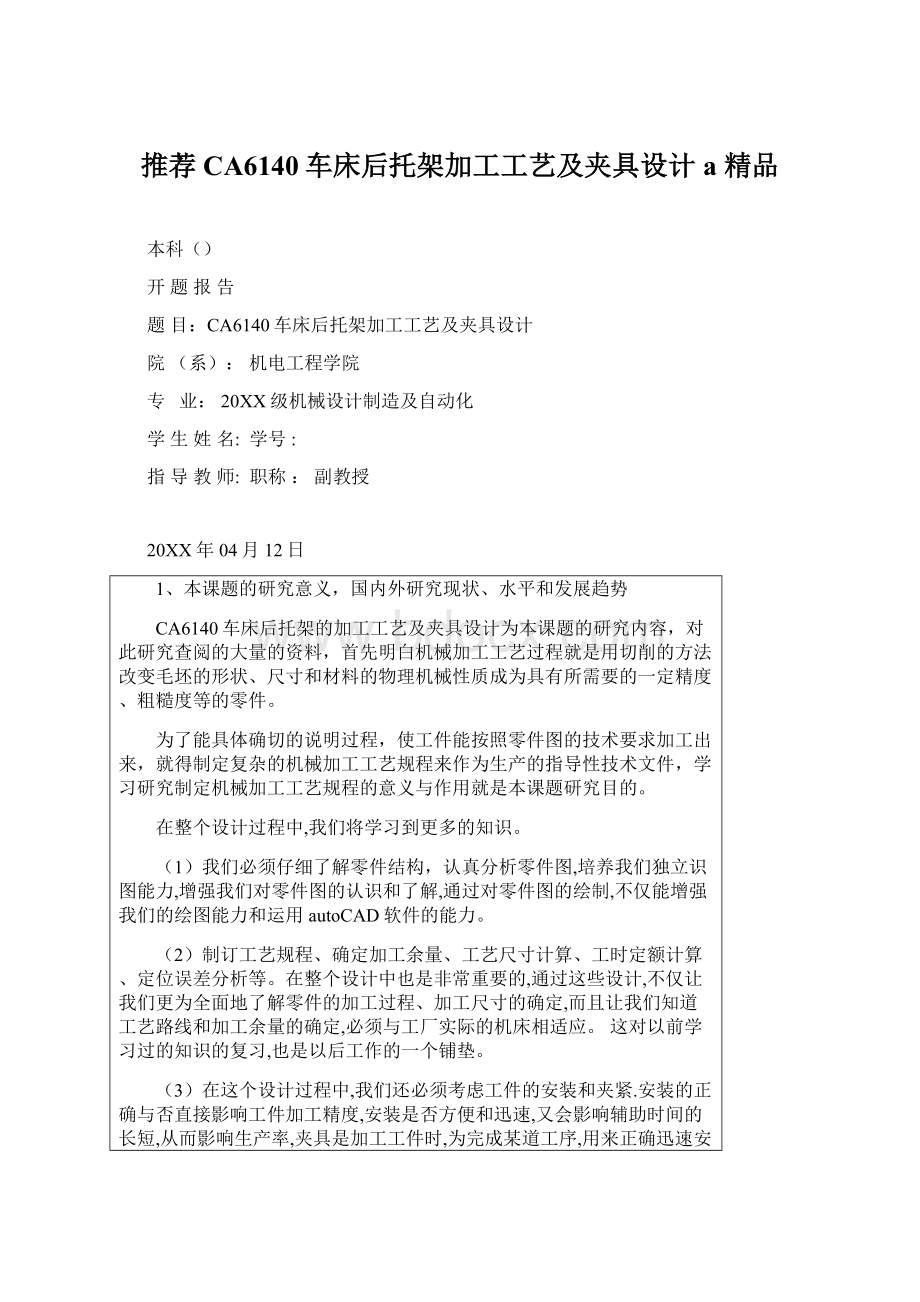
推荐CA6140车床后托架加工工艺及夹具设计a精品
本科()
开题报告
题目:
CA6140车床后托架加工工艺及夹具设计
院(系):
机电工程学院
专业:
20XX级机械设计制造及自动化
学生姓名:
学号:
指导教师:
职称:
副教授
20XX年04月12日
1、本课题的研究意义,国内外研究现状、水平和发展趋势
CA6140车床后托架的加工工艺及夹具设计为本课题的研究内容,对此研究查阅的大量的资料,首先明白机械加工工艺过程就是用切削的方法改变毛坯的形状、尺寸和材料的物理机械性质成为具有所需要的一定精度、粗糙度等的零件。
为了能具体确切的说明过程,使工件能按照零件图的技术要求加工出来,就得制定复杂的机械加工工艺规程来作为生产的指导性技术文件,学习研究制定机械加工工艺规程的意义与作用就是本课题研究目的。
在整个设计过程中,我们将学习到更多的知识。
(1)我们必须仔细了解零件结构,认真分析零件图,培养我们独立识图能力,增强我们对零件图的认识和了解,通过对零件图的绘制,不仅能增强我们的绘图能力和运用autoCAD软件的能力。
(2)制订工艺规程、确定加工余量、工艺尺寸计算、工时定额计算、定位误差分析等。
在整个设计中也是非常重要的,通过这些设计,不仅让我们更为全面地了解零件的加工过程、加工尺寸的确定,而且让我们知道工艺路线和加工余量的确定,必须与工厂实际的机床相适应。
这对以前学习过的知识的复习,也是以后工作的一个铺垫。
(3)在这个设计过程中,我们还必须考虑工件的安装和夹紧.安装的正确与否直接影响工件加工精度,安装是否方便和迅速,又会影响辅助时间的长短,从而影响生产率,夹具是加工工件时,为完成某道工序,用来正确迅速安装工件的装置.它对保证加工精度、提高生产率和减轻工人劳动量有很大作用。
这是整个设计的重点,也是一个难点
近年来,机械制造工艺有着飞速的发展。
比如,应用人工智能选择零件的工艺规程。
因为特种加工的微观物理过程非常复杂,往往涉及电磁场、热力学、流体力学、电化学等诸多领域,其加工机理的理论研究极其困难,通常很难用简单的解析式来表达。
近年来,虽然各国学者采用各种理论对不同的特种加工技术进行了深入的研究,并取得了卓越的理论成就,但离定量的实际应用尚有一定的距离。
然而采用每一种特种加工方法所获得的加工精度和表面质量与加工条件参数间都有其规律。
因此,目前常采用研究传统切削加工机理的实验统计方法来了解特种加工的工艺规律,以便实际应用,但还缺乏系统性。
受其限制,目前特种加工的工艺参数只能凭经验选取,还难以实现最优化和自动化,例如,电火花成形电极的沉入式加工工艺,它在占电火花成形机床总数95%以上的非数控电火花成形加工机床和较大尺寸的模具型腔加工中得到广泛应用。
虽然已有学者对其CAD、CAPP和CAM原理开展了一些研究,并取得了一些成果,但由于工艺数据的缺乏,仍未有成熟的商品化的CAD/CAM系统问世。
通叉零件加工
完成图所示拨叉零件加工。
图1拨叉
一、分析零件工艺结构性;
CA6140车床的拨叉。
它位于车床变速机构中,主要起换档,使主轴回转运动按照工作者的要求工作,获得所需的速度和扭矩的作用。
通过上方的力拨动下方的齿轮变速。
两件零件铸为一体,加工时分开。
(1)以φ14为中心的加工表面
这一组加工表面包括:
φ14的孔,以及其上下端面,上端面与孔有位置要求
(2)以φ40为中心的加工表面
这一组加工表面包括:
φ40的孔,以及其上下两个端面。
这两组表面有一定的位置度要求,即φ40的孔上下两个端面与φ14的孔有垂直度要求。
由上面分析可知,加工时应先加工一组表面,再以这组加工后表面为基准加工另外一组。
二、选用毛坯或明确来料状况;
零件材料为ZG45。
考虑零件在机床运行过程中所受冲击不大,零件结构又比较简单,故选择铸件毛坯。
有的采用HT200
三、基面的选择
基面选择是工艺规程设计中的重要工作之一。
基面选择得正确与合理可以使加工质量得到保证,生产率得以提高。
否则,加工工艺过程中回问题百出,更有甚者,还会造成零件的大批报废,是生产无法正常进行。
(1)粗基准的选择。
对于零件而言,尽可能选择不加工表面为粗基准。
而对有若干个不加工表面的工件,则应以与加工表面要求相对位置精度较高的不加工表面作粗基准。
根据这个基准选择原则,现选取φ14孔的不加工外轮廓表面作为粗基准,利用一组共两块V形块支承这两个φ25作主要定位面,限制5个自由度,再以一个销钉限制最后1个自由度,达到完全定位,然后进行铣削
(2)精基准的选择。
主要应该考虑基准重合的问题。
当设计基准与工序基准不重合时,应该进行尺寸换算。
四、制订工艺路线
制定工艺路线得出发点,应当是使零件的几何形状、尺寸精度及位置精度等技术要求能得到合理的保证,在生产纲领已确定的情况下,可以考虑采用万能性机床配以专用工卡具,并尽量使工序集中来提高生产率。
除此之外,还应当考虑经济效果,以便使生产成本尽量下降。
工序一以φ5外圆为粗基准,粗铣φ14孔下端面。
工序二精铣φ14孔上下端面。
工序三以φ14孔上端面为精基准,钻、扩、铰、精铰φ14孔,保证垂直度误差不超过0.05mm,孔的精度达到IT7。
叉零件加工
完成图所示拨叉零件加工。
图1拨叉
一、分析零件工艺结构性;
CA6140车床的拨叉。
它位于车床变速机构中,主要起换档,使主轴回转运动按照工作者的要求工作,获得所需的速度和扭矩的作用。
通过上方的力拨动下方的齿轮变速。
两件零件铸为一体,加工时分开。
(1)以φ14为中心的加工表面
这一组加工表面包括:
φ14的孔,以及其上下端面,上端面与孔有位置要求
(2)以φ40为中心的加工表面
这一组加工表面包括:
φ40的孔,以及其上下两个端面。
这两组表面有一定的位置度要求,即φ40的孔上下两个端面与φ14的孔有垂直度要求。
由上面分析可知,加工时应先加工一组表面,再以这组加工后表面为基准加工另外一组。
二、选用毛坯或明确来料状况;
零件材料为ZG45。
考虑零件在机床运行过程中所受冲击不大,零件结构又比较简单,故选择铸件毛坯。
有的采用HT200
三、基面的选择
基面选择是工艺规程设计中的重要工作之一。
基面选择得正确与合理可以使加工质量得到保证,生产率得以提高。
否则,加工工艺过程中回问题百出,更有甚者,还会造成零件的大批报废,是生产无法正常进行。
(1)粗基准的选择。
对于零件而言,尽可能选择不加工表面为粗基准。
而对有若干个不加工表面的工件,则应以与加工表面要求相对位置精度较高的不加工表面作粗基准。
根据这个基准选择原则,现选取φ14孔的不加工外轮廓表面作为粗基准,利用一组共两块V形块支承这两个φ25作主要定位面,限制5个自由度,再以一个销钉限制最后1个自由度,达到完全定位,然后进行铣削
(2)精基准的选择。
主要应该考虑基准重合的问题。
当设计基准与工序基准不重合时,应该进行尺寸换算。
四、制订工艺路线
制定工艺路线得出发点,应当是使零件的几何形状、尺寸精度及位置精度等技术要求能得到合理的保证,在生产纲领已确定的情况下,可以考虑采用万能性机床配以专用工卡具,并尽量使工序集中来提高生产率。
除此之外,还应当考虑经济效果,以便使生产成本尽量下降。
工序一以φ5外圆为粗基准,粗铣φ14孔下端面。
工序二精铣φ14孔上下端面。
工序三以φ14孔上端面为精基准,钻、扩、铰、精铰φ14孔,保证垂直度误差不超过0.05mm,孔的精度达到IT7。
叉零件加工
完成图所示拨叉零件加工。
图1拨叉
一、分析零件工艺结构性;
CA6140车床的拨叉。
它位于车床变速机构中,主要起换档,使主轴回转运动按照工作者的要求工作,获得所需的速度和扭矩的作用。
通过上方的力拨动下方的齿轮变速。
两件零件铸为一体,加工时分开。
(1)以φ14为中心的加工表面
这一组加工表面包括:
φ14的孔,以及其上下端面,上端面与孔有位置要求
(2)以φ40为中心的加工表面
这一组加工表面包括:
φ40的孔,以及其上下两个端面。
这两组表面有一定的位置度要求,即φ40的孔上下两个端面与φ14的孔有垂直度要求。
由上面分析可知,加工时应先加工一组表面,再以这组加工后表面为基准加工另外一组。
二、选用毛坯或明确来料状况;
零件材料为ZG45。
考虑零件在机床运行过程中所受冲击不大,零件结构又比较简单,故选择铸件毛坯。
有的采用HT200
三、基面的选择
基面选择是工艺规程设计中的重要工作之一。
基面选择得正确与合理可以使加工质量得到保证,生产率得以提高。
否则,加工工艺过程中回问题百出,更有甚者,还会造成零件的大批报废,是生产无法正常进行。
(1)粗基准的选择。
对于零件而言,尽可能选择不加工表面为粗基准。
而对有若干个不加工表面的工件,则应以与加工表面要求相对位置精度较高的不加工表面作粗基准。
根据这个基准选择原则,现选取φ14孔的不加工外轮廓表面作为粗基准,利用一组共两块V形块支承这两个φ25作主要定位面,限制5个自由度,再以一个销钉限制最后1个自由度,达到完全定位,然后进行铣削
(2)精基准的选择。
主要应该考虑基准重合的问题。
当设计基准与工序基准不重合时,应该进行尺寸换算。
四、制订工艺路线
制定工艺路线得出发点,应当是使零件的几何形状、尺寸精度及位置精度等技术要求能得到合理的保证,在生产纲领已确定的情况下,可以考虑采用万能性机床配以专用工卡具,并尽量使工序集中来提高生产率。
除此之外,还应当考虑经济效果,以便使生产成本尽量下降。
工序一以φ5外圆为粗基准,粗铣φ14孔下端面。
工序二精铣φ14孔上下端面。
工序三以φ14孔上端面为精基准,钻、扩、铰、精铰φ14孔,保证垂直度误差不超过0.05mm,孔的精度达到IT7。
叉零件加工
完成图所示拨叉零件加工。
图1拨叉
一、分析零件工艺结构性;
CA6140车床的拨叉。
它位于车床变速机构中,主要起换档,使主轴回转运动按照工作者的要求工作,获得所需的速度和扭矩的作用。
通过上方的力拨动下方的齿轮变速。
两件零件铸为一体,加工时分开。
(1)以φ14为中心的加工表面
这一组加工表面包括:
φ14的孔,以及其上下端面,上端面与孔有位置要求
(2)以φ40为中心的加工表面
这一组加工表面包括:
φ40的孔,以及其上下两个端面。
这两组表面有一定的位置度要求,即φ40的孔上下两个端面与φ14的孔有垂直度要求。
由上面分析可知,加工时应先加工一组表面,再以这组加工后表面为基准加工另外一组。
二、选用毛坯或明确来料状况;
零件材料为ZG45。
考虑零件在机床运行过程中所受冲击不大,零件结构又比较简单,故选择铸件毛坯。
有的采用HT200
三、基面的选择
基面选择是工艺规程设计中的重要工作之一。
基面选择得正确与合理可以使加工质量得到保证,生产率得以提高。
否则,加工工艺过程中回问题百出,更有甚者,还会造成零件的大批报废,是生产无法正常进行。
(1)粗基准的选择。
对于零件而言,尽可能选择不加工表面为粗基准。
而对有若干个不加工表面的工件,则应以与加工表面要求相对位置精度较高的不加工表面作粗基准。
根据这个基准选择原则,现选取φ14孔的不加工外轮廓表面作为粗基准,利用一组共两块V形块支承这两个φ25作主要定位面,限制5个自由度,再以一个销钉限制最后1个自由度,达到完全定位,然后进行铣削
(2)精基准的选择。
主要应该考虑基准重合的问题。
当设计基准与工序基准不重合时,应该进行尺寸换算。
四、制订工艺路线
制定工艺路线得出发点,应当是使零件的几何形状、尺寸精度及位置精度等技术要求能得到合理的保证,在生产纲领已确定的情况下,可以考虑采用万能性机床配以专用工卡具,并尽量使工序集中来提高生产率。
除此之外,还应当考虑经济效果,以便使生产成本尽量下降。
工序一以φ5外圆为粗基准,粗铣φ14孔下端面。
工序二精铣φ14孔上下端面。
工序三以φ14孔上端面为精基准,钻、扩、铰、精铰φ14孔,保证垂直度误差不超过0.05mm,孔的精度达到IT7。
常只能采用手工的方法或部分借助于CAD造型、部分生成复杂电极的三维型面数据。
随着模糊数学、神经元网络及专家系统等多种人工智能技术的成熟发展,人们开始尝试利用这一技术来建立加工效果和加工条件之间的定量化的精度、效率、经济性等实验模型,并得到了初步的成果。
因此,通过实验建模,将典型加工实例和加工经验作为知识存储起来,建立描述特种加工工艺规律的可扩展性开放系统的条件已经成熟。
并为进一步开展特种加工加工工艺过程的计算机模拟,应用人工智能选择零件的工艺规程和虚拟加工奠定基础。
同时,在机械加工过程中,夹具占有非常重要的地位,它可靠地保证了工件的加工精度,提高了加工效率,减轻了劳动的强度,夹具的设计过程中,应深入生产实际,(对工件的图纸,工艺文件,生产纲领等分析),精心调查研究,吸取国内外的先进技术,制订出合理的设计方案。
我们都知道减少停工检修期是提高生产力、使生产能力利用系数最大化的一项重要因素。
然而零件加工过程中的精确定位和装夹的重复精度也是改进效率和质量的关键。
譬如柔性加工中心的产生就是为了减少产品循环周期。
目前中国制造业发展迅猛,以前的我国制造业普遍使用刚性专机加工各种各样的零部件,导致改型和生产个零部件周期较长。
随着我国制造业发展和各种各种零件的需求与日俱增,加工设备和工艺也向着柔性化的方向转变。
加工装备的柔性概念和需求主要体现在对设备快速性和适应性的需求上,因此制造商不得不寻求柔性和产量之间的最佳组合。
当然,在满足了柔性的条件下、也有着不同的解决方案,如:
模块化、可变换化、可重新配置化、在线兼容性等。
不论采用哪种方案,使用高性能的液压夹具都显得尤为重要,现在,柔性专机、可重新配置的机床及专用加工中心的组合应用,使得发动机零件的加工变得越来越柔性化,具体情况取决于每个加工项目的产量配额
使用液压夹具的主要优势是能节省夹紧和松卸工件时所花的大量的时间。
有关统计资料表明液压夹紧相比机械夹紧节省90%~95%的时间,缩小了生产循环周期,从而增加了产量也就意味着降低了成本。
当加工一长型铝合金零件时,刀具通过时旋转油缸可快速让开,刀具通过后可快速复位。
液压夹具系统的第二项重要特点是可实现非常高的定位精度。
关键在于夹紧力在定位和夹紧过程中保持恒定不变。
从而确保了同一道工序下的加工质量一致性。
由于变形造成的废品率将会微乎其微
夹具是机械加工不可缺少的部件,在机床技术向高速、高效、精密、复合、智能、环保方向发展的带叉零件加工
完成图所示拨叉零件加工。
图1拨叉
一、分析零件工艺结构性;
CA6140车床的拨叉。
它位于车床变速机构中,主要起换档,使主轴回转运动按照工作者的要求工作,获得所需的速度和扭矩的作用。
通过上方的力拨动下方的齿轮变速。
两件零件铸为一体,加工时分开。
(1)以φ14为中心的加工表面
这一组加工表面包括:
φ14的孔,以及其上下端面,上端面与孔有位置要求
(2)以φ40为中心的加工表面
这一组加工表面包括:
φ40的孔,以及其上下两个端面。
这两组表面有一定的位置度要求,即φ40的孔上下两个端面与φ14的孔有垂直度要求。
由上面分析可知,加工时应先加工一组表面,再以这组加工后表面为基准加工另外一组。
二、选用毛坯或明确来料状况;
零件材料为ZG45。
考虑零件在机床运行过程中所受冲击不大,零件结构又比较简单,故选择铸件毛坯。
有的采用HT200
三、基面的选择
基面选择是工艺规程设计中的重要工作之一。
基面选择得正确与合理可以使加工质量得到保证,生产率得以提高。
否则,加工工艺过程中回问题百出,更有甚者,还会造成零件的大批报废,是生产无法正常进行。
(1)粗基准的选择。
对于零件而言,尽可能选择不加工表面为粗基准。
而对有若干个不加工表面的工件,则应以与加工表面要求相对位置精度较高的不加工表面作粗基准。
根据这个基准选择原则,现选取φ14孔的不加工外轮廓表面作为粗基准,利用一组共两块V形块支承这两个φ25作主要定位面,限制5个自由度,再以一个销钉限制最后1个自由度,达到完全定位,然后进行铣削
(2)精基准的选择。
主要应该考虑基准重合的问题。
当设计基准与工序基准不重合时,应该进行尺寸换算。
四、制订工艺路线
制定工艺路线得出发点,应当是使零件的几何形状、尺寸精度及位置精度等技术要求能得到合理的保证,在生产纲领已确定的情况下,可以考虑采用万能性机床配以专用工卡具,并尽量使工序集中来提高生产率。
除此之外,还应当考虑经济效果,以便使生产成本尽量下降。
工序一以φ5外圆为粗基准,粗铣φ14孔下端面。
工序二精铣φ14孔上下端面。
工序三以φ14孔上端面为精基准,钻、扩、铰、精铰φ14孔,保证垂直度误差不超过0.05mm,孔的精度达到IT7。
叉零件加工
完成图所示拨叉零件加工。
图1拨叉
一、分析零件工艺结构性;
CA6140车床的拨叉。
它位于车床变速机构中,主要起换档,使主轴回转运动按照工作者的要求工作,获得所需的速度和扭矩的作用。
通过上方的力拨动下方的齿轮变速。
两件零件铸为一体,加工时分开。
(1)以φ14为中心的加工表面
这一组加工表面包括:
φ14的孔,以及其上下端面,上端面与孔有位置要求
(2)以φ40为中心的加工表面
这一组加工表面包括:
φ40的孔,以及其上下两个端面。
这两组表面有一定的位置度要求,即φ40的孔上下两个端面与φ14的孔有垂直度要求。
由上面分析可知,加工时应先加工一组表面,再以这组加工后表面为基准加工另外一组。
二、选用毛坯或明确来料状况;
零件材料为ZG45。
考虑零件在机床运行过程中所受冲击不大,零件结构又比较简单,故选择铸件毛坯。
有的采用HT200
三、基面的选择
基面选择是工艺规程设计中的重要工作之一。
基面选择得正确与合理可以使加工质量得到保证,生产率得以提高。
否则,加工工艺过程中回问题百出,更有甚者,还会造成零件的大批报废,是生产无法正常进行。
(1)粗基准的选择。
对于零件而言,尽可能选择不加工表面为粗基准。
而对有若干个不加工表面的工件,则应以与加工表面要求相对位置精度较高的不加工表面作粗基准。
根据这个基准选择原则,现选取φ14孔的不加工外轮廓表面作为粗基准,利用一组共两块V形块支承这两个φ25作主要定位面,限制5个自由度,再以一个销钉限制最后1个自由度,达到完全定位,然后进行铣削
(2)精基准的选择。
主要应该考虑基准重合的问题。
当设计基准与工序基准不重合时,应该进行尺寸换算。
四、制订工艺路线
制定工艺路线得出发点,应当是使零件的几何形状、尺寸精度及位置精度等技术要求能得到合理的保证,在生产纲领已确定的情况下,可以考虑采用万能性机床配以专用工卡具,并尽量使工序集中来提高生产率。
除此之外,还应当考虑经济效果,以便使生产成本尽量下降。
工序一以φ5外圆为粗基准,粗铣φ14孔下端面。
工序二精铣φ14孔上下端面。
工序三以φ14孔上端面为精基准,钻、扩、铰、精铰φ14孔,保证垂直度误差不超过0.05mm,孔的精度达到IT7。
叉零件加工
完成图所示拨叉零件加工。
图1拨叉
一、分析零件工艺结构性;
CA6140车床的拨叉。
它位于车床变速机构中,主要起换档,使主轴回转运动按照工作者的要求工作,获得所需的速度和扭矩的作用。
通过上方的力拨动下方的齿轮变速。
两件零件铸为一体,加工时分开。
(1)以φ14为中心的加工表面
这一组加工表面包括:
φ14的孔,以及其上下端面,上端面与孔有位置要求
(2)以φ40为中心的加工表面
这一组加工表面包括:
φ40的孔,以及其上下两个端面。
这两组表面有一定的位置度要求,即φ40的孔上下两个端面与φ14的孔有垂直度要求。
由上面分析可知,加工时应先加工一组表面,再以这组加工后表面为基准加工另外一组。
二、选用毛坯或明确来料状况;
零件材料为ZG45。
考虑零件在机床运行过程中所受冲击不大,零件结构又比较简单,故选择铸件毛坯。
有的采用HT200
三、基面的选择
基面选择是工艺规程设计中的重要工作之一。
基面选择得正确与合理可以使加工质量得到保证,生产率得以提高。
否则,加工工艺过程中回问题百出,更有甚者,还会造成零件的大批报废,是生产无法正常进行。
(1)粗基准的选择。
对于零件而言,尽可能选择不加工表面为粗基准。
而对有若干个不加工表面的工件,则应以与加工表面要求相对位置精度较高的不加工表面作粗基准。
根据这个基准选择原则,现选取φ14孔的不加工外轮廓表面作为粗基准,利用一组共两块V形块支承这两个φ25作主要定位面,限制5个自由度,再以一个销钉限制最后1个自由度,达到完全定位,然后进行铣削
(2)精基准的选择。
主要应该考虑基准重合的问题。
当设计基准与工序基准不重合时,应该进行尺寸换算。
四、制订工艺路线
制定工艺路线得出发点,应当是使零件的几何形状、尺寸精度及位置精度等技术要求能得到合理的保证,在生产纲领已确定的情况下,可以考虑采用万能性机床配以专用工卡具,并尽量使工序集中来提高生产率。
除此之外,还应当考虑经济效果,以便使生产成本尽量下降。
工序一以φ5外圆为粗基准,粗铣φ14孔下端面。
工序二精铣φ14孔上下端面。
工序三以φ14孔上端面为精基准,钻、扩、铰、精铰φ14孔,保证垂直度误差不超过0.05mm,孔的精度达到IT7。
叉零件加工
完成图所示拨叉零件加工。
图1拨叉
一、分析零件工艺结构性;
CA6140车床的拨叉。
它位于车床变速机构中,主要起换档,使主轴回转运动按照工作者的要求工作,获得所需的速度和扭矩的作用。
通过上方的力拨动下方的齿轮变速。
两件零件铸为一体,加工时分开。
(1)以φ14为中心的加工表面
这一组加工表面包括:
φ14的孔,以及其上下端面,上端面与孔有位置要求
(2)以φ40为中心的加工表面
这一组加工表面包括:
φ40的孔,以及其上下两个端面。
这两组表面有一定的位置度要求,即φ40的孔上下两个端面与φ14的孔有垂直度要求。
由上面分析可知,加工时应先加工一组表面,再以这组加工后表面为基准加工另外一组。
二、选用毛坯或明确来料状况;
零件材料为ZG45。
考虑零件在机床运行过程中所受冲击不大,零件结构又比较简单,故选择铸件毛坯。
有的采用HT200
三、基面的选择
基面选择是工艺规程设计中的重要工作之一。
基面选择得正确与合理可以使加工质量得到保证,生产率得以提高。
否则,加工工艺过程中回问题百出,更有甚者,还会造成零件的大批报废,是生产无法正常进行。
(1)粗基准的选择。
对于零件而言,尽可能选择不加工表面为粗基准。
而对有若干个不加工表面的工件,则应以与加工表面要求相对位置精度较高的不加工表面作粗基准。
根据这个基准选择原则,现选取φ14孔的不加工外轮廓表面作为粗基准,利用一组共两块V形块支承这两个φ25作主要定位面,限制5个自由度,再以一个销钉限制最后1个自由度,达到完全定位,然后进行铣削
(2)精基准的选择。
主要应该考虑基准重合的问题。
当设计基准与工序基准不重合时,应该进行尺寸换算。
四、制订工艺路线
制定工艺路线得出发点,应当是使零件的几何形状、尺寸精度及位置精度等技术要求能得到合理的保证,在生产纲领已确定的情况下,可以考虑采用万能性机床配以专用工卡具,并尽量使工序集中来提高生产率。
除此之外,还应当考虑经济效果,以便使生产成本尽量下降。
工序一以φ5外圆为粗基准,粗铣φ14孔下端面。
工序二精铣φ14孔上下端面。
工序三以φ14孔上端面为精基准,钻、扩、铰、精铰φ14孔,保证垂直度误差不超过0.05mm,孔的精度达到IT7。
叉零件加工
完成图所示拨叉零件加工。
图1拨叉
一、分析零件工艺结构性;
CA6140车床的拨叉。
它位于车床变速机构中,主要起换档,使主轴回转运动按照