烧结配料知识.docx
《烧结配料知识.docx》由会员分享,可在线阅读,更多相关《烧结配料知识.docx(14页珍藏版)》请在冰豆网上搜索。
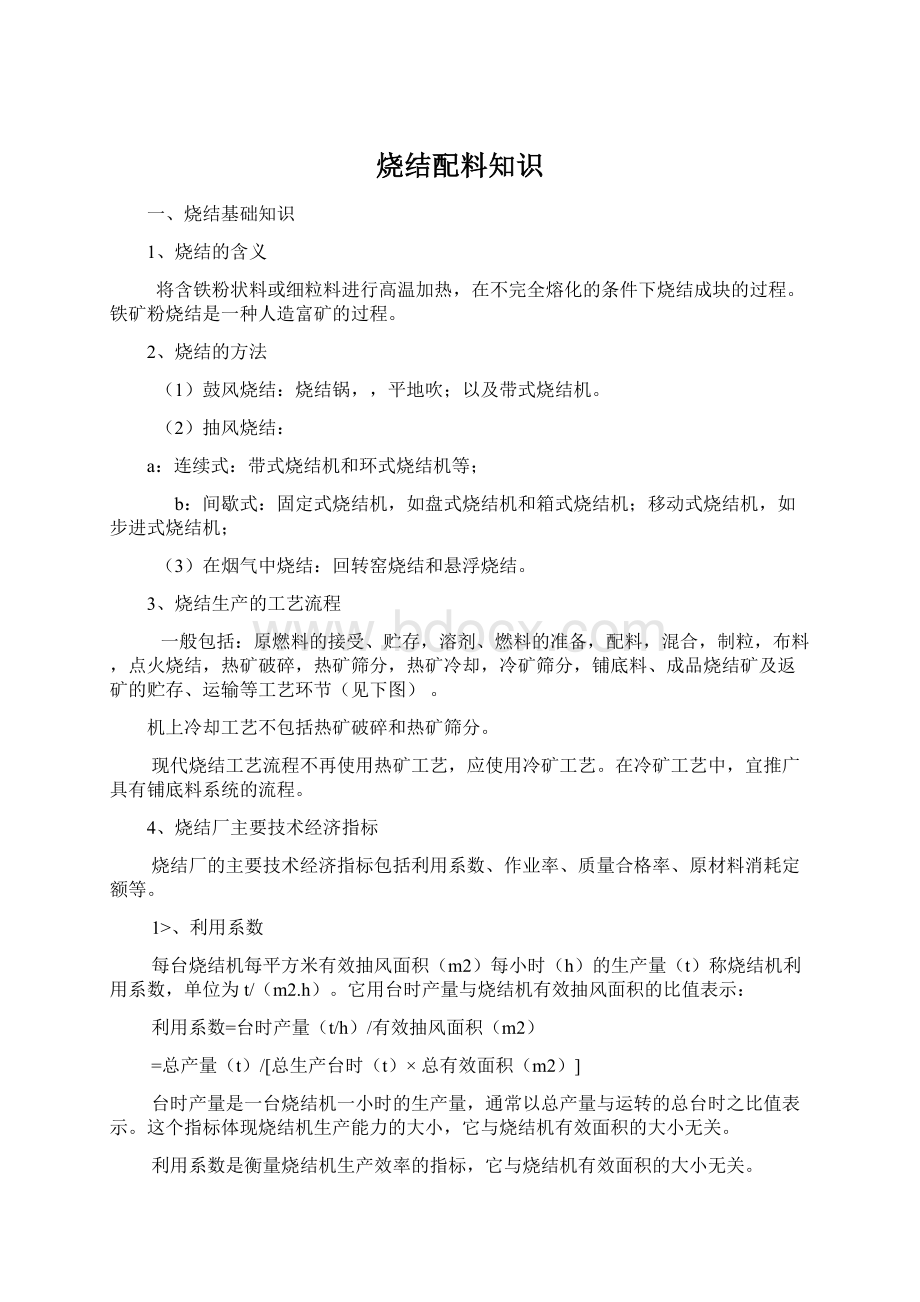
烧结配料知识
一、烧结基础知识
1、烧结的含义
将含铁粉状料或细粒料进行高温加热,在不完全熔化的条件下烧结成块的过程。
铁矿粉烧结是一种人造富矿的过程。
2、烧结的方法
(1)鼓风烧结:
烧结锅,,平地吹;以及带式烧结机。
(2)抽风烧结:
a:
连续式:
带式烧结机和环式烧结机等;
b:
间歇式:
固定式烧结机,如盘式烧结机和箱式烧结机;移动式烧结机,如步进式烧结机;
(3)在烟气中烧结:
回转窑烧结和悬浮烧结。
3、烧结生产的工艺流程
一般包括:
原燃料的接受、贮存,溶剂、燃料的准备,配料,混合,制粒,布料,点火烧结,热矿破碎,热矿筛分,热矿冷却,冷矿筛分,铺底料、成品烧结矿及返矿的贮存、运输等工艺环节(见下图) 。
机上冷却工艺不包括热矿破碎和热矿筛分。
现代烧结工艺流程不再使用热矿工艺,应使用冷矿工艺。
在冷矿工艺中,宜推广具有铺底料系统的流程。
4、烧结厂主要技术经济指标
烧结厂的主要技术经济指标包括利用系数、作业率、质量合格率、原材料消耗定额等。
1>、利用系数
每台烧结机每平方米有效抽风面积(m2)每小时(h)的生产量(t)称烧结机利用系数,单位为t/(m2.h)。
它用台时产量与烧结机有效抽风面积的比值表示:
利用系数=台时产量(t/h)/有效抽风面积(m2)
=总产量(t)/[总生产台时(t)× 总有效面积(m2)]
台时产量是一台烧结机一小时的生产量,通常以总产量与运转的总台时之比值表示。
这个指标体现烧结机生产能力的大小,它与烧结机有效面积的大小无关。
利用系数是衡量烧结机生产效率的指标,它与烧结机有效面积的大小无关。
2>、烧结机作业率
作业率是设备工作状况的一种表示方法,以运转时间占设备日历时间的百分数表示:
设备作业率=运转台时/日历台时× 100%
日历台时是个常数,每台烧结机一天的日历台时即为24台时。
它与台数、时间有关。
日历台时=台数× 24× 天数
事故率是指内部事故时间与运转时间的比值,以百分数表示:
事故率=事故台时/运转台时× 100%
设备完好率是衡量设备良好状况的指标。
按照完好设备的标准,进行定期检查。
设备完好率是全厂完好设备的台数与设备总台数的比值,用百分数表示:
设备完好率=完好设备台数/设备总台数× 100%
3>、质量合格率
烧结矿的化学成分和物理性能符合原冶金部YB/T421-92标准要求的叫烧结矿合格品,不符合的烧结矿叫出格品(见附件表1-1)。
根据部颁标准的规定,实际生产检验过程及工艺试验中出现的一部分未检验品和试验品,不参加质量合格率的计算。
因此:
质量合格率=(总产量-未验品量-试验品量-出格品量)/(总产量-未验品量-试验品量)× 100%
质量合格率是衡量烧结矿质量好坏的综合指标。
烧结矿合格品、一级品或出格品的判定根据其物理化学性能的检验结果而定,主要包括烧结矿全铁(TFe)、氧化亚铁(FeO)、硫(S)含量、碱度(CaO/SiO2)、转鼓指数(≥6.3mm)、粉末(< 5mm)等,有的厂还包括氧化镁(MgO)、氟(F)、磷(P)等。
一级品率=一级品量/合格品量× 100%
转鼓指数=检测粒度(≥5mm)的重量/试样重量×100%
烧结矿筛分指数=筛分后粒度(≤5mm)的重量/试样重量×100%
4>、烧结矿的原料、燃料、材料消耗定额
生产一吨烧结矿所消耗的原料、燃料、动力、材料等的数量叫消耗定额,包括含铁原料、熔剂料、燃料、煤气、重油、水、电、炉蓖条、胶带、破碎机锤头、润滑油、蒸气等。
5>、生产成本与加工费
生产成本是指生产一吨烧结矿所需的费用,由原料费及加工费两部分构成。
加工费是指生产一吨烧结矿所需的加工费用(不包括原料费)。
它包括辅助材料费(如燃料、润滑油、胶带、炉蓖条、水、动力费等),工人工资,车间经费(包括设备折旧费、维修费等)。
6>、劳动生产率
劳动生产率是指每人每年生产烧结矿的吨数。
这个指标反映工厂的管理水平和生产技术水平,它又称全员劳动生产率(全员包括工人和干部)。
另外,还有工人劳动生产率,即每个工人每年生产烧结矿的吨数。
配料知识
烧结成分的稳定性对高炉顺行、以及增铁节焦具有重大的意义,因此,搞好配料工作是高炉优质、高产、低耗的先决条件,是获得优质烧结矿的前提,烧结矿使用的原料种类繁多,物理化学性质各不相同。
为了合理综合利用国家资源,生产出符合高炉冶炼要求而且成分相对稳定的烧结矿,同时还要兼顾生产过程的要求,烧结厂必须根据本厂原料的供应情况及物理化学性质选择合适的原料,通过计算确定配料比,并严格按配比确定每条电子称皮下料量,经常进行重量检查(跑盘)及时调整。
所谓配料就是根据高炉对烧结矿的产品质量要求及原料的化学性质,将各种原料、熔剂、燃料、以及高炉炉尘、铁屑和热返矿等按一定比例进行配加的工序。
配料的目的是根据烧结过程的要求,将各种不同的含铁原料、溶剂和燃料进行准确的配料,以获得较高的生产率和理化性能稳定的优质烧结矿,符合高炉冶炼的要求。
目前国内常用的配料方法有两种,即容积配料法和重量配料法。
容积配料法是利用物料的堆比重,通过给料设备对物料容积进行控制,达到配加料所要求的添加比例的一种方法。
此法优点是设备简单,操作方便。
其缺点是物料的堆比重受物料水分、成分、粒度等影响。
所以,尽管闸门开口大小不变,若上述性质改变时,其给料量往往不同,造成配料误差。
重量配料法是按照物料重量进行配料的一种方法,该法是借助于电子皮带称和定量给料自动调节系统实现自动配料的。
优点是:
重量配料比容积配料更加精确,特别是对添加数量较少的原料,这一点更明显。
除这两种配料法外,化学成分配料是一种目前最为理想的配料方法,它采用先进的在线检测技术,随时测出原料混合料成分并输入微机进行分析、判断、调整,使烧结矿质量稳固在高水平。
国外对这种方法也处于开发阶段,我国的宝钢、首钢已具备开发这种水平的条件。
原燃料性质及其对烧结过程和质量的影响
1、含铁原料
精矿粉是含铁贫矿经过细磨选矿处理,除去了一部分脉石和杂质使含铁量提高的极细的矿粉。
在烧结生产过程中,除了精矿粉外,往往还添加一些其它的含铁原料(如高炉返矿、铁皮和富矿粉等),这样做有两个目的,一是为了增加烧结混合料成球核心,改善混合料的透气性,提高烧结机利用系数,降低烧结矿成本。
二是为了提高烧结矿的品位,为高炉顺行、高产创造条件。
返矿具有多孔的结构,含低熔点化合物,有利于烧结过程液相的生成,提高烧结矿的强度,有利于烧结料粒度的组成,改善透气性,提高烧结矿质量。
因此,返矿的配加量、返矿质量的好坏,直接影响烧结生产过程的进行。
2、熔剂
(1)熔剂的分类
熔剂可分为碱性熔剂、酸性熔剂和中性熔剂三类。
我国铁矿的脉石多以SiO2为主,所以普遍使用碱性熔剂。
碱性熔剂即含CaO和MgO高的熔剂。
常用的熔剂有:
石灰石(CaCO3)生石灰(CaO)、消石灰(Ca(OH)2)和白云石(主要是CaCO3和MgCO3)。
(2)烧结对熔剂的要求
碱性氧化物含量要高;S、P杂质要少;酸性氧化物含(SiO2+Al2O3 ) 越低越好,;粒度和水分适宜。
(3)配加熔剂的目的
烧结生产过程中配加熔剂的目的主要有三个;一是将高炉冶炼时高炉所配加的一部分或大部分熔剂和高炉中大部分化学反应转移到烧结过程中来进行,从而有利于高炉进一步提高冶炼强度和降低焦比;二是碱性熔剂中的CaO和MgO与烧结料中的氧化物及酸性脉石SiO2、Al2O3 等在高温作用下,生成低熔点的化合物,以改善烧结矿强度、冶金性和还原性;三是加入碱性熔剂,可提高烧结料的成球性和改善料层透气性,提高烧结矿质量和产量。
白灰也称生石灰,主要成分是CaO,其遇水即消化成消石灰(Ca(OH)2)后,在烧结料中起粘结剂的作用,增加了料的成球性,并提高了混合料成球后的强度,改善了烧结料的粒度组成,提高了料层的透气性。
其次,由于消石灰粒度极细,比表面积比消化前增大100倍左右,因此与混合料中其它成分能更好的接触,加快固液相反应,不仅加速烧结过程,而且防止游离CaO存在,而且它还可以均匀分布在烧结料中,有利于烧结过程化学反应的进行。
再次,白灰消化放出的热量,可以提高混合料料温。
从另一个方面来看,生石灰用量也不宜过多;
a、生石灰用量过多,烧结料会过分疏松,混合料堆密度下降,生球强度反而会变坏。
由于烧结速度过快,返矿率增加,产量降低。
另外,生石灰量过多,烧结料水分不易控制。
b、烧结前必须使生石灰全部消化,使用生石灰时必须相应增加混合前打水量,保证必要消化时间,使生石灰颗粒一般在一次混合机内松散开,绝大多数消化,生石灰粒度一般要小于3mm。
c、生石灰在配料前的运输和储运中,尽量避免受潮,以防止事先消化去CaO的作用。
d、生石灰不宜长途运输和皮带转运,极易产生粉尘,恶化劳动条件。
(4)、烧结料中加入石灰石对烧结矿质量的影响
a、CaO成分增加,其软化区间缩小,燃烧层厚度减薄,改善料层透气性。
b、石灰石的细粉比精矿粘结性好,有利于混合料成球,而较粗的部分本身就具有良好的透气性,可以改善烧结料透气性。
c、烧结过程中石灰石分解,放出CO2,起疏松料层作用,大大改善料层透气性。
通过石灰石的加入,使垂直燃烧速度增加,产量提高。
d、石灰石的加入量也不宜过多,如石灰石量过多成球条件变坏,由于透气性变好,机速加快,矿物结晶不完全。
另外,CaO过多易形成正硅酸钙体系液相,导致冷却时粉化碎裂,使烧结矿强度降低。
(5)、用消石灰来代替石灰石的好处
a、消石灰粒度很细,亲水性强,而且有粘性,大大改善烧结料透气性,提高小球强度。
b、消石灰比表面积大,增加混合料最大湿容量,可使烧结料过湿层有较好的透气性。
c、粒度细微的消石灰颗粒比粒度较粗的石灰石颗粒更易产生低熔点化合物,液相流动好,凝结成块,从而降低燃料用量和燃烧带阻力。
但消石灰用量也不宜过多,过多的消石灰使烧结料过于松散,烧结矿脆性大,强度下降,成品率下降。
3、烧结矿碱度
(1)碱度的分类
碱度是烧结矿的碱性氧化物与酸性氧化物百分比含量比值。
二元碱度R=Cao/SiO2;
三元碱度R=(CaO+MgO)/SiO2;
四元碱度R=(CaO+MgO)/(SiO2+Al2O3 )
烧结矿按R分为三种;普通烧结矿、自熔性烧结矿,高碱性烧结矿。
普通烧结矿又叫酸性烧结矿。
即烧结矿的碱度低于高炉炉渣的碱度,一般小于1.0,这种烧结矿在入炉冶炼时需加入一定数量的熔剂。
自熔性烧结矿的碱度等于或稍高于高炉炉渣的碱度,一般为1.2-1.5左右,其烧结矿在入炉冶炼时不需另加熔剂。
高碱度烧结矿又叫熔剂性烧结矿,其碱度高于高炉炉渣的碱度,一般都大于1.5。
其烧结矿在入炉冶炼时,可以代替部分或全部熔剂,常与富矿或酸性烧结矿、酸性球团矿配合使用。
(2)高碱度烧结矿的特点
因现在普遍生产的是高碱度烧结矿,就其特点做一概述;
a、高碱度烧结矿强度高,稳定性好,粒度均匀,粉末少。
b、高碱度烧结矿具有良好的还原性,这是因为高碱度烧结矿是以易还原的铁酸钙为主要液相;随碱度提高,烧结矿中FeO降低,还原性得到改善;高碱度烧结矿处于还原性最好的结构状态。
其中的磁铁矿晶粒细小且密集,并被铁酸钙包裹或溶蚀。
c、高碱度的烧结矿软化开始温度和软化终了温度均有所下降。
d、高碱度烧结矿含硫量有所提高,这是因为烧结料中的CaO有吸硫作用,形成CaS留于烧结矿中。
(3)烧结中配加白云石的目的
烧结料中加入白云石主要是为了提高烧结矿MgO含量从而提高烧结矿的质量(强度),并改善高炉炉渣的流动性。
4、影响烧结矿TFe高低和碱度高低的原因
(1)含铁原料品位不稳定
当品位高时,烧结矿的TFe升高,SiO2下降,CaO正常,R上升。
当品位低时,烧结矿的TFe降低,SiO2升高,CaO正常,R下降。
(2)熔剂下料量不稳定
下料量大,相当于配比高,SiO2稍低,烧结矿TFe下降,CaO上升,R上升。
下料量小,相当于配比代,SiO2稍高,烧结矿TFe上升,CaO下降,R下降。
(3)含铁原料下料不稳定
下料量大,铁上升,SiO2稍高,CaO下降,R下降。
下料量小,铁下降,SiO2稍低,CaO上升,R上升。
(4)熔剂中CaO不稳定
CaO高时,SiO2变动不大,R上升。
CaO低时,SiO2变动不大,R下降。
(5)熔剂水分变化,相当于配比或下料量变化
水分大,SiO2稍高,铁上升,CaO下降,R下降。
水分小,SiO2稍低,铁下降,CaO上升,R上升。
1烧结球团生产基本知识3
六、什么是球团矿?
它有何特点?
答:
球团矿是细精矿粉(-200目,即粒度0.074mm的矿粉占80%以上、比表面积在1500cm2/g以上)加入少量的添加剂混合后,在造球上加水,依靠毛细力和旋转运动的机械力造成直径8~16mm的生球,然后在焙烧设备上干燥,在高温氧化性气氛下Fe2O3再结晶的晶桥键固结成的品位高、强度好、粒度均匀的球状炼铁原料。
它有以下特点:
1、使用品位很高的精矿粉生产,酸性氧化球团矿的品位可达68%,SiO2在1%~2%;
2、无烧结矿具有的大气孔所有气孔都以微气孔形式存在,有利于气-固相还原;
3、FeO含量低(一般在1%左右),矿物主要是Fe2O3,还原性好;
4、冷强度好,每个球可耐2800~3600N(300~400kg·f)的压力粒度均匀,运输性能好;
5、自然堆角小在24°~27°,在高炉内布料易滚向炉子中心;
6、含硫很低,因为在强氧化性气氛下焙烧,可以去除原料中95~99%的硫;
7、具有还原膨胀的缺点,在有K2O、Na2O等催化的作用下会出现异常膨胀;
8、酸性氧化球团矿的软熔性能较差,即它的软化开始温度低,软熔温度区间窄,但它仍比天然富块矿的好,仍是合适炉料结构中高碱度烧结矿的最佳搭配料。
七、精矿粉是怎样成为8~16mm的生球的?
答:
精矿粉的成球是由其在自然状态下滴水成球的特性和在机械力作用下密集的能力造成的。
在造球机上成球的过程按下列3个阶段进行:
母球形成。
装入造球盘中的物料通常水分含量为8%~10%,处于比较松散的状态,各个矿粉颗粒为吸附水和薄膜水所覆盖,毛细水仅存在于各颗粒间的接触点上,其余空间为空气所充填,颗粒之间接触不紧密,薄膜水还不能起作用。
另外,由于毛细水数量太少,毛细孔过大,毛细压力小,颗粒间结合力较弱,不能成球,为此,须进行不均匀的点滴润湿,并通过机械力的作用,使部分颗粒接触得更紧密,造成更细的毛细孔和较大的毛细压力,将周围矿粒拉向水滴中心,形成较紧密的颗粒集合体,从而形成母球。
母球长大。
母球在造球盘上继续滚动,母球进一步压紧,内部毛细管变细,过剩的毛细水被挤到母球表面,这样过湿的母球靠毛细力作用将周围含水较少的矿粉粘结起来,使母球长大。
当母球达到所需要的粒度,必须向母球表面补充喷水。
但喷水量要适度,如果过大,颗粒完全为水所饱和而产生重力水,使颗粒脱离接触,瓦解母球,对造球极为不力。
生球压实。
仅靠毛细力结合起来的生球,强度不大。
为了提高生球强度,必须停止喷水,使生球在造球盘上滚动,将生球内部的毛细水全部挤出,为周围矿粉所吸收;同时使生球内的矿粉颗粒排列得更紧密,使薄膜水层有可能相互接触,形成众多颗粒共有的水化膜而加强结合力,从而使生球强度大大提高。
当生球达到一定粒度和密度后,由于造球盘的离心力作用,生球自动被抛出盘外。
从造球机出来的生球用瓷辊筛筛去粒度大于16mm和8mm的,生球抗压强度要达到15~20N/个球,落下强度(单个生球从0.5m高处落到钢板上反复跌落,直到生球破坏为止的次数)不4小于次,符合以上两个指标即是合格生球。
八、目前主要有哪几种球团焙烧方法?
答:
目前国内外焙烧球团矿的方法有3种:
竖炉焙烧;带式焙烧;链箅机-回转窑焙烧。
竖炉是最早采用的球团矿焙烧设备。
现代竖炉在顶部设有烘干床,焙烧室中央设有导风墙。
燃烧室内产生的高温气体从两侧喷入焙烧室向顶部运动,生球从上部均匀地铺在烘干床上被上升热气体干燥、预热,然后沿烘干床斜坡滑入焙烧室内焙烧固结,在出焙烧室后与从底部鼓进的冷风气相遇,得到冷却。
最后用排矿机排出竖炉。
竖炉的结构简单,对材质无特殊要求;缺点是单炉产量低,只适用于磁精粉球团焙烧,由于竖炉内气体流难于控制,焙烧不均匀造成球团矿质量也不均匀。
带式焙烧机是目前使用最广的焙烧方法。
带式焙烧的特点:
1、采用铺底料和铺边料以提高焙烧质量,同时保护台车延长台车寿命;2、采用鼓风和抽风干燥相结合以改善干燥过程,提高球团矿的质量;3、鼓风冷却球团矿,直接利用冷却带所得热空气助燃焙烧带燃料燃烧、以及干燥带使用;只将温度低含水分高的废气排入烟囱;5、适用于各种不同原料(赤铁矿浮选精粉、磁铁矿磁选精粉或混合粉)球团矿的焙烧。
九、国产球团与进口球团相比有何差距?
答:
1、比进口矿品位低3~5%、SiO2含量高3~4%;
2、我国球团矿的精矿粉粒度0.074mm(-200目)的只有60~80%,比表面积小,大部分在1000cm2/g左右,造球困难,靠多加膨润土来弥补,大部分厂家添加量在5%以上,而每多配加1%膨润土,就使球团矿的品位降低0.6%。
国外造球用精矿粉的比表面积达到1500~1700cm2/g,膨润土添加量在0.5%左右;
3、球团矿焙烧不均匀,尤其是用竖炉焙烧的球团矿;
4、部分竖炉生产的球团矿的强度差,FeO含量高,冶金性能差。
球团基础1
第一章绪论
第一节球团矿在钢铁工业中的地位及作用
钢铁工业的不断发展,使得其对炼铁原料的粒度、强度、化学成分及冶炼特性的要求日趋严格。
由于我国贫矿多,富矿少,直接炼铁入炉矿品位不够,所以必须进行铁矿粉造块,生产高品位的人造富矿,即烧结矿和球团矿。
球团矿作为良好的高炉炉料,具有品位高、强度好、易还原、粒度均匀等优点,而且酸性球团矿与高碱度烧结矿搭配,可以构成高炉合理的炉料结构,使高炉达到增产、节焦、提高经济效益的目的。
大力发展球团矿已成为钢铁企业的共识。
第二节球团的概念
球团是人造块状原料的一种方法,是一个将粉状物料变成物力性能和化学组成能够满足下一步加工要求的过程。
球团过程中物料不仅由于滚动成球和粒子密集而发生物理变化,如:
密度、空隙率、形状、大小和机械强度等变化,更重要的是发生了化学变化,如:
化学组成,还原性、膨胀性、高温还原软化性、低温还原粉化性、熔融性能等变化,使物料的冶金性能得到改善。
高炉对球团的要求:
无层状结构、断面均一、充分氧化、具有最大还原性。
第三节球团矿生产工艺简介
球团是较为广泛应用的造块工艺之一。
它与烧结生产工艺相比,具有下述特点:
(1)对原料要求严格,而且原料品种较单一。
一般用于球团生产的原料都是细磨精矿,比表面积大于1500~200cm2/g。
水分应低于适宜造球水分,不能太高;
(2)由于生球结构较紧密,且含水分较高,在突然遇高温时会产生破裂甚至爆裂,因此高温焙烧前必须设置干燥和预热工序;
(3)球团形状一致,粒度均匀,料层透气性好,因此采用带式焙烧机或链篦机—回转窑生产球团矿时,一般可使用低负压风机;
(4)大多数球团料中不含固体燃料,焙烧球团矿所需要的热量由液体或气体燃料燃烧后的热废气通过料层供热,热废气在球团料层中循环使用,因此热利用率较高。
球团生产应用较为普通的方法有竖炉球团法,带式焙烧机球团法和链篦机—回转窑球团法。
竖炉球团法是最早发展起来的,曾一度发展很快。
但随着钢铁工业的发展,要求球团工艺不仅能处理磁铁矿,而且能处理赤铁矿、褐铁矿及土状赤铁矿等。
另外高炉对球团矿的需求量不断增加,要求设备向大型化发展。
因此相继发展了带式焙烧机,链篦机—回转窑,环形焙烧炉等方法。
这些方法一直处于彼此相互竞争状态。
目前世界上用得最多的还是竖炉球团,带式焙烧机球团和链篦机—回转窑球团法。
第四节竖炉法焙烧球团矿
一、概述
竖炉是国外用来焙烧铁矿球团最早的设备。
它具有结构简单、材质无特殊要求、投少、热效率高,操作维修方便等优点,所以自美国伊利公司投产世界上第一座竖炉以,直到1960年竖炉生产的球团矿占全世界球团矿总产量的70%。
但是由于竖炉单炉量小,对原料适应性差,不能满足现代高炉对熟料的要求,因此在应用和发展上受到限。
自20世纪70年代以后国外除摩洛哥1972年扩建一个年产60万吨竖炉,1975年美国米德兰公司为阿根廷建立一个年产200万吨竖炉厂外,就再没有建竖炉了,所以竖炉生产的球团矿比例也就随之下降,1971年下降到18.1%,1976年进一步下降到13.3%,1980年下降到9%左右。
然而竖炉对于焙烧磁精矿,规模较小的球团厂仍具有一定的优势。
据不完全统计,国外竖炉球团厂共37家,计110多座竖炉,最高年产量曾达2700万吨,最大竖炉断面积为16m2左右.
国外竖炉普遍存在下述缺点:
(1)电耗高。
根据瑞典LKAB分析,每吨球团矿的电耗高达50KW/h。
电耗高的主要原因是竖炉料柱高,气流阻力大,主风机工作压力高。
加拿大格里菲什矿的15.62m2竖炉,风机压力为64247pa,伊利竖炉主风机压力为54936Pa。
(2)国外竖炉球团一般都采用高热值燃料油或天然气体,并只限制于焙烧磁铁精矿球团。
(3)鉴于竖炉本身的料仓式结构,排料时同一料面的球团矿下料速度不均匀,正对排料口中心下料快,而两边相应慢些,使球团矿在炉内停留时间不同,因而使球团矿焙烧固结不均匀。
2球团基础1
(4)国外竖炉一般采用横向布料线路布料,布料时间长而不均匀。
一座长6.4m,宽2.44m竖炉布料一次要140秒,布料机沿宽度方向要走8个来回。
我国竖炉球团起步较晚。
1968年济钢和承钢首先投产8m2竖炉,到1975年共建24座竖炉,但由于原、燃料条件的限制,投入生产的仅10座,正常生产的7座。
本钢于1987年9月投产一座16m2竖炉,这是目前世界上最大的竖炉。
济钢也于1988年1月又投产了10m2竖炉。
这两座竖炉的投产标志我国竖炉技术已进入了大型化发展阶段。
到1989年为止我国共有19座竖炉正常生产,除萍乡钢铁厂原料为褐铁矿外,其余均以磁铁矿为原料。
与国外竖炉相比,中国竖炉有以下特点:
炉内架有导风墙、干燥床;采用低真空度风机;低热值的高炉煤气及低焙烧温度操作。
二、竖炉球团工艺流程
(一)布料
竖炉是一种按逆流原则工作的热交换设备,其特点是在炉顶通过布料设备将生球装炉内,球以均匀的速度连续下降,燃烧室的热气体从喷火口进入炉内,热气体自下而上自上而下的生球进行热交换。
生球经过干燥、预热进入焙烧区,在焙烧区进行高温固反应,然后在炉子下部进行冷却和排出,整个过程是在竖炉内一次完成。
由此可知竖炉正常操作的最重要的先决条件,是炉料应具有良好的透气性。
为了保