企业制造工艺分析分析报告.docx
《企业制造工艺分析分析报告.docx》由会员分享,可在线阅读,更多相关《企业制造工艺分析分析报告.docx(11页珍藏版)》请在冰豆网上搜索。
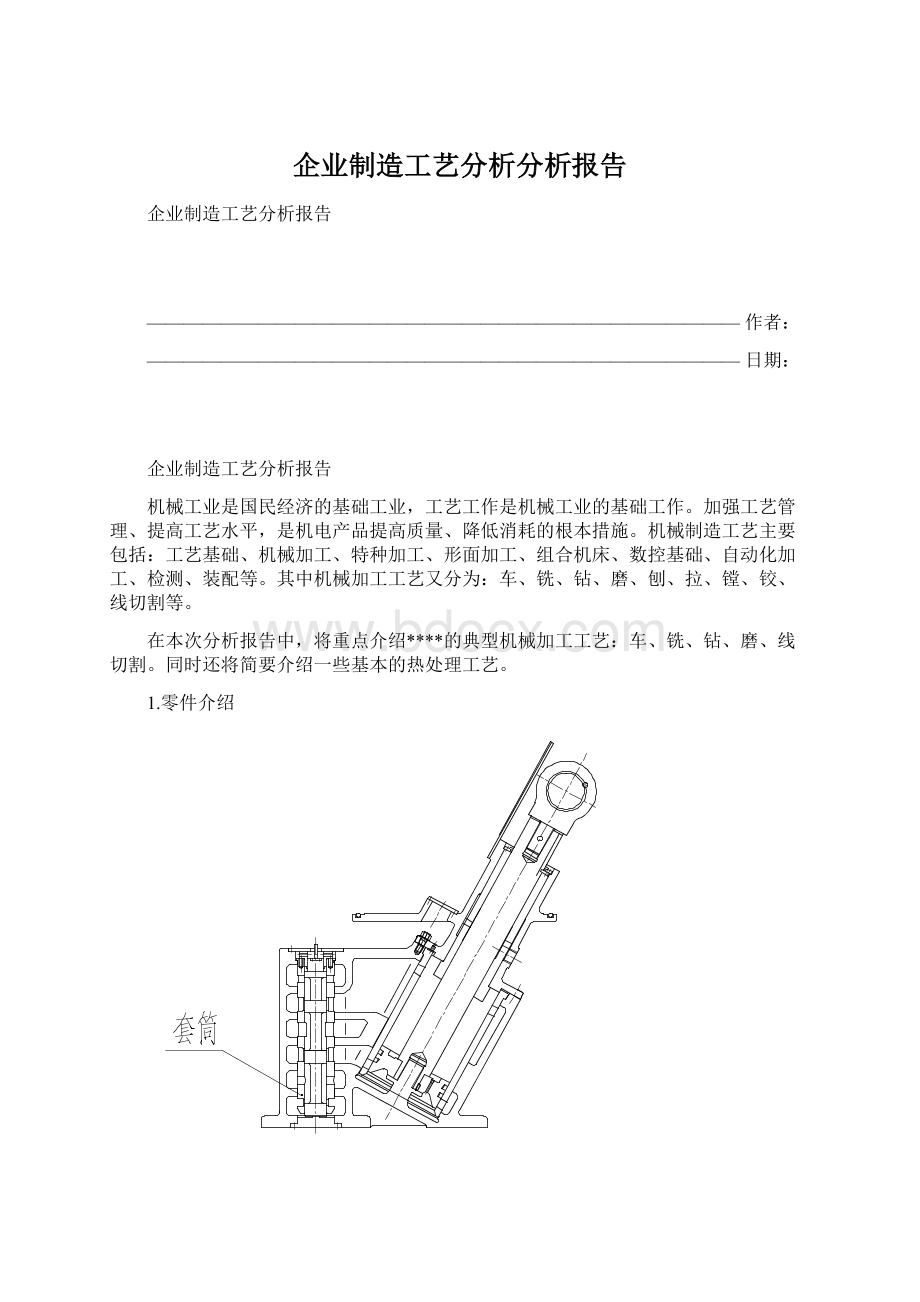
企业制造工艺分析分析报告
企业制造工艺分析报告
————————————————————————————————作者:
————————————————————————————————日期:
企业制造工艺分析报告
机械工业是国民经济的基础工业,工艺工作是机械工业的基础工作。
加强工艺管理、提高工艺水平,是机电产品提高质量、降低消耗的根本措施。
机械制造工艺主要包括:
工艺基础、机械加工、特种加工、形面加工、组合机床、数控基础、自动化加工、检测、装配等。
其中机械加工工艺又分为:
车、铣、钻、磨、刨、拉、镗、铰、线切割等。
在本次分析报告中,将重点介绍****的典型机械加工工艺:
车、铣、钻、磨、线切割。
同时还将简要介绍一些基本的热处理工艺。
1.零件介绍
现以高压油动机中的轴类零件套筒为例,对典型机械加工工艺加以介绍。
油动机又称液压伺服马达,是调节汽阀的执行机构,它将二次油信号转换为有足够作功能力的行程输出以操纵调节阀,控制汽轮机进汽。
它接受DEH控制系统发出的指令,操纵汽轮机阀门的开启和关闭,从而达到控制机组转速、负荷以及保护机组安全的目的。
套筒是油动机中重要组成部分,图1.1为套筒在高压油动机J3301.3602中的安装位置,图1.2为套筒J3301.3602.003零件图。
图1.1高压油动机
图1.2套筒零件图
2.机械设备及制造工艺分析
套筒加工的主要工艺流程如下:
调质
精车
粗车
备料
钻孔
划线
铣削
划线
线切割
磨削
钳工
铣削
精磨
氮化
2.1备料、粗加工、热处理
原材料选用25Cr2MoVA-5+6的氮化钢,尺寸不大,采用圆棒料即可。
外圆表面车削加工,粗车切去毛坯硬皮和大部分余量,单边留有余量3mm。
为改善材料的力学性能,为后续的加工过程及渗氮做好准备,以调质作为预备热处理。
调质即淬火加高温回火的复合热处理,钢经调质处理后得到由铁素体基体和弥散分布于其上的细粒状渗碳体组成的回火索氏体组织,使钢的强度、塑性、韧性配合恰当,具有良好的综合力学性能。
2.2精车
本道工序应完成的加工内容是:
车外圆φ100h6和内孔φ60H7留0.5mm磨量,其余尺寸按图纸要求车准。
在车床上利用车刀加工工件的过程称为车削。
车削的工艺特点有以下几方面:
⑴车削是在机械制造中使用最广泛的一种加工方法,主要用于加工内、外回转表面;⑵易于保证零件各加工面的位置精度;⑶车刀结构简单、制造容易,便于根据加工要求对刀具材料、几何角度进行合理选择;⑷切削过程平稳,可采用较大的切削用量,生产效率高;⑸对零件的结构、材料、生产批量等有较强的适应性,应用广泛。
车削加工时,工件的旋转运动为主运动,车刀的水平移动为进给运动,因此,车削最适合加工回转体零件。
主要用于加工内外圆柱面、圆锥面、断面、台阶面、中心孔、沟槽、螺纹及成型面等。
在车削加工中,车外圆是最常见、最基本的加工方法。
精车外圆是切去留下的少量金属层,从而达到预定的加工要求。
切削用量一般取:
α=0.2-0.5mm;f=0.1-0.3mm,vc<0.1m/s或vc>1.6m/s。
采用90°偏刀或宽刃精车刀。
车孔是指用车削方法扩大零件的孔或加工空心零件的内表面,也是一种常用的加工方法,加工过程中工件旋转、车刀移动,孔径大小可由车刀的切深量和走刀次数予以控制。
工件其他部分的尺寸可参照车外圆、内孔等加工方法按图纸要求加工。
在厂内采用普通车床即可完成的工序常用C620车床来加工。
该车床床面上车削的最大直径400mm,刀架上车削的最大直径210mm,能完成车削圆柱阶梯轴、镗孔、切槽、车端面等工作。
C620车床由电机带动,全部采用机械传动,主轴箱润滑油由油泵供给,其余润滑部位每日要进行加油润滑。
床头箱I轴上装有多片式摩擦离合器,操纵方便并能保护传动系统,主轴前轴承为可调整的特殊双列滚珠轴承。
加工精密螺纹时可由挂轮箱直联丝杠,并利用精密的交换齿轮选择螺距;溜板箱内有落下蜗杆,可防止送刀系统损坏,并能利用固定在床身上的挡铁自动停止送刀;床头箱及送刀箱各轴轴承(除主轴外)都能在箱外调整而不需要拆卸任何零件。
C620机床传动系统图见图2.2。
图2.2C620机床传动系统图
2.3划线、铣削
本道工序应完成的加工内容是:
划中心十字线,B-B剖凹槽线;铣D-D剖扁方,B-B剖38×32凹槽。
D-D剖加工要求见图2.3。
图2.3D-D剖视图
划线是指根据图样的尺寸要求,用划线工具在毛培或半成品上划出待加工部位的轮廓线或作为基准的点、线的操作。
划线可分为平面划线和立体划线,其主要作用是:
⑴划出清晰的尺寸界线,作为工件安装或加工的依据;⑵检查毛培形状与尺寸是否合乎要修,剔除不合格毛坯;⑶合理分配各加工表面的加工余量。
划线的一般步骤如下:
⑴分析图样,确定划线基准;⑵在划线表面涂上一层薄而均匀的涂料;⑶选用合适的工具和安放工件位置,工件支撑要牢固;⑷正确选用画线工具,划出的线条要求准确、清晰,关键部位要划辅助线,并注意在一次支撑中应把需要划的平行线划全,以免再次支撑补划造成误差;⑸划好线后,要反复核对尺寸,确保准确无误。
在铣床上利用铣刀的旋转和工件的移动对工件进行切削加工,称为铣削加工。
铣削加工的主要特点有:
⑴生产效率高;⑵刀齿散热条件好;⑶容易产生震动;⑷加工成本高。
铣削加工范围很广,主要用来加工各类平面(水平面、垂直面、斜面)、沟槽(直槽、键槽、角度槽、T形槽、V形槽、圆弧槽、螺旋槽等)和成型面,也可进行钻孔、镗孔、铰孔等。
在本道加工工序中主要利用立式铣床在工件表面铣削凹槽,根据凹槽宽度选择合适的立铣刀,通过进刀量和走刀次数来控制槽的深度。
在企业中铣削加工的常用设备是X53K立式铣床。
X5040立式铣床(也叫X53K立式铣床)属于铣床中广泛应用的一种机床,是一种强力金属切削机床,该机床刚性强,进给变速范围广,能承受重负荷切屑。
X5040立式铣床主轴锥孔可直接或通过附件安装各种圆柱铣刀、圆片铣刀、成型铣刀、端面铣刀等,适于加工各种零件的平面、斜面、沟槽、孔等。
该铣床属于通用机床,可用各种圆柱铣刀、圆片铣刀、角铣刀、成型铣刀和端面铣刀加工各种平面、斜面、沟槽齿轮等,也可选配万能铣头、圆工作台、分度头等铣床附件,扩大加范围。
特别适用于单件、小批生产和工具、修理部门,也可用于成批生产。
2.4划线、钻孔、铣削
本道工序应完成的加工内容是:
划各窗口加工参考线,A-A剖窗口划φ20落刀孔,B-B剖窗口正中划φ5穿线孔。
划2-M12-6H螺孔线,4-φ20孔线,60°×1槽线。
钻各穿线孔φ5及M12底孔φ10.2,钻孔4-φ20及各落刀孔。
铣A-A剖窗口,E-E剖60°×1油槽铣成60°×1.5。
加工要求见图2.4-1~2.4-3。
图2.4-1A-A剖视图图2.4-2C-C剖视图
图2.4-3E-E剖视图
划线及铣削工艺同上,这里就不再赘述。
用钻头在工件实体部位加工孔称为钻孔。
钻削的特点有:
⑴钻头不像其他单刃刀具那样容易弯曲,切削深度达到孔径的一半,金属切削效率高;⑵钻削过程是半封闭的,由于钻头伸入孔内并占据较大空间,容易造成切屑堵塞,因此排屑和散热困难;⑶钻削时冷却条件较差,切削温度高,因此限制了切削速度的提高,生产效率低;⑷钻削为粗加工,精度较低。
在对单件或小批量零件进行钻孔之前,应在零件上通过划线确定所要钻孔的中心点,然后在孔中心点处用样冲点,找正孔中心与钻头的相对位置后钻削;如果生产批量较大或孔的位置精度要求较高时,需采用钻模来保证。
对于较深的孔,钻孔时要经常退出钻头,排除切屑并进行冷却润滑,防止切屑堵塞、钻头过热、磨损加快或钻头折断。
Z35摇臂钻床是一种用途较广的钻床,厂内也会经常用到。
它的主要传动方式是由一台4.5kW电动机通过齿轮变速实现;立柱锁紧由一台0.6kW电动机通过液压机构带动;升降台由一台1.7kW电动机通过丝杠螺母带动。
主轴传动、进给传动、升降传动均装有钢珠离合器作为故障保险。
机床参数如下:
最大钻孔直径:
50mm
主轴孔锥度:
莫氏5号
主轴转速:
正转18级32-1700r/min,反转18级40-2000r/min
进刀量:
0.06-1.2mm/r
主轴中心至立柱母线距离450-1500mm
Z35摇臂钻床立柱最大回转角360度
主轴端面至工作台距离0-1000mm
主轴的最大移动距离(手动或机动)350mm
主轴箱水平最大移动量手动1050mm
2.5线切割
本道工序应完成的加工内容是:
⑴夹左端外圆校正,开机,用钼丝接触右端面,以电火花为准。
拆去钼丝,走坐标25.5mm,穿上钼丝,按工艺附图1切割D-D剖窗口,拆去钼丝;⑵走坐标136.5mm,穿上钼丝,按工艺附图2切割B-B窗口,拆去钼丝;⑶走坐标139mm,按工艺附图2切割B-B窗口,拆去钼丝。
具体加工要求见图2.5-1~2.5-2。
图2.5-1F向视图图2.5-2B-B剖视图
电火花线切割加工是一种新的工艺形式,是用线状电极(钼丝或铜丝)靠火花放电对工件进行切割,故称为电火花线切割,简称线切割。
电火花线切割加工有如下特点:
⑴由于工具电极是直径较小的细丝,省掉了成型工具电极的制作,靠数控技术实现复杂的切割轨迹,缩短了生产准备时间,加工周期短;⑵脉冲电源的加工电流较小,脉冲宽度较窄,属中、精加工范畴,所以只采用正极性加工,工件与脉冲电源的正极相接;⑶采用水或水基工作液,不会引燃起火,容易实现安全无人运转;⑷线切割电极丝比较细,切缝很窄,可以加工微细异形孔、窄缝和复杂形状的工件。
线切割加工主要适用于模具、电火花成型加工用的电极、精密零件等的加工。
线切割机主要由机床、数控系统和高频电源这三部分组成,目前厂里所用的是DK7730B线切割机。
线切割机数控系统由单片机、键盘、变频检测系统构成,具有间隙补偿、直线插补、圆弧插补、断丝自动处理等主要功能,能切割材料,如高强度、高韧性、高硬度、高脆性、磁性材料,以及精密细小和形状复杂的零件。
机床由床身、储丝机构、线架、XY工作台、油箱等部件组成,绕在储丝筒上的钼丝经过线架作高速往复运动。
加工工件固定在XY工作台上,X、Y两方向的运动各由一台步进电机控制。
数控系统每发出一个信号,步进电机就走一步,并通过中间传动机构带动两方向的丝杠旋转,分别使得X、Y工作台进给。
2.6钳工处理
本道工序应完成的加工内容是:
修准个窗口,去毛刺,攻丝。
钳工是手持工具改变工件的形状、尺寸或确定工件间相互位置的加工。
去毛刺时使用锉刀,交叉采用交叉锉、顺向锉、推锉等方法加工,最终使零件表面光滑无毛刺。
攻丝采用丝锥,在预先钻好的螺纹孔内用丝锥加工出内螺纹。
2.7磨削
本道工序应完成的加工内容是:
磨内孔φ60H7,留0.1mm余量。
在磨床上利用砂轮作为作为切削刀具,对工件表面进行切削加工的过程成为磨削,它是工件精加工的常用方法之一。
磨削加工有以下特点:
⑴加工质量高;⑵可加工高硬度材料;⑶应用范围广;⑷加工温度高;⑸需要预加工;⑹径向分力大。
磨削加工范围很广,不同类型的磨床可加工不同的形面。
它通常可精加工各种平面、内外圆柱面(外圆、内孔等)、内外圆锥面、沟槽、成形面(螺纹、齿形等)以及刃磨各种刀具和工具;此外,还可用于毛坯的预加工和清理等粗加工。
内圆磨削可在普通内圆磨床、万能内圆磨床、无心内圆磨床及行星磨床上完成。
磨削内圆时,多数以工件的内圆或端面定位,一般采用三爪卡盘装夹。
其磨削方法主要有周磨法和端磨法两种。
厂内磨削加工常用M131W万能外圆磨床,可用于加工圆柱形、圆锥形或其他形状素线展成的外表面和轴肩端面。
工件支承在头架和尾座的两顶尖之间,由头架的拨盘带动旋转作圆周进给运动。
头架和尾座装在工作台上,可作纵向往复的进给运动。
工作台分上下两层,上工作台可调整一个不大的角度,以磨削圆锥形表面。
磨床的砂轮架上附有内圆磨削附件,砂轮架和头架都能绕竖直轴线调整一定角度,头架上除拨盘能旋转外,主轴也能旋转,这样就扩大了加工范围,可磨削内孔和锥度较大的内、外锥面。
2.8氮化处理
本道工序应完成的加工内容是:
按技术要求氮化处理。
渗氮(又称氮化)是将氮渗入钢件表面,以提高其硬度、耐磨性、疲劳强度和耐蚀性能的一种化学热处理方法。
钢的渗氮具有以下优点:
⑴高硬度和高耐磨性;⑵高的疲劳强度;⑶变形小而规律性强;⑷较好的抗咬合性能;⑸较高的抗蚀性能。
钢的渗氮分为3个基本过程,即渗氮介质分解形成活性氮原子、活性氮原子背钢件表面吸收及氮原子由表面向内部的扩散。
为了正确的制定渗氮工艺,保证渗氮质量,就需要选择好气氛氮势、渗氮温度、渗氮时间三个工艺参数。
一般渗氮工艺中,采用控制氨分解率的方法来控制氮势,即通过改变氨流量来控制氨分解率,从而达到控制气氛渗氮能力的目的。
其基本原则是:
欲使气氛氮势提高,应加大气体流量,降低氨分解率;反之,则应减小气体流量,提高氨分解率。
渗氮温度的选择主要应根据对零件表面硬度的要求而定,硬度高者,渗氮温度应适当降低。
渗氮时间影响层深,因此主要依据所需的渗层深度而定。
2.9精磨、完检入库
本道工序应完成的加工内容是:
百分表校正,磨准外圆φ100h6和内孔φ60H7。
按图纸及工艺要求完检,涂超薄膜防锈油入库。
用百分表检验圆度,工件转动,测头不动,得到半径变动量按要求后磨准外圆和内孔,磨削的工艺在前文已有详细的介绍。
依完检和工艺要求,⑴用游标卡尺测量窗口尺寸34(+0.05、0)和24(+0.05、0),用块规检查窗口2.5±0.05;⑵将工件放置平板上,用高度尺测量检查窗口位置;⑶将零件和粗糙度量块进行比较,目测得到粗糙度值。
若无法满足要求,均采用磨削加以修正。
3.小结
参考文献
[1]熊良山,严晓光,张福润.机械制造技术基础[M].武汉:
华中科技大学出版社,2010.
[2]王辉,刘茂福.机械制造技术[M].北京:
北京理工大学出版社,2010.
[3]黄树红.汽轮机原理[M].北京:
中国电力出版社,2008.
[4]郑修本.机械制造工艺学[M].北京:
机械工业出版社,2012.
[5]窦金平,周广.通用机械设备[M].北京:
北京理工大学出版社,2011.
[6]张江华,吴小邦.机械制造工艺[M].北京:
机械工业出版社,2012.
[7]朱秀琳.机械制造基础(第二版)[M].北京:
机械工业出版社,2012.
[8]郑祖斌.通用机械设备[M].北京:
机械工业出版社,2004.
[9]李建跃.机械制造基础(Ⅱ)[M].长沙:
中南大学出版社,2006.
[10]黄开榜,张庆春,那海涛.金属切削机床[M].哈尔滨:
哈尔滨工业大学出版社,2006.