烘炉机烘炉方案.docx
《烘炉机烘炉方案.docx》由会员分享,可在线阅读,更多相关《烘炉机烘炉方案.docx(9页珍藏版)》请在冰豆网上搜索。
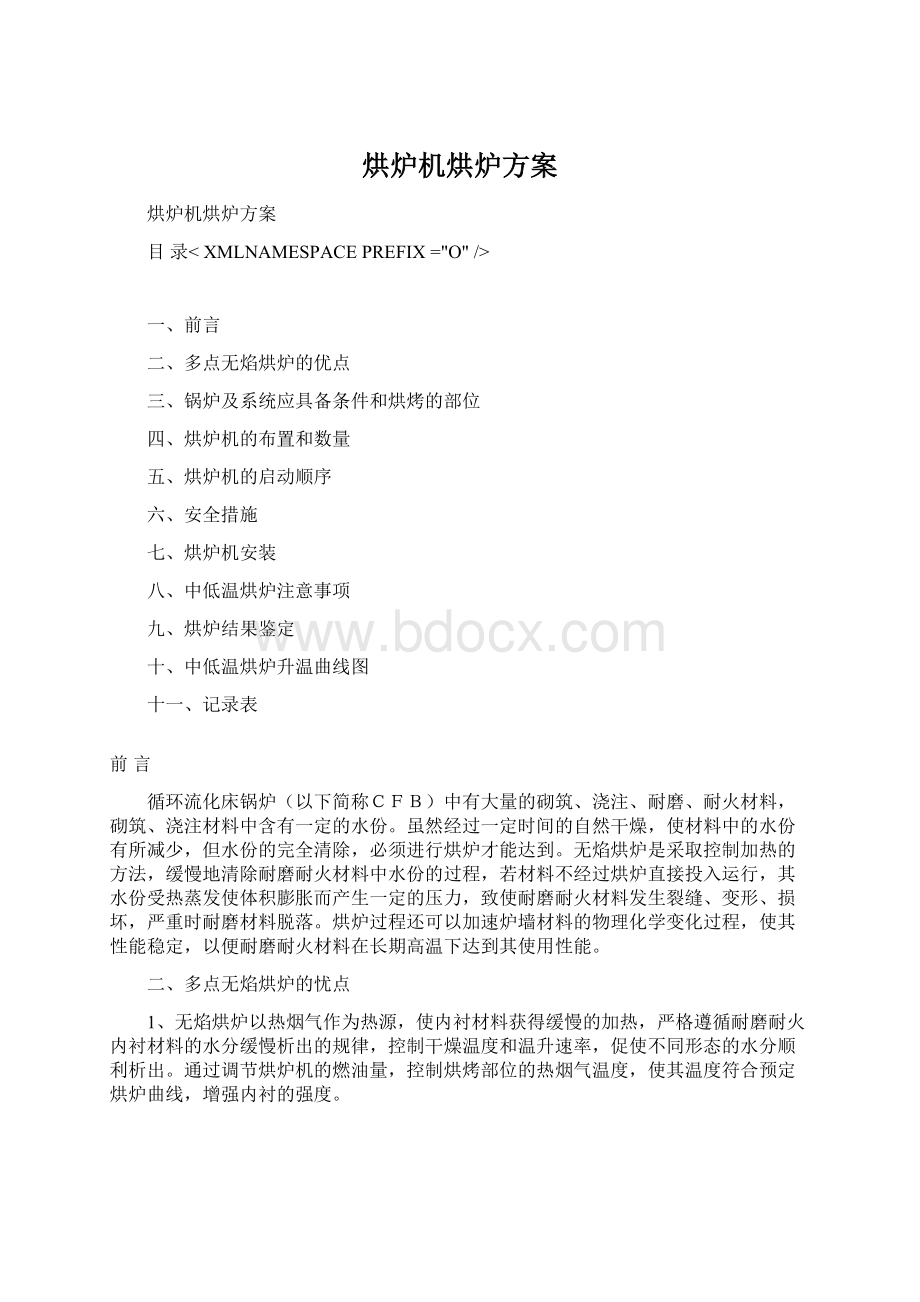
烘炉机烘炉方案
烘炉机烘炉方案
目录
一、前言
二、多点无焰烘炉的优点
三、锅炉及系统应具备条件和烘烤的部位
四、烘炉机的布置和数量
五、烘炉机的启动顺序
六、安全措施
七、烘炉机安装
八、中低温烘炉注意事项
九、烘炉结果鉴定
十、中低温烘炉升温曲线图
十一、记录表
前言
循环流化床锅炉(以下简称CFB)中有大量的砌筑、浇注、耐磨、耐火材料,砌筑、浇注材料中含有一定的水份。
虽然经过一定时间的自然干燥,使材料中的水份有所减少,但水份的完全清除,必须进行烘炉才能达到。
无焰烘炉是采取控制加热的方法,缓慢地清除耐磨耐火材料中水份的过程,若材料不经过烘炉直接投入运行,其水份受热蒸发使体积膨胀而产生一定的压力,致使耐磨耐火材料发生裂缝、变形、损坏,严重时耐磨材料脱落。
烘炉过程还可以加速炉墙材料的物理化学变化过程,使其性能稳定,以便耐磨耐火材料在长期高温下达到其使用性能。
二、多点无焰烘炉的忧点
1、无焰烘炉以热烟气作为热源,使内衬材料获得缓慢的加热,严格遵循耐磨耐火内衬材料的水分缓慢析出的规律,控制干燥温度和温升速率,促使不同形态的水分顺利析出。
通过调节烘炉机的燃油量,控制烘烤部位的热烟气温度,使其温度符合预定烘炉曲线,增强内衬的强度。
2、无死角区域:
因多点部置,使其炉膛密相区,点火燃烧器、水冷风室、回料斜腿、立腿、分离器进、出口烟道,分离器、各部位都能受到均匀的加热,从而达到其设计耐磨、耐火性能。
3、节省大量的人力、物力,缩短烘炉时间,提高工作效率。
三、锅炉及系统应具备条件和烘烤的部位
1.锅炉及系统应具备条件
1.1锅炉烟气系统安装完成,为防止烟气及热量散失,除热烟气通入孔外其余门孔应堵严(用硅酸铝纤维棉板);
1.2锅炉内所有耐火耐磨材料砌筑完毕,并自然养护7天以上;
1.3锅炉部位膨胀指示器齐备,指针调整至零位,支撑吊杆安装齐全,所有弹簧吊架的定位销烘炉前拆除;
1.4消防系统经验收并具备投运条件;
1.5锅炉汽水系统、排污系统、疏水系统、排汽系统安装完毕并经验收合格,可投运,锅炉给水和蒸汽管道已安装完成。
1.6炉膛、分离器部分DCS烟温测量系统校准具备投运条件;
1.7锅炉生火排汽门开关灵活;
1.8锅炉汽包水位计安装完毕具备投运条件,锅炉汽包水位、压力监视系统调试完毕具备投运条件。
1.9锅炉照明满足烘炉条件。
1.10烘炉前在点火风道、点火装置、回料器、分离器出口等部位的钢板上已开L=100-200mm的排湿汽孔;烘炉用的临时设施已装好。
1.11锅炉操作方面
向锅炉注入处理合格的软水,并上至正常水位。
上水前将锅炉有关阀门置于下列位置:
阀门名称及说明
状 态
主给水管路上的闸阀
关闭
主给水管路上的止回阀
自动
饱和蒸汽引出管上的放气阀
开启
锅筒高、低位水位计水侧及汽侧截止阀
开启
锅筒高、低位水位计疏水阀
关闭
锅水加药用截止阀
关闭
锅筒紧急放水阀
关闭
锅筒连续排污阀
关闭
炉水取样阀
关闭
锅筒压力表用三通阀
开启
饱和蒸汽取样阀
关闭
锅炉集中下降管排污阀
关闭
水冷壁下集箱定期排污阀
关闭
过热器进口集箱疏水阀
开启
过热器出口集箱疏水阀
开启
高温过热器出口连接管道对空排汽阀
自动
喷水减温器手动截止阀
关闭
注意:
上水时,当相应部件的放气阀冒水时,就关闭该放气阀;检查锅筒电接点水位计在主控室内的显示情况,并同就地水位计的读数作准确的比较;引风机进口导片开度:
全开。
1.12临时燃油系统:
烘炉机所用燃料为0#轻柴油(GB252-87一级品),烘炉机前的油压为0.6-0.8Mpa每小时300-800㎏送油量,并保持持续稳定。
1.13临时压缩空气系统:
油枪雾化压缩空气烘炉机前的气压为0.6-0.8Mpa,排气量每分钟4立方米,并保持持续稳定。
1.14临时电源、电路系统:
烘炉机电源电压为380V(三相四线制),每台电机功率为18.5KW,共计10台烘炉机。
(烘炉机陆续投入)
2.烘烤的重点部位:
点火燃烧器、水冷风室、炉膛密相区、分离器、返料器、返料器斜腿、水平烟道等。
四、烘炉机的布置和数量(共12台,两台备用)
1、床下点火燃烧器2台烘炉机,左右各1台。
2、炉膛4台烘炉机,左右各2台。
3、回料器2台烘炉机,左右各1台。
4、分离器进口烟道2台烘炉机,左右各1台。
五、烘炉机的启动顺序
1、启动床下点火燃烧器2台烘炉机,以小油量低烟温投运,稳燃后逐步加大油量,并按升温曲线升温及保温。
烘炉开始点火,从环境温度以5℃/h升温到150℃,需12小时。
2、启动炉膛2台烘炉机,以小油量低烟温投运,稳燃后逐步加大油量,并按升温曲线升温及保温。
在启动床下点火燃烧器2台烘炉机约3.5-4.5小时后,启动炉膛2台烘炉机。
3、启动回料器2台烘炉机,以小油量低烟温投运,稳燃后逐步加大油量,按升温曲线升温及保温。
在启动床下点火燃烧器2台烘炉机约9-10小时后,启动回料器2台烘炉机。
4、启动分离器入口2台炉烘机,以小油量低烟温投运,稳燃后逐步加大油量,按烘炉升温曲线升温及保温。
在启动床下点火燃烧器2台烘炉机约72小时后启动分离器入口2台炉烘机。
5、根据升温情况,再启动炉膛另两台烘炉机,以小油量低烟温投运,稳燃后逐步加大油量,按烘炉升温曲线升温及保温。
六、安全措施
1、给水系统供水稳定,保证锅炉汽包正常水位,保证排汽阀开关灵活,不泄漏。
2、保证烟道系统畅通,挡板调整灵活。
3、清除烘炉机附近无用的易燃、易爆物品,无法移动的设备及物品需有关人员妥善保管。
4、在烘炉期间,其它施工单位不得在油系统及烘炉机旁进行电焊、气割等操作。
5、每台烘炉机旁配备灭火器。
6、油系统设专人看管,与烘炉无关人员不得操作烘炉设备。
7、烘炉期间,尽量避免施工单位交叉作业,烘炉机与锅炉连接烟道附近不得有人员流动,防止烫伤。
8、保证夜间照明,锅炉照明系统调试完毕并能满足烘炉条件,保证道路畅通。
烘炉机运行区域内设警示绳牌。
9、烘炉过程中,注意检查锅炉本体的安全性。
熄火立即关断油阀门,不准有漏油现象。
10、如在锅炉烘炉过程中危及人身及设备安全时,应及时消除,必要时停止烘炉。
11、如在烘炉过程中,发现异常情况,应及时调整,并立即汇报指挥人员。
12、烘炉过程中应严格控制温度,根据炉墙材料厂家提供的烘炉曲线进行烘炉。
13、所有参加烘炉人员应进行技术交底,熟悉了解整个烘炉过程,烘炉过程中,加强安全管理,防止热辐射和蒸汽泄漏伤人。
停炉后,严禁在高温下进入炉内。
烘炉机运行期间应设专人不间断看守。
如烘炉机熄火应立即断油,并通风吹扫10分钟。
七、烘炉机安装
1.为防止烟气及热量的散失,除烘炉机用孔外,其余门孔均应关闭或堵死,以防止烟气及热量散失。
具体应关闭烟道(设置临时隔断)及人孔门等:
2.防止烟气从灰斗孔逸出,其插板门必须关闭严密。
3.防止烟气从吹灰器管孔逸出。
4.炉膛和旋风分离器上的门孔关闭严密,以防止热量从门孔逸出而影响烘炉效果。
5.临时排烟:
利用锅炉的排烟系统排烟。
6.临时排湿、排汽孔切割:
在旋风分离器锥体部分、回料阀及回料阀下部、床下点火燃烧器等部位,开足够的烘炉泄水孔和排湿孔。
排湿孔的开孔根据实际情况可按炉墙材料厂家的要求开孔。
7.烘炉机安装:
烘炉机自重160kg/台、输风机自重186kg/台。
烘炉机与热烟气管道采取全口焊接方式。
热烟气管道与人孔加压石棉绳密封。
烘炉机可根据现场情况(炉体构造、场地空间等)利用2吨的手动葫芦、吊盘、升降机(起重机)等设备工具采取平装、仰装、侧装、吊装、支架等多种安装方式,安装过程中要避免烘炉机的摔碰,尤其调风、配气端。
安装时观察镜要先行拆下,安装完毕后再另行装配。
安装过程中涉及到围栏、扶梯等处的拆割及烘炉后恢复。
8.烘炉机热烟气连接管道规格为Ф273mm或Ф325mm的碳钢管,长度及形状按现场实际调整,安装、支撑按烘炉机布置位置和实际情况确定。
连接管道在连接时不宜采用直角弯的形式和管道入口向下布置(火焰向下)的形式,采用以上形式容易造成烘炉升温时烧穿连接管道。
在热烟气连接管道和烘炉机出口相连接时,热烟气连接管道一般留有0.5~1m左右的直段,以便均匀混合热烟气。
9.烘炉机与锅炉连接管道连接处密封。
10.烘炉机的拆卸可采用气割或其它等拆卸方法,按安装反向顺序拆卸。
11.临时隔断:
在炉膛出口和旋风分离器入口交界处、安装临时隔墙封闭。
尾部竖井高过处安装临时隔墙,隔墙四周留有30-50mm空隙。
隔墙材料采用白铁皮,固定在临时搭建的钢脚手架上面。
八、中、低温烘炉注意事项
1.锅炉上水前后记录膨胀位移,烘炉过程中根据温升连续记录膨胀位移。
烘炉时注意控制升温率和恒温时间,烘炉温度偏差在±20℃。
2.烘炉应连续进行,每0.5小时记录烘炉各部位温度,注意观察锅炉膨胀情况,发现异常及时汇报,并每隔6小时记录锅炉各部位膨胀值。
3.烘炉人员应严格控制烘炉温度,发现温度偏离烘炉温度,应及时调整。
4.引风机进口挡板开度根据排烟情况而定。
5.在烘炉全过程中,始终保持锅筒水位在正常水位±50mm之间,锅炉上水前水位应低于正常水位。
6.当锅筒压力达到~0.1Mpa(表压)时,关闭汽包及过热器空气阀。
7.在锅筒压力达到0.17Mpa(表压)后,借助短期排污操作,检查水位计显示,确认水位计可靠并冲洗压力表。
8.锅炉压力升至0.3MPa,冲热工表管,定排污一次,0.49MPa热紧螺栓。
压力达1.0-1.2Mpa,关过热器疏水。
9.烘炉期间,汽包压力控制在烘炉曲线要求范围内。
10.烘炉前通知电除尘专业对阴极振打瓷轴进行适当防油烟保护。
11.烘炉过程中,根据需要对锅炉进行定期排污。
烘炉72小时后,每隔8小时定期排污一次。
九、烘炉结果鉴定
烘炉后耐磨材料表面平整、无贯通性裂缝。
用手锤轻敲炉墙衬里,发出清脆的回声,炉墙衬里无松动情况,取出预设试块进行含水率测试,其含水率小于2.5%。
为校验烘炉效果,在炉墙施工的同时制作模拟炉墙的试块。
具体数量如下:
1、炉膛底部布风板2块;
2、回料器2块;
3、分离器进口2块:
4、床下点火燃烧器2块;
5、水平烟道2块。
总计:
8块
十、中低温烘炉升温曲线图(见下页图)
1.烘炉起始温度及恒温控制时间
1.1烘炉开始点火,从环境温度以5℃/h升温到150℃,需12小时。
1.2恒温150℃保持36小时。
1.3从150℃以4.6℃/h升温到260℃,需24小时。
1.4恒温260℃保持36小时。
1.5从260℃以2.5℃/h升温到380℃,需48小时。
1.6恒温380℃保持12小时。
1.7根据耐磨耐火材料的特性,温差可控制在±20℃之间范围。
2.烘炉过程温度测量控制
2.1炉膛温度:
按热工图纸沸下温度B、E点(前后墙)为特征温度;
2.2燃烧器温度:
采用床下启动燃烧器低温段温度左右各一作为特征温度;
2.3分离器温度:
采用分离器出口(左右各一)的温度作为特征温度;
2.4返料床温度:
采用返料床床料温度(左右各一)作为特征温度;
2.5水冷风室:
采用水冷风室温度左右各一。
2.6返料腿:
返料腿床料温度左右各一
3.各处热电偶检测的平均烟气温度与预定烘炉曲线相比较,随时调节各处烘炉机的投油量,保证各处测点烟气温度尽量符合预定的烘炉曲线在允许温差±20℃的范围内。
4.温度检测记录:
烘炉温度监测数据,由烘炉公司和电厂运行人员共同记录DCS的温度,火电一公司试运人员记录热膨胀数据。
十一、记录表
分离器中、低温烘炉升温曲线图
序号
温度℃
温升率℃
时间
1
80—150℃
3℃/h
24小时
2
150℃
恒温±20℃
24小时
3
150—260℃
3℃/h
36小时
4
260℃
恒温±20℃
24小时
5
260—360℃
2℃/h
48小时
6
360℃
恒温±20℃
12小时
1:
因耐火耐磨材料在80—100℃期间水份没有蒸发,炉墙是预热阶段,所以在烘炉的初始阶段80—100℃对耐火材料是安全的,所以开始温度可80℃以上。
2.温度与锅炉压力关系:
150℃—300℃压力2Mpa—4Mpa
300℃—380℃压力4Mpa—7Mpa
3.因炉膛温度自下而上升温,所以炉膛温度380℃.分离器温度360℃。
分离器出口340℃此温度为烘炉最终温度。
炉膛中、低温烘炉升温曲线图
序号
温度℃
温升率℃
时间
1
80—150℃
5℃/h
12小时
2
150℃
恒温±20℃
36小时
3
150—260℃
4.6℃/h
24小时
4
260℃
恒温±20℃
36小时
5
260—380℃
2.5℃/h
48小时
6
380℃
恒温±20℃
12小时
1:
因耐火耐磨材料在80—100℃期间水份没有蒸发,炉墙是预热阶段,所以在烘炉的初始阶段80—100℃对耐火材料是安全的,所以开始温度可80℃以上。
2.温度与锅炉压力关系:
150℃—300℃压力2Mpa—4Mpa
300℃—380℃压力4Mpa—7Mpa
3.因炉膛温度自下而上升温,所以炉膛温度380℃。
分离器温度360℃。
分离器出口340℃此温度为烘炉最终温度。
引文来源 鹤岗立达矸石热电有限责任公司