1317Critical impact velocity in the solid particles impact erosion of metallic materials英文翻译.docx
《1317Critical impact velocity in the solid particles impact erosion of metallic materials英文翻译.docx》由会员分享,可在线阅读,更多相关《1317Critical impact velocity in the solid particles impact erosion of metallic materials英文翻译.docx(15页珍藏版)》请在冰豆网上搜索。
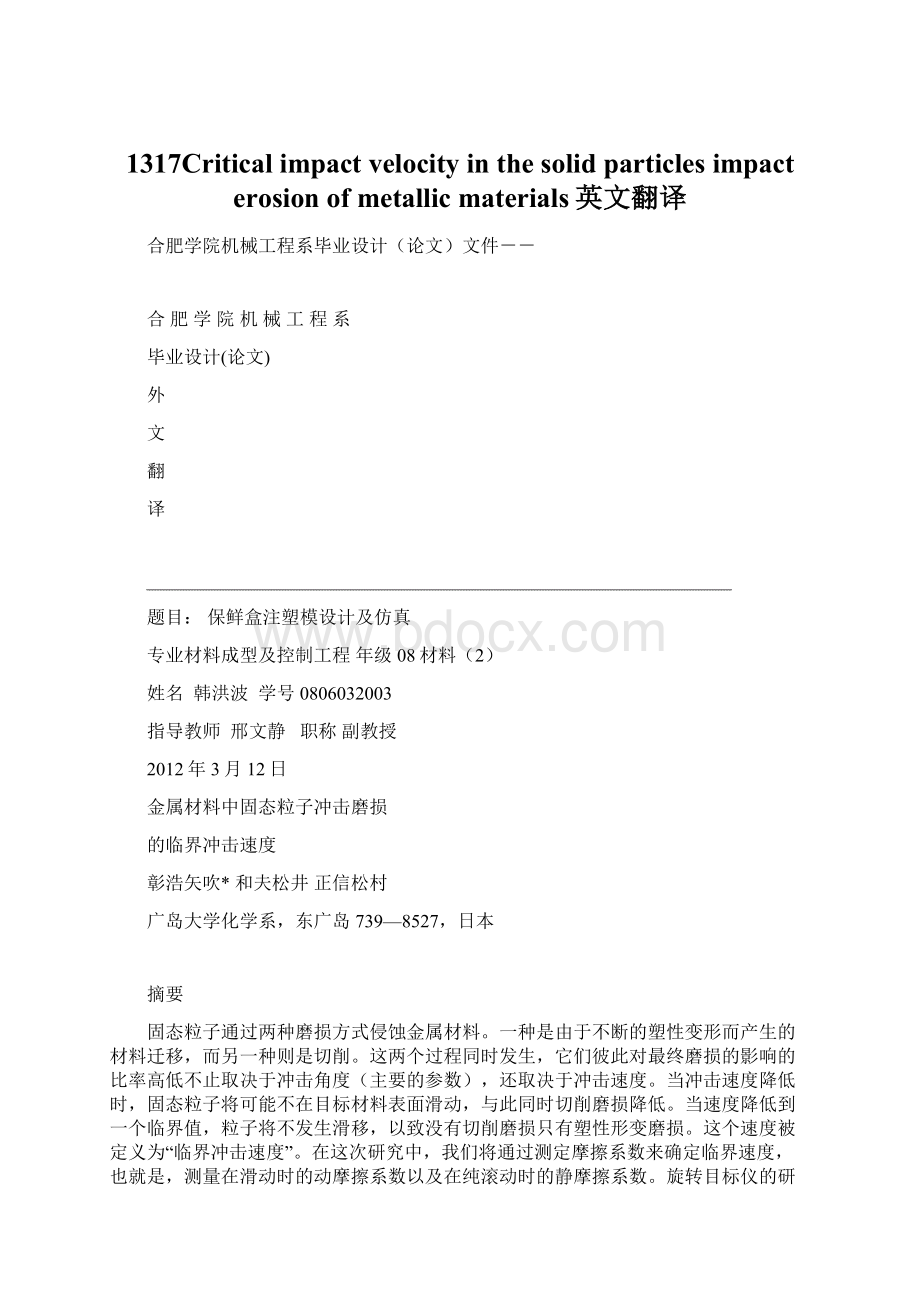
1317Criticalimpactvelocityinthesolidparticlesimpacterosionofmetallicmaterials英文翻译
合肥学院机械工程系毕业设计(论文)文件--
合肥学院机械工程系
毕业设计(论文)
外
文
翻
译
题目:
保鲜盒注塑模设计及仿真
专业材料成型及控制工程年级08材料
(2)
姓名韩洪波学号0806032003
指导教师邢文静职称副教授
2012年3月12日
金属材料中固态粒子冲击磨损
的临界冲击速度
彰浩矢吹*和夫松井正信松村
广岛大学化学系,东广岛739—8527,日本
摘要
固态粒子通过两种磨损方式侵蚀金属材料。
一种是由于不断的塑性变形而产生的材料迁移,而另一种则是切削。
这两个过程同时发生,它们彼此对最终磨损的影响的比率高低不止取决于冲击角度(主要的参数),还取决于冲击速度。
当冲击速度降低时,固态粒子将可能不在目标材料表面滑动,与此同时切削磨损降低。
当速度降低到一个临界值,粒子将不发生滑移,以致没有切削磨损只有塑性形变磨损。
这个速度被定义为“临界冲击速度”。
在这次研究中,我们将通过测定摩擦系数来确定临界速度,也就是,测量在滑动时的动摩擦系数以及在纯滚动时的静摩擦系数。
旋转目标仪的研发以利于测出粒子冲击时的摩擦系数,临界冲击速度不仅取决于材料和粒子的硬度,还取决于固态粒子的形状和大小。
关键词:
腐蚀;固态粒子;临界冲击速度;摩擦系数;冲击角
1.引言
固态粒子成分经机器和装备处理会因固态粒子冲击而产生一些磨损,从而引发塑性变形以导致材料从表面的迁移。
这种现象被称为磨料磨损或者固态粒子冲击腐蚀。
这将影响到这些机器的寿命,以避免严重的损失。
因此,在实验室中一些诸如预测在这一过程中的磨损量或者选取合适的材料以延长寿命的实验正在进行。
然而,我们都一致认为由加速测试得到的实验结果并不与装备的实际应用相一致。
甚至于材料的排行也不能完全与在这一领域的工作寿命保持一致。
这种实验结果和材料实际应用的之间的矛盾是基于两种磨损进程所造成的金属腐蚀和两者对最终磨损的贡献比率是由很多方面所决定的,特别是粒子的冲击角[1,2]。
当固态粒子几乎垂直地以高冲击角撞击金属材料,金属材料迁移的发生主要是由于重复的塑性变形。
另一方面,在小冲击角下由于切削引起的迁移与塑性形变相比占主导地位。
这两个过程同时发生,它们彼此对最终磨损的影响的比率不止取决于冲击状态(冲击角,速度)还有固态粒子的机械性能(强度,硬度等)。
然而,我们得出了一个出乎想象的结论:
腐蚀作用的测试结果对于在石膏硫酸溶液灰浆中两种铬钢,由实验室的先进设备获得与现实中在灰浆井中的使用是一致的,虽然固态粒子的冲击速度和冲击角是完全不同的。
更精确的说,在实验室的测试中固态粒子的冲击速度为1.7m/s,而在灰浆井中它超过10m/s。
在实验室的测试中固态粒子的冲击角为将近90度,而在现实的灰浆井中它很小[3]。
这一出乎想象的结论的原因如下。
当冲击速度降低,固态粒子将不再目标材料的表面滑动,这将减少切削磨损。
当速度减小到一定程度,粒子将不发生滑移,以致没有切削磨损只有塑性形变磨损。
这个速度被定义为“临界冲击速度”。
这说明由实验所得的粒子冲击速度比临界速度要低,这是因为固态粒子以低速高角度冲击试样会使切削过程不发生。
另一方面,在灰浆井中的固态粒子比实验中的粒子小且软。
甚至于这些粒子以高速低角度冲击材料表面,材料也不会有切削磨损。
换而言之,在灰浆井中的临界速度10m/s比实际的速度要大。
然而,加速实验测试的结果与实际在灰浆井中的表现一致是一个理所当然的问题,这是因为在两种状况下塑性变形不断地破坏机械性能。
为了提够支持临界冲击速度的证据,一个允许硅炭粒子自由落在有倾斜度的软钢表面的实验开始了。
将磨损的表面浸入PH=2的酸性氯化氢酸性溶液中测出溶解度。
在不同冲击角下磨损的表面的溶解率聚为一个通过降低冲击速度(表1[4])的共同速度。
当冲击速度为1.7m/s时,溶解速度趋于一致也就是临界速度,因为一致的溶解速度表示的是机械性能磨损的一致。
正如预期的那样,在实际的机器和设备中腐蚀磨损发生在临界速度或小于它的时候。
如果是这样,在低于临界速度的冲击速度下而不是在加速磨损速度,实验所得结果也许会与实际机器使用相符。
更重要的是,一个好的结论即使在应用和实验相互矛盾也是令人期待的。
正如上所述,临界冲击速度在预测材料的腐蚀时十分重要。
各种结合粒子和材料的临界速度可以通过测量溶解速度而得到。
然而这种方法将花费大量的时间和人力。
对于一种材料,任何合适的溶解的液体或任何测量溶解速度的方法不能总是被找到。
在这次研究中,通过国际应用的测量固态粒子和材料间的摩擦系数来决定临界冲击速度。
图1.损坏表面的溶解速率和SiC粒子对低碳钢撞击速度之间的关系
2.实验步骤
2.1.摩擦系数
旋转目标仪(图2)是用来测量在粒子冲击过程中的摩擦系数的。
一个固态粒子被允许从一定距离自由下落冲击旋转的圆锥样品目标。
在冲击之后,固态粒子被反弹到测量板上。
在冲击过程中,固态粒子受在切线方向由于样品的旋转而导致偏离反弹方向的摩擦力的影响。
角度的偏差取决于被标记的粒子冲击有或没有旋转标本的两点之间的距离。
摩擦系数可以通过偏离角α获得。
粒子冲击速度由下落距离控制,冲击角则由半垂直角β控制,与样品旋转速度相同。
四种材料被用作目标样品,它们是铝,黄铜,碳钢和淬火碳钢。
它们的化学组成和机械性能被列在表1中。
半垂直角分别为20度,30度和40度。
样品表面经2000#刚砂纸抛光。
图2测量粒子冲击时的摩擦系数的旋转目标装置示意图
两种球形粒子和三种角形粒子被用来作为冲击粒子。
它们的机械性能被列于表2中。
测量板是由聚氯乙烯制成或者是其表面覆盖着粉笔和白垩通过使用可视燃料的渗透剂实验。
粒子冲击测试板的位置将被粉末记录下来。
固态粒子的速度范围从1.0到5.0m/s,冲击角为15度,20度和30度。
表1.目标样品的化学成分与机械性能
表2.粒子的机械和物理性能
2.2临界冲击速度
临界冲击速度由摩擦系数推导出来并不难,也就是说,动摩擦系数在滑动时,静摩擦系数在滚动但无滑动时。
动摩擦系数的价值比静摩擦系数的小,这是因为它总是随滑动速度[5]的改变而不断变化。
然而,粒子起初在样本表面滑动将会很容易被发现,这便是摩擦系数和冲击速度之间关系的转折点,这个速度便是临界速度。
3.实验方法
3.1.摩擦系数
在固态球形粒子以V0冲击以2πrn转动的目标样本,两种力作用在粒子上(图3)。
一种是作用在目标表面切线方向的摩擦力F,另一种则是作用在目标样本正方向上的弹力W(图3(a))。
F可分解为在标本旋转方向的F
cosг和在标本脊方向的Fsinг。
粒子速度V0可如图3(b)分解为Vt和Vr,在冲击过程中转化为V0′。
粒子冲击旋转样本的轨迹
图3.粒子冲击目标样本的轨迹:
(a)粒子所受的力:
(b)冲击前后粒子的速度:
(c)粒子冲击目标样本的冲击速度及冲击角
摩擦系数µ可由以下公式定义。
(1)
偏离角的正切形式如下。
(2)
首先,我们考虑在标本转动方向的速度分量。
Vt是由粒子冲击时在样品旋转方向的摩擦力产生的。
公式3是在样本旋转方向原有的动量。
(3)
将式1代入式3可得
(4)
摩擦系数µ在冲击过程中不断变化,很难确定其在某一瞬间的具体数值。
由于这个原因平均摩擦系数ū被引入
(5)
将(5)与(4)合并可得
(6)
然后,我们考虑在标本表面正方向的速度分量。
列出在样本表面瞬时的动量变化。
(7)
弹性系数e被定义为在样本表面冲击前后速度的比例[7]
E=Vrsinβ′/V0sinβ
将Vr′由Vr,β和β′表示
(8)
将用Vr,β表示
(9)
把
(2),(7),(9)所得结果代入(6)式得
(10)
同时,我们考虑速度在标本脊方向的分量。
通过动量定理可得
(11)
将式7代入式11可得
(12)
将式8与式12合并可得
(13)
最后,将式13代入式10可得
(14)
粒子与样本之间的反弹角由式8,式12合并可得
(15)
冲击速度,冲击角由以下式表示图3(c)。
图3(c)可使我们更清晰的了解粒子冲击样本表面时的实际冲击速度。
(16)
(17)
(18)
平均摩擦系数可由式14,15和18以及偏离角α计算得出。
冲击条件由式16,17决定。
需留意的是摩擦系数为一个平均量。
弹性系数e由平均摩擦系数计算所得。
尽管如此,可将e取0到1之间的任意值代入公式。
3.2确定实验方法
3.2.1摩擦系数
为了确定理论公式,定值α被代入公式以获得球形粒子以β垂直角冲击目标样本时摩擦系数:
在相同的冲击条件下,这个公式应能表示出ū并非与β相关。
在碰撞角度为20度,β角分别为20度、30度、40度时,按上述方法用直径为0.6毫米的钢球撞击碳钢样本得到的ū值如图4所示。
几乎每一点都在同一条直线上证明这个公式相当可靠。
ū值在高冲击速度下保持不变,但是当速度低于一定值时其便如预期的那样开始减小。
ū值随速度增大而减小可解释为:
静摩擦力的变化取决于在冲击过程下各力组分的比例,更进一步ū是是滑动动摩擦系数和在滑动之后的滚动摩擦系数的平均值。
图4.摩擦系数与不同的冲击速度引起的半垂直角之间的关系
3.2.2临界冲击速度
为了确定临界冲击速度,需仔细观察钢球冲击留下的弹痕以获得ū与冲击速度之间的关系。
粒子以冲击角30度冲击碳钢表面留下直径5mm的痕迹。
当ū如图五中所示为2.0m/s时,冲击速度为1.9和2.5m/s。
圆心速度为1.9m/s相对于冲击方向的2.5m/s可以让我们清晰地由弹痕表层认识到其形状地不同。
这个观察结果与粒子滑动时的冲击速度超过2.0m/s并不矛盾,并证明了低于该速度粒子将不再滑动。
所以,我们把转折点的速度作为临界冲击速度。
图5.S45C粒子以介于1.9mrs至2.5mrs的冲击速度冲击低碳钢所留痕迹的金相图
4.结果与讨论
4.1临界速度测定
4.1.1球形粒子的临界冲击速度
球形粒子的临界冲击速度取决于通过改变冲击条件,如冲击角,粒子直径和目标材料时的摩擦系数。
当钢球以20度,30度,40度冲击碳钢并留下直径不同的弹痕时的摩擦系数如图6所示。
摩擦系数与直径为0.6mm的钢球的冲击速度一样与冲击角无关。
改变样品目标所测数据列于图7中。
总而言之,临界冲击速度与摩擦系数都随粒子直径和样品材料的改变而剧烈变化。
黄铜冲击4种样品目标所得冲击速度与摩擦系数列于表3中,包括以上所提及的结果。
图6.在不同的粒子直径以及冲击角度下的冲击速度与摩擦系数的关系
图7.不同的冲击试样的冲击速度与摩擦系数的关系
表3.在各种冲击条件下的球形粒子冲击速度和摩擦系数
4.1.2角形粒子的临界冲击速度
通过测量碳钢上直径为0.88mm的弹痕可得摩擦系数。
在相同的冲击条件下所测得的摩擦系数仍有可能不同。
在四种不同冲击速度下的摩擦系数分布如图8所示。
当冲击速度高于2.6m/s时分布比较接近,当冲击速度为1.9m/s时,分布变化最大。
这可由以下来说明:
当为较高的冲击速度时,由于粒子在目标表面滑行,更准确的说,有滑动摩擦的存在,使其不发生变化;他的散乱是源于角形粒子形状的不规则所引起的反弹方向的偏离。
在低速范围内,它的增长与静摩擦所伴随的相同原因,那便是,粒子的不规则形状。
解释是基于当摩擦系数变化最频繁时为代表的冲击速度。
如图9所示为以2.2m/s的速度冲击铝样本所得数据点连接所得图象。
表3所列为碳化硅和矽土粒子冲击碳钢样本所留下的弹痕直径结果。
图10为球形粒子和角形粒子的直径与临界冲击速度之间的关系。
当为球形粒子时,直径越大临界冲击速度越大。
当为角形粒子时,直径越大冲击速度就越小。
然而,粒子形状的作用清晰的反映了粒子形状和冲击速度的关系。
图8.不同冲击速度下的角粒子的摩擦系数的归一化频率分布
图9.角粒子冲击时摩擦系数和冲击速度之间的关系
图10.粒子直径对球形以及角形粒子的影响
4.2不同材料间的相互关系
我们研究了摩擦系数和材料性能对于临界冲击速度的影响。
众所周知固态粒子的磨损腐蚀与粒子和样本之间硬度比值有很大关系[8]。
图11所示为两种球形粒子的临界冲击速度和样品硬度(HVs)与粒子硬度(HVp)的比值。
在两种情况下,临界冲击速度都随着硬度比例的增加而增加。
尽管如此,这种关系依旧不能被定义为线性关系,也就是说硬度比例并非普遍参数。
临界冲击速度与动摩擦系数之间的关系如图12所示。
球形粒子的临界冲击速度与动摩擦系数相关,角形粒子则不相关。
从前面的所有实验可以看出临界冲击速度可以与硬度,动摩擦系数等机械性能联系起来尽管如此,仍然没有单独或者一系列参数能与固态粒子和目标材料直接联系起来。
更加值得注意的是,对于角形粒子来说粒子的形状也可决定临界冲击速度。
包含着以上各参数的公式在第一页[9]中。
图11.冲击样品与粒子的维氏硬度比例和球形粒子冲击速度的关系
图12.不同冲击条件下球星粒子的冲击速度与摩擦系数的关系
5.结论
1.通过旋转目标仪测试摩擦系数的方法确定了。
2.通过固态粒子冲击时的摩擦系数来测量临界冲击速度的方法确定了。
3.临界冲击速度取决于固态粒子和样品的机械性能。
4.球形粒子的临界冲击速度与摩擦系数以及固态粒子和样品的硬度有关,角形粒子的临界冲击速度除以上两点外还需考虑粒子形状。
鸣谢
这次研究的得到了教育部自然基金(第07455292)的部分支持。
作者希望感谢Messrs.H.Ishibashi,S.Kawase,Y.Nishino,T.Kawabata,J.Shimazumi,Y.Tabata,M.Kakimi,T.Katsuki和F.Takenaga在实验过程中给予的帮助。
参考文献
[1]J.G.A.Bitter,Wear6(1963)5and169.
[2]M.Matsummura,Y.Oka,M.Yamawaki,Proc.7thint.Conf.onErosionbyLiquidandSolidImpact,paper40,Cambridge,1987.
[3]Y.Oka,M.Matsummura,M.Yamawaki,M.Sakai,ASTMSTP946(1987)141.
[4]M.Matsummura,Corros.Rev.12(1994)321
[5]C.A.Coulomb,MemoriesdeMathematiqueetdePhaysiquedeI’AcademieRoyaldeSciences,1785,p.161.
[6]F.P.Bowden,P.A.Persson,Proc.R.Soc.A260(1960)433
[7]A.D.Salman,A.Verba,Zs.Lukenics,M.Szavo,PERIOD.Polytech.Chem.Eng.35(1991)43.
[8]K.Wellinger,H.Uetz,Wear1(1957)225.
[9]A.Yabuki,K.Matsuwaki,M.Matsumura(1998)(paperisWEA8260).