汽车试验技术第十章汽车室内台架试验系统.docx
《汽车试验技术第十章汽车室内台架试验系统.docx》由会员分享,可在线阅读,更多相关《汽车试验技术第十章汽车室内台架试验系统.docx(18页珍藏版)》请在冰豆网上搜索。
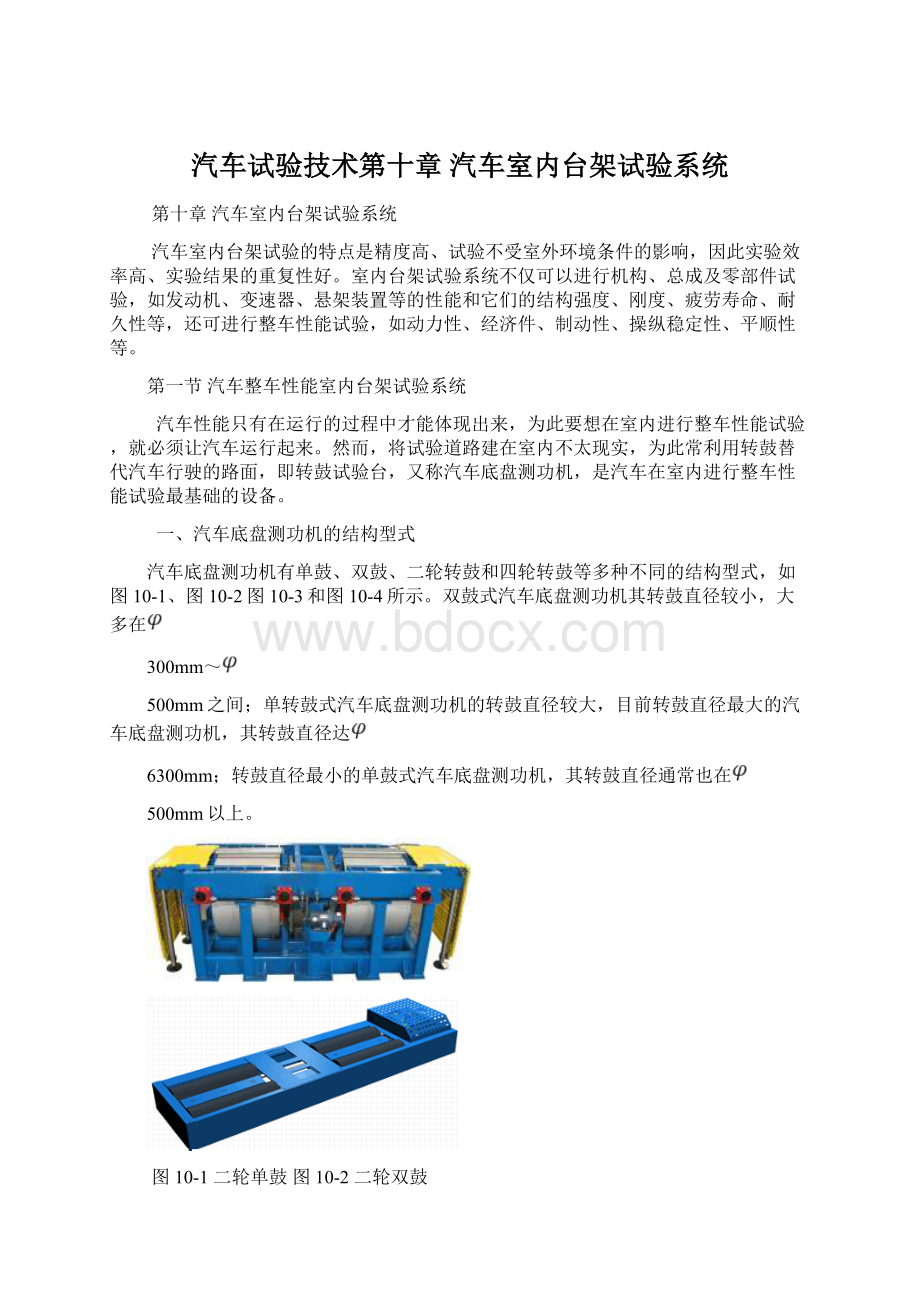
汽车试验技术第十章汽车室内台架试验系统
第十章汽车室内台架试验系统
汽车室内台架试验的特点是精度高、试验不受室外环境条件的影响,因此实验效率高、实验结果的重复性好。
室内台架试验系统不仅可以进行机构、总成及零部件试验,如发动机、变速器、悬架装置等的性能和它们的结构强度、刚度、疲劳寿命、耐久性等,还可进行整车性能试验,如动力性、经济件、制动性、操纵稳定性、平顺性等。
第一节汽车整车性能室内台架试验系统
汽车性能只有在运行的过程中才能体现出来,为此要想在室内进行整车性能试验,就必须让汽车运行起来。
然而,将试验道路建在室内不太现实,为此常利用转鼓替代汽车行驶的路面,即转鼓试验台,又称汽车底盘测功机,是汽车在室内进行整车性能试验最基础的设备。
一、汽车底盘测功机的结构型式
汽车底盘测功机有单鼓、双鼓、二轮转鼓和四轮转鼓等多种不同的结构型式,如图10-1、图10-2图10-3和图10-4所示。
双鼓式汽车底盘测功机其转鼓直径较小,大多在
300mm~
500mm之间;单转鼓式汽车底盘测功机的转鼓直径较大,目前转鼓直径最大的汽车底盘测功机,其转鼓直径达
6300mm;转鼓直径最小的单鼓式汽车底盘测功机,其转鼓直径通常也在
500mm以上。
图10-1二轮单鼓图10-2二轮双鼓
图10-3四轮单鼓图10-4四轮双鼓
汽车底盘测功机的结构型式和转鼓直径的大小对实验精度有很大影响。
要想获得高精度的测试结果,常采用大直径的单转鼓式汽车底盘测功机。
其原因是:
当转鼓直径
远大于汽车车轮直径
时,车轮在转鼓上行驶的动力学特征与在道路上行驶时的动力学特征十分接近,即转鼓曲率对测试精度的影响非常小。
理论和实践都表明,当转鼓直径达到6m以上时,转鼓曲率对测试结果的影响几乎可以完全忽略不计;若继续增大转鼓的直径,对测试精度的贡献已微乎其微,但设备的制造成本却会大幅上升。
正因为如此,在进行高精度汽车动力性和经济性试验时,多采用大直径单鼓式汽车底盘测功机,尤其是大直径四轮单鼓式汽车底盘测功机。
即便是对于单轴驱动的汽车亦是如此,因为四轮转鼓能准确再现汽车行驶时的滚动阻力。
由于大直径单鼓式汽车底盘测功机的体积庞大、制造成本因转鼓直径的增大而大幅提高,因此,对于滚动阻力的大小对测试结果不构成明显影响的试验项目,如汽车噪声、排放、行驶可靠性与耐久性等试验项目则通常采用体积小、制造成本较低的双鼓式或转鼓直径相对较小的单鼓式汽车底盘测功机。
对于双鼓式汽车底盘测功机,由于转鼓直径不可能做得很大,因此转鼓曲率对测试结果的影响不可忽视。
不仅如此,由图10-5不难看出,车轮在双鼓上运行的受力状态与在道路上行驶时的受力状态完全不同。
汽车在双鼓式底盘测功机上运行时,车轮由二个转鼓支承,其支承力
和
与车轮的垂直载荷
间的夹角为
,若忽略车轮驱动力所带来的转鼓支承力的变化,则此三力之间的关系是:
(10-1)
由于
,因此
,汽车在转鼓上行驶的滚动阻力比在道路上行驶的阻力大。
车轮半径越大,
越小,
与
的差值越小;车轮半径越小,
越大,
与
的差值越大。
此外,由于汽车在双转鼓上车轮与转鼓的作用状态与在路面上的作用状态存在很大的差异,由此亦会带来较大的测试误差。
图10-5双鼓式底盘测功机车轮在转鼓上的受力
二、汽车底盘测功机的结构原理
汽车底盘测功机主要有测功机、传感器、转鼓组件、控制系统与车辆固定装置等组成,如图10-6所示。
转鼓组件4是汽车室内性能试验的行驶“路面”;汽车在室内试验时,由于汽车没有移动,只是车轮推动转鼓转动,汽车在道路上行驶的空气阻力、坡道阻力及加速阻力均不存在,因此需要借用测功机1模拟汽车行驶时的空气阻力、坡道阻力及加速阻力;为了得到测试结果,需要在汽车底盘测功机上安装各种传感器,如转矩传感器、转速传感器等;为了获得所需的测试精度,需对模拟汽车行驶的各种阻力及汽车的驾驶操作进行准确控制,其控制对象是测功机1和自动驾驶仪2;为保证汽车在底盘测功机安全可靠运行,需要一套专用的车辆固定装置9。
(a)(b)
图10-6汽车底盘测功机的组成
(a)汽车底盘测功机的外形(b)底盘测功机的组成
1—电力测功机,2—自动驾驶仪,3—测试用传感器,4—转鼓,
5—显示器,6—实验室中心机房,7—主控计算机,8—电源柜,9—车辆固定装置
汽车底盘测功机的核心部分是测功机和计算机控制系统,当然,为了满足某些特殊性能试验的需要,需对汽车底盘测功机的机械部分(转鼓组件、动力传动装置、测功机等)进行特殊设计。
如要在室内测试汽车的行驶噪声,需要用专门设计的低噪声汽车底盘测功机。
测功机有水力、电涡流和电力等多种不同的结构型式。
由于电力测功机既可模拟汽车行驶时的各种阻力,又可利用其驱动功能模拟汽车的惯性,因此装用电力测功机的汽车底盘测功机具有最优的各项性能。
此外,电力测功机在模拟汽车行驶阻力的过程中处于发电模式,汽车车轮施加给测功机的机械能被转换为电能并回馈给电网,因此它具有良好的节能效果。
水力侧功机和电涡流测功机都不具有驱动功能,为了模拟汽车行驶时的惯性,常在汽车底盘测功机上配有可自由组合的惯性飞轮组。
计算机控制系统是汽车底盘测功机的“神经中枢”,控制试验的全过程。
底盘测功机性能的优劣在很大程度上取决于计算机控制系统软件的功能。
三、汽车整车室内台架试验的内容
汽车整车室内台架试验的内容十分丰富,除前面述及的汽车动力性和经济性的各项性能外,室内台架试验还可以进行汽车制动性能(见图8-4)、汽车低高温环境实验(见图1-13a)、汽车噪声试验(见图1-13b)、汽车操纵稳定性试验、汽车行驶平顺性试验、汽车排放试验及其他各类研究性试验。
汽车动力性、经济性、噪声、环境、可靠性与耐久性等的室内试验,所用的主体基础设备都是汽车底盘测功机,对于不同的试验项目,视其试验内容和要求的不同,在室内构建与之相适应的测试环境,并补充相应的传感器就可完成相关的试验,故在此不再展开讨论。
下面仅对实验设备较为特殊的汽车操纵稳定性和行驶平顺性试验作简要介绍。
1、汽车操纵稳定性试验系统
由于汽车操纵稳定性试验直接影响到行车安全,因此世界各大汽车公司都十分重视。
但汽车操纵稳定性的实车试验往往比较困难,如:
高速蛇行、高速回正、转向盘转角脉冲、转向盘转角阶跃等项目的试验。
除此之外,还有更极端工况的试验,如汽车高速紧急避障、汽车下陡坡失去速度控制状态下的急转等试验在实车上几乎根本不可能进行,但类似的上述极端工况在实际的行驶过程中不时还会发生。
为很好地解决汽车操纵稳定性问题,有些汽车公司开始利用模拟试验台(见图10-7)进行汽车操纵稳定性试验。
汽车操纵稳定性模拟试验台主要有驾驶舱3、驾驶模拟器2、汽车行车场景显示系统1、液压伺服系统4、计算机
图10-7汽车操纵稳定性模拟试验台
1—行驶场景显示器,2--驾驶模拟器,3—驾驶仓,4—液压伺服系统,5—计算机控制系统
控制系统5及各种传感器等组成。
传感器的选用由试验内容确定:
对于前面所述的汽车操纵稳定性实验内容,需装用的传感器有激光陀螺、车身三向加速度传感器、转向盘转角/转矩传感器(有的操纵稳定性模拟试验台自带转向盘转角/转矩传感器)等。
传感器的安装和在汽车上的安装相同。
将汽车的整车参数及与汽车操纵稳定性相关的汽车总成部件的参数(如车轮的垂直与测向刚度、悬架的刚度与阻尼比、转向器的结构型式、转向系统的刚度与阻尼、整车质量与轴荷分配等等)、试验所需要的道路状态参数与试验内容等输入模拟试验台的计算机控制系统,计算机控制系统便可配制出试验所需的试验场景并控制液压伺服系统根据试验操作的要求同步驾驶仓的运动。
2、汽车行驶平顺性试验系统
汽车行驶平顺行驶性台架试验需在专门的单鼓四轮式汽车底盘测功机上进行,如图10-8所示。
该底盘测功机与前面述及的单鼓四轮式汽车底盘测功机的最大区别是:
四个转鼓不是固定的,它可以根据所加载的路谱作上下运动;
转鼓表面装有与所试路面状态接近的一层特殊组件(见图10-9)。
需进行在不同路面上的行驶平顺性试验时,只需更换安装在转鼓表层的与所试路面相对应的组件,并输入相应的路谱,试验时汽车底盘测功机的四个转鼓在转动的同时依据路谱进行振动。
该底盘测功机除可进行室内汽车行驶平顺性试验外,还可以进行汽车整车的行驶可靠性与耐久性试验。
图10-8汽车行驶平顺性试验台图10-9转鼓表面状态
第二节汽车整车道路振动模拟试验系统
汽车整车的振动特性、汽车结构件与传力部件的结构疲劳强度、整车异响评估、汽车悬架与车身的可靠性耐久性等性能参数,是汽车研发过程中必须的重要技术资料。
为了快速方便地获得这些性能参数,目前国际上的汽车制造商普遍采用汽车整车道路振动模拟试验系统。
一、汽车整车道路振动模拟试验设备
汽车整车道路振动模拟试验于上个世纪六十年代中期开始用于研究汽车整车可靠性,近些年该项试验技术的发展十分迅速,其应用范围已拓展到了整车异响评估、噪声与汽车整车动态特性研究等领域。
汽车整车道路振动模拟试验的工作原理是:
根据引起汽车疲劳损伤的主要因素,编排汽车在典型道路或汽车试验场行驶的路面,采集汽车在典型道路或汽车试验场行驶过程中车轮轴头的振动响应信号,通过对所采信号的编辑和处理,获得汽车在行驶过程中的道路谱;然后,将汽车置于汽车整车道路振动模拟试验台上进行试验。
在试验的起始阶段,先将汽车视作一个未知的控制系统,给车轮激振器一个噪声信号的驱动,通过测量该噪声信号产生的车轴响应及计算频率响应函数识别该未知系统。
编排后的道路谱信号是道路振动模拟试验期望得到的响应信号,将测得车轴的频率响应函数信号与之进行比较,并通过反复迭代计算逐渐修正初始驱动信号,以得到模拟路面行驶所需的高精度目标驱动信号。
再将获得的目标驱动信号作为输入进行试验。
汽车整车道路振动模拟试验台有电动式和电控液压伺服式两种,由于电控液压伺服式道路模拟振动试验台具有制造成本相对较低且性能优良的特点,因此得到了广泛的应用。
汽车整车道路振动模拟试验台由液压站、带车轮(或车轴)托架的液压伺服激振器、路谱模拟控制器等组成。
早期的汽车道路振动模拟试验台大多采用单轴式结构,如图10-10所示。
尽管单轴振动试验方法作为一种通用试验方法的实用性已经为工程试验所证实,并以此为基础制定了许多振动环境试验的标准和规范,但用单轴振动模拟汽车实际运行过程中的多轴振动环境的真实性仍受到质疑。
为了获得更加精确、可靠的试验结果,三轴六自由度的汽车整车道路振动模拟试验系统受到了行业各界的广泛重视,已成为汽车制造与产品研发部门的主流设备。
美国MTS公司生产的MTS329型汽车整车道路振动模拟试验台(如图10-11所示)除具有前面述及的全部试验功能外,还增设了转向模拟功能,即可以模拟汽车转向行驶时所产生的附加侧向力,因此试验结果更加真实可靠。
图10-10单轴汽车道路振动模拟试验台图10-11三轴六自由度的汽车整车道路振动模拟试验台
第三节汽车排放试验系统
自1957年美国加州颁布实施世界上第一部汽车排放法规以来,世界各国陆续制定了自己的汽车排放法规。
由于我国汽车产业的发展相对比较滞后,因此直到1983年才出台了第一份汽车排放标准,其内容是检测汽油车怠速污染物浓度和柴油车自由加速的烟度。
但到上个世纪末,由于汽车保有量的快速增长,汽车所带来的大气环境污染日益严重。
我国对大城市大气环境监测的结果表明,汽车排放对大气环境污染的贡献率已超过60%以上。
为了改善大气环境质量,我国自2001年开始改变过去只检测汽油车怠速污染物浓度和柴油车自由加速烟度的方法,引进欧共体的汽车排放标准体系,制定了我国的第一部汽车排放法规,对新开发的车型采用工况法检测汽车排放有害气体的总量。
由于受设备条件和可操作性等因素的限制,对于新车的出厂检验和在用车,沿用老标准直到2005年才出台了新的简易工况法的汽车排放标准。
一、汽油车双怠速及简易工况法排放测试系统
我国汽车排放标准GBl8285—2005《点燃式发动机汽车排气污染物排放及测量方法(双怠速法及简易工况法)》中所述及的双怠速是指:
发动机的怠速和“高怠速”二种运行状态。
严格地讲,发动机的怠速只有一个,即发动机不带任何负荷状态下的最低稳定转速。
标准中的高怠速是为了表达方便而创造出的一个特殊名词(发动机原本只有一个怠速,不存在所谓的高怠速),国标规定,轻型汽车的高怠速转速为2500±100r/min;重型车的高怠速转速为1800±100r/min。
双怠速排放的测试方法是:
测试发动机怠速运行和高怠速运行工况所排出废气中HC、CO和NOX等有害气体的浓度。
国标中定义的简易工况有三种,即:
稳态工况、瞬态工况和简易瞬态工况,对于机动车保有量大、污染严重的地区,可任选其中一种。
由于瞬态工况和简易瞬态工况排放检测的测定值是汽车按照规定的工况行驶,每一公里所排出HC、CO、NOX和CO2等气体成分的克数,其检测设备应具有和下面将要介绍的“工况法”所用设备相同的功能,因此很少在实际中得到应用。
稳态工况排放检测,国标定义了二个匀速运行工况:
一是汽车在底盘测功机上以25±1.5km/h的车速、50%的负荷匀速运行;二是汽车在底盘测功机上以40±1.5km/h的车速、25%的负荷匀速运行。
测试此二个工况下汽车排气中HC、CO和NOX等有害气体的浓度。
综上所述,双怠速排放测试所需的测试设备是能够检测HC、CO和NOX等三种有害气体的废气分析仪。
目前用得较多的是四气或五气分析仪,如图10-12所示;对于稳定工况的汽车排放检测,则需要将图10-12所示的四气或五气分析仪与图10-1和图10-2所示的汽车底盘测功及配合使用。
图10-12五气分析仪
二、柴油车烟度测试系统
GB3847—2005《车用压燃式发动机和压燃式发动机汽车排气烟度排放限值及测量方法》中规定,柴油车应对发动机全负荷稳定运转、自由加速及加载减速等运行状态的烟度进行检测。
关于烟度的检测,目前的主流设备是不透光式烟度计,如图8-7所示。
欲检测发动机全负荷稳定运转及加载减速等运行状态的烟度,还需调用汽车底盘测功机。
三、工况法汽车排放测试系统
我国汽车排放法规所规定的工况法采用的是欧共体的排放体系,测试汽车按照规定的15个工况运行四个循环加上400S的郊外高速运行工况全过程平均每公里所排出HC、CO、NOX和PM(碳烟)等有害气体的质量(g)。
由于工况法汽车排放测试需要模拟较为复杂的汽车运行工况,因此需要使用性能良好的高精度汽车底盘测功机;汽车排放污染物测试需采用硬、软件设备有:
汽车排放定容稀释采样系统、多组份排放分析系统、颗粒物测试系统、汽车排放检测控制系统和汽车排放测试主控软件系统等,如图10-13所示。
1、汽车排放定容稀释采样系统
要想准确的检测出汽车尾气中CO、HC、NOX等有害气体的质量,目前常采用的方式是:
利用清洁空气对排气进行稀释(稀释用清洁空气的量是汽车排出废气的8倍以上),然后采用汽车排放定容稀释采样系统,检测稀释后样气的浓度,便可计算出单位行驶里程的CO、HC、NOX质量。
试验控制与数据处理由计算机控制自动完成。
图10-13汽车排气污染物测试系统
1--定容稀释采样系统,2--多组份排放分析系统,3--颗粒物测试系统,4--汽车排放检测控制系统
2、多组份排放分析系统
多组份排放分析系统有直接模态大量检测、稀释尾气检测、实时连续检测多种不同的数据处理方式,检测的气体包括CO、CO2、HC、NOX、O2等成分。
3、颗粒物测试系统
颗粒物测试常用的有扩散荷电法和部分流法二种不同的测试方式。
扩散荷电法的测试原理是汽车排出的废气经喷射泵稀释后,使气体离子带电,通过测量电流数值从计算颗粒物的浓度;部分流法的测试原理是按照一定比例对排气进行采样、稀释,然后通过过滤的方式采集并测试稀释排气中的颗粒物的质量。
4、汽车排放检测控制系统
汽车排放检测控制系统的作用是对汽车排气污染物测试系统全工作过程的自动跟踪控制,其控制内容包括汽车底盘测功机的工况模拟控制和汽车排气的稀释与检测控制二大部分,是汽车排气污染物测试系统的中枢神经系统。
第四节汽车主要总成室内台架试验系统
汽车是一个由多总成部件构成的十分复杂的机电一体化系统,任何一个总成部件的质量与设计缺陷,都会对汽车整车性能构成极大的危害,为此汽车业界都十分重视汽车总成部件的试验工作。
此外,汽车总成部件的种类、数量特别繁多,汽车总成部件的试验设备必然十分繁杂,试验设备的种类、数量和试验内容比整车试验要多得多,由于受篇幅的限制不可能逐一介绍,在此只给出几个主要典型总成部件试验系统的示例。
一、发动机台架试验系统
发动机是汽车中结构最复杂、要求最高的总成,汽车各项性能直接或间接地受发动机性能的影响,因此在发动机的研发过程中需要做各类大量的试验。
图10--14是发动机性能与道路行驶模拟试验系统,可以完成发动机的速度特性、负荷特性、万有特性、调速特性、可靠性耐久性及模拟汽车在道路上行驶时发动机的运行工况等试验;图10-15是发动机的噪声试验系统,用于测试或研究发动机的工作噪声;图10-16是发动机的排放试验系统,可以用来进行发动机的各类排放试验;图10-17是发动机消声器试验系统,用于测试或研究消声器的消声特性;图10-18是发动机转动惯量测试系统,可以方便快捷地测出发动机的转动惯量。
图10-14发动机性能与道路行驶模拟试验系统
图10-15发动机噪声试验系统图10-16发动机排放试验系统
图10-17发动机消声器试验系统图10-18发动机转动惯量测试系统
二、汽车动力与传动试验系统
业内人士都知道,将国际上性能最优的汽车总成部件组合起来装配成一辆汽车,并非一定能获得优良的整车性能,这便揭示了系统匹配的重要性。
汽车动力与传动试验系统是从事汽车动力与传动系统研发与匹配研究不可或缺的重要工具。
它不仅可以用于汽车动力与传动系统开发、性能研究(整车动力性、经济性、可靠性、排放与噪声),更重要的是,在汽车动力与传动系统的各总成部件开发的前期,就可以借助于汽车动力与传动试验系统进行汽车整车性能的预测与评估、修正与确定传动系统的结构与性能参数,如此不仅可以大大缩短汽车产品的开发周期,而且还可以有效的规避产品研发风险。
图10-19和图10-20是发动机前置前轴驱动轿车动力与传动试验系统和四轮驱动轿车动力与传动试验系统,主要用于汽车新产品开发前期的系统匹配与整车性能研究。
事实上,图10-20所示的动力与传动试验系统可用于发动机前置后轴驱动、发动机中置后轴驱动及发动机后置后轴驱动的各类汽车。
图10-21所示的测试系统主要用于汽车动力与传动系统的噪声研究。
图10-22所示的试验系统可以用于完整汽车底盘的各项性能研究。
图10-19发动机前置前轴驱动轿车动力与传动试验系统
图10-20四轮驱动汽车动力与传动试验系统图10-21四轮驱动汽车动力与传动噪声试验系统
图10-22汽车底盘实验系统
三、传动系统主要总成部件试验系统
1、变速器、离合器试验系统
图10-23是汽车变速器与离合器综合性能试验系统,可以对变速器传动效率、运转平稳性、动力传动能力、可靠性耐久性、变速操纵机构、离合器的传扭能力、摩擦片的寿命、离合器结合的平稳性、离合器操纵力等内容进行测试。
图10-23变速器与离合器试验系统
2、传动轴试验系统
图10-24是汽车传动轴试验系统,可以按照设定的主从动轴夹角变化规律模拟汽车行驶工况对其进行各项性能试验,为研究传动轴的结构、性能、寿命及开发新产品提供技术支持。
图10-24传动轴试验系统
图10-25至图10-28分别是汽车悬架、驱动桥、座椅和制动器试验系统,事实上还有许许多多的各类汽车总成部件试验系统,在此不再一一介绍。
图10-25汽车悬架试验系统
图10-26驱动桥试验系统图10-27汽车座椅试验系统
图10-28汽车制动器试验系统