力学性能试验操作工艺规程DOC复习课程.docx
《力学性能试验操作工艺规程DOC复习课程.docx》由会员分享,可在线阅读,更多相关《力学性能试验操作工艺规程DOC复习课程.docx(15页珍藏版)》请在冰豆网上搜索。
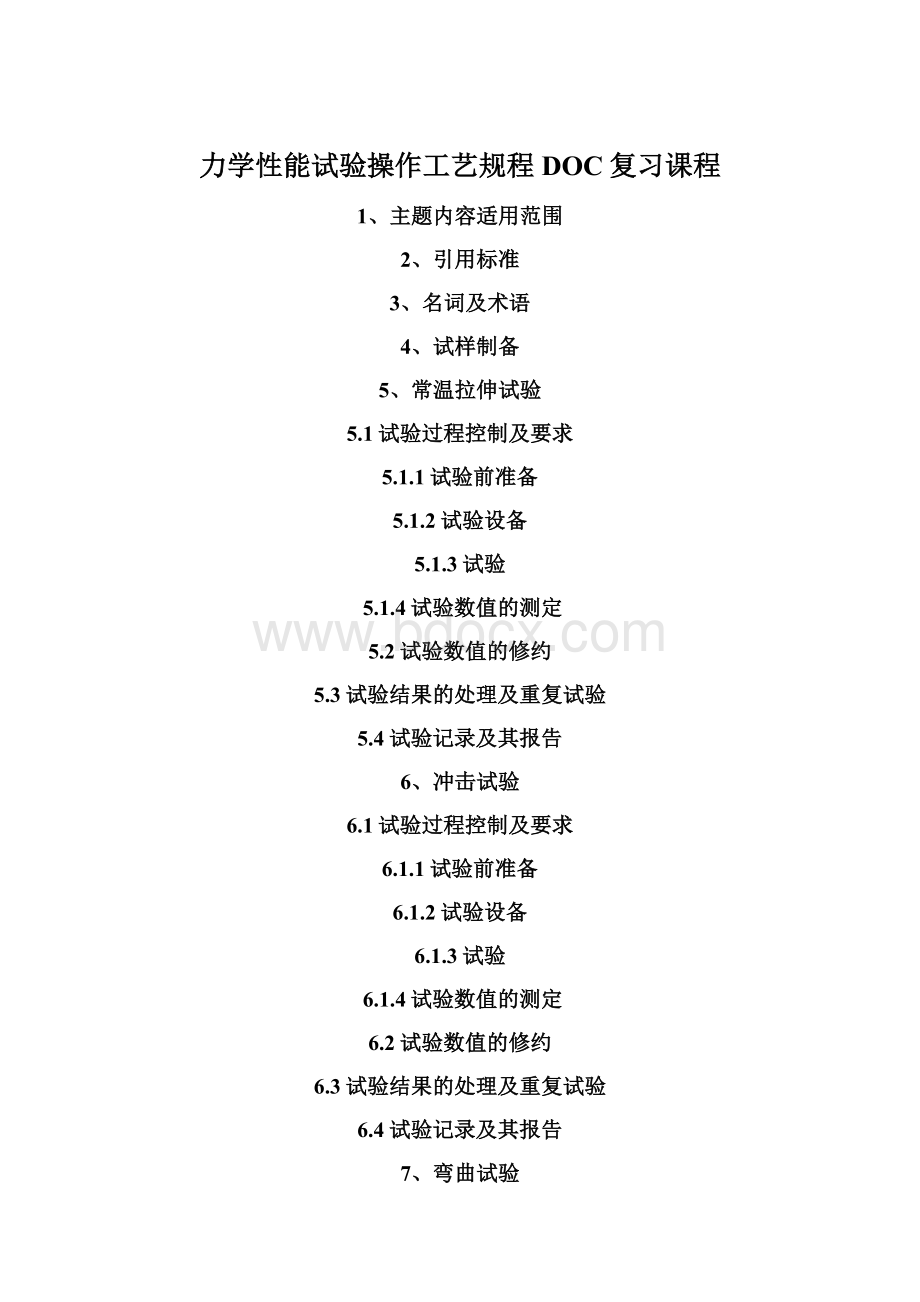
力学性能试验操作工艺规程DOC复习课程
1、主题内容适用范围
2、引用标准
3、名词及术语
4、试样制备
5、常温拉伸试验
5.1试验过程控制及要求
5.1.1试验前准备
5.1.2试验设备
5.1.3试验
5.1.4试验数值的测定
5.2试验数值的修约
5.3试验结果的处理及重复试验
5.4试验记录及其报告
6、冲击试验
6.1试验过程控制及要求
6.1.1试验前准备
6.1.2试验设备
6.1.3试验
6.1.4试验数值的测定
6.2试验数值的修约
6.3试验结果的处理及重复试验
6.4试验记录及其报告
7、弯曲试验
7.1试验过程控制及要求
7.1.1试验前准备
7.1.2试验设备
7.1.3试验
7.1.4试验数值的测定
7.2试验结果的处理及重复试验
7.3试验记录及其报告
8、硬度试验
8.1试验过程控制及要求
8.1.1试验前准备
8.1.2试验设备
8.1.3试验
8.1.4试验数值的测定
8.2试验数值的修约
8.3试验结果的处理及重复试验
8.4试验记录及其报告
9、压扁试验
9.1试验过程控制及要求
9.1.1试验前准备
9.1.2试验设备
9.1.3试验
9.2试验结果的评定
9.3试验结果的处理及重复试验
9.4试验记录及其报告
前言
为加强技术管理,严格操作规程,保证力学性能试验工作更好地为公司的生产和检验服务,根据我公司理化试验室的试验项目要求,结合试验室现有试验设备,吸取和参考了相应的试验标准及验收标准的基础上以规范性与准确性为原则,经深入地学习和探索,并经系统的总结和整理,编写成了这本“力学性能试验操作工艺规程”。
本标准由质量管理部提出并归口。
本标准起草单位:
质量管理部。
本标准起草人:
。
本标准由质量管理部负责解释。
1、主题内容与适用范围
1.1本标准文件对原材料、焊接接头等的力学性能试验的操作过程进行了规定,同时针对不同产品类型所涉及的试验要求进行了阐述,以满足不同的验收标准的要求。
1.2本标准文件适用于对原材料、焊接接头进行常温拉伸,冲击[常温、低温冲击(10~-60℃)],弯曲(三点式),硬度(布氏、洛氏、维氏、里氏),压扁的力学性能试验的操作工艺规程。
2.引用标准
下列标准所包含的条文,通过在本标准中引用而构成为本标准的条文。
本标准出版时,所示版本均为有效。
所有标准都会被修订,使用本标准的各方应探讨使用下列标准最新版本的可能性。
GB228—2002金属材料室温拉伸试验方法
GB229—1994金属夏比缺口冲击试验方法
GB230—91金属洛氏硬度试验方法
GB231—84金属布氏硬度试验方法
GB246—97金属管压扁试验方法
GB4340—99金属维氏硬度试验方法
GB232—99金属材料弯曲试验方法
GB/T14452—93金属弯曲力学性能试验方法
GB2650—89焊接接头冲击试验方法
GB2651—89焊接接头拉伸试验方法
GB2652—89焊缝及熔敷金属拉伸试验方法
GB2653—89焊接接头弯曲及压扁试验方法
GB2654—89焊接接头及堆焊金属硬度试验方法
GB8170—87数值修约规则
GB12160—2002单轴试验用引伸计的标定
ASME材料篇
JB4708—2000钢制压力容器焊接工艺评定
DG0509—1999原材料及焊缝试样的制备
蒸汽锅炉安全技术监察规程
JB4744—2000钢制压力容器产品焊接试板的力学性能检验
SD340—89火力发电厂锅炉压力容器焊接工艺评定
3.名词及术语
3.1标距
测量伸长用的试样圆柱或棱柱部分的长度。
3.2原始标距(L0)
施力前的试样标距。
3.3断后标距(Lu)
试样断裂后的标距
3.4平行长度(Lc)
试样两头部或两夹持部分(不带头试样)之间平等部分的长度。
3.5伸长率
原始标距的伸长与原始标距之比的百分率。
3.6断后伸长率(A)
断后标距的残余伸长与原始标距之比的百分率。
3.7引伸计标距(Le)
用引伸计测量试样延伸时所使用试样平行长度部分的长度。
3.8断面收缩率(Z)
断裂后试样横截面积的最大缩减量(S0-Su)与原始横截面积(S0)之比的百分率。
3.9最大力(Fm)
试样在屈服阶段之后所能抵抗的最大力。
对于无明显屈服(连续屈服)的金属材料,为试验期间的最大力。
3.10应力
试验期间任一时刻的力除以试样原始横截面积(S0)之商。
3.11抗拉强度(Rm)
相应最大力(Fm)的应力
3.12屈服强度
当金属材料呈现屈服现象时,在试验期间达到塑性变形发生而力不增加的应力点,应区分上屈服强度和下屈服强度。
3.13上屈服强度(ReH)
试样发生屈服而力首次下降前的最高应力
3.14下屈服强度(ReL)
在屈服期间,不计初始瞬时效应的最低应力。
3.15规定非比例延伸强度(Rp)
非比例延伸率等于规定的引伸计标距百分率时的应力。
3.16规定总延伸强度(Rt)
总延伸率等于规定的引伸计标距百分率时的应力。
3.17冲击吸收功
规定形状和尺寸的试样在冲击试验力一次作用下折断时所吸收的功。
3.18跨距
弯曲试验装置上试样两支承点的距离。
3.19弯曲力
垂直于试样两支承点间连接的横向集中力。
3.20面弯
试样受拉面为焊缝正面的弯曲。
具有较大焊缝宽度的面称为正面;当两面焊缝宽度相等则先完成盖面层焊缝的一侧为正面。
3.21背弯
试样受拉面为焊缝背面的弯曲。
3.22侧弯
试样受拉面为焊缝横截面的弯曲。
4.试样制备
4.1应按照相关产品标准或GB/T2975—98的要求切取样坯和制备试样。
4.2试样的制备应避免由于加工硬化或过热而影响金属的力学性能。
4.3试样的形状和尺寸应符合相关标准和产品技术要求。
5.常温拉伸试验
5.1操作过程控制及要求
5.1.1试验前准备
5.1.1.1原始横截面积的测定应选用合适的量具或测量装置,当横截面尺寸大于2.0~10.0时量具或测量装置的分辨率应不大于0.01,当横截面尺寸>10.0时,其分辨率应不大于0.05。
5.1.1.2原始标距(L0)的标记应用小标记、细划线或细墨线标记原始标距,但不得用引起过早断裂的缺口作标记。
对于比例试样,应将原始标距的计算值修约至最接近5mm的倍数,中间数值向较大一方修约。
原始标距的标记应准确到±1%。
如平行长度(L0)比原始标距长许多,例如不经机加工的试样,可以标记一系列重叠的原始标距。
有时,可以在试样表面划一条平行于试样纵轴的线,并在此线上标记原始标距。
5.1.2试验设备
5.1.2.1试验机应按照GB/T16825进行检验并应为I级或优于I级的准确度。
5.1.2.2引伸计的准确度级别应符合GB/T12160的要求,测定上屈服强度、下屈服强度,规定非比例延伸强度,规定总延伸强度,应使用不劣于C级准确度的引伸计。
5.1.3试验
5.1.3.1试验速率:
除非产品标准另有规定,试验速率取决于材料特性并应符合要求。
5.1.3.1.1测定屈服强度时的试验速率:
当材料弹性模量E<150000N/mm2时,夹头分离速率应在2~20N/mm2.S-1范围内;当E>150000N/mm2时,夹头分离速率应在6~60N/mm2.S-1范围内,否则将影响测定结果。
5.1.3.1.2测定抗拉强度(Rm)的试验速率:
塑性范围内时,平等长度的应变速率不应超过0.008/s;弹性范围内时,如试验不包括屈服强度或规定强度的测定(如焊接接头),试验机的速率可以达到塑性范围内允许的最大速率。
5.1.3.2试样的夹持:
应使用例如楔形夹头、螺纹夹头,套环夹头等合适的夹具夹持试样并应尽最大的努力确保夹持的试样受轴向拉力的作用。
5.1.3.3引伸计的夹持:
对于无明显屈服点的材料,应测定规定非比例延伸强度(Rp0.2)或规定总延伸强度(Rt0.2)。
其引伸计的夹持应位于平行长度(Lc)的中部,并应夹持牢靠,其夹持点连线应平行于试样拉伸轴线方向。
5.1.4试验数值的测定
5.1.4.1断后伸长率的测定:
应将试样断裂的部分仔细地配接在一起使其断裂部分适当接触并使其轴线处于同一直线上,采用分辨率优于0.1mm的量具或测量装置测定断后标距(Lu),准确到±0.25mm。
5.1.4.2屈服强度的测定:
对于呈现明显屈服(不连续屈服)现象的金属材料,可采用指针法直接读取测力度盘指针首次回转前指示的最大力和不计初始瞬时效应时屈服阶段中指示的最小力或首次停止转动指示的恒定力。
将其分别除以试样原始横截面积(S0)以得到上屈服强度和下屈服强度。
对于无明显屈服(不连续屈服)现象的金属材料,应按标准要求测定其规定非比例延伸强度(RP0.2)或规定总延伸强度(Rt0.5)。
规定非比例延伸强度(RP0.2)可按以下图解法测定,以试验机绘制的力—夹头位移曲线测定规定非比例延伸率为0.2%时的强度作为其强度值。
图解法:
用自动记录方法绘制力—伸长曲线时,力轴每毫米所代表的应力,一般应不大于10N/mm2,曲线的高度应使Fp处于力轴量程的二分之一以上。
伸长放大倍数n的选择应使下图中的OC段的长度不小于5mm。
在曲线上,自弹性直线段与伸长轴交点O起,截取一相应于规定非比例伸长的OC段[OC=n×Le×0.2%(n为伸长放大倍数,Le为引伸计标距)],过C点作弹性直线段的平行线CA交曲线与A点,A点所对应的力Fp为所测规定非比例延伸力,规定非比例延伸强度按下式计算:
RP0.2=Fp/S0(S0为试样原始横截面积)
规定总延伸强度(Rt0.5)可采用引伸计测出规定总延伸率为0.5%时的强度为规定总延伸强度(Rt0.5)。
5.1.4.3抗拉强度的测定:
可采用指针法直接读取测力度盘上所指示的试验过程中的最大力,并除以试样原始截面积S0而得到。
5.1.4.4断面收缩率(Z)的测定:
将试样断裂部分仔细地配接在一起,使其轴线处于同一直线上。
对于圆形横截面试样,在缩颈处相互垂直方向测量直径,取其算术平均值计算最小横截面积;对于矩形横截面试样,测量缩颈处的最大宽度和最小厚度,两者之乘积为断后最小横截面积。
原始横截面积(S0)与断后最小横截面积(Su)之差除以原始横截面积的百分率得到断面收缩率(Z)。
5.2试验数值的修约
试验测定的性能结果数值应按下表的要求进行修约。
修约的方法按照GB/T8170
性能结果数值的修约间隔
性能
范围
修约间隔
ReH,ReL,Rp,Rt,Rm
≤200N/mm2
>200~1000N/mm2
>1000N/mm2
1N/mm2
5N/mm2
10N/mm2
A
/
0.5%
Z
/
0.5%
5.3试验数值的处理及重复试验
5.3.1试验出现下列情况之一其试验数值无效,应重做同样数量的试样进行试验:
a)试样断在标距处或断在机械刻划的标距标记上,而且断后伸长率小于规定最小值;
b)试验期间设备发生故障,影响了试验数值。
5.3.2试验后试样出现两个或两个以上的缩颈以及显示出肉眼可见的冶金缺陷(例如分层、气泡、夹渣、缩孔等),应在试验记录和报告中注明。
5.3.3断后伸长率的测定,原则上只有断裂处与最接近的标距标记的距离不小于原始标距的1/3情况方为有效。
但断后伸长率大于或等于规定值,不管断裂位置处于何处,测量均为有效。
5.3.4试验结果的评定应按相应的验收标准或产品技术条件所要求的项目及合格范围进行综合评定。
5.3.5当有某项不合格时,应从原检验试件中取双倍位伸试样复验或将原检验试件与产品再热处理一次后进行全面复验,重复试验后的结果确定评定可再次按相应验收标准的相应条款进行评定。
5.4试验记录及其报告
5.4.1应有正式记录备查,且试验记录的保管期限至少应为五年。
5.4.2试验报告一般应包括下列内容:
标准号;试样标识;材料名称、牌号;试样类型;试样的取样方向和位置;所测性能结果;断口上发现的缺陷种类;评定结果。
6.冲击试验
6.1操作过程控制及要求
6.1.1试验前准备
6.1.1.1室温冲击试验应在10~35℃进行。
对于低温冲击试验,温度控制装置应能将试验温度稳定在规定值的±2℃以内且恒温槽测温仪的误差应不超过±0.1%。
可使用液体介质在恒温槽中冷却试样,恒温槽应有足够的容量和介质,并应有使介质温度均匀的装置。
6.1.1.2对于低温冲击试验,其试验温度<0~10℃时,可使用水+冰混合物作为恒温槽冷却介质,试验温度-70~0℃时,可用乙醇+干冰混合物作为冷却介质,且试样应在规定所需要的设定温度下保持足够时间,一般在上述冷却介质中应不少于5分钟。
移取试样的夹具应与试样同时在恒温槽中冷却。
使其温度与介质温度相近。
6.1.1.3试验间应检查试样的尺寸是否符合标准要求,其量具的最小分度值应不大于0.02mm。
6.1.1.4冲击试验机的标准打击能量为300J(±10J)和150J(±10J),为使冲击试验机能在摆锤最大能量的10%~90%范围内使用,应合理选用冲击摆锤。
6.1.1.5冲击试验前应检查摆锤空击时被动指针的回零差,回零差不应超过最小分度值的四分之一。
6.1.1.6试样应紧贴支座放置,并使试样缺口的背面朝向摆锤刀刃。
且使用对刀样板放置试样,使试样缺口对称面位于两支座对称面上,其偏差不应大于0.5mm。
6.1.2试验设备
6.1.2.1恒温槽应有足够的容量和介质,并应有使介质温度均匀的装置,且恒温槽测温仪的误差应不超过±0.1%。
6.1.2.2冲击试验机其打击瞬间摆锤的冲击速度应为5.0~5.5m/s。
6.1.2.3冲击试验机的试样支座及摆锤刀刃尺寸应符合GB/T229—94要求,其它技术条件应符合GB3808规定,并定期按JJG145检定。
6.1.3试验
6.1.3.1将从动指针拔至零位
6.1.3.2试样从液体介质中移出至打击的时间应在2s之内,如不能满足上述要求,则必须在3~5s内打断试样,此时应采用过冷试样的方法补偿温度损失。
一般试验温度在-60~0℃时,其过冷补偿温度为1~2℃。
6.1.4试验数值的测定
6.1.4.1试验数值可直接从冲击试验机上从动指针所对应的刻度盘上读出。
6.2试验结果数值的修约
6.2.1冲击吸收功数值至少应保留两位有效数字,修约方法按GB8170执行。
6.2.2试验数值的评定应按相应的验收标准要求的合格范围进行评定。
6.3试验数值的处理及重复试验
6.3.1由于试验机打击能量不足使试样未完全折断,应在试验数据之前加大于符号“>”,其他情况则应注明“未折断”。
6.3.2不同类型和尺寸试样的试验数值不能直接对比和换算。
6.3.3试验后试样断口有肉眼可见裂纹或缺陷时,应在试验报告中注明。
6.3.4试验中如有下列情况之一时,试验数值无效,应重做同样数量的试样进行试验:
a.误操作;
b.试样打断时有卡锤现象。
6.3.5冲击试验不合格时,应从原检验试件中再取三个试样复验或将原检查试件与产品再热处理一次后进行全面复验。
重复试验后的数值确认评定可再次按相应验收标准或产品技术条件的相应条款进行评定。
6.4试验记录及其报告
6.4.1各项检验均应有正式记录备查,且试验记录的保管期限至少五年。
6.4.2试验报告一般应包括下列内容:
标准号;试样标识;材料名称、牌号、规格;试样尺寸、型式(U或V)及缺口位置(对于焊接接头应注明母材、熔合线、热影响区、熔敷金属的冲击);试验温度;冲击吸收功;断口上发现的缺陷种类;试验结果。
7.弯曲试验
7.1操作过程控制及要求
7.1.1试验前准备
7.1.1.1弯曲试验应在室温10~35℃下进行。
7.1.1.2施力滚柱的直径应按缺陷验收标准要求选用且长度应大于试样直径或宽度且应具有足够的硬度。
对于两支承滚柱其直径应相同且安装轴线平行。
7.1.1.3采用支辊式弯曲装置进行三点式弯曲时,支辊间距应按下表确定:
l=(d+3a)±0.5a此距离在试验期间应保持不变。
7.1.1.4对于焊接接头,焊缝的正、背表面均应用机械方法修整,使之与母材的原始表面齐平,但任何咬边均不得用机械方法去除,除非产品标准中另有规定。
7.1.2试验设备
各类万能试验机和压力试验机均可使用。
7.1.3试验
7.1.3.1试验应控制试验速度,加卸力应平稳,无振动、冲击。
7.1.3.2试验时弯曲试验装置不应发生相对移动和转动。
7.1.3.3施力滚柱的轴线应与支承滚柱的轴线平行且至两支承滚柱轴线的距离应相等,施力时,力的作用方向应垂直于两支承滚柱的轴线所在平面,对于焊接接头,其压头力的作用点应在焊缝中部。
7.1.3.4缓缓施力弯曲至验收标准所要求的弯曲角度。
7.1.4试验结果数值的测定
试验后检查试样拉伸面上出现的裂纹或焊接缺陷的尺寸及位置。
7.2试验数值的处理及重复试验
7.2.1试验数值的评定应按相应的验收标准要求或产品技术条件进行评定。
7.2.2当弯曲试验结果不符合要求时,应从原检验试件中取双倍弯曲试样复验或将原检验试件与产品再热处理一次后进行全面复验,重复试验后的结果确定评定可再次按相应验收标准或产品技术条件的相应条款进行评定。
7.3试验记录及其报告
7.3.1应有正式的记录备查,且试验记录的保管期限至少五年。
7.3.2试验报告一般应包括下列内容:
标准号;试样标识;材料名称、牌号、规格;试样类型(对于焊接接头应注明是面弯、背弯、侧弯);试样形状及尺寸;压头直径及弯曲角度;试验结果。
8.硬度试验
8.1操作过程控制及要求
8.1.1试验前准备
8.1.1.1试验一般在10~35℃室温进行。
8.1.1.2对于洛氏、里氏硬度试验,试验前应使用相应的与试样硬度值相近的标准洛氏、里氏硬度试块对硬度计进行校验,其示值误差及重复性应不大于相应国家标准要求。
8.1.1.3试样的试验面、支承面、试台表面和压头表面应清洁且无其它污物(氧化皮、油脂、灰尘等)。
试样应稳固地放置在试台上,以保证在试验过程中不产生位移及变形。
8.1.1.4对于洛氏硬度,试样支承面、支座和试台工作面上均不得有压头压痕。
8.1.1.5试样的试验面最好是平面,试验面应具有金属光泽,不应有氧化皮及其他污物,试样的表面粗糙度应符合相应标准要求。
布氏、洛氏硬度试样其表面粗糙度应不大于Ra0.8,里氏硬度应不大于Ra1.6,维氏硬度应不大于Ra0.4。
8.1.1.6对于焊接接头,试验前可用腐蚀剂使焊接接头各区域金属显示清晰后在指定位置测定。
8.1.1.7试验前应选用合适的压头及试验载荷。
8.1.2试验设备
硬度计、压头及标准硬度块、压痕测量装置均应符合相应的标准及检定要求。
8.1.3试验
8.1.3.1试验时,必须保持试验力方向与试样的试验面垂直,加力过程中不应有冲击和振动,直至将试验力施加至规定值。
8.1.3.2整个试验过程中,硬度计应避免受到冲击和振动。
8.1.3.3对于洛氏硬度,在任何情况下,不允许压头与试台及支座触碰。
且调整示值指示器至零点后,应在2~8s内施加全部主试验力,施加主试验力后,总试验力的保持时间应以示值指示器指示基本不变为准。
布氏、维氏硬度其试验力保持时间应符合相应试验标准要求。
8.1.3.4对于布氏、洛氏、维氏硬度试验中,任一压痕至试样边缘距离应符合相应试验标准要求。
8.1.3.5对于里氏硬度测定小件试样时,可在大物件上进行耦合后进行测定,但试验面应与支承台面平行,试样背面和支承台面必须平坦光滑,可在耦合的平面上涂以适量的耦合剂,使试样与支承台面在垂直耦合面的方向上成为承受压力的刚性整体。
试验时,冲击方向必须垂直于耦合平面。
建议用凡士林作为耦合剂。
对于大面积板材,长杆、弯曲件等试样,在试验时应予以适当的支承及固定以保证冲击时不产生位移及弹动。
8.1.3.7里氏硬度计不适用于带磁后的材料测定,且不应在强烈震动、严重粉尘、腐蚀性气体或强磁场的场合使用。
8.1.3.8试样上试验点数应不少于相应试验标准规定要求。
8.1.4试验结果的测定
8.1.4.1布氏硬度
8.1.4.1.1应在两相互垂直方向测量压痕直径,压痕两直径最大差不应超过较小直径的2%。
对各向异性明显材料,两直径可不受此限制,但应在有关标准中规定。
8.1.4.1.2用压痕两直径的算术平均值按GB231查得布氏硬度值。
8.1.4.2洛氏硬度
从硬度计标尺上直接读出相应的洛氏硬度值。
8.1.4.3维氏硬度
8.1.4.3.1应测量压痕两条对角线的长度,用其算术平均值按GB/T4340.1之附录查出相应的维氏硬度值。
8.1.4.3.2在平面上压痕两对角线长度之差应不超过对角线平均值的5%,如果超过5%,则应在试验报告中注明。
8.1.4.4里氏硬度
用五个有效试验点的平均值作为一个里氏硬度试验数据。
8.2试验结果数值的修约
8.2.1测定的洛氏硬度值应精确至0.5个洛氏硬度单位。
8.2.2对于圆柱面和球面上测得的洛氏硬度值,应按GB/T230之附录进行修正。
8.3试验结果的处理及重复试验
8.3.1遇有测点处出现冶金及焊接缺陷时,则该点试验结果无效,应重做同样数量的试样进行试验:
8.3.2试验结果的评定应按相应的验收标准或产品技术条件所要求的项目及合格范围进行评定。
8.3.3当有某项不合格时,应从原检验试件中取双倍硬度试样复验或将原检验试件与产品再热处理一次后进行全面复验,重复试验后的结果确定评定可再次按相应验收标准或产品技术要求的相应条款进行评定。
8.4试验记录及其报告
8.4.1应有正式记录备查,且试验记录的保管期限至少应为五年。
8.4.2试验报告一般应包括下列内容:
标准号;试样标识;材料名称、牌号、规格;热处理状态;所测的硬度值;评定结果。
9.压扁试验
9.1操作过程控制及要求
9.1.1试验前准备
9.1.1.1如有关标准未规定试验温度,则试验应在室温下进行。
9.1.1.2管接头的焊缝余高应用机械方法去除,使与母材原始表面齐平。
9.1.2试验设备
各类万能试验机和压力试验机均可试验。
9.1.3试验
9.1.3.1试验时将试样放在两个平行压板之间,用压力机或其它方法垂直于钢管的轴线方向对试样均匀地加压至有关标准或产品技术要求中规定的两压板之间的距离。
如闭合压扁,试样内表面接触的宽度应至少为试样压扁后其内宽度的1/2。
9.1.3.2对于焊管压扁试验,其焊缝应置于有关产品标准所规定的位置,如未规定具体要求,则焊缝应置于与力作用方向呈90°的位置施压。
而对于环焊缝管接头压扁试验,其焊缝应位于加压中心线上加压;纵焊缝压扁试验,其纵焊缝应位于与作用力相垂直的半径平面内,加压至规定的压板距离H。
两压板间距离H值接下式计算:
H=(1+e)s/(e+s/D)
式中:
S——管壁厚,mm;
D——管外径,mm;
e——单位伸长的变形系数,由产品规范规定。
9.1.3.3出现争议或仲裁试验时,压板的移动速度不应超过25mm/min。
9.2试验结果的评定
9.2.1无缝管和焊管压扁试验时,当压至规定的压板距离时检查试样弯曲变形处,在有关标准未作具体规定的情况下,试验后试样无肉眼可见的裂纹应评定为合格。
仅在试样棱边处出现轻微的开裂不应判报废。
9.2.3管接头压扁试验时,当压至规定的压板距离(H)时,检查焊缝拉伸部位有无裂纹或焊接缺陷,其允许缺陷尺寸按相应产品标准或技术条件评定。
9.3试验结果的处理及重复试验
当有某项不合格时,应从原检验试件中取双倍压扁试样复验或将原检验