水的结垢与防治.docx
《水的结垢与防治.docx》由会员分享,可在线阅读,更多相关《水的结垢与防治.docx(8页珍藏版)》请在冰豆网上搜索。
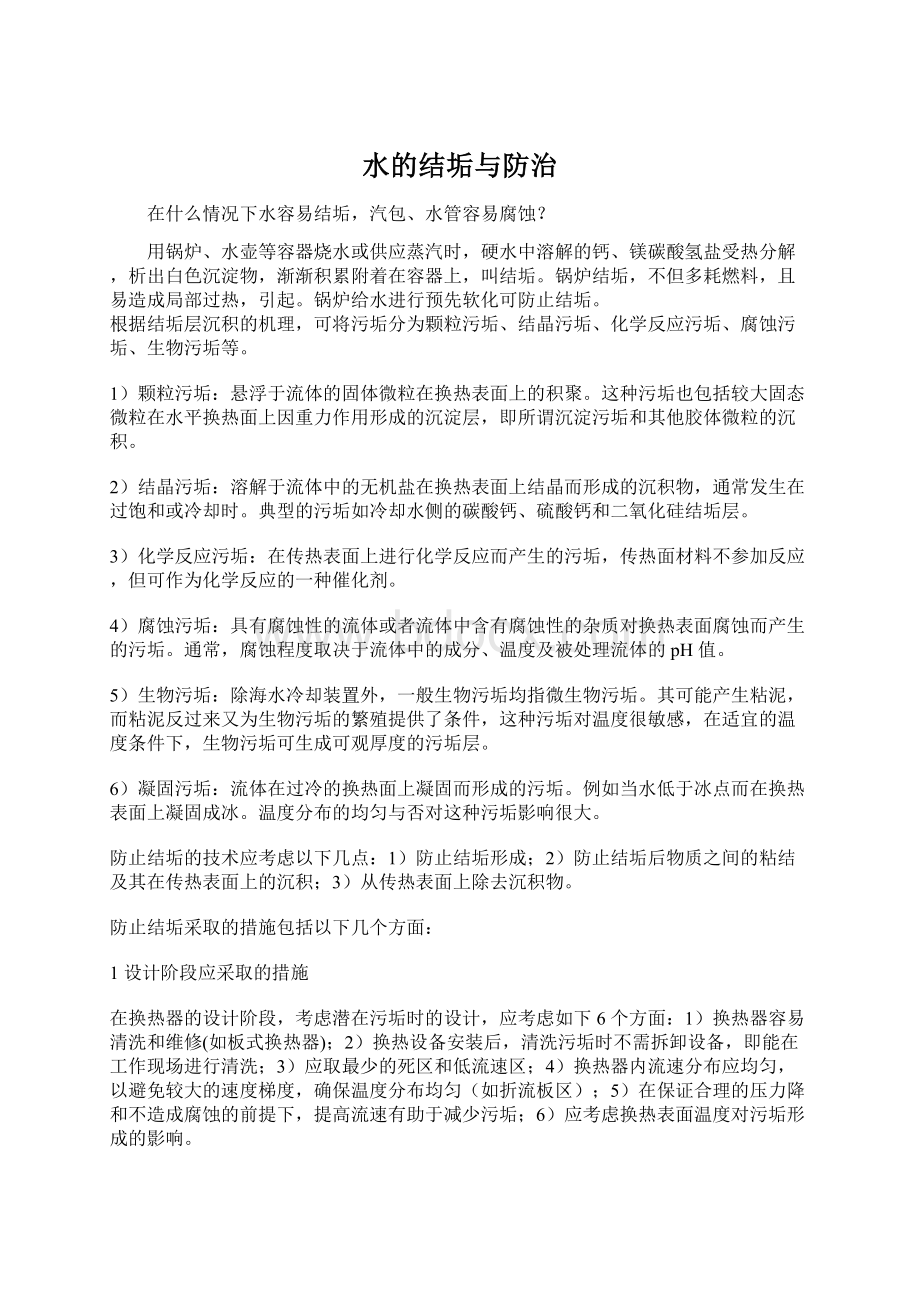
水的结垢与防治
在什么情况下水容易结垢,汽包、水管容易腐蚀?
用锅炉、水壶等容器烧水或供应蒸汽时,硬水中溶解的钙、镁碳酸氢盐受热分解,析出白色沉淀物,渐渐积累附着在容器上,叫结垢。
锅炉结垢,不但多耗燃料,且易造成局部过热,引起。
锅炉给水进行预先软化可防止结垢。
根据结垢层沉积的机理,可将污垢分为颗粒污垢、结晶污垢、化学反应污垢、腐蚀污垢、生物污垢等。
1)颗粒污垢:
悬浮于流体的固体微粒在换热表面上的积聚。
这种污垢也包括较大固态微粒在水平换热面上因重力作用形成的沉淀层,即所谓沉淀污垢和其他胶体微粒的沉积。
2)结晶污垢:
溶解于流体中的无机盐在换热表面上结晶而形成的沉积物,通常发生在过饱和或冷却时。
典型的污垢如冷却水侧的碳酸钙、硫酸钙和二氧化硅结垢层。
3)化学反应污垢:
在传热表面上进行化学反应而产生的污垢,传热面材料不参加反应,但可作为化学反应的一种催化剂。
4)腐蚀污垢:
具有腐蚀性的流体或者流体中含有腐蚀性的杂质对换热表面腐蚀而产生的污垢。
通常,腐蚀程度取决于流体中的成分、温度及被处理流体的pH值。
5)生物污垢:
除海水冷却装置外,一般生物污垢均指微生物污垢。
其可能产生粘泥,而粘泥反过来又为生物污垢的繁殖提供了条件,这种污垢对温度很敏感,在适宜的温度条件下,生物污垢可生成可观厚度的污垢层。
6)凝固污垢:
流体在过冷的换热面上凝固而形成的污垢。
例如当水低于冰点而在换热表面上凝固成冰。
温度分布的均匀与否对这种污垢影响很大。
防止结垢的技术应考虑以下几点:
1)防止结垢形成;2)防止结垢后物质之间的粘结及其在传热表面上的沉积;3)从传热表面上除去沉积物。
防止结垢采取的措施包括以下几个方面:
1设计阶段应采取的措施
在换热器的设计阶段,考虑潜在污垢时的设计,应考虑如下6个方面:
1)换热器容易清洗和维修(如板式换热器);2)换热设备安装后,清洗污垢时不需拆卸设备,即能在工作现场进行清洗;3)应取最少的死区和低流速区;4)换热器内流速分布应均匀,以避免较大的速度梯度,确保温度分布均匀(如折流板区);5)在保证合理的压力降和不造成腐蚀的前提下,提高流速有助于减少污垢;6)应考虑换热表面温度对污垢形成的影响。
2运行阶段污垢的控制
1)维持设计条件由于在设计换热器时,采用了过余的换热面积,在运行时,为满足工艺需要,需调节流速和温度,从而与设计条件不同,然而应通过旁路系统尽量维持设计条件(流速和温度)以延长运行时间,推迟污垢的发生。
2)运行参数控制在换热器运行时,进口物料条件可能变化,因此要定期测试流体中结垢物质的含量、颗粒大小和液体的pH值。
3)维修措施良好换热设备维修过程中产生的焊点、划痕等可能加速结垢过程形成,流速分布不均可能加速腐蚀,流体泄漏到冷却水中,可为微生物提供营养,对空气冷却器周围空气中灰尘缺少排除措施,能加速颗粒沉积和换热器的化学反应结垢的形成。
用不洁净的水进行水压试验,可引起腐蚀污垢的加速形成。
4)使用添加剂针对不同类型结垢机理,可用不同的添加剂来减少或消除结垢形成。
如生物灭剂和抑制剂、结晶改良剂、分散剂、絮凝剂、缓蚀剂、化学反应抑制剂和适用于燃烧系统中防止结垢的添加剂等。
5)减少流体中结垢物质浓度通常,结垢随着流体中结垢物质浓度的增加而增强,对于颗粒污垢可通过过滤、凝聚与沉淀来去除;对于结疤类物质,可通过离子交换或化学处理来去除;紫外线、超声、磁场、电场和辐射处理紫外线对杀死细菌非常有效,超强超声可有效抑制生物污垢,现在的研究还有磁场、电场和辐射处理装置,结论有待进一步研究。
3化学或机械清洗技术
化学清洗技术是一种广泛应用的方法,有时在设备运行时,也能进行清洗,但其主要缺点是化学清洗液不稳定,对换热器和连结管处有腐蚀。
机械清洗技术通常用在除去壳侧的污垢,先将管束取出,沉浸在不同的液体中,使污垢泡软、松动,然后用机械方法除去垢层。
4机械在线除垢技术
1)使用磨粒在流体中加入固体颗粒来摩擦换热器表面,以清除污垢,但对换热器表面易产生腐蚀。
2)海绵胶球连续除垢主要应用于电站凝汽器中冷却水侧的污垢清除,海绵胶球在换热器管内通过泵打循环,胶球比管子直径略大,通过管子的每只胶球轻微地压迫管壁,在运动中擦除沉积物。
3)自动刷洗换热器管道刷洗设施由2个外罩和1个尼龙刷组成,外罩安装在每根管的两端,改变水流方向可使刷子沿管道前后推进刷洗。
水流换向可使刷子沿管道前推刷洗。
水流换向由压缩空气驱动并定时控制联结在管道上的四通阀来完成。
现从锅炉内表面氧和二氧化碳腐蚀现象分析腐蚀的机理,提出防治措施。
1腐蚀产生机理
由于锅炉是一种有极性的电解质,在水的极性分子的吸引下,钢材表面的一部分铁原子开始移入锅炉水而成为带正电的铁离子,而钢材上保留多余的电子带负电荷。
若铁离子不断进入锅炉水,则使钢板(管)上逐渐出现坑洞,产生腐蚀。
其化学反应:
Fe+2H2O=Fe(OH)2+H2↑
2H2+O2=2H2O
4Fe(OH)2+O2+2H2O=4Fe(OH)3↓
另外,水中的溶解氧又是阴极去极化剂,即:
O2+4e+2H2O=4OH—
所以氧腐蚀速度与水中含氧量成正比。
由于溶解氧本身是阴极去极化剂,对金属的危害十分严重;而二氧化碳在水溶液中呈酸性,直接破坏金属表面保护膜,加速了氧对金属的电化学腐蚀。
在天然水中,碱度主要由HCO3的盐类[如Ca(HCO3)2、Mg(HCO3)2]组成,这些重碳酸盐(暂时硬度)在低压锅炉中经过一系列的变化,在水中产生二氧化碳和碳酸,从而引起锅炉内表面腐蚀。
特别是有些使用单位对原水不进行任何处理,直接送入锅炉,在锅炉内被加热的过程中,重碳酸盐被分解,产生沉淀物,即:
生成的重碳酸铁[Fe(HCO3)2]对锅炉产生腐蚀。
换句话说,只要水中存在CO2,腐蚀铁的反应就会一直进行下去,直到CO2消耗完为止。
重碳酸铁[Fe(HCO3)2]溶解于水。
如果水中不存在O2,那么,Fe(HCO3)2以溶解液状态被加热分解,产生沉淀物——Fe2O3(红锈),它是松散的水渣,通过排污排掉。
这种腐蚀的特点是内表面腐蚀均匀,呈现光亮。
如果水中存在O2,那么O2就和Fe(HCO3)2反应,产生二氧化碳即:
4Fe(HCO3)2]+O2+2H2O→4Fe(OH)3↓+8CO2
Fe(OH)3又与水溶液中的Fe(OH)2相互碰撞后生成Fe3O4(黑锈)保护膜。
新产生的CO2又变为碳酸,破坏保护膜,腐蚀内表面。
反应反复进行,直到O2全部消耗完为止。
实验表明,即使存在少量的O2,也明显加快了腐蚀进程。
二氧化碳的产生除与直接进入锅炉的原水有关外,还与是否采用除氧方式有关,当采用热力式除氧时,软化水在系统外先被加热,当水温达到60℃以上时,重碳酸钠NaHCO3就开始分解出Na2CO3和CO2,CO2及原水中游离的O2、N2等气体在除氧器中被除掉,不进入系统,重碳酸盐则以NaCO3形式进入系统。
如果不采用任何除氧方式,那以NaHCO3未分解直接进入锅炉,在炉内被加热分解,产生二氧化碳。
2氧和二氧化碳对低压锅炉腐蚀的原因分析
2.1一是大量补入的原水未采用钠离子交换软化和未采用任何除氧方式。
低压锅炉由于用气量大,需要大量均衡连续的给水,当补给水水质达不到标准规定要求,补给水中的重碳酸盐在炉内加热的过程中产生二氧化碳;或在直接补入生水的过程中,即补进了溶解氧,对锅炉金属壁面产生腐蚀。
2.2PH值过低,加速了金属壁腐蚀。
如果锅炉给水能够达到标准规定要求,金属壁即使有腐蚀也是均匀腐蚀,即当PH=9.5~11时,金属具有坚硬的氧化保护层,可大大减缓腐蚀,甚至避免腐蚀情况的发生。
但是当PH值<7时,氧分子、氢离子、氯离子等作为腐蚀介质都很活路,由于水中氧分子、氢离子、氯离子的存在,就使锅炉受热面产生了腐蚀。
同时二氧化碳溶于水也会降低PH值。
2.3水温的影响。
锅水的温度高,钢材表面温度也高,则Fe2+在水溶液中的扩散速度加快,电解质水溶液的电阻降低。
由于氧腐蚀的基本原理是靠扩散,扩散速度愈快,氧腐蚀速度亦快。
对于低压锅炉来说,腐蚀速度随着水温的升高,局部腐蚀的程度和速度明显提高,当温度升高到脱氧温度(1000℃)以上时,气体氧随蒸汽进入蒸汽系统,水侧的腐蚀相应减小。
2.4停炉后不注意维护保养,造成吸氧腐蚀。
锅炉停用,有的装满生水,有的随意裸露在大气中,这样由于保养不善或不保养,停炉状态下的腐蚀往往比运行状态下更严重。
3防止腐蚀的措施
3.1选择有效的水处理方式
3.1.1采用锅外化学处理一钠离子交换软化法的同时,增设有效的除氧装置,除去水中的溶解氧。
低压锅炉一般采用化学除氧,常用的化学试剂有亚硫酸钠、亚硫酸钠加催化剂、联安等。
并定期化验,使锅水含量控制在标准范围内。
3.1.2采用炉外加热法。
这种方法简单易行,是对原水(正常运行主要是补水)在炉外进行加热,而不是进行钠离子交换。
由于加热,原水中重碳酸盐被分解出CO2以及其它气体,同时形成沉淀物,CO2以及其它气体通过上部排气孔排掉,沉淀物通过下部排污阀泄掉。
这样,补水中不会再含有NaHCO3或Na2CO3,并且不管热煤参数如何,系统内都不会再产生CO2,从而避免腐蚀。
同时根据重碳酸钙、镁沉淀析出的原理,也可以避免在炉内形成水垢,满足防腐、防垢的要求。
炉外加热的设备应考虑到自身结垢和除气的问题,最好采用蒸汽混合式加热的方法,通过蒸汽将补给水的温度加热到沸点,在充分分解重碳酸盐的同时,将气体放掉。
水箱和加热器可使用塑料等耐腐蚀材料,以便定期以酸洗的方式除掉水箱内表面及加热器上的水垢。
3.2充分利用邻近锅炉的排污水。
由于低压锅炉防止腐蚀主要是消除补水中的CO2和游离O2,那么就可以在一个同时设有2台以上锅炉的锅炉房内,对邻近锅炉的排污水通过沉淀,等排出水渣后,再作为补给水使用,这样一方面可以对邻近锅炉的排污水进行二次利用,另一方面又可以满足补水的水质和防腐要求。
3.3采用锅内加药处理,控制锅水PH值。
这是系统防腐的必要条件,同时也是最简单、最有效的方法。
当锅炉循环水PH值低于10时可增加磷酸三钠和氢氧化钠药量进行调整,将PH值控制在10~12之间,使锅水中的钙、镁离子形成疏松的水渣,通过排污排出炉外。
3.4做好停炉保养工作是防止锅炉腐蚀的有效途径之一。
通常短期停炉采用湿法保养,长期停炉采用干法保养。
干法保养是将炉膛灰渣清除后,将盛装生石灰块或氯化钙的容器放在锅筒、炉膛及烟道中,同时将检查门、炉门、出灰门以及通用挡板加以密封,防止潮气进入。
汽包结垢和腐蚀的原理,因为水中有HCO3离子、钙、镁离子,温度低时溶于水,当加热时就生成碳酸钙、碳酸镁等不溶于水的物质,日常你烧开水时应该发现了有结垢现象。
汽包注水不应该是新鲜水而是新鲜水要经过处理装置除去水中的阳离子,而且需要不严格控制水中的氯离子等有害物质以免对汽包发生腐蚀.在向汽包注水前的工段应的除氧和加磷酸三钠等装置.
结垢主要根据水的水质和系统的工艺状况,以及现场的控制,包括水温过高,水的PH偏高等
一般循环水都会有一定的浓缩倍数,使系统中的离子含量和菌藻含量增加,所以如果控制不是很好。
水管容易腐蚀的原因是
水中有气泡,使水中溶解了氧;
水的流速过快
水的PH偏低
氯离子含量偏高
水温偏高等
水中离子较多,加上水质原因在遇到环境(温度、PH值)变化后和管道、设备中的离子发生反应而形成物质沉淀、聚合形成污垢。
汽包结垢和腐蚀的原理,因为水中有HCO3离子、钙、镁离子,温度低时溶于水,当加热时就生成碳酸钙、碳酸镁等不溶于水的物质,日常你烧开水时应该发现了有结垢现象。
汽包注水不应该是新鲜水而是新鲜水要经过处理装置除去水中的阳离子,而且需要不严格控制水中的氯离子等有害物质以免对汽包发生腐蚀.在向汽包注水前的工段应的除氧和加磷酸三钠等装置.
如果是金属材质,在含离子水中就会发生电化学腐蚀,尤其是氯离子引起的点蚀危害更大.水中含有腐蚀性气体会加速腐蚀,并且与生产装置运行温度有关,如敞开装置有溶解氧的情况,腐蚀会随温度升高先增加后缓慢下降达到平稳.主要是腐蚀控制不同.初期由氧扩散控制腐蚀速度,后期溶解氧降低,主要是分析动力学控制.[/hide]
水中含有钙镁离子和碳酸根离子就容易结垢
避免汽包结垢要从多方面入手:
1、材质,避免电化学腐蚀
2、水中的氯离子、氧和钙镁离子含量要控制
3、汽包定期排污[/hide]
⒈固相物的生成
⑴形成污垢的原因:
①多组份过饱和溶液中盐类的结晶析出;
②有机胶状物和矿质胶状物的沉积;
③不同分散度的某些物质固体颗粒的粘结;
④某些物质的电化学还原过程生成物等。
以上混合物沉积总称作污垢。
⑵形成水垢的原因:
水中溶解盐类产生固相沉淀是构成结垢(水垢)的主要因素,其产生固相沉淀的条件是:
①随着温度的升高,某些盐类的溶解度降低,如Ca(HCO3)2、CaCO3、Ca(OH)2、CaSO4、MgCO3、Mg(OH)2等;
②随着水份的蒸发,水中溶解盐的浓度增高,达到过饱和程度;
③在被加热的水中产生化学过程,某些离子形成另一些难溶的盐类离子。
具备了上述条件的某些盐类,首先在金属表面上个别部分沉积出原始的结晶胚,并以此为核心逐渐合并增长。
之所以易沉积于金属表面,这是因为金属表面在微观上具有一定的粗糙度,微观上的凹凸不平成为过饱和溶液中固体结晶核心;同时加热面上的氧化膜对固相物也有很强的吸附力。
作为构成水垢的盐类——钙镁,在过饱和溶液中生成固相结晶胚芽,逐变而为颗粒,具有无定形或潜晶型结构,接着互相聚附,形成结晶或絮团。
固相沉渣的生成与胚芽核心的生成速度有关,即与单位时间内出现的结晶核数量与结晶生长的线速度有关,而这两个因素又与水温和水中含盐浓度及其它杂质的存在有关。
⒉重碳酸盐的分解
冷却水结垢的主要原因是因为水中含有较多的重碳酸钙,在加热过程中失去平衡,分解为碳酸钙、二氧化碳和水。
碳酸钙溶解度较低,因而首先在冷却设备表面沉积下来。
温度、压力等因素也影响结垢的强度与速度。
重碳酸钙是反溶解度盐类,在超过一定温度(临界点)时,其饱和浓度急剧减小。
⒊钙、镁碳酸盐水垢
碳酸盐水垢通常以致密的结晶沉淀在加热器壁面甚至冷却塔填料或壁上。
但当水温在过热面超过100℃时,CaCO3沉淀是海绵状的絮状体。
虽然,在沸腾温度以下,也有可能出现硫酸钙的沉淀,但这只能是特例,因为硫酸钙的三种状态:
CaSO4、2CaSO4·H2O、CaSO4·2H2O三者的溶解度都很大,因而在冷却水的具体条件下,可以完全不必考虑硫酸钙的沉积问题。
氢氧化钙的溶解度也是随温度升高而降低的,但在一般情况下在水中不会生成氢氧化钙,因而也不必考虑。
重点在于钙镁的碳酸盐:
Ca2++2HCO3=H2O+CO2↑+CaCO3↓
Ca(HCO3)2=CaCO3↓+H2O+CO2↑
Mg(HCO3)2=MgCO3↓+H2O+CO2↑
MgCO3的溶解度比CaCO3的溶解度大六倍以上,而且在水中的MgCO3会很快水解。
MgCO3+H2O=Mg(OH)2↓+CO2↑
在水中以Mg(OH)2状态存在,而Mg(OH)2的溶解度因温度升高所起的变化较慢,基本上很少会沉积,况且在天然水中的钙离子远远大于镁离子,镁盐的沉积在数量上影响较微,可以忽略不计。
⒋垢成份及来源
⑴污垢的分类:
无机盐类的沉积称为"垢",它有固定晶格,比较硬,其主要成份为Ca3(PO4)2、CaCO3、SiO2,镁盐和铁的氧化物。
而有机物、菌类、藻类、悬浮物等称为"污",即水中呈胶体状的粘泥。
它比较软,无固定形态。
⑵污垢成份:
污垢包括水垢、腐蚀产物、生物污泥、悬浮物沉积等。
其主要成份为:
SiO2、P2O5、SO42-、Fe2O3、Al2O3、CaO、MgO、CuO、CO2、灼烧减量等。
⑶污垢来源:
胶体有机物泥、原水滓、污物、可溶性铁、微生物沾污物、灰尘、空气带入;活性气体:
H2S、SO2、NH3等;源水垢:
CaCO3、CaSO4、MgSiO3;腐蚀产物:
Fe2O3、循环水生产中泄漏物:
烃、硫化物、微生物污垢。
冷却水系统中的污垢,不单纯是钙镁碳酸盐的结垢沉积,污垢的成份及其形成的因素是复杂的。
①结晶:
溶解盐类的析出,以如前述,主要是钙、镁的碳酸盐;在热交换器加热面上也有可能产生硅酸盐水垢(当水中SiO2含量>200PPM时),以及含有钙、镁、铝、钠等复盐的硬垢。
而当水中磷酸盐和铁含量较高,而碱度又低时,则有可能产生铁磷酸盐的水垢NaFePO4。
结晶水垢的种类大致有:
a、低温下的重碳酸钙热分解:
α-CaCO3松软水垢;
b、高PH时Mg(OH)2的沉积:
Mg(OH)2;
c、壁面致密的碳酸钙β-CaCO3;
d、过剩的铁离子:
FeCO3。
②沉积:
腐蚀产物、粘土、砂尘的沉积,如补充水中带入的泥砂或悬浮物,进冷却塔空气带入的微尘粒子;换热器中渗漏的工艺杂质、油脂、细菌、藻类、真菌类所生成的粘泥。
这些沉积物往往吸附在化学反应晶体水垢表面上而对反应起催化作用,加速了污垢的形成。
③反应与聚合:
油泥、有机氧化物等的沉积。
④腐蚀所造成的糙壳:
⒌阻垢机理
水中的钙、镁离子与碳酸根、磷酸根等结合生成难溶的小晶体,这些小晶体不断碰撞并按一定的方向增长变成大晶体。
水中的钙、镁盐晶体及其不溶性微粒同时受到两个力的作用,即与管壁上的水垢结合生成体积更大的垢的结晶力和水流的剪切力,当结晶力较大时便易使垢增长,当结晶力较小时(如加入阻垢剂后)或剪切力较大(如水流速较大的部位)时,垢无法增厚,水中的微粒只能以水渣的形式被水冲走。
⑴增溶机理
有些阻垢剂能与水中的钙镁离子形成比碳酸钙等难溶盐更稳定的可溶解于水的络合物,使钙、镁无法形成碳酸钙等小晶体。
这种阻垢剂不但能阻垢,若浓度达到一定程度,还能起到除垢的作用。
⑵晶格畸变的机理
阻垢剂的活性基团与碳酸钙等晶体上的钙结合,由于阻垢剂分子的空间阻扰,使碳酸钙等难溶盐无法按正常的晶格方向增长,结晶力被削弱,垢变得松软,易被水流冲掉。
汽包结垢和腐蚀的原理,因为水中有HCO3离子、钙、镁离子,温度低时溶于水,当加热时就生成碳酸钙、碳酸镁等不溶于水的物质,日常你烧开水时应该发现了有结垢现象。
汽包注水不应该是新鲜水而是新鲜水要经过处理装置除去水中的阳离子,而且需要不严格控制水中的氯离子等有害物质以免对汽包发生腐蚀.在向汽包注水前的工段应的除氧和加磷酸三钠等装置.[/
结垢:
水的碱度和硬度高、PH值高、悬浮物高。
腐蚀原因:
有溶解氧、CO2、沉淀物下腐蚀、酸性腐蚀、碱性腐蚀等
那在什么情况下水比较容易结垢和腐蚀?
PH值偏低,钙、镁离子脱除效果不好。
如何从工艺上避免或降低这些的可能性(除了加剂之外)?
采用脱盐水或者凝液,建议PH控制在9-11、溶解氧(μg/l)≤15、SiO2(mg/l)≤2、PO43+(mg/l)5-15、电导(us/cm)≤50。
只要是金属材质,在含离子水中就会发生电化学腐蚀,尤其是氯离子引起的点蚀危害更大.水中含有腐蚀性气体会加速腐蚀,并且与生产装置运行温度有关,如敞开装置有溶解氧的情况,腐蚀会随温度升高先增加后缓慢下降达到平稳.主要是腐蚀控制不同.初期由氧扩散控制腐蚀速度,后期溶解氧降低,主要是分析动力学控制.