2烟气余热可行性报ND钢与304对比.docx
《2烟气余热可行性报ND钢与304对比.docx》由会员分享,可在线阅读,更多相关《2烟气余热可行性报ND钢与304对比.docx(35页珍藏版)》请在冰豆网上搜索。
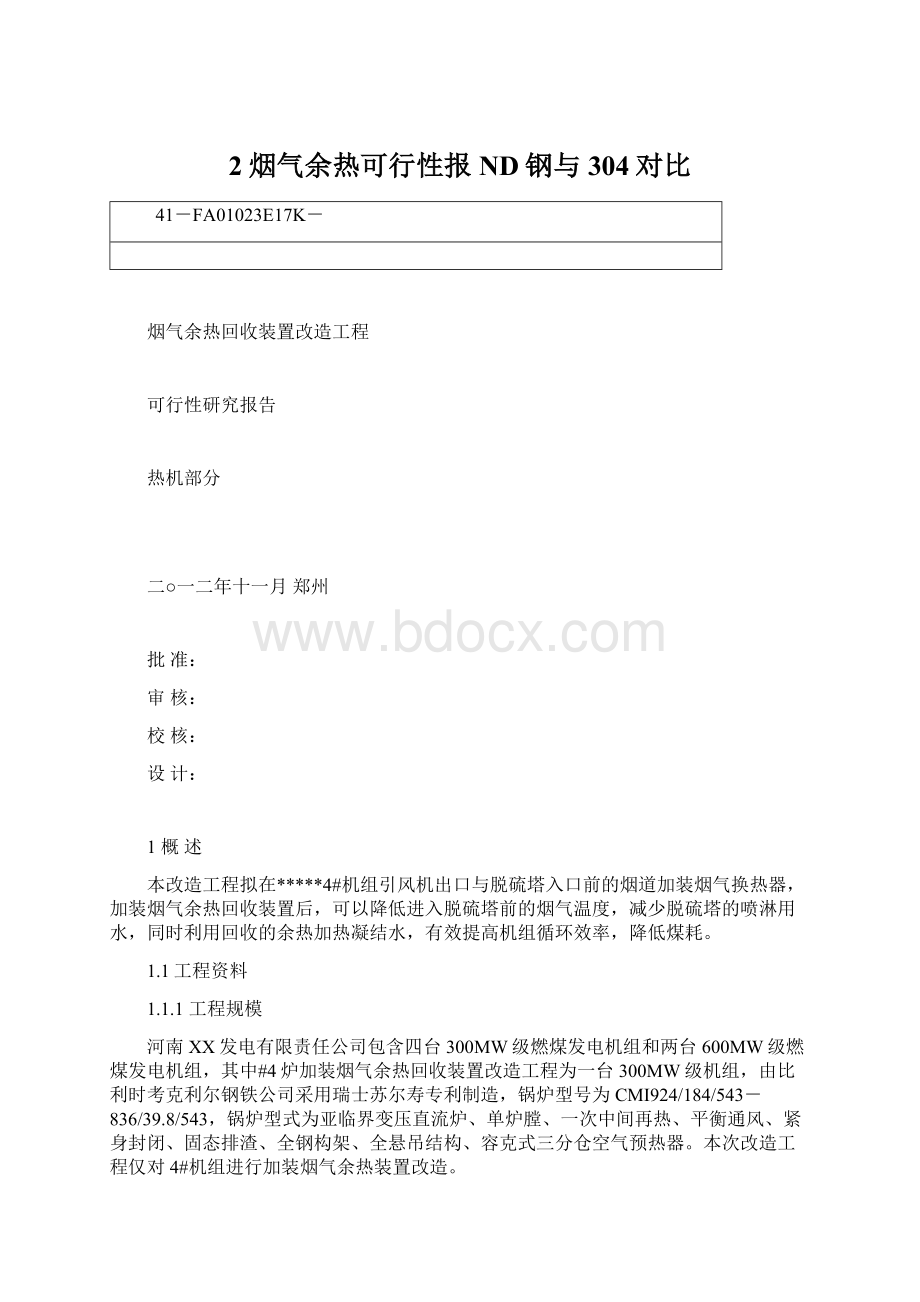
2烟气余热可行性报ND钢与304对比
41-FA01023E17K-
烟气余热回收装置改造工程
可行性研究报告
热机部分
二○一二年十一月郑州
批准:
审核:
校核:
设计:
1概述
本改造工程拟在*****4#机组引风机出口与脱硫塔入口前的烟道加装烟气换热器,加装烟气余热回收装置后,可以降低进入脱硫塔前的烟气温度,减少脱硫塔的喷淋用水,同时利用回收的余热加热凝结水,有效提高机组循环效率,降低煤耗。
1.1工程资料
1.1.1工程规模
河南XX发电有限责任公司包含四台300MW级燃煤发电机组和两台600MW级燃煤发电机组,其中#4炉加装烟气余热回收装置改造工程为一台300MW级机组,由比利时考克利尔钢铁公司采用瑞士苏尔寿专利制造,锅炉型号为CMI924/184/543-836/39.8/543,锅炉型式为亚临界变压直流炉、单炉膛、一次中间再热、平衡通风、紧身封闭、固态排渣、全钢构架、全悬吊结构、容克式三分仓空气预热器。
本次改造工程仅对4#机组进行加装烟气余热装置改造。
1.1.2锅炉容量和主要参数
锅炉主要技术参数见表1.1.2。
表1.1.2锅炉主要技术参数表
序号
项目名称
单位
预期工况
100%工况
1
过热蒸汽参数
1.1
过热器出口蒸汽流量
t/h
943.28
923.76
1.2
过热器出口蒸汽压力
MPa.a
18.42
18.39
1.3
过热器出口蒸汽温度
℃
543
543
2
再热蒸汽参数
2.1
再热器蒸汽流量
t/h
859.46
836.35
2.2
再热器进口蒸汽压力
MPa.a
4.34
4.23
2.3
再热器进口蒸汽温度
℃
334.2
334.5
2.4
再热器出口蒸汽压力
MPa.a
4.017
3.98
2.5
再热器出口蒸汽温度
℃
543
543
3
给水温度
℃
258.6
251.7
4
空气预热器出口热风温度
4.1
热一次风温度
℃
276.7
277.4
4.2
热二次风温度
℃
305
304.1
5
空气预热器进口冷风温度
5.1
冷一次风温度
℃
27
27
5.2
冷二次风温度
℃
27
27
6
空气预热器出口烟气温度
℃
6.1
修正前温度
℃
128.5
128.5
6.2
烟气修正后温度
℃
123.4
123.4
7
保证锅炉效率
%
91.58
91.58
7.1
排烟损失
%
5.27
5.27
7.2
未完全燃烧损失
%
2.20
2.20
7.3
其他损失
%
0.95
0.95
7.4
总热损失
%
8.42
8.42
8
省煤器出口空气过剩系数
%
1.25
1.25
9
空预器出口空气过剩系数
%
1.38
1.38
1.1.3燃料特性
根据*****提供的煤质资料,本改造工程燃煤主要成分与特性见表1.1.3-1。
表1.1.3-1燃煤成分与特性表
序
号
名称
符号
单位
设计煤种
校核煤种
1
煤种
混煤1
混煤2
2
工业分析
收到基全水分
Mt
%
6.4
5.5
空气干燥基水分
Mad
%
1.36
1.43
干燥无灰基挥发分
Vdaf
%
36.17
39.37
收到基灰分
Aar
%
39.34
44.44
收到基低位发热值
Qnet.ar
kJ/kg
17190
15670
kcal/kg
4105.8
3742.7
3
元素分析
收到基碳分
Car
%
44.64
40.94
收到基氢分
Har
%
2.58
2.58
收到基氧分
Oar
%
5.34
5.60
收到基氮分
Nar
%
0.73
0.69
收到基硫分
St.ar
%
0.97
0.25
4
可磨性系数
哈氏可磨度
HGI
—
96
75
5
煤灰熔融性
变形温度
DT
℃
1340
1460
软化温度
ST
℃
>1500
>1500
半球温度
HT
℃
>1500
>1500
流动温度
FT
℃
>1500
>1500
6
灰成分分析
二氧化硅
SiO2
%
61.72
61.48
三氧化二铝
Al2O3
%
26.78
25.84
五氧化二磷
P2O5
%
0.05
0.05
三氧化二铁
Fe2O3
%
3.70
4.04
氧化钙
CaO
%
3.80
4.18
氧化镁
MgO
%
0.62
0.68
氧化钠
Na2O
%
0.66
0.68
氧化钾
K2O
%
1.24
1.24
二氧化钛
TiO2
%
0.80
0.84
三氧化硫
SO3
%
0.14
0.08
其它
/
%
0.50
0.89
7
煤灰比电阻(设计煤种电压2700V,校核煤种电压2400V)
温度24℃时
Ω.cm
2.10×108
5.77×108
温度100℃时
Ω.cm
2.46×108
2.16×108
温度120℃时
Ω.cm
2.62×1010
8.08×109
温度140℃时
Ω.cm
2.00×1011
9.32×1010
温度150℃时
Ω.cm
4.66×1011
1.28×1012
温度160℃时
Ω.cm
1.05×1012
1.54×1012
温度170℃时
Ω.cm
1.30×1012
1.92×1012
温度180℃时
Ω.cm
1.86×1012
2.31×1012
温度200℃时
Ω.cm
2.36×1012
2.51×1012
本工程采用0号轻柴油作为锅炉点火和助燃用油。
轻柴油为市场议价商品油,采用汽车运输。
燃油品质见表1.1.3-2。
表1.1.3-2燃油品质表
序号
项目
单位
指标
1
十六烷值
—
≥45
2
粘度(20℃)
恩氏粘度
°E
1.2~1.67
运动粘度
mm2/s
3.0~8.0
3
残炭
≤0.3
4
灰分
%
≤0.01
5
硫含量
%
≤0.2
6
机械杂质
%
无
7
水分
%
≤痕迹
8
闪点(闭口)
℃
≥55
9
凝点
℃
≤0
10
低位发热量
MJ/kg
39.776~41.868
1.1.4锅炉给水
锅炉给水水质量:
pH值(25℃)
9.2~9.6(加热器为钢管)
总硬度
≈0
铁
≤0.01mg/l
铜
≤0.003mg/l
氧
≤0.007mg/l
二氧化硅
≤0.015mg/l
联氨
0.01~0.03mg/l
1.1.5锅炉辅助系统
锅炉运行方式:
带基本负荷并能调峰。
给水调节:
每台机组配置50%B-MCR容量的三台电动给水泵。
向锅炉连续供水并向锅炉过热器、再热器及汽轮机高压旁路供减温水。
制粉系统形式:
锅炉配备的制粉系统为正压直吹式系统,共有两台离心式一次风机、五台碗式中速磨煤机、五台刮板式给煤机组成。
设计从给煤机启动到喷燃器见到火焰约1分钟;在低负荷时,从切除给煤机到火焰熄灭的排空时间约为1~6分钟。
锅炉的风烟系统由两台入口静叶可调式轴流吸风机和两台动叶可调式轴流送风机组成。
目前空气预热器为豪顿华工程有限公司设计制造的容克式三分仓空预器,型式28VNT1600,空气预热器的主轴垂直布置,采用顶部中心驱动方式,烟气和空气以逆向流动方式换热,烟气向下,空气向上流动。
计划在脱硝改造工程中相应改造空气预热器以适应脱硝装置的运行。
锅炉的除渣装置为刮板式捞渣机。
除尘器目前为高效率的静电除尘器,计划改为五电场旋转电极的静电除尘器以保证烟囱出口含尘浓度满足新的《火电厂大气污染物排放标准》(GB13223-2011)。
烟气脱硫系统采用石灰石—石膏湿法烟气脱硫(FGD)工艺,一炉一塔方案,脱硫效率≥95%。
烟气脱硫部分及全部配套工程均由北京康瑞健生环保工程技术有限公司EPC总承包。
1.1.6厂址环境条件
气温
历年平均气温15.3℃
历年极端最高气温42.6℃
历年极端最低气温-18.8℃
湿度
平均相对湿度67%
气压
历年平均气压1006.8hPa
降水量、积雪深度
历年平均降水量754.6mm
历年最大降水量1323.6mm
历年最小降水量373.9mm
多年平均降水量742.4mm
历年最大积雪深度220mm
最大冻土深度140mm
风
冬季主导风向NE频率14%
夏季主导风向NE频率9%
30年一遇10min平均最大风速39.7m/s(离地面10米高)
基本风压0.45kPa
地震基本烈度:
6度
1.2工程改造原则及依据
工程改造原则主要有:
a)坚持“安全可靠、经济适用、符合国情”的电力建设原则。
b)贯彻节约用地,节约用水,保护环境的设计原则。
c)保证现有指标不降低、原设计功能不改变,原布置少改动原则。
d)尽可能降低机组煤耗。
工程设计原则主要遵循的标准及规范有:
·GB50660-2011《大中型火力发电厂设计规范》;
·DL/T5366-2006《火力发电厂汽水管道应力计算技术规程》;
·DL/T5054-1996《火力发电厂汽水管道设计技术规定》;
·DL/T5121-2000《火力发电厂烟风煤粉管道设计技术规程》;
·DL/T5203-2005《火力发电厂煤和制粉系统防爆设计技术规程》;
·国家有关法令、法规、政策及有关设计规程、规范等。
1.3工程改造范围
改造工程主要涉及4#机组进行烟气余热回收系统改造的整套设备和安装,包括烟气余热回收装置本体、相应的吹灰系统、烟气系统、凝结水系统、各系统所需配备的辅助设备、设施、管道连接、保温等。
1.4工程改造背景
对于火力发电厂的热力系统而言,可以采用以下三种方法提高全厂的热效率。
(a)提高蒸汽参数,这是国内外主机制造厂不断追求的目标,从亚临界、超临界到目前的超超临界机组,国外正在为进一步蒸汽温度到650~700℃作不懈的技术研究。
但是蒸汽参数每跨一个台阶,锅炉和汽轮机都需要采用更高档的材料,大大提高了主机设备的成本。
(b)降低汽轮机的排汽参数。
由于受电厂所处地理位置和气候条件的限制,循环冷却水温是在一定的范围内变化的,因此汽轮机的排汽参数下降的幅度是有限的。
(c)减少锅炉烟气的排放热损失。
烟气热量回收装置的运用就是设法利用锅炉排烟余热的一种手段。
排烟损失是锅炉热损失中最大的一项,大中型电站锅炉在正常运行时,排烟损失占到锅炉燃料输入热量的4%到8%;而排烟温度每降低15℃--25℃,就可提高锅炉效率1%左右。
随着国家对节能工作不断深入,以及目前煤炭价格的不断上涨,人们越来越重视由于排烟温度高而造成的能源浪费问题,少量电厂已经开始尝试利用烟气余热回收装置,使烟气的温度再降低20到50℃,并取得了初步成效。
利用烟气余热回收装置进一步降低烟气温度的主要优点有:
吸收余热,并将余热用于加热供暖热网水、生活热水、生水、凝结水等介质,提高锅炉效率,并带来一定的经济效益;
降低排烟温度,使烟气在进入脱硫塔时达到最佳脱硫效率状态,大大减少了脱硫塔中的冷却水耗。
节约了宝贵的水资源。
对于布置在除尘器尘前的烟气余热回收装置,还可以通过降低排烟温度而使烟气中的粉尘比电阻降低、烟气的体积流量减少,从而提高了电除尘的效率,降低了粉尘的排放。
(本工程布置在除尘器后,不涉及本项)
利用烟气余热加热凝结水是目前电厂余热回收应用最多的一种方式,尤其是在南方地区的纯凝机组。
其节能原理是:
汽轮机热力系统中的凝结水在烟气热量回收系统中吸收排烟热量,降低排烟温度,自身被加热、升高温度后再返回汽轮机低压加热器系统,代替部分低压加热器的作用。
烟气热量回收装置将节省部分汽轮机的回热抽汽,在汽轮机进汽量不变的情况下,节省的抽汽继续膨胀做功,因此,在发电量不变的情况下,可节约机组的能耗。
图1.4-1是烟气热量回收装置的系统连接示意。
通常从某个低压加热器引出部分或全部冷凝水,送往烟气热量回收装置。
图1.4-1烟气热量回收装置系统
1.5烟气热量回收装置应用情况
本锅炉排烟设计温度一般在120~130℃左右,但由于受燃料特性改变及运行环境变化,锅炉实际运行排烟温度也将会改变。
虽然加装烟气热量回收装置后烟气阻力有所上升,但是烟气阻力增加引起的引风机耗电量还不到节约成本的10~30%,因此烟气热量回收装置能有效的提高锅炉效率、节约能源,减少生产成本,具有良好的应用前景。
目前在国内也已有一些电厂进行了类似的烟气热量回收装置的安装和改造工作。
国内某1000MW机组的烟气热量回收装置系统已经于2009年4月投入运行,机组在#2低加进口的凝结水管道上设置了一台烟气热量回收装置,将凝结水温度从60.6℃提升到81.6℃,同时烟气温度从125℃下降到85℃,其相关系统连接如图1.5-1。
图1.5-1某1000MW机组烟气热量回收装置示意图
在国外,类似的烟气热量回收装置同样较早就得到了应用。
起先,苏联为了减少排烟损失而改装锅炉机组时,在锅炉对流竖井的下部装设低温省煤器供加热热网水用。
对于近期发展起来的超超临界发电机组而言,同样烟气热量回收装置已被普遍使用,德国SchwarzePumpe电厂2×800MW褐煤发电机组在静电除尘器和烟气脱硫塔之间加装了烟气换热器,利用烟气加热锅炉凝结水,其原理同烟气热量回收装置一致。
德国科隆Nideraussem1000MW级褐煤发电机组采用分隔烟道系统充分降低排烟温度,把烟气热量回收装置加装在空气预热器的旁通烟道中,在烟气热量足够的前提下引入部分烟气到旁通烟道内加热锅炉给水。
日本的常陆那珂电厂采用了水媒方式的管式GGH。
烟气放热段的GGH布置在电气除尘器上游,烟气被循环水冷却后进入低低温除尘器(烟气温度在90~100℃左右),烟气加热段的GGH布置在烟囱入口,由循环水加热烟气。
烟气放热段的GGH的原理和烟气热量回收装置一样。
烟气热量回收装置在国内和国外已经有运用业绩,在德国锅炉排烟温度较高,均达到170℃左右(这是因为这些锅炉燃用的是褐煤),而加装烟气换热器后排烟温度下降到100℃左右,回收的热量是相当可观的。
因此烟气换热器对于高排烟温度的锅炉的节能效果是非常明显的。
日本的情况与本工程较为相似,锅炉设计排烟温度不是很高(125℃左右),经过管式GGH后烟气温度可降低到85℃左右,但是管式GGH将烟气的热量加热脱硫塔出口的烟气,并不节约机组的煤耗量,没有节能的效果,但防腐效果较为明显。
对于本工程,烟气换热器入口烟温设计值取140℃,以该值作为换热器及管道选型用,烟气换热器出口烟温设计值取90℃。
热经济性计算时烟气换热器入口烟温取130℃(排烟温度设计值为123.3℃,烟气经引风机温度提高5~6℃),烟气换热器出口烟温取90℃。
2烟气余热回收方案
2.1整体方案描述
将4#机组1#低加进口处的凝结水部分引入烟气余热回收装置,利用烟气的余热直接加热凝结水,被加热后的凝结水引回、进入3#低加出口。
图2.1系统示意图
2.2烟气余热回收装置的布置
目前*****4#机组BMCR工况运行时,空预器夏季出口排烟温度为140℃,过高的排烟温度损失了大量的热量,降低了机组效率。
为实现节能减排目标,拟在4#机组锅炉下游烟道中加装烟气热量回收装置吸收排烟余热,将除尘器后烟气温度从140℃降低到90℃左右,提高机组的经济性,节约能源。
由于烟气热量回收装置的传热温差低,因此换热面积大,占地空间也较大,所以在加装烟气热量回收装置时,需合理考虑其在锅炉现场的布置位置,并采用受热面优化设计方法来缩小烟气热量回收装置的外型尺寸,缓解布置上的困难。
如采用H型翅片管代替光管,增加换热面积,减少管排的数量。
烟气热量回收装置在烟气侧的布置共有三种方式。
a)布置在电器除尘器的进口,如图2.2-1。
日本的不少大型火电厂,如常陆那珂电厂(1000MW)和Tomato-Atsuma电厂(700MW)等都有类似的布置。
管式的GGH烟气放热段布置在空预器和除尘器之间。
管式GGH将烟气温度降低到90℃左右,并采用低低温电气除尘器。
对于本工程可以借鉴日本电厂的成熟经验,采用空预器下游烟气余热利用+低低温电气除尘器。
所谓低低温除尘器就是指入口烟气温度在100℃以下(烟气酸露点以下)的除尘器。
烟气换热器布置在电除尘前的优势有:
1)回收烟气余热,提高机组经济性;
2)烟气经低烟气换热器降温后,烟气体积减小,飞灰比电阻降低,可大大提高除尘器的收尘性,可实现更高的除尘效率,降低排放烟气中的含尘量;
3)烟温降低,烟气体积减小,引风机和脱硫增压风机(如有)容量相应减小,可降低引风机和脱硫增压风机(如有)能耗;
4)对于湿法脱硫,由于脱硫装置入口烟温降低,蒸发水分少,可节约脱硫用水。
但是采用此方案存在除尘器及下游设备烟道腐蚀的风险。
图2.2-1换热器布置在电除尘进口
b)布置在吸收塔入口,如图2.2-2。
布置位置在除尘器、引风机(增压风机)之后,烟气并不会对这些设备造成腐蚀,因而避免了腐蚀危险。
因为吸收塔内本来就是个酸性环境,烟气离开吸收塔时温度约为45~50℃。
塔内进行了防腐处理。
这种布置方式只要考虑对烟气换热器的低温段材料和烟气换热器与吸收塔之间的烟道进行防腐。
烟气换热器布置在引风机后至脱硫装置前的烟道内的优势:
1)烟气换热器布置在引风机后至脱硫装置前,可充分利用引风机温升,更大化提高烟气余热利用;
2)经过除尘器收尘,烟气换热器工作环境含尘少,对换热管道的磨损较小,运行风险大为降低;
3)对于湿法脱硫,由于脱硫装置入口烟温降低,蒸发水分少,可节约脱硫用水。
采用这种布置方式的缺点是无法利用烟气温度降低带来的提高电气除尘器效率、减少引风机(增压风机)功率的好处;其次,其布置位置远离主机,用于降低烟气温度的凝结水管和用于吹灰的辅助蒸汽管道也较方案一长,凝结水泵需克服的管道阻力也更高。
图2.2-2换热器布置在吸收塔进口
c)分段布置在吸收塔入口和电除尘器进口的两级布置。
烟气换热器两级布置兼有第一、第二两种布置方式的优势(如图2.2-3),但是烟气换热器体积较大,给布置带来一定的困难;由于烟气换热器两级布置,两级换热器串联布置,系统连接复杂,管道需求量比前两种方式都要大,管路阻力及烟阻也将有一定的增加。
图2.2-3换热器的两级布置
2.3烟气换热器热力参数的选取原则
烟气换热器热力参数选取的原则是:
在满足安全性要求的前提下,兼顾经济性。
所以首先要保证烟气换热器的受热面的能够安全的工作,不会因为腐蚀、磨损等问题而停运,这就需要对酸露点、烟气的低温腐蚀特性及管壁温度与管内外介质的关系等问题进行研究;在满足安全性的基础上,要尽量提高烟气换热器运行的经济性,尽可能多且高效的回收烟气余热,同时尽量减少自身能耗,提高电厂的经济效益,所以要对回热系统的运行参数进行优化。
2.3.1酸露点的计算
对于锅炉的烟气露点温度,国内外有大量的研究结果,由于锅炉的烟气结露问题复杂、研究价值大,所以有大量的人力从不同的侧重点进行了研究,研究结论差别很大。
对于同一种烟气成分,应用不同的研究结论进行计算所得到的烟气露点温度差别很大。
一般来讲,烟气露点温度和燃煤成分中的水分含量、硫含量、氢含量、灰分含量、发热量、炉膛燃烧温度、过量空气系数等因素有关,但这些因素的影响幅度不同,所以有的计算中会忽略有些因素的影响。
煤质分析资料见表1.1.3-1。
在众多酸露点计算公式中,苏联1973年锅炉热力计算标准中推荐的公式应用最广泛,也比较接近实际。
烟气酸露点温度计算公式为:
(2.3.1-1)
其中:
tld为酸露点温度,
为水露点温度,β取125,Szs为折算硫分,Azs为折算灰分,αfh为飞灰含量,取0.85。
将表2.3.1中的数据代入式(2.3.1-1)可得:
设计煤种的酸露点为90.34℃,水露点为38.4℃;
校核煤种的酸露点为70.14℃,水露点为39.14℃。
2.3.2露点腐蚀的影响因素
影响露点腐蚀的因素很多,按照影响程度,可以认为,影响露点腐蚀速率最大的几个因素是燃料、转化率、酸沉积率、温度、材料。
可以写成:
露点低温腐蚀速率=f(燃料,转化率,酸沉积率,温度,材料)
关于露点低温腐蚀,国外研究比较早,通过学习和了解国外在露点腐蚀研究领域的已有成果和最新进展,我们至少可以得出以下几个结论:
(a)试验表明:
金属的腐蚀与换热面的金属壁面温度有关;
(b)露点低温腐蚀速率受控于腐蚀性元素的氧化转化率;
(c)腐蚀速率受控于酸冷凝沉积率,而不是酸和金属的反应速率;
(d)最大露点腐蚀速率并不是发生在露点温度,而是发生在酸露点温度之下和水露点温度以下,图2.3.2示出了不同材料腐蚀速度随壁温变化图;
图2.3.2腐蚀速度随壁温变化图
通过选择优质的ND钢材料,可以解决硫酸露点腐蚀的问题,但是如果换热元件的金属表面温度过低,还是会有问题的。
图2.3.2是高硫烟气通过一组温度逐次降低的金属管排而发生低温腐蚀的实验数据,当金属壁温接近酸露点温度时,低温腐蚀最初阶段并不严重,这是因为最初凝结下来的硫酸浓度比较高,而浓硫酸对金属的腐蚀性不强。
随着金属壁温的进一步降低,烟气中的硫酸蒸汽不断减少,凝结出得硫酸浓度也在降低,当凝结出得硫酸浓度到达50%左右时,达到腐蚀高峰,这是因为50%的硫酸对金属的腐蚀性最强。
之后,凝结出的硫酸浓度低于50%,腐蚀速率又逐渐降低。
当金属壁温接近水露点温度的时候,大量水蒸气发生凝结,水溶解了多种酸性物质,其腐蚀机理会非常复杂,腐蚀速率将在水露点附件大幅上升,金属管减薄将超过0.2mm/年,因此我们需要将烟气换热器的入水温度设置在水露点温度25℃以上的安全区域。
2.4烟气换热器布置方案
2.4.1布置方案
根据前述换热器布置方式及热力参数选取原则,并结合电厂实际情况,提出三种布置方案以供参考、对比和分析。
方案一:
设计将烟气换热器布置在电除尘前的两个垂直烟道内,每个烟道布置一台烟气换热器,共布置2台,烟气温度由140℃降至105℃左右。
方案二:
设计将烟气换热器布置在脱硫塔前的一个水平烟道内,只需布置一台烟气换热器,烟气温度由140℃降至90℃左右。
方案三:
设计将一级烟气换热器布置在电除尘前的两个垂直烟道内,每个烟道布置一台烟气换热器,烟气温度由140℃降至105℃左右;二级烟气换热器布置在脱硫塔前的一个水平烟道内,烟气温度由105℃降至90℃左右。
两级共布置3台换热器。