司质量管理考核办法.docx
《司质量管理考核办法.docx》由会员分享,可在线阅读,更多相关《司质量管理考核办法.docx(13页珍藏版)》请在冰豆网上搜索。
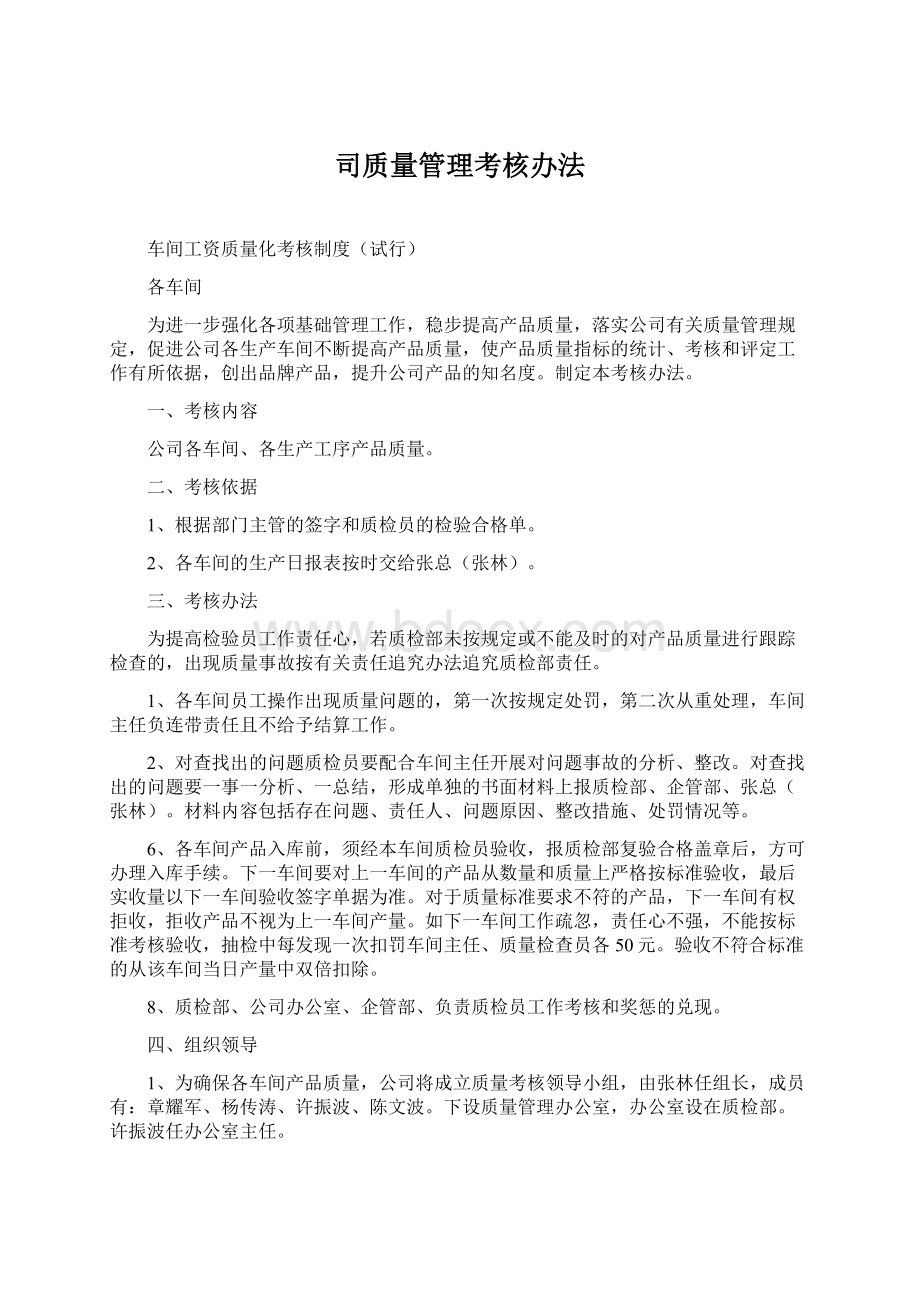
司质量管理考核办法
车间工资质量化考核制度(试行)
各车间
为进一步强化各项基础管理工作,稳步提高产品质量,落实公司有关质量管理规定,促进公司各生产车间不断提高产品质量,使产品质量指标的统计、考核和评定工作有所依据,创出品牌产品,提升公司产品的知名度。
制定本考核办法。
一、考核内容
公司各车间、各生产工序产品质量。
二、考核依据
1、根据部门主管的签字和质检员的检验合格单。
2、各车间的生产日报表按时交给张总(张林)。
三、考核办法
为提高检验员工作责任心,若质检部未按规定或不能及时的对产品质量进行跟踪检查的,出现质量事故按有关责任追究办法追究质检部责任。
1、各车间员工操作出现质量问题的,第一次按规定处罚,第二次从重处理,车间主任负连带责任且不给予结算工作。
2、对查找出的问题质检员要配合车间主任开展对问题事故的分析、整改。
对查找出的问题要一事一分析、一总结,形成单独的书面材料上报质检部、企管部、张总(张林)。
材料内容包括存在问题、责任人、问题原因、整改措施、处罚情况等。
6、各车间产品入库前,须经本车间质检员验收,报质检部复验合格盖章后,方可办理入库手续。
下一车间要对上一车间的产品从数量和质量上严格按标准验收,最后实收量以下一车间验收签字单据为准。
对于质量标准要求不符的产品,下一车间有权拒收,拒收产品不视为上一车间产量。
如下一车间工作疏忽,责任心不强,不能按标准考核验收,抽检中每发现一次扣罚车间主任、质量检查员各50元。
验收不符合标准的从该车间当日产量中双倍扣除。
8、质检部、公司办公室、企管部、负责质检员工作考核和奖惩的兑现。
四、组织领导
1、为确保各车间产品质量,公司将成立质量考核领导小组,由张林任组长,成员有:
章耀军、杨传涛、许振波、陈文波。
下设质量管理办公室,办公室设在质检部。
许振波任办公室主任。
2、质量考核领导小组负责对各车间的产品质量进行日常的监督检查,发现问题及时督促各单位限期整改,保证产品质量达标要求,各车间发货必须签定质量检验审批单。
3、各车间成立相应的质量管理领导小组,名单报质检部。
五、本考核办法自公布之日起执行。
附件:
1、产品质量考核标准
2、质量管理处罚规定
二О一一年十月二十日
附件1:
产品质量考核标准
一、板材质量标准
1.1 出口板材质量标准
1.1.1 A级板材质量标准
径向加工年轮细密通顺,颜色一致。
不允许腐朽、蓝变、开裂、虫眼、油线、夹皮、弯曲、翘曲、扭曲及加工材质缺陷。
1.1.2 B级板材质量标准
径向加工年轮线基本通直,颜色基本一致,允许一个大面完好,另一个大面有1cm以内的活节2-3个。
不允许腐朽、蓝变、开裂、虫眼、油线、夹皮、弯曲、翘曲、扭曲及加工材质缺陷。
1.1.3 A级集成材质量标准
径向加工、弦向加工、径弦不分三种加工方式。
颜色一致,条幅宽度一致,指接处不允许有空隙,涂胶均匀,二大面无任何材质及加工缺陷。
砂光根据客户要求。
不允许修补。
1.1.4 B级集成材质量标准
径向加工、弦向加工、径弦不分三种加工方式。
颜色基本一致,条幅宽度一致,指接处不允许有空隙,涂胶均匀,一个大面完好,别一大面允许1cm以内的活节2-3个。
无任何材质及加工缺陷。
砂光根据客户要求,允许修补但不允许有修补痕迹。
1.2 国内板材质量标准:
1.2.1 A级板材质量标准
径弦切材不分,允许一个板面上有1cm内的活节2个,别一大面完好,不允许腐朽、虫眼、变色、开裂、油线、夹皮等,材质及加工缺陷。
1.2.2 B级板材质量标准
径弦切材不分,两大面允许轻微色差,活节1cm以内5个,不允许开裂、虫眼、蓝变、腐朽、死节等加工缺陷。
1.3 铁杉地板质量标准
1.3.1 A级铁杉地板标准
树种铁杉,板面平整,光滑采用240#砂光,不允许弯曲、翘曲、扭曲、腐朽、虫眼、蓝变、开裂、死节、修补及加工缺陷和材质缺陷,几何尺寸必须准确无误。
1.3.2 B级铁杉地板标准
树种铁杉,板面平整,采用240#砂光,不允许弯曲、翘曲、扭曲、腐朽、虫眼、蓝变、开裂、死节、修补。
允许1cm以内的活节1-2个,轻微色差允许。
不允许其他加工缺陷和材质缺陷。
几何尺寸必须准确无误。
1.3.3 合格品铁杉地板标准
树种铁杉,板面平整,采用240#砂光,不允许弯曲、翘曲、扭曲、腐朽、开裂、死节。
轻微色差允许,活节允许,其它缺陷不可。
1.3.4 两端必须成90°。
1.4 规格材质量标准
1.4.1 严格按照客户订单质量标准执行。
1.4.2 所有产品(成品)不允许负公差。
二、原木质量标准
2.1 原木名称,定义的解释。
按GB155.2-84《针叶树木材缺陷名称,定义和对材质的影响》,GB4823.2-84《阔叶树木材缺陷名称,定义和对材质的影响》的规定执行,各种缺陷的允许限度,按原木标准的规定执行。
2.2 检量各种缺陷的尺寸单位规定
2.2.1 纵裂长度,外夹皮长度,弯曲水平长度,弯曲拱高,扭转纹倾斜高度,环裂半径,弧裂拱高,外伤深度,偏枯深度均量至厘米止(以下均以cm表示),不足厘米者舍去。
2.2.2 其他各种缺陷均量至毫米止(以下均以mm表示),不足毫米者舍去.对节子尺寸,虫眼最小直径和深度,裂纹宽度,外夹皮深度的计算起点尺寸,均按本标准有关条款的规定执行。
2.3 检尺长范围
检尺长范围外的缺陷,除漏节,腐朽外,其他缺陷不予计算.
2.4 节子
2.4.1 节子尺寸的检量是与树干纵长方向成垂直量得的最大节子尺寸与检尺径相比,以百分率节子尺寸不足30mm和阔叶树的活节,均不计算尺寸和个数。
2.4.1.1 针叶树的活节,应检量颜色较深,质地较硬部分(似黑眼球)的尺寸。
2.4.1.2 节子基部呈凸包形的,应量凸包上部的节子正常部位尺寸。
2.4.1.3 阔叶树活节断面上的腐朽或空洞,按死节处理。
量其腐朽或空洞尺寸(与量节子尺寸方法相同)作为死节尺寸。
2.4.1.4 大头连岔,指在树干两个分岔下部造材形成,断面有两个髓心并呈两组年轮系统,这种现象,不论连岔部位有无缺陷均不计算;如不构成两组年轮系统或因一般节子形成者,则按节子计算。
2.4.2 节子个数的统计是在材身检尺长范围内,任意选择节子个数最多的1m中查定.但跨在该1m长一端交界线上不足二分之一的节子和检尺长终止线上及断面上的节子均不予计算。
统计1m中的节子个数时,针叶树原木的活节,死节,漏节应相加计算;阔叶树原木的死节,漏节应相加计算。
2.5 漏节
漏节不论其尺寸大小,均应查定在全材长范围内的个数,在检尺长范围内的漏节,还应计算其尺寸。
2.6 材腐朽(外部腐朽)
2.6.1 边材腐朽的检量:
断面上的边材腐朽(包括不正形的),以通过腐朽部位径向量得的量大厚度与检尺径相比,以百分率表示。
材身上的边材腐朽以弧长最宽处量得的边材腐朽深度与检尺径相比,如边材腐朽弧长不超过该断面圆周长的一半者,则以边材腐朽深度的二分之一与检尺径相比。
检量材身边材腐朽深度,以尺杆顺材长贴平材身表面,与尺杆成垂直径向最取。
2.6.1.1 表现在断面的多块边材腐朽,其各块边材腐朽的弧长应相加计算。
2.6.1.2 表现在材身的多块边材腐朽,以弧长最大一块的最宽处量得边材腐朽深度为准。
计算弧长时,应将该处同一圆周线上的多块边材腐朽弧长相加。
2.6.2 材身,断面均有边材腐朽(含材身贯通到断面的),应以降等最低一处为评等依据。
断面上边材腐朽与心材腐朽相连的,按边材腐朽评等;断面边材部位的腐朽未露于材身外表的,按心材腐朽评等。
2.7 心材腐朽(内部腐朽)
2.7.1 心材腐朽的检量,是以腐朽面积与检尺径断面面积(指按检尺径计算的面积)相比,以百分率表示.
在同一断面内有多块各种形状(弧状,环状,空心等)的分散腐朽,均合并相加,调整成相当于腐朽的实际面积与检尺径断面面积相比。
2.7.2 在同一断面同时存在心材腐朽和边材腐朽,如该两种腐朽同属于三等原木限度者,应降为等外原木。
2.7.3 桦木断面粗糙,材色正常(有的是伪心材),木质坚硬的属于正常现象。
如木质粗糙松软,年轮不清晰,材异变,这种状态按腐朽处理。
2.7.4 已脱落劈裂材劈裂面上的腐朽,如贯通材身表面的按边材腐朽计算,通过腐朽部位径向检量其腐朽厚度;未贯通材身表面的按心材腐朽计算,与材长方向成垂直检量腐朽最大宽度作为心材腐朽直径,并视为圆形面积与检尺径断面面积相比;腐朽露于断面的以断面上腐朽的面积与检尺径断面面积相比。
2.8 虫眼
在材身检尺长范围内,任意选择虫眼最多的1m中查定个数。
应计算的虫眼,是指虫眼最小直径自3mm以上,同时深度自10mm以上,不足以上尺寸的不计。
虫眼直径以量得最小孔径为准;深度以贴平材表面垂直量得的深度为准。
查定虫眼个数量,跨在1m长交界线上和检尺长终止线上的虫眼以及原木断面上的虫眼,均不予计算。
2.9 裂纹
原木中一般只计算纵裂纹。
裂纹在针叶树原木中,其宽度不足3mm;阔叶树原木中,其宽度不足5mm的不予计算。
2.9.1 纵裂纹是以其长度与检尺长相比,以百分率表示。
2.9.1.1 材身有两根或数根纵裂,彼此相隔的木质宽度不足3mm的,应合并为一根计算长度;自3mm以上的,应分别计算其长度。
2.9.1.2 沿材身扭转开裂的裂纹,按纵裂计算。
应与材长纵轴平行检量裂纹长度。
2.9.1.3 松木的油线开裂和阔叶树材身的冻裂,其开裂部分的长度,均按纵裂计算。
2.9.2 环裂,弧裂,以断面最大一处环裂(指开裂超过半环的)半径或弧裂(指开裂不超过半环)拱高与检尺径相比。
2.9.3 阔叶树原木断面径向开裂成三块或数块,其中有三条裂口,宽度表现在该端材身上均足10mm,称为“炸裂”。
炸裂应按裂纹评等后再降一等,但三等的不再降等。
2.10 弯曲
2.10.1 检量弯曲应从大头至小头拉一直线,其直线贴材身两个落线点间的距离为内曲水平长,与该水平直线成垂直量其弯曲拱高,与该内曲水平长相比,以百分率表示.如有几个弯曲,评等时应以最大拱高的弯曲为准。
遇有两处最大弯曲拱高相等,则以其降等最低一处弯曲为准。
2.10.2 量内曲水平长时,遇有节子,瘤包应当让去,取正常部位检量。
对于双心,肥兜,凸兜形成树干外形弯曲,均不按弯曲计算。
2.11 扭转纹
扭转纹是检量小头1m长范围内的纹理扭转起点至终点的倾斜高度(在小头断面上表现为弦长)与检尺径相比,以百分率表示。
2.12 外夹皮
外夹皮深度不足3cm的不计。
自3cm以上的,则检量其夹皮全长与检尺长相比,以百分率表示。
2.12.1 外夹皮是顺材长呈沟条状,有的沟条底部裸露枯死木质,近似偏枯。
为了便于区别检量,凡沟条最宽处的两内侧或底部的宽度不超过检尺径10%的,按外夹皮计算;超过10%的,按偏枯处理。
2.12.2 断面上外夹皮处木质有腐朽,如腐朽位于沟条内侧或底部的,按外夹皮,心材腐朽降等最低缺陷量算;腐朽位于沟条外部的,按外夹皮,边材腐朽降等最低一种缺陷计算。
2.12.3 材身外夹皮沟条处木质有腐朽,按外夹皮,漏节降等最低一种缺陷计算。
2.13 偏枯
偏枯是量其径向深度与检尺径相比,以百分率表示.已腐朽的偏枯,按偏枯,边材腐朽降等最低一种缺陷计算。
检量偏枯深度或边材腐朽深度,应以尺杆横贴原木表面径向量取。
2.14 外伤
外伤包括割脂伤,摔伤,烧伤,风折,刀斧伤,材身磨伤和其他机械损伤(打枝伤,刨勾眼不计)。
风折是查定个数,锯口伤限制深度外,其他各种外伤均量其损伤深度与检尺径相比,以百分142-84《直接用原木》和GB143.3-84《针叶树加工用原木分等》,GB4813.3-84《阔叶树加分等》中,均不得超过检尺径的20%,超过者应予让尺。
2.15 其他
2.15.1 材身树瘤外表完好的,不按缺陷计算。
如树瘤上有空洞或腐朽的,按死节计算;已引起内部木质腐朽的,按漏节计算。
2.15.2 啄木鸟眼按虫眼和外伤计算。
如引起树干内部木质腐朽,按漏节计算;引起树干外表木质腐朽的,则按边材腐朽处理。
2.15.3 原木大头抽心,其抽心面积不超过检尺径断面面积16%的不计;超过16%应评为二等材。
2.15.4 白蚂蚁蛀蚀,其深度不足10mm的不计;自10mm以上的,在材身上按边材腐朽计算,在断面上按心材腐朽计算。
附件2:
质量管理处罚规定
(一)
1.1 适用车间
物流中心
1.2 质量标准处罚规定
1.2.1 原木不严格按材种、材质分类,没有明显标示,每发现一次扣货场办公室主任20元。
1.2.2 树皮不及时清理集中保存,每发现一次扣货场办公室主任10元。
1.2.3 不按指令造材,每发现一次扣当班人员每人20元。
1.2.4 不结合原木长度认真分析会诊,盲目造材并造成原木轻微浪费,每发现一次扣当班人员每人20元,造成整根原木不能使用的提交公司对当班人员按照质量事故处理。
1.2.5 造材原木长度、材种混放,码放不整齐,每发现一次扣当班人员每人10元。
1.2.6 消极怠工影响生产,每发现一次扣罚责任人100元。
1.2.7 不按照设备保养要求维护车辆,下班前不对车辆清洁保养,每发现一次扣罚责任人10元。
造成车辆损毁影响生产,扣罚责任人100元并按事故处理。
1.2.8 丢失、损坏车辆配件,每发现一次扣罚责任人20元并照价赔偿。
1.2.9 直径在30mm以上的原木表面无节、年轮线细密(日本级)的原木另行堆码,如不按标准和质量分票堆码,发现一次扣罚当班人员10元、质检员10元、单位负责人20元,并当日以书面式的整改材料上报质检部。
(二)
2.1 适用车间
一车间(制材车间)
2.2 质量标准处罚规定
2.2.1 清理:
2.2.1.1 原木表面清理不彻底遗留有细微沙砾、树皮,每发现一次扣当班人员每人10元。
2.2.1.2 清理不彻底造成锯条被毁影响正常生产,赔偿锯条损失并提交公司对当班人员按照质量事故处理。
2.2.1.3 不按要求对原木进行调整消极怠工,每发现一次扣责任人10元。
2.2.2 带锯操作:
2.2.2.1 未经允许擅自生产,每发现一次扣当班人50元;造成规格误差严重,提交公司按质量事故处理。
2.2.2.2 责任心不强不能按质取材,造成产品附加值降低,每发现一次扣当班人20元。
2.2.2.3 不爱惜设备,每天不进行维护保养,每发现一次扣当班人10元。
2.2.3 摇尺:
2.2.3.1 不熟悉生产定单加工规格,每发现一次扣当班人员10元。
2.2.3.2 定尺错误,造成规格误差,每发现一次扣当班人员20元。
造成整根原木浪费的,提交公司对责任人按质量事故处理。
2.2.3.3 不爱惜设备,每天不进行维护保养,每发现一次扣当班人10元。
2.2.4 带锯接料:
2.2.4.1 不按产品规格、材种码放,每发现一次扣当班人员每人10元。
2.2.4.2 边皮料、板材混放,每发现一次扣当班人员每人10元。
2.2.5 台锯操作:
2.2.5.1 不按要求对板材进行清边,每发现一次扣当班人员20元。
2.2.5.2 不按规格厚度加工,每发现一次扣当班人员20元。
2.2.5.3 大方加工成普通板材,每发现一次扣当班人员50元。
2.2.5.4 不爱惜设备,每天不进行维护保养,每发现一次扣当班人10元。
2.2.6 台锯接料:
2.2.6.1 不按产品规格、材种码放,每发现一次扣当班人员每人10元。
2.2.6.2 边皮料、板材混放,每发现一次扣当班人员每人10元。
2.2.7 叉车司机:
2.2.7.1 不按照安全操作规程作业,每发现一次扣当班人员20元。
2.2.7.2 不按照设备保养要求维护车辆,下班前不对车辆清洁保养,每发现一次扣罚责任人10元。
造成车辆损毁影响生产,扣罚责任人100元并按事故处理。
2.2.7.3 消极怠工影响生产,每发现一次扣当班人员20元。
2.2.7.4 丢失、损坏车辆配件,每发现一次扣当班人员20元并赔偿。
(三)
3.1 适用车间
二车间(干燥车间)
3.2 质量标准处罚规定
3.2.1 码料:
3.2.1.1 码料时不按材种、等级、厚度码垛,每发现一次扣罚责任人每人10元。
3.2.1.2 垫方、隔条放置不正确,不按规定高度码垛,每发现一次扣罚责任人每人10元。
3.2.1.3 规定回收尺寸内木料没有回收单独码放,每发现一次扣罚责任人每人10元。
3.2.1.4 边皮料与板材混码,每发现一次扣罚责任人每人10元。
3.2.2 装窑、出窑:
3.2.2.1 不按厚度装窑或混装时超过公差要求,每发现一次扣罚车间主任、责任人每人20元。
3.2.2.2 随意装窑,造成窑内空间利用率低,每发现一次扣罚车间主任、责任人每人50元。
3.2.2.3 出窑板材不按要求放入指定位置,每发现一次扣罚责任人10元。
3.2.3干燥:
3.2.3.1 干燥板材含水率高于12%,车间提交质量事故分析报告并扣罚责任人50元。
3.2.3.2 干燥板材合格率低于95%,车间提交质量事故分析报告并扣罚责任人50元。
3.2.3.3 不按要求记录设备运行数据,每发现一次扣罚责任人20元。
3.2.4叉车司机:
3.2.4.1 不按照安全操作规程作业,每发现一次扣罚责任人20元。
3.2.4.2 不按照设备保养要求维护车辆,下班前不对车辆清洁保养,每发现一次扣罚责任人10元。
造成车辆损毁影响生产,扣罚责任人100元并按事故处理。
3.2.4.3 消极怠工影响生产,每发现一次扣罚责任人20元。
3.2.4.4 丢失、损坏车辆配件,每发现一次扣罚责任人20元并赔偿。
3.2.4.5 不按质量标准分类码垛,不予绩算绩效工资,从当月绩效工资扣除并立即整改。
(四)
4.1 适用车间
三车间(刨切车间)
4.2 质量标准处罚规定
4.2.1 蒸煮:
4.2.1.1 不按照操作规程作业,每发现一次扣罚责任人20元。
4.2.1.2 不按照材质蒸煮时间要求作业,造成原木材质达不到刨切要求影响生产,每发现一次扣罚责任人50元。
4.2.2 刨切:
4.2.2.1 单板表面有刀痕、厚度不一致,每发现一次扣罚责任人20元。
4.2.2.2 不按操作规程作业,每发现一次扣罚责任人20元。
4.2.2.3 不爱惜设备,每天不进行维护保养,每发现一次扣当班人10元。
4.2.3 单板干燥:
4.2.3.1 干燥单板含水率高于12%,每发现一次扣罚责任人20元。
4.2.3.2 不按操作规程作业,每发现一次扣罚责任人20元。
4.2.3.3 不爱惜设备,每天不进行维护保养,每发现一次扣当班人10元。
4.2.4 剪切:
4.2.4.1 不按规格剪切、产品剪切不平行,每发现一次扣罚责任人20元。
4.2.4.2 不按操作规程作业,每发现一次扣罚责任人20元。
4.2.4.3 不爱惜设备,每天不进行维护保养,每发现一次扣当班人10元。
4.2.5 分检:
4.2.5.1 不按质量等级标准分检,每发现一次扣罚责任人20元。
4.2.5.2 不按要求验收、检验、包装,每发现一次扣罚责任人20元。
4.2.6 叉车司机:
4.2.6.1 不按照安全操作规程作业,每发现一次扣罚责任人20元。
4.2.6.2 不按照设备保养要求维护车辆,下班前不对车辆清洁保养,每发现一次扣罚责任人10元。
造成车辆损毁影响生产,扣罚责任人100元并按事故处理。
4.2.6.3 消极怠工影响生产,每发现一次扣罚责任人20元。
4.2.6.4 丢失、损坏车辆配件,每发现一次扣罚责任人20元并赔偿。
4.2.6.5 车间生产的所有产品,凡检查不合格,不予绩算绩效工资,并按值赔偿,在当月绩效工资内扣除。
(五)
5.1 适用车间
四车间(指接车间)
5.2 质量标准处罚规定
5.2.1 刨光:
5.2.1.1 厚度不同板材同时加工,每发现一次扣罚责任人每人10元。
5.2.1.2 刨光板材出现漏刨、凹凸、条楞、厚度不均等缺陷,每发现一次扣罚责任人每人10元。
5.2.1.3 材种、等级不分同时加工,每发现一次扣罚责任人每人10元。
5.2.1.4 不按生产加工通知单加工,每发现一次扣罚责任人每人10元。
5.2.1.5 不爱惜设备,每天不进行维护保养,每发现一次扣当班人10元。
5.2.2 制条:
5.2.2.1 不按材种、厚度、等级分别加工,每发现一次扣罚责任人每人10元。
5.2.2.2 指接条不按原有级别码放,每发现一次扣罚责任人每人10元。
5.2.2.3 不爱惜设备,每天不进行维护保养,每发现一次扣当班人10元。
5.2.3 截断:
5.2.3.1 取材长度低于250mm,超出900mm,每发现一次扣罚责任人10元。
5.2.3.2 不按标准分选或错放,每发现一次扣罚责任人10元。
5.2.3.3 不爱惜设备,每天不进行维护保养,每发现一次扣当班人10元。
5.2.4 指接:
5.2.4.1 指接条存在厚度、颜色或不按要求区分径弦,每发现一次扣罚责任人10元。
5.2.4.2 规格不同混接、错齿,指接条不按规格、等级码放,每发现一次扣罚责任人10元。
5.2.4.3 不爱惜设备,每天不进行维护保养,每发现一次扣当班人10元。
5.2.5 四面刨光:
5.2.5.1 养护期内加工,每发现一次扣罚责任人10元。
5.2.5.2 加工后还存有缺陷,每发现一次扣罚责任人10元。
5.2.5.3 不爱惜设备,每天不进行维护保养,每发现一次扣当班人10元。
5.2.6 拼板:
5.2.6.1 不按等级标准排板,每发现一次扣罚责任人10元。
5.2.6.2 版面拼条宽度不一致,每发现一次扣罚责任人10元。
5.2.6.3 版面不平整,有开胶现象,每发现一次扣罚责任人10元。
5.2.6.4 不爱惜设备,每天不进行维护保养,每发现一次扣当班人10元。
5.2.7 裁板:
5.2.7.1 不按生产加工通知单裁板,每发现一次扣罚责任人20元。
5.2.7.2 出现负公差,车间提交质量事故分析报告并扣罚责任人50元。
5.2.7.3 不爱惜设备,每天不进行维护保养,每发现一次扣当班人10元。
5.2.8 砂光:
5.2.8.1 不按生产加工通知单磨砂,每发现一次扣罚责任人10元。
5.2.8.2 砂光后出现板面不平整、啃头每发现一次扣罚责任人10元。
5.2.8.3 砂光后出现负公差,车间提交质量事故分析报告并扣罚责任人50元。
5.2.8.4 不爱惜设备,每天不进行维护保养,每发现一次扣当班人10元。
5.2.9 地板:
5.2.9.1 选面生产A级无节、无腐朽、开裂、虫眼、变色,两端开榫后必须成90°,不能有歪斜,拼在一起必须平整。
5.2.9.2 B级:
允许有细小的活节(活节在10mm以内),其它质量标准和A级一样。
5.2.9.3 C级:
允许有节(在10mm以内),但不能脱落,其它质量标准和B级一样。
5.2.9.4 不按质量规格生产发现一次扣当班人员50元,造成重大损失,按质量事故分析处理。
5.2.10 叉车司机:
5.2.10.1 不按照安全操作规程作业,每发现一次扣罚责任人20元。
5.2.10.2 不按照设备保养要求维护车辆,下班前不对车辆清洁保养,每发现一次扣罚责任人10元。
造成车辆损毁影响生产,扣罚责任人100元并按事故处理。
5.2.10.3 消极怠工影响生产,每发现一次扣罚责任人20元。
5.2.10.4 丢失、损坏车辆配件,每发现一次扣罚责任人20元并赔偿。
5.2.10.5 车间每道工序不按质量标准生产,扣罚当班人员10元、车间负责人20元,所有产品验货不符合质量标准的不给予绩算绩效工资,并按材积扣除绩效工资,并按价赔偿,从当月绩