塑胶模具基本结构.docx
《塑胶模具基本结构.docx》由会员分享,可在线阅读,更多相关《塑胶模具基本结构.docx(25页珍藏版)》请在冰豆网上搜索。
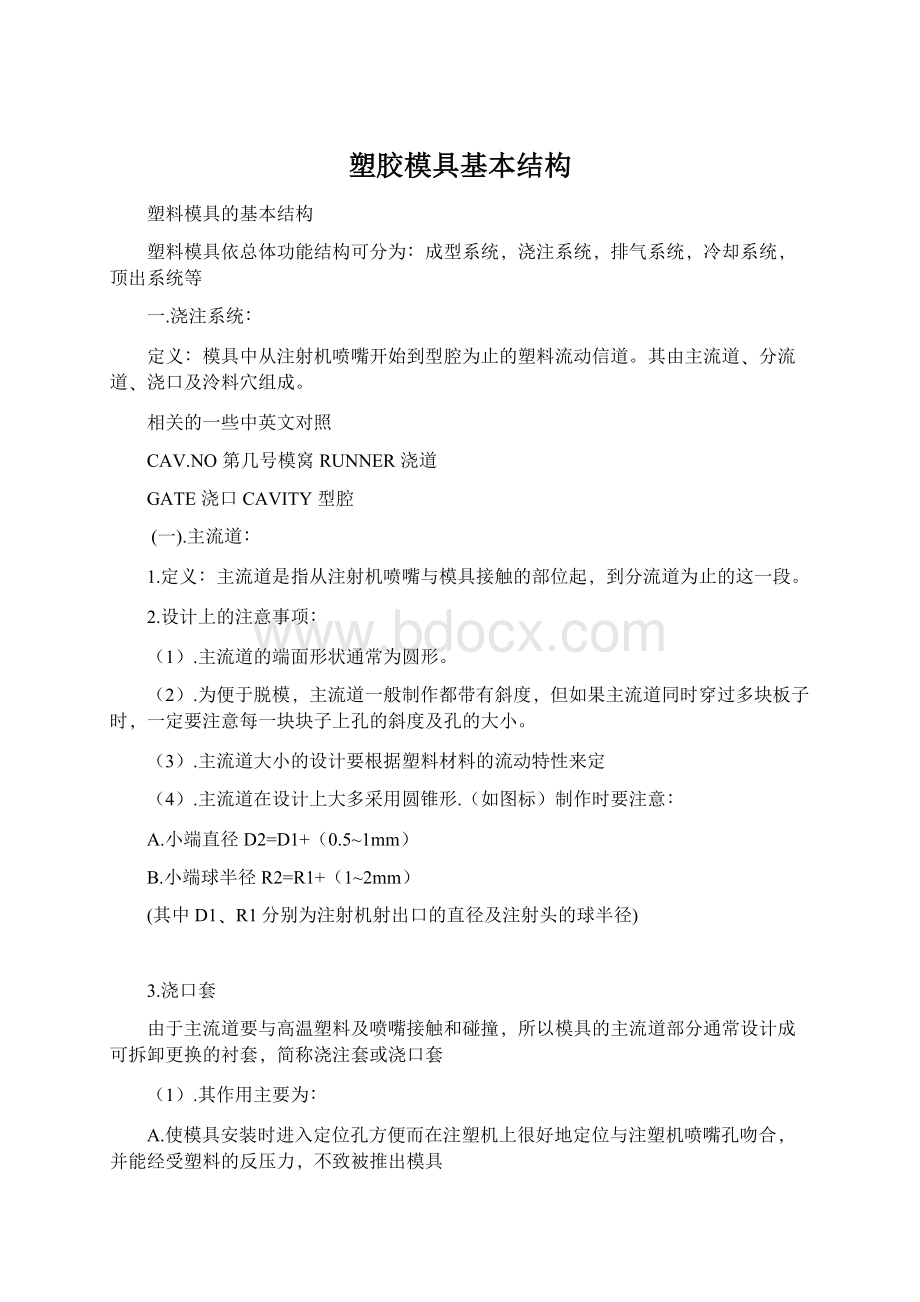
塑胶模具基本结构
塑料模具的基本结构
塑料模具依总体功能结构可分为﹕成型系统﹐浇注系统﹐排气系统﹐冷却系统﹐顶出系统等
一.浇注系统﹕
定义﹕模具中从注射机喷嘴开始到型腔为止的塑料流动信道。
其由主流道﹑分流道﹑浇口及泠料穴组成。
相关的一些中英文对照
CAV.NO第几号模窝RUNNER浇道
GATE浇口CAVITY型腔
(一).主流道﹕
1.定义﹕主流道是指从注射机喷嘴与模具接触的部位起﹐到分流道为止的这一段。
2.设计上的注意事项﹕
(1).主流道的端面形状通常为圆形。
(2).为便于脱模﹐主流道一般制作都带有斜度﹐但如果主流道同时穿过多块板子时﹐一定要注意每一块块子上孔的斜度及孔的大小。
(3).主流道大小的设计要根据塑料材料的流动特性来定
(4).主流道在设计上大多采用圆锥形.(如图标)制作时要注意﹕
A.小端直径D2=D1+(0.5~1mm)
B.小端球半径R2=R1+(1~2mm)
(其中D1﹑R1分别为注射机射出口的直径及注射头的球半径)
3.浇口套
由于主流道要与高温塑料及喷嘴接触和碰撞﹐所以模具的主流道部分通常设计成可拆卸更换的衬套﹐简称浇注套或浇口套
(1).其作用主要为﹕
A.使模具安装时进入定位孔方便而在注塑机上很好地定位与注塑机喷嘴孔吻合﹐并能经受塑料的反压力﹐不致被推出模具
B.作为浇注系统的主流道﹐将料筒内的塑料过渡到模具内﹐保证料流有力畅通地到达型腔﹐在注射过程中不应有塑料溢出﹐同时保证主流道凝料脱出方便。
(2)结构形式有整体式和分体式
整体式﹕即台肩与构成主流道部份做成一体
分体式﹕即台肩与构成主流道部份分开制作
日本的工业标准﹕JIS
中国的工业标准﹕SJB
(二)。
分流道﹕
定义﹕主流道与浇口之间的一段﹐它是熔融塑料由主流道流入型腔的过渡段也是浇注系统中通过断面面积变化及塑料转向的过渡段﹐能使塑料得到平稳的转换。
1.截面设计
A.一般设计截面为圆形
B.从加工方便性来看一般设计为U形﹐V形﹐梯形﹐正六边形
C.分流道的断面形状及尺寸大小﹐应根据塑件的成型体积﹐塑件壁厚﹐塑件形状﹐所用塑料工艺特性﹐注射速率﹐分流道长度等因素来确定。
2.分流道的布置形式有平衡式进料和非平衡式进料两种形式。
平衡式进料就是保证各个进料口同时均衡地进料﹐非平衡式进料就是各个进料口不能同时均衡地进料﹐一般要做模流分析来进行评估。
(三).浇口
1.定义﹕浇口又称进料口或内流道。
它是分流道与塑件之间狭窄的部份﹐也称浇注系统最短小的部份﹔
2.作用﹕能使分流道输送过来的熔融塑料的流速产生加速度﹐形成理想的流态﹐顺序﹐并速速地充满型腔﹐同时还起着封闭型腔防止熔料倒流的作用﹐并在成型后便于使浇口与塑件分离。
3.浇口的形式﹕
内侧浇口
普通侧浇口(边缘浇口)﹕
外侧浇口
扇形浇口﹕常用来成型宽度较大的薄片状塑件
平缝式浇口
护耳式浇口
隙式浇口
一般点浇口
潜伏式浇口(我公司大多采用此种方式)
盘环型浇口
轮辐式浇口
爪形浇口
园环形浇口
3>.浇口位置的选择
(1)浇口选择有阻挡物最近的距离。
(2)浇口的尺寸及位置选择应避免产生喷射和蠕动。
(3)浇口应开设在塑件断面最厚处。
(4)浇口位置的选择应使塑料流程最短﹐料流变向最少。
(5)浇口位置选择应有利于型腔内气体的排出。
(6)浇口位置的选择应减少或避免塑件的熔接痕增加熔接牢度。
(7)浇口位置的选择应防止料流将型腔﹐型蕊﹐嵌件挤压变形。
(四).冷料穴
1.结构﹕冷料穴是用来储臧注射间隔期间产生的冷料头的﹐防止冷料进入型腔而影响塑件质量﹐并使熔料能顺利地充满型腔﹐冷料穴又称冷料井。
2.拉料形式﹕
(1)钩形(工形)拉料杆
(2)球形拉料杆
3.圆锥形拉料杆
4.拉料穴﹕A.带顶杆﹔B.不带顶杆
第一章塑料
一﹑塑料的分子结构﹕塑料主要成份是树脂﹐树脂有天然树脂和合成树
脂两种。
二﹑塑料的成份﹕
2.树脂﹕主要作用是将塑料的其它成份加以粘合﹐并决定塑料的类型(热
塑性或热固性)和主要性能﹐如机械﹑物理﹑电﹑化学性能等。
树脂在塑料中的比例一般为40~65%。
2.填充剂﹕又称填料﹐正确地选择填充剂﹐可以改善塑料的性能和扩
大它的使用范围。
3.增塑剂﹕有些树脂的可塑性很小﹐柔软性也很差﹐为了降低树脂的
熔融粘度和熔融温度﹐改善其成型加工性能﹐改进塑料的柔
韧性﹐弹性以及其它各种必要的性能﹐通常加入能入树脂相
容的不易挥发的高沸点的有机化合物。
这类物质称增塑剂。
增塑常是一种高沸点液纳或熔点固体的酯类化合物。
4.着色剂﹕又称色料﹐主要是起美观和装饰作用﹐包括涂料两部分。
5.稳定剂﹕凡能阴缓塑料变质的物质称稳定剂﹐分光稳定剂﹑热稳定
剂﹑抗氧剂。
6.润滑剂﹕改善塑料熔体的流动性﹐减少或避免对设备或模具的磨擦
和粘附﹐以及改进塑件的表面光洁度。
三﹑塑料的工艺特性﹕
塑料在常温下是玻璃态﹐若加热则变成高弹态﹐进而变成粘流态﹐从而具有优良的可塑性﹐可以用许多高生产率的成型方法来制造产品﹐这样就能节省原料﹑节省工时﹐简化工艺过程﹐且对人工技朮要求低﹐易组织大批量生产。
1.收缩率或称缩水率。
设计前一定先问供货商的缩水率﹐模具设计时采用计算收缩率=常温模具尺寸-常温塑件尺寸
2.比容和压缩率。
3.流动性。
是塑料成形中一个很重要的因素﹐流动性好的易长毛边﹐设计时配合的间隙﹐气槽的深度等要根据不同材料的流动性设计尺寸。
4.吸湿性﹑热能性及挥发物含量。
吸水的塑料有的在塑料成型后直接放于水中让它吸饱水后再进行使用﹐有的塑料吸湿性特别大﹐比例有1﹕100
5.结晶性。
6.应力开裂及熔体液裂。
7.定型速度。
四﹑塑料种类﹕
1.热塑性塑料﹕这类塑料的合成树都是线型或支链型高聚物﹐因而受热变软﹐甚至成为可流动的稳定粘稠液体﹐在此状态时具有可塑性﹐可塑制成一定形状的塑件﹐冷却后保持既得的形状﹐如再加热又可变软成另一种形状﹐如此可以进行反复多次。
这一过程中只有物理变化﹐而无化学变化﹐其变化是可逆的。
(反复多次成型)
塑料种类﹕a.聚氯乙烯(PVC)产量大﹐有毒不能用作食品包装。
b.聚苯乙烯(PS)是最早的工业化塑料品种之一。
c.聚乙烯(PE)d.聚炳烯(PP)
e.尼龙(PA)f.聚甲醛(POM)
g.聚碳酸脂(PC)可用于食品包装﹐镜片。
h.ABS塑料
i.聚砚(PSU)j.聚苯醚(PPO)
K.氟塑料l.聚酯树脂
N.有机玻璃(PMMA)
2.热固性塑料﹕这类塑料的合成树脂是体型高聚物﹐因而在加热之初﹐因分子呈线型构具有可熔性和可塑性﹐可塑制成一定形状的塑件﹐当继续加热时﹐分子呈现风状结构﹐当温度达到一定程度后﹐树脂变成不溶和不熔的体型结构﹐使形状固定下来﹐不再变化。
如有加热也不软化﹐不再具有可。
在一定变化过程中﹐既有物理变化﹐又有化学变化﹐因此﹐变化过程中不可逆的。
(一次成型)
种类﹕A.酚酸塑料PF
B.氨基塑料
C.环氧树脂EP
D.酚醛塑料(PF)又称电木﹐用于电气开关﹐热固性材料。
第二章通用注射成型系统及工作循环
一﹑通用注射线型系统﹐是指热塑料的通用注射成形系统﹐其包括用来成型的和最后成型好的塑件﹐以及用来保证塑件成型的注射机和注射模待组成。
常用注射成型系统﹕1.机身2.电同及油泵3.注射油缸4.齿轮箱5.齿轮传动电同6.料斗7.螺杆8.加热器9.料筒10.喷嘴11.定模固定板12.模具13.导柱14.动模固定板15.合模机构16.合模油缸17.螺杆传动齿轮18.螺杆花键19.油箱
重点﹕1.料斗干燥﹑储料作用(一般在成型之前要对塑料作干燥)
2.螺杆核心部位﹐起混料﹑碾料﹑产生压力﹑推料等作用
3.喷嘴与模具上的主胶道相连接
二﹑塑料成型种类﹕射出成型﹑压铸成型﹑吸塑成型﹑吹塑成型﹑发泡成型﹑挤压成型等。
三﹑工作循环﹕计量塑化注射充模保压增密制品冷却
开模顶件取件闭模后加料
四﹑1.单色模具注射机分立式﹑卧式﹑角式等。
2.单色多模注射机。
3.多色单模注射机。
4.多色多模的注射机。
立式注射机﹕料斗在上面﹐母模在上﹐公模在下﹐开模时母模上开﹐公模不动。
四﹑注射机装置部分技朮参数﹕
1.公称注射量(g或m3)2.注射压力(Pa)
3.注射速度4.线型时间
5.指压6.螺杆转速
7.注射行程8.喷嘴接力
9.加热功率10.喷嘴温度
11.料筒温度12.喷嘴球半径
13.喷嘴孔直径14.螺杆直径
15.螺杆有效长度16.螺杆长径比
17.螺杆的压缩比
五﹑合模装置部分技朮参数﹕
1.锁模力(合模力)﹐是指注射机的合模机构对模具所能施加的夹紧力
(KN)。
2.合模速度(m/s)动模转动最高速度。
3.开模力(KN)为取出制品﹐模具开启最大力。
4.开模速度(M/S)开模时﹐动模移动速度。
5.顶出力(KN)顶出装置的最大推力。
6.模温控制参数(℃)﹐模具要求恒定的温度值。
7.合模装置的基本尺寸。
第三章塑件
一﹑塑件的基本内容
1.立体空间内容﹐几何结构﹐尺寸及精度。
2.塑件表面的内容﹑标记﹑符号﹑文字﹑表面图案﹑图形﹑粗糙度。
3.静态﹑动态性能﹐机械﹑物理﹑化学等性能。
4.环境﹑人机工程。
5.塑料的选择。
6.成本﹑价格。
7.成型模具及成型方法实现的可行性﹐经济性等。
二﹑几何结构及尺寸精度
1.结构包括内部结构和外部结构的设计。
1-1.形状﹕塑件的形状应尽可能保证有利于成型原则。
1-2.脱模斜度﹕由于塑件冷却后产生收缩﹐会使塑件紧紧包住模具型
芯和型腔中的凸起部分(主要包模仁)﹐为了便于取出塑件﹐防止
脱模时撞伤或擦伤塑件﹐设计塑件时﹐其内外表面沿脱模方向均应具有足够的脱模斜度。
在设计时﹐应注意以下几个方面﹕
a.压缩成型较大的塑件时﹐要求内表面的脱模斜度大于外表面的脱
模斜度。
b.常用脱模斜度值为1°~1.5°﹐也可小到0.5°。
c.对于高度不大的塑件﹐可不取脱模斜度。
1-3.壁厚﹕塑件的壁厚与使用要求及工艺要求有关。
a.在塑模成型上﹐壁厚过小﹐熔融塑料在模具型腔中的流动阴力较
大。
b.壁厚过大﹐会造成用料过多﹐增加成本﹐且会给成型工艺带来困
难。
在塑件上还会产生气泡﹐缩孔﹑凹痕﹑翘曲等﹐影响产品外
观。
c.在成型工艺上还要求塑件各部位的壁厚尽可能均匀。
1-4.加强筋﹕它是塑件中经常会用到的增加塑件强度的办法﹐其优点﹕
a.使塑件壁厚均匀﹐即节约了材料﹐又提高了强度﹐还可避免塑
件中外观缺陷。
b.增加塑件的刚性。
c.沿料流方向的加强筋还能降低塑料的充模阴力。
加强筋的设计要求﹕
a.为了增强塑件的强度及刚性﹐加强筋应设计得矮一些﹐多一些
为好。
b.加强筋之间的中心距应大于两倍的壁厚。
c.对于薄壁塑件﹐也可将其设计成球面或拱曲面形状。
1-5.支承面﹕以塑件的整个底面作为支承面是不合理的。
通常利用的
是边框支承或底脚支承。
1-6.圆角﹕塑件上除了使用上要求必须采用尖角之外﹐其余所有转角
处均应采用圆弧过渡﹐因为尖角处易产生应力集中﹐影响塑件强
度。
采用圆角的优点主要有两方面﹕
a.避免应力集中﹐提高了塑件强度及美观。
b.模具在淬火和使用时不致因应力集中而开裂。
1-7.孔﹕塑件上的孔是用模具的型芯来成型的﹐在设计上应注意以下
几点﹕
a.孔应设置在不易削弱塑件强度的地方。
b.在孔之间及孔与边缘之间均应有足够的距离(一般应大于孔径)。
c.对于盲孔﹐在挤塑或注射成型时﹐其孔深不得大于孔径的4倍。
1-8.合页的设计﹕合页的设计主要有以下几点﹕
b.对于塑件本身壁厚小的中间薄膜处应相薄﹐壁厚大的﹐薄膜处应
厚一些﹐但不得超过0.5mm。
b.合页部分的厚度应均匀一致。
c.成型时﹐塑料必须从塑件本身的边通过中间薄膜流向另一边﹐脱
模后立即折曲几次。
1-9.止转凸凹﹕塑件上设计的止转凸凹一般是为了便用握持和塑件成
型后易于拧出﹐在设计时应当注意﹕凸凹纹方向与脱模方向一致
性及模具便于加工性。
1-10.螺纹﹕
a.塑件上的螺纹可以模塑时直接成型﹐也可在模塑后机械加工成型。
e.模塑的螺纹其外螺纹直径不宜小于4mm﹐内螺纹直径不宜小于
2mm﹐精度不高于3级。
g.为防止塑件上螺孔的最外围螺纹崩裂或变形﹐应使孔始端有一深
度0.2~0.8mm的台阶孔﹐螺纹末端也不宜延伸到与底面相接。
1-11.齿轮﹕
a.齿轮各部分的尺寸有如下的规定﹕
a-1.轮缘宽度最小为齿高的3倍。
a-2.辐板的厚度应等于或小于轮缘厚度。
a-3.轮壳厚度应等于或大于轮缘厚度。
a-4.轮壳外径最小应为轴孔径的1.5~3倍。
a-5.轮壳长度应相当于轴径。
b.在设计齿轮时﹐还应注意﹕
b-1.尽量避免截面的突然变化。
b-2.尽可能加大圆角及圆弧过渡的半径。
b-3.轴与孔尽可能不采用过盈配合﹐可采用过渡配合。
1-12.嵌件﹕
嵌件的用途﹕
a.增加塑件局部的强度﹑硬度﹑耐磨性﹑导电性﹑导磁性。
b.增塑件的尺寸和形状的稳定性﹐提高精度。
c.降低塑料的消耗及满足其它多种要求。
2.嵌件表面形式﹕菱形滚花﹑直纹滚花﹑六边形﹑切口﹑打孔﹑折弯﹑
压偏等。
3.嵌件的设计要`求﹕
3-1.为了防塑件应力开裂﹐嵌件周围的塑料层应有足够的厚度﹐同时
嵌件本身结构不应带有尖角。
3-2.单侧带有嵌件的塑件﹐因两侧收缩不均匀﹐造成很大的内应力﹐
会使塑件产生弯曲或断裂。
3-3.为了防止嵌件受到塑料流动压力产生位移或变形﹐嵌件应牢固固
定在模具内。
3-4.嵌件设计应尽量用不通孔或不通螺孔。
3-5.为了避免鼓胀﹐套筒嵌件不应设置在塑件的表面或边缘附近。
3-6.为了提高嵌件装在模具里的稳定性﹐在条件许可时﹐嵌件上应有
凸缘﹐并便其凹入或凸起1.5~2mm。
3-7.当嵌件自由伸出长度超过嵌件支承的直径2倍时﹐垂直于压塑方
向的嵌件应有支承柱。
3-8.当嵌件为螺杆时﹐光杆部分与模具的配合部分应具有IT9级精度
的间隙配合。
3-9.为了使嵌件与塑件牢固地连接在一起﹐嵌件的表面应具有止动的
部分﹐以防嵌件移动。
塑料模具的基本结构
塑料模具依总体功能结构可分为﹕成型系统﹐浇注系统﹐排气系统﹐冷却系统﹐顶出系统等
一.浇注系统﹕
定义﹕模具中从注射机喷嘴开始到型腔为止的塑料流动信道。
其由主流道﹑分流道﹑浇口及泠料穴组成。
相关的一些中英文对照
CAV.NO第几号模窝RUNNER浇道
GATE浇口CAVITY型腔
(一).主流道﹕
1.定义﹕主流道是指从注射机喷嘴与模具接触的部位起﹐到分流道为止的这一段。
2.设计上的注意事项﹕
(1).主流道的端面形状通常为圆形。
(2).为便于脱模﹐主流道一般制作都带有斜度﹐但如果主流道同时穿过多块板子时﹐一定要注意每一块块子上孔的斜度及孔的大小。
(3).主流道大小的设计要根据塑料材料的流动特性来定
(4).主流道在设计上大多采用圆锥形.(如图标)制作时要注意﹕
A.小端直径D2=D1+(0.5~1mm)
B.小端球半径R2=R1+(1~2mm)
(其中D1﹑R1分别为注射机射出口的直径及注射头的球半径)
3.浇口套
由于主流道要与高温塑料及喷嘴接触和碰撞﹐所以模具的主流道部分通常设计成可拆卸更换的衬套﹐简称浇注套或浇口套
(1).其作用主要为﹕
A.使模具安装时进入定位孔方便而在注塑机上很好地定位与注塑机喷嘴孔吻合﹐并能经受塑料的反压力﹐不致被推出模具
B.作为浇注系统的主流道﹐将料筒内的塑料过渡到模具内﹐保证料流有力畅通地到达型腔﹐在注射过程中不应有塑料溢出﹐同时保证主流道凝料脱出方便。
(2)结构形式有整体式和分体式
整体式﹕即台肩与构成主流道部份做成一体
分体式﹕即台肩与构成主流道部份分开制作
日本的工业标准﹕JIS
中国的工业标准﹕SJB
(二)。
分流道﹕
定义﹕主流道与浇口之间的一段﹐它是熔融塑料由主流道流入型腔的过渡段也是浇注系统中通过断面面积变化及塑料转向的过渡段﹐能使塑料得到平稳的转换。
1.截面设计
A.一般设计截面为圆形
B.从加工方便性来看一般设计为U形﹐V形﹐梯形﹐正六边形
C.分流道的断面形状及尺寸大小﹐应根据塑件的成型体积﹐塑件壁厚﹐塑件形状﹐所用塑料工艺特性﹐注射速率﹐分流道长度等因素来确定。
2.分流道的布置形式有平衡式进料和非平衡式进料两种形式。
平衡式进料就是保证各个进料口同时均衡地进料﹐非平衡式进料就是各个进料口不能同时均衡地进料﹐一般要做模流分析来进行评估。
(三).浇口
1.定义﹕浇口又称进料口或内流道。
它是分流道与塑件之间狭窄的部份﹐也称浇注系统最短小的部份﹔
2.作用﹕能使分流道输送过来的熔融塑料的流速产生加速度﹐形成理想的流态﹐顺序﹐并速速地充满型腔﹐同时还起着封闭型腔防止熔料倒流的作用﹐并在成型后便于使浇口与塑件分离。
3.浇口的形式﹕
内侧浇口
普通侧浇口(边缘浇口)﹕
外侧浇口
扇形浇口﹕常用来成型宽度较大的薄片状塑件
平缝式浇口
护耳式浇口
隙式浇口
一般点浇口
潜伏式浇口(我公司大多采用此种方式)
盘环型浇口
轮辐式浇口
爪形浇口
园环形浇口
3>.浇口位置的选择
(1)浇口选择有阻挡物最近的距离。
(2)浇口的尺寸及位置选择应避免产生喷射和蠕动。
(3)浇口应开设在塑件断面最厚处。
(4)浇口位置的选择应使塑料流程最短﹐料流变向最少。
(5)浇口位置选择应有利于型腔内气体的排出。
(6)浇口位置的选择应减少或避免塑件的熔接痕增加熔接牢度。
(7)浇口位置的选择应防止料流将型腔﹐型蕊﹐嵌件挤压变形。
(四).冷料穴
1.结构﹕冷料穴是用来储臧注射间隔期间产生的冷料头的﹐防止冷料进入型腔而影响塑件质量﹐并使熔料能顺利地充满型腔﹐冷料穴又称冷料井。
2.拉料形式﹕
(1)钩形(工形)拉料杆
(2)球形拉料杆
3.圆锥形拉料杆
4.拉料穴﹕A.带顶杆﹔B.不带顶杆
一般凹模结构设计
一.首先复习一下上节课所讲的内容﹕
1.分模面的确定
从分模面与开模的方向来看﹐有平行于开模方向﹐垂直于开模方向﹐与开模方向成斜角。
2.分模线﹕分模线不要影响产品外观,尽量选择在产品棱边上。
产品的外表面是由母模制作﹐产品的内表面是由公模仁成型制成。
3.cavity数量的确定﹕
3-1.是根据所用注射机的最大注射量确定型腔数量。
(切记算出之数
值不能四舍五入,只能取小)。
3-2.根据注射机的最大锁模力确定型腔数量。
3-3.根据塑件精度确定型腔数量。
3-4.根据经济性确定型腔数。
备注﹕注射机的规格主要是用机器吨位或锁模力﹐另一种是用注射
量确定。
二.一般母模的设计﹕
凹模是成型产品外形的主要部件。
其结构特点﹕随产品的结构和模具的加工方法而变化。
镶拼的组合方式的优点﹕
对于形状复杂的型腔﹐若采用整体式结构﹐比较难加工。
所以采用组合式的凹模结构。
同时可以使母模边缘的材料的性能低于母模的材料﹐避免了整体式凹模采用一样的材料不经济﹐由于凹模的镶拼结构可以通过间隙利于排气﹐减少母模热变形。
对于母模中易磨损的部位采用镶拼式﹐可以方便模具的维修﹐避免整体的母模报废。
镶拼的组合方式的缺点﹕
组合式凹模的刚性不及整体式的易在塑件表面留下痕迹﹐模具结构比较复杂。
(镶拼式的结构可以平衡变形量)。
1.整体式凹模
a.完全整体式母模﹕
它是由整块材料制作而成﹐这种结构比较简单﹐不易变形产品的质量好﹐如果产品塑件比较复杂﹐采用一般的加工方法制造母模型腔就较困难。
所以完全整体式的适合简单的塑件。
b.整体嵌入式母模块﹕
它属于一种完全整体式凹模的演变﹐即将完全整体式凹模变为整体式凹模块直接嵌入到固定板中﹐或先嵌在模框中
模框在嵌到固定板中的形式。
完全整体式凹模整体嵌入式母模块
2.完全整体式凹模块+局部镶拼嵌入﹐是在守全整体式凹模块或整体
嵌入式凹模块的易损坏的部位及难加工的部位﹐如图所示﹕
A.图所示的结构比较简单﹐但结合面要平整﹐否则会有塑料流入使
毛边加厚。
B.图所示的结构﹐采用圆柱形配合﹐塑料不易流入。
3.完全镶拼嵌入式母模块。
上图是一种侧壁和底部大面积的母模结构﹐镶拼凹模块可直接嵌入到固定板中﹐或嵌入到模框﹐模框再嵌入到固定板中。
上图所表示的是底部大面积镶嵌组合式凹模。
成型部分设计
1、分模面的确定
为了将塑件和浇注系统凝料等从密闭的模具内取出,以及为了安放嵌件,将模具适当地分成两个或若干个主要部分,这些可以分离的接触表面,通称为分模面。
分模面的表示方法:
1.模具分开时,2.分模面两边的模板都作移动;
3.模具分开时,4.其中一方模板不5.动,6.另一方模板作移动
A.分模面的数目有:
单分模面、双分模面、多分模面
B.分模面的形状有:
平面、斜面、阶梯面、曲面
C.分模面与D.开模方向关系有:
平行于开模方向、垂直于开模方向、与E.开模方向成一斜角
选择分模面考虑原则:
1.塑件质量考虑,2.
确保塑件尺寸精度
同A.轴度要求的部份应在公模内成型,B.若放在公母模内成型,C.会因合模不D.准确而E.难于保证同F.轴度
G.选择分模面时,H.应考虑减小由于脱模斜度造成塑件大小端尺寸差异,I.若模窝设在公模,J.会因脱模斜度造成塑件大小端尺寸差异太大,K.当塑件不L.允许有较大的脱模斜度时,M.采用这种结构使脱模困难,N.若塑件外观无严格要求,O.可将P.分模选在塑件中部,Q.它可采用较小的脱模斜度有利于脱模
确保塑件表面要求:
分模面尽可能选择在不影响塑件外观的部位以及塑件外观的要求
3.注射机技术规格考虑:
A.锁模力考虑:
尽可能减少塑件在分模面上的投影面积。
当塑件在分型面上的投影面积接近接近于注射机的最大注射面积时,B.有产生溢料的可能,C.模具的分模面尺寸在保证不D.溢料的情况下,E.应尽可能减少分模面接触面积,F.以增加分模面的接触压力,G.防止溢料,H.并简化分模面的加工
I.模板间距考虑:
分模面的确定要保证公母模开模行程最短
4.模具结构考虑
A.尽量简化脱模部件
a.为便于塑件脱模,b.应使塑件在开模时尽可能留在公模,c.只要使塑件与d.公模的结合力大于塑件与e.母模的结合力即可,f.尽可能使塑难看与g.母模之间有一定的结合力,而h.不i.要把塑件与j.模具的结合力都放在公模
k.当塑件的外形简单,l.但内形有较多的孔或复m.杂孔时,n.塑件成型后必然留在模仁上,o.此时模窝可设在母模上,p.开模后可用推板顶出塑件,q.若模窝设在公模上,r.使脱模困难
s.当带有金属嵌件时,t.因为嵌件不u.会收缩包紧模仁,v.所以模窝应设在公模,w.否则开模后塑件留在母模,x.使脱模困难
y.若塑件的模仁对z.称分布时,aa.应迫使塑件留在公模上