轴承座课程设计说明书.docx
《轴承座课程设计说明书.docx》由会员分享,可在线阅读,更多相关《轴承座课程设计说明书.docx(14页珍藏版)》请在冰豆网上搜索。
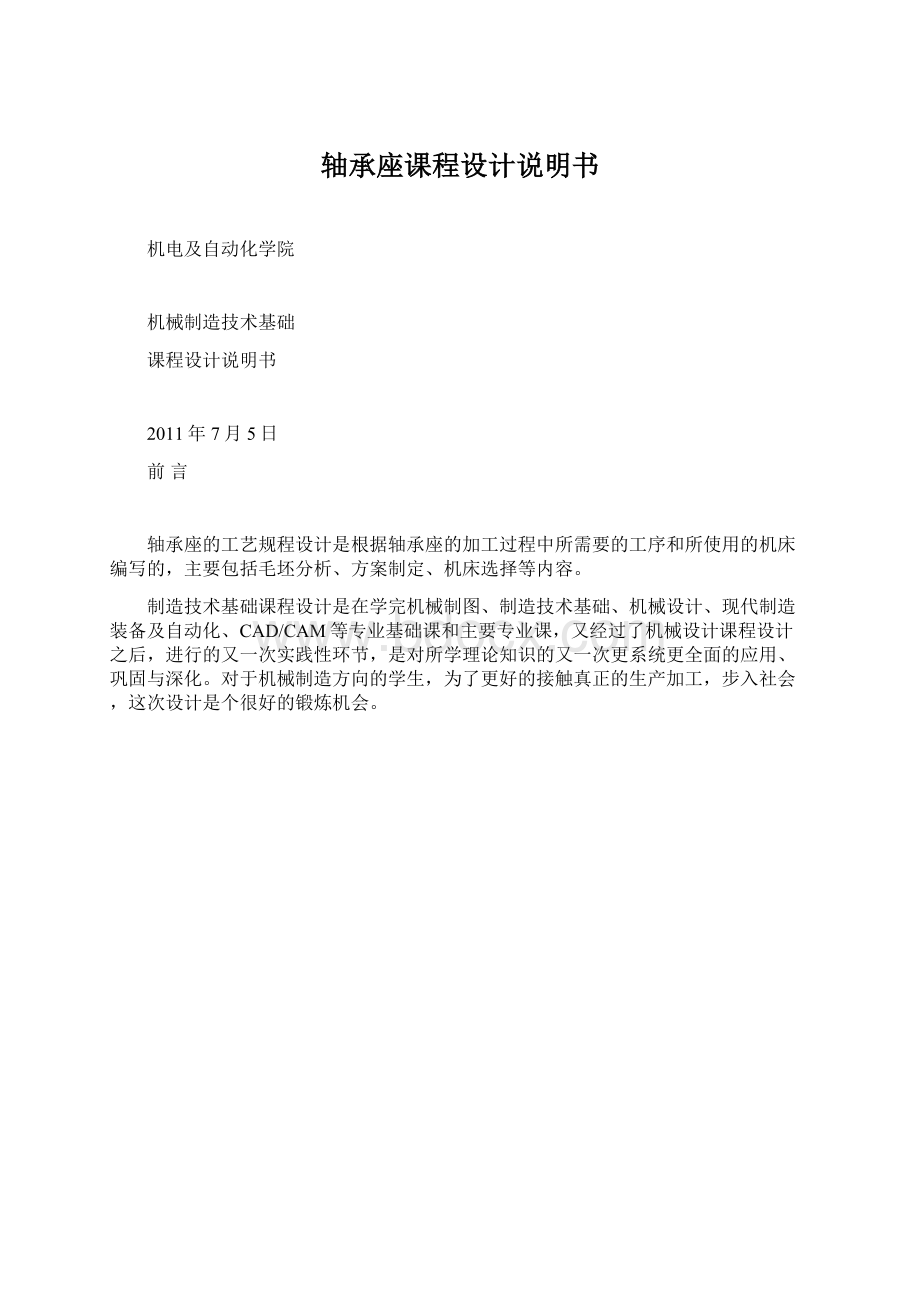
轴承座课程设计说明书
机电及自动化学院
机械制造技术基础
课程设计说明书
2011年7月5日
前言
轴承座的工艺规程设计是根据轴承座的加工过程中所需要的工序和所使用的机床编写的,主要包括毛坯分析、方案制定、机床选择等内容。
制造技术基础课程设计是在学完机械制图、制造技术基础、机械设计、现代制造装备及自动化、CAD/CAM等专业基础课和主要专业课,又经过了机械设计课程设计之后,进行的又一次实践性环节,是对所学理论知识的又一次更系统更全面的应用、巩固与深化。
对于机械制造方向的学生,为了更好的接触真正的生产加工,步入社会,这次设计是个很好的锻炼机会。
1零件的分析
1.1零件的作用
轴承座是用于支撑轴类零件的,孔的目的是为了满足滚动轴承的外圈和轴承孔的配合要求,或者是滑动轴承外圆与轴承孔的配合,两个孔是用于固定轴承座的,单边固定是出于满足结构和安装位置的要求。
1.2零件的工艺分析
⑴φ30孔具有较高的精度要求,表面粗糙度Ra的值为1.6um,是加工的关键表面。
⑵轴承座上、下表面及前、后两端面的表面粗糙度Ra为3.2um,是加工的重要表面。
轴承座的上表面平面度度要求0.008,而且与轴承孔中心线有平行度要求0.003。
轴承座的前、后端面与轴承孔中心线垂直度要求为0.003,是重要的加工表面。
⑶φ8孔,φ13沉孔加工表面粗糙度要求较低。
⑷其余表面要求不高。
加工机床部分采用通用机床,部分采用专用机床;按零件分类,部分布置成流水线,部分布置成机群式;广泛采用专用夹具,可调夹具;按零件产量和精度,部分采用通用刀具和量具,部分采用专用刀具和量具;部分采用划线找正装夹,广泛采用通用或专用夹具装夹;有较详细的工艺规程,用工艺卡管理生产。
2工艺规程设计
2.1、确定轴承座毛坯的制造形式
根据机轴承座材料(HT200)具有铸造性能好,工艺简单,铸造应力小,易加工,需人工时效;有一定的机械强度及良好的减振性,流动性能好、体收缩和线收缩小;综合力学性能低,抗压强度比抗拉强度高约3-4倍;耐热性较好;可承受较大的弯曲应力;同时工件作用为连接,不承受外部应力,且没有动载荷之类的影响。
为提高加工效率,尽量使毛坯和零件图接近,因此选择毛坯的制造形式为铸件形式。
毛坯工艺特征
(1)毛坯采用铸造,精度适中,加工余量相对较大
(2)加工设备采用车床、铣床、钻床
(3)加工设备采用组合夹具
(4)工艺需编制详细的加工工艺过程卡片和工序卡片
(5)生产效率低,对人工的技术要求高
2.2选择精基准
经分析零件图可知,轴承座底面为高度方向基准,轴承座前端面为宽度方向基准。
考虑选择以加工的轴承座底面为精基准,保证底面与φ30孔中心线的距离为30该基准面积较大,工件的装夹稳定可靠,容易操作,夹具结构也比较简单。
2.3选择粗基准
选择不加工的φ30孔外轮廓面为基准,能方便的加工出φ30孔,保证孔中心线与轴承座上端面平行度。
φ30孔外轮廓面的面积较大,无浇口、冒口飞边等缺陷,符合粗基准的要求。
2.4选择加工方法
根据加工表面的精度和表面粗糙要求,查附表可得内孔、平面的加工方案,
表2轴承座各面的加工方案
加工表面
精度要求
表面粗糙度Ra/um
加工方案
底面
IT9
3.2
粗铣→精铣
两上表面
IT9
3.2
粗铣→精铣
四端面
IT9
3.2
粗铣→精铣
轴承孔两侧面
IT14
25
粗铣
两槽
IT14
25
粗刨
φ30孔
IT7
1.6
粗镗→半精镗→精镗
φ35孔
IT14
25
粗镗
φ9、φ13孔
IT8
12.5
钻削
φ8
IT8
12.5
钻削铰削
φ6、φ4孔
IT14
25
钻削
2.5拟定机械加工工艺路线
表2工艺路线的方案之一
工序号
工序名称
工序内容
05
检验
外协毛坯检验
10
铣削
夹轴承孔两侧毛坯,铣轴承底面,照顾尺寸30mm和表面粗糙度
15
铣削
以已加工底面定位基准,在轴承孔处压紧,铣轴承座两上表面
20
铣削
以已加工底面定位基准,铣82mm两侧面
25
铣削
以上下两底面为基准,并夹紧,铣前后两端面
30
铣削
以82mm两侧面为基准,夹紧前后两端面,铣42mm两侧面
35
刨削
把工件旋转一定角度,刨2mm×1mm槽
40
钻削
铰削
钻φ9孔和φ13孔,保证φ13孔深8+0.20mm,同时φ8孔用钻削和铰削保证孔与孔之间尺寸64±0,3和20mm
45
钻削
以上下两平面为基准,夹紧前后两端面,钻φ6孔
50
钻削
以后端面为基准,夹紧两侧面,钻φ4孔,并保证中心线到地面的距离为7mm
55
车削
以底平面和前端面为基准,夹紧两侧面,车φ30和φ35两孔,并保证孔中心线到底平面的距离为30mm,间接保证上底面到φ30孔中心线的距离及其公差值15+0.050mm
60
车削
车1x45倒角
65
去毛刺
70
总见入库
表3工艺路线的方案之二
工序号
工序名称
工序内容
05
检验
外协毛坯检验
10
铣削
夹轴承孔两侧毛坯,铣轴承底面,照顾尺寸30mm和表面粗糙度
15
镗削
夹轴承孔两侧毛坯,以φ30外轮廓面和底面为基准镗φ30
孔保证30mm尺寸
20
铣削
以已加工底面定位基准,在轴承孔处压紧,铣轴承座两上表面保证上表面到φ30孔中心线的距离及其公差值15+0.050mm
25
铣削
以已加工底面定位基准,铣82mm两侧面
30
铣削
以上下两底面为基准,并夹紧,铣前后两端面
35
铣削
以82mm两侧面为基准,夹紧前后两端面,铣42mm两侧面
40
刨削
把工件旋转一定角度,刨2mm×1mm槽
45
钻削
铰削
钻φ9孔和φ13孔,保证φ13孔深8+0.20mm,同时φ8孔用钻削和铰削保证孔与孔之间尺寸64±0,3和20mm
50
钻削
以上下两平面为基准,夹紧前后两端面,钻φ6孔
55
钻削
以后端面为基准,夹紧两侧面,钻φ4孔,并保证中心线到地面的距离为7mm
60
镗削
夹轴承孔两侧毛坯,以底面前后两端面为基准镗φ35孔
65
镗削
镗削1X45内孔倒角
70
去毛刺
75
总见入库
方案比较:
方案一优点:
工序比较集中
缺点:
车削φ30和φ35两孔要用专用夹具,成本较高较麻烦,部分工序安排不合理,加工φ30孔放到最后其他平面形位公差较难定位
方案二优点:
镗削φ30和φ35不要用专用夹具。
缺点:
镗削加工φ30和φ35孔工序分散,效率低。
综合比较后最终选择方案二。
3.加工余量及工序尺寸的确定
结合轴承座尺寸及查阅《机械制造技术基础课程设计指南》,《机械制造工艺学》,《互换性与测量技术基础》《机械加工工艺设计使用手册》等资料得到相关数据可计算得到加工余量、工序尺寸如表4
表4加工余量、工序尺寸(mm)
加工面
粗糙度
Ra
公差
IT
机械加工总
单边余量
各工序尺寸
及工序单边余量
毛坯尺寸
底平面
3.2
8
4
粗铣→313
精铣→301
34
两上平面
3.2
8
3
粗铣→162
精铣→151
18
左右两侧面
3.2
8
3
粗铣→842
精铣→821
88
前后两端面
3.2
8
3
粗铣→402
精铣→381
44
轴承孔两侧面
25
无
2
粗铣→422
46
轴承座槽
25
无
2X1
粗刨→2X12X1
0
φ9孔
12.5
无
4.5
钻→φ94.5
0
φ13孔
12.5
无
2
钻→φ132
φ9
φ8孔
12.5
8
4
钻→φ7.83.9
铰→φ80.1
0
φ6孔
25
无
3
钻→φ63
0
φ4孔
25
无
2
钻→φ42
0
φ30孔
1.6
7
3
粗镗→φ271.5
半精镗→φ291
精镗→φ300.5
φ24
φ35孔
25
无
2.5
粗镗→φ352.5
φ30
4.毛坯尺寸的确定及毛坯图
根据各工序加工余量及零件尺寸可得毛坯图如下:
5确定切削用量
据工件尺寸和相关要求,并参考《实用机械加工工艺手册》等资料,可得工件尺寸和切屑深度的选择为:
粗铣每齿进给量为0.16mm,半精铣每转进给量为1.0mm,精铣每转进给量为0.5mm;
钻孔进给量:
Φ4进给量为0.3mm/r;Φ6进给量为0.3mm/r;Φ9进给量为0.5mm/r;Φ8进给量为0.5mm/r;Φ13进给量为0.7mm/r
Φ8铰孔进给量为0.25mm/r
粗镗Φ30Φ35为0.5mm/r;半精镗Φ30进给量为0.2mm/r,精镗Φ30进给量为0.15mm/r
6、重要加工面基本工时的确定
(1)工序10:
粗铣,精铣下底面
切屑深度分别为:
3.0mm
1.0mm
铣平面参数:
每齿进给量为af=0.16mm/z,采用W18Cr4V硬质合金钢端铣刀,牌号YG6,齿数为Z=10,直径D=100mm,刀具寿命180min,
则每转进给量为:
f=af
Z=1.6mm/r
=0.5mm/r
切屑速度分别为:
V1=1.0m/s,
V2=1.3m/s
转速:
n
r/min
代人相关数据可得:
191.08r/min
248.40r/min
根据机床型号,选择转速
160r/min
210r/min
基本时间tj=(L+la+lb)i/nf
其中la=lb=D/2
代人相关数据得:
tj1=0.32min
tj2=0.75min
(2)工序15:
粗镗半精镗精镗Φ30孔
切屑深度为
=1.5mm,
=1mm,
=0.5mm
进给量分别为:
f1=0.5mm/r,f2=0.2mm/r,f3=0.15mm/r
切屑速度
V1=V2=40m/minV3=30m/min
转速:
n
r/min
代人相关数据可得:
424.63r/min
424.63/min
318.47r/min
根据机床型号,选择转速
410r/min
410r/min
300r/min
基本时间
i
代人相关数据得:
tj1=0.38min
ti2=1.03min
tj3=2.09min
(3)工序20:
粗铣,精铣两上表面
切屑深度分别为:
2.0mm
1.0mm
铣平面参数:
每齿进给量为af=0.16mm/z,采用W18Cr4V硬质合金钢端铣刀,牌号YG6,齿数为Z=10,直径D=100mm,刀具寿命180min,
则每转进给量为:
f=af
Z=1.6mm/r
=0.5mm/r
切屑速度分别为:
V1=1.0m/s,
V2=1.3m/s
转速:
n
r/min
代人相关数据可得:
191.08r/min
248.40r/min
根据机床型号,选择转速
160r/min
210r/min
基本时间tj=(L+la+lb)i/nf
其中la=lb=D/2
代人相关数据得:
tj1=0.16min
tj2=0.37min
(4)工序35:
粗铣,精铣前后两端面
切屑深度分别为:
2.0mm
1.0mm
铣平面参数:
每齿进给量为af=0.16mm/z,采用W18Cr4V硬质合金钢端铣刀,牌号YG6,齿数为Z=10,直径D=100mm,刀具寿命180min,
则每转进给量为:
f=af
Z=1.6mm/r
=0.5mm/r
切屑速度分别为:
V1=1.0m/s,
V2=1.3m/s
转速:
n
r/min
代人相关数据可得:
191.08r/min
248.40r/min
根据机床型号,选择转速
160r/min
210r/min
基本时间tj=(L+la+lb)i/nf
其中la=lb=D/2
代人相关数据得:
tj1=0.32min
tj2=0.75min
(5)工序60:
粗镗Φ35孔
切屑深度为
=2.5mm
进给量分别为:
f=0.5mm/r
切屑速度
V=40m/min
转速:
n
r/min
代人相关数据可得:
n=363.96r/min
根据机床型号,选择转速n=340r/min
基本时间
i
代人相关数据得:
tj=0.64min
7设计总结
经过一周的设计,轴承座的设计已经完成。
这次设计不但巩固了也学知识,也是对个人能力训练。
课程设计是锻炼个人能力的最好方法,对于安排给自己的任务必须独自完成,有问题就和老师同学讨论,设计中不但要考虑方法,也要考虑设计后用于实践的成本,以及适用性,因此设计也要和实际相联系,源于实践,处于理论,用于实践。
最后,感谢老师和同学在这次设计中的帮助。
参考文献
【1】王富山,陈抗生主编,机械制造基础课程设计,机械工业出版社,2002。
【2】王韶俊主编,机械制造工艺设计手册,哈尔滨工业大学出版社,1981。
【3】孟少农主编,机械加工工艺手册第1卷,机械工业出版社,1991。
【4】孟少农主编,机械加工工艺手册第2卷,机械工业出版社,1991。
【5】李军主编,互换性与测量技术,华中科技大学出版社,2007。
【6】王先逵主编,机械制造工艺学,机械工业出版社,2006。