《汽车机械基础》实习实验指导书要点.docx
《《汽车机械基础》实习实验指导书要点.docx》由会员分享,可在线阅读,更多相关《《汽车机械基础》实习实验指导书要点.docx(21页珍藏版)》请在冰豆网上搜索。
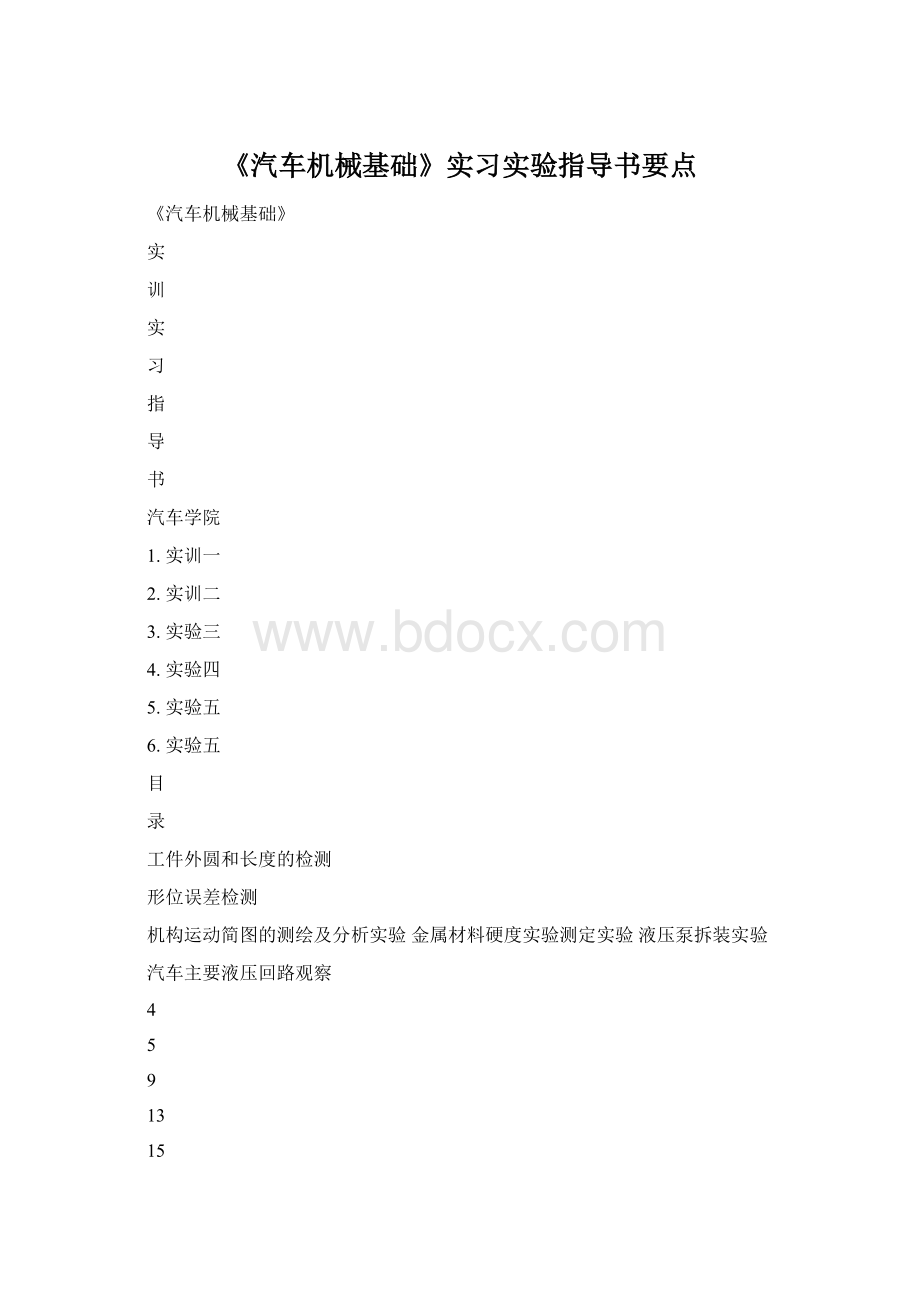
《汽车机械基础》实习实验指导书要点
《汽车机械基础》
实
训
实
习
指
导
书
汽车学院
1.实训一
2.实训二
3.实验三
4.实验四
5.实验五
6.实验五
目
录
工件外圆和长度的检测
形位误差检测
机构运动简图的测绘及分析实验金属材料硬度实验测定实验液压泵拆装实验
汽车主要液压回路观察
4
5
9
13
15
16
7.学生实验(训)报告
18
说明
1.本手册适用于课程设置的实践实训教学环节。
2.凡进入实习(训)教学阶段的学生均按实习(训)教学大纲和实习(训)计划的要求,在实习(训)过程中认真做好实习(训)情况记录,完成实习(训)报告(设计)等工作任务。
3.认真填写各项内容记录,若某项内容的纸张不够填写可另附纸张。
实习(训)结束后,应将本手册提交指导教师审阅。
4.各专业的实习(训)要求不尽相同,若手册中的实习(训)报告格式不适应用于专业实习(训)报告(设计)的要求,可另行确定报告(设计)的格式。
5.学生实习(训)记录、实习(训)报告等材料是实习(训)教学的重要资料,将作为教师指导实习(训)工作检查和考核的依据,请各教学单位注意收集保存。
实训一
工件外圆和长度的检测
一、实验目的
1、熟悉游标卡尺、深度游标卡尺和外径千分尺的使用方法
2、了解游标类、微分类量具的种类
二、实验设备及工具
游标卡尺、深度游标卡尺、外径千分尺、被测工件
合理选用量具:
根据图纸的标注,被测工件尺寸公差≥0.05mm,用游标类量具检测,游标卡尺的分度值为
0.02mm、0.05mm等,测量范围一般为0-150mm、0-200mm、0-300mm、0-500mm、0-1000mm、0-2000mm及0-3000mm。
反之用千分尺测量,千分尺的分度值为0.01mm,规格有0-25mm、25-50mm、50-75mm直至600-700mm。
二、实验内容
1、校对游标卡尺、千分尺的零位。
若零位不能对正时,记下此时得代数值,将零件的各测量数据减去该代数值。
2、用游标卡尺测量标准量块,根据标准量块值熟悉掌握游标尺卡脚和工件接触的松紧程度。
3、根据附图三零件的图纸标注要求,选择合适的计量器具。
4、如果测量外圆,应在圆柱体不同截面、不同方向测量3—5点,记下读数;若测量长度,可沿圆周位置测量几点,记录读数。
5、测量外圆时,可用不同分度值的计量器具测量,对结果进行比较,判断测量的准确性。
6、将这些数据取平均值并和图纸要求比较,判断其合格性。
作出实训报告。
4
实训二
形位误差检测
一、实训目的
掌握平行度、垂直度、跳动、同轴度、平面度的测量方法
二、实训器具
大平板、水平仪、V型铁、偏摆仪、百分表(千分表)、磁性表座、厚薄规、被测工件等
三、测量说明及方法
要合理选用百分表和千分表,若公差值≥0.01mm,选用百分表测量,若被测工件的形位公差值<0.01mm,则用千分表检测。
1、平行度误差测量:
平行度误差常用的方法有打表法和水平仪法。
这些方法是采用与理想要素比较的检测原则。
2、垂直度误差测量:
常用垂直度测量方法有光隙法(透光法)、打表法、水平仪法、闭合测量法等。
本次以光隙法测量垂直度,用光隙法测量简单快捷,也能保证一定的测量精度。
3、测量同轴度误差时,可用通用测量器具检测,常用的方法有芯轴打表法、双向打表法、壁厚差法,光轴法、径向圆跳动替代法。
本次测量是以径向圆跳动替代法测量。
4、跳动误差是被测表面基准轴线回转时,测头与被测面作法向接触的指示表上最大值与最小值的差值。
5、测量平面度的具体方法和测直线度的方法基本相同,主要用间隙法、打表法、光轴法和干涉法。
本次实训主要以打表法测量平面度误差。
四.实训步骤
1、平行度误差测量:
①测量前,擦净平板2和零件1,然后按图一将被测零件1的基准面放
在平板2上,并使被测零件(附图一或附图三)的基准面和平板工作面贴合,(最薄的厚薄规不能塞入两面之间)。
这样,平板的工作面既是被测零件的模拟基准,又是测量基准,两者重合。
图一
图二
2将百分表装入磁性表座3,把百分表测量头放在被测平面上,预压百分表0.3---0.5mm。
并将指示表指针调至零。
3移动表座3,沿被测平面多个方向移动,此时,被测平面对基准的不平行度由百分表(千分表)直接读出,同时记录所有读数。
4将所有读数中的最大值和最小值之差即为平行度误差。
5作出实训报告。
2、垂直度误差测量:
①按图二所示,将被测件(附图一)的基准平面和检验角尺放在检验平
板上,并用塞尺(厚薄规)检查是否接触良好。
5
②移动检验角尺,对着被测表面轻轻接触,观察光隙部位的光隙大小,
用厚薄规检查最大光隙值。
也可以估计出最大光隙值。
③作出实训报告。
3、同轴度误差测量:
①根据附图二(或三)中的同轴度要求,用3#莫氏塞规,插入被测件的
锥孔中(或直接将基准放在V型铁上),利用两端中心孔将其装在偏摆仪上,擦净顶尖和中心孔,锁紧偏摆仪的紧定螺钉。
此时被测件不能轴向窜动但能转动自如。
②将百分表或杠杆百分表装在磁性表座上,把指示表的测量头轻轻放在
零件的被测面上,并压表0.2--0.4mm,然后将指示表指针调到零。
3转动被测件,同轴度误差从指示表中反映出,记录指针摆动的范围。
4将指示表放在不同的被测位置,重复步骤③,记录所有的读数。
读数
中的最大值(忽略了被测要素的圆度误差)即同轴度误差。
⑤作出实训报告。
注:
测量时,测量头要和回转轴线垂直
4、跳动误差测量:
①根据附图四,将被测件安装在偏摆仪上。
安装完后,被测件不能轴向
窜动,但能转动自如。
②将装有百分表或杠杆百分表的表座移到被测件φ65+0.021+0.002尺寸的表面
(两处),将指示表预压0.2—0.3mm,然后将指示表的指针调到零,轻轻转动被测件,从指示表中读出数据并记录,数据中最大值和最小值之差即为跳动误差。
③将被测件从偏摆仪上取下,以上述测量的部位为基准,放在V型铁上
(见图三),重复2)步骤。
④作出实训报告
5、平面度误差测量:
①如图四所示,将被测件放在检验平板上,用对角线法,调节被测平面
下的螺母,将被测件平面两对角线的对角点分别调平(即指示表示值相同);也可以用三远点法,即选择平面上三个较远的点,调平这三点,即三点指示表读数相同。
②然后在被测面按图五的布点形式进行测量,测量平板时,四周的布点
应离平板边缘10mm,并记录数据。
③数据处理:
a:
方法有两大步骤,首先按不同的测量方法,将测得数据
图三
图四
换算成各点相对检验平板的高度值;然后根据最小条件准则确定评定基准平面,计算出平面度误差值。
6
0
+34
+4
+8
+8
+33
+19
+14
+8
a1
b1
c1
a2
b2
c2
a3
b3
c3
0
-5
-10
+4
+20
-3
+6
-9
+8
0
-5+Q
-10+2Q
+4+P
+20+P+Q
-3+P+2Q
+6+2P
-9+2P+Q
+8+2P+2Q
被测平面
图五
0P2P…nP
QP+Q2P+Q…nP+Q2QP+2Q2P+2Q…nP+2Q
..
..
..
..
..
..
.
.
.
nQP+nQ2P+nQ…nP+nQ
图六
b.测量所得数据是相对测量基准而言的,为了评定平面度的误差值,还需要进行坐标变换,将测得值转换为评定方法相应得评定基准得坐标值。
其平面坐标值可按图六所示规律变换,不影响实际被测平面真实情况。
c.根据判断准则列方程,求出P、Q值。
举例说明:
图七为一平面相对检验平板的坐标值按上述方法评定平面度误差
图七
解1:
三点法
任取三点+4,-9,-10按图六的规律列出三点等值方程:
+4+P=-9+2P+Q
-10+2Q=+4+P
由上式解出P=+4,Q=+9,按图六规律和P、Q值转换被测平面的
坐标值,得到如图七所示
→
图八
所以,平面度误差=(+34)-0=34μm
解2:
对角线法按图六规律列出两等值对角点的等值方程:
0=+8+2P+2Q
+6+2P=-10+2Q
7
+16
-19
0
-3
-6
+2
-5
-6
0
解得P=-6,Q=+2。
按图六规律和P、Q值转换被测平面的坐标值得到图九所示形式0+4+P+6+2P
-5+Q+20+P+Q-9+2P+Q
-10+2Q-3+P+2Q+8+2P+Q
→
图九
其平面度误差=(+16)-(-19)=35μm
d.按上述的一种方法求出被测平面的平面度误差。
注:
用三点法求平面度误差,因为人为因素太大(因三点任选),一般不采用。
④作出实训报告
8
实训三机构运动简图的测绘及分析实验
一、实验目的
1、熟悉机构运动简图的绘制方法,掌握从实际机构中测绘机构运动简图的技能;2、巩固机构结构分析原理及自由度计算方法;
3、加深理解平面四杆机构的演化过程及验证曲柄存在条件。
二、实验设备及工具
1、测绘用各种机构实物模型;
2、测量用尺、分规、铅笔及草稿纸。
三、实验原理
1、机构运动简图的常用符号
如图1至图4所示(详见《机械制图》GB4460—84“机构运动简图符号”)。
(1)转动副,如图1所示。
(a)全为活动构件时
(b)构件1为机架时
图1
(2)移动副,如图2所示。
转动副
(a)全为活动构件时
(b)构件1为机架时
图2
(3)高副,如图3所示。
移动副
(a)全为活动构件时
(b)构件1为机架时
图3
(4)构件图例,如图4所示
高副
9
(a)具有两个运动副元素时
(b)具有三个运动副元素时
(c)具有四个运动副元素时
图4构件图例
2、实验原理
机构各部分的运动,是由其原动件的运动规律、该机构中各运动副的类型(高副、低副,转动副、移动副等)和机构的运动尺寸来决定的,而与构件的外形、断面尺寸、组成构件的零件数目及固联方式等无关。
所以,只要根据机构的运动尺寸,按一定的比例尺定出各运动副的位置,就可以用运动副的代表符号和简单的线条把机构的运动简图作出来。
正确的机构运动简图中各构件的尺寸、运动副的类型和相对位置以及机构组成形式应与原机构保持一致,从而保证机构运动简图与原机构具有完全相同的运动特性,以便根据该图对机构进行运动及动力分析。
所谓机构运动简图就是从运动的观点出发,用规定的符号和简单的线条按一定的尺寸比例来表示实际机构的组成及各构件间相对运动关系。
3、绘制机构运动简图的方法及步骤
(1)分析机构的实际构造和运动情况
任选原动件并缓慢转动,根据各构件之间有无相对运动,分清机构是由哪些构件组成的;按照机构运动的传递顺序,仔细观察各构件之间相对运动的性质,从而确定运动副的类型和数目。
(2)合理选择投影面和原动件位置,作机构示意图
选择恰当的投影面,一般选择与大多数构件的运动平面相平行的平面为视图平面;合理选择原动件的一个位置,以便简单清楚地将机构的运动情况正确地表达出来。
撇开各构件的具体结构形状,找出每个构件上的所有运动副,用简单的线条联接该构件上的所有运动副元素来表示每一个构件。
即用简单的线条和规定符号来代表构件和运动副,从而在所选投影面上作出机构的示意图。
(3)计算机构的自由度并检验机构示意图是否正确
a、机构自由度计算公式:
F=3n-2P式中:
n——机构活动构件数
L-P
H
P
H
——平面低副个数
P
L——平面高副个数
b、核对计算结果
机构具有确定运动的条件为:
机构的自由度大于零且等于原动件数。
因本实验中各机构模型均具有确定的运动,故各机构计算自由度应与其原动件数相同:
否则说明所作示意图有误,应对机构重新进行分析、作示意图。
注意:
转动副和移动副虽同为低副,但因其运动性质不同,在作示意图时一定不能混淆互换。
可单单通过自由度计算,又不能发现转动副与移动副相混淆的错误情况,故应将所作图中的各运动副类型与原机构进行逐一核对检查。
(4)量取运动尺寸
运动尺寸是指与机构运动有关的、能确定各运动副相对位置的尺寸。
在原机构上量取机构的运动尺寸,并将这些尺寸标注在机构示意图上。
(5)绘制机构运动简图
选取适当的长度比例尺,依照机构示意图,按一定顺序进行绘图,并将比例尺标注在图上,即为机构运动简图。
10
1
长度比例尺的意义如下:
l
实际长度(m)图示长度(mm)
例如:
某构件的长度LAB
=1m,绘在图上的长度AB=1000mm,则长度比例尺为:
l
LAB
AB
0.0011000
m
mm
(6)标注比例尺和运动尺寸,画斜线表示机架,在原动件上画箭头表示运动方向。
四、例题:
绘制出偏心轮机构的运动简图,并计算其自由度。
图5(a)
图5(b)
1、选择手柄作为原动件并缓慢转动,根据各构件之间有无相对运动,分清机构是由哪些构件组成的。
在图5(a)中,机构由1—机架,2—手柄(即曲柄,本例中取为原动件),3—连杆,4—滑块(即从动件)组成。
2、从原动件开始,按照机构运动的传递顺序,仔细观察各构件之间相对运动的性质,确定运动副的类型和数目。
在图5(a)中,曲柄2为原动件,则运动传递顺序为:
曲柄2,连杆3,滑块4。
回转件的回转中心是相对回转表面的几何中心,而构件2可以绕构件1的偏心轴A作相对转动,故构件3与构件2在B点处也组成转动副;构件4与构件3在C点处又组成转动副;构件4沿X-X方向在构件1上作相对直线运动,组成移动副。
3、合理选择原动件的一个位置,以便简单清楚地将机构的运动情况正确地表达出来,如图5(b)所示,用规定的符号和简单的线条画出机构的示意图。
4、计算机构自由度
(1)机构自由度计算公式:
F=3n-2PL-PH
本例所作示意图中,n=3,PL=4,PH=0,代入上式得:
F=3n-2P
L-P
H
=3×3-2×4-0=1
(2)核对计算结果
观察各构件的运动可知该机构的运动是确定的,则机构的自由度应大于零且等于原动件数,由计算得:
F=1=原动件数,从而验证以上所作机构示意图的正确性。
5、量取运动尺寸
在构件2、3上分别量取两相临转动副中心之间的距离LAB距离,并将所量尺寸标注在机构示意图上。
6、作图(略)
五、实验内容
、LBC
;量取转动副A到滑块运动轨迹X-X之间的
1、据上述原理对选择2~3种机构进行机构运动简图测绘,并说明是何种机构,并计算机构的自由度。
2、并可任意选择一种机构验证曲柄存在的条件。
六、实验报告
实验名称:
机构运动简图的测绘与分析
班级
姓名
实验日期
一、按比例绘制机构运动简图机构名称:
比例尺:
11
机构运动简图:
机构自由度计算:
F=
七、思考题:
1、机构运动简图应包括哪些内容?
2、原动件选取不同、原动件位置不同对绘制机构运动简图有什么影响?
3、在绘制机构运动简图时,应标注哪些尺寸?
12
2
实训四金属材料硬度实验测定实验
一、实验目的
1、了解硬度测定的基本原理及常用硬度试验法的应用范围。
2、学会正确使用硬度计。
二、实验说明
1、概述
硬度是指材料抵抗另一较硬的物体压入表面抵抗塑性变形的一种能力,是重要的力学性能指标之一。
与其它力学性能相比,硬度实验简单易行,又无损于工件,因此在工业生产中被广泛应用。
常用的硬度试验方法有:
布氏硬度试验――主要用于黑色、有色金属原材料检验,也可用于退火、正火钢铁零件的硬度测定。
洛氏硬度试验——主要用于金属材料热处理后产品性能检验。
维氏硬度试验——用于薄板材或金属表层的硬度测定,以及较精确的硬度测定。
显微硬度试验——主要用于测定金属材料的显微组织组分或相组分的硬度。
2、布氏硬度试硷
(1)原理用载荷P把直径为D的淬火钢球压人试件表面,并保持一定时间,而后卸除载荷,测量钢球在试样表面上所压出的压痕直径d,从而计算出压痕球面积A,然后再计
算出单位面积所受的力(P/A值),用此数字表示试件的硬度值,即为布氏硬度,用符号HB表示。
布氏硬度试验原理如图1
所示。
设压痕深度为h,则压痕的球面积为
A=πDh=πD
试中P——施加的载荷,kg;
D——压头(钢球)直径mm;
A——压痕面积,mm;
d——压痕直径,mm。
3、洛氏硬度试验
(1)原理:
洛氏硬度试验是用特殊的压头(金刚石压头或钢球压头)在先后施加的两个载荷(预载荷和总载荷)的作用下压入金属表面来进行的。
总载荷P为预载荷P0和主要载荷P1之和,即
P=P
0
+P
1
洛氏硬度值是施加总载荷P并卸除主载荷P
1
引起的残余压入深度e来计算(图2)。
图中h
0
表示在预载荷
P
0
作用下,压头压入被试材料的深度;h
1
表示施加总载荷P并卸除主载荷P
1
,但仍保留预载荷P
0
时,压头压入
被试材料的深度。
深度差e=h
1
+h
0
,该值用来表示被测材料硬度的高低。
在实际应用中,为了使硬材料测出的硬度值比软材
料的硬度值高,并符合一般的习惯,将被测材料的硬度值用公式加以适当变换,即
HR=K-(h1-h0)/C
试中K――常数,其值在采用金刚石压头时为0.2,采用钢球压头时为0.26;
C——常数,代表指示器读数盘每一刻度相当于压头压入被测材料的深度,其值为0.002mm;
HR——标注洛氏硬度的符号,当采用金刚石压头及150kg的总载荷时应标注HRC,当采用钢球压头及100kg,总载荷试验时,则应标注HRB。
HR值为一无名数,测量时可直接由硬度计表盘读出,表盘上有红﹑黑两种刻度,红线刻度的30和黑线刻度的0相重合,如图13.4所示。
三、实验内容及方法指导
1、布氏硬度试验测定。
2、洛氏硬度试验测定。
3、试验方法指导。
学生分成若干组,利用备好的硬度试块或试样,在硬度计上测定其相应硬度值,使之学
13
会硬度计的使用方法。
四、实验所用设备及材料
1)布氏硬度计
2)读数放大镜
3)洛氏硬度计
4)硬度试块若干
5)铁碳合金退火试样若干(ф20×10mm的工业纯铁,20,45,60,T8,T12等)。
6)ф20×10mm的20,45,60,T8,T12钢退火态,正火态,淬火及回火态的试样。
五、实验注意事项
1)试样两端要平行,表面要平整,若有油污或氧化皮,可用砂纸打磨,以免影响测定。
2)圆柱形试样应放在带有“V”形槽的工作台上操作,以防试样滚动。
3)加载时应细心操作,以免损坏压头。
4)测完硬度值,卸掉载荷后,必须使压头完全离开试样后再取下试样。
5)金刚钻压头系贵重物品,资硬而脆,使用时要小心谨慎,严禁与试样或其它物件碰撞。
6)应根据硬度实验机的使用范围,按规定合理选用不同的载荷和压头,超过使用范围,将不能获得准确的硬度值。
六、实验报告要求
1)简述布氏和洛氏硬度试验原理。
2)测定碳钢(20﹑45﹑60﹑T8﹑T12)退火试样的布氏硬度值(HBS)。
3)测定碳钢(45﹑T8﹑T12)正火及淬火试样的洛氏硬度值(HRC)。
4)测定45钢调质试样的洛氏硬度值(HRC)。
14
0
实训五、液压泵拆装实验
1、实验目的:
了解常用液压泵的结构特点
2、实验要求:
通过对液压泵的拆装,加深对液压泵结构特点和工作原理的认识。
3、实验内容:
(一)、齿轮泵拆装分析
1.齿轮泵型号:
CB-B型齿轮泵
2.拆卸步骤:
1)松开6个紧固螺钉2,分开端盖1和5;从泵体4中取出主动齿轮及轴、从动齿轮及轴;
2)分解端盖与轴承、齿轮与轴、端盖与油封。
此步可不做。
装配顺序与拆卸相反。
3.主要零件分析
1)泵体4泵体的两端面开有封油槽d,此槽与吸油口相通,用来防止泵内油液从泵体与泵盖接合面外泄,泵体与齿顶圆的径向间隙为0.13~0.16mm。
2)端盖1与5前后端盖内侧开有卸荷槽e(见图中虚线所示),用来消除困油。
端盖1上吸油口大,压油口小,用来减小作用在轴和轴承上的径向不平衡力。
3)齿轮3两个齿轮的齿数和模数都相等,齿轮与端盖间轴向间隙为0.03~0.04mm,轴向间隙不可以调节。
4.思考题
1)齿轮泵的密封容积怎样形成的?
2)该齿轮泵有无配流装置?
它是如何完成吸、压油分配的?
3)该齿轮泵中存在几种可能产生泄漏的途径?
为了减小泄漏,该泵采取了什么措施?
4)该齿轮泵采取什么措施来减小泵轴上的径向不平衡力的?
5)该齿轮泵如何消除困油现象的?
(二)、限压式变量叶片泵拆装分析
1.叶片泵型号:
YBX型变量叶片泵
2.拆卸步骤:
1)松开固定螺钉,拆下弹簧压盖,取出弹簧4及弹簧座5;
2)松开固定螺钉,拆下活塞压盖,取出活塞11;
3)松开固定螺钉,拆下滑块压盖,取出滑块8及滚针9;
4)松开固定螺钉,拆下传动轴左右端盖,取出左配流盘、定子、转子传动轴组件和右配流盘;
5)分解以上各部件。
拆卸后清洗、检验、分析,装配与拆卸顺序相反。
3.主要零件分析
1)定子和转子定子的内表面和转子的外表面是圆柱面。
转子中心固定,定子中心可以左右移动。
定子径向开有13条槽可以安置叶片。
2)叶片该泵共有13个叶片,流量脉动较偶数小。
叶片后倾角为24,有利于叶片在惯性力的作用下向外伸出。
3)配流盘图实验1-3所示,配流盘上有四个圆弧槽,其中a为压油窗口,c为吸油窗口,b和d是通叶片底部的油槽。
a与b接通,c与d接通。
这样可以保证,压油腔一侧的叶片底部油槽和压油腔相通,吸油腔一侧的叶片底部油槽与吸油腔相通,保持叶片的底部和顶部所受的液压力是平衡的。
4)滑块滑块8用来支持定子,并承受压力油对定子的作用力。
5)压力调节装置压力调节装置由调压弹簧4、调压螺钉3和弹簧座5组成。
调节弹簧的预压缩量,可以改变泵的限定压力。
6)最大流量调节装置调节螺钉10可以改变活塞11的原始位置,也改变了定子与转子的原始偏心量,从而改变泵的最大流量。
15
7)压力反馈装置泵的出口压力作用在活塞上,活塞对定子产生反馈力。
4.思考题
1)单作用叶片泵密封空间由哪些零件组成?
共有几个?
2)单作用叶片泵和双作用叶片泵在结构上有什么区别?
3)限压式变量泵配流盘上开有几个槽孔?
各有什么用处?
4)应操纵何种装置来调节限压式变量泵的最大流量和限定压力?
(三)、柱塞泵拆装分析
1.柱塞泵型号:
SCY14-1B型手动变量轴向柱塞泵
2.拆装步骤
1)松开固定螺钉,分开左端手动变量机构、中间泵体和右端泵盖三部件;
2)分解各部件;
3)清洗