自学考试机械制造及自动化精密与特种加工考纲.docx
《自学考试机械制造及自动化精密与特种加工考纲.docx》由会员分享,可在线阅读,更多相关《自学考试机械制造及自动化精密与特种加工考纲.docx(35页珍藏版)》请在冰豆网上搜索。
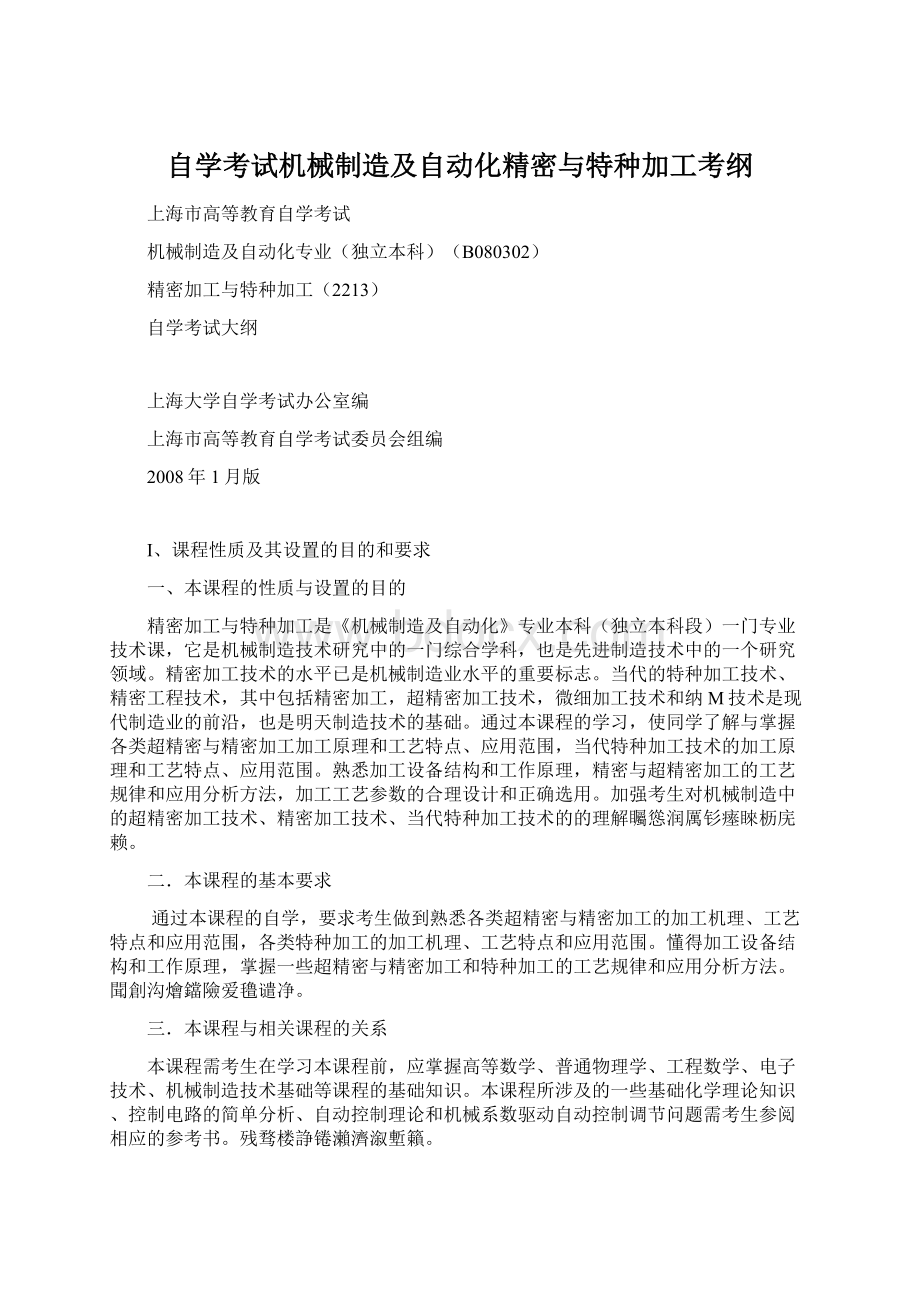
自学考试机械制造及自动化精密与特种加工考纲
上海市高等教育自学考试
机械制造及自动化专业(独立本科)(B080302)
精密加工与特种加工(2213)
自学考试大纲
上海大学自学考试办公室编
上海市高等教育自学考试委员会组编
2008年1月版
Ⅰ、课程性质及其设置的目的和要求
一、本课程的性质与设置的目的
精密加工与特种加工是《机械制造及自动化》专业本科(独立本科段)一门专业技术课,它是机械制造技术研究中的一门综合学科,也是先进制造技术中的一个研究领域。
精密加工技术的水平已是机械制造业水平的重要标志。
当代的特种加工技术、精密工程技术,其中包括精密加工,超精密加工技术,微细加工技术和纳M技术是现代制造业的前沿,也是明天制造技术的基础。
通过本课程的学习,使同学了解与掌握各类超精密与精密加工加工原理和工艺特点、应用范围,当代特种加工技术的加工原理和工艺特点、应用范围。
熟悉加工设备结构和工作原理,精密与超精密加工的工艺规律和应用分析方法,加工工艺参数的合理设计和正确选用。
加强考生对机械制造中的超精密加工技术、精密加工技术、当代特种加工技术的的理解矚慫润厲钐瘗睞枥庑赖。
二.本课程的基本要求
通过本课程的自学,要求考生做到熟悉各类超精密与精密加工的加工机理、工艺特点和应用范围,各类特种加工的加工机理、工艺特点和应用范围。
懂得加工设备结构和工作原理,掌握一些超精密与精密加工和特种加工的工艺规律和应用分析方法。
聞創沟燴鐺險爱氇谴净。
三.本课程与相关课程的关系
本课程需考生在学习本课程前,应掌握高等数学、普通物理学、工程数学、电子技术、机械制造技术基础等课程的基础知识。
本课程所涉及的一些基础化学理论知识、控制电路的简单分析、自动控制理论和机械系数驱动自动控制调节问题需考生参阅相应的参考书。
残骛楼諍锩瀨濟溆塹籟。
Ⅱ、课程内容与考核目标
第一篇精密与超精密加工技术
第一章精密和超精密加工技术及其发展展望
一、学习目的与要求
通过本章节学习,要求同学了解精密和超精密加工技术的产生及发展过程,特点和发展趋势
二、课程内容
第一节发展精密和超精密加工技术的重要性
第二节超精密加工技术的现状
(一)超精密加工技术的新发展
(二)超精密切削的机床设备
(三)金刚石刀具和超精密切削机理的研究
(四)检测和误差补偿
(五)超稳定的加工环境条件
第三节越精密加工技术发展展望
三、考核知识点
(一)精密和超精密加工技术现状与发展研究方向
(二)精密和超精密加工研究领域
四、考核要求
(一)识记
1、精密和超精密加工加工技术现状
2、精密和超精密加工发展研究方向
3、精密和超精密加工研究领域
第一章超精密切削与金刚石刀具
一、学习目的与要求
通过本章节学习,要求同学了解超精密切削加工机理和基本特点、懂得超精密切削加工过程中影响加工质量的诸多因素、懂得金刚石刀具的特点和性能、金刚石刀具材料特性、掌握刀具设计基本要点。
酽锕极額閉镇桧猪訣锥。
二、课程内容
第一节超精密切削的切削速度选择
第二节超精密切削时刀具的磨损和寿命
第三节超精密切削时积屑瘤的生成规律
(一)超精密切削时切削参数对积屑瘤生成的影响
(二)超精密切削时积屑瘤对切削力和加工表面粗糙度的影响
(三)使用切削液减小积屑瘤,减小加工表面粗糙度
第四节切削参数变化对加工表面质量的影响
(一)切削速度的影响
(二)进给量和修光刃对加工表面粗糙度的影响
(三)切削刃形状对加工表面粗糙度的影响
(四)背吃刀量变化对加工表面粗糙度的影响
(五)背吃刀量变化对加工表面残留应力的影响
第五节切削刃锋锐度对切削变形和加工表面质量的影响
(一)切削刃锋锐度的测量
(二)切削刃锋锐度对加工表面粗糙度的影响
(三)切削刃锋锐度对切削变形和切削力的影响
(四)切削刃锋锐度对切削表面层的冷硬和组织位错的影响
(五)切削刃锋锐度对加工表面残留应力的影响
第六节金刚石刀具超精密切削中的若干理论问题
(一)超精密切削能达到的最小切削厚度
(二)金刚石刀具晶面选择对切削变形和加工表面质量的影响
(三)工件材料的晶体方向对切削变形和加工表面质量的影响
(四)脆性材料用超精密切削加工出优质表面
第七节超精密切削对刀具的要求及金刚石的性能和晶体结构
(一)超精密切削对刀具的要求
(二)金刚石晶体的性能
(三)金刚石的晶体结构
第八节金刚石晶体各晶面的耐磨性和好磨难磨方向
(一)金刚石晶体各晶面的耐磨性
(二)金刚石晶体各晶面的好磨难磨方向
(三)金刚石晶体研磨时摩擦系数的各向异性
第九节单晶金刚石刀具的磨损破损机理
(一)单晶金刚石刀具磨损形态和微观崩刃的观察
(二)金刚石晶体的破损机理和微观强度
(三)金刚石各晶面的微观破损强度
第十节金刚石晶体的定向
(一)金刚石晶体的人工目测定向
(二)金刚石晶体的X射线定向
(三)金刚石晶体的激光定向
第十一节金刚石刀具的设计与制造
(一)金刚石刀具的设计
(二)金刚石刀具的研磨加工
三、考核的知识点
(一)金刚石刀具超精密切削加工的适用范围
(二)超精密切削加工过程中积屑瘤的形成机理及对加工表面质量的影响
(三)超精密切削加工过程中切削用量、刀具几何参数、刀刃锋锐度等因素对切削变形和加工表面质量的影响
(四)超精密切削时最小切削厚度的分析方法
(五)超精密切削加工对刀具性能的要求
(六)金刚石的晶体结构与材料性能的关系
(七)金刚石刀具晶面选择对切削变形和加工表面质量的影响
(八)金刚石刀具破损机理
(九)金刚石刀具设计基本要点
(十)金刚石刀具制造方法。
四、考核要求
(一)识记
1、金刚石刀具超精密切削加工的适用范围
2、金刚石刀具在超精密切削加工中的切削用量
3、超精密切削加工过程中积屑瘤现象及对加工质量的影响
4、超精密切削加工对刀具的要求
5、金刚石材料的晶体结构和物理性能
6、金刚石刀具的制作方法及过程。
(二)领会
1、金刚石材料性能与超精密切削加工的关系
2、超精密切削加工过程中切削用量、刀具几何参数、刀刃锋锐度等因素对切削变形和加工表面质量的影响和机理
3、超精密切削时最小切削厚度的分析方法和研究意义
4、金刚石的晶体结构与材料性能的关系
5、金刚石刀具晶面选择对切削变形和加工表面质量的影响
6、金刚石刀具破损机理与金刚石材料晶体结构的关系
(三)应用
1、金刚石刀具设计的基本要点
第三章精密磨削和超精密磨削
一、学习目的与要求
通过本章节学习,要求同学懂得和熟悉各类精密和超精密磨削方法的加工机理与工艺特点、适用范围、各类精密和超精密磨削方法所用设备的性能要求和特点。
磨具的特点与性能参数,修整方法。
彈贸摄尔霁毙攬砖卤庑。
二、课程内容
第一节概述
(一)精密和超精密磨料加工方法分类
(二)精密和超精密砂轮磨料磨具
(三)精密和超精密涂覆磨具
第二节精密磨削
(一)精密磨削机理
(二)精密磨削砂轮选择
(三)精密磨削时的砂轮修整
(四)精密磨床
(五)精密磨削用量
第三节超硬磨料砂轮磨削
(一)超硬磨料砂轮磨削特点
(二)超硬磨料砂轮修整
(三)超硬磨料砂轮磨床
(四)超硬磨料砂轮磨削工艺
(五)超硬磨料砂轮的平衡
第四节超精密磨削
(一)超精密磨削和镜面磨削
(二)超精密磨削机理
(三)超精密磨床
(四)超精密磨削工艺
(五)超硬微粉砂轮超精密磨削
第五节精密和超精密砂带磨削
(四)砂带磨削方式、特点和应用范围
(五)砂带磨削机理
(六)精密砂带磨床和砂带头架
(七)精密砂带磨削工艺
三、考核的知识点
(一)精密和超精密磨料加工方法分类。
(二)砂轮磨具的结构与性能参数。
(三)精密磨削机理(砂轮磨削)
(四)超精密磨削机理(砂轮磨削)
(五)影响超精密磨削质量的一些主要因素
(六)精密和超精密砂轮磨削的工艺特点
(七)精密磨削机床的性能要求
(八)超硬磨料砂轮磨削的特点
(九)超硬磨料砂轮修整方法及分类
(十)精密和超精密砂带磨削的加工机理
(十一)精密和超精密砂带磨削的工艺特点
(十二)砂带磨削方法分类。
(十三)砂带磨具的制作方法及种类
(十四)影响砂带磨削加工质量的一些主要因素
(十五)精密和超精密砂带磨削设备的结构及主要部件的工作原理
四、考核要求
(一)识记
1、精密磨削和超精密磨料加工方法分类。
2、砂轮磨具的基本特点及组成结构
3、精密和超精密砂轮磨削的工艺特点
4、精密磨削和超精密磨削设备的要求与特点
5、超硬磨料砂轮磨削的特点
6、精密和超精密砂带磨削的工艺特点
7、砂轮修整方法及分类
8、砂带磨削方法分类。
9、砂带磨具的制作方法及种类
(二)领会
1、精密和超精密砂轮磨削的加工机理
2、超硬磨料砂轮磨削特点
3、超硬磨料砂轮修整方法及分类
4、精密和超精密砂带磨削的加工机理
(三)应用
1、影响砂轮磨削加工质量的一些主要因素
2、影响砂带磨削加工质量的一些主要因素
(四)精密和起精密加工的机床设备
一、学习目的与要求
通过本章节学习,要求同学了解精密和超精密机床的结构型式,懂得主要部件的工作原理和结构特点。
熟悉机床系统稳定性对控制加工质量的关系、机床系统及环境条件中的振动和热变形问题及解决方法。
謀荞抟箧飆鐸怼类蒋薔。
二、课程内容
第一节精密和超精密机床发展简况
(一)精密和超精密机床的发展情况
(二)超精密机床进一步发展的规划
第二节典型超精密机床的简介
第三节精密主轴部件
(一)液体静压轴承主轴
(二)空气静压轴承主轴
(三)超精密机床主轴和轴承的材料
(四)主轴的驱动方式
第四节机床的总体布局和床身导轨
(一)超精密机床的总体布局
(二)床身和导轨的材料
(三)滚动导轨
(四)液体静压导轨
第五节进结驱动系统
(一)精密数控系统
(二)滚珠丝杆副驱动
(三)摩擦驱动
第六节微量进给装置
(六)对微量进给装置的要求
(七)电致伸缩传感器
(八)电致伸缩传感器微量进给装置的结构
(九)电致伸缩式微量进给装置的驱动电源
第七节机床运动部件位移的激光在线检测系统
(一)超精密机床的在线检测系统
(二)美国超精密机床的激光检测系统
(三)三坐标测量机用激光位移测量系统
(四)美国大型光学金刚石车床激光测量系统
第八节机床的稳定性和减振隔振
(一)机床的稳定性
(二)提高机床结构的抗振性和消除、减少机床内的振动
(三)隔离振源,使用隔振沟、隔振墙和空气隔振垫以减少外界振动的影响
第九节减少热变形和恒温控制
(一)温度变化对精密机床和精密加工误差的影响
(二)减小机床热变形的措施
(三)美大型超精密车床的恒温控制
三、考核的知识点
(一)精密和超精密机床的结构型式和特点
(二)超精密机床的床身布局
(三)超精密机床中精密主轴部件单元的结构型式和工作原理
(四)床身结构和床身材料的选用
(五)精密机床和超精密机床的导轨部件的结构型式和工作原理
(六)精密机床和超精密机床的进给传动部件的结构型式和工作原理
(七)微量进给装置的工作原理
(八)激光位移在线检测系统的工作原理和应用
(九)超精密机床系统稳定性的重要性
(十)超精密机床减振隔振的方法
(十一)减少工艺系统热变形的方法和实行恒温控制的方法
四、考核要求
(一)识记
1、精密和超精密机床的结构型式及其特点
2、微量进给装置的工作原理
3、机床运动部件位移的激光在线检测系统的工作原理
(二)领会
1、精密和超精密机床中主轴支承的工作原理、结构型式与特点
2、精密和超精密机床中主轴与驱动电机的连接型式与特点
3、精密和超精密机床中导轨部件的工作原理、结构型式与特点
4、精密和超精密机床中进给传动部件的工作原理、结构型式与特点
5、精密和超精密机床系统稳定性的重要性。
(三)应用
1、提高精密和超精密机床系统稳定性的相关技术措施
2、减振隔振方法在精密和超精密加工中应用
3、减少工艺系统热变形的方法
4、超精密机床中恒温控制的方法
5、精密和超精密机床中主轴部件的运动精度,进给传动部件的运动精度与机床精度的关系
第五章精密加工中的测量技术
一、学习目的与要求
通过本章节学习,要求同学懂得测量技术对精密加工的重要性、熟悉几何量精密测量方法及其测量原理。
懂得回转精度测量方法的工作原理及其分析计算公式。
懂得激光测量的基本原理,单频激光测量原理和双频激光原理。
厦礴恳蹒骈時盡继價骚。
二、课程内容
第一节精密测量技术概述
(一)精密测量技术的新发展
(二)精密测量的环境条件
(三)量具和量仪材料的选择
第二节测量基准
(一)M制长度基准
(二)量块
(三)工厂自己专用的长度基准
(四)平台——测量基准
第三节直线度、平面度和垂直度的测量
(一)直线度的测量
(二)平面度测量
(三)垂直度测量
第四节角度和圆分度的测量
(一)角度基准
(二)正弦工作台
(三)精密测量转台
(四)精密多齿分度盘
第五节圆度和回转精度的测量
(一)圆度的测量方法和圆度误差的评定
(二)圆度仪及其测量精度分析
(三)圆度的在线测量
(四)主轴回转精度的测量
第六节激光测量
第七节自由曲面的测量
(一)自由曲面的测量
(二)自由表面的测量结果的评定
三、考核的知识点
(一)精密测量的环境要求
(二)量具和量仪材料选择
(三)长度基准、角度基准、测量平台
(四)角度测量、直线度测量和平行度测量方法
(五)圆分度测量方法
(六)多齿分度盘的工作原理
(七)圆度测量方法及圆度测量仪
(八)主轴回转精度的测量方法
(九)激光干涉测量方法
(十)激光干涉测量方法在位移测量中的应用
(十一)激光干涉测量方法在小角度、表面粗糙度测量中的应用
四、考核要求
(一)识记
1、长度基准、角度基准的型式和功用
2、测量平台
3、激光测量的基本原理
(二)领会
1、直线度、平面度和垂直度的测量方法
2、角度和圆分度的测量方法
3、圆度测量方法及圆度测量误差
4、单频激光测量原理和双频激光测量原理
5、影响激光测量精度的一些因素。
(三)应用
1、精密多齿分度盘的小角度分度方法
2、主轴回转精度测量中,三点误差分离原理测量方法的工作原理
3、激光干涉测量方法在位移、小角度、表面粗糙度测量中的应用
第六章在线检测与误差补偿技术
一、学习目的与要求
通过本章节学习,要求同学懂得在线检测与误差补偿技术在精密加工中的作用和熟悉其基本原理和实现方法。
懂得徽位移系统的功用、了解其分类、懂得其典型结构型式、工作原理和特性。
茕桢广鳓鯡选块网羈泪。
二、课程内容
第一节概述
(一)保证零件加工精度的途径
(二)加工精度的检测
(三)误差补偿技术
第二节在线检测与误差补偿方法
(一)形状位置误差的在线检测
(二)在线检测与误差补偿系统的应用实例
第三节微位移技术
(一)微位移系统及其应用
(二)微位移机构的类型
(三)典型微位移工作台
三、考核的知识点
(一)加工精度的检测
(二)在线检测与误差补偿方法
(三)在线检测与误差补偿方法的应用
(四)形状误差、位置误差的多点检测、误差分离测量方法
(五)微位移技术
四、考核要求
(一)识记
1、在线检测与误差补偿技术的基本知识
(二)领会
1、在线检测与误差补偿方法在机械加工中应用
2、徽位移技术
3、电磁控制、磁致伸缩、电致伸缩微位移工作台的工作原理,主要驱动器件的特性
(三)应用
1、在线检测与误差补偿的实现方法
第七章精密研磨和抛光
一、学习目的与要求
通过本章节学习,要求同学能掌握研磨和抛光工艺的基本机理,特点及适用范围。
了解超精密平面研磨和抛光的工艺特点、新工作原理下的超精密研磨抛光的特点、熟悉其适用范围。
鹅娅尽損鹌惨歷茏鴛賴。
二、课程内容
第一节研磨
(一)研磨加工的机理
(二)研磨加工的特点
第二节抛光
(一)抛光机理
(二)微小机械去除与化学作用
第三节精密研磨与抛光的主要工艺因素
(一)工艺因素及其选择原则
(二)研磨与抛光设备
(三)研磨盘与抛光盘
(四)磨粒
(五)加工液
(六)工艺参数
第四节精密研磨抛光新技术
(一)无损伤抛光
(二)非接触抛光
(三)界面反应抛光
(四)电、磁场辅助抛光
第五节曲面研磨抛光技术
(一)磁性磨粒加工
(二)磁流变加工
(三)气囊抛光
(四)应力盘抛光
三、考核的知识点
(一)研磨加工机理
(二)抛光加工机理
(三)研磨和抛光加工工艺因素和基本要求
(四)新工作原理的超精密抛光方法
四、考核要求
(一)识记
1、研磨加工机理
2、抛光加工机理
3、研磨和抛光加工工艺因素和基本要求
(二)领会
1、新工作原理下的超精密抛光方法
(三)应用
1、研磨和抛光加工的工艺参数
第八章微细加工技术
一、学习目的与要求
通过本章节学习,要求同学能掌握微细加工的概念、基本特征、工艺特点,懂得微细加工的机理、电子束加工方法,离子束加工方法,激光束加工方法的加工机理、特点和熟悉其应用范围。
籟丛妈羥为贍偾蛏练淨。
二、课程内容
第一节微细加工技术的出现
(一)制造技术自身加工的极限
(二)微细加工出现的历史背景
第二节微细加工的概念及其特点
(一)微细加工的概念
(二)微细加工的特点
第三节微细加工机理
(一)切削厚度与材料剪切应力的关系
(二)材料缺陷分布对其破坏方式的影响
(三)各种微细加工方法的加工机理
第四节微细加工方法
(一)微细加工方法分类
(二)微细加工的基础技术
(三)光刻加工技术
(四)立体复合工艺
第五节集成电路与印制线路板制作技术
(一)集成电路制作技术
(二)印制线路板制作技术
三、考核的知识点
(一)微细加工技术的基本知识、概念及其特点
(二)微细加工技术的工艺特点
(三)微细加工机理
(四)微细加工方法与微细加工方法分类
(五)电子束加工方法的加工机理、特点和应用范围
(六)电子束加工设备
(七)离子束加工方法的加工机理、特点和应用范围
(八)离子束加工设备
(九)激光束加工方法的加工机理、特点和应用范围
(十)激光加工设备
四、考核要求
(一)识记
1、微细加工技术的基本知识、概念及其特点
2、微细加工技术的工艺特点
3、微细加工方法与微细加工方法分类
4、电子束加工、离子束加工、激光束加工的特点和应用范围
5、电子束加工、离子束加工、激光束加工设备的结构与工作原理
(二)领会
1、微细加工机理
2、电子束、离子束加工、激光束的加工机理
第九章精密和超精密加工的外部支撑环境
一、学习目的与要求
通过本章节学习,要求同学懂得加工支撑环境要素与精密和超精密加工技术的关系和其重要作用。
了解影响加工支撑环境的诸多因素、熟悉精密和超精密加工支撑环境的实现方法。
預頌圣鉉儐歲龈讶骅籴。
二、课程内容
第一节空气环境和热环境
(一)空气环境
(二)热环境
(三)洁净室
(四)分层次的局部环境
第二节振动环境
(一)振动干扰的影响
(二)振动干扰的消除
(三)隔振器的隔振原理
(四)隔振元器件
(五)隔振器件的新进展
第三节噪声环境
(一)噪声及其影响
(二)噪声源
(三)噪声控制
第四节其它环境
(一)光环境
(二)静电环境
第五节精密和超精密加工的环境设施
三、考核的知识点
(一)精密和超精密加工对支撑环境的基本要求
(二)加工支撑环境与精密和超精密加工技术的关系
(三)影响加工支撑环境的诸多因素
(四)精密和超精密加工支撑环境的实现方法
四、考核要求
(一)识记
1、精密和超精密加工对支撑环境的基本要求
2、影响加工支撑环境的诸多因素
(二)领会
1、加工支撑环境要素与精密和超精密加工技术的关系
(三)应用
1、精密和超精密加工支撑环境的实现方法。
第十章纳M技术
一、学习目的与要求
通过本章节学习,要求同学了解纳M技术的定义,特点;懂得纳M测量技术、纳M加工技术的基本机理和实现方法;了解纳M级器件、微型机械和微型机电系统的工作原理和特点。
渗釤呛俨匀谔鱉调硯錦。
二、课程内容
第一节纳M技术概述
(一)纳M技术的特点
(二)发展纳M技术的重要性
(三)纳M技术的主要内容
第二节纳M级测量和扫描探针测量技术
(一)纳M级测量方法简介
(二)Fabry-Perot标准具的测量技术
(三)X射线干涉测量技术
(四)扫描隧道显微测量技术
(五)微观表面形貌的扫描探针测量和其他扫描测量技术
第三节纳M级加工技术和原子操纵
(一)纳M级加工的物理实质分析
(二)纳M级加工精度
(三)使用SPM进行原子操纵
(四)使用SPM加工微结构
第四节微型机械、微型机电系统及其制造技术
(一)微型机械、微型机电系统
(二)微型机械、微型机电系统的制造技术
三、考核的知识点
(一)纳M技术的特点及主要内容
(二)纳M测量技术中的各种测量方法与基本原理
(三)纳M级表层物理力学性能检测方法和基本原理。
(四)纳M级加工技术的基本原理和特点。
(五)微型机械和微型机电系统的组成和特点。
三、考核要求
(一)识记
1、纳M技术的特点及主要内容
2、纳M级加工技术的基本原理和特点。
3、微型机械和微型机电系统的组成和特点。
(二)领会
1、扫描遂道显微测量技术与基本原理
第二篇特种加工
第一章概论
一、学习目的与要求
要求了解特种加工的产生及发展过程,特点和趋势,了解特种加工的分类及特种加工对材料可加工性和结构工艺性等的影响。
铙誅卧泻噦圣骋贶頂廡。
二、课程内容
第一节特种加工的产生及发展
第二节特种加工的分类
第三节特种加工对材料可加工性和结构工艺性等的影响
三、考核的知识点
(一)特种加工的定义和特种加工工艺的特点
四、考核要求
(一)识记
1、特种加工的定义
2、特种加工对材料可加工性和结构工艺性等的影响
第二章电火花加工
一、学习目的与要求
要求理解电火花加工的基本原理、工作机理与电火花加工中的一些基本规律。
了解电火花加工机床的特点和主要部件的工作原理、电火花穿孔成形加工的工艺参数、其它电火花加工特点和应用范围。
掌握电火花穿孔成形加工中电极的设计方法。
擁締凤袜备訊顎轮烂蔷。
二、课程内容
第—节电火花加工的基本原理及其分类
(一)电火化加工的原理和设备组成
(二)电火化加工的特点及其应用
(三)电火化加工工艺方法分类
第二节电火花加工的机理
(一)极间介质的电离、击穿,形成放电通道
(二)介质热分解、电极材料熔化、气化热膨胀
(三)电极材料的抛出
第三节电火花加工中的一些基本规律
(一)影响材料放电腐蚀的主要因素
(二)电火化加工的加工速度和工具的损耗速度
(三)影响加工精度的主要因素
(四)电火化加工的表面质量
第四节电火花加工用脉冲电源
(一)对脉冲电源的要求及其分类
(二)RC线路脉冲电源
(三)晶体管试脉冲电源
(四)各种派生脉冲电源
第五节电火花加工的自动进给调节系统