注塑不良分析.docx
《注塑不良分析.docx》由会员分享,可在线阅读,更多相关《注塑不良分析.docx(39页珍藏版)》请在冰豆网上搜索。
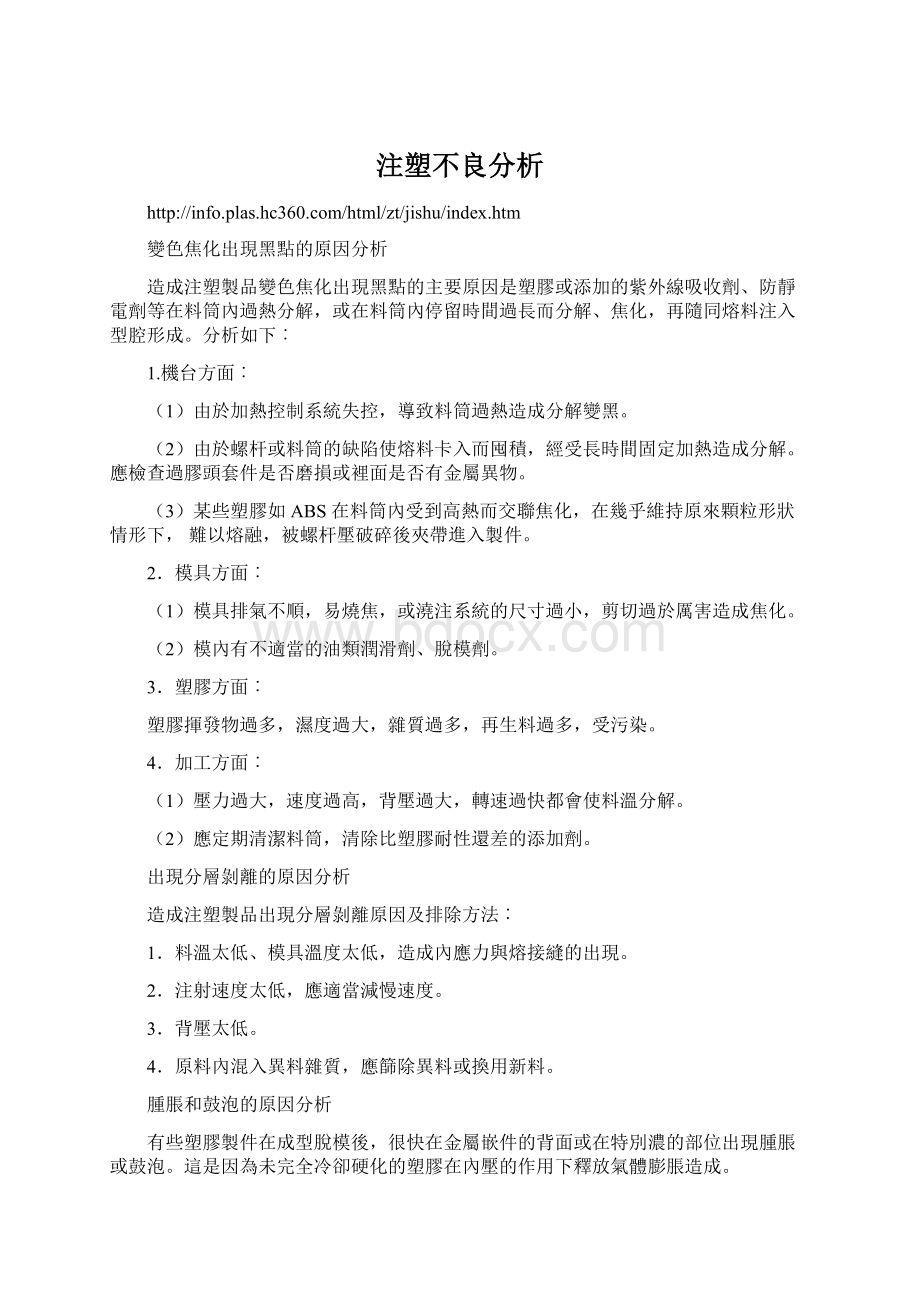
注塑不良分析
變色焦化出現黑點的原因分析
造成注塑製品變色焦化出現黑點的主要原因是塑膠或添加的紫外線吸收劑、防靜電劑等在料筒內過熱分解,或在料筒內停留時間過長而分解、焦化,再隨同熔料注入型腔形成。
分析如下︰
1.機台方面︰
(1)由於加熱控制系統失控,導致料筒過熱造成分解變黑。
(2)由於螺杆或料筒的缺陷使熔料卡入而囤積,經受長時間固定加熱造成分解。
應檢查過膠頭套件是否磨損或裡面是否有金屬異物。
(3)某些塑膠如ABS在料筒內受到高熱而交聯焦化,在幾乎維持原來顆粒形狀情形下,難以熔融,被螺杆壓破碎後夾帶進入製件。
2.模具方面︰
(1)模具排氣不順,易燒焦,或澆注系統的尺寸過小,剪切過於厲害造成焦化。
(2)模內有不適當的油類潤滑劑、脫模劑。
3.塑膠方面︰
塑膠揮發物過多,濕度過大,雜質過多,再生料過多,受污染。
4.加工方面︰
(1)壓力過大,速度過高,背壓過大,轉速過快都會使料溫分解。
(2)應定期清潔料筒,清除比塑膠耐性還差的添加劑。
出現分層剝離的原因分析
造成注塑製品出現分層剝離原因及排除方法︰
1.料溫太低、模具溫度太低,造成內應力與熔接縫的出現。
2.注射速度太低,應適當減慢速度。
3.背壓太低。
4.原料內混入異料雜質,應篩除異料或換用新料。
腫脹和鼓泡的原因分析
有些塑膠製件在成型脫模後,很快在金屬嵌件的背面或在特別濃的部位出現腫脹或鼓泡。
這是因為未完全冷卻硬化的塑膠在內壓的作用下釋放氣體膨脹造成。
解決措施︰
1.有效的冷卻。
降低模溫,延長開模時間,降低料的乾燥與加工溫度。
2.降低充模速度,減少成形週期,減少流動阻力。
3.提升保壓壓力和時間。
4.改善製件壁面太濃或濃薄變化大的狀況。
透明缺陷的原因分析
熔斑、銀紋、裂紋聚苯乙烯、有機玻璃的透明製件,有時候透過光線可以看到一些閃閃發光的細絲般的銀紋。
這些銀紋又稱爍斑或裂紋。
這是由於拉應力的垂直方向產生了應力,使聚合物分子在流動方向取向,使得取向部分與未取向部分折射率不同,光線透過兩者界面時發生折射產生銀紋。
解決方法︰
(1)消除氣體及其它雜質的干擾,對塑膠充分乾燥。
(2)降低料溫,分段調節料筒溫度,適當提升模溫。
(3)增加注射壓力,降低注射速度。
(4)增加或減少預塑背壓壓力,減少螺杆轉速。
(5)改善流道及型腔排氣狀況。
(6)清理射嘴、流道和澆口可能的堵塞。
(7)縮短成型週期,脫模後可用退火方法消除銀紋︰對聚苯乙烯在78℃時保持15分鐘,或50℃時保持1小時,對聚碳酸酯,加熱到160℃以上保持數分鐘。
發脆的原因
製品發脆很大一部分是由於內應力造成的。
造成製品發脆的原因很多,主要有︰
一設備方面
(1)機筒內有死角或障礙物,容易促進熔料降解。
(2)機器塑化容量太小,塑膠在機筒內塑化不充分;機器塑化容量太大,塑膠在機筒內受熱和受剪切作用的時間過長,塑膠容易老化,使製品變脆。
(3)頂出裝置傾斜或不平衡,頂杆截面積小或分佈不當。
二模具方面
(1)澆口太小,應考慮調整澆口尺寸或增設輔助澆口。
(2)分流道太小或配置不當,應盡量安排得平衡合理或增加分流道尺寸。
(3)模具架構不良造成注塑週期反常。
三工藝方面
(1)機筒、噴嘴溫度太低,調高它。
如果物料容易降解,則應提升機筒、噴嘴的溫度。
(2)降低螺杆預塑背壓壓力和轉速,使料稍為疏松,並減少塑膠因剪切過熱而造成的降解。
(3)模溫太高,脫模困難;模溫太低,塑膠過早冷卻,熔接縫融合不良,容易開裂,特別是高熔點塑膠如聚碳酸酯等更是如此。
(4)型腔模芯要有適當的脫模斜度。
模芯難脫模時,要提升型腔溫度,縮短冷卻時間;
型腔難脫時,要降低型腔溫度,延長冷卻時間。
(5)盡量少用金屬嵌件,像聚苯乙烯這類脆性的冷熱比容大的塑膠,更不能加入嵌件注塑。
四原料方面
(1)原料混有其它雜質或攙雜了不適當的或過量的溶劑或其它添加劑時。
(2)有些塑膠如ABS等,在受潮狀況下加熱會與水汽發生催化裂化回應,使製件發生大的應變。
(3)塑膠再生次數太多或再生料含量太高,或在機筒內加熱時間太長,都會促使製件脆裂。
(4)塑膠本身質量不佳,例如分子量分佈大,含有剛性分子鏈等不均勻架構的成分佔有量過大;或受其它塑膠攙雜污染、不良添加劑污染、灰塵雜質污染等也是造成發脆的原因。
五製品設計方面
(1)製品帶有容易出現應力開裂的尖角、缺口或濃度相差很大的部位。
(2)製品設計太薄或鏤空太多。
氣泡的原因分析
氣泡(真空泡)的氣體十分稀薄屬於真空泡。
一般說來,如果在開模瞬間已發現存在氣泡是屬於氣體干擾問題。
真空泡的形成是由於充注進塑膠不足或壓力較低。
在模具的急劇冷卻作用下,與型腔接角的熔料牽拉,造成體積損失的結果。
解決辦法︰
(1)提升注射能量︰壓力、速度、時間和料量,並提升背壓,使充模豐滿。
(2)增加料溫流動順暢。
降低料溫減少收縮,適當提升模溫,特別是形成真空泡部位的局部模溫。
(3)將澆口設定在製件濃的部份,改善噴嘴、流道和澆口的流動狀況,減少壓力的消耗。
(4)改進模具排氣狀況。
表面光澤差的原因分析
造成注塑製表面光澤差,主要有兩個原因影響整體透明度。
一是模面拋光不好,二是熔料過早冷卻。
具體解決方法如下︰
(1)增加料溫,注射壓力與速度,特別是模溫。
模溫對光澤有顯著的影響。
(2)改善澆口的位置,注意料流通暢。
(3)防止塑膠的降解或塑化不完全。
(4)增長模內冷卻時間,保壓時間也應加長一些。
震紋的原因分析
PS等剛性塑膠製件在其澆口附近的表面,以澆口為中心的形成密集的波紋,有時稱為震紋。
產生原因是熔體黏度過大而以滯流形式充模時,前端的料一接觸到型腔表面便很快冷凝收縮起來,而後來的熔料又脹開已收縮的冷料繼續前進過程的不斷交替使料流在前進中形成了表面震紋。
解決方法︰
(1)提升料筒溫度特別是射嘴溫度,還應提升模具溫度。
(2)提升注射壓力與速度,使其快速充模型腔。
(3)改善流道、澆口尺寸,防止阻力過大。
(4)模具排氣要良好,要設定足夠大的冷料井。
(5)製件不要設計得過於薄。
泛白的原因分析
造成注塑製品泛白、霧暈。
這是由於氣體或空氣中的雜質的污染而出現的缺陷。
主要解決方法︰
(1)消除氣體的干擾,就意防止雜質的污染。
(2)提升料溫與模溫,分段調節料筒溫度,但要防止溫度過高而分解。
(3)增加注射壓力,延長保壓時間,提升背壓。
射料不滿的原因分析
造成注塑製品射料不滿的主要原因是缺料和注射壓力與速度不妥(包括阻力造成壓力過於耗損)。
可能由以下幾個方面的原因導致而成︰
1.注塑機台原因︰
機台的塑化量或加熱率不定,應選用塑化量與加熱功率大的機台;螺杆與料筒或過膠頭等的磨損造成回料而出現實際充模量不足;熱電偶或發熱圈等加熱系統故障造成料筒的實際溫度過低;注射油缸的密封元件磨損造成漏油或回流,而不能達到所需的注射壓力;射嘴內孔過小或射嘴中心度調節不當造成阻力過大而使壓力消耗。
2.注塑模具原因︰
1)模具局部或整體的溫度過低造成入料困難,應適當提升模溫;
2)模具的型腔的分佈不平衡。
製件壁濃過薄造成壓力消耗過度而且充模不力。
應增加整個製件或局部的壁濃或可在填充不足處的附近,設定輔助流道或澆口解決。
3)模具的流道過小造成壓力損耗;過大時會出現射膠無力;過於粗糙都會造成製件不滿。
應適當設定流道的大小,主流道與分流道,澆口之間的過渡或本身的轉彎處應用適當的圓弧過渡。
4)模具的排氣不良。
進入型腔的料受到來不及排走的氣體壓力的阻擋而造成充填不滿。
可以充分利用螺杆的縫隙排氣或降低鎖模力利用分型面排氣,必要時要開設排氣溝道或氣孔。
飛邊的原因分析
飛邊又稱溢邊、披鋒、毛刺等,大多發生在模具的分合位置上,如動模和靜模的分型面,滑塊的滑配部位、鑲件的絕隙、頂杆孔隙等處,飛邊在很大程度上是由於模具或機台鎖模力失效造成。
具體可能有以下幾個方面的原因造成︰
1.注塑機台原因︰
機台的最高鎖模力不夠應選用鎖模力夠的機台。
鎖模機鉸磨損或鎖模油缸密封元件磨損出現滴油或回流而造成鎖模力下降。
加溫系統失控造成實際溫度過高應檢查熱電偶、加熱圈等是否有問題。
2.注塑模具原因︰
(1)模具型腔分佈不衡或平行度不夠造成受力不平衡而造成局部飛邊,局部不滿,應在不影響製件完整性前提下流道應盡量安置在質量對稱中心。
(2)模具中活動構件、滑動模芯受力不平衡時會造成飛邊。
(3)模具排氣不良時受壓的空氣會使模的分型面脹開而出現飛邊,應開設良好的排氣系統,或在分型面上挖排氣溝。
3.塑膠的流動性過大,或加太多的潤滑劑,應適當降低壓力、速度、溫度等,減小潤滑劑的使用量,必要時要選用流動性低的塑膠。
4.加工、調整方面︰
(1)設定的溫度、壓力、速度過高,應採用分段注射。
注射時間、保壓時間、加料量過多都會造成飛邊。
(2)調節時,鎖模機鉸未伸直,或開、鎖模時調模螺母經常會動而造成鎖模力不足出現飛邊。
(3)調節頭與二極的平行度不夠或調節的系統壓力過大。
5.飛邊和製件不滿反覆出現的原因︰
(1)塑膠原料粒度大小懸殊不均時會使加料份量不定。
(2)螺杆的過膠頭、過膠圈及過膠墊圈的磨損過大,使熔料可能在螺杆處經與料筒內之間滑行及回流造成飛邊或不滿。
(3)入流口的冷卻系統失效,令進料的調。
(4)料筒調定的注料量不足,即緩沖墊過小會使射料時多時少而出現飛邊或製件不滿。
澆口區冷料斑的原因分析
冷料斑主要是指製件近澆口處帶有霧色或亮色的斑紋,或從澆口出發的宛如若蚯蚓貼在上面的彎曲疤痕,它們由進入型腔的塑膠前鋒或因過分的保壓作用而後來擠進型腔的冷料造成,前鋒料因為射咀或流道的冷卻作用傳去熱量,在進入型腔前部分被冷卻固化,當透過狹窄的澆口而擴張注入型腔時,形成熔體破裂,緊接著又被後來的熱熔料推擁,於是就成了冷料斑。
解決方法︰
(1)冷料井要開設好。
還要考慮澆口上的形式、大小和位置,防止料的冷卻速度懸殊。
(2)射咀中心度要調好,射咀與模具入料上的配合尺寸要設計好,防止漏料或造成有冷料被帶入型腔。
(3)模具排氣度良好。
氣體的干擾會使澆口出現混濁性的斑紋。
(4)提升模溫。
減慢注射速度,增大注射壓力,減低保壓與注射時間,減低保壓壓力。
(5)乾燥好塑膠。
少用潤滑劑,防止粉料被污染。
收縮凹陷的原因分析
注塑成型過程中,製品收縮凹陷是比較常見的現象。
造成這種情況的主要原因有︰
1.機台方面︰
(1)射嘴孔太大造成融料回流而出現收縮,太小時阻力大料量不足出現收縮。
(2)鎖模力不足造成飛邊也會出現收縮,應檢查鎖模系統是否有問題。
(3)塑化量不足應選用塑化量大的機台,檢查螺杆與料筒是否磨損。
2.模具方面︰
(1)製件設計要使壁濃均勻,保證收縮一致。
(2)模具的冷卻、加溫系統要保證各部份的溫度一致。
(3)澆注系統要保證通暢,阻力不能過大,如主流道、分流道、澆口的尺寸要適當,光潔度要足夠,過渡區要圓弧過渡。
(4)對薄件應提升溫度,保證料流暢順,對濃壁製件應降低模溫。
(5)澆口要對稱開設,盡量開設在製件濃壁部位,應增加冷料井容積。
3.塑膠方面︰
結晶性的塑膠比非結晶性塑膠收縮歷害,加工時要適當增加料量,或在塑膠中加成換劑,以加快結晶,減少收縮凹陷。
4.加工方面︰
(1)料筒溫度過高,容積變化大,特別是前爐溫度,對流動性差的塑膠應適當提升溫度、保證暢順。
(2)注射壓力、速度、背壓過低、注射時間過短,使料量或密度不足而收縮壓力、速度、背壓過大、時間過長造成飛邊而出現收縮。
(3)加料量即緩沖墊過大時消耗注射壓力,過小時,料量不足。
(4)對於不要求精度的製件,在注射保壓完畢,外層基本冷凝硬化而夾心部份尚柔軟又能頂出的製件,及早出模,讓其在空氣或熱水中緩慢冷卻,可以使收縮凹陷平緩而不那麼顯眼又不影響使用。
翹曲變形的原因分析
注塑製品變形、彎曲、扭曲現象的發生主要是由於塑膠成型時流動方向的收縮率比垂直方向的大,使製件各向收縮率不同而翹曲,又由於注射充模時不可避免地在製件內部殘留有較大的內應力而引起翹曲,這些都是高應力取向造成的變形的表現。
所以從根本上說,模具設計決定了製件的翹曲傾向,要透過變更成型條件來抑制這種傾向是十分困難的,最終解決問題必須從模具設計和改良著手。
這種現象的主要有以下幾個方面造成︰
1.模具方面︰
(1)製件的濃度、質量要均勻。
(2)冷卻系統的設計要使模具型腔各部分溫度均勻,澆注系統要使料流對稱避免因流動方向、收縮率不同而造成翹曲,適當加粗較難成型部份的分流道、主流道,盡量消除型腔內的密度差、壓力差、溫度差。
(3)製件濃薄的過渡區及轉角要足夠圓滑,要有良好的脫模性,如增加脫模余度,改善模面的拋光,頂出系統要保持平衡。
(4)排氣要良好。
(5)增加製件壁濃或增加抗翹曲方向,由加強筋來增強製件抗翹曲能力。
(6)模具所用的材料強度不足。
2.塑膠方面︰
結晶型比非結晶型塑膠出現的翹曲變形機會多,加之結晶型塑膠可利用結晶度隨冷卻速度增大而降低,收縮率變小的結晶過程來矯正翹曲變形。
3.加工方面︰
(1)注射壓力太高,保壓時間太長,熔料溫度太低速度太快會造成內應力增加而出現翹曲變形。
(2)模具溫度過高,冷卻時間過短,使脫模時的製件過熱而出現頂出變形。
(3)在保持最低限度充料量下減少螺杆轉速和背壓降低密度來限制內應力的產生。
(4)必要時可對容易翹曲變形的製件進行模具軟性定型或脫模後進行退火處理。
成型時主流道粘模的原因分析
注塑成型時主流道粘模的原因及排除方法︰
(1)冷卻時間太短,主流道尚未凝固。
(2)主流道斜度不夠,應增加其脫模斜度。
(3)主流道襯套與射嘴的配合尺寸不當造成漏流。
(4)主流道粗糙,主流道無冷卻井。
(5)射嘴溫度過低,應提升溫度。
成型時生產緩慢的原因分析
注塑成型時生產緩慢的原因及解決方法如下︰
(1)塑膠溫度、模具溫度高,造成冷卻時間長。
(2)熔膠時間長。
應降低背壓壓力,少用再生料防止架空,送料段冷卻要充分。
(3)機台的動作慢。
可從油路與電路調節使之適當加快。
(4)模具的設計要方便脫模,盡量設計成全自動操作。
(5)製作壁濃過大,造成冷卻時間過長。
(6)噴嘴流涎,妨礙正常生產。
應採用自鎖式射嘴,或降低射嘴溫度。
(7)料筒供熱量不足。
應換用塑化容量大的機台或加強對料的預熱。
注塑機介紹及注塑問題解決方案注塑機功能介紹
注塑機具有能一次成型外型複雜、尺寸精確或帶有金屬嵌件的質地密致的塑膠製品,被廣泛應用於國防、機電、汽車、交通運輸、建材、包裝、農業、文教衛生及人們日常生活各個領域。
注射成型工藝對各種塑膠的加工具有良好的適應性,生產能力較高,並易於實現自動化。
在塑膠工業迅速發展的今天,注塑機不論在數量上或品種上都佔有重要地位,從而成為目前塑膠機械中增長最快,生產數量最多的機種之一。
我國塑膠加工企業星羅其布,遍佈全國各地,設備的技術水準參差不齊,大多數加工企業的設備都需要技術改造。
這幾年來,我國塑機行業的技術進步十分顯著,尤其是注塑機的技術水準與國外名牌產品的差距大大縮小,在控制水準、產品內部質量和外觀型式等方面均取得顯著改觀。
選擇國產設備,以較小的投入,同樣也能生產出與進口設備質量相當的產品。
這些為企業的技術改造創造了條件。
要有好的製品,必須要有好的設備。
設備的磨損和腐蝕是一種自然規律,人們掌握了這種規律,就可以預防或減少設備的磨損和腐蝕,延長設備的使用週期,保證設備的完好率。
為加強塑膠機械的使用、維護和管理工作,我國有關部門已製訂了有關標準和實施細則,要求各設備管理部門和生產企業對設備的管理和使用做到“科學管理、正確使用、合理潤滑、精心維護、定期保養、計畫檢修,提升設備完好率,使設備經常處於良好狀態。
本文撰寫了注塑機維護、保養的有關知識和技術資料可供設備管理部門和生產企業的管理人員和技術人員參考。
塑膠注射成型技術是根據壓鑄原理從十九世紀末二十世紀初發展起來的,是目前塑膠加工中最普遍採用的方法之一。
該法適用於全部熱塑性塑膠和部分熱固性塑膠(約占塑膠總量的1/3)。
1.1注塑成型機的工作原理
注塑機的工作原理與打針用的注射器相似,它是借助螺杆(或柱塞)的推力,將已塑化好的熔融狀態(即粘流態)的塑膠注射入閉合好的模腔內,經固化定型後取得製品的工藝過程。
注射成型是一個循環的過程,每一週期主要包括︰定量加料─熔融塑化─施壓注射─充模冷卻─啟模取件。
取出塑件後又再閉模,進行下一個循環。
1.2注塑機的架構
注塑機根據塑化模式分為柱塞式注塑機和螺杆式注塑機;按機器的傳動模式又可分為液壓式、機械式和液壓─機械(連杆)式;按操作模式分為自動、半自動、手動注塑機。
(1)臥式注塑機︰這是最常見的類型。
其合模部分和注射部分處於同一水準中心線上,且模具是沿水準方向打開的。
其特點是︰機身矮,易於操作和維修;機器重心低,安裝較平穩;
製品頂出後可利用重力作用自動落下,易於實現全自動操作。
目前,市場上的注塑機多採用此種型式。
(2)立式注塑機︰其合模部分和注射部分處於同一垂直中心線上,且模具是沿垂直方向打開的。
因此,其占地面積較小,容易安放嵌件,裝卸模具較方便,自料斗落入的物料能較均勻地進行塑化。
但製品頂出後不易自動落下,必須用手取下,不易實現自動操作。
立式注塑機宜用於小型注塑機,一般是在60克以下的注塑機採用較多,大、中型機不宜採用。
(3)角式注塑機︰其注射方向和模具分界面在同一個面上,它特別適合於加工中心部分不允許留有澆口痕跡的平面製品。
它占地面積比臥式注塑機小,但放入模具內的嵌件容易傾斜落下。
這種型式的注塑機宜用於小機。
(4)多模轉盤式注塑機︰它是一種多工位操作的特殊注塑機,其特點是合模裝置採用了轉盤式架構,模具圍繞轉軸轉動。
這種型式的注塑機充分發揮了注射裝置的塑化能力,可以縮短生產週期,提升機器的生產能力,因而特別適合於冷卻定型時間長或因安放嵌件而需要較多輔助時間的大批量塑製品的生產,但因合模系統龐大、複雜,合模裝置的合模力往往較小,故這種注塑機在塑膠鞋底等製品生產中應用較多。
一般注塑機包括注射裝置、合模裝置、液壓系統和電氣控制系統等部分。
注射成型的基本要求是塑化、注射和成型。
塑化是實現和保證成型製品性量的前提,而為滿足成型的要求,注射必須保證有足夠的壓力和速度。
同時,由於注射壓力很高,相應地在模腔中產生很高的壓力(模腔內的平均壓力一般在20~45MPa之間,見表1),因此必須有足夠大的合模力。
由此可見,注射裝置和合模裝置是注塑機的關鍵部件。
1.4注塑機的操作
1.4.1注塑機的動作程式
噴嘴前進→注射→保壓→預塑→倒縮→噴嘴後退→冷卻→開模→頂出→退針→開門→關門→合模→噴嘴前進。
1.4.2注塑機操作項目︰注塑機操作項目包括控制鍵盤操作、電器控制柜操作和液壓系統操作三個方面。
分別進行注射過程動作、加料動作、注射壓力、注射速度、頂出型式的選擇,料筒各段溫度及電流、電壓的監控,注射壓力和背壓壓力的調節等。
1.4.2.1注射過程動作選擇︰
一般注塑機既可手動操作,也可以半自動和全自動操作。
手動操作是在一個生產週期中,每一個動作都是由操作者撥動操作開關而實現的。
一般在試機調模時才選用。
半自動操作時機器可以自動完成一個工作週期的動作,但每一個生產週期完畢後操作者必須拉開安全門,取下工件,再關上安全門,機器方可以繼續下一個週期的生產。
全自動操作時注塑機在完成一個工作週期的動作後,可自動進入下一個工作週期。
在正常的連續工作過程中無須停機進行控制和調整。
但須注意,如需要全自動工作,則
(1)中途不要打開安全門,否則全自動操作中斷;
(2)要及時加料;(3)若選用電眼感應,應注意不要遮閉了電眼。
實際上,在全自動操作中通常也是需要中途臨時停機的,如給機器模具噴射脫模劑等。
正常生產時,一般選用半自動或全自動操作。
操作開始時,應根據生產需要選擇操作模式(手動、半自動或全自動),並相應撥動手動、半自動或全自動開關。
半自動及全自動的工作程式已由線路本身確定好,作業員只需在電柜面上更改速度和壓力的大小、時間的長短、頂針的次數等等,不會因操作者調錯鍵鈕而使工作程式出現混亂。
當一個週期中各個動作未調整妥當之前,應先選擇手動操作,確認每個動作正常之後,再選擇半自動或全自動操作。
1.4.2.2預塑動作選擇
根據預塑加料前後注座是否後退,即噴嘴是否離開模具,注塑機一般設有三種選擇。
(1)固定加料︰預塑前和預塑後噴嘴都始終貼進模具,注座也不移動。
(2)前加料︰噴嘴頂著模具進行預塑加料,預塑完畢,注座後退,噴嘴離開模具。
選擇這種模式的目的是︰預塑時利用模具注射孔抵助噴嘴,避免熔料在背壓較高時從噴嘴流出,預塑後可以避免噴嘴和模具長時間接觸而產生熱量傳遞,影響它們各自溫度的相對穩定。
(3)後加料︰注射完成後,注座後退,噴嘴離開模具然後預塑,預塑完再注座前進。
該動作適用於加工成型溫度特別窄的塑膠,由於噴嘴與模具接觸時間短,避免了熱量的流失,也避免了熔料在噴嘴孔內的凝固。
注射結束、冷卻計時器計時完畢後,預塑動作開始。
螺杆旋轉將塑膠熔融並擠送到螺杆頭前面。
由於螺杆前端的止退環所起的單向閥的作用,熔融塑膠積存在機筒的前端,將螺杆向後迫退。
當螺杆退到預定的位置時(此位置由行程開關確定,控制螺杆後退的距離,實現定量加料),預塑停止,螺杆停止轉動。
緊接著是倒縮動作,倒縮即螺杆作微量的軸向後退,此動作可使聚集在噴嘴處的熔料的壓力得以解除,克服由於機筒內外壓力的不平衡而引起的“留涎”現象。
若不需要倒縮,則應把倒縮停止開關調到適當位置,讓預塑停止開關被壓上的同一時刻,倒縮停止開關也被壓上。
當螺杆作倒縮動作後退到壓上停止開關時,倒縮停止。
接著注座開始後退。
當注座後退至壓上停止開關時,注座停止後退。
若採用固定加料模式,則應注意調整好行程開關的位置。
一般生產多採用固定加料模式以節省注座進退操作時間,加快生產週期。
1.4.2.3注射壓力選擇
注塑機的注射壓力由調壓閥進行調節,在調定壓力的情況下,透過高壓和低壓油路的通斷,控制前後期注射壓力的高低。
普通中型以上的注塑機設定有三種壓力選擇,即高壓、低壓和先高壓後低壓。
高壓注射是由注射油缸通入高壓壓力油來實現。
由於壓力高,塑膠從一開始就在高壓、高速狀態下進入模腔。
高壓注射時塑膠入模迅速,注射油缸壓力表讀數上升很快。
低壓注射是由注射油缸通入低壓壓力油來實現的,注射過程壓力表讀數上升緩慢,塑膠在低壓、低速下進入模腔。
先高壓後低壓是根據塑膠種類和模具的實際要求從時間上來控制通入油缸的壓力油的壓力高低來實現的。
為了滿足不同塑膠要求有不同的注射壓力,也可以採用更換不同直徑的螺杆或柱塞的方法,這樣既滿足了注射壓力,又充分發揮了機器的生產能力。
在大型注塑機中往往具有多段注射壓力和多級注射速度控制功能,這樣更能保證製品的質量和精度。
1.4.2.4注射速度的選擇
一般注塑機控制板上都有快速─慢速旋鈕用來滿足注射速度的要求。
在液壓系統中設有一個大流量油幫浦和一個小流量幫浦同時營運供油。
當油路接通大流量時,注塑機實現快速開合模、快速注射等,當液壓油路只提供小流量時,注塑機各種動作就緩慢進行。