鞍钢金狮集团马来西亚万津区域高炉项目初步设计鞍钢集团电子.docx
《鞍钢金狮集团马来西亚万津区域高炉项目初步设计鞍钢集团电子.docx》由会员分享,可在线阅读,更多相关《鞍钢金狮集团马来西亚万津区域高炉项目初步设计鞍钢集团电子.docx(34页珍藏版)》请在冰豆网上搜索。
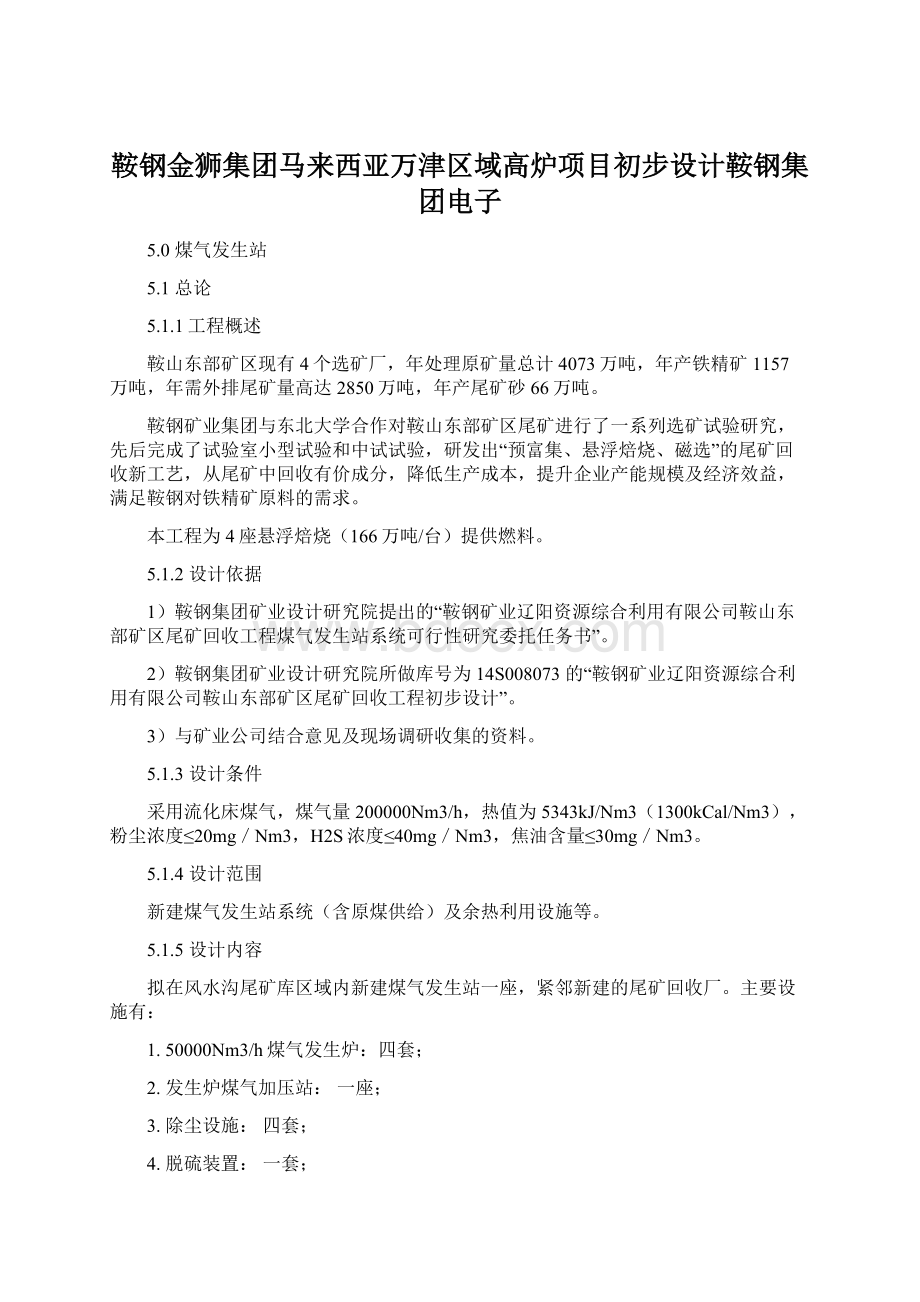
鞍钢金狮集团马来西亚万津区域高炉项目初步设计鞍钢集团电子
5.0煤气发生站
5.1总论
5.1.1工程概述
鞍山东部矿区现有4个选矿厂,年处理原矿量总计4073万吨,年产铁精矿1157万吨,年需外排尾矿量高达2850万吨,年产尾矿砂66万吨。
鞍钢矿业集团与东北大学合作对鞍山东部矿区尾矿进行了一系列选矿试验研究,先后完成了试验室小型试验和中试试验,研发出“预富集、悬浮焙烧、磁选”的尾矿回收新工艺,从尾矿中回收有价成分,降低生产成本,提升企业产能规模及经济效益,满足鞍钢对铁精矿原料的需求。
本工程为4座悬浮焙烧(166万吨/台)提供燃料。
5.1.2设计依据
1)鞍钢集团矿业设计研究院提出的“鞍钢矿业辽阳资源综合利用有限公司鞍山东部矿区尾矿回收工程煤气发生站系统可行性研究委托任务书”。
2)鞍钢集团矿业设计研究院所做库号为14S008073的“鞍钢矿业辽阳资源综合利用有限公司鞍山东部矿区尾矿回收工程初步设计”。
3)与矿业公司结合意见及现场调研收集的资料。
5.1.3设计条件
采用流化床煤气,煤气量200000Nm3/h,热值为5343kJ/Nm3(1300kCal/Nm3),粉尘浓度≤20mg/Nm3,H2S浓度≤40mg/Nm3,焦油含量≤30mg/Nm3。
5.1.4设计范围
新建煤气发生站系统(含原煤供给)及余热利用设施等。
5.1.5设计内容
拟在风水沟尾矿库区域内新建煤气发生站一座,紧邻新建的尾矿回收厂。
主要设施有:
1.50000Nm3/h煤气发生炉:
四套;
2.发生炉煤气加压站:
一座;
3.除尘设施:
四套;
4.脱硫装置:
一套;
5.备煤送煤设施:
一套;
6.变压吸附制氮站:
一座;
7.残碳燃烧设施:
一套;
8.控制楼:
一座。
5.1.6本设计执行的主要标准
《发生炉煤气站设计规范》GB50195-2013;
《工业企业煤气安全规程》GB6222-2005;
《建筑设计防火规范》GB50016-2014;
《爆炸火灾危险环境电力装置设计规范》GB50058-2014;
《供配电系统设计规范》GB50052-2009;
《石油化工企业可燃气体和有毒气体检测报警设计规范》GB50116-2013;
其它有关标准、规范。
5.1.7能源消耗
5.1.7.1总耗电量
装机容量:
8750kW
有功功率:
Pjs=4550kW
无功功率:
Qjs=2202kvar
视在功率:
Sjs=5055kVA
功率因数:
cosΦ=0.90
年耗电量:
0.27×108kWh
5.1.7.2蒸汽消耗
煤气发生炉产蒸汽65t/h,发生炉自身消耗28t/h,外送37t/h;残炭炉产蒸汽50~55t/h。
5.1.7.3氮气消耗
~3400Nm3/h
5.1.8劳动定员
按四班制配备45人(含残炭炉12人)
5.2燃气
5.2.1设计范围
根据东部矿区尾矿悬浮焙烧条件,为悬浮焙烧提供燃料,需新建煤气发生站一座及配套设施,燃气专业设计范围为煤气发生站、煤气冷却、煤气除尘、煤气加压、变压吸附制氮等设计。
1.煤气热值的要求:
5343kJ/Nm3(1300kcal/Nm3)。
2.出界区压力≥25kPa;H2S≤40mg/Nm3;
3.单台煤气炉设计煤气发生量:
50000Nm3/h,共4台套,煤气总量200000Nm3/h;4台炉冷煤气总发热量1.07×109kJ/h。
5.2.2设计内容
本工程新建煤气发生站一座、煤气干法除尘设施四套、煤气加压站一座、变压吸附制氮站一座及连接管道等。
5.2.2.1主要工艺流程
煤气站主要由煤气化炉、气化剂预热器以及辅助系统组成,以空气和蒸汽为气化剂,气化炉工艺系统流程及参数说明如图5-1所示。
煤场中的煤经筛分破碎后由上煤皮带送至发生炉储煤仓,通过给煤机将煤加入气化炉,煤从气化炉炉膛的中下部加入,在气化炉炉膛与底部通入的气化剂发生气化反应,生成煤气。
从气化炉炉顶部排出的煤气与颗粒的气固混合物经第一级高温旋风分离器分离,从第一级高温旋风分离器分离下来的高温物料直接再返回炉膛进行循环,循环物料中未反应的碳在炉膛中与气化剂进一步发生气化反应,以提高气化过程中碳的转化率。
煤气经过空气预热器降温后,经余热锅炉继续降温,同时产生1.3MPa,192℃的饱和蒸汽,部分用作气化剂,部分外供,煤气再经二级旋风除尘器、冷却器和布袋除尘器冷却除尘,然后脱硫、加压供给用户。
图5-1循环流化床煤气化系统工艺流程图
5.2.2.2主要设施
1.煤气发生站
1)煤气发生站规模,工作制度及耗煤量
煤气发生站内安装4套循环流化床气化炉,单台套生产能力50000Nm3/h,年运转7920小时,耗煤量为17.5t/h/台。
2)煤的来源,主要性能及气化指标
循环流化床气化炉主要采用褐煤,入炉煤粒度要求<10mm;干燥无灰基挥发分:
≥30%;灰熔融性:
≥1200℃;对二氧化碳的反应活性:
950℃,α%≥60%;焦渣特性:
≤3。
3)煤气站的工艺流程
由备煤系统送来经筛分破碎后的粉煤,通过传输皮带进入贮煤仓,经过螺旋供煤机从气化炉中下部加入。
在气化炉内粉煤与气化剂经过气化反应生成煤气,生成的煤气和粉尘一同由气化炉进入一级高温旋风分离器,从一级高温旋风分离器分离下来的高温物料直接再返回气化炉进行循环,煤气中未反应的煤尘在此返回气化炉与气化剂进一步发生气化反应,出自一级高温旋风分离器的煤气进入空气预热器,煤气经过空气预热器降温后,经余热锅炉继续降温,通过余热锅炉降温后进入二级旋风除尘器粗除尘后,再经冷却器降温进入煤气干式布袋除尘系统进行精除尘。
4)煤气的主要参数和设备性能简述(按单套)
每套发生炉冷却器出口的煤气流量为50000Nm3/h,煤气压力4~7kPa,煤气温度≤200℃,含尘量≤50g/Nm3干煤气。
每套发生炉主要设备气化炉、一级高温旋风分离器、空气预热器、余热锅炉、二级旋风除尘器、煤气冷却器、炉底排渣系统、输灰系统。
气化炉是气化反应的主要设备,炉壳为钢板,其内衬保温砖和耐火砖。
高温空气和蒸汽的混合气体通过炉体底部进入气化炉,与从气化炉中下部加入的煤粉发生气化反应生成煤气,气化炉的操作温度为900~950℃,干煤气化率~3Nm3/kg。
一级高温旋风分离器分离主要是将随煤气带出的未反应的煤尘回收,直接再返回炉膛进行循环,循环物料中未反应的碳在炉膛中与气化剂进一步发生气化反应,以提高气化过程中碳的转化率。
余热锅炉利用高温煤气的显热,供余热锅炉的软化水经过热交换转化成蒸汽。
余热锅炉出口的煤气温度<220℃;余热锅炉产生蒸汽~15t/h,温度192℃,压力1.3MPa,可供发生炉自用。
低温旋风除尘器用于分离煤气中的粉尘,除尘后的煤气含尘量~50g/Nm3。
炉底排渣系统主要由2台螺旋排渣机组成。
积存于发生炉底部的炉渣,通过经过2支排渣管进入2台螺旋排渣机,使灰渣通过胶带机送到渣场,每套发生炉炉底排渣量<0.4t/h。
余热锅炉、二级旋风除尘器及干法除尘的排灰<2t/h,通过气力输灰方式将灰送至中间灰仓,再通过气力输灰方式送往残炭炉燃烧发电。
5)主要技术经济指标(单套)
入炉煤:
耗煤量17.5t/h;入炉煤粒度<10mm;干燥无灰基挥发分:
≥30%;灰熔融性:
≥1200℃;对二氧化碳的反应活性:
950℃,α%≥60%;焦渣特性:
≤3。
产出煤气:
流量50000Nm3/h,压力4~7kPa,温度≤200℃,热值≥5343kJ/Nm3(1300kcal/Nm3),含尘量~50g/Nm3。
消耗蒸汽:
蒸汽量~7t/h。
产出蒸汽:
蒸汽量~9.25t/h;
软水(除盐除氧):
耗量21.5t/h,;
氮气:
耗量3400Nm3/h,压力0.6MPa,温度:
常温;
粉尘:
炉渣量<0.4t/h,C≤2%;
飞灰量<2t/h,C≤30%。
2.煤气干法除尘系统
每台煤气发生炉炉对应一套干式布袋除尘系统,共4套除尘系统,除尘后的净煤气经煤气冷却器降温冷却。
每2套干式布袋除尘系统并排布置在一个框架内。
1)煤气除尘系统基本参数(单套)
煤气发生量V=50000Nm3/h(正常),V=55000Nm3/h(最大)
煤气压力P=4kPa~7kPa
煤气温度t=~200℃
粗煤气含尘量50g/Nm3
净煤气含尘量20mg/Nm3
2)煤气干法滤袋除尘净化工艺流程
(1)发生炉煤气干式滤袋除尘工艺
设计选用6台DN4200干法滤袋除尘器进行煤气净化,其中五台工作,一台离线低压氮气脉冲清灰。
滤袋清灰可采用压差控制或定时顺序控制,进行低压氮气脉冲清灰。
净化后的净煤气含尘量≤20mg/m3,可满足用户对煤气质量要求。
净煤气温度约~200℃,然后进入煤气冷却塔。
除尘器的粗、净煤气管的阀门采用电动蝶阀,并在阀后(靠近除尘器侧)设置全密封煤气电动插板阀。
电动蝶阀的开、闭按工艺程序由计算机操作。
(2)气力输灰、卸灰系统
输灰采用气力输灰,干法除尘箱体锥形灰仓上设置高、低料位计,控制灰斗中的灰位,当灰斗中的灰达到高料位时,打开插板阀,灰由锥形灰仓落入仓泵,当灰斗中的灰降到低料位时,关闭插板阀,由仓泵通过管道将灰送到中间灰仓,中间灰仓的灰由气力输灰通过仓泵输送至残炭炉。
锥形灰斗设置氮气脉冲气炮以便利卸灰,锥形灰斗中煤气采用低料位进行密封,整个输灰系统以氮气作动力。
全套清灰工艺过程由计算机控制,并设有模拟显示。
3)煤气干法布袋除尘主要设备和设施
(1)粗煤气处理量的确定
单台发生炉煤气发生量50000Nm3/h,按发生炉正常生产的条件,粗煤气可能达到的最高温度200℃和最低压力4.5kPa计算,则进入干法滤袋除尘器系统的工况荒煤气量为~90000m3/h。
(2)干法滤袋除尘器数量、滤料和过滤负荷
每台发生炉,选用6个直径DN4200滤袋除尘器,其中5台工作,则每套干法滤袋除尘器粗煤气处理量为~18000m3/h。
每台除尘器设计过滤面积F=1066m2,由此可见过滤负荷为:
~16.9m3/m2·h,过滤风速:
~0.28m/min。
(3)干法滤袋除尘煤气入口和净煤气出口管径和阀门
根据每台干法除尘器处理的工况煤气量,其粗煤气入口及净煤气出口的管径均为DN800。
为此选用的入、出口电动煤气蝶阀及全密闭电动插板阀的规格为DN800,PN0.1MPa,阀门工作温度t=300℃。
(4)中间灰仓(飞灰)
设计选用1个中间灰仓,4套余热锅炉,低温旋风除尘器及干式布袋除尘器的粉尘全部进入1个中间灰仓。
按24小时卸灰一次,进中间灰仓总贮灰量~180t,灰仓的贮量系数按0.85,灰尘堆密度按600kg/m3计算,灰仓的设计水容积350m3。
(5)布袋除尘器的含尘量检测
为检测每套干式除尘器净煤气含尘量,确定每个除尘器运行状况,知道每个除尘器内滤袋是否有破损,在煤气干式除尘系统总入口管道上安装一台在线煤气含尘量检测仪,在每个除尘器出口均安装一台在线煤气含尘量检测仪,用于检测煤气中的含尘量。
(6)煤气干法除尘系统用氮设施
每个除尘器低压氮气脉冲清灰用氮气量为6.7Nm3/次。
脉冲时间~2min,瞬时用氮气量为200Nm3/h,工作压力0.6MPa;同时设置氮气稳压阀组二套,处理氮气量V=2000Nm3/h。
(7)布袋除尘器的支撑设施
每套发生炉配置5个布袋除尘器箱体,单排布置,每两套发生炉的除尘系统并排支撑在一个公用框架上,整个框架长26.5m,宽21m,每个箱体有四个支撑点,进出口管道的阀门均支撑在此框架上。
3.煤气加压站
从脱硫系统出来的煤气进入煤气加压站加压后输送用户。
1)加压站能力确定
脱硫后煤气量200000Nm3/h,压力~3kPa。
通过加压后送焙烧炉用户使用,要求煤气接点压力≥25kPa,需建煤气加压站一座,加压站能力20000Nm3/h,煤气加压至~29kPa送往焙烧炉使用。
2)加压站主要设备选择
加压站为单层建筑。
其中加压机间占地面积42×12=504m2,轨面标高9m;内设5台离心鼓风机,4工1备,每台离心鼓风机流量取51000Nm3/h,升压26kPa,变频调速运行;为了检修和安装方便,站内还安装一台10t桥式起重机。
煤气加压站进口主管为DN1800,出口主管为DN1800每台风机的进、出口管道均为DN1200;并设置电动蝶阀及电动盲板阀。
4.变压吸附制氮
1)有关参数
本项目氮气主要用户为:
气化炉煤气除尘脉冲清灰及气力输灰、设备及管道置换等。
有关要求如下:
氮气纯度:
>98%
氮气压力:
0.4~0.6MPa
氮气氧含量:
<1%
氮气露点(大气压):
≤-40℃
氮气流量:
~3400Nm3/h
2)工艺选择
根据要求,本工程拟新建氮气站,采用灵活调度的变压吸附制氮工艺。
设1700Nm3/h变压吸附制氮机组2套,纯度>99.0%。
详见工艺流程图。
氮气站厂房占地~36m×16m,一层建筑,高8m。
详见附图。
空气压缩机、冷干机组、变压吸附制氮机、氮气纯化装置等室内安装,氮气储罐、氮气减压阀组等室外布置。
3)变压吸附制氮简要工艺流程图
空气
合格氮气
不合格氮气
流量计
氮气检测装置
氮气缓冲罐
氧氮分离装置
PSA
空气净化
空压机
空气储罐CG
4)变压吸附制氮站工艺流程简述
首先原料压缩空气,压力为≥0.85Pa,经空气缓冲罐,分2路分别进入制氮机组,经高效除油器(三级过滤)除去大部分油、水、尘埃后,进入冷冻式干燥机除去压缩空气中的水分,再进入精密过滤器,后再进入填充颗粒状活性炭的活性炭过滤器,使残油含量至≤0.001ppm,再经氮气储气罐后进入二个填装吸附剂的变压吸附分离系统,即制氮机组。
洁净的压缩空气由吸附塔底端进入,气流经空气扩散器扩散以后,均匀进入吸附塔,进行氧氮吸附分离,然后从出口端流出氮气,进入氮气缓冲罐,这一产氮过程约1分钟,之后经均压和减压(至常压),脱除所吸附的杂质组分(主要为氧气),完成吸附剂的再生。
二个吸附塔交替循环操作,连续送入原料空气,单套连续生产纯度≥99.0%的氮气,产量为1700Nm3/h,氮气输出压力为~0.6MPa(可调),氮气露点为≤-40℃。
5)氮气站工艺设计参数
氮气产量:
~1700Nm3/h,最大~3400Nm3/h(2套)
工作压力:
~0.8MPa
氮气纯度:
>99.0%
露点:
-40℃
6)主要设备工艺参数
(1)压缩及预处理系统技术参数:
①螺杆式空气压缩机,4台,以下为单机参数
型号:
MH250-8
排气量:
45m³/min
排气压力:
~0.8MPa
电源:
3Φ380V/50Hz
冷却方式:
(水冷)
功率:
250kW/台
②压缩空气缓冲罐(前级),2台
容积:
10m3
介质:
空气
工作压力:
1.0MPa
③压缩空气缓冲罐(后级),2台
容积:
10m3
介质:
空气
工作压力:
1.0MPa
④冷冻式干燥机,2台
额定处理量:
100m3/min
冷却方式:
水冷
功率:
45kW
进气温度:
标准80℃以下
露点温度:
2℃~10℃
环境温度:
<40℃
干燥机控制方式:
接触器-按钮控制
干燥器电源:
380V/50Hz/15kW
⑤HA级油水分离器,2台(过滤器组)
额定处理量:
110m3/min
最大工作压力:
1.0MPa
压力损失:
<0.015MPa
过滤精度:
0.01μm
滤芯寿命:
8000h
滤芯材质:
不锈钢,深层短阵混合纤维介质
最大残留油份:
0.01ppm
自动排水器:
压差表:
(2)1700Nm3/h变压吸附空分制氮装置,2套,单机参数如下:
氮气流量:
1700Nm3/h
出口压力:
~0.6MPa
重量:
6000kg
氮气纯度:
≥99.0%(无氧含量)
氮气露点:
≤-40℃
功率:
1kW
(3)氮气缓冲罐,1台
容积:
10m3
介质:
氮气
工作压力:
1.0MPa
(4)氮气储罐,1台
容积:
50m3
介质:
氮气
工作压力:
1.0MPa
7)自动控制系统
全自动PLC控制,无人值守自动运行。
控制系统设置在煤制气控制室统一管理。
8)氮气系统主要能耗
序号
设备名称
单台功率kW
数量
循环水Nm3/h
总功率kW
总水量Nm3/h
1
空压机
250
4
25
1000
100
2
冷干机
15
2
10
30
20
3
制氮机
0
2
1
合计
1031
120
5.2.2.3主要设备
1.煤气发生炉
煤气流量:
50000Nm3/h
煤气压力:
4~7kPa
煤气温度:
≤200℃
煤气热值:
≥5.46MJ/Nm3(1300kCal/Nm3)
数量:
4套
2.干式布袋除尘装置
除尘能力:
50000~55000Nm3/h
入口压力:
≥4.5kPa
入口含尘量:
50g/Nm3
出口含尘量:
20mg/Nm3
阻力损失:
0.5kPa
布袋除尘箱体:
直径DN4200
进、出口管道直径:
DN800
每套除尘器箱体数量:
6台
干式布袋除尘系统数量:
4套
3.煤气鼓风机
煤气流量:
51000Nm3/h
煤气升压:
26kPa
数量:
4台
5.3总图
5.3.1总平面布置
5.3.1.1设计内容
储煤场、制气炉、残炭炉、煤气净化、煤气加压站、余压发电、制氮系统、配电及主控室。
5.3.1.2平面布置
根据总体规划布置,煤气制气炉系统布置在整个规划区域的南侧,考虑汽车运输的需要储煤场布置在该区域西南侧,储煤场采用两跨布置,采用人工及机械混合卸车方式,中间设置地下受料槽及输出带式输送机通廊,周边设置汽车运输通道;新建制气炉共四套50000m3/h煤制气,每两套为一组,布置在煤场的东南侧,干法除尘布置在其右侧;为了减少物料输送距离,残炭炉布置在制气炉的西北侧;煤气净化及煤气加压站布置在制气炉东南侧;余压发电布置在煤气净化区域的西北侧;制氮系统布置在制气炉东南侧;配电及主控室布置在煤场西北侧,整个区域用地10.31万m2,详见平面布置图。
5.3.1.3竖向设计
新建煤制气工程位于山坡上,该区域西南侧低,东北侧较高,地面标高介于150m~200m之间。
根据总体规划考虑,该区域设计平土标高为180m。
厂区雨排水通过道路两侧明沟收集排入整个厂区排水系统中,最终排至厂区外东南侧现有河流中。
5.3.1.4运输
新建四套50000m3/h煤制气所用褐煤经由鞍钢灵山站、鞍钢环市铁路运至调军台热电厂卸煤车间(运距约16km)后,经汽车倒运至新建煤气发生炉煤场(运距约15km),全年运量约为55万吨。
煤场到发生炉采用胶带运输,发生炉煤灰通过管道输送至残炭炉,炉渣每年1200吨,全部由汽车外运。
厂区采用沥青混凝土道路,主干道宽7.0m,次干道宽4.0m,总铺砌面积3000m2(不含区域外部共用主干道)。
5.3.1.5外部管线
新建煤制气区域所需水、电等介质均由矿山设计院统一考虑送入红线区域。
5.3.2.6绿化及消防
为了美化环境、减少污染,使新建工厂成为花园式工厂,在建筑物四周空闲地带及道路两侧种植一些花卉、草坪和树木等等。
绿化系数为15%,绿化面积15465m2。
为了满足消防的要求,在厂区四周设消防通道,在通道范围内设计环状消防水管网,各建构、筑物之间间距满足防火要求。
新设计的各种架空管线与消防通道交叉其垂直净空不小于5m,道路交叉口曲线半径不小于9.0m,满足消防通道安全行车要求。
鞍山东部矿区尾矿回收工程厂区距齐大山镇消防站约5km,厂区有公路通往齐大山镇消防站,5分钟内消防队可以到回收厂,所以厂区不考虑新建消防站。
5.3.2.7需要说明的问题
1.运煤所需的运输车辆由外协解决,本设计未予考虑。
2.厂区平土、围墙、外部通道及区域外公用道路由矿山院统一考虑。
3.发生炉产生的炉渣需矿山设计院在总体规划中考虑堆放场地。
4.厂区南侧外部联络通道,由于坡度较大,距离长,冬季遇道路结冰时,需考虑运输车辆能否通行。
5.3.2.8总图运输主要技术经济指标
总图运输主要技术经济指标
序号
项目名称
单位
数量
备注
1
占地面积
㎡
103100
2
新建道路
㎡
3000
3
新建路缘石
m
1200
4
新建排水沟
m
1100
5
绿化用地系数
%
15
6
绿地面积
㎡
15465
5.4热力
5.4.1飞灰残碳炉
5.4.1.1残碳燃烧工艺
由于气化炉产生的飞灰还含有大约30%碳,这部分飞灰如不加以利用会造成能源的浪费。
本工程新建2台残碳燃烧炉对飞灰进一步燃烧,产生的蒸汽送入新建的汽轮机进行发电。
气化产生的飞灰经气体输送至中间储仓,作为气化系统和残炭燃烧系统的中间储灰仓,储存在中间仓里的飞灰经仓泵气体输送至残炭炉的煤仓,由螺旋给料机送入残炭炉炉膛,飞灰在炉膛内燃烧后带出的颗粒经分离器返回炉膛继续二次燃烧,飞灰燃烧产生的热量被锅炉吸收产生蒸汽,烟气经脱硫、脱硝、除尘后有烟筒排入大气。
图5-2残碳燃烧工艺(未标示出脱硫脱硝工艺)
5.4.1.2残碳炉主要技术经济指标(2台合计)
序号
项目
单位
数量
备注
1
飞灰含碳
%
~30
2
飞灰量
吨/小时
~8
3
燃烧后渣含碳量
%
<2.5
4
燃烧后灰渣量
吨/小时
~7.8
6
产生蒸汽温度
℃
350
7
蒸汽产量
吨/小时
50-55
8
蒸汽压力
MPa
1.6
5.4.1.3烟气处理工艺:
根据《锅炉大气污染物排放标准》GB13271-2014规定,锅炉烟气排放标准如下,二氧化硫不大于300mg/m3;氮氧化物不高于300mg/m3;烟尘颗粒物不大于50mg/m3。
为符合环保指标,对烟气进行脱硫、脱硝、除尘处理。
1.脱硝
1)锅炉烟气参数
(1)烟气量:
30000-40000Nm3/h(单台);
(2)烟气含氮量约为:
500mg/Nm3。
2)脱硝工艺描述
本项目选用SNCR脱硝技术方案,采用尿素溶液作为还原剂。
选取最佳的温度窗口,将稀释至10%以下的尿素溶液通过喷枪雾化后喷至锅炉内进行反应,良好的雾化效果能够保证足够的穿透深度和充分的覆盖面。
工程主要组成部分:
(1)尿素溶液储存及输送系统
通过尿素溶解罐将外购的袋装尿素溶解,然后通过泵输送至尿素存储罐中,综合考虑制作运输成本,尿素溶液储罐用于存储2台锅炉在满负荷的条件下运行不少于7天的存储量。
储罐上设有液位检测系统来控制储罐内的尿素溶液总量。
在尿素制备存储区设置一个现场操作箱,用于实现对各类泵的就地启动与检修。
①尿素溶液储罐,容积20m3,材质为304不锈钢,规格Φ3×3。
②尿素溶液输送泵3台(两用一备),离心泵,不锈钢材质。
③尿素溶解罐,容积为5m3,材质为304不锈钢,规格Φ2×1.5。
锅炉设置3台尿素溶液输送泵,两用一备,在DCS系统的控制下实现远程操控,也可以通过操作箱就地控制;计量后的尿素溶液通过经过静态混