高炉自动控制系统技术方案.docx
《高炉自动控制系统技术方案.docx》由会员分享,可在线阅读,更多相关《高炉自动控制系统技术方案.docx(20页珍藏版)》请在冰豆网上搜索。
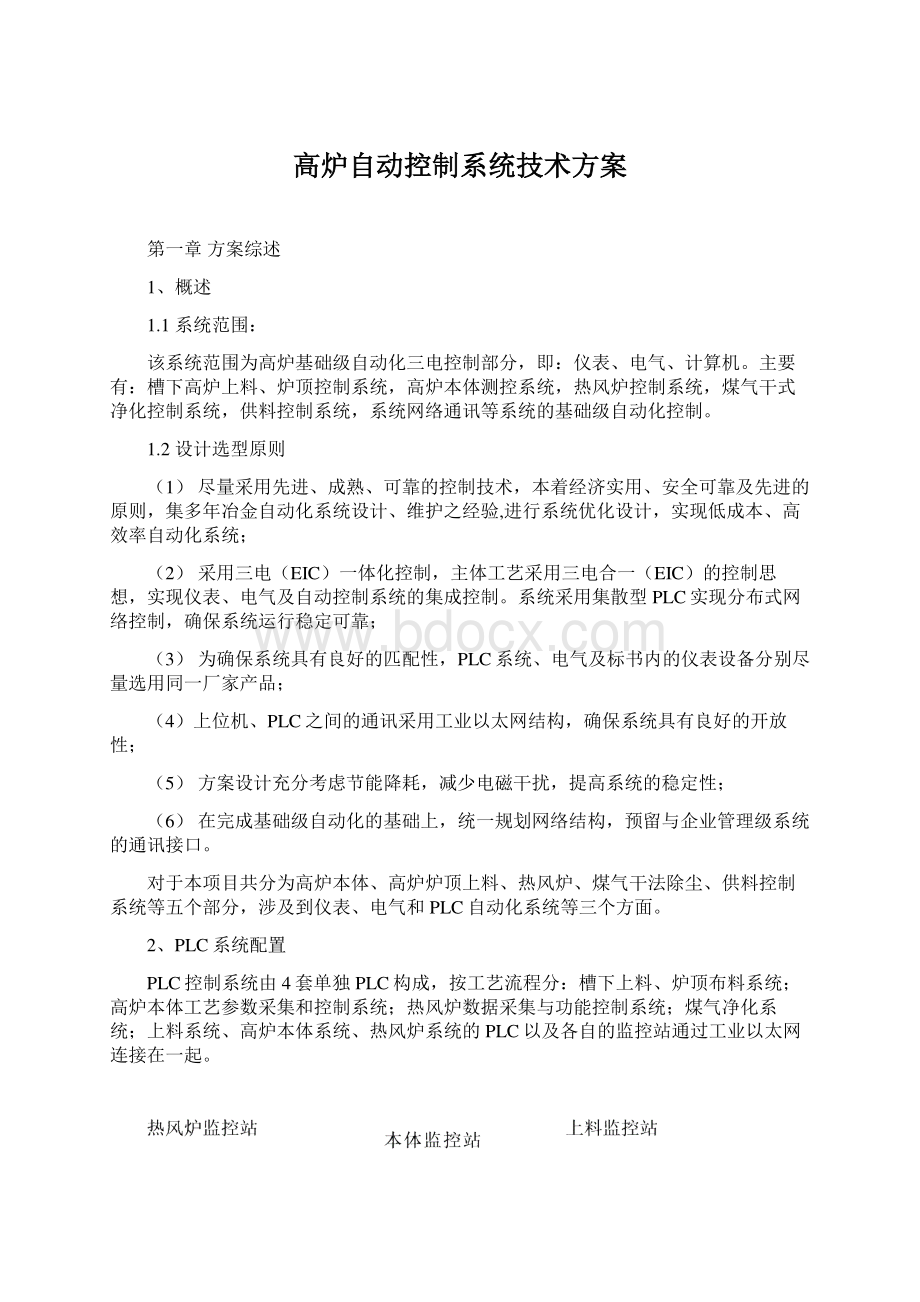
高炉自动控制系统技术方案高炉自动控制系统技术方案第一章方案综述1、概述1.1系统范围:
该系统范围为高炉基础级自动化三电控制部分,即:
仪表、电气、计算机。
主要有:
槽下高炉上料、炉顶控制系统,高炉本体测控系统,热风炉控制系统,煤气干式净化控制系统,供料控制系统,系统网络通讯等系统的基础级自动化控制。
1.2设计选型原则
(1)尽量采用先进、成熟、可靠的控制技术,本着经济实用、安全可靠及先进的原则,集多年冶金自动化系统设计、维护之经验,进行系统优化设计,实现低成本、高效率自动化系统;
(2)采用三电(EIC)一体化控制,主体工艺采用三电合一(EIC)的控制思想,实现仪表、电气及自动控制系统的集成控制。
系统采用集散型PLC实现分布式网络控制,确保系统运行稳定可靠;(3)为确保系统具有良好的匹配性,PLC系统、电气及标书内的仪表设备分别尽量选用同一厂家产品;(4)上位机、PLC之间的通讯采用工业以太网结构,确保系统具有良好的开放性;(5)方案设计充分考虑节能降耗,减少电磁干扰,提高系统的稳定性;(6)在完成基础级自动化的基础上,统一规划网络结构,预留与企业管理级系统的通讯接口。
对于本项目共分为高炉本体、高炉炉顶上料、热风炉、煤气干法除尘、供料控制系统等五个部分,涉及到仪表、电气和PLC自动化系统等三个方面。
2、PLC系统配置PLC控制系统由4套单独PLC构成,按工艺流程分:
槽下上料、炉顶布料系统;高炉本体工艺参数采集和控制系统;热风炉数据采集与功能控制系统;煤气净化系统;上料系统、高炉本体系统、热风炉系统的PLC以及各自的监控站通过工业以太网连接在一起。
工业以太网组网结构图系统采用西门子S7-400S7-300系列PLC,编程软件采用STEP7V5.3,监控软件采用WINCC6.0中文版。
PLC与上位机间采用以太网通讯模式,PLC与PLC之间同样采用以太网通讯模式总线结构。
在高炉上料值班室、高炉工长值班室之间采用双绞线以太网,高炉工长值班室与热风炉值班室、除尘值班室通过光纤连接,采用Dlink工业光纤口以太网交换机,高炉上料值班、热风炉值班室设置工业以太网交换机。
PLC系统I/O余量大于10%。
HMI操作配备7台操作站。
上料控制室安装2台上位监控机;高炉本体2台上位监控机放于工长值班室内;热风炉2台上位机放置于热风炉控制室内;煤气净化系统上位机1台放置于煤气净化控制室。
上位机采用研华工控机,21吋飞利浦纯平显示器,均采用当前流行配置。
针对现场的实际情况,上料值班室安置1个仪表柜,主要是10台称量斗和两个中间仓的重量变送;还设有上料远程PLC柜和继电器柜组成分布式系统,通过Profibus与炉长室的上料本地PLC柜通讯。
炉长室设有上料本地PLC柜,负责上料和炉顶设备的控制;还设有本体PLC柜和信号隔离柜负责高炉本体的监控;HMI操作包括两台上料系统操作站和两台本体监控用操作站;HMI与PLC之间通过以太网通讯。
在热风炉值班室有热风炉PLC柜及热风炉隔离柜,负责热风炉的控制;还有除尘本地PLC柜和除尘隔离柜,负责除尘系统的控制;HMI操作包括两台热风炉系统操作站和一台除尘系统监控操作站。
在除尘配电室设有除尘远程PLC柜和继电器柜,通过Profibus与除尘本地PLC柜通讯,组成分布式系统。
3、电气部分电气部分包括高炉本体、高炉矿槽、高炉炉顶的供配电。
主要电气元件选用国内外著名公司产品。
其中,主卷扬变频器采用西门子6SE70系列变频器,功率400KW。
4、西门子系统简介4.1硬件性能SIEMENS自动化系统具有强大的信号处理和逻辑运算能力,具有模板化、可扩充的体系结构,适用于工业实时控制和制造过程控制。
高性能:
(1)高吞吐量,使得更多的程序运行时间更短。
(2)附加的数学协处理器能满足更多的控制要求,提供更多的可能性及更高的产品质量。
高完备性:
(1)适于苛刻的工业环境,例如复杂的电气设备及环境温度。
(2)SIMENS符合UL.CSA和工厂等级FM1,Div2的要求,给用户提供一个安全的选择。
(3)可选的冗余电源、电缆,为重要场合提供安全保障。
(4)SIEMENS专利的段调度技术使得I/O更新和程序扫描同步进行,从而实现安全,可预测的控制。
方便使用:
(1)SIEMENS系统中不使用DIP开关,全部地址用转换开关设定,SIEMENS控制器提供了所有下装模块的配置特征。
(2)十进制地址方式排除了在编程,检查系统时记忆转换的繁琐过程。
(3)所有的I/O模板使用同样的I/O接线端子,这样不必考虑板子与接线端子的对应关系。
(4)运行时每块模板都有正常信息显示,使用户维护更容易。
(5)扩展总线的LED组,能够减少诊断故障时间。
(6)所有模板均可插入底板的任一槽中,对于除了电源模板外的所有模板,没有对所在槽位的配置限制。
(7)所有模板均有LED显示灯指示操作状态。
(8)允许模板带电插拔。
(9)用于现场接线的端子排插于模板前部。
4.2WINCC功能结构4.2.1基本功能WINCC自动化软件为操作人员和贯穿整个管理的应用软件提供实时的数据。
实时数据的处理是如何更加有效的利用资源、人力,最终提高自动化程度的关键。
WINCC最基本的功能就是数据采集和数据管理。
(1)数据采集:
WINCC软件采集数据时无需特定的硬件,它可以通过高性能、高速I/O驱动程序与硬件通讯。
(2)数据管理:
一旦接收到数据,应用程序对数据进行处理与引导。
(3)数据完整性:
数据采集与数据管理为WINCC执行的所有自动化任务提供了基础。
数据的完整性是WINCC软件的核心,并且是WINCC开发体系的固有部分。
4.2.2人机界面及监控与数据采集功能
(1)显示:
WINCC强大的数字、文本、图像格式提供了最友善的人机界面。
(2)监控:
操作人员直接从计算机改变设定值和其它关键值的功能与监视数据显示相配合。
(3)报警:
WINCC以多种途径(包括多媒体)将得到的报警通知操作人员。
(4)控制:
WINCC软件包括连续控制、批处理控制、统计控制功能,利用算法调整过程量。
留有用户程序接口,方便诸如优化、模糊控制的嵌入。
4.2.3报表功能及数据存档系统中能够以用户指定的速率采样数据并将数据存储在数据文件中。
任何时候,都能从数据文件中检索数据,创建历史数据的趋势显示。
已存储的数据是正确处理和优化过程的强大工具。
报表:
WINCC支持操作人员通过工业标准数据交换协议如DDE和ODBCSQL双向访问WINCC数据。
操作人员能够用如Microsoft的Excel电子表格建详细报表。
4.2.4开放式结构功能WINCC提供了用VB、C、C+和VC等一系列语言对系统中任何数据点、报警及历史数据进行读写访问功能。
系统的开放式结构提供给现场工程师丰富的工具,使他们编写应用软件解决特定的自控需求。
开放式的结构也允许工程师编写应用程序为操作管理软件和现场其它数据平台提供重要的实时数据。
第二章高炉本体方案1、PLC系统硬件高炉本体部分采用S7-400系列控制器412-2DP,以太网通讯模式。
高炉本体主要是各种参数的检测报警以及部分设备的控制。
系统配置如下表:
工长室PLC系统材料明细序号名称型号产地单位数量备注1AA1,AA2进线柜GGDII济南伊斯达台22AA3配电柜GGDII济南伊斯达台13工长室PLC柜GGDII济南伊斯达台14工长室隔离柜GGDII济南伊斯达台15打印机ML1610三星台16研华工控机IPC6102.8G512M内存台湾台27显示器21寸纯平飞利浦台28交换机(带光口)DLINK16口台19网线米35010光纤4芯多模米20011水晶头个5012光纤接头个213UPS电源1KVA易事特台12、控制功能2.1实现温度、流量、冷却水压力等检测数据的报警功能例如:
温度报警,在检测超过某一设定值时,进行判断并进行报警功能,如在监控画面闪烁或变色。
炉身温度报警示意图:
2.2实现炉顶压力的手动/自动调节功能2.3监控画面功能监控画面包括整个高炉本体工艺流程的形象描绘,画面和谐统一,操作简单安全可靠。
监控画面包括所有模拟量输入数字量输入信号的显示和所有模拟量输出数字量输出的操作。
对于数据显示都有根据工艺要求的上下限报警显示,对于调节系统都有根据实际请况的手自动切换。
对一些重要数据还有报表打印功能。
对于冷风流量、冷风压力、热风温度、炉顶压力等参数都有实时趋势和历史趋势显示。
第三章高炉上料方案1、PLC系统配置及设备高炉上料部分采用S7-400系列控制器414-2DP和ET200组成分布式控制系统。
设两台上位机互为备用。
高炉上料系统包括了槽下备料、卷扬上料、炉顶布料等三部分的逻辑顺序控制,并且和工长值班室通过以太网相连,并进行直接的数据交换。
量斗称重设有称重仪表柜,并具有远程复位功能。
上料系统材料明细序号名称型号产地单位数量备注1AA1,AA2进线柜GGDII济南伊斯达台22AA3配电柜GGDII济南伊斯达台13皮带、三通分料器柜GGDII济南伊斯达台14探尺柜GGDII济南伊斯达台15振筛、给料机柜GGDII济南伊斯达台16PLC柜GGDII济南伊斯达台27JC继电器柜GGDII济南伊斯达台18SF炉顶伺服柜GGDII济南伊斯达台19变频柜GGDII济南伊斯达台210QH切换柜GGDII济南伊斯达台111电阻柜GGDII济南伊斯达台112UPS电源2KVA易事特台113研华工控机IPC6102.8G512M内存台湾台214显示器21寸纯平飞利浦台215交换机(带光口)DLINK16口台116Profibus电缆6XV1830-0EH10西门子米30017数字输入模块6ES7321-1BH02-0AA0西门子块1供料18数字输入模块6ES7321-1BL00-0AA0西门子块1供料19数字输出模块6ES7322-1BH01-0AA0西门子块1供料20探尺深度传感器TCY-2济南伊斯达台2探尺深度21压力传感器3吨余姚只30称量仪表22压力传感器6吨余姚只6称量仪表23重量变送器PLY300济南伊斯达台12称量仪表24接线盒余姚台12称量仪表25仪表柜GGDII济南伊斯达台1称量仪表26接近开关欧姆龙个30*2、控制功能2.1槽下配料功能槽下控制能够根据料单内容实现振筛、给料机、斗闸门、翻板、皮带等的完全自动化逻辑控制。
并根据槽下料单的填写内容实现自动称量补偿等计算累计功能:
振筛的手/自动启停斗闸门的手/自动开关皮带的手/自动启停翻板的自动定位中间斗的自动排料称重远程复位2.1.1料单设定:
周期设定:
料单设A、B、C、D、E、F、G、H等八种料批,根据需要可设其中的一种或几种,故周期设定中只允许填写A、B、C、D、E、F、G、H对应的代号1、2、3、4、5、6、7、8,第一位不能是空格,连续书写,不能超过10个字母,程序遇0或执行完10周期后自动返回周期1执行。
料单修改标志设定:
料单上有一“料单传送”标志,此标志为1,说明修改过料单,当前放料料批执行完时,重新按新设定的料单开始控制。
料批内料型设定:
A、B、C、D、E、F、G、H等八种料批,每个批次均设1-4个车次,相应位置填入料型组合代码,而每一种料型组合代码又对应着所选料仓代号组合。
各称量斗设定值以千克(KG)为单位,填入各斗的设定值。
焦炭设定为干焦值,在画面中进行焦炭水份设定,程序自动转换成湿焦值。
附加焦设定:
在需要附加焦的放料批次中减小放料车次,直到附加焦执行完。
称量及补偿的计算公式如下:
本次称量值=本次实际称量值*30%+上次称量值*70%本次余振量=本次满值-本次控制值下次余振量=70%*上次提前量+30%*本次提前量本次入炉量=本次满值-本次空值本次误差值=本次设定值-本次入炉量累计误差=累计误差+本次误差下次设定值=设定值+本次误差下次控制值=下次设定值-下次余振量2.12振筛的自动启停控制根据料单的设定情况,被选择的仓在设定好后,检测下面的称量斗闸门已经关好,并且称量未满,则启动振筛振料,待称量斗发出满信号,则停止振动给料。
振动筛或给料机启动T秒后,还未发出斗“满”信号,就发出上卡料报警信号。
2.13称量斗的称量和排料控制当排料程序发出后,矿石称量斗闸门开,料排出。
当称量值为控制值(初始时为设定值的95%)的5%时,发出料空信号并关闭闸门,当闸门关好并称空好后,振动筛或给料机开始启动。
称量值到控制值(经补正)时,振动筛或给料机停机,进行满称量。
若达110%控制值(经补正)时发出报警信号。
根据预先选定的装料程序,矿石中间称量斗一“空”且闸门关好,槽下翻板翻到位,矿石皮带机启动后,开始排料。
排料顺序:
球团、杂矿单装时按料单内所填仓号的先后顺序进行排料(矿石称量斗排料最多不同时超过五个)。
当前一个称量斗闸门开启,发出空信号后,发出下一个斗排料指令。
排料斗的闸门开到位延时T秒后,还未发出斗“空”信号,则发出下卡料报警信号。
2.14翻板皮带中间斗的运转控制根据程序计数判断,应该备某侧中间斗,则翻板动作翻到位,依据排料的仓的位置,左或右皮带机开始动作,继而选中的称量斗开始排料,当该侧称量斗已经排完后,该侧皮带机延时停。
当相应的称量斗称空设定好后,对应的碎矿或碎焦皮带开始动作,对相应的称量斗都已经称满后,碎矿或碎焦皮带延时停。
排料是由放料车数计数的奇偶性来选择放料次序的。
2.2主卷上料功能根据和槽下、炉顶程序无缝链接实现对料车的上行下行的自动控制,并能够进行完全手动操作,能够对松绳、过卷等故障作出紧急反应,保障料车的安全运行。
2.2.1机旁/计算机操作根据调试和安全的需要,设置主卷扬操作室机旁操作箱,用之进行机旁调试和系统恢复。
在上料HMI操作站上设置主卷扬系统的操作,主要是系统的紧急停车制动等操作和一般故障操作恢复。
计算机操作也包括手动/自动操作,手动操作料车上行下行和根据程序逻辑的自动化化运行。
机旁/计算机操作均可以双向点动运行。
2.2.2料车的行走曲线我们根据现场的实际情况和要求,给出1个加速点和2个减速点,采用S形加速斜坡和减速斜坡,停车采取紧急抱闸制动。
变频器配备大功率制动单元和制动电阻。
速度点的设定和匀速段速度的设定根据现场实际要求设定。
一般过程是料车在底,接到行走命令开始按预定斜坡一次加速,在到达斜桥的某位置后,开始进行二次加速,二次加速完毕开始匀速段运行,料车到达一次减速点后开始按预定减速斜坡进行一次减速,在到达二次减速点后进行二次减速,到达停车点后,立即制动停车。
2.2.3系统故障保护对于变频器的保护,配备了进线电抗和出线电抗,防止变频器遭到电流冲击。
对于电机有线路过流保护和变频器过流跳闸设置。
对于超极限、松绳等保护主要通过硬线回路来实现,通过和接触器连锁执行。
对于系统的恢复一般通过机旁电动操作来实现,与主电源连锁也通过机旁操作来解除。
2.2.4炉顶布料能对炉顶设备包括受料斗挡料阀、上密封阀、下密封阀、料流阀、布料溜槽、探尺等进行完全控制,并根据操作人员填写的炉顶料单自动开关定位,实现布料的自动化顺序控制:
能够实现探尺的自动提放和料面跟踪实现受料斗自动装料、料罐自动装料能够根据炉顶料单实现自动多环布料和定点布料2.2.5探尺运转控制左右探尺的操作方式分为机旁操作和计算机操作,计算机操作又分为自动和手动操作。
探尺的工作制度分为左尺为准、右尺为准、双尺为准等三种。
以单尺为准时,左尺右尺探测料面,当选定该尺到达料线后,认为已经到达料线,应该提尺布料了;以双尺为准时,当左右双尺都探到料线时才能提尺布料。
探尺采用两台西门子6RA70全数字直流调速装置进行控制,位置信号采用编码器。
当一罐料布完,探尺开始下探,当探尺到料线后,如果料罐已经满,则提尺布料,如果料罐未满,则继续下探,如果探到下限则自动提尺。
当料罐已满,探尺到料线提尺,料罐开始布料,探尺保持在上位。
当料罐布完料,开始下一个循环。
2.2.6料罐自动装料过程根据料罐的工作状态,我们给料罐定义了1、2、3、4四个状态:
正在装、料罐满、正在布、料罐空。
我们根据料罐这四个状态来进行程序判断和执行。
料罐已经空,上密封阀、下密封阀、均压阀等都已经关到位,料罐处于状态4;此时,如果受料斗已经满,则料罐应该开始装料,首先放散阀打开,放散好后。
进入状态1;开上密封封阀,上密封阀开到位,关放散阀到位,开挡料阀,挡料阀开到位,延时20-30秒,关上挡料阀,挡料阀关到位,关下密封阀,下密封阀关到位,料罐进入状态2;当料罐满,开均压阀,均压好后,进入状态3,调整角到位、角到位、角料头来,开始开下密封阀到位,关均压阀到位。
当料空信号来,调整角到最大位置、角料头设定自动布进60度,料流阀关闭,关下密封阀到位,进入状态4。
2.2.7炉顶料单根据槽下料单的8个批次的设定,同时设定该批次的布料代号,针对个批次设定其布料代号1-8,每个布料代号对应每个批次的布料参数检索。
当某批次的料装进料罐后,同样传入该批次的布料代号,并由此检索出溜槽的倾动角度设定角、角。
其中角每批次1个设定角度,角每批次6个设定角度,并给出每个角的布料圈数。
2.3监控画面功能监控画面包括整个高炉上料工艺流程的形象描绘,画面和谐统一,操作简单安全可亲。
监控画面包括槽下料单、炉顶料单的填写和槽下、炉顶各设备的操作和各设备的状态显示。
对于各设备一般都有手自动选择操作和重点设备的确认操作。
画面还包括探尺实时趋势和历史趋势的显示和根据工艺要求的报表功能。
3、电气和仪表部分高炉上料部分电气,包括高炉矿槽、炉顶部分的供配电以及检修照明等设备的配置。
上料部分的仪表包括12台称量传感器以及他们的显示变送。
第四章除尘方案1、PLC系统配置及设备干法除尘系统同样采用西门子S7300控制器和ET200组成分布式系统,一台上位监控机,与高炉本体、上料、热风炉等系统通过光纤以太网进行数据通讯。
布袋除尘PLC系统材料明细序号名称型号产地单位数量备注1公用配电柜GGDII济南伊斯达台12上电动盲板阀配电柜GGDII济南伊斯达台13下电动盲板阀配电柜GGDII济南伊斯达台14振动机、叶轮给料机配电柜GGDII济南伊斯达台15除尘系统PLC柜GGDII济南伊斯达台26除尘系统隔离柜GGDII济南伊斯达台17除尘系统继电器柜GGDII济南伊斯达台18PROFIBUS电缆6XV1830-0EH10西门子米3009研华工控机IPC6102.8G512M内存台湾台110显示器21寸纯平飞利浦台111UPS电源1KVA易事特台12、控制功能干法除尘系统主要实现各除尘器的离线手/自动清灰功能和卸灰功能。
并保持炉顶压力的稳定安全。
在除尘系统出现故障的时候,能够紧急打开旁路,使高炉不至于休风减风而影响生产。
各设备均设置机旁操作箱,能执行机旁/计算机手自动操作。
(1)通过控制除尘器前后密封蝶阀和盲板阀来控制高炉煤气是否通过干法除尘设备。
(2)通过控制各除尘器的进口、出口液动盲板阀的动作来控制除尘器的在线和离线清灰。
并根据工艺选择实现定时或定压差自动清灰模式。
(3)对除灰和卸灰系统的控制,可以实现手动和自动卸灰。
2.1定时清灰根据使用情况,从监控画面设定系统清灰的时间间隔,当设定时间到时,程序将清灰指令发出,并给出循环指令计数1-10,对应10个除尘器,根据计数判断动作的除尘器,并按次序进行。
2.2定压差清灰根据工艺要求,当入口煤气与除尘后净煤气的压差达到4KPa时,开始循环清灰,传递清灰计数指令。
通过控制卸灰球阀等设备来实现系统的自动放灰卸灰功能。
2.3监控画面监控画面实现整个工艺流程在线设备的状态监控,并实现某些重要参数的报警,通过参数设定能够实现除尘系统的在线离线的自动清灰方式,同时能够对在线设备进行计算机的手动操作。
对一些数据有实时和历史的趋势,有故障统计和报表打印功能。
第五章热风炉方案1、PLC系统配置及设备热风炉自动化控制系统采用西门子S300控制器,上位机与控制器间采用以太网模式,热风炉主控室通过以太网实现与高炉工长值班室及其他控制系统的通讯。
热风炉PLC系统材料明细序号名称型号产地单位数量备注1AA1,AA2进线柜GGDII济南伊斯达台22AA3配电柜GGDII济南伊斯达台13公用配电柜GGDII济南伊斯达台14PLC柜GGDII济南伊斯达台15隔离柜GGDII济南伊斯达台16UPS电源1KVA易事特台17研华工控机IPC6102.8G512M内存台湾台18显示器21寸纯平飞利浦台12、控制功能热风炉PLC控制系统主要是实现三座热风炉的燃烧、焖炉、送风等三个状态的转换,以及实现三座热风炉状态转换时的相互连锁。
保障热风炉的送风温度和风量,促进高炉炼铁的顺利进行。
2.1阀门内容及连锁热风炉的工作状态有燃烧、焖炉、送风三种状态,状态的转换靠控制各阀门的动作,其受控阀门及三种状态对应的阀门状态如下图所示:
受控阀门内容及状态表(K-开,G-关)序号设备名称燃烧送风焖炉传动及控制方式1第一煤气阀KGG液压传动,参加联锁2第二煤气阀KGG液压传动,参加联锁3空气阀KGG液压传动,参加联锁4第一烟道阀KGG液压传动,参加联锁5第二烟道阀KGG液压传动,参加联锁6废气阀K/GGG液压传动,参加联锁7冷风均压阀GK/GG液压传动,参加联锁8冷风阀GKG液压传动,参加联锁9热风阀GKG液压传动,参加联锁10氮气阀K/GGG电动,参加联锁11煤气放散阀GKK电动,参加联锁2.2工作制度热风炉有以下三种工作制:
两烧一送,两送一烧,一烧一送,详见下图。
两烧一送工作制炉别工作状态1#2#3#两送一烧工作制炉别工作状态1#2#3#一送一烧工作制炉别工作状态1#2#3#-送风-燃烧空格-焖炉两烧一送及两送一烧工作制为热风炉正常工作制,这种工作制换炉次数少,从而风量及风温稳定;一烧一送工作制为非正常工作制,换炉频繁,容易造成风量及风温波动,实际生产中应尽量采用正常工作制。
无论是正常工作制或非正常工作制在发出送风换炉时,操作上必须先将燃烧的热风炉转送风后,才能将送风的热风炉转燃烧。
注送风与燃烧之间的转换均须先转焖炉。
一般采取两烧一送的模式。
2.3综合功能实现三座热风炉的相互连锁,促进高炉的稳定生产,主要是冷风连锁功能。
并通过工艺参数的设定,保障热风炉燃烧制度的实现。
实现热风炉状态转换的阀门连锁和自动开关,达到能够实现计算机手动/半自动换炉的目的,在设备条件、工艺调件达到要求的时候能够实现自动换炉。
对煤气总管压力调节阀、空气总管压力调节阀、煤气支管调节阀、空气支管调节阀能够进行计算机手动操作,在设备条件达到的情况下,能够进行自动调节。
对一些重要的参数实现报警功能。
比如煤气总管压力、