镀镍故障.docx
《镀镍故障.docx》由会员分享,可在线阅读,更多相关《镀镍故障.docx(14页珍藏版)》请在冰豆网上搜索。
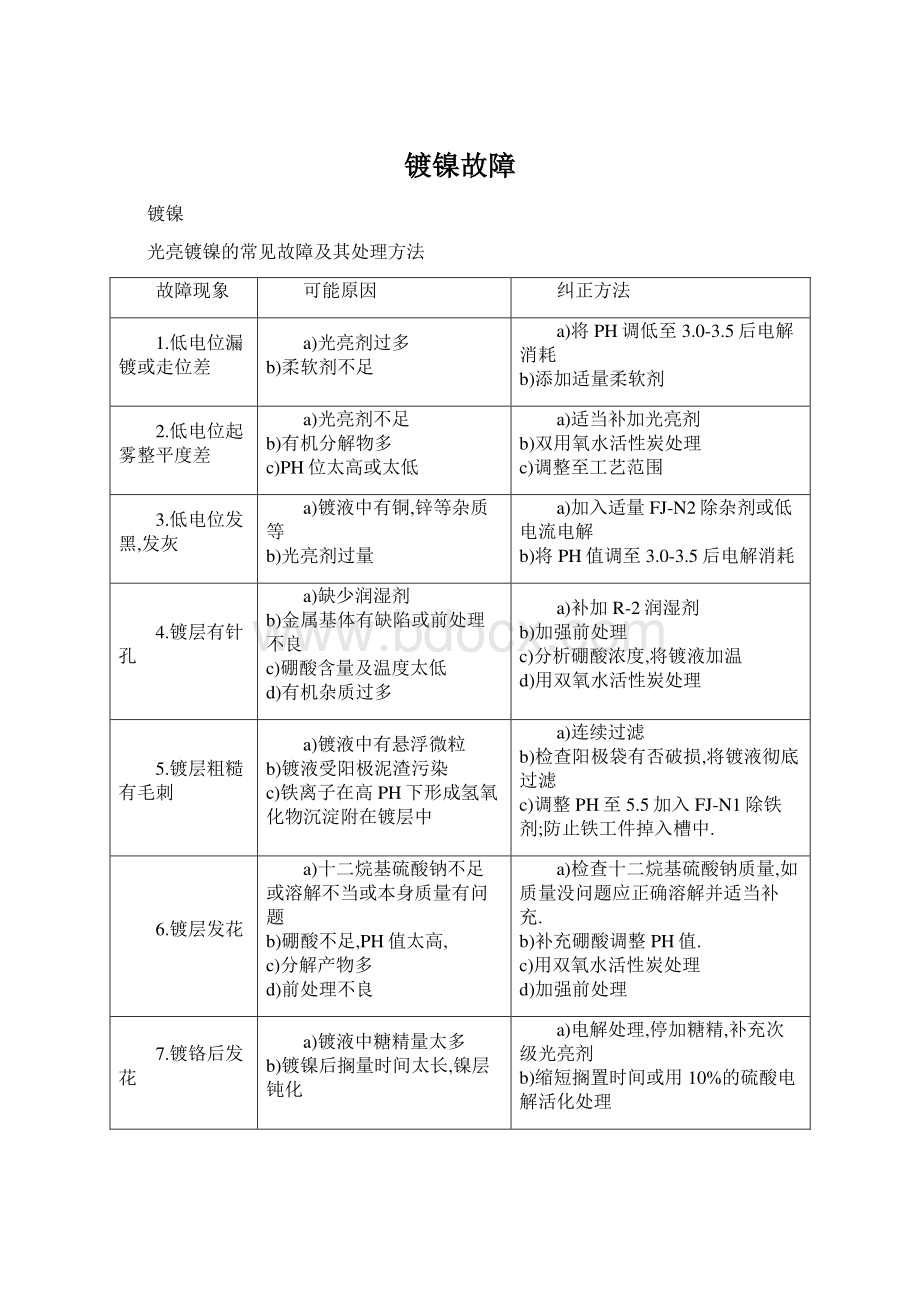
镀镍故障镀镍故障镀镍光亮镀镍的常见故障及其处理方法故障现象可能原因纠正方法1.低电位漏镀或走位差a)光亮剂过多b)柔软剂不足a)将PH调低至3.0-3.5后电解消耗b)添加适量柔软剂2.低电位起雾整平度差a)光亮剂不足b)有机分解物多c)PH位太高或太低a)适当补加光亮剂b)双用氧水活性炭处理c)调整至工艺范围3.低电位发黑,发灰a)镀液中有铜,锌等杂质等b)光亮剂过量a)加入适量FJ-N2除杂剂或低电流电解b)将PH值调至3.0-3.5后电解消耗4.镀层有针孔a)缺少润湿剂b)金属基体有缺陷或前处理不良c)硼酸含量及温度太低d)有机杂质过多a)补加R-2润湿剂b)加强前处理c)分析硼酸浓度,将镀液加温d)用双氧水活性炭处理5.镀层粗糙有毛刺a)镀液中有悬浮微粒b)镀液受阳极泥渣污染c)铁离子在高PH下形成氢氧化物沉淀附在镀层中a)连续过滤b)检查阳极袋有否破损,将镀液彻底过滤c)调整PH至5.5加入FJ-N1除铁剂;防止铁工件掉入槽中.6.镀层发花a)十二烷基硫酸钠不足或溶解不当或本身质量有问题b)硼酸不足,PH值太高,c)分解产物多d)前处理不良a)检查十二烷基硫酸钠质量,如质量没问题应正确溶解并适当补充.b)补充硼酸调整PH值.c)用双氧水活性炭处理d)加强前处理7.镀铬后发花a)镀液中糖精量太多b)镀镍后搁量时间太长,镍层钝化a)电解处理,停加糖精,补充次级光亮剂b)缩短搁置时间或用10%的硫酸电解活化处理8.镀层有条纹a)镀液中锌杂质过量b)镀液浓度太低c)PH值太低,DK太大d)有机杂质污染a)加入FJ-N2除杂剂b)提高硫酸镍含量c)调整到工艺规范d)对症处理9.镀层易烧焦a)主盐浓度太低b)镀液温度太低c)硼酸含量不足,PH高d)润湿剂过量a)分析成份后补充b)提高温度至55-60OCc)补充硼酸调整PH值d)采用活性炭吸附10.镀层脆性大a)光亮剂过量b)有机杂质污染c)金属杂质过高d)六价铬污染a)调整PH值3.03.5电解消耗b)用活性炭双氧水处理c)加入FJ-N2除杂剂d)用保险粉处理11.阴极电流效率低a)主盐浓度不足b)PH值过低c)阳极钝化阳极面积不够d)镀液被氧化剂污染a)提高主盐浓度b)调整工艺范围c)提高氦离子含量,增加阳极面积d)对症处理光亮镀镍故障处理针孔1.针孔、麻点呈癣状。
大多在镀件下面产生原因镀液中铁杂质积累过多。
处理方法去除铁杂质最有效的处理方法,是用质量分数为30的双氧水24mLL,将镀液中二价铁氧化成三价铁;再用质量分数为5的氢氧化钠或碳酸镍溶液调高pH值至5560,静置8h以上,使Fe成为Fe(on)沉淀,过滤除去。
如果不能停产,可用电解法,增大阴极面积,用01Adm2阴极电流密度电解处理一段时间,问题得到缓解。
2.针孔、麻点在镀件棱边和面向阳极的一面产生原因
(1)阴极电流密度过大;
(2)金属杂质积累过多;(3)硼酸含量过低。
处理方法
(1)降低阴极电流密度。
(2)参照上述相关处理方法除去。
(3)根据化学分析结果添加硼酸。
镀液中硼酸含量过低,必然使pH值升高,产生氢氧化物,与镍层一起沉积,使镀层出现针孔、麻点。
光亮镀镍层产生针孔与麻点的基本原因,是镀镍时阴极有氢气析出,吸附在镀件表面上,阻碍镀层金属的沉积。
如果氢气泡在镀件上停留的时间长,就形成针孔;停留的时间短,就形成麻点。
因此,针孔、麻点往往混杂在一起。
结合力不良1整个镀层从基体脱落产生原因
(1)工件前处理不良;
(2)钢铁件阴极除油或化学浸蚀的时间长,基体渗氢,电镀后氢气外溢。
处理方法
(1)加强对工件在预镀前的除油、除锈和清洗工序,确保基体表面洁净。
(2)适当缩短阴极电解除油、酸洗时间,防止工件基体渗氢。
2镀镍层起泡、脱皮产生原因
(1)复杂零件或挂具涂料绝缘层破裂而夹带溶液引起起泡;
(2)镀液中十二烷基硫酸钠含量过高。
处理方法
(1)对于复杂零件,操作时必须认真清洗所夹带的溶液;整修绝缘层破裂的挂具。
(2)采用粉状活性炭3gL,将镀液进行大处理除去过量十二烷基硫酸钠。
据文献L6论述:
油污带入镀液时,由于十二烷基硫酸钠分子的定向排列,能将油污包围成一层吸附膜,此时,油污进入胶束内部的憎水基之间,成球形或层状胶束。
随着十二烷基硫酸钠浓度升高,这些吸附有油污的胶束数量也增多,在电镀过程中它们被夹杂在镀层中就会起泡。
3镀层脱皮至底铜层产生原因(I)工件镀铜(包括氰化物镀铜、酸铜)后,清洗不干净或在空气中存放时间长,表面氧化;
(2)镀液中糖精含量过高(指镍层粉状脱落);(3)丁炔二醇过多(指镍层块状脱落)。
处理方法
(1)加强镀铜后清洗和镀镍之前的活化工序;尽可能缩短镀铜件在空气中的停留时间。
(2)低电流密度电解处理,或用活性炭吸附。
(3)参照上述相关处理方法除去。
4镀层从边缘脱落产生原因
(1)拉应力大;
(2)阴极电流密度过大;(3)铁杂质和有机物多。
处理方法
(1)添加应力减少剂,如适当提高糖精含量,能使镀层具有压应力,增强镀层的延展性能。
(2)降低阴极电流密度。
(3)参照上述相关处理方法除去。
镀层脆性大产生原因
(1)金属杂质积累过多,尤其是铬酸根离子;
(2)硼酸含量过低;(3)(次、初级)光亮剂过多;(4)pH值过高;(5)镀液温度过低;(6)阴极电流密度过大。
处理方法
(1)去除六价铬一般用保险粉或硫酸亚铁还原。
如六价铬的质量浓度为05gL时,加硫酸亚铁016gL,将pH值调高到6,温度70C,搅拌,可将cr3沉淀,过滤,最后把pH值调至工艺规范。
(2)按分析结果添加硼酸至正常范围。
(3)用低电流密度电解或活性炭吸附。
(4)调低pH值至工艺规范。
(5)升高镀液温度至工艺规范。
(6)降低阴极电流密度。
覆盖能力差1低电流密度区无镀层产生原因
(1)六价铬的影响;
(2)(次、初级)光亮剂过多;(3)pH值过低;(4)挂具接触不良;(5)有机杂质过多;(6)前处理不良;(7)氯离子含量过低。
处理方法
(1)参照上述相关处理方法除去。
(2)用低电流密度电解或活性炭吸附。
(3)调高pH值至工艺规范。
(4)整修或更换新的挂具。
(5)参照上述相关处理方法除去。
(6)检查前道镀铜后表面清洗状况,并加以彻底清洗干净。
(7)按分析结果添加氯化镍至工艺规范。
氯化物能减少阳极钝化,使镍阳极正常溶解,提高镀液导电能力和改善镀液的覆盖能力、分散能力。
2镀不上铬或铬镀层局部“露黄”、发花
(1)镍镀层表面钝化;
(2)镍层上光亮剂吸附或有凝结物;(3)镀镍液中金属杂质过多。
处理方法
(1)对镀镍后放置较长时间的镀件,可用质量分数为10的硫酸溶液或用铬酸浸渍后镀铬。
(2)适当减少光亮剂,必要时用活性炭处理。
在冬季时,为了防止工件带出液在表面形成凝结物,难以在冷水中洗净。
因此,镀镍后应先在温水中清洗,然后经活化处理后镀铬,就可以消除发花现象。
(3)参照上述相关处理方法除去。
镀镍溶液pH值调整方法不当引起的故障镀镍溶液的pH值偏高,调低时用浓硫酸,结果浓硫酸虽加入不多;pH值即直线下降,后又用浓的氢氧化钠溶液由低往高调,结果pH值又调过了头,经多次反复,最后不但pH值未能调合适,还破坏了整槽镀镍溶液,先是引起溶液中不少硫酸镍的结晶析出,后又成为稠稠的浆状。
这是因为开始浓硫酸加入过量,引起溶液中不少硫酸镍结晶析出(硫酸镍溶解度降低),后又用浓氢氧化钠溶液往回调时,由于浓氢氧化钠与镍盐起化学反应,生成胶体状氢氧化镍沉淀的结果。
出现上述情况时应将溶液进行过滤,并通电处理,溶液中有关成分也应通过化验分析后进行调整,否则就会增加溶液的电阻,镀出镀层粗糙并出现针孔。
为了防止上述现象再次发生,无论在溶液的pH值由高往低调,还是由低往高调时,用的是硫酸溶液,还是氢氧化钠溶液的浓度都要稀释至3以下,且必须边搅拌、边慢慢加入,这样pH值才不会有大的波动,也不至于出现硫酸镍的结晶析出和氢氧化镍的沉淀而造成镍盐的损耗。
光亮剂过剩对镀层质量的危害光亮镀镍溶液中的光亮剂不宜过多,有的厂家为获得更为光亮的镍层质量,任意添加过多的光亮剂,其实这样做很不妥当,这时不但镀层容易发花,还可能引起脆性,结合强度降低,镀层暴皮等一系列质量问题的发生。
防备方法:
根据镀层光亮度变化的需要添加,添加时应勤加、少加,由专人负责添加并做好记录。
镀镍溶液遭铅污染爆发性地出现下列故障:
工件的尖角部位明显镀焦,调小电流也不起作用,均镀能力差,镀层结合力差。
用活性炭进行处理后再用电解法进行电解处理都未见有所改善。
怀疑是受到对镀镍溶液极为敏感的铅所污染。
采取较大的阴极面积、较小的电流密度(0102Adm2)进行长时间的通电处理。
光亮镀镍溶液中氯离子过高引起的故障,亮镍溶液中氯化镍含量过高会引起镍阳极溶解过快,阳极泥渣增加,放电概率升高,造成操作环境恶化,镀层出现毛刺、裂纹、电流效率降低,内应力增加等一系列问题的发生。
镀镍溶液因错用铁质加温管而被污染镀镍溶液尚较清澈,见工件上的针孔多在工件的上面,有别于受到有机质污染形成的针孔(多在工件的朝下面),测得豹pH值略有升高,但还在范围之内。
从以上现象分析溶液有可能是被铁离子污染,否则针孔不可能多誉出现在工件的朝上部位,加十二烷基硫酸钠也应该有效。
除去镀镍溶液中铁离子的方法比较简单,通过添加双氧水,提高溶液的pH值至55后过滤,经调整pH值至45后试镀针孔现象完全消失。
镀镍液中混入硝酸根的故障镀镍溶液中加入硫酸镍后镀出镍层即出现灰黑色,电流效率很低,这一症状是由硝酸根引起的。
硫酸镍是由硝酸镍转化过来的,若制造工艺不够严格,很有可能有未曾洗脱的硝酸存在。
为治理这槽溶液,以通人电流使硝酸根还原为氨的方法进行处理,具体方法是:
初始以051Adm2通电56h,然后将电流密度降至0102Adm2继续处理,总通电量为:
019L硝酸根,则需通电1Ah,可以达到除尽的目的。
镀镍溶液中氯化镍加入过量镍层起毛刺氯化镍添加过量阳极会出现异常溶解,溶液中泥渣增多,继而使镀层产生毛刺。
取出原使用的铸造镍板,改用电解镍板(电解镍板在高氯化镍溶液中溶解性比浇铸镍均匀),同时用的确良布包扎镍板,经此改进后,镀层出现毛刺问题基本得到解决光亮镀镍电流密度过大引起镍层发雾、发花电流密度过大会引起镀层发雾,即我们所说的烧焦。
电流密度过小也同样不能获得满意的透明光亮的亮镍层。
这种情况常表现为:
在一串镀件中的上下几个工件常是比较光亮,而中间的几个工件光亮度较差(这是因为一串工件中的中间部位工件的电流密度总是比较小。
镍槽中阳极面积过小引起镀镍层发雾、发花阳极面积太小,起不到应有的作用,从而引起镀层的阴、阳面,或是双面都出现雾状。
溶液中镍盐含量过高引起镀镍层发雾、发花光亮镀镍溶液中镍盐含量过高引起镀镍层发雾、发花溶液中镍盐含量过低引起镀镍层发雾、发花光亮镀镍出现发花较易察觉,由于活化剂、氯化镍含量的严重不足,镍阳极严重钝化,最后出现镍层发花的严重后果。
由此可见,维护镍盐含量也是保证光亮镀镍层质量的关键。
镀液pH值过高引起镀镍层发雾、发花电镀镍(亮镍)过程中溶液的pH值是有所上升的,这是因为电解过程中班狐之故,为此要经常予以测定调整,否则当pH值过高时镀层中会有夹杂物,此夹杂物大多是碱式盐,从而促使镀层结晶粗糙,出现不透亮的白雾。
亮镍溶液大处理之后镀层出现发雾、发花亮镍溶液经用双氧水大处理之后镀出亮镍层严重发雾,色泽也很差,发暗,估计这种故障与大处理工艺有关,尤其是加的双氧水有可能未能充分分解。
这不但会破坏光亮剂,还可能导致镀层出现雾状,严重时还会引起镀层掉皮。
镀液温度过低影响镍层的结合强度镀镍工艺中严格控制溶液温度是保证镀层质量的一个重要环节,当溶液温度过低时,溶液中的盐类溶解度和导电率会明显降低,镍离子向阴极的扩散速度减慢,镀层内应力增加,从而影响到镀层的结合强度,为此,严格控制溶液温度是保证镀层结合强度的重要因素之一。
光亮镀镍溶液的温度低于工艺规范有以上同样的不利之外,还会使得镀层光亮范围变小、光亮度降低,若稍稍提高电流密度还容易被烧焦。
铜离子污染影响镀镍层结合强度镀镍溶液中的铜离子对镀层结合强度影响很大,当浓度稍高时会明显地出现置换铜层。
铜离子通常由以下几个途径进入镀镍槽中的:
(1)化工原料或阳极质地不纯;
(2)阳极铜质挂钩因接触溶液而遭到电化学溶解;(3)铜件或镀铜件接触溶液时的化学溶解;(4)擦洗铜杠时铜屑进入溶液;(5)工件镀铜后镀镍之前清洗不彻底而带进镀铜溶液。
防备方法:
(1)尽可能选用较高纯度的化工原料和阳极材料;
(2)阳极挂钩要远离镀液;(3)铜件或镀铜件要带电人槽;(4)擦洗铜杠时要从槽面上卸下来;(5)镀铜后进入镀镍槽之前要加强清洗;(6)常用小电流电解处理溶液;电流间断影响继镀层的结合强度电流间断多发生在镀薄片件中。
薄片件比较轻,工件挂在移动的阴极杠上挂镀时,由于阴极的移动,容易引起挂钩与阴极极杠脱离,电流间断。
防备方法:
挂钩和阴极极杠都要洗刷干净(挂钩能卡住阴极杠则更好),以改善两者之间电流的传导能力,也可在一串工件的末端绑一废品,以增加工件的质量,使其牢牢压在阴极杠上,从而防止工件脱电。
如能采用框架式挂具则既有利操作,更可防止上述现象的发生。
取工件观察时间过长影响镀镍层结合强度镀镍时,特别是在高温下镀亮镍时,从槽中取出工件观察时间不可过长,否则工件在空气中极易干化并迅速氧化,当继续再镀时,又会造成镍层上镀镍,会严重影响镀层的结合强度。
有机质污染影响镀镍层的结合强度光亮镀镍溶液中有机杂质产生的原因主要是:
使用的化工原料纯度低、光亮剂的分解和抛光膏的带入以及工件的前处理欠彻底、隐蔽部位藏有污物的带入。
有机杂质影响镀镍的结合强度。
防备方法:
溶液要定期进行净化处理,具体方法简述如下。
(1)在搅拌下向溶液中加入双氧水13mLL;
(2)将溶液加热至5060;(3)在搅拌下加入粉末状活灶炭23gL(如栗如的是颗粒状的则应加倍的量加入,否则效果欠佳);(4)继续搅拌2h;(5)静止2h后过滤;(6)添加适量添加剂后试镀,若效果不够好可通电处理予以纠正。
最根本的要求是从工艺上严格把关,防止有害物质的混入。
镀镍层出现灰黑镀镍层出现黑色通常是溶液被铜、锌等金属杂质污染所致。
操作者在操作工序中,工件从这一工序移到下一工序时都是蜻蜓点水似的,一下一上即算完成这一工序。
却未曾想到,这样做怎能把工件表面前一工序中带来的溶液清洗干净呢?
诸如镀完氰化铜后的清洗还是中和处理都是同样的一下一上,如此处理方法不可能把形状复杂工件上的溶液清洗干净,而是把工件表面的铜离子带入镀镍槽中,污染镀镍溶液,就算镀上了镍层,结合力必然也是很差的。
镀镍溶液大处理之后镀层易烧焦镀镍层易烧焦的原因是很多的,如电流密度过大、阳极布置不合理、溶液温度过低、镍离子浓度过低等。
镀镍溶液大处理之后镀层易烧焦的原因可能是溶液大处理时镍离子有过大消耗,主要是在提高pH值清除金属杂质过程中以氢氧化物形式沉淀的同时,部分镍离子也会随之而一起沉淀,这是其一;同时在过滤时溶液的损耗和槽底沉积的废弃的量也是不少的,这几个方面的损耗加在一起有可能达整槽溶液的10,即相当于3040gL,如原先溶液中镍离子的浓度已处在配方范围的下限,则有可能出现上述质量故障。
镀镍溶液大处理之后镀层出现针孔镀镍溶液经活性炭处理之后,镀出工件出现针孔,这是因为溶液经粉末状活性灰处理之后,原有的湿润剂也会随之被吸附,同时在高pH值条件下,镍离子也会与其起反应,生成不溶性的化合物而沉淀之故。
这一故障现象经添加湿润剂之后消失。
镍层鼓泡镀镍层鼓泡只在预处理工艺上找原因是不够的。
其实除此之外,还有许多种原因会引起镀层鼓泡,其中以下四点尤为多见。
(1)由砂眼、孔隙、裂纹、划伤等缺陷引起的鼓泡。
在电解过程中这些部位析出的氢气由于逸出口狭隘,阻力越大,有的只能隐藏在内,最后干燥、老化处理时气体受热膨胀,把镍层顶起来,形成鼓泡。
也有因这些部位渗有溶液,在镀后隔一定时间或在干燥、老化的溶液中的酸、碱与基体或镀层起化学作用,降低了镀层与基体金属的结合力,而氢气造成的压力分离了镀层与基体金属的结合而形成鼓泡。
(2)由析氢引起鼓泡。
这种鼓泡多出现在电流密度较大的部位,如棱角、尖端部位,工件的凹陷、隐蔽部位却少见,这是电流密度较大部位电流密度较高,电流效率低,易析氢所致,析出的氢部分吸附在基体金属上和基体金属内部,当工件干燥、老化时,由于吸附在基体金属上的氢气对镀层施加一定的压力而造成鼓泡。
(3)由光亮剂、添加剂含量过高引起鼓泡。
添加剂、光亮剂添加过量必然增加有机物的分解量,当有机杂质积聚过多之后,会使镀层中的晶格严重扭曲,内应力增加,从而导致脆性增大,形成镀层鼓泡。
为此,添加剂的添加量要适度,并适时对溶液进行大处理,这是解决这一问题的关键所在。
(4)由溶液温度过低而电流密度过高引起鼓泡。
当温度过低时,溶液的导电性能差,此时添加剂吸附强,却脱附困难,此时若采取较高的电流密度,则会造成边棱部位烧焦,添加剂夹杂增多,镀层脆性增大、鼓泡。
多层镀镍中的故障镀层出现故障的原因是多种多样的,分析要有针对性地进行,尤其要查清故障发生在哪一工艺段,这样查找就能缩小目标。
跨越界限不但找不到真正的原因,有时反而会把问题嫁祸于“人”,而隐蔽了真正的祸根,故障现象照常会继续发生。
在此以某次镍铜镍铬引起镀层结合力不良为例,应先看当时出现镀层结合力问题是出在基体金属与镍层之间,镍层与铜层之间,铜层与亮镍层之间,还是亮镍层与亮镍层之间。
如果结合力问题发生在基体金属与镍层之间,就要从基体的预处理是否彻底、工件表面是否有油污、氧化膜,以及电化学除油,弱腐蚀等工艺中去寻找根源。
如果结合力问题发生在镍层与亮铜之间,就要检查镀镍后是否当即镀铜,如镀镍后在空气中停留时间过久,镍层表面遭到氧化。
如这时再以带电入槽的,则有可能影响铜层在镍层上的结合力。
如果结合力问题发生在亮铜与亮镍层之间,就要检查镀铜层是否经过脱膜处理。
有的亮铜工艺配方中有OP乳化剂之类的添加剂,这类添加剂会在铜层上形成一层膜,不易除去,在此膜层上沉积的镍层必然不会牢固。
此外铜层遭到钝化或镀前未经活化处理,或镀亮镍溶液本身有故障(如溶液表面有油膜,工件入槽时被油膜所包住),或亮镍溶液被无机杂质所染(如有铁质会引起镍层脆性,镀镍溶液中添加剂失调)等,对镍在铜层上的结合力都有影响。
如果结合力问题发生在双层镍上,这一结合力问题另有原因,常见的有如下两个方面。
(1)镀镍时中途停过电,包括因接触不好短时间脱过电;
(2)操作上出现过双性电极,工件脱离极梗后仍处在阴、阳极之间,从而促使工件的局部处发生过钝化。
镀层在不同的工艺段发生结合力问题,其发生原因都是不一样的,不同情况要不同分析,不可张冠李戴。
统归前处理问题,这样做既不公平,更难以对症下药去解决问题。
镍阳极发生钝化铸造阳极表面有一层致密的氧化膜,这层氧化膜若事先未用浓盐酸浸泡、刷去,直接使用,则使用初期必然是不易溶解的,此时也必然会出现高电压,低电流的现象。
光亮镍溶液高锰酸钾-活性炭净化处理在双氧水的氧化能力不够的情况下,可采用高锰酸钾净化处理,即高锰酸钾一活性炭净化法其效果会更好,其处理方法简述如下。
(1)用稀硫酸调整镀镍溶液的pH值达3左右,加热至6080。
(2)高锰酸钾配成5的水溶液,在剧烈搅拌下缓慢加入溶液中。
其用量在处理大槽之前应先在烧杯中做好试验,以出现轻微紫红色为限量,然后按此用量再计算处理大槽时需要高锰酸钾的用量。
(3)加温至6570,持续搅拌2h,使其与高锰酸钾加速氧化反应:
2KMn04十10FeS04十8H2S045Fe2(S04)3+2MnS04+K2S04+8H20(4)在搅拌下加入氢氧化镍或碳酸镍,提高pH至556,使Fe3+形成氢氧化铁沉淀Fe2(S04)3+3Ni(0H)22Fe(0H)3+3NiS04注意:
氢氧化镍必须配制新鲜溶液,商品氢氧化镍溶解性差。
配成后弃去上层清液,将沉淀用水清洗几遍后即可使用。
(5)加入5浓度的双氧水,以还原过剩的高锰酸钾,并使硫酸锰氧化成二氧化锰沉淀排除,此时溶液的淡红色应已褪尽。
操作时应边加入双氧水边搅拌,同时观察淡红色褪除后停止加入双氧水。
(6)加入FJN5除铜剂,沉淀铜杂质,加完后继续搅拌30min。
(7)加入35gL化学纯活性炭粉末状活性炭(加入前先调成糊状),继续搅拌2h,使有机杂质充分被吸附除去。
(8)静置34h后过滤。
(9)调整pH值至工艺范围,低电流通电处理,根据试镀情况,若无异常即可将配制量的12的糖精及略高于此值的初级光亮剂各溶于少量水中,在搅拌下加入槽中即可试镀。
光亮镍溶液双氧水-活性炭净化处理采用双氧水一活性炭净化处理光亮镀镍溶液是行之有效的大处理方法之一,但当处理工序安排不当,操作方法不严,有可能事倍功半,达不到预期效果,甚至有可能出现故障。
下面就此法作简要叙述。
(1)用5浓度的稀硫酸将镀镍溶液的pH值调至335,此pH值条件有利于提高双氧水的氧化能力。
(2)在搅拌下缓慢地加入双氧水24mLL(加入前先稀释510倍,以利于发挥其作用,减少损耗),继续搅拌1h,使溶液中的Fe2+氧化成Fe抖,有机杂质存在时也易被氧化,容易被活性炭吸附。
(3)加温至40左右,继续搅拌lh,使双氧水充分发挥氧化作用,促使Fe2+充分氧化成Fe3+2FeS04+H202+H2S04Fe2(S04)3+2H20并促使有机杂质还原成碳。
(4)加温至70,在此温度条件下,使残余的双氧水充分分解,以免光亮剂遭到破坏。
2H2022H20+02(5)在搅拌下加入氢氧化镍或碳酸镍,提高pH至556,使Fe3+形成氢氧化铁沉淀Fe2(S04)3+3Ni(0H)22Fe(OH)2+3NiS04注意:
氢氧化镍必须配制新鲜溶液,商品氢氧化镍溶解性差NiS04+2Na0HNi(0H)2+Na2S04配成后弃去上层清液,将沉淀用水清洗几遍后即可使用。
(6)加入FJN5去铜剂13mLL,搅拌1530min,使铜杂质沉淀。
(7)将35gL化学纯粉末状活性炭用水调成糊状后加入,继续搅拌2h,使有机杂质充分被吸附除去,静止34h后过滤(沉淀时间不宜过长,否则有可能因脱附而影响处理效果)。
(8)调整pH值至工艺规范后试镀,如色泽正常即可补充光亮剂,并以0102Adm2的低电流处理,以除去残存的重金属杂质,经一定时间处理之后称取按工艺配制量的l2的糖精,并将略高于此值的初级光亮剂溶于少量水中,在搅拌下加入槽中即可试镀。
镀镍层返修一法将返修件中属于发白、发黑、光泽性差、有装夹印痕、气流等工件挑选出来,通过下列步骤的预处理之后,即可再在此基础上加厚镀层。
(1)装夹;
(2)浸稀盐酸:
HCl200mLLT室温t46min(3)二道流水冲洗;(4)阳极活化处理:
H2S04100mLLT室温t051minU051V经上述预处理之后,原来镍层表面变成灰色,经充分清洗后即可转入镀镍槽中二次镀镍