钢柱制造作业指导书.docx
《钢柱制造作业指导书.docx》由会员分享,可在线阅读,更多相关《钢柱制造作业指导书.docx(16页珍藏版)》请在冰豆网上搜索。
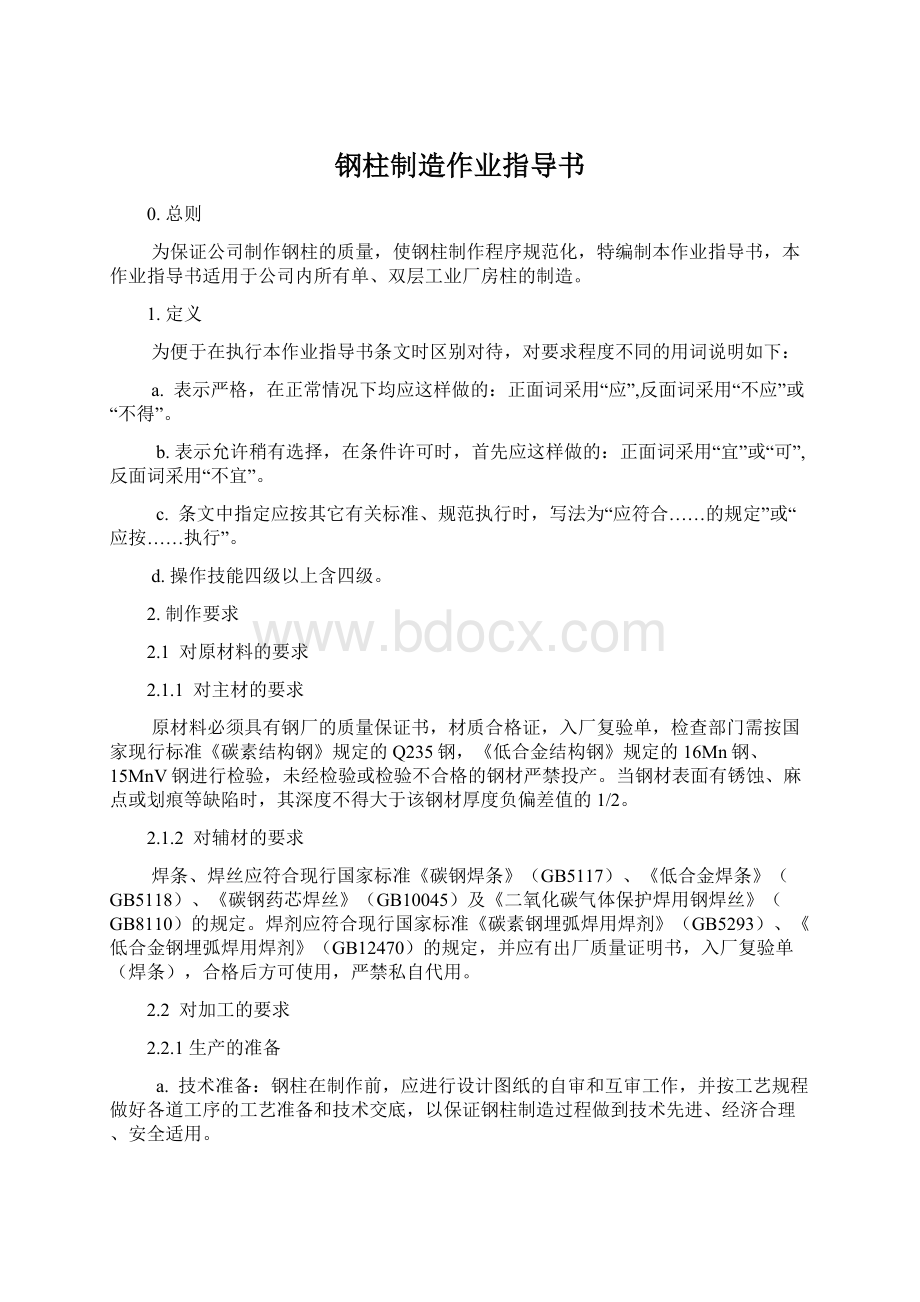
钢柱制造作业指导书
0.总则
为保证公司制作钢柱的质量,使钢柱制作程序规范化,特编制本作业指导书,本作业指导书适用于公司内所有单、双层工业厂房柱的制造。
1.定义
为便于在执行本作业指导书条文时区别对待,对要求程度不同的用词说明如下:
a.表示严格,在正常情况下均应这样做的:
正面词采用“应”,反面词采用“不应”或“不得”。
b.表示允许稍有选择,在条件许可时,首先应这样做的:
正面词采用“宜”或“可”,反面词采用“不宜”。
c.条文中指定应按其它有关标准、规范执行时,写法为“应符合……的规定”或“应按……执行”。
d.操作技能四级以上含四级。
2.制作要求
2.1对原材料的要求
2.1.1对主材的要求
原材料必须具有钢厂的质量保证书,材质合格证,入厂复验单,检查部门需按国家现行标准《碳素结构钢》规定的Q235钢,《低合金结构钢》规定的16Mn钢、15MnV钢进行检验,未经检验或检验不合格的钢材严禁投产。
当钢材表面有锈蚀、麻点或划痕等缺陷时,其深度不得大于该钢材厚度负偏差值的1/2。
2.1.2对辅材的要求
焊条、焊丝应符合现行国家标准《碳钢焊条》(GB5117)、《低合金焊条》(GB5118)、《碳钢药芯焊丝》(GB10045)及《二氧化碳气体保护焊用钢焊丝》(GB8110)的规定。
焊剂应符合现行国家标准《碳素钢埋弧焊用焊剂》(GB5293)、《低合金钢埋弧焊用焊剂》(GB12470)的规定,并应有出厂质量证明书,入厂复验单(焊条),合格后方可使用,严禁私自代用。
2.2对加工的要求
2.2.1生产的准备
a.技术准备:
钢柱在制作前,应进行设计图纸的自审和互审工作,并按工艺规程做好各道工序的工艺准备和技术交底,以保证钢柱制造过程做到技术先进、经济合理、安全适用。
b.材料准备:
材料的矫正必须在划线前进行,其矫正后的尺寸允许偏差应符合GB50205-2001《钢结构工程施工质量验收规范》中表7.3.5的规定。
辅助材料包括焊条、焊丝、焊剂、保护焊用气体等,应与有关钢材匹配使用,妥善保管。
c.设备准备:
根据钢柱的重量和型式配备10吨-75吨吊车,仿形切割机、小车式半自动切割机、射吸式割炬、九辊平板机、龙门式剪板机、刨边机、碳弧气刨、摇臂钻床、埋弧自动焊机、二氧化碳保护焊机、手弧电焊机、反变形机、切割机、锯床、以上设备的维护和保养应符合ZYZDS-8《设备维修、保养作业指导书》的要求。
d.钢柱工程施工及验收所使用的计量器具必须合格,定期对所使用的计量器具送计量部门进行计量检定,并保证在检定有效期内使用。
计量检验应符合ZYZDS-6《计量检测作业指导书》中的规定。
2.2.2放样和号料
a.要求划线工应具有较高的操作技能(四级以上),要有熟练的看图和绘图知识,并熟悉钢柱的生产过程,了解各工序的生产特点,加工方法和机械设备性能及工艺要求,最好是具有较为丰富的生产经验。
b.划线工号料前必须审图,图纸不清或有疑问应及时找有关技术人员联系解决,所使用计量器具应符合2.2.1中d条的规定。
c.放样前应核对施工图纸并熟悉工艺要求,对施工图中结构件的重要节点尺寸放实样或计算校核。
d.样板、样杆可采用厚度为0.3-0.5mm的薄钢板制作。
样板、样杆制作尺寸的允许偏差应符合YB9254-95《钢结构制作安装施工规程》中表4.2.2的规定。
e.号料前应照发料单核对钢材规格、材质、批号、并应清除钢材表面油污、泥土等脏物,且表面质量应符合2.1.1的规定。
f.号料人员在号料时应在钢板或型材上注明构件号、零件号、规格、数量、并做好标记的移植(按ZYZDS-1《材料标记及移植规定》执行)。
对不同材质零件,采用不同颜色标注。
g.对于柱翼缘板、腹板在号净料时应划上检查线,其形式如下图:
h.厂房柱焊接H型钢、腹板、翼缘板宽度方向号净料,长度方向一次号料加荒料50mm。
在号净料的基础上予留焊接收缩余量及切割边缘加工等加工量应符合表1规定。
表1单位:
mm
加工余量
锯切
剪切
手工切割
半自动切割
精密切割
切割缝
1
4-5
3-4
2-3
刨边
2-3
2-3
3-4
1
1
铣平
3-4
2-3
4-5
2-3
2-3
i.焊接H型钢腹板,翼缘板拼接焊缝应相互错开500mm以上,与加劲板错开200mm以上。
板材、型材长度方向拼接长度为:
Lmin500mm。
角钢、槽钢采用标准接头或执行合同要求,并注意错开与其它零件连接的位置。
j.钢柱板材拼接坡口要求用刨边机加工。
埋弧焊:
1020光双产45钝6
2040光双产35钝6
手工焊:
620光双产35钝2
k.钢柱柱身的连接孔为成品孔,号孔时应以柱肩处为准。
零件板上的孔为样板号孔,号孔应使用与孔径相等的圆规规孔,并打上样冲作出标记,便于钻孔后检查孔位是否正确。
l.如出现号错料、切错料问题时,应及时和有关技术人员联系解决,如需换料时,必须填写材料反馈通知单。
(见附录)包括设计变更时换料。
2.2.3切割
a.切割人员必须具有特殊工种操作证,或具有较高的操作技能(四级以上),熟悉所使用的切割设备的机械性能和一些技术参数,有丰富的生产实践经验。
b.厚度等于或大于8mm的板材可采用自动或半自动气割。
型材采用手工切割或锯床切割。
采用手工切割时,切割面需用砂轮打磨处理。
厚度小于或等于6mm的板采用龙门剪床剪切,其允许偏差应符合GB50205-2001《钢结构工程施工质量验收规范》中表7.2.2的规定。
c.碳素结构钢,在环境温度低于-20℃时,低合金结构钢在环境温度低于-15℃时,不得剪切。
d.气割用氧气纯度应在99.5%以上,乙炔纯度应在96.5%以上,丙烯纯度在98%以上。
e.板材气割应在专用平台上进行,平台与板材的接触应为线状或点状接触。
其形式如图所示:
f.切割前应将钢材表面距切割边缘约50mm范围内的铁锈、油污等清除干净。
对高强度大厚度钢板的切割,在环境温度较低时应进行预热,预热温度100℃-150℃。
g.气割后,断口上不得有裂纹和分层,并清除边缘上的熔瘤和飞溅物,其允许偏差应符合表2规定。
气割的允许偏差(mm)表2
项目
允许偏差
零件宽度、长度
3.0
切割面平面度
0.05t且不大于2.0
割纹深度
0.2
局部缺口深度
1.0
切割面垂直度
不大于钢材厚度的10%且不大于1.5mm
注:
t为切割面厚度
h.自动、半自动气割工艺参数可采用表3规定。
表3
割嘴号码
板厚(mm)
氧气压力(MPa)
乙炔压力(MPa)
气割速度(mm/min)
1
6-10
0.69-0.78
0.3
650-450
2
10-20
同上
0.3
500-350
3
20-30
同上
0.3
450-300
3
30-40
同上
0.3
400-300
4
40-60
同上
0.4
350-250
5
60-100
同上
0.4
300-200
2.2.4制孔
a.制孔人员须有较高的操作技能(四级以上),熟悉并能熟练使用所用的摇臂钻床,了解本工序的生产特点和工艺要求。
b.柱主材上的孔为成品钻孔,零件板上的孔为板叠套钻或钻模制孔,但最多不得超过3块,且应小于60mm。
c.采用钻模时,钻模制作允许偏差应符合下列规定。
1>相邻两孔中心距:
0.2mm。
2>两最外排孔中心距:
0.3mm。
3>两对角线孔中心距:
0.45mm。
d.零件、部件孔如设计无要求时,孔距的允许偏差应符合表4的规定。
表4
序
项
允许偏差
号
目
500
500-1200
1200-3000
3000
1
同一组内相邻两孔间
0.7
2
同一组内任意两孔间
1.0
1.2
3
相邻两组的端孔间
1.2
1.5
2.0
3.0
e.高强度螺栓孔允许偏差参见表5。
表5
名称
允许偏差(mm)
螺栓名义直径
12
16
20
22
24
30
孔的直径
13.5
17.5
21.5
23.5
26
32
孔径允许偏差
+0.40
0
+0.50
0
+0.80
0
圆度
1.0
1.0
1.5
中心线倾斜度
应不大于板厚的3%,且单层板不得大于1.0mm,多层板迭组合不得大于2.0mm
f.制孔后应用磨光机清除孔边毛刺,并不得损伤母材。
2.3对装配的要求
2.3.1材料的拼接
a.接料人员应熟悉图纸的要求和工艺要求。
b.型材拼接时,采用国家规定的标准接口,或执行合同要求。
c.板材接料,应严格控制对接接头的错边量,其偏差应符合表6规定。
表6
板厚(mm)
818
18
偏差
s1.5
s2.0
d.对接口错边量必须由专检人员(电焊)检查合格后,才能进行焊接,作业方法按ZYZDS-13《埋弧自动焊作业指导书》;ZYZDS-17《手工电弧焊作业指导书》执行。
e.所有板材接料焊缝应进行无损检查,合格后方能转入下道工序。
无损检查方法按ZYZDS-5《无损检验作业指导书》进行,对有不允许存在缺陷的焊缝应用碳弧气刨清根后方可焊接,经无损检查仍有局部不合格时,对不合格的局部缺陷进行返修,返修次数最多不得超过三次。
接口焊缝的外观质量须经电焊专检人员检查合格后,方可转入下道工序。
电焊专检人员应有一定的焊接知识和丰富的经验,熟悉焊接工艺过程和焊缝专用符号。
f.对柱翼缘钢板厚度32mm低合金钢或40mm低碳钢的接料焊缝应进行热处理,其方法按ZYZDS-18《热处理作业指导书》执行。
2.3.2构件的组装
a.装配铆工要有较高的操作技能(四级以上),要有熟悉的看图本领,并熟悉和了解本工序的生产特点和加工方法及工艺要求,生产经验丰富。
b.装配铆工在装配前,应认真审图,校核零件尺寸,对不合格的零件不得装配。
c.连接接触面和沿焊缝边缘每边30-50mm范围内的铁锈、毛刺、污垢、冰雪等应清除干净。
d.钢柱的结构形式有实腹式钢柱和格构式钢柱。
e.对焊接H型钢的翼缘板可提前进行反变形加工,加工方法有火焰加工和用反变形机加工,利用反变形机加工时,其反变形值可参
表7
板厚
板宽B
12
14
16
20
25
28
30
36
40
挠度
150
2
2
1.5
1
1
1
0.5
0.5
0.5
200
2.5
2.5
2
2
1.5
1
1
0.5
0.5
250
3
3
2.5
2
2
1.5
1
0.5
0.5
300
4
3.5
3
2.5
2.5
1.5
1.5
1
0.5
350
4.5
4
3.5
3
3
2
1.5
1
0.5
400
5
4.5
4
3.5
3
2
1.5
1
1
450
5.5
5
4
4
3.5
2
2
1
1
500
6
5.5
4.5
4.5
4
2.5
2
1.5
1
550
-
6
5
4.5
4
2.5
2
1.5
1
600
-
-
5
5
4.5
3
2.5
1.5
1
650
-
-
-
5
5
3
2.5
1.5
1.5
700
-
-
-
-
5
3.5
3
2
1.5
750
-
-
-
-
-
4
3
2
1.5
800
-
-
-
-
-
4
3.5
2.5
-
f.H型钢和槽形分肢装配形式和焊接顺序,如图示
.划线与安装定位角铁.装配T形梁装配工字梁
1.翼板2.定位角铁3.腹板4.拉杆5.直角尺6.吊具7.楔铁
g.焊接连接组装的允许偏差应符合表8的规定。
焊接连接组装的允许偏差(mm)表8
项目
允许偏差
图例
高度(h)
2.0
垂直度()
b/100且大于2.0
中心偏移(e)
2.0
h.焊接后的H型钢、槽形钢的矫正(加热温度不应超过900°C),其方法如下:
I.格构式钢柱的装配和焊接顺序:
格构式钢柱由柱脚、柱身、扁头及柱头组成,柱身有两肢工字形、槽形等多种,柱头多为工字形:
柱头人孔的装配,首先将已焊好的人孔圈按图纸要求的位置放在柱头腹板上,在人孔圈两边点焊定位,在人孔圈中间加上临时支撑,以防收缩变形。
人孔圈的焊接顺序与方向如图:
柱身的装配以柱肩板刨光端为准,划出柱身腹杆的装配线,装配连接板,装配腹杆和腹杆焊接顺序如下图所示:
柱头与柱身的装配,首先在柱身腹板上划出柱头的装配线,插柱头时要对准翼板中心线和腹板中心线,在吊车梁的支撑板(柱肩)上划出装配线,并将支撑板放置在柱身上端对正装配线后定位焊。
见下图:
装配柱脚以柱肩为准,确定柱身的下端尺寸,将多余长度加工至要求尺寸,在柱底板上划出二肢的装配线,焊定位档铁即可装配柱脚如图:
注:
1.定位挡铁2.找平工字钢3.柱底板
柱头与柱身的连接部分焊接时顺序如下图。
柱角焊接应先焊水平焊缝后焊竖缝,焊主焊缝(先焊里侧,再焊外侧)。
j.实腹式钢柱的装配和焊接顺序工艺过程与格架式钢柱基本相同。
k.凡多层柱,其接触面处必须铣平,端铣平面的允许偏差为:
两端铣平面后构件长度2.0mm
端铣面不平直度0.3mm
端铣面的倾斜度1/1500
l.顶紧接触面应有75%以上的面积紧贴,用0.3mm塞尺检查,其塞入面积应小于25%,边缘间隙不应大于0.8mm。
m.多层钢柱必须在厂内拼装,拼装的钢柱其质量应符合设计要求和本指导书的规定。
预装所用平台或支承凳应测量找平,安装螺栓时不得用大锤击,检查前所有临时固定和拉紧装置应全部拆除。
检查方法:
观察检查。
用I型试孔器检查每组孔的通过率应为100%,用
型应为90%。
钢柱厂内预拼装的允许偏差项目和检验方法应符合GB50205-2001《钢结构工程施工质量验收规范》中附录D的规定。
n.拼装接头预留200mm的现场焊缝并在柱底板和柱身上用样冲打上中心线和构件号。
如下图所示:
2.4焊接和焊接检验
2.4.1对焊接的要求
a.对首次采用的钢材、焊接材料、焊接方法,应进行焊接工艺评定,并根据评定报告确定焊接工艺。
焊接工艺评定按ZYZDS-15《焊接工艺评定作业指导书》中的规定进行。
b.焊工应经过考试并取得合格证后方可从事焊接工作。
c.焊接时不得使用药皮脱落或焊芯生锈的焊条和受潮结块的焊剂及已熔烧过的渣壳。
作业方法按ZYZDS-13《埋弧自动焊作业指导书》、ZYZDS-17《手工电弧焊作业指导书》执行。
d.焊条、焊剂使用前应按产品说明书规定的烘焙时间和温度进行烘焙、低氢型焊条经烘焙后应放入保温筒内,随用随取。
e.焊接材料型号应与焊件材质相匹配,Q235钢手工焊用E4303焊条、自动焊用H08Mn焊剂431;16Mn钢手工焊用E5016焊条、自动焊用H10Mn2焊剂431;15MnV钢手工焊用E5015焊条、自动焊用H10Mn2Si焊剂350。
f.施焊前,焊工应复查焊件接头质量和焊区处理情况,当不符合要求时,应修整合格后方可施焊。
g.对接接头,T形接头、十字接头等对接焊缝及对接和角接组合焊缝,应在焊缝的两端设置引弧和引出板,其材质和坡口形式应与焊件相同,引弧和引出板的焊缝长度:
埋弧焊应大于50mm,手工电弧焊应大于20mm,焊接完毕后,应采用气割切除引弧和引出板,并修平整,不得用锤击落,并要求在主焊缝附近打上焊工钢印。
如下图所示:
h.焊接时,焊工应遵守焊接工艺,不得自由施焊及在焊边外的母材上引弧,焊接顺序按2.3.2中规定施焊。
i.厚度大于40mm的碳素结构和厚度大于36mm的低合金结构钢,施焊前应进行预热,焊后进行后热。
j.焊接完毕,焊工应清理焊缝表面熔渣及两侧的飞测物,检查焊缝大小是否符合图纸要求。
2.4.2焊接检验
a.碳素结构钢应在焊缝冷却到环境温度,低合金结构钢应在完成焊接24h后,方可进行焊缝探伤检验。
b.板材拼接及钢柱上要求焊透的焊缝应100%UT,焊接接头内部缺陷分级应符合现行国家标准《钢焊缝手工超声波探伤方法和探伤结果分级的规定》。
c.局部探伤的焊缝,有不允许缺陷时,应在该缺陷两端的延伸部位增加探伤长度,增加的长度不应小于该焊缝长度的10%,且不应小于200mm。
仍有不允许缺陷时,应对该缝100%探伤检查。
d要求焊缝饱满无气孔、夹渣、裂纹并清除焊接区的飞测和熔渣。
2.5钢柱的验收
a.检查人员必须具有一定的视图本领,熟悉图纸和钢柱的生产过程及工艺要求,最好具有丰富的经验。
b.钢柱制作完成后,应按照施工图和本指导书的规定进行验收。
c.钢柱外形尺寸允许偏差应符合GB50205-2001《钢结构工程施工质量验收规范》中附录C中表C、0、3和C、0、4。
d.检查是否按要求打上构件中心线和钢印号。
3.钢柱的涂装、编号和包装发运
3.1钢柱的涂装
a.钢柱的除锈和涂装应在制作质量检验合格后进行。
b.钢柱表面的除锈方法和除锈等级应符合GB50205-2001《钢结构工程施工质量验收规范》中表14.2.1中的规定,其质量要求符合现行国家标准《涂装前钢材表面锈蚀等级》的规定。
应与设计采用的涂料相适应。
c.涂装工人应具有一定的涂装经验。
d.涂装遍数、涂层厚度应符合设计要求,作业方法按ZYZDS-2《钢结构涂装作业指导书》执行。
3.2钢柱的编号
涂装完毕后应在钢柱上标注钢柱的原编号。
大型钢柱应标明重量、重心位置和定位标记。
3.3钢柱的包装和发运
3.3.1钢柱出厂时,应有以下资料
a.产品合格证
b.施工图和设计变更文件。
设计变更内容应在施工图中相应部位注明。
c.制作中对技术问题的处理协议。
d.钢材连接材料,涂装材料的质量说明书或试验报告。
e.焊接工艺评定报告。
f.高强度螺栓磨擦面抗滑移系数试验报告,焊缝无损检验报告和涂层检测资料。
g.预拼装记录。
3.3.2构件发运和包装按ZYZDS-4《成品包装发运作业指导书》执行。
4.质量记录
4.1质量事故记录和设计变更记录
4.2一次检查产品合格记录
4.3预拼装记录
4.4涂装、编号、包装和发运记录
4.5无损检查报告
4.6摩擦面抗滑移系数试验报告
4.7工艺评定报告
4.8材料反馈通知单
5.附录
材料反馈通知单
反馈单位
订货号
构件号
构件名称
数量
重量(kg)
反
馈
理
由
技术负责人
生产工艺部
物资部