实习目的张报.docx
《实习目的张报.docx》由会员分享,可在线阅读,更多相关《实习目的张报.docx(14页珍藏版)》请在冰豆网上搜索。
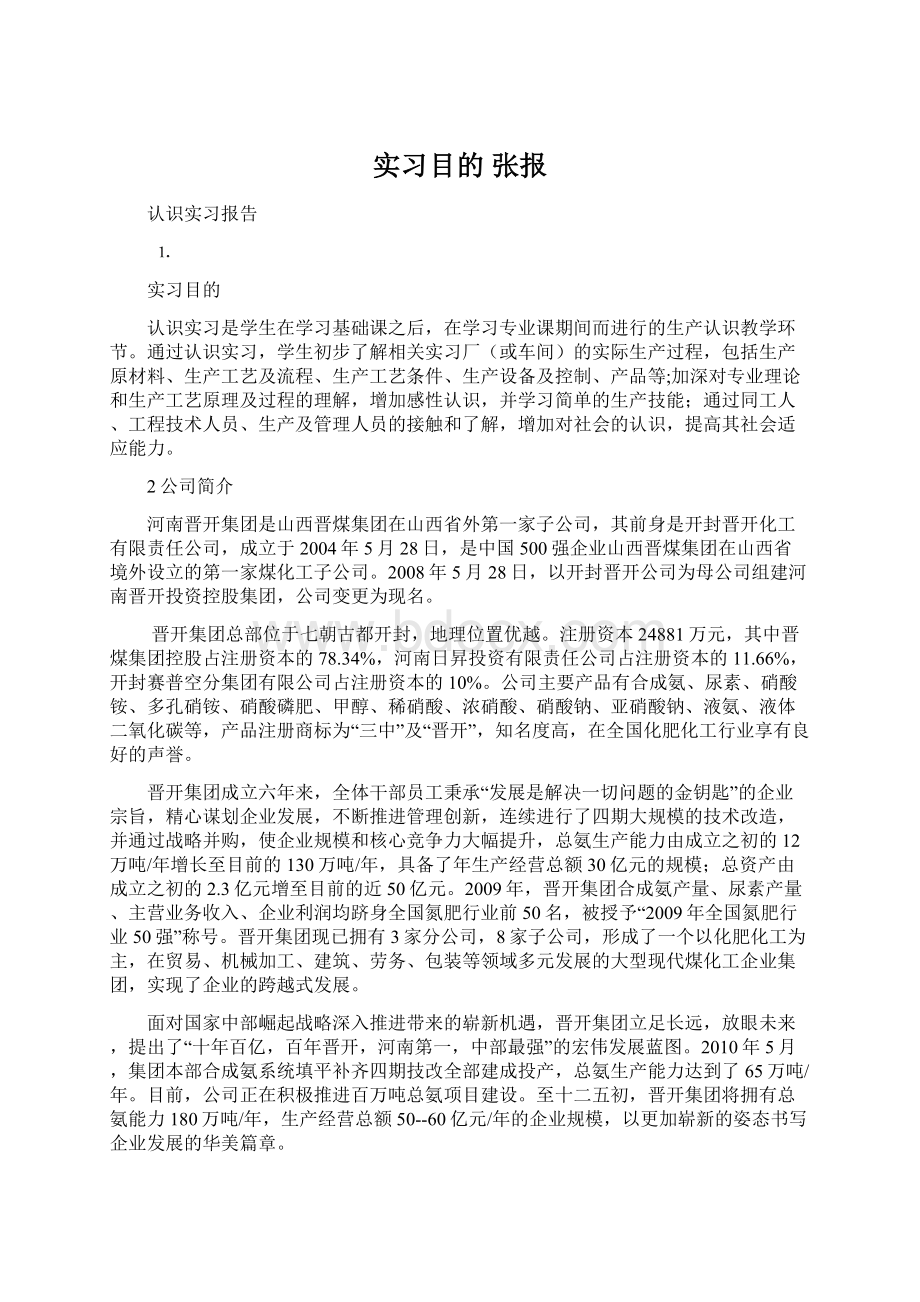
实习目的张报
认识实习报告
实习目的
认识实习是学生在学习基础课之后,在学习专业课期间而进行的生产认识教学环节。
通过认识实习,学生初步了解相关实习厂(或车间)的实际生产过程,包括生产原材料、生产工艺及流程、生产工艺条件、生产设备及控制、产品等;加深对专业理论和生产工艺原理及过程的理解,增加感性认识,并学习简单的生产技能;通过同工人、工程技术人员、生产及管理人员的接触和了解,增加对社会的认识,提高其社会适应能力。
2公司简介
河南晋开集团是山西晋煤集团在山西省外第一家子公司,其前身是开封晋开化工有限责任公司,成立于2004年5月28日,是中国500强企业山西晋煤集团在山西省境外设立的第一家煤化工子公司。
2008年5月28日,以开封晋开公司为母公司组建河南晋开投资控股集团,公司变更为现名。
晋开集团总部位于七朝古都开封,地理位置优越。
注册资本24881万元,其中晋煤集团控股占注册资本的78.34%,河南日昇投资有限责任公司占注册资本的11.66%,开封赛普空分集团有限公司占注册资本的10%。
公司主要产品有合成氨、尿素、硝酸铵、多孔硝铵、硝酸磷肥、甲醇、稀硝酸、浓硝酸、硝酸钠、亚硝酸钠、液氨、液体二氧化碳等,产品注册商标为“三中”及“晋开”,知名度高,在全国化肥化工行业享有良好的声誉。
晋开集团成立六年来,全体干部员工秉承“发展是解决一切问题的金钥匙”的企业宗旨,精心谋划企业发展,不断推进管理创新,连续进行了四期大规模的技术改造,并通过战略并购,使企业规模和核心竞争力大幅提升,总氨生产能力由成立之初的12万吨/年增长至目前的130万吨/年,具备了年生产经营总额30亿元的规模;总资产由成立之初的2.3亿元增至目前的近50亿元。
2009年,晋开集团合成氨产量、尿素产量、主营业务收入、企业利润均跻身全国氮肥行业前50名,被授予“2009年全国氮肥行业50强”称号。
晋开集团现已拥有3家分公司,8家子公司,形成了一个以化肥化工为主,在贸易、机械加工、建筑、劳务、包装等领域多元发展的大型现代煤化工企业集团,实现了企业的跨越式发展。
面对国家中部崛起战略深入推进带来的崭新机遇,晋开集团立足长远,放眼未来,提出了“十年百亿,百年晋开,河南第一,中部最强”的宏伟发展蓝图。
2010年5月,集团本部合成氨系统填平补齐四期技改全部建成投产,总氨生产能力达到了65万吨/年。
目前,公司正在积极推进百万吨总氨项目建设。
至十二五初,晋开集团将拥有总氨能力180万吨/年,生产经营总额50--60亿元/年的企业规模,以更加崭新的姿态书写企业发展的华美篇章。
3实习要求
2010年11月2日,我们进公司的第一天,进行了进入工厂车间前的安全教育。
由工厂的安保管理人为我们做了工厂劳动保护、安全技术、放火、防爆、防毒以及保密等内容的安全生产教育。
晋开化肥厂的生产作业多为高温、高压、易燃易爆的高危企业。
原料化肥生产中的氨气、CO有毒气体、H2易燃易爆,液氨有毒,若做不好有效地安全防范工作,很容易发生事。
此外,晋开化肥厂还有许多转动设备如压缩机、透平机、鼓风机、泵等;装置中有较大的大型水槽、灌等;生产过程中几乎都在高、低温以及高、中压条件下进行。
这就要求我们认识实习人员务必要遵守工厂内的操作规章,不能乱摸乱碰,以免伤害自己或造成公司损失。
进工作区域之前惊醒相当的安全教育后舍非常必要的。
4.实习安排
我们在晋开集团参观实习3天,主要实习车间有:
净化车间、合成车间、尿素合成车间、联合车间和造气车间,主要熟悉各个车间的设备和工艺流程;为以后专业课程的学习打下一定的基础。
5.生产流程
5.1造气车间:
原料气的制造
原料:
空气、煤
产品:
CO、H2、CO2、H2S、CH4、N2(其中CO、H2即半水煤气为有用气体)
5.1.1工艺方法:
蓄热法即用空气和蒸汽分别送入燃料层,也称间歇气化法先送空气以提高燃料层温度,生成吹风气大部分放空;然后,送入蒸汽进行气化反应,导致燃料层温度下降,所得水煤气配部分吹风气成为半水煤气。
工业上间歇式气化过程,是在固定层煤气炉中进行的。
燃料层从上到下可分为:
干燥层,干馏层,气化层,灰渣层;燃料层温度随空气的加入升高,蒸汽的加入而下降。
每个工作循环一般可分为5个阶段:
1.吹风:
底部送入空气,提高燃料层温度,吹风气放空;
2.上吹制气:
从下加蒸汽,燃料层下部温度下降,上部因煤气通过上升;
3.下吹制气:
从上加蒸汽,燃料层温度趋向平衡;
4.二上吹:
从下加蒸汽,将底部煤气排空,为吹风准备;
5.吹净:
从下加空气吹风,将二上吹制得煤气回收,给半水煤气中加氮。
吹气过程主要反应:
C+O2=CO2+Q
2C+O2=CO2+Q
2CO+O2=2CO2+Q
CO2+C=2CO+Q
制气过程主要反应:
C+H2O=CO+H2–Q
C+2H2O=CO2+2H2–Q
CO2+C=2CO–Q
CO+H2O=CO2+H2+Q
5.1.2工艺条件:
操作温度:
略低于燃料灰熔点,维持不结疤的最高温度。
吹风速度:
高时反应快,CO含量低,热损失少,但燃料损失大,会出现风洞、吹翻。
蒸汽用量:
上吹时热损失大,时间要小于下吹,可适当加空气(加氮),使燃烧放热。
燃料层高度:
高有利于蒸汽分解,但阻力大。
循环时间分配:
根据燃料性质。
工艺流程图如下:
5.2净化车间
原料气的净化
脱硫,变换,脱碳,气体的精制.
5.2.1脱硫
晋开化肥厂使用固体煤作为合成原料,在原料气生成反应时会生成含有一定成分的硫化物,主要是H2S,其次是CS2,COS,RSH等有机硫。
其含量取决于原料的含硫量及其加工方法,以煤为原料时,所得原料气中H2S含量一般为2~3g·m-3,有的高达20~30g·m-3。
由于H2S对合成氨生产有着严重的危害,它对设备和管道有腐蚀作用,可使变换及合成系统的催化剂中毒,还可使铜洗系统的低碳钢生成硫化亚铜沉淀,使操作恶化,增加铜耗。
按脱硫剂的状态可分为干法和湿法两种。
前者是用固体脱硫剂(如氧化锌、活性炭、分子筛等)将气体中的硫化物吸收除掉;后者用碱性物质或氧化剂的水溶液即液体脱硫剂(如氨水法、碳酸盐法、乙醇胺法、腐酸二磺酸钠法及砷碱法等)吸收气体中的硫化物。
干法脱硫的优点是既能脱无机硫,又能脱有机硫,可把硫脱至极微量。
干法的共同缺点是脱硫剂不能再生。
湿法脱硫采用液体脱硫,便于再生并能回收硫,易于构成连续脱硫循环系统,可采用较小的设备脱除大量硫化物。
湿法的缺点是对有机硫脱除能力差,且净化度不如干法高。
脱硫后的气体中含硫量,依合成氨工艺过程有所差异。
气态烃蒸汽转化法中的镍催化剂对硫十分敏感,脱硫后的气体中含硫量要求低于5ug·g-1。
5.2.2变换
用煤或烃生产出的气体都含有相当量的CO,例如固体燃料制得的半水煤气中含28%-31%,气体烃蒸汽转化法中含15%~18%,重油气化法含46%左右。
变换利用水蒸气把CO变换为H2,既将CO转变成易于清除的CO2,同时又制得了所需的原料气H2。
其反应为:
CO+H2O(g)=CO2+H2ΔH0=-41kJ·mol-1
这是一个体积不变的可逆放热反应,只有在催化剂的作用下才能大规模生产。
温度、反应物组成及催化剂性能都是影响平衡转化率的因素。
nCO:
nH2O=1:
1时,在500K温度下,转化率为92.1%;400K下,则可达97.5%;当温度为500K时,nCO:
nH2O=1:
6,转化率可提高到99.8%。
中变催化剂的铁铬或铁镁催化剂反应温度高,反应速度大,有较强的耐硫性,价廉而寿命长。
低温的铜系催化剂则正相反。
为了取长补短,工业上采用中变低变串联的流程。
原料气约320—380℃进入中变一段后温度升至450—500℃,用水蒸气冷激到380℃后再进行中变二段反应。
温度升到425~450℃,转化率达90%,反应后气体喷入水蒸气,使温度下降并使剩余水蒸气成饱和水蒸气。
经废热锅炉2冷却到330℃,热交换器冷却至200℃,除去其中的冷凝水,再进入低变,变换后温度上升15—20℃,转化率可达99%。
压力对平衡无影响,所以变换可在常压下进行。
国内中型厂用1.5~3.0MPa加压变换,小型厂0.2~0.8MPa加压变换。
加压变换的缺点是对设备腐蚀严重。
5.2.3脱碳
变换气中含有大量的二氧化碳(15%一35%),一方面它的存在对原料气的进一步精制及氨合成不利;另一方面,它也是制造尿素、纯碱、碳酸氢铵等的原料。
因此,变换气中的二氧化碳必须清除,并加以回收利用。
脱除二氧化碳的方法很多,工业上常用的是溶液吸收法,分为物理吸收和化学吸收两种。
物理吸收是利用二氧化碳能溶于水和有机溶剂的特点。
常用的方法有加压水洗、低温甲醇洗涤等。
如在3MPa、-30—-70℃下,甲醇洗涤气体后气体中的CO2可以从33%降到10μg·g-1,脱碳十分彻底。
化学吸收是用氨水、有机胺或碳酸钾的碱性溶液为吸收剂,利用二氧化碳能与溶液中的碱性物质进行化学反应而将其吸收。
小型合成氨厂用氨水吸收变换气中的二氧化碳就属化学吸收脱碳法,大中型厂多采用改良热碱法,以K2CO3水溶液为吸收液,并添加少量活化剂如氨基乙酸或乙二醇胺,缓蚀剂如V2O5等。
吸收解吸反应如下:
K2CO3+CO2+H2O=2KHCO3
当吸收液中添加氨基乙酸,吸收压强2~3MPa、温度85~100℃时,气体中的CO2可从20~28%降至0.2%~0.4%;解吸压强为10~30kPa,温度105~110℃
5.2.4气体的精制
经净化过的气体仍有少量的CO(等有害气体)。
气体的精制就是要将它们进一步脱除,晋开化工厂采用铜洗法。
铜洗法即醋酸铜氨液洗涤法:
由醋酸铜和氨通过化学反应配成的铜液中含有氨及醋酸亚铜络二氨等有效成分,在加压的情况下与CO、CO2生一系列化学反应将其脱除。
反应式为
CO(液相)+Cu(NH3)2Ac+NH3(游离)=[Cu(NH3)3CO]Ac+Q
2NH3+CO2+H2O=(NH4)2CO3+Q
(NH4)2CO3+CO2+H2O==2NH4HCO3+Q
反应在铜洗塔中进行,吸收后的铜液送到再生器中,用减压和加热方法解吸后铜液循环使用。
铜液不仅可以吸收CO,CO2,还可以同时吸收O2和H2S。
5.3压缩车间(联合车间)
此车间的作用是对净化后的气体进行压缩,有的企业在此车间处进行气体的压缩外还进行甲醇气体的合成。
晋开化肥厂就属于后者。
在此车间有脱硫工序后净化的半水煤气,在常温及1.3KPa左右的压力下及如压缩机第一段气缸,压缩到压力为0.25MPa、温度为154°C左右排出,经过一段水冷凝器到室温,然后静如油水分离器对油水进行分离后进入第二级气缸压缩,压缩至1.04MPa排出,然后进入第二级油水冷却和油水分离,降温并排出油水后,去变换工序将一氧化碳变换成二氧化碳,来自变换岗位的气体压力大约在0.8MPa,进入压缩系统气体三段缓冲分离器,除去所夹带的水分后在进入第三级压缩气缸,压缩至2.8MPa,然后依次进入第三级的冷凝和油水分离器,去脱碳工序除去原料气中的大部分二氧化碳。
在进入第四阶段的缓冲分离器,依次进入第四阶段气缸、水冷器和油水分离器、第五阶段、水冷器、水分离器。
及压缩后压力达到14.0MPa.最后在经过第六级压缩至31.4MPa.及冷却和油水分离后一部分进行甲醇的合成,另一部分送往氨的合成车间。
在压缩阶段所采用的压缩机类型有离心式压缩机、往复式压缩机、汽轮式压缩机等,晋开厂所采用的是往复式。
5.3.1甲醇的合成
用合成气合成甲醇,按照压力高低一般分为高压法(340-420℃,30-50MPa下用锌-铬氧化物作催化剂)、中压法(10-27MPa,235-315℃条件下)、低压法(5MPa,275℃左右采用铜基催化剂)。
一般选用中压法合成甲醇。
主要设备有甲醇合成塔、水冷却塔、甲醇分离塔、循环压缩机等。
大概流程如下:
5.4合成车间(氨合成)
合成氨概述
合成氨工业诞生于本世纪初,其规模不断向大型化方向发展,目前大型氨厂的产量占世界合成氨总产量的80%以上。
氨是重要的无机化工产品之一,在国民经济中占有重要地位。
除液氨可直接作为肥料外,农业上使用的氮肥,例如尿素、硝酸铵、磷酸铵、氯化铵以及各种含氮复合肥,都是以氨为原料的。
合成氨是大宗化工产品之一,世界每年合成氨产量已达到1亿吨以上,其中约有80%的氨用来生产化学肥料,20%作为其它化工产品的原料。
德国化学家哈伯1909年提出了工业氨合成方法,即“循环法”,这是目前工业普遍采用的直接合成法。
反应过程中为解决氢气和氮气合成转化率低的问题,将氨产品从合成反应后的气体中分离出来,未反应气和新鲜氢氮气混合重新参与合成反应。
合成氨反应式如下:
N2+3H2≈2NH3
合成氨的主要原料可分为固体原料、液体原料和气体原料。
经过近百年的发展,合成氨技术趋于成熟,形成了一大批各有特色的工艺流程,但都是由三个基本部分组成,即原料气制备过程、净化过程以及氨合成过程。
现代大型合成氨厂大多数以天然气为原料,生产过程中,天然气经脱硫、转化及变换等工序,制得合成氨的粗原料气,它的主要成分为H2,N2,CO2。
粗原料气经净化(包括脱碳和甲烷化工序),制得合成氨所需的H2,N2混合气体。
H2、N2混合气体经压缩后送入合成工序合成制得氨,后由冷冻工序提供冷源值得分离产品氨。
上述工艺过程大致可分为制气、净化和合成三个部分。
此外还有一套完整的蒸汽动力系统穿插于各个工序内。
合成氨技术的发展
近年来,氨合成工艺技术已取得长足进步。
特别是市场经济体制的建立,各氮肥企业为了在市场竞争中走在前列,纷纷围绕节能降耗,加大技改力度,为氨合成技术的新发展提供了一个平台。
在此形势下,各企业对氨合成装置的要求,逐渐由以前的强化高负荷生产转变到现在的轻负荷低消耗运行模式
5.4.1氨的主要特点
氨在标准状态下是无色气体,比空气密度小,具有刺激性气味。
会灼伤皮肤、眼睛,刺激呼吸器官粘膜。
空气个氨质量分数在0.5%-1.0%时,就能使人在几分钟内窒息。
氨的相对分子质量为17.3沸点(0.1013MPa)-33.5C冰点一77.7C,临界温度132.4C,临界压力ll.28MPa.液氨的密度0.1013MPa、-334C为0.6813kg?
L‘。
标准状态下气氨的密度7.714×10E4 kg-L 摩尔体积22.08L?
mol-1液氨挥发性很强。
气化热较大。
氨基易挥发,可生产含氨15%~30%(质量)的商品氨水,氨溶解时放出大量的热。
氨水溶液呈弱碱性,易挥发。
液氨和干燥的气氨对大部分材料没有腐蚀性,但是在有水存在的条件下。
对铜、银、锌等金属有腐蚀性。
氨是一种可燃性物质,自然点为630C,一般较难点燃。
氨与空气或氧的混合物在一定范围内能够发生爆炸,常压,室温下的爆炸范围分别为15.5%~28%和13.5%~82% 氨的化学性质较活泼,能与碱反应生成盐。
5.4.2合成氨工艺的流程
1、分流进塔:
反应气分成两部分进塔,一部分经塔外换热器预热,依次进入塔内换热管、中心管,送到催化剂第一床层,另一部分经环隙直接进入冷管束,两部分气体在菱形分布器内汇合,继续反应,这样使低温未反应气直接竟如冷管束,稍加热后,作为一、二段间的冷激气,从而减少冷管面积和占用空间,提高了催化剂筐的有效容积,并强化了床层温度的可调性。
同时仅有65~70%的冷气进入塔内换热器和中心管,减轻了换热器负荷,因而减少了换热面积,相对增加了有效的高压容积,也使出塔反应气温度提高(310~340℃),即回收热品位提高。
气体分流进塔还使塔阻力和系统阻力比传流程小。
2、进塔外换热器的冷气不经环隙,这样温度更低,使进水冷器的合成气温度更低(约75℃左右),提高了合成反应热的利用率,降低了水冷器的负荷和冷却水的消耗。
3、水冷后的合成气直接进入冷交管间,由上而下边冷凝边分离,液氨在重力和离心力的作用下分离,既提高了分离效果,又减小了阻力。
4、塔后放空置于水冷、冷交后,气体经连续冷却,冷凝量多,因此气体中氨含量低,惰气含量高,故放空量少,降低了原料气消耗。
5、塔前补压:
循环机设于冷交之后,气体直接进塔,使合成反应处于系统压力最高点,有利于反应,同时循环机压缩的温升不消耗冷量,降低了冷冻能耗。
6、设备选用结构合理,使消耗低,运行平稳,检修量减少,工艺趋于完善。
7、选用先进的自控手段,如两级放氨,氨冷加氨,废锅加水,系统近路的控制,均用了DCS计算机集散系统自动化控制,冷交、氨分用液位检测采用国内近几年问世的电容式液位传感器等新技术使操作更加灵活、平稳、可靠,降低了操作强度。
5.4.3合成氨工艺流程图
5.4.4氨合成工艺条件
(1)温度:
合成塔壁≤150℃
进塔主气流175℃-185℃
分流气出塔150℃-160℃
零米360℃-380℃
一段热点460℃-470℃
二段进口400℃-430℃
废锅进口310℃-340℃
废锅出口190℃-200℃
水冷进口≤75℃
水冷出口≤30℃
氨冷出口0—5℃
(2)压力:
系统压力≤31.4Mpa
输氨压力≤1.9Mpa
放氨压力≤2.55Mpa
氨蒸发压力≤2.45Mpa
废锅蒸汽压力≤1.3Mpa
总回收压力:
0.4-0.7Mpa
(3)气体成分:
补充气CO+CO2≤20PPm
进塔H2/N22.0-2.8
进塔CH4+Ar20%
进塔NH3%:
≤2.5%
5.4.5氨的净化和输送
合成车间液氨仓库经液氨升压泵加压后的原料液氨,压力大于
,温度约<20
直接送入尿素生产车间27米楼面的液氨过滤器,进入液氨缓冲槽原料室。
来自一段循环系统冷凝器回收的液氨,自氨冷凝器A、B流入液氨缓冲槽的回流室,其中一部分液氨正常为60%,作为一段吸收塔回流液氨用,而其余液氨经过液氨缓冲槽的中部溢流隔板,进入原料室与新鲜原料液氨混合后一起至高压氨泵,这样可使液氨保持较低的温度以减少高压氨泵进口氨气化。
氨缓冲槽压力维持在
左右,设置在高为23米平面上,是为了具有足够的压头,使液氨回流进入一段吸收塔,同时也为了保证高压氨泵所需要的吸入压头。
氨缓冲槽原料室的液氨,进入高压氨泵(单动卧式三联柱塞泵、打液能力为每台
,反复次数180次/分、电动机250KW、三台高压氨泵一台备用)将液氨加压
5.4.6主要设备特点
(1)合成塔
进入合成塔的其他主要由两部分组成,一部分是占气体总量65%-70%的主反应气,从塔底进入位于塔内最底层的换热器和中心管进行加热,升温至360℃-370℃,进入第一催化剂床层反应,反应温度达到470℃-480℃,,另外一部分为为热护气和冷护气的混合气体,约占总气体量的30%-35%,由下而上进入合成塔内件与壳层的环隙,从塔顶顶部进入催化剂层冷管束,被管外热气加热至250℃,上升至冷激分气盒进入催化剂第二床层。
主反应气与热护气和冷护气的混合气体在第一反应床层混合后依次进入第二、第三床层反应。
进入合成塔内件与壳层环隙的气体主要起保护作用:
因为合成氨的反应条件为高温高压,而塔设备的材料决定了其只能在反应时承受高温或者高压,而不能同时承受高温高压,进入环隙的保护气在加压后压力和塔内的压力相当,避免了塔内件承受高压而只承受高温,同时气体处于低温状态可以吸收反应放出的热量,避免了塔的壳层承受高温而只承受高压。
反应放出的热量对保护气加热也实现了能量的充分利用。
(2)一段转化炉
一段转化炉为方格式炉子,整个炉子由辐射段、过渡段、对流段、出口烟道、引风机组成。
辐射段是炉子的主体,里面设置完成转化过程的“竖琴”系统,它由进口急风管、猪尾管、转化管、下集气管、上升管和输气总管组成、炉顶设烧嘴向下喷烧供热,对流段有多组换热器,用烟道气加热其他介质。
原料气脱硫后,则希望以比较经济的方法将原料气转化生成氢气。
原料气蒸汽混合气与镍催化剂接触,同时提高温度和压力来促进此反应。
该反应是一吸热反应,需要一段炉供给恒定的热量以维持适合一段转化反应的温度。
在一段炉和二段炉中,催化剂促使两个同时发生的平衡反应,它们是蒸汽-甲烷反应:
但事实上不是这样的,二段炉出口气中含有大量的CO,大部分未变换的CO再变换中氧化成
从而提高产氢率。
一段转化炉炉管内装有环状或圆柱状的镍催化剂,各炉管内催化剂装填应均匀,从而保证其压降相等,使通过每根转化管的气体分配均匀。
如果某根转化管的压降不正常,则可能会发生过热或转化不充分,造成操作不正常。
(3)二段转化炉
二段转化炉为立式圆筒形反应器。
受压主体为碳钢制圆筒壳,两端为锥形封头,由于内部温度高,在壳外部有水夹套,这样既可降低壳体温度,也可是壳体受热均匀。
空气-蒸汽由混合器均匀喷出,工艺气则通过带孔的环形分布板,这样可保证空气-蒸汽和工艺气均匀混合燃烧。
转化炉下部为带孔的耐火金刚玉砖拼成的球形承重拱。
出一段炉的经部分转化的气体经过一段有水夹套的输送管线107-D,沿切线方向进入二段炉(103-D)的入口室,二段转化炉进口的温度大约830
。
一段转化后的气体仍含有较多的甲烷,为了进一步转化则需要更高的温度。
这个任务在内热式二段炉里完成。
在此加入空气,于是气体中的
,同时气体中的
、CO也可能燃烧,放出大量的热,温度可达1200-1250
,因此,残余的
继续转化。
出口温度降到900-1000
左右。
进入二段转化的空气,也为合成提供了N2。
(4)热交换器
热交换器为管式换热器,进热交换器的冷气不经过合成塔的间隙,这样使温度更低,使进水冷器的合成气温度更低,提高了合成反应热利用,同时也降低了水冷器的负荷和冷却水的消耗。
(5)循环机
循环机设与冷交换热气之后,气体经循环机加压后直接进塔,使合成反应处于系统压力最高点,有利于反应。
气体在设备中流动和反应都会使得整个体系的压力降低,循环机起到补充系统压力的作用
上来。
因此氨合成的关键设备合成塔,在同等规模条件下,也逐渐的被大塔取代,出现了“大马拉小车”的局面。
一些Φ1200、Φ1500、Φ1600、Φ1800、Φ2000的大直径塔逐渐被研制出来,并投入到工业生产中去。
伴随着大直径塔的使用,氨合成系统工艺运行条件发生了变化。
低温低压氨合成催化剂的应用,也是企业节能降耗可行途径之一。
大直径塔及低温低压催化剂的使用,加大了企业的设备投入。
企业势必采取各种措施保持装置长周期运行,以求得更多的有效生产时间。
因此,原料气的净化度高,避免催化剂中毒,至关重要。
积极使用原料气净化新技术,实现原料气微量(CO+CO2)趋近于“零”,避免铜液、油水入塔,最大限度的减少毒物对催化剂的影响将会被人们逐渐重视。
6.环境保护
晋开化工集团对于环保的努力(以尿素项目开工前的评价为例)
虽然在厂里面实习了仅仅几天时间,但是我明显的感觉到了晋开化工集团对于环境保护的重视。
在其年产50万吨合成氨、52万吨尿素及配套装置项目开工之前,集团聘请开封市环境科研设计所进行了环境影响评价,评价的目的是
(1)分析本项目的建设与国家产业政策的相符性,论证厂址可行性;程、产污环节及污染物排放情况;
(3)调查监测评价区域环境质量现状,明确环境保护目标;
(4)预测本项目投产后污染物排放对周围环境影响的程度和范围,并对其进行影响评价,给出影响结论;
(5)分析论证本项目拟采取的污染防治措施的技术经济可行性;
(6)分析本项目清洁生产水平,并
(2)通过同行业类比、查阅数据手册和物料平衡等方法,分析本项目工艺流提出持续清洁生产的建议
(7)分析本项目完成后全厂污染物排放量是否符合区域总量控制要求;
(8)预测环境风险事故发生后对周围环境及