毕业设计基于AT89C51单片机的大型电力机车自动停车器的设计.docx
《毕业设计基于AT89C51单片机的大型电力机车自动停车器的设计.docx》由会员分享,可在线阅读,更多相关《毕业设计基于AT89C51单片机的大型电力机车自动停车器的设计.docx(56页珍藏版)》请在冰豆网上搜索。
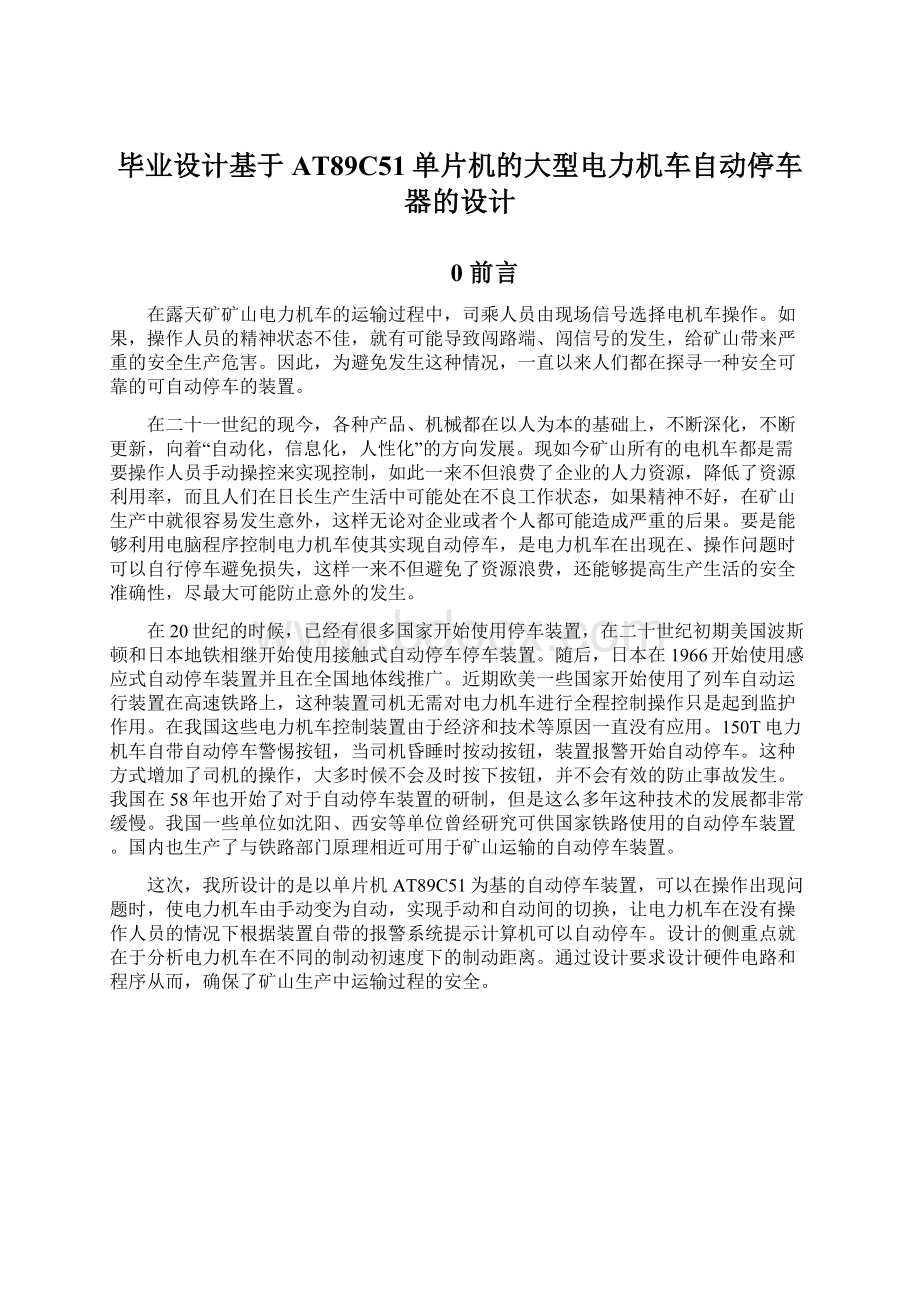
毕业设计基于AT89C51单片机的大型电力机车自动停车器的设计
0前言
在露天矿矿山电力机车的运输过程中,司乘人员由现场信号选择电机车操作。
如果,操作人员的精神状态不佳,就有可能导致闯路端、闯信号的发生,给矿山带来严重的安全生产危害。
因此,为避免发生这种情况,一直以来人们都在探寻一种安全可靠的可自动停车的装置。
在二十一世纪的现今,各种产品、机械都在以人为本的基础上,不断深化,不断更新,向着“自动化,信息化,人性化”的方向发展。
现如今矿山所有的电机车都是需要操作人员手动操控来实现控制,如此一来不但浪费了企业的人力资源,降低了资源利用率,而且人们在日长生产生活中可能处在不良工作状态,如果精神不好,在矿山生产中就很容易发生意外,这样无论对企业或者个人都可能造成严重的后果。
要是能够利用电脑程序控制电力机车使其实现自动停车,是电力机车在出现在、操作问题时可以自行停车避免损失,这样一来不但避免了资源浪费,还能够提高生产生活的安全准确性,尽最大可能防止意外的发生。
在20世纪的时候,已经有很多国家开始使用停车装置,在二十世纪初期美国波斯顿和日本地铁相继开始使用接触式自动停车停车装置。
随后,日本在1966开始使用感应式自动停车装置并且在全国地体线推广。
近期欧美一些国家开始使用了列车自动运行装置在高速铁路上,这种装置司机无需对电力机车进行全程控制操作只是起到监护作用。
在我国这些电力机车控制装置由于经济和技术等原因一直没有应用。
150T电力机车自带自动停车警惕按钮,当司机昏睡时按动按钮,装置报警开始自动停车。
这种方式增加了司机的操作,大多时候不会及时按下按钮,并不会有效的防止事故发生。
我国在58年也开始了对于自动停车装置的研制,但是这么多年这种技术的发展都非常缓慢。
我国一些单位如沈阳、西安等单位曾经研究可供国家铁路使用的自动停车装置。
国内也生产了与铁路部门原理相近可用于矿山运输的自动停车装置。
这次,我所设计的是以单片机AT89C51为基的自动停车装置,可以在操作出现问题时,使电力机车由手动变为自动,实现手动和自动间的切换,让电力机车在没有操作人员的情况下根据装置自带的报警系统提示计算机可以自动停车。
设计的侧重点就在于分析电力机车在不同的制动初速度下的制动距离。
通过设计要求设计硬件电路和程序从而,确保了矿山生产中运输过程的安全。
1设计总纲
1.1电力机车制动概述
1.1.1制动距离的影响因素
影响电力机车的制动因素有很多,如“制动机形式、闸瓦的数量、闸瓦的材料及其磨损程度、列车自重与载重、运行线路坡度、曲率半径等”。
但是当客观条件固定的时候,制动距离仅受制动初速度的影响。
设制动初速度为VH,Sm为制动距离。
由矿山铁路电力机车运行规程要求可知,在不同线路上电力机车会限制速度。
例如,在架线区段行车速度限制在50公里/时以下;旁架线区段行车速度必须在20公里/时以下。
为了安全生产,无论电力机车在什么制动初速度时,都不可以发生闯路端、闯信号等事故。
由此,我做了一些制动实验,实测在不同客观条件下制动初速度不同时的制动距离。
我将测出的实际值与理论值做了比较,又对照参考文献所提供的参数,得出计算方程式:
(1-1)
由上式可得出电力机车制动曲线,如图1—1。
图1-1制动曲线
Fig.1-1Brakingcurve
1.1.2电力机车制动特点
制动过程中,会受到风阻、管路长度等因素影响,我们设
为靠惯性所走的空走距离,
为闸瓦动作后到电车停下来的这段距离——实制动距离。
而制动距离是由空走距离和实制动距离组成,形成公式入下:
(1-2)
实验过程中证实制动距离与制动初速度VH的有关,制动初速度不同,相对应的制动距离也不相同。
由制动曲线(如图1-1)可以看出,制动距离随着制动初速度的递增而递增,并且一一对应。
设计这个自动停车装置的目的是在电力机车由手动转为自动停车后,无论在何种制动初速度下都能够在误差允许的情况下停在预定点附近,确保电车失控后达到理想的停车目的,保证生产生活的安全性。
1.2判别电力机车运行方式
1.2.1判别的运行方式的重要意义
不同的行车方式会为选择停车方案来困难。
触发信号接收装置会受到客观条件的限制,所以只能够安装在电力机车上。
当机车在前方尾车在后做牵引时,位置信号由安装在行车前端以方便位置信号的接收;当尾车在前机车在后时,电力机车为顶推运行,尾车行驶出去一段距离后,机车才到达触发位置。
如此一来,无论采用哪种行车方式都不能使电力机车停在指定位置。
如果改变触发器放置的位置就只能满足一种行车方式,而矿山行车路端的长度是一定的。
为了使电力机车能够停在指定位置,如何让确定行车方式就变得十分重要。
1.2.2判别方法
电力机车在不同的行车方式下,其驾驶方式也是不同的,可以根据这一点来辨别行车方式。
在电力机车运行时司机所在的驾驶台一定向前行驶,为了方便识别我把两个驾驶台设为1号驾驶台和2号驾驶台。
而司机所在的操作台的控制手柄一定要置放于前,并非前进方向的驾驶台上的手柄就要置零。
当控制手柄在机车行进方向时,就可以靠空余触点发出位置信号。
从而判别出运行的驾驶台,由此判断行车方式。
但列车编组比较频繁,挂列方向不能始终保持一致。
有时挂在1号,有时挂在2号。
换言之,列车挂在1号方向,则2号操作为牵引,1号操作为顶推。
在2号方向挂车时则相反。
为适应现场的实际情况,设计了一个简单的按钮电路,见图1-2。
假设列车挂在2号驾驶台侧,在1号驾驶台操作即为牵引运行。
列车编组完毕后,随即将“1号牵引”按钮按下。
如列车挂在1号驾驶台侧,则在2号驾驶台操作为牵引运行,此时将“2号牵引”按钮按下。
完成此动作后,从图上可以看出,无论牵引或顶推运行,都能自动识别。
当牵引运行时,继电器JL得电,其主触点闭合辅助触点断开,发出一个牵引控制脉冲;当顶推运行时,继电器JT得电,其主触点闭合辅助触点断开,发出一个顶推控制脉冲。
最坏的是触发后无识别,则继电器JL和继电器JT失电,主触点都断开。
但它们的辅助触点都闭合,串联后发出一个顶推脉冲。
这样设计的目的是以最坏的打算来避免事故的发生。
图1-2行车方式的按钮电路
Fig.1-2ThebuttoncircuitDrivingpatterns
1.3设计电力机车位置触发器
在接近路端或信号前端一定位置的架空线上,安置电磁无接触式位置触发器。
当电机车运行至该位置时,安装在电机车上的信号接收器接收到位置信号,并传送到单片机。
单片机接收到位置信号后,内部程序记为1,发出声光报警,提醒司机注意,单片机也开始对接收到的齿频脉冲计数。
此时,如果司乘人员精神状态良好,按一下复位按钮,将单片机中的记数清0,电机车继续行进,同时停车方式变为手动控制。
如果司乘人员精神不集中,没有按复位按钮,那么电机车的停车方式就是自动方式。
1.3.1电磁位置触发器工作机理
由图1-3可以看出,触发器安装在A点,AB距离130米为车长转换区,BC距离也是130米为速度检查区。
(此距离可根据实际需要而变化)。
而CD距离为108米,叫做路端区。
它是100吨电机车牵引九节自翻车,在重车、线路无坡度、无曲率、行车速度为30公里/小时的制动距离。
另外,视情况而定,可设有若干米长度的安全距离。
每个区段都有一个LED(LEDAB、LEDBC、LEDCD)来表示,当灯亮时,代表火车进入该区域。
图1-3触发器安装及触发后行车示意图
Fig.1-3Triggerinstalledanddrivingmapsaftertrigger
AB:
为车长转换区,130米.在顶推运行时,单片机接收到触发信号就发出报警命令;
BC:
为速度检查区(报警区),130米.列车在此区段行车应将车速调整到30公里/时以下;
CD:
为预制动区,108米.该区段是重列在30公里/时的制动距离;
DE:
为安全区,即为电机车停车允许的误差区,长度为15米。
假设为牵引方式。
机车牵引运行至A点时,触发器接收到的位置信号传到单片机里,单片机根据内部已经写入的程序,开始对齿频信号进行计数(LEDAB亮,其它灭),并且允许电机车继续前行130米,当进入车长转换区后至B点或附近,误差不大于1m(由于单片机从A点开始就对齿频脉冲进行计数,到脉冲数达到程序设定的数目B时),单片机就发出报警命令(LEDBC亮,其它灭),启动报警装置提醒司机注意,同时重新对齿频脉冲进行计数。
当单片机接收到的齿频脉冲数等于C时,锁定当时列车的速度及再次重新开始对齿频脉冲进行计数(LEDCD亮,其它灭),并通过单片机内的程序设定,对电机车的制动选择制动方案。
当脉冲数等于制动方案设定的齿频脉冲数时,单片机就发出制动命令,高速开关断开,放风阀排风,全部LED灭。
假设为顶推方式。
机车顶推运行至A点时,行车前端——尾部已到达B点,此时单片机就收到位置触发器的触发信号,单片机就发出报警命令(LEDBC亮,其它灭),启动报警装置提醒司机注意,同时对齿频脉冲进行计数。
当单片机接收到的齿频脉冲数等于C时,锁定当时列车的速度及重新开始对齿频脉冲进行计数(LEDCD亮,其它灭),并根据单片机内的程序设定,对电机车的制动进行控制。
余下的步骤跟顶推一样。
1.3.2接收并传输触发信号
1)接收
位置触发信号的接收由信号接收器来完成。
信号接收器由一组并联的干簧管组成,并联组装在一个条形封闭、用环氧树脂固化的壳体内。
如图1-4所示。
当信号接收器在位置传感器下经过时,任意一个干簧管触点在磁力的作用下吸合,都能使A、B之间导通,完成了位置触发信号的接收。
当接收器远离位置传感器时,干簧管触点断开,为下一次的吸合作准备。
图1-4信号接收器
Fig.1-4Signalreceivers
由于电机车的工作环境很差,再加上具体条件的制约,以及电机车在运输时有一定的摆动量,所以信号接收器里的干簧管必须是多个并联使用的。
这样就避免了单个干簧管接触不稳定,或因路面不平使干簧管未正好在位置触发器下经过,而影响监控仪的稳定性造成不必要的事故发生,以保证可靠的接收到位置触发信号。
2)传输
位置触发信号的传输由光电隔离器来完成的。
当信号接收器(即干簧管)经过位置传感器(即磁铁)下方时,将受到电磁力的作用。
在电磁力的作用下,干簧管A、B间吸合导通,电路构成通路,发光二极管中有电流流过并发光。
由发光二极管发出的光照射光电三极管,于是光电三极管饱和导通,并输出低电平,即输出一负脉冲。
这样就完成一个触发信号的传输。
图1-5信号传输器
Fig.1-5Signaltransmissiondevice
光电隔离器的电路如图1-5所示。
它是一个具有10KV耐压的光电隔离器,可以隔离10KV的高压。
图中E为高容量的1.5V干电池,R为限流电阻,A、B端为干簧管,电信号经过光电隔离器输出对人无伤害的触发信号。
根据光电隔离器资料得知,发光电流在3mA~100mA时均能正常工作。
那么,限流电阻R的阻值可用下式计算。
(1-3)
式中:
R——限流电阻(单位,KΩ);
E——电池电压(单位,V);
I——发光电流(单位,mA)。
经计算,取限流电阻R的阻值为20K。
这样,在干电池正常电压为1.5V时,发光电流为75mA,可以正常工作。
当干电池电压降到0.5V时,发光电流为25mA,也能正常工作。
因为干电池经常在工作在开路状态下,电能消耗非常小,所以只考虑干电池的存放时间。
为了确保人身安全,我们把所接收到的位置信号必须经过隔离后方能进入单片机。
因为信号接收器安装在与DC1800V架线电压接触的电机车受电弓子上,电压较高,非常危险。
如果不加一个光电隔离器,而是直接引入接线,那么当导线的绝缘皮破损时将是非常危险的。
1.3.3安装触发器
在路端或信号前选一合适的地点,在架空线上装一电磁式位置触发器。
安装在路端前的位置触发器即一块永久性磁铁,用夹具安装在架线上。
安装在电机车上的位置接收器经过时,将接收到位置信号。
安装在信号前的位置触发器则是一块受控于行车信号的电磁铁,通过信号机的辅助接点相连。
当行车信号为红灯时电磁铁有电,电机车过此位置时触发。
当行车信号为绿灯时电磁铁失电,机车不触发,可正常运行,如图1-6所示。
因列车运行时的行车速度、载重情况、坡道情况均不尽相同,所以位置触发器的安装位置应考虑到列车运行时的具体情况而设置。
具体的安装位置还应当通过实测的方法来确定。
总之,应使其在限定的最高停车速度下、在车辆满载及下坡的情况下,保证有足够的制动距离。
图1-6位置触发器的安装
Fig.1-6Positiontriggerinstalled
1.4传感器的设计
齿轮脉冲传感器的工作系统是由传感器集成电路、反偏磁铁和目标(齿轮齿)等部分组成。
传感器作用面和齿轮之间为空气隙,目标每转过一次,开关动作一次,每一次开关动作都记作一个齿频脉冲。
1.4.1霍尔齿频脉冲传感器
本次设计选用A3046/3056型霍尔效应齿频传感器。
A3046/3056作为一个基于霍尔效应的单片集成电路,主要用于目标检测,例如检测电力机车转速和运行位置。
其允许的工作电压为4V~24V,能够输出可达20mA电流,重复频率为20kHZ,可以与双极型MOS逻辑电路兼容。
A3046/3056型霍尔效应齿轮脉冲传感器的工作参数如下表1-1所示:
表1-1A3046/3056型霍尔效应齿轮脉冲传感器工作参数
Table.1-1A3046/3056HalleffectGear’spulsesensors
工作温度
-40℃~85℃
存储温度
-65~170℃
电源电压
28V
反向电池电压
-30V
输出断电压
28V
反向输出电压
-0.5V
输出电流
25mA
功耗
500mW
它具有以下特点:
1)检测铁目标可低至零速(0rpm);
2)大的有效空气隙;
3)宽的工作温度范围;
4)可用于稳定电源工作;
5)高速工作;
6)输出与全部逻辑电路兼容;
7)反向电池保护;
8)固态可靠性;
9)抗物理应力。
1.4.2安装A3046/3056传感器
在本次设计中,把霍尔效应齿轮齿传感器固化在一个铜壳内,以增加其机械强度,并利于安装。
再安装一个与车轮同步转动的圆盘。
根据需要,在圆盘周围安装数块(本例中选定为10块)磁钢(永久磁铁),组成一个与车轮同步转动的齿盘,一块永久磁钢为一个齿。
齿盘用非导磁材料铜或铝制造,以免磁钢失去作用。
将霍尔传感器安装在齿盘上方,与磁钢接近,距离齿盘顶距离δ,只要传感器端部相距齿顶距离δ≤4mm均能准确无误的将齿频信号发送出来,齿频传感器允许接进的频率很高,远远满足最高行车速度下的齿频传递。
齿盘每转过一个磁钢,传感器就发出一个脉冲,若齿盘周围装有n个磁钢。
每个脉冲相当于行车距离为:
(1-4)
式中:
S——每个脉冲相当于的行车距离(mm);
D——为车轮直径(mm);
n——为齿盘四周的磁钢数。
在本装置内部,经过单片机的检测和计算,把齿频信号处理后,可反映出行车速度、行车位置等。
齿频传感器的安装位置示意图如图1-7。
它的信号输出端将与单片机的P3.4端口相连。
图1-7霍尔传感器安装示意图
Fig.1-7ThediagramofhallsensorsInstallation
1.5设计机车制动电路
图1-8制动电路原理图
Fig.1-8TheSchematicofBrakecircuit
制动控制器由单片机、直流继电器等电路组成。
单片机的输出端P2.1在正常状态下输出低电平,直流继电器JZ得电吸合。
由直流继电器JZ再控制一个较大的继电器JO,放风筏继电器线圈串接在继电器JO1的得电常闭接点上,得电不排风。
同时,供电电源高速断路开关的继电器线圈,也串接在继电器JO2的得电常开接点上,得电吸合,维持电机车电源的正常供电。
当单片机经过内部的程序运算后,得出单片机的制动输出P2.1端输出变为高电平,继电器JZ、JO均释放。
放风阀继电器及高速断路开关继电器断电。
放风阀排风制动的同时,高速断路开关断开高压供电电源,使电机车失去牵引力,增加行车阻力,即紧急停车。
电路原理如图1-8所示。
1.6设计报警及电源装置
1)报警装置
图1-9由定时器构成的多谐振荡器
Fig.1-9Multivibratorposedbytimer
报警装置主要由555定时器和R1、RP1、C等组成的多谐振荡器来完成。
555定时器是一种模拟和数字功能相结合的中规模集成器件。
一般用双极性工艺制作的称为555,用CMOS工艺制作的称为7555,除单定时器外,还有对应的双定时器556/7556。
555定时器的电源电压范围宽,可在4.5V~16V工作,7555可在3~18V工作,输出驱动电流约为200mA,因而其输出可与TTL、CMOS或者模拟电路电平兼容。
555的主要功能取决于比较器。
当比较器C2的触发器输入端(用TR标注)V2<1/3Vcc(Vc1=1,Vc2=0)时,触发器被置位,泄放晶体管V1截止。
当比较器C1的阈值输入端(用TH标注)V1>2/3Vcc时(Vc1=0,Vc2=1),触发器被复位,V1导通。
当V1>VR1,V2>VR2时,C1、C2均输出高电平,触发器维持原状态不变。
若R(非)为低电平,则强制触发器复位。
不需要复位时R应接高电平。
这样,即可控制脉冲的宽度为94.2us。
主要功能参考表1-2。
表1-2555功能表
Table.1-2555menu
输入
输出
阈值输入V1
触发输入V2
复位R
泄放管V1
输出V0
×
×
0
导通
0
<2/3Vcc
<1/3Vcc
1
截止
1
>2/3Vcc
>1/3Vcc
1
导通
0
<2/3Vcc
>1/3Vcc
1
不变
不变
为了驱动扬声器发出有规律的声音,就用555定时器构成一个多谐振荡器如上面图1-9所示。
图1-10多谐振荡器工作波形图
Fig.1-10Multi-standardoscillator’sworkwaveformfigure
多谐振荡器工作原理。
接通电源后,VCC通过R1,RP1给以充电,Vc逐渐上升。
当Vc升到2/3VCC时,比较器C1输出低电平VC1=0,555内部RS触发器被复位,V1导通,输出V0=0,之后电容C通过RP1和V1放电,使VC下降。
当VC下降到1/3VCC时,比较器C2输出低电平VC2=0,555内RS触发器又被置位,输出V0=1变为高电平。
这时V1截止,电容C再次充电。
如此周而复始,在输出端得到一个周期性的矩形脉冲。
当控制端为高电平时,多谐振荡器振荡,报警装置发音;控制端为低电平时,多谐振荡器停振,报警装置不发音。
多谐振荡器工作波形如上面图1-10所示。
其振荡频率f=1.44/(R1+2RP1)C1,图示参数的频率在600HZ~20KHZ之间,可通过调节RP1来选定。
tw1=0.7(R1+R2)C
tw2=0.7R2C
该震荡器振荡与否,取决于复位端4脚的电平。
当4脚呈低电平时,555处于停振状态;当4脚呈高电平时,则起振,报警装置发出调定的音频信号。
整个报警电路的设计如图1-11所示。
图1-11报警电路图
Fig.1-11Thediagramofalarmcircuit
报警装置它的复位端口4脚与单片机的P2.2端口相连,受控于单片机。
当电机车收到位置触发器的触发信号时,经过单片机的内部程序检测和计算,计算出电机车进入报警区域时,就从P2.2发出高电平。
当报警装置得到发音指令(高电平),就开始发出声光报警,提醒司乘人员注意快到路端停车区了,要控制好电机车的速度。
当司乘人员完成减速工作后,想关闭正响的报警系统,就按一下复位按扭,声光报警就会停止。
复位按钮直接与单片机的P1.3端口相连。
当单片机从P1.3接收到一个高电平时,经过内部程序运算,使输出端口P2.2输出一个低电平,所以报警系统停止报警。
2)电源装置
电源装置是从电网中取得能量,经变换后对一个或多个负载提供电能的装置。
选择正确而稳定的电源装置不仅能够使系统正常工作,还能延长硬件使用寿命。
所以,电源装置的使用得当也是很重要的。
本次设计所用的电源装置的原理是从蓄电池直接引入24V电压,经过稳压变换后即可输出芯片所需要大小的电压。
如图1-12所示。
由于单片机AT89C51和8155等需要的都是+5V的稳压直流电源,所以我把24V蓄电池稳压变换输出+5V的电源。
用来对于装置供电,使装置能够正常稳定的工作。
图1-12电压变换
Fig.1-12Voltageconversion
2机车制动参数的计算
2.1机车制动方案的选择
上面介绍过,制动初速度不同,制动的距离也不会相同,因此,我们需要一些实验和计算的手段来确定在不同初速度的状态下,电力机车的制动方案,应用于设计中,使其能够有效制动。
由图1-3可知,CD制动区域的长度为108m,这是电机车以速度30km/h刚过C点时,立即制动的制动距离,这时电机车能够准确停到预定的位置(即安全区域),不会发生闯路端。
由于制动的长度已经确定,在实际中不能够随意的更改。
所以,当以低于30km/h的速度通过C时,单片机就立即对电机车进行制动,就会出现电机车的停车位置没有停在预定的区域内或离预定区域还有一段的距离,这就达不到本设计设定的方案要求。
为了满足方案的要求,现在利用单片机的强大运算能力和逻辑分析能力,对电机车的准确停车进行控制。
假设,电机车的制动距离为Sm。
若速度V小于等于30km/h时,它离预定点距离是
(2-1)
式中:
S——制动区域长度;
Sm——是电机车在初速度V时的制动距离;
S2——是电机车停车位置与预定位置的相差距离;
由后面表2-3,2-4可以经计算得到S2的距离,如表2-1。
所以,当电机车以低于30km/h的速度通过C点时,为了要将电机车停在预定的安全区域,电机车必需要继续运行S2的距离,然后才立即对电机车发出停车信号,对电机车进行制动控制。
这样才能满足方案的要求。
根据各个相差距离S2i求出各个相差距离的差的平均值:
Z3=(7-0+13-7+20-13+26-20+32-26+37-32+42-37+47-42+51-47)/10
=47/10
=4.7m(2-1)
同时得:
Z2=3.1m(2-2)
Z1=1.8m(2-3)
表2-1初速度与相差距离的对应关系表
Table.2-1Therelationtablebetweenearlyspeedanddistance
初速度km/h
制动距离m
相差
距离m
初速度km/h
制动距离m
相差
距离m
初速度km/h
制动距离m
相差
距离m
30
108
0
20
53
55
10
20
88
29
101
7
19
49
59
9
18
90
28
95
13
18
45
63
8
16
92
27
88
20
17
41
67
7
14
94
26
82
26
16
37
71
6
12
96
25
76
32
15
34
74
5
10
98
24
71
37
14
31
77
4
8
100
23
66
42
13
28
80
3
6
102
22
61
47
12
2