油品储运车间事故案例分析.docx
《油品储运车间事故案例分析.docx》由会员分享,可在线阅读,更多相关《油品储运车间事故案例分析.docx(13页珍藏版)》请在冰豆网上搜索。
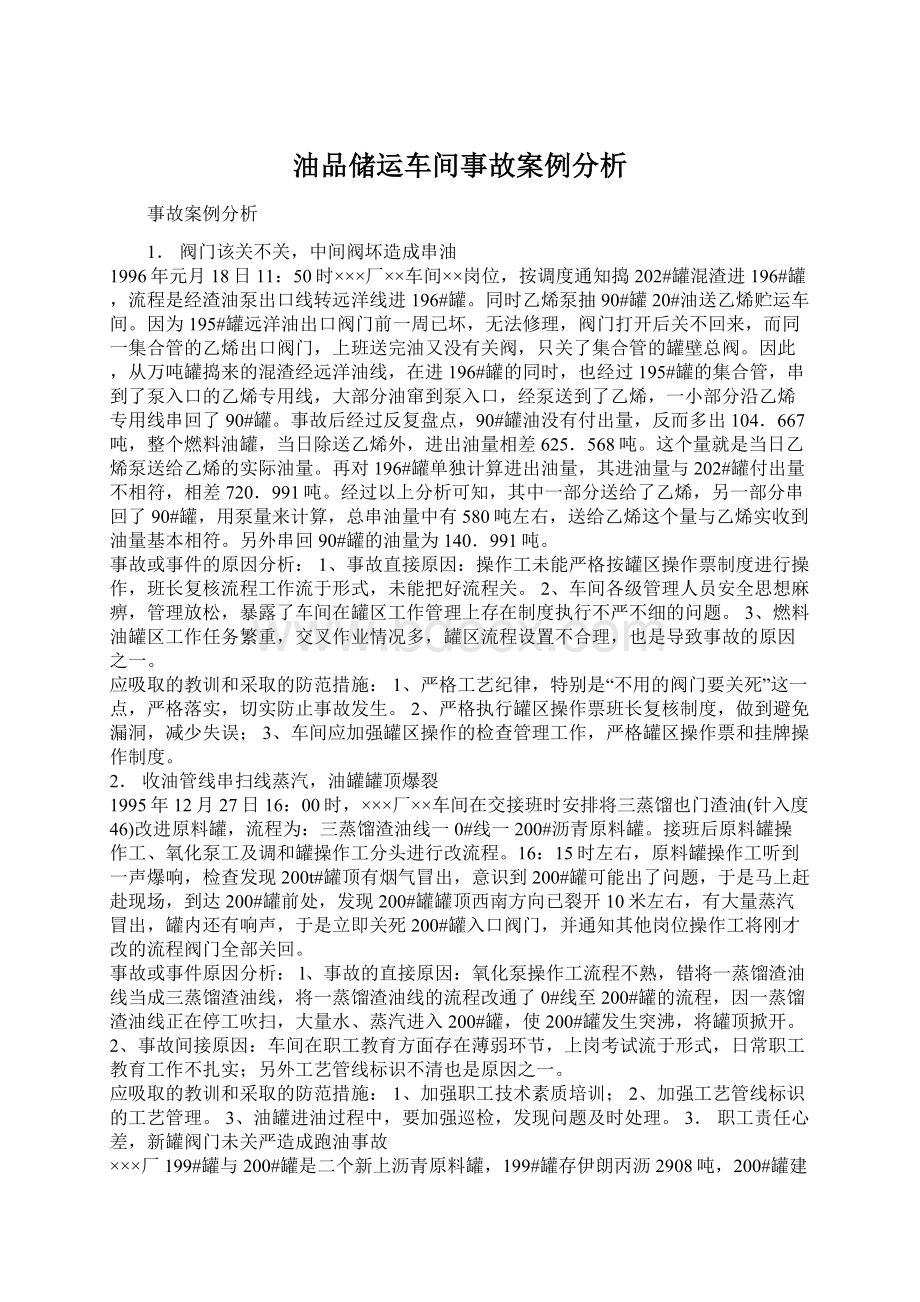
油品储运车间事故案例分析
事故案例分析
1.阀门该关不关,中间阀坏造成串油
1996年元月18日11:
50时×××厂××车间××岗位,按调度通知捣202#罐混渣进196#罐,流程是经渣油泵出口线转远洋线进196#罐。
同时乙烯泵抽90#罐20#油送乙烯贮运车间。
因为195#罐远洋油出口阀门前一周已坏,无法修理,阀门打开后关不回来,而同一集合管的乙烯出口阀门,上班送完油又没有关阀,只关了集合管的罐壁总阀。
因此,从万吨罐捣来的混渣经远洋油线,在进196#罐的同时,也经过195#罐的集合管,串到了泵入口的乙烯专用线,大部分油窜到泵入口,经泵送到了乙烯,一小部分沿乙烯专用线串回了90#罐。
事故后经过反复盘点,90#罐油没有付出量,反而多出104.667吨,整个燃料油罐,当日除送乙烯外,进出油量相差625.568吨。
这个量就是当日乙烯泵送给乙烯的实际油量。
再对196#罐单独计算进出油量,其进油量与202#罐付出量不相符,相差720.991吨。
经过以上分析可知,其中一部分送给了乙烯,另一部分串回了90#罐,用泵量来计算,总串油量中有580吨左右,送给乙烯这个量与乙烯实收到油量基本相符。
另外串回90#罐的油量为140.991吨。
事故或事件的原因分析:
1、事故直接原因:
操作工未能严格按罐区操作票制度进行操作,班长复核流程工作流于形式,未能把好流程关。
2、车间各级管理人员安全思想麻痹,管理放松,暴露了车间在罐区工作管理上存在制度执行不严不细的问题。
3、燃料油罐区工作任务繁重,交叉作业情况多,罐区流程设置不合理,也是导致事故的原因之一。
应吸取的教训和采取的防范措施:
1、严格工艺纪律,特别是“不用的阀门要关死”这一点,严格落实,切实防止事故发生。
2、严格执行罐区操作票班长复核制度,做到避免漏洞,减少失误;3、车间应加强罐区操作的检查管理工作,严格罐区操作票和挂牌操作制度。
2.收油管线串扫线蒸汽,油罐罐顶爆裂
1995年12月27日16:
00时,×××厂××车间在交接班时安排将三蒸馏也门渣油(针入度46)改进原料罐,流程为:
三蒸馏渣油线一0#线一200#沥青原料罐。
接班后原料罐操作工、氧化泵工及调和罐操作工分头进行改流程。
16:
15时左右,原料罐操作工听到一声爆响,检查发现200t#罐顶有烟气冒出,意识到200#罐可能出了问题,于是马上赶赴现场,到达200#罐前处,发现200#罐罐顶西南方向已裂开10米左右,有大量蒸汽冒出,罐内还有响声,于是立即关死200#罐入口阀门,并通知其他岗位操作工将刚才改的流程阀门全部关回。
事故或事件原因分析:
l、事故的直接原因:
氧化泵操作工流程不熟,错将一蒸馏渣油线当成三蒸馏渣油线,将一蒸馏渣油线的流程改通了0#线至200#罐的流程,因一蒸馏渣油线正在停工吹扫,大量水、蒸汽进入200#罐,使200#罐发生突沸,将罐顶掀开。
2、事故间接原因:
车间在职工教育方面存在薄弱环节,上岗考试流于形式,日常职工教育工作不扎实;另外工艺管线标识不清也是原因之一。
应吸取的教训和采取的防范措施:
1、加强职工技术素质培训;2、加强工艺管线标识的工艺管理。
3、油罐进油过程中,要加强巡检,发现问题及时处理。
3.职工责任心差,新罐阀门未关严造成跑油事故
×××厂199#罐与200#罐是二个新上沥青原料罐,199#罐存伊朗丙沥2908吨,200#罐建后未投用。
1995年8月31日17:
00时,因生产需要,管线岗位操作工梁群英打开199罐0#线出口阀,由沥青原料泵抽原料去调和罐生产重交沥青。
9月1日上午8:
30时间干部巡检时发现200#罐人孔有油流出来,造成200#罐周围约有1.8吨沥青跑损。
事故或事件原因分析:
l、事故直接原因:
操作工改动流程时,未检查出0#线与200#罐罐底线的连通阀未关,当199#罐0#线出口阀打开时,199#罐内的沥青原料从0#线经200#罐罐底阀窜入200#,因200#罐未封人孔,因此造成了跑油事故。
2、交接班制度未真正执行落实,巡回检查制度未能得到很好落实,存在走过场的现象。
吸取的教训和采取的防范措施:
1、加强工艺纪律管理,严格执行交接班制度,操作工要按要求进行巡回检查。
2、加强职工的安全意识教育,提高职工的安全工作责任心。
4.收油不巡检,油罐冒油
1993年8月17日,×××厂零点班接班后,98#罐续收丙沥A、B套沥青。
上班23:
00时该罐尺头为5.55米罐空。
0:
35时,操作工吴建恒接班后前往检查并检尺,当时98#罐空为4.46米。
检查后,直到3:
40时当班操作工才进行巡检,这时98#罐已发生冒罐事故。
当班操作工当即停止98#罐进油,并打开97#罐入口阀,让98#罐油压过97#罐,以降低液面,减少损失。
4:
05时,将丙烷A、B套送来的沥青全部改进194#罐空罐。
经计算,98#罐冒罐跑油1.5吨。
事故或事件原因分析:
l、事故的直接原因:
操作工违反了岗位巡回检查制度,不按时巡检,没有对油罐动态进行定期的检查检尺,从而导致了事故的发生。
2、事故间接原因:
职工的安全意识淡薄。
应吸取的教训和采取的防范措施:
1、认真总结冒油刮油事故教训,对职工进行全面的安全教育和责任心的教育。
2、加强工艺管理,严格执行工艺纪律,操作纪律。
5.粗心看错罐空,进油量增大冒罐
1990年5月22日,×××厂90#罐零点班交下来时的罐空为2.850m,并收残油、四线油、裂化渣油这三种油品。
202#罐存油957.695吨,在装完6个铁路槽车后,厂调度在12:
00时左右来电,通知把202#罐底油抽干净,待接三蒸馏管线用。
当时班长尹安然同志接到通知后,看了一下90#罐的罐存记录,错把21日零点班的罐空高度为9.59m,作为22日零点班的罐空高度,于12:
40时将202#罐油改进90#罐,由于90#罐的罐空看错,认为罐空较多,所以没有加强检查。
90#罐当时收四种油品,进油量较大,故14:
00时多更超过了安全高度,幸得14:
15时燃料油岗位的操作工周建同志去检查,及时发现油从透光孔冒出来,立即通知泵工将泵停下和将减四线等三种油品改进95#罐。
事故或事件原因分析:
1、工作责任心不强,工作不认真、仔细。
2、没有严格执行油罐交库制度。
应吸取的教训和采取的防范措施:
1、加强对油罐的管理制度。
2、加强对各岗位巡回检查制度的监督。
3、严格要求油槽工执行油罐交库的时间,按时去检尺作交库工作。
6.漏关中间阀污油串入沥青罐
1988年6月29日19:
45~次日0:
40时,6月28日四点班,×××厂丙烷脱沥青装置操作工说残油线憋压,可能管线不太畅通。
18:
00时,从丙烷脱沥青装置给蒸汽往原油扫线罐吹扫残油线。
我装置当班管线工梁志雄便将残油线和与残油线连接的抽出油线一起改往新146#线同时吹扫。
至29日19:
45时,当班管线工肖友兴接厂调度通知:
残油线停止吹扫,丙烷脱沥青装置出来的残油改进93#罐。
肖接通知后,即去改通抽出油线与147#线连接的阀门,再去打开93#罐的147#线进口阀,然后关闭原抽出油线与新146#线的连通阀。
但忘记关闭残油线与新146#线吹扫用的连通阀。
20:
00时,焦化装置送污油经新35#线和新146#线进我装置的扫线罐。
30日0:
40时,管线工梁志雄接肖友兴的班后进行检查,发现残油线与新146#线的连通阀未关,他立即汇报班长尹安然和车间值班员何鸿志,同到现场查看清楚后便关闭该阀。
班长尹安然一面向厂调度作了汇报,一面组织油罐操作工周建等,于1:
00时对93#罐进行检尺,结果是:
进油高度2cm,约8吨。
事故或事件原因分析:
工作不认真,检查也不过细,致改残油进93#罐时,忘记关闭残油线与新146#线吹扫用的连通,巡检也没及时发现。
应吸取的教训和采取的防范措施:
l、对装置内两条线都可走油的状态,加强管理外,可以改造而又有必要的,进行简化操作流程改造,确保安全。
2、严格执行交接班制度,真正履行十交五不接。
3、加强职工安全意识教育,增强职工工作责任心。
7.岗位间联系失调,装沥青装成渣油
1987年4月4日,×××厂204#罐减渣压往208#罐,下午15:
10时左右,渣油车台来一排(30个)车准备装200#沥青、罐工钟运强同志因外出检尺未回,所以未改好装车管线,15:
35时钟运强同志检尺未回后,才听装车工说此排车要装200#沥青,因当时接近下班时间,所以钟运强不再去改管线,但也未能及时告诉泵工不能开泵。
15:
50时装车工在做完检查槽车,放好鹤管等准备工作后,即按电铃通知泵工开泵,因运销调度说该排车要赶在18:
00时出车,泵工郭柱栋,只接到装车台电铃而未接到钟运强的通知的情况下就急于开泵装车,当班班长曾信邦发现开泵后,即向钟了解管线是否改好,钟说管线未改好,曾即打电话通知泵工停泵,开泵时间为几分钟,共有10个槽车同时装车,此10个车后经运销调度同意,改装206#罐混渣出厂。
事故或事件原因分析:
1、岗位之间的联系不足,协调性差是事故的根本原因。
2、装车管理制度不够完善。
3、职工责任心差,当班的工作临近交班时间就不想做,刻意留给下班。
应吸取的教训和采取的防范措施:
1、明确各班组、各岗位的任务,当班应做的事不能推给下班。
2、加强岗位与岗位之间的联系,互相配合,以免再出现类似事故。
3、完善装车台的管理制度。
8.关阀指令不执行造成重大跑油事故
1985年11月13日上午9:
00时,×××厂调度电话通知渣油泵房操作工麦广宏,准备进3吨抽出油入95#罐,并说明抽出油专用管线动火不能用,麦即提出走哪条管线;调度经调和管线、万吨罐岗位联系,决定将抽出油与残脱油一起走调和新146#线转旧146#线95#罐,调度通知万吨罐工谢洪基关新146#线去大坑车台阀,但此阀一直未关。
9:
10麦改通流程,10:
00时东罐区开始送油,下午13:
30时检尺搞库存,95#罐收油量仅吨,此异常情况麦不向调度及班长汇报,也不通知上下游岗位检查流程。
到16:
00时接班,接班的庞海强并没有认真检查核实95#罐的存油量,跑油继续;直到22:
00时库存,95#罐收油反而少了33吨油,才查出油往大坑车台跑了,共计跑油508吨。
事故或事件原因分析:
1、岗位间联系脱节,调和管线工知道自己岗位的146#线走油,但未联系确认相关吨罐岗位关闭新146it线去大坑阀便开始走油。
2、万吨罐岗位没有细心听清和严格执行调度的指令。
3、燃料罐岗位发现异常情况时没有引起足够的重视,安全危害意识淡薄。
4、交接班制度不落实,没有严格执行巡检制度。
应吸取的教训和采取的防范措施:
1、加强岗位与岗位之间的联系,互相配合,以免再出现类似事故。
2、严格执行罐区操作票班长复核制度,做到避免漏洞,减少失误,切实做好安当作。
3、对操作人员进行全面贯彻HSE管理体系强化培训,提高安全危害意识。
9.罐存高温渣油,收油带水突沸罐变形
1983年7月20日14:
30时,×××厂沥青装置由201#罐压渣油至88#罐,于18:
45时停止压油改用泵抽201#罐渣油往88#罐。
当时201#罐油温高达140~C,至19:
40时停止。
21日零点班2:
30时接厂生产调度通知88#罐收焦油,当班改好流程后,回复调度可以进油。
4:
55时一操作工现场检查发现88#罐有较大响声,同时罐顶冒出大量烟气,马上报告厂调度,立即停止进油,关闭罐进出口阀。
事后检查88#罐项往上掀起,顶部第一、二圈板严重变形。
事故或事件原因分析:
1、送油单位操作工未按规定提升焦油升降管,送来焦油严重带水;2、88#罐进了高温渣油,高温渣油遇水突沸,罐压力剧增震动所致。
应吸取的教训和采取的防范措施:
加强油罐管理,防止送油带水;油品调合严格按规定控制油温,同时收油要注意检查来油状况。
10.液化烃泄漏事件
2000年10月23日9:
30时×××厂球罐区泵房,在旧泵房丙烯线进行更换动火过程中,动火前用火监护人陈超对动火点周围及用火安全措施进行了一一核对落实后,同意施工单位开始动火,9:
30时,当陈超对动火现场进行巡检时,发现正对动火点不到一米处的泵-10B进口过滤器附近的压力表指示压力正在快速上升,指示值已达到安全阀定压值,但仍未见安全阀起跳。
危险!
他立刻制止了动火,并马上用水对刚动火的管线和焊渣进行降温,正准备对泵-10B入口管线进行消压时,泵-10B入口过滤器[wiki]法兰[/wiki]处垫片突然被撕裂,大量液化气喷出,他紧急对管线进行了泄压,控制了事态的发展。
由于他检查认真,及时发现了隐患,并及时采取了果断的措施,避免了一起重大火灾爆炸事故。
事故原因分析:
液化气送装车台泵入口管线距离长口径大,而且处理两端封闭的静止状念,充满液化烃的管线在太阳爆晒下,压力快速上升,系统安全阀失灵,未能起到保护作用,当压力超出一定范围时,造成法兰挚片撕裂,液化烃泄漏。
应吸取的教训和采取的防范措施:
1、加强安全阀的管理,确保压力管线和容器的安全;2、加强对看火人的安全培训,严格看火过程的动态检查制度,确保用火安全。
可能出现类似事故之处:
液化气送装车台系统各泄漏点
二、火灾、爆炸
11.测温器快速提拉,甲苯罐爆炸起火
1981年5月28目9对30分,×××厂油品车间l59#甲苯罐(2000m。
拱顶罐)产生静电燃烧爆炸。
事故前,l59#罐存甲苯1713吨,贮存高度10.924m(罐总高12.575m,安全高度11.10m),处于不动罐状态,每天进行一次复尺和测温。
5月28日8~18点班,9时20分左右,班长和量油工一起巡回检查到159#甲苯罐时,班长叫量油工上罐复尺和测温。
量油工上罐顶后,用右脚踏着量油口盖板踏脚,将盖板打开,先用双手将卷尺铜锤放下去然后收看;随即手提棉纱绳,将放入液下五米深的插有温度汁的锌镀铁皮筒提上来看油温指示,发现油温异常。
他又把此温度计放入油内复测。
稍等片刻,快速拉起,当拉到量油口时,只听“当”的一声,随着一团黑烟裹着火焰从量油口喷出。
量油工心一紧、脚一松,量油口盖板自动盖上,紧接着“轰”的一声,油罐的东北方向治罐壁朐焊缝间炸开一条长80cm、宽40cm的喇叭口,浓烟和火焰从裂口喷出。
经过扑救,及时控制了事故扩大,保住了油罐和罐内剩留的甲苯,没有造成重大的经济损失。
事故发生的原因:
事故发生后,经有关部门一系列检查及试验证明,这次事故是由测温器在甲苯中快速提拉产生静电火花,点燃了甲苯罐内的油气引起燃烧爆炸。
教训:
①测温器在油品中提拉的速度,对产生静电电位高低有直接关系。
提拉越快,静电电位就越高;提拉越慢,静电电位就越低。
油罐采样和测温应防止快拉,提拉速度越慢越好。
②测温器的表面光滑程度不同,对产生静电电位高低也有影响。
表面光滑,产生静电电位就低;表面粗糙,产生静电电位就高。
测温器、采样筒外表制造要求越光滑越好,降低摩擦系数。
③测温器、油尺、重锤材质不同,对产生静电电位高低也不一样。
锕质的比镀锌铁皮的产生静电电位低。
预防措施:
油罐检尺、采样必须严格执行《预防静电危害的十条规定》,不准使用两种材质的检尺、测温、采样工具进行作业。
凡是使用金属材料制成的测温、采样器,必须用金属导线做绳索与罐体进行接地,操作时不得猛拉快提。
12.动火引燃草坪
1998年12月9日上午,×××厂输油车间维修班班长龙某、火焊工罗某、班员谭某,看火人许某到北山罐区128#罐东北面管沟补焊二专线的蒸汽管,1l时,火焊工罗某在点着火枪后,不小心将与他距离1.5米远的北面防火堤的草坪引燃。
由于草皮干燥,很快蔓延,面积大约有70平方米的草皮,在场的人员拿起灭火器,奋力抢救,在消防救火车到达之前将火扑灭。
事故原因分析:
1、动火前安全措施落实不到位,动火点附近的草皮没有用水淋湿或用石棉布盖好,没有严格执行公司“三不动火”的规定。
2、车间火票审批人员没有严格执行公司的用火管理制度,没有到动火现场认真落实动火的安全措施。
应吸取的教训和采取的防范措施:
1、加强对看火人和动火人的安全培训,要求严格按规定动火和看火,严格执行公司“三不动火”的规定。
2、加强职工的防火知识的培训,积极开展防火灭火的反事故演练,提高职工的防火灭火的技能。
3、全体职工要真正树立“安全第一”的思想,确保将事故消灭在萌芽状态。
严把安全生产关。
4、车间在每项动火施工前必须制订并落实动火安全措施。
5、火票审核、审批人员必须严格执行公司的用火管理标准,亲自到现场检查安全防范措施落实后才能签名,批准用火。
13.装车油速突快,引起静电起火
1982年6月25日,×××厂装油站台0~8点班接班后,踊道和五道继续同时装70#汽油。
2时20分左右,轻油罐区因83#罐油已装完,换装84#罐(满罐,油尺8.33米)。
由于罐区在山上,装车站台在山下,又是满罐,汽油流速很快,换罐后很快就装了三个多槽车。
到2点40分对,四道前数第八个槽车已装油2/3左右。
此时,听到正在进油的槽车“轰”的一声,大火冲天而起,同时引着了五道的槽车和整个电机沟道的油气。
着火后,五道的装油工当机立断,很快停止五道对位,切断总电源。
然后指挥操作台旁的同志,迅速关闭四道风阀、电阀,提起装油大鹤管,并将开着的窗户关上。
又跑到第三层平台关闭了四道手阀。
正在五道检尺、封车、拧螺拴的二名装油工被火势冲了一下,便从槽车上跳了下去,其中一人造成左脚踝骨和右腿腿骨两处骨折,另一人摔伤较轻,但他们仍奋不顾身从槽车底下钻过去,绕过着火的电机沟,跑上二台顶部关闭了五道手阀。
在三台装车的一名操作工,看到火起,提了两个干粉灭火器就向二台奔跑过去。
他机警地绕过正在着火的链条沟,跑上二层平台,见槽车还在燃烧,就飞起一脚,将槽车盖踢倒盖好,把这台槽车的火扑灭。
随后,其它各台的当班人员都提着灭火机扑向着火现场,将四道着火槽车和地沟的火焰全部扑灭。
由于站台工人的果断扑救,只烧坏了部分塑料风管和电线,装车作业停了12小时。
通过对事故的分析,着火的原因是:
当83#罐汽油装空换到84#罐时,因为是满罐,致使油品流速加快(经计算,汽油在管中流速已达到7~8米/秒),产生静电集聚放电火花引起的。
14.航煤进罐刚停,采样静电起火
l982年l0月16日,×××厂油品车间620航煤中间罐进油后,护罐工和分析站取样员到罐上检尺、取样。
护罐工检完尺,取样员先取上部油样倒入样瓶,将剩余量600ml从采样口倒回罐内,第二次取下部油样。
当手中棉绳放入罐内4~5m时(取样盒浸入油面约2m),突然听到罐内丝丝响声,同时感到有一种力量撞击油罐;接着,看到左前方罐沿向上凸起,很快罐顶边沿裂开一条两尺多长的口子并呼呼冒气;紧接着,采样口喷出火来,把采样员脸部燎伤。
当她跑下油罐,距罐2~3m时,一声巨响,油罐起火。
经奋力扑救将火扑灭。
这次火灾使罐顶边沿四分之三裂开并塌入罐内,中心法兰连接螺栓全部拉断,罐上部2.4m罐壁变形,烧掉航煤2.7吨,直接经济损失一千三百多元。
事故原因:
经分析,发生这次事故须有两个条件:
一是有可爆气体,二是火源。
事故发生后[wiki]测试[/wiki]819航煤罐,其可燃气体占4%,正好在爆炸极限内;经凋查,外来明火及金属摩擦产生火花的可能均不存在,唯一因素是静电产生火花:
①航煤组份油与管道在输送过程中产生大量静电电荷,当进油刚停止,油面的静电电荷还没有衰减时就捡尺采样,加之将剩余的60Dml油倒入罐内,冲击油面,使油面静电电位更为增加,为静电放电提供了条件。
②当第二次把采祥器放入罐内时,因金属采样器感应带电,而采样绳为棉纱线不导电,则瞬间电压增高,击穿了空气介质向罐内仪表补气导管放电,引燃可爆气体。
15.明沟积油,引爆着火事故1999年2月11日,×××厂火炬岗位白班接班后,检查加裂容4和一催化容一4时发现各有60%的液而,经检查为水,随即将其排入密闭的地下罐(火炬容1)。
10:
00时,火炬岗位人员开泵抽地下罐的污水送催化容l含油污水井,11:
15时停泵。
下午13:
55时,岗位人员在操怍室听到一声响声,立即冲出操作室,发现火炬西南角围墙外(接近门岗段)有烟火,立即报火警。
此时火已烧至围墙外水沟口及污水池,当班人员赶紧从泵房开水灭火,约5分钟消防车赶到并投入灭火,20分钟后火被扑灭。
事故或事件的原因分析:
1、火炬西面污水沟上游有油水排下,长期积累在排水口隔栅处,并不时有油花外排,造成厂外水沟积油。
2、水沟及旧污水池存的污水污油因天气炎热,油气挥(蒸)发形成可燃可爆气体。
3、由于厂外水泥厂西面水沟破小明火种引燃,火苗沿水沟往上游燃烧,烧至火炬西而水沟口,引燃了火炬区的水沟及旧污水池。
应吸取的教训和采取的防范措施:
l、对火炬区域排水沟重新设汁,设置南北两个水封井,防止厂外火源烧进装置内。
2、填埋火炬区域内的旧污水池。
3、加强现场检查和[wiki]环境[/wiki]可燃气体监测,发现可疑情况及时查明原因并处理。
16.59#阀拆盲板,硫化[wiki]氢[/wiki]逸出中毒事故
1996年12月17同,×××厂××车间委托华粤五公司拆除催化火炬54#、55#、59#阀及90#阀后法兰盲扳。
其中一组三人(二男一女)拆59#阀盲板,9:
55时,存拆开螺栓取盲扳时,蹲低取盲扳的曾某突然昏倒,经抢救后苏醒脱险。
事故或事件原因分析:
1、事故直接原因:
59#阀使用时间长,闸板槽有含硫化物沉积物,闸板关不到位,致使含硫化氢瓦斯气体泄漏,使曾某吸入硫化氢中毒。
2、事故间接原因:
盲板前、阀后空间积仔含硫化物无法吹扫,硫化物积存造成闸阀关不严;作业者安全意识淡薄,在从事接触硫化氢作业时选择站位方向不对,而且现场作业环境的硫化氢浓度已超过所使用的过滤式防毒而具的使用范围。
应吸取的教训和采取的防范措施:
l、凡在瓦斯、液态烃、酸性气、酸性水系统管网加、拆盲板作业时,必须执行公司防止硫化氢中毒的有关规定,选戴供风式、供氧式或长管式防毒面具或空气呼吸器。
2、作业人员站在上风向,派专人监护。
3、当拆丌螺栓后,先用撬棍撬开法兰,待管内积存气体散发后,方可加、拆盲板和放垫片紧固。
4、凡在瓦斯、液态烃、酸性气、酸性水系统管网加、拆盲板作业时,申请公司消防气防中心、医院监护,以防发生突发中毒事故时能及时抢救处理。
5、加强承包商的管理,施工单位必须具备相应的资质,配备必需的器材:
如压缩机,供风式、供氧式或长管式防毒面具、空气呼吸器,轴流风机等。
6、编制详细的施工方案,做好危害识别和风险评估,按规定办理《接触硫化氢作业许可证》,落实施工安全防范措施。
7、加强外来施工人员的安全教育,实行重大危害告知,指出作业过程中的重要环节和主要注意事项。
8、生产车间实行全方位监管,配备责任心强、熟悉工艺流程的作业监护人。
17.55#阀加盲板不当,火炬管线爆炸事故
×××厂1995年4月份,因一催化火炬线系统大修,有关阀门需加盲板。
具体程序是:
23日车间组织人员改好流程,由催化火炬切换加裂火炬投用,停下催化火炬系统。
27日上午由一预分离装置给汽在催化火炬预吹扫,下午在容l、2接力给汽吹往催化火炬,28日上午8:
00时停止蒸汽吹扫,8:
30时交中石化四建公司加盲板。
15:
30时,当拆开55#阀门法兰,将盲扳插入时,发现盲板偏大,螺栓拧不上;15:
50时,加盲板人员离开现场,车间设备主任开车将盲板拉去制硫维修班割小。
17:
2l时,55#阀至催化火炬段管线发生闪爆,造成12米Dg500管线移位,法兰错位l米,Dg50排凝线第一道焊口拉断。
后将管线从龙门架两边割断,消除应力,吊复原位,才加好55#阀盲板。
事故或事件原因分析:
1、事故直接原因:
催化火炬线系统预吹扫时,由于管线长,蒸汽量小,该段管线末吹到,管内仍有瓦斯积存;火炬有抽力,空气从拆开的法兰口进入管内,致使管内硫化铁自燃引起管内瓦斯闪爆。
2、间接原因;当发现盲板不符时,拆开的阀兰未用石棉板盖住法兰口或管内给入蒸汽掩护,致使空气进入管内;
应吸取的教训和采取的防范措施:
l、在54#、55#阀后全催化火炉线加蒸汽吹扫线,以便今后管线切换加盲板时,容易吹扫干净。
2、关闭