落料拉深复合模毕业设计.docx
《落料拉深复合模毕业设计.docx》由会员分享,可在线阅读,更多相关《落料拉深复合模毕业设计.docx(33页珍藏版)》请在冰豆网上搜索。
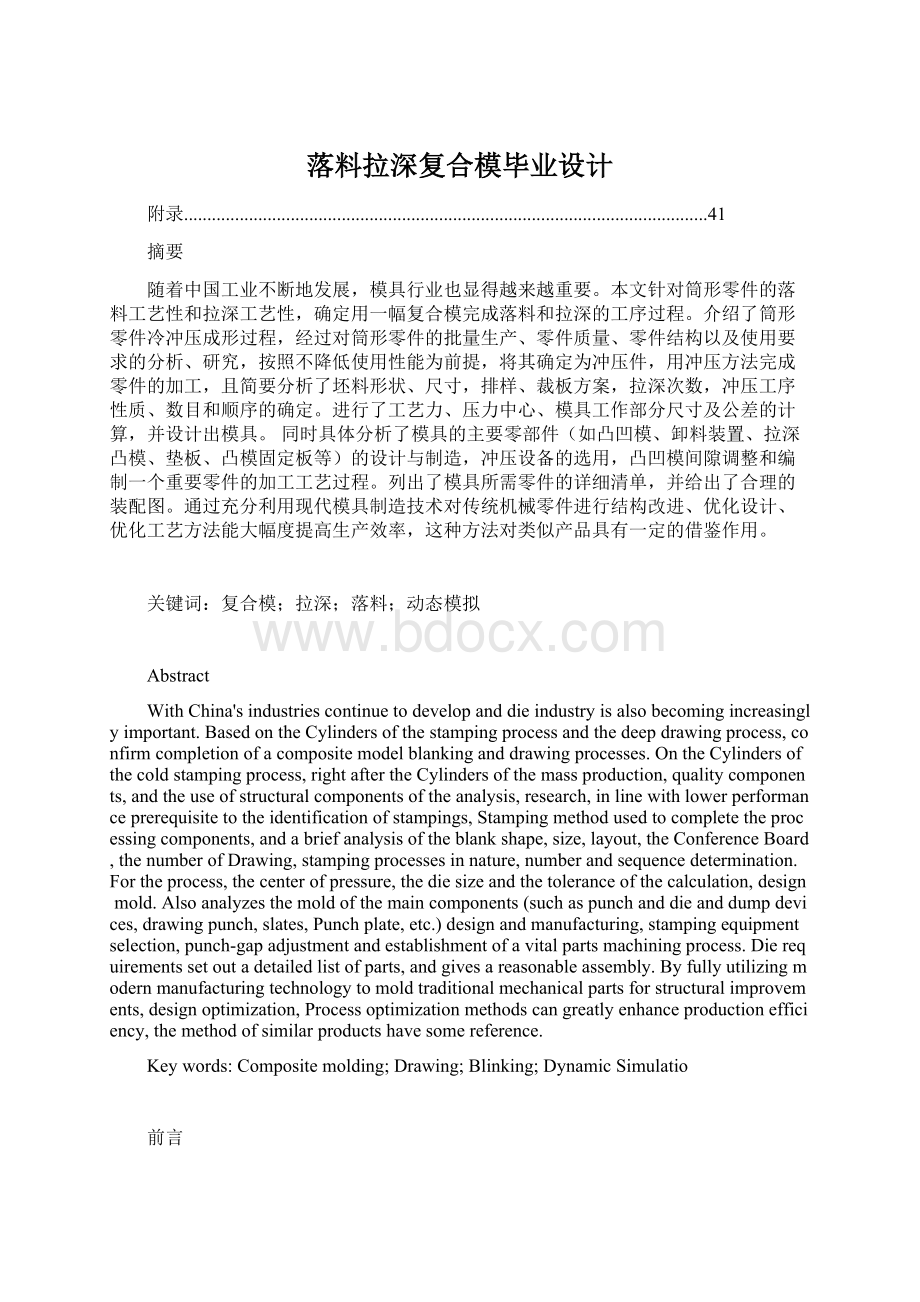
落料拉深复合模毕业设计
附录.................................................................................................................41
摘要
随着中国工业不断地发展,模具行业也显得越来越重要。
本文针对筒形零件的落料工艺性和拉深工艺性,确定用一幅复合模完成落料和拉深的工序过程。
介绍了筒形零件冷冲压成形过程,经过对筒形零件的批量生产、零件质量、零件结构以及使用要求的分析、研究,按照不降低使用性能为前提,将其确定为冲压件,用冲压方法完成零件的加工,且简要分析了坯料形状、尺寸,排样、裁板方案,拉深次数,冲压工序性质、数目和顺序的确定。
进行了工艺力、压力中心、模具工作部分尺寸及公差的计算,并设计出模具。
同时具体分析了模具的主要零部件(如凸凹模、卸料装置、拉深凸模、垫板、凸模固定板等)的设计与制造,冲压设备的选用,凸凹模间隙调整和编制一个重要零件的加工工艺过程。
列出了模具所需零件的详细清单,并给出了合理的装配图。
通过充分利用现代模具制造技术对传统机械零件进行结构改进、优化设计、优化工艺方法能大幅度提高生产效率,这种方法对类似产品具有一定的借鉴作用。
关键词:
复合模;拉深;落料;动态模拟
Abstract
With China's industries continue to develop and die industry is also becoming increasingly important. Based on the Cylinders of the stamping process and the deep drawing process, confirm completion of a composite model blanking and drawing processes. On the Cylinders of the cold stamping process, right after the Cylinders of the mass production, quality components, and the use of structural components of the analysis, research, in line with lower performance prerequisite to the identification of stampings, Stamping method used to complete the processing components, and a brief analysis of the blank shape, size, layout, the Conference Board, the number of Drawing, stamping processes in nature, number and sequence determination. For the process, the center of pressure, the die size and the tolerance of the calculation, design mold. Also analyzes the mold of the main components (such as punch and die and dump devices, drawing punch, slates, Punch plate, etc.) design and manufacturing, stamping equipment selection, punch-gap adjustment and establishment of a vital parts machining process. Die requirements set out a detailed list of parts, and gives a reasonable assembly. By fully utilizing modern manufacturing technology to mold traditional mechanical parts for structural improvements, design optimization, Process optimization methods can greatly enhance production efficiency, the method of similar products have some reference.
Key words:
Composite molding;Drawing;Blinking;Dynamic Simulatio
前言
该设计是为了安装在电器或凸起轴端上的一个防止电漏的零件的落料拉深模具的设计。
通过对这套模具的设计,把所学的专业知识和在工厂实习的实际经验结合起来,进行了一次全面的理论与实践的融合。
此套模具采用复合模,复合模是指在压力机的一次行程内在模具的一个工位上完成两道以上冲压工序的模具,是一种多工序冲压模。
常见的复合模有落料和冲孔复合模,落料和首次拉深复合模。
与单工序模相比,主要优点是:
①生产效率高;②冲压件精度高。
其的缺点是:
模具结构复杂,不易制造。
适用于生产精度要求较高的软材料或薄板料冲压件。
通过该次设计,首先进一步培养了独立工作和综合分析问题的能力,提高了解决冷冲压模具设计与制造以及冷冲压生产过程中遇到问题的能力,同时进一步巩固和加强了在学校四年来学到的专业和相关的知识,为今后在学习和实际工作中解决问题打下良好的基础。
在整个设计中我懂得了许多东西,树立了对自己工作能力的信心,相信会对今后的学习工作生活有非常重要的影响。
而且大大提高了动手的能力,使我充分体会到了在创造过程中探索的艰难和成功时的喜悦。
第一章绪论
1.1冲压的概念、特点及应用
冲压是利用安装在冲压设备(主要是压力机)上的模具对材料施加压力,使其产生分离或塑性变形,从而获得所需零件(俗称冲压或冲压件)的一种压力加工方法。
冲压通常是在常温下对材料进行冷变形加工,且主要采用板料来加工成所需零件,所以也叫冷冲压或板料冲压。
冲压是材料压力加工或塑性加工的主要方法之一,隶属于材料成型工程术。
冲压所使用的模具称为冲压模具,简称冲模。
冲模是将材料(金属或非金属)批量加工成所需冲件的专用工具。
冲模在冲压中至关重要,没有符合要求的冲模,批量冲压生产就难以进行;没有先进的冲模,先进的冲压工艺就无法实现。
冲压工艺与模具、冲压设备和冲压材料构成冲压加工的三要素,只有它们相互结合才能得出冲压件。
与机械加工及塑性加工的其它方法相比,冲压加工无论在技术方面还是经济方面都具有许多独特的优点。
主要表现如下:
(1)冲压加工的生产效率高,且操作方便,易于实现机械化与自动化。
这是因为冲压是依靠冲模和冲压设备来完成加工,普通压力机的行程次数为每分钟可达几十次,高速压力要每分钟可达数百次甚至千次以上,而且每次冲压行程就可能得到一个冲件。
(2)冲压时由于模具保证了冲压件的尺寸与形状精度,且一般不破坏冲压件的表面质量,而模具的寿命一般较长,所以冲压的质量稳定,互换性好,具有“一模一样”的特征。
(3)冲压可加工出尺寸范围较大、形状较复杂的零件,如小到钟表的秒表,大到汽车纵梁、覆盖件等,加上冲压时材料的冷变形硬化效应,冲压的强度和刚度均较高。
(4)冲压一般没有切屑碎料生成,材料的消耗较少,且不需其它加热设备,因而是
一种省料,节能的加工方法,冲压件的成本较低。
但是,冲压加工所使用的模具一般
具有专用性,有时一个复杂零件需要数套模具才能加工成形,且模具制造的精度高,技术要求高,是技术密集形产品。
所以,只有在冲压件生产批量较大的情况下,冲压加工的优点才能充分体现,从而获得较好的经济效益。
冲压在现代工业生产中,尤其是大批量生产中应用十分广泛。
相当多的工业部门越来越多地采用冲压法加工产品零部件,如汽车、农机、仪器、仪表、电子、航空、航天、家电及轻工等行业。
在这些工业部门中,冲压件所占的比重都相当的大,少则60%以上,多则90%以上。
不少过去用锻造=铸造和切削加工方法制造的零件,现在大多数也被质量轻、刚度好的冲压件所代替。
因此可以说,如果生产中不采用冲压工艺,许多工业部门要提高生产效率和产品质量、降低生产成本、快速进行产品更新换代等都是难以实现的。
1.2 冲模分类
1.2.1根据工艺性质分类
(1)冲裁模 沿封闭或敞开的轮廓线使材料产生分离的模具。
如落料模、冲孔模、切断模、切口模、切边模、剖切模等。
(2)弯曲模 使板料毛坯或其他坯料沿着直线(弯曲线)产生弯曲变形,从而获得一定角度和形状的工件的模具。
(3)拉深模 是把板料毛坯制成开口空心件,或使空心件进一步改变形状和尺寸的模具。
(4)成形模 是将毛坯或半成品工件按图凸、凹模的形状直接复制成形,而材料本身仅产生局部塑性变形的模具。
如胀形模、缩口模、扩口模、起伏成形模、翻边模、整形模等。
1.2.2根据工序组合程度分类
(1)单工序模 在压力机的一次行程中,只完成一道冲压工序的模具。
(2)复合模 只有一个工位,在压力机的一次行程中,在同一工位上同时完成两道或两道以上冲压工序的模具。
(3)级进模(也称连续模) 在毛坯的送进方向上,具有两个或更多的工位,在压力机的一次行程中,在不同的工位上逐次完成两道或两道以上冲压工序的模具。
1.2.3依产品加工方法分类
(1)冲剪模具:
是以剪切作用完成工作的,常用的形式有剪断冲模、下料冲模、冲孔冲模、修边冲模、整缘冲模、拉孔冲模和冲切模具。
(2)弯曲模具:
是将平整的毛胚弯成一个角度的形状,视零件的形状、精度及生产量的多寡,乃有多种不同形式的模具,如普通弯曲冲模、凸轮弯曲冲模、卷边冲模、圆弧弯曲冲模、折弯冲缝冲模与扭曲冲模等。
(3)抽制模具:
抽制模具是将平面毛胚制成有底无缝容器。
(4)成形模具:
指用各种局部变形的方法来改变毛胚的形状,其形式有凸张成形冲模、卷缘成形冲模、颈缩成形冲模、孔凸缘成形冲模、圆缘成形冲模。
(5)压缩模具:
是利用强大的压力,使金属毛胚流动变形,成为所需的形状,其种类有挤制冲模、压花冲模、压印冲模、端压冲模。
1.3 我国冲压现状与发展方向
1.3.1冲压模具市场情况
我国冲压模具无论在数量上,还是在质量、技术和能力等方面都已有了很大发展,但与国发经济需求和世界先进水平相比,差距仍很大,一些大型、精度、复杂、长寿命的高档模具每年仍大量进口,特别是中高档轿车的覆盖件模具,目前仍主要依靠进口。
一些低档次的简单冲模,已趋供过于求,市场竟争激烈。
根据中国模具工业协会发布的统计材料,2004年我国冲压模具总产出约为220亿元,其中出口0.75亿美元,约合6.2亿元。
根据我国海关统计资料,2004年我国共进口冲压模具5.61亿美联社元,约合46.6亿元.从上述数字可以得出2004年我国冲压模具市场总规模约为266.6亿元.其中国内市场需求为260.4亿元,总供应约为213.8亿元,市场满足率为82%.在上述供求总体情况中,有几个具体情况必须说明:
一是进口模具大部分是技术含量高的大型精密模具,而出口模具大部分是技术含量较低中的中低档模具,因此技术含量高的中高档模具市场满足率低于冲压模具总体满足率,这些模具的发展已滞后于冲压件生产,而技术含量低的中低档模具市场满足率要高于冲压模具市场总体满足率;二是由于我国的模具价格要比国际市场低格低许多,具有一定的竟争力,因此其在国际市场前景看好,2005年冲压模具出口达到1.46亿美元,比2004年增长94.7%就可说明这一点;三是近年来港资、台资、外资企业在我国发展迅速,这些企业中大量的自产自用的冲压模具无确切的统计资料,因此未能计入上述数字之中。
1.3.2冲压模具技术状况
随着工业产品质量的不断提高,冲压产品生产正呈现多品种、少批量,复杂、大型、精密,更新换代速度快的变化特点,冲压模具正向高效、精密、长寿命、大型化方向发展。
为适应市场变化,随着计算机技术和制造技术的迅速发展,冲压模具设计与制造技术正由手工设计、依靠人工经验和常规机械加工技术向以计算机辅助设计(CAD)、数控切削加工、数控电加工为核心的计算机辅助设计与制造(CAD/CAM)技术转变。
至今,我国模具制造行业的产值已经超过机床工业。
有关板料冲压技术方面的问
题愈来愈为人们所关注,相应的冲压工艺理论的研究及冲压加工机理的探讨也随之不断深化,如何从冲压工序基本应力与变形状态的分析着手,改善冲件的质量精度,并提高模具的使用寿命也就显得愈为重要。
1.3.3我国冲压模具的发展方向
模具技术的发展应该为适应模具产品“交货期短”、“精度高”、“质量好”、“价格低”的要求服务。
达到这一要求急需发展如下几项:
(1)全面推广CAD/CAM/CAE技术模具CAD/CAM/CAE技术是模具设计制造的发展方向。
随着微机软件的发展和进步,普及CAD/CAM/CAE技术的条件已基本成熟,各企业将加大CAD/CAM技术培训和技术服务的力度;进一步扩大CAE技术的应用范围。
计算机和网络的发展正使CAD/CAM/CAE技术跨地区、跨企业、跨院所地在整个行业中推广成为可能,实现技术资源的重新整合,使虚拟制造成为可能。
(2)高速铣削加工国外近年来发展的高速铣削加工,大幅度提高了加工效率,并可获得极高的表面光洁度。
另外,还可加工高硬度模块,还具有温升低、热变形小等优点。
高速铣削加工技术的发展,对汽车、家电行业中大型型腔模具制造注入了新的活力。
目前它已向更高的敏捷化、智能化、集成化方向发展。
(3)模具扫描及数字化系统高速扫描机和模具扫描系统提供了从模型或实物扫描到加工出期望的模型所需的诸多功能,大大缩短了模具的在研制制造周期。
有些快速扫描系统,可快速安装在已有的数控铣床及加工中心上,实现快速数据采集、自动生成各种不同数控系统的加工程序、不同格式的CAD数据,用于模具制造业的“逆向工程”。
模具扫描系统已在汽车、摩托车、家电等行业得到成功应用,相信在“十五”期间将发挥更大的作用。
(4)电火花铣削加工电火花铣削加工技术也称为电火花创成加工技术,这是一种替代传统的用成型电极加工型腔的新技术,它是有高速旋转的简单的管状电极作三维或
二维轮廓加工(像数控铣一样),因此不再需要制造复杂的成型电极,这显然是电火花成形加工领域的重大发展。
国外已有使用这种技术的机床在模具加工中应用。
预计这一技术将得到发展。
(5)提高模具标准化程度我国模具标准化程度正在不断提高,估计目前我国模具标准件使用覆盖率已达到30%左右。
国外发达国家一般为80%左右。
(6)优质材料及先进表面处理技术选用优质钢材和应用相应的表面处理技术来提高模具的寿命就显得十分必要。
模具热处理和表面处理是否能充分发挥模具钢材料性能的关键环节。
模具热处理的发展方向是采用真空热处理。
模具表面处理除完善应发展工艺先进的气相沉积(TiN、TiC等)、等离子喷涂等技术。
(7)模具研磨抛光将自动化、智能化模具表面的质量对模具使用寿命、制件外观质量等方面均有较大的影响,研究自动化、智能化的研磨与抛光方法替代现有手工操作,以提高模具表面质量是重要的发展趋势。
(8)模具自动加工系统的发展这是我国长远发展的目标。
模具自动加工系统应有多台机床合理组合;配有随行定位夹具或定位盘;有完整的机具、刀具数控库;有完整的数控柔性同步系统;有质量监测控制系统。
我国冲压模具与发达国家企业之间的差距不小,因此要发挥整体优势和综合竞争力,要加强统筹协调、完善合作机制,创造性地工作。
也需要加大对模具相关专业人才的综合素质培训投入。
1.4 国外模具发展趋势及行业特点
1.4.1国外模具发展趋势
1988年美国日本,西德的模具产值分别达到62亿美元,83亿美元,4亿美元,比1957年增长了约100倍,并超过了这些国家机床工业的产值。
据有关资料介绍,工业发达国家的工业产品生产中。
对模具的需求量日益增多,美国,日本约有4050的工业产品的生
产需用模具国际市场中模具的贸易量十分可观.近年来,由于工业发达国家的工费用增加,模具生产有向东南亚国家转移的趋势。
日本的生产以高,精模具为主,需要人工劳动
量大的模具则依靠进口解决.以模具出口大国日本为例,其间提高了5.3倍由此可见,中
低档模具的国际市场潜力十分巨大,只要我国模具的质量能有提高,交货期能有保证,模具出口的前景是十分乐观的.此外,国际市场对塑料模具模架及模具标准件的需求量也很大,目前我国只有塑料模具模架有少量出口。
1.4.2模具行业特点
(1)随着科学技术的发展,模具行业已由劳动密集型逐步3转化为技术劳动密集型。
(2)尽管模具行业已应用了先进的数控设备,检验仪器和计算机辅助设计/分析/制造软件,但仍然需要高技艺的劳动。
所以,模具行业又是高技术和高技艺紧密结合的一门行业。
(3)为适应不同制品的需要,模具的种类繁多,从设计,制造工艺,装备以至原材料都各不都各不相同所以企业生产的模具宜专而不宜全,规模宜小而不宜大。
(4)模具基本上是单件生产。
即使是生产专业化的模具企业,在生产同一类模具时,也会由于不同模具的精度要求,复杂程度,加工难度等的不同而需要变化设备的配置和工程的安排。
因此,模具企业还应在专业化的基础上实现生产的素性化三,市场分析据国际生产协会预测,到2009年工业品零件粗加工的75%,精加工的5%将由模具成型,可见模具在工业生产中的作用将日益重要.工业发达国家的模具行业在近四十年来取得了异常迅速的发展,已摆脱了属地位而成为独立的行业,并成为基础工业的重要组成部分。
1.5 模具设计及加工技术的现状
1.5.1 模具设计技术
(1)工业发达国家在模具设计上已经大量使用计算机辅助设计软件进行模具的结构设计,并普及了计算机绘图。
据有差资料介绍,美国和日本75的模具厂已使用了该项技术,香港的模具厂也开始采用这项技术。
(2)在注塑模具设计中,已开始普及应用计算机辅助工程分析软件,对塑料的流动填充,冷却情况及模具的浇口配置,浇道大小,冷却加热系统和模具的刚度,强度等进行科学的分析和计算,从而保证注塑制品的质量与合理的生产节拍。
(3)国外的注塑模具中,多型腔,多层,大型精密模具已占50%,不仅提高了生产效率,而且节省了大量塑料原料。
1.5.2.模具加工技术
(1)国外已大量使用数控机床,应用计算机辅助加工软件和数控编程技术对模具,特别是对具有复杂型腔(三维曲面)的模具进行加工,使模具的质量和附加值大为提高。
模具的加工周期减少6以上,成本降低3以上,生产效率提高60以上为了提高加工效率及满足各种复杂曲面加工的要求,国外已开发出四轴和五轴的数控自动编程软件并且进了实用阶段。
(2)模具标准化程度日益提高,模具标准模架及模具标准件的应用日益普及,已实现商品化。
(3)模具结构更多地采用新技术,如注塑模具的热流道技术等。
(4)针对不同制品的要求,开发出适用于各种不同模具的专用模具钢,并实现商品化。
韩国有1570家模具企业仅占总数的9%;新加坡有460家模具企业仅占总数的3香港有6500家模具企业也占总数的0.46%。
第二章零件的工艺性分析
冲压制件图如下图所示:
图1工件
冲压技术要求:
1.材料:
08钢
2.材料厚度:
0.5mm
3.生产批量:
大批量
4.未注公差:
IT14.
2.1零件的工艺性分析
分析冲压零件的工艺性包括技术和经济两个方面。
在技术方面根据产品图纸,主要分析冲压件的形状特点、尺寸大小、尺寸标注方法、表面质量要求和材料性能等因素是否符合冲压工艺要求;在经济方面,主要根据冲压件的生产批量分析产品成本,阐明采用冲压生产可取得的经济效益。
因此,冲压件的工艺性好与差,主要是指在不影响使用要求的前提下,能否最简单最经济的方法冲压出来。
能做到的,表明该冲压件的工艺好;反之,工艺性差,影响冲压件工艺性。
影响冲压件工艺性的因素有很多,从技术和经济方面考虑,主要因素有:
(1)外形尺寸:
该零件材料为08钢,轮廓结构比较简单,形状对称,是一个回转体拉深制件。
该冲裁件外形和尺寸都符合要求适合冲裁。
但是该零件是由材料厚0.5mm的08钢材料制成,不仅材料薄,且相对高度h/d较大。
其凸缘相对直径d凸/d>1.4,属于宽凸缘件。
所需工序繁杂,成形难度大,特别是拉深工艺成形难道更大。
(2)冲裁件的精度与粗糙度:
冲裁件的经济公差等级不高于IT14级,一般落料公差等级最好低于IT10级,此工件取公差等级IT14,查表可得其基本尺寸为:
D17
,65
R3
。
(3)冲裁件的材料:
由《模具设计与制造简明手册》【2】可查得08钢为优质碳素结构钢,为极软的碳素钢,强度、硬度很低,而韧性和塑性极高,具有良好的深冲、拉延、弯曲和镦粗等冷加工性能、焊接性能。
但存在时效敏感性,淬硬性及淬透性极低。
大多轧制成高精度的薄板或冷轧钢带用以制造易加工成形,强度低的深冲压或深拉延的覆盖零件和焊接构件。
其力学性能如下:
●化学成份:
碳C:
0.05~0.12硅Si:
0.17~0.37
锰Mn:
0.35~0.65硫S:
≤0.035
磷P:
≤0.035铬Cr:
≤0.10
镍Ni:
≤0.25铜Cu:
≤0.25
●力学性能:
抗拉强度σb(MPa):
≥325(33)
屈服强度σs(MPa):
≥195(20)
伸长率δ5(%):
≥33
断面收缩率ψ(%):
≥60
硬度:
未热处理,≤131HB
由以上分析可知,该工件符合冲压工艺要求。
2.2确定工艺方案
该圆筒件在首次拉深成形过程中主要工序有:
下料、落料、拉深、切边。
工艺方案一:
下料→落料→首次拉深→切边;
工艺方案二:
下料→落料首次拉深复合→切边;
工艺方案三:
下料→落料首次拉深级进→切边;
对上述三种工艺方案进行比较并确定最佳方案:
方案一:
从生产效率上讲,该方案分为四个工序,工艺过于分散,需要多次定位,将会降低零件的加工精度同时也延长了加工工时,降低了生产效率。
方案二:
与方案一不同的是用到了复合模将落料和拉深工序放到一个复合模具上完成,简短了加工工时,提高了生产效率,同时在一定程度上提高了零件的加工精度,完全能满足工件制造的工艺要求。
方案三:
这个方案与前两种方案相比最突出的特点是它的主要成形加工程序在一套级进模上完成,生产效率较高,同时还提高了零件的加工精度,但级进模具制作加工很复杂,造价很高,耗时耗力耗财。
综上所述,我认为方案二是最合理可行的。
第三章冲压模具总体结构设计
3.1模具类型
根据零件的加工工艺方案,本次设计主要设计该工件主要工序——落料拉深复合的模具,故需设计一套落料首次拉深复合模。
3.2操作与定位方式
落料首次拉深复合模考虑零件大批量生产,安排生产可采用手工送料方式能够达到批量生产,且能降低模具成本,因此采用手工送料方式.零件尺寸较小,厚度较薄,为保证孔的精度及较好的定位,可采用导尺导正,为了降低模具的复杂程度可采用固定挡料销;为降低模具复杂程度,靠手工把工件取出。
3.3卸料与出件方式
考虑零件尺寸较小,厚度较薄,落料时采用刚性卸料方式,拉深工序时则采用打杆卸料和橡胶弹性卸料,为降低模具复杂程度,靠手工进行送料同时把废料和工件取出。
3.4模架类型及精度
由于零件材料较薄,尺寸较小,考虑零件精度要