《回流焊接技术的工艺要点和技术整合考虑》.docx
《《回流焊接技术的工艺要点和技术整合考虑》.docx》由会员分享,可在线阅读,更多相关《《回流焊接技术的工艺要点和技术整合考虑》.docx(19页珍藏版)》请在冰豆网上搜索。
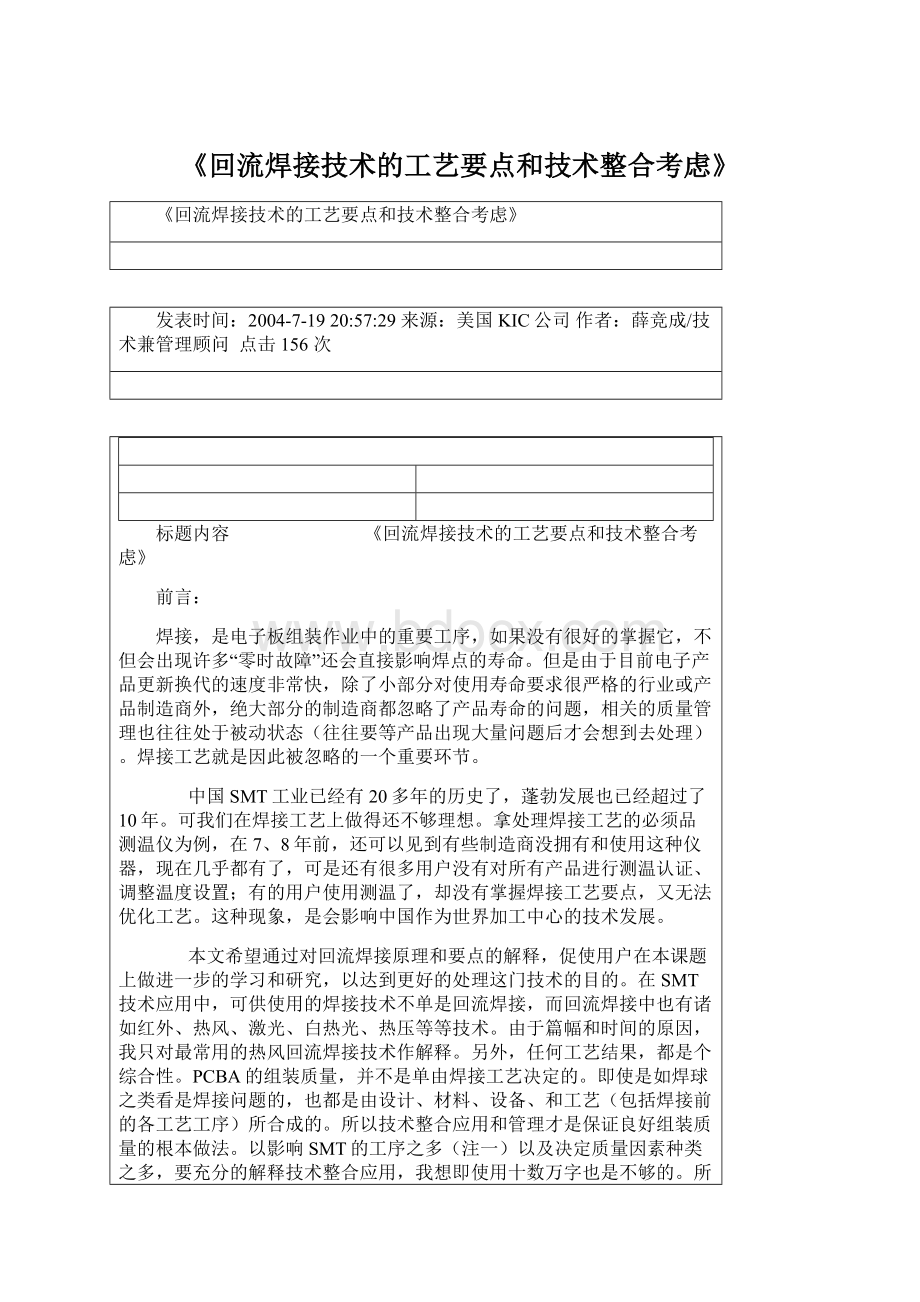
《回流焊接技术的工艺要点和技术整合考虑》
《回流焊接技术的工艺要点和技术整合考虑》
发表时间:
2004-7-1920:
57:
29 来源:
美国KIC公司 作者:
薛竞成/技术兼管理顾问 点击156次
标题内容 《回流焊接技术的工艺要点和技术整合考虑》
前言:
焊接,是电子板组装作业中的重要工序,如果没有很好的掌握它,不但会出现许多“零时故障”还会直接影响焊点的寿命。
但是由于目前电子产品更新换代的速度非常快,除了小部分对使用寿命要求很严格的行业或产品制造商外,绝大部分的制造商都忽略了产品寿命的问题,相关的质量管理也往往处于被动状态(往往要等产品出现大量问题后才会想到去处理)。
焊接工艺就是因此被忽略的一个重要环节。
中国SMT工业已经有20多年的历史了,蓬勃发展也已经超过了10年。
可我们在焊接工艺上做得还不够理想。
拿处理焊接工艺的必须品测温仪为例,在7、8年前,还可以见到有些制造商没拥有和使用这种仪器,现在几乎都有了,可是还有很多用户没有对所有产品进行测温认证、调整温度设置;有的用户使用测温了,却没有掌握焊接工艺要点,又无法优化工艺。
这种现象,是会影响中国作为世界加工中心的技术发展。
本文希望通过对回流焊接原理和要点的解释,促使用户在本课题上做进一步的学习和研究,以达到更好的处理这门技术的目的。
在SMT技术应用中,可供使用的焊接技术不单是回流焊接,而回流焊接中也有诸如红外、热风、激光、白热光、热压等等技术。
由于篇幅和时间的原因,我只对最常用的热风回流焊接技术作解释。
另外,任何工艺结果,都是个综合性。
PCBA的组装质量,并不是单由焊接工艺决定的。
即使是如焊球之类看是焊接问题的,也都是由设计、材料、设备、和工艺(包括焊接前的各工艺工序)所合成的。
所以技术整合应用和管理才是保证良好组装质量的根本做法。
以影响SMT的工序之多(注一)以及决定质量因素种类之多,要充分的解释技术整合应用,我想即使用十数万字也是不够的。
所以本文在有限的篇幅中,只对焊接工艺做重点解释,对于其他相关的工艺、可制造性设计、材料质量、设备能力等等都假设做得到位。
在实际工作中,读者还应该进一步学习和研究其他因素的影响,方能很好的处理所有组装问题。
焊接的基本要求:
不论我们采用什么焊接技术,都应该保证满足焊接的基本要求,才能确保有好的焊接结果。
高质量的焊接应具备以下5项基本要求。
1.适当的热量;
2.良好的润湿;
3.适当的焊点大小和形状;
4.受控的锡流方向;
5.焊接过程中焊接面不移动。
适当的热量指对于所有焊接面的材料,都必须有足够的热能使它们熔化和形成金属间界面(IMC),足够的热也是提供润湿的基本条件之一。
另一方面,热量又必须控制在一定程度内,以确保所接触到的材料(不只是焊端)不会受到热损坏,以及IMC层的形成不至于太厚(注二)。
润湿除了是较好可焊性的象征外,也是形成最终焊点形状的重要条件。
不良的润湿现象通常说明焊点的结构不理想,包括IMC的未完整成形以及焊点填充不良等问题。
这些问题都会影响焊点的寿命。
要焊点有足够的寿命,就必须确保焊点的形状和大小符合焊端结构的要求。
太小的焊点其机械强力不足,无法承受使用中的应力,甚至连焊接后存在的内应力也无法承受。
而一旦在使用中开始出现疲劳或蠕变开裂,其断裂速度也较快。
焊点的形状不良还会造成舍重取轻的现象,缩短焊点的寿命期。
受控的锡流方向也是焊接工艺中的重要部分。
熔化的焊锡必须往所需要的方向流动,才能确保焊点的形成受控。
在波峰焊接工艺中的‘盗锡焊盘’和阻焊层(绿油)的使用,以及回流焊接工艺中的吸锡现象,就是和锡流方向控制有关的技术细节。
焊接过程中如果焊端移动,根据移动的情况和时间而定,不但会影响焊点的形状大小,还可能造成虚焊和内孔情况。
这都将影响焊点的质量寿命。
所以整个产品的设计以及工艺,都必须照顾到焊接过程中焊端保持不动状态。
在回流焊接工艺中,除了以上通用焊接条件外,还有特别的一点,就是必须把经过印刷工艺后没有作用的锡膏中的化学成分及时挥发处理。
这点尤其是在双面焊接工艺中的首面要求更严格。
以上的技术要求,我们在设计和处理回流焊接工艺时都必须注意。
下面我们来进一步了解回流焊接工艺以及它可控制的手段技巧。
回流焊接温度直线:
由于整个回流焊接的工艺要点在于控制PCBA上各点的温度和时间,温度曲线是个常用和重要的工艺管理工具。
从基本理论上来看,图一中的温度‘直线’是可以做到焊接效果的。
图一
基本上,如果我们能够在升温不太快的情况下(避免造成热冲击损害),使焊端的温度上升到超过其熔化温度(但不超过产品安全温度),并保持适当的时间(提供适当的热量)后受控降温。
我们是可能达到焊接要求的。
事实上这很难做到。
主要存在三个问题。
一是我们的实际产品存在不同的器件和布线,这意味着PCBA上不同点有热容量的差别。
所以我们可能出现以下图二中的情况。
图二
从图二中我们可以看到板上有热点和冷点需要同时照顾到其各自的温度/时间需求。
当我们如图二中把冷点(B)的温度调到符合焊接要求时,板上的热点(A)有可能已经超出安全温度而造成损坏。
但如果我们把温度降低到A点符合要求时,则B点可能又出现冷焊故障。
温度直线所面对的第二个问题,是在实际焊接中我们必须首先处理锡膏中已经无
无用的成分,使其完全并温和的挥发。
这挥发工艺对于不同的锡膏有不同的要求。
而由于锡膏中存在溶剂、稳定剂、稀释剂和浓化剂等多种成分,各成分对挥发所需要的时间和温度又有不同,我们未必在以上热、冷点的限制下能够通过直线完成。
在产品设计不复杂的情况下(热容量差距小和安全窗口大),我们可能可以通过放缓升温速度来达到要求,但从室温到峰值温度一般需要200度左右(无铅技术更高),这对需要快速生产的用户又是个难题。
第三个问题,是PCBA设计一般牵涉到许多不同的器件材料和封装,而我们面前采用的回流炉子以热风技术为多,空气本身并不是个很好的热导体,其传热必须依靠对流效果。
而空气流动的控制是个高难度的工艺,何况必须控制到SMT焊端这么微小的面积精度上,更几乎是不可能做得很好。
加上PCBA上器件的布局对空气流动的影响,使我们在处理PCBA上各点的温度和时间关系上难以兼顾。
这造成了我们如果要解决所有焊接相关的问题(例如焊球、气孔、吸锡等),我们必须有个能够灵活设置和调整的‘曲线’。
回流温度曲线:
如果我们要避开以上温度直线的问题,并拥有较好的工艺能力的话。
我们需要类似以下图三的温度‘曲线’。
图三:
温度曲线
从上图中我们可以看到,整个回流焊接过程可以分5个工序。
即是:
1.升温
2.恒温
3.助焊
4.焊接
5.冷却
第一工序的升温目的,是在不损害产品的情况下,尽快使PCBA上的各点的温度进入工作状态。
所谓工作状态,即开始对无助于焊接的锡膏成份进行挥发处理。
恒温区起着两个作用。
一是恒温,就是提供足够的时间让冷点的温度‘追’上热点。
当焊点的温度越接近热风温度时,其升温速率就越慢,我们就利用这种现象来使冷点的温度逐渐接近热点温度。
使热冷点温度接近的目的,是为了减少进入助焊和焊接区时峰值温差的幅度,便于控制个焊点的质量和确保一致性。
恒温区的第二个作用是对锡膏中已经没有用的化学成份进行挥发处理。
助焊工序是锡膏中的活性材料(助焊剂)发挥作用的时候。
此刻的温度和时间提供助焊剂清洗氧化物所需的活化条件。
当温度进入焊接区后,所提供的热量足以熔化锡膏的金属颗粒。
一般上器件焊端和PCB焊盘所使用的材料,其熔点都高于锡膏,所以本区的开始温度由锡膏特性决定。
例如以63Sn37锡膏来说,此温度为183oC。
升温超过此温度后,温度必须继续上升,并保持足够的时间使熔化的锡膏有足够的润湿性,以及能够和各器件焊端以及PCB焊盘间形成IMC为准。
最后的冷却区作用,除了使PCBA回到室温便于后工序的操作外,冷却速度也可以控制焊点内部的微结晶结构。
这影响焊点的寿命。
回流焊接工艺故障和曲线的关系:
以上提到的5个回流焊接工序中,每一部分都有它的作用,而相关的故障模式也不同。
处理这些工艺问题的关键在于对它们的理解以及如何判断故障模式和工序的关系。
比如第一个升温工序,如果设置不当造成的故障将可能是‘气爆’、‘溅锡引起的焊球’、‘材料受热冲击损坏’等问题。
恒温工序造成的问题可能是‘热坍塌’、‘连锡桥接’、‘高残留物’、‘焊球’、‘润湿不良’、‘气孔’、‘立碑’等等。
助焊工序相关问题有‘焊球’、‘润湿不良’、‘虚焊’等等。
焊接工序设置不当的相关问题可能是‘润湿不良’、‘吸锡’、‘缩锡’、‘焊球’、‘IMC形成不良’、‘立碑’、‘过热损坏’、‘冷焊’、‘焦炭’、‘焊端溶解’等等。
冷却所可能造成的问题一般较少和较轻。
但如果设置不当,也将可能影响焊点的寿命。
如果马上进入清洗工艺,则可能造成清洁剂内渗而难以清洗的问题。
必须注意的是,前4项工序是连贯性的,相互间也有关系。
所以故障模式并不常是那么容易区分。
例如‘立碑’和‘焊球’故障往往必须综合调整才能够完全解决问题。
常见的回流焊接工艺设置问题:
本文开始时我提到了不少用户在回流焊接上做得不理想。
以下是常见的一些问题和错误。
读者不妨也看看本身是否存在这些问题。
1.完全按照锡膏供应商所提供的温度曲线指标来设置炉温
目前绝大多数的用户,在焊接温度的设置上都只用锡膏供应商所提供的资料作为根据。
这引出了两个问题。
一是锡膏供应商所建议的曲线只做锡膏焊接性方面的考虑,而并不可能知道用户PCBA上的其他要求。
所以曲线只能作为参考而非标准。
尤其是焊接区的温度和时间部分,用户的考虑需求往往不是锡膏方面的。
另外,锡膏供应商在恒温区的特性要求上往往不是十分精确,这和锡膏供应行业的特性有关。
因此造成了用户焊接工艺设置不能优化。
2.缺乏‘工艺窗口’的概念
在工程项目中,我们很忌讳缺乏‘窗口’、‘上下限’和‘公差’的概念。
因为这样将使我们忽略和无法优化以及控制我们的技术特性参数。
回流焊接工艺也是如此。
虽然以上如图二在解释原理时我们只用单一曲线指标。
但实际工作中,我们对于每一个工艺特性参数,都必须有上限和下限。
也就是有个明确的‘工艺窗口’才好操作。
3.
1.热冷点的错误判断
有了工艺窗口后,适当的做法是确保PCBA上的每一点的温度都在这窗口范围内。
在实际工作中我们不可能对每一个焊点进行测量。
所以回流焊接工艺设置的要点在于如何确认PCBA上的最冷和最热点。
当我们将这两点的要求都能够通过工艺调整来满足时,其他的焊点自然就同时得到满足。
传统的做法中,用户多通过外观观察器件的大小来决定测温热耦该设置在什么地方。
这是一套十分陈旧的做法。
在以往的红外线焊接技术中还可能有几分可靠。
,但到了热风焊接中其可靠性就很小了。
如果读者曾见到诸如0603的小矩形件的两端温差高达8度,或QFP四周引脚温差达13度,或在拼版上不同电路的同一器件焊点位置上有高达20度的温差情况时,就会相信这观察预测的做法是绝对不行的。
我甚至见过有用户使用未贴片裸板,把热耦选择接在四角和中央位置来测温的,这和盲目设置炉温又有什么两样。
?
4.
1.轻重取舍不清
在设置和调制焊接工艺时,我们可能会遇到设计难度高的产品。
这些产品可能由于板上器件的选择和布局造成其间热容量出现巨大的差异。
如果再遇到所采用的回流炉能力不是很强,或所采用的锡膏在焊接窗口上容忍性不是很高的话,工艺调制可能无法兼顾到所有的焊点质量。
在这种情况下,我们就必须对焊点质量进行取舍。
不少用户由于DFM/DFR(可制造性设计/可靠性设计)做得不到位,或生产部对产品上各材料/焊点的寿命要求不了解,造成无法有效进行取舍,正由于缺乏前面3步的正确做法,不少用户甚至对于这种工艺调制优化的做法完全没有意识。
5.
1.误把五个工艺当成单一工艺
本文先前提到,回流焊接事实上是包括了升温、恒温、助焊、焊接、和冷却5个工序的一套工艺。
如果忽略了这个重要环节,对于我们解决工艺问题可能造成混乱或错误的决策。
例如焊球问题的处理,焊球问题在升温、恒温或助焊工序处理不当时都可能出现,但成因各异。
升温工序造成的焊球问题多是由于气爆引起,也多半和材料质量、库存时间和条件以及锡膏印刷工艺有关(注三)。
但如果是恒温工序造成的,则多和温度/时间设置不当,或锡膏变质有关。
和助焊工序相关的,则是氧化程度偏高以及温度/时间设置不当引起。
各情况下出现的焊球其表象各不相同,处理方法也不一样。
如果没有把它当成不同工序不同机理来分析,就只可能胡乱调整设备或盲目尝试了。
我曾在一些国内外的技术论文中见到用DOE来优化回流炉温度和链速参数设置的。
这是把5种工序混成一体处理的做法。
这做法的效果(注四)应该给于仔细评估。
在没有使用热冷点测温做法的情况下,这种DOE做法或许能给我们带来改善。
,但如果误把这改善当作工艺优化,我想在工艺管理上就是大错特错了。
6.
1.对供应商资料的误解和盲目跟从
有不少用户对供应商的资料的含义和使用方法产生误解。
很多供应商指标本为参考值,或起着‘傻瓜机’作用(注五)。
但用户并不了解这一点,而代表供应商与用户直接沟通联系的销售人员也并没有强调或说明清楚,造成用户盲目的使用而发生错误。
例如图四中器件供应商的焊接要求指标。
其中不少信息并非该器件所决定。
例如‘Preflow’部分的指标主要受锡膏特性影响较大,该器件供应商所提的不过是一种牌子型号的锡膏,未必就是用户使用的那种。
图四:
器件焊接要求
7.
1.供应商指标问题
供应商指标本身也经常出现问题。
这是由于许多供应商所从事的工作和SMT组装工艺本身有些差距,而供应商的工程人员未必清楚地掌握SMT技术要求。
例如以上图四中,‘Peakreflowtemperature’的20度窗口,以及‘Timeabove183oC’的60秒窗口是个常用的焊接曲线‘傻瓜机’式的数据,这曲线适用于整个PCBA的温度参考(即包括最热最冷点)。
作为器件所提出的指标要求不宜这样描述。
另一个例子,是‘Componentbodytemperature’的描写,有时也可能出现问题。
原因是缺乏区分温度敏感和热能敏感器件。
所以作为用户有时候会出现设置上的问题。
另外一个常见的例子如图五所示。
图五的焊接温度曲线是器件供应商所提供。
和图四的问题一样,其中信息并非都和器件有关。
而一些重要的器件工艺性指标,例如热冲击承受能力,最大热量承受能力却没有明确的给于量化表示。
图五是个常见的通用焊接温度曲线。
对于用户处理所采购的器件并没有很好的帮助。
图五:
器件供应商技术资料
8.
1.缺乏工艺调制能力
焊接工艺的其中一个挑战,是各焊点之间出现的温差。
一些焊接故障如立碑、偏移、吸锡和桥接等,都和温差有关。
温差形成的原因除了热容量的设计外,和焊接过程中热风的对流情况,以及材料和PCB基板的传热情况有关。
工艺调制的工作,就在于分析这些热容量、热对流、热传导等条件,和适当的给予调整补偿。
由于在炉子上基板的传送只有一个速度。
,工艺调整必须尽量借助于各炉子温区的设置。
而上下温区对PCBA的加热方式有所不同(注六),上下温区的配合更是能够发挥工艺优化的能力的。
但由于许多用户都未掌握这种有用的调制技术。
,我们常见到的都是一成不变的上下温区同温设置。
9.缺乏工艺管制手段
以上8点问题,都是针对焊接工艺的设置和调制的。
撇开这些不谈,目前不少用户在工艺管制上也缺乏一套好的做法。
一般用户对本身的回流炉能力并未进行详细的考评。
例如炉子的稳定性、回温能力、排风影响等等。
而在设置了工艺参数后,一般也不进行任何确保工艺不过度偏移的监控措施。
做法较规范的,主要是定期(例如每班次)进行过板温度测量。
但这种做法是否足够或有效,在没有对炉子进行详细的能力认证前是无法知道的。
例如有一台价格不菲并享有良好声誉的炉子,经过测试评估后,其处理负荷变化的能力不太理想。
如果遇到负荷较大的产品以及进板时间不稳定受控时,是有可能出现焊接不理想的结果的。
在实际生产中,每一块板的实际温度变化情况如何,用户并不知道。
所以目前一般的工艺管制做法是靠一个‘信’字,而且似乎信得有不少盲目成份。
10.缺乏技术整合的研究和做法
良好的回流焊接工艺,并非只靠对焊接工艺机理的了解,或对工艺参数的调制就能够有保证的。
其实工艺调制的能力可能非常有限。
因为它受到设备、工艺(可制造性)设计和材料等先决条件的限制。
即使拥有很好的工艺知识,工艺工程师也未必能够保证工艺质量。
所以要做得好,一家企业必须推行技术整合以及技术/管理整合。
可惜这方面的做法和投入,在本区域市场
上也是较缺乏的。
例如许多用户在产品设计时,并没有对焊接需求进行详细的策划评估;企业内也缺乏对新器件进行焊接性(注七)认证的工作;设备选购时缺乏采购前的实际测试(注八);设备安装后也缺乏对其焊接加热能力进行量化管理,并制定工艺能力和设计规范等等。
这些都是缺乏技术整合的现象。
李氏回流温度曲线:
约三年前,美国SMT界对传统的回流曲线(图二)提出了质疑。
当时由于一位‘李’氏提出了一项技术成果报告,认为把曲线的升温和恒温部分改成稍慢的直线升温做法(见图六),可以解决好些工艺问题。
从那时候起,行业杂志、书籍、报告等就先后出现了很多论文支持该论点和做法。
图六:
李氏的缓升温度曲线
如果我们采取的工艺调制方法,缺乏冷热点调制,也缺乏对不甚精确的锡膏回流曲线指标的仔细认证,光是靠看焊接结果的外观的话,那‘李氏曲线’很有可能给我们带来改善。
因为我们不容易在缺乏以上科学做法中侥幸获得一个优化的设置。
我曾读过一些论文,说回流焊接工艺中要完全去除‘焊球’和‘气孔’是不可能的。
这相信也是因为缺乏以上科学调制法的原因。
据我所知,目前很好使用热冷点评估设置工艺的用户十分少。
而能够掌握上下不同温配合技巧的更是寥寥无几。
这就是造成对这门技术误解的原因。
李氏曲线之所以有用,是因为许多用户先前并没有把温度曲线摸清和设置好,从而造成了焊球和残留物等问题。
李氏曲线的最大特点,是缓慢的从室温升温到助焊和焊接时间。
这给整个挥发工序带来了‘温和’的好处。
所以一切由于‘升温’和‘恒温’区分不清的问题,以及因为对锡膏特性了解不精确的问题等等,都得以改善,看来效果良好。
李氏曲线可能带来的问题。
是生产速度稍慢,以及焊点寿命的缩短。
生产速度方面的问题可能还不敏感。
,原因是从事这些工艺研究的企业,大多有多温区和设计较好的炉子。
在炉子加热效率好以及加热长度够的情况下,炉子生产速
度的压力并不大。
,往往还有余额空间。
而寿命方面虽然是个大问题,但如果没有仔细的焊点可靠性分析,或没有遇到产品设计较难的(热容量差距大),这问题也许根本不会被发现。
李氏曲线较传统曲线最不足的,是其恒温效果差。
,所以对于热容量差距大的板,焊接温度的保证较困难。
曾有一篇报告说李氏曲线可能出现较多的溅锡问题,应该就是因为热容量差距问题造成的。
另外,李氏曲线不适合于红外线加热技术。
所以使用红外加热的(以较早期的日本设备较多)用户不宜使用。
李氏曲线,也称为‘慢升温曲线’或‘直线升温曲线’,事实上也是属于一种‘傻瓜机’概念(注四)。
它对于新手或对焊接工艺和设备认识不深的用户来说,是比较容易操作和避免较多的问题的。
不过,李氏曲线在优化能力上是不如传统曲线的。
其实,做为SMT用户,我们不应该局限于什么曲线外观。
关键是了解您的材料、设计、设备的能力和需求,从而设置出支持它们的工艺曲线。
读者可曾看过阶梯式的温度/时间曲线?
我们曾在欧洲的一个产品上以它来排除所有的焊接问题!
正确的回流工艺做法:
回流焊接技术,事实上并不如许多人所认为的那么简单。
尤其是当您要求达到零缺陷和焊接可靠性(寿命)保证的情况下。
我也只能暂时在做法上和大家分享经验。
要确保有良好的回流焊接工艺,应该有以下的做法:
1.了解您PCBA上的质量和焊接要求,例如最高温度要求和最需要在寿命上得到照顾的焊点和器件;
2.了解PCBA上的焊接难点,例如锡膏印刷大于焊盘的部分,间距特小的部分等等;
3.找出PCBA上最热和最冷的点,并在点上焊接测温热耦;
4.决定其他必需接热耦测温的地方,例如BGA封装和底部焊点,热敏感器件本体等等(尽量利用所有测温通道来获得最多信息);
5.设置初始参数,并和工艺规范比较(注九)以及调整;
6.对焊接后的PCBA在显微镜下进行仔细观察,观察焊点形状和表面状况、润湿程度、锡流方向、残留物和PCBA上的焊球等等。
尤其是对以上第2点记录下的焊接难点处更要注意。
一般而言,经过以上的调整后不会出现什么焊接故障。
但如果有故障出现,针对故障模式分析,再针对其机理配合上下温区控制进行调整。
如果没有故障,从所得曲线和板上焊点情况决定是否要进行微调优化。
目的是要使设置的工艺最稳定以及风险最小。
调整时一并考虑炉子负荷问题以及生产线速度问题,以便在质量和产量上得到较好的平衡。
以上的工艺曲线的设置调整,必须用实际产品进行才会有把握。
使用实际产品的测试板,成本可能是个问题。
有些用户所组装的板价格十分昂贵,这造成用户不愿意经常测试温度的原因。
用户应该对调试成本和一旦出现问题的成本进
行评估。
此外,测试板的成本还可以通过使用假件、废板和选择性贴片等做法来进一步节省资源。
焊接工艺管制:
上面我们谈的6个步骤是工艺的设置和调制。
当我们对其效果满意后,便可以进入批量生产。
由此刻起,工艺管制就十分重要了(注十)。
一旦焊接参数(温度、时间、风量、风速、负载因子、排风等)决定了之后,确保这些参数有一定的稳定性是工艺监控的目标。
目前较不理想的,是许多用户对于以上的工艺参数并未进行任何监控。
做得稍微好的可能在固定时间段对温度曲线进行认证。
做法是使用测试板和测温仪器过炉测量后和原先纪录进行比较。
即使如此,这做法上仍然有些缺点。
一是测量的频率和时间缺乏科学性的制定,以感性作决策为多。
其二是抽样的可靠性偏低。
这种做法如果要确保较高的效益,必须配合并建立在对设备有深入的研究和性能认证工作的基础上。
对于从事高质量要求的行业,例如汽车电子、军用品、医疗设备、超级电脑、电力保护等等,以上的抽样式管制是不够的。
目前市场上有一种实时监测系统,可以不间断的对炉子内的气流和温度情况进行监测。
达到100%的工艺控制目的。
唯一不足的,是目前该设计还未能和炉子的温控系统进行闭环整合,所以还是属于一种‘监测系统’而非‘控制系统’。
不过这系统已经在工艺管制的领域中带给用户好处。
据了解,目前这类技术在欧美使用很多,日本和韩国企业这两年也开始采用,台资企业由于受美国的影响也在近年较多的使用。
而唯独中国企业使用得很少。
这和采购观念(注十一)以及对技术应用和管理的认识有关。
但我觉得只是个认识和学习的过程现象。
相信将来中国的企业也会大量使用这门工艺管制技术。
我曾对这系统和一些SMT用户交流过,不少用户其实并不了解这技术,常误以为它重复了炉子内部的温度控制功能。
事实上炉子内部控制系统一般只监控‘温度’而不监控‘气流’,炉子的回温反应也有一定的延误,绝对不是预防性的。
这也就是说,以目前的炉子控制技术来说,炉子本身并不能够保证不会出错。
而这实时监测系统,虽然目前也不能预防质量问题的出现,但却有能力告诉用户炉子所不能够提供的故障信息。
除了这点,该系统还具备‘风险预测’功能和QA功能。
是个值得考虑的工具。
设备要求:
好的回流炉子是确保良好工艺的重要部分。
尤其是从事加工服务类的企业(CM或EMS行业),因为缺乏对设计方面的控制力,工艺补偿和调整能力便成为成功的关键了。