凸焊焊接标准.docx
《凸焊焊接标准.docx》由会员分享,可在线阅读,更多相关《凸焊焊接标准.docx(37页珍藏版)》请在冰豆网上搜索。
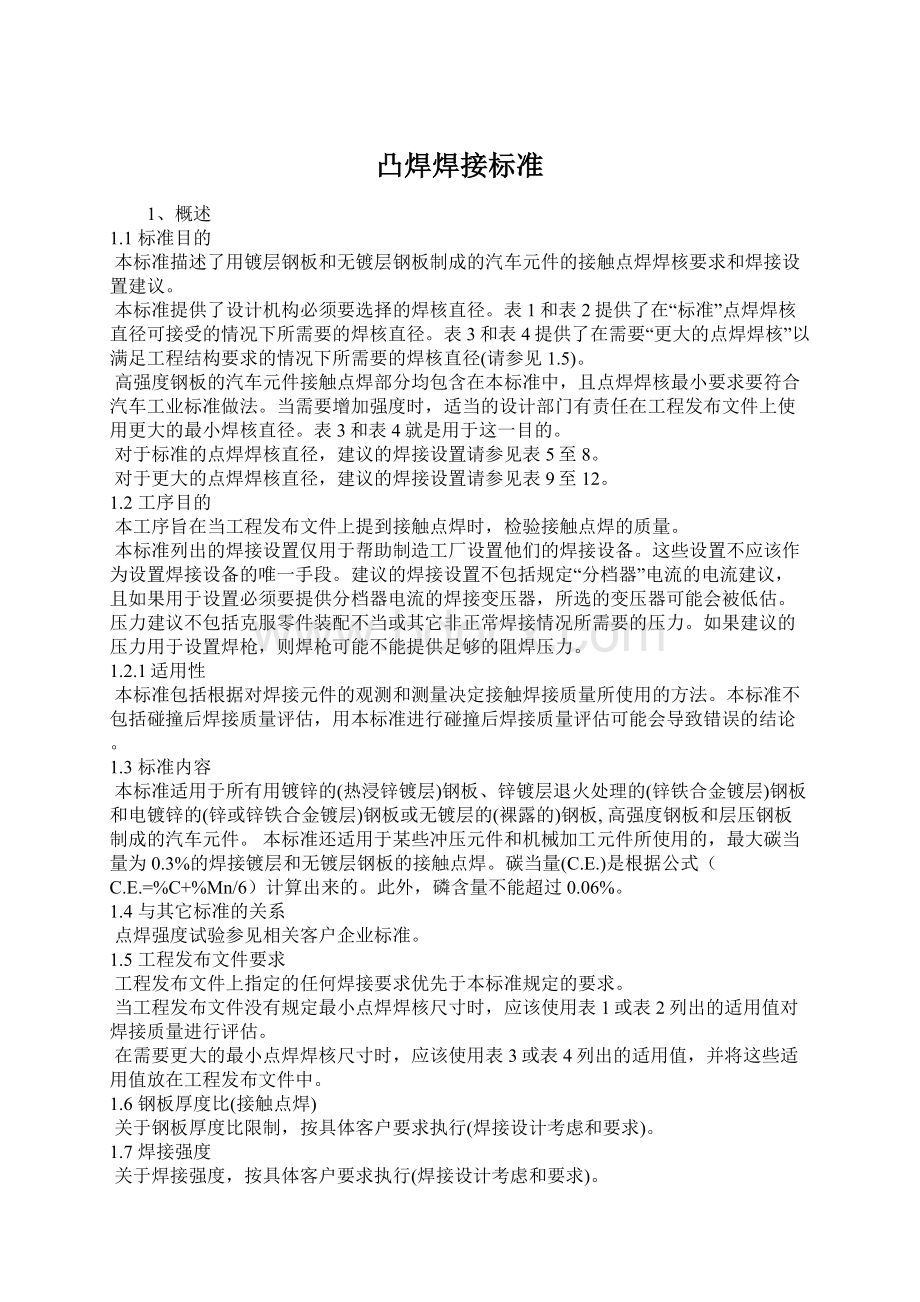
凸焊焊接标准
1、概述
1.1标准目的
本标准描述了用镀层钢板和无镀层钢板制成的汽车元件的接触点焊焊核要求和焊接设置建议。
本标准提供了设计机构必须要选择的焊核直径。
表1和表2提供了在“标准”点焊焊核直径可接受的情况下所需要的焊核直径。
表3和表4提供了在需要“更大的点焊焊核”以满足工程结构要求的情况下所需要的焊核直径(请参见1.5)。
高强度钢板的汽车元件接触点焊部分均包含在本标准中,且点焊焊核最小要求要符合汽车工业标准做法。
当需要增加强度时,适当的设计部门有责任在工程发布文件上使用更大的最小焊核直径。
表3和表4就是用于这一目的。
对于标准的点焊焊核直径,建议的焊接设置请参见表5至8。
对于更大的点焊焊核直径,建议的焊接设置请参见表9至12。
1.2工序目的
本工序旨在当工程发布文件上提到接触点焊时,检验接触点焊的质量。
本标准列出的焊接设置仅用于帮助制造工厂设置他们的焊接设备。
这些设置不应该作为设置焊接设备的唯一手段。
建议的焊接设置不包括规定“分档器”电流的电流建议,且如果用于设置必须要提供分档器电流的焊接变压器,所选的变压器可能会被低估。
压力建议不包括克服零件装配不当或其它非正常焊接情况所需要的压力。
如果建议的压力用于设置焊枪,则焊枪可能不能提供足够的阻焊压力。
1.2.1适用性
本标准包括根据对焊接元件的观测和测量决定接触焊接质量所使用的方法。
本标准不包括碰撞后焊接质量评估,用本标准进行碰撞后焊接质量评估可能会导致错误的结论。
1.3标准内容
本标准适用于所有用镀锌的(热浸锌镀层)钢板、锌镀层退火处理的(锌铁合金镀层)钢板和电镀锌的(锌或锌铁合金镀层)钢板或无镀层的(裸露的)钢板,高强度钢板和层压钢板制成的汽车元件。
本标准还适用于某些冲压元件和机械加工元件所使用的,最大碳当量为0.3%的焊接镀层和无镀层钢板的接触点焊。
碳当量(C.E.)是根据公式(C.E.=%C+%Mn/6)计算出来的。
此外,磷含量不能超过0.06%。
1.4与其它标准的关系
点焊强度试验参见相关客户企业标准。
1.5工程发布文件要求
工程发布文件上指定的任何焊接要求优先于本标准规定的要求。
当工程发布文件没有规定最小点焊焊核尺寸时,应该使用表1或表2列出的适用值对焊接质量进行评估。
在需要更大的最小点焊焊核尺寸时,应该使用表3或表4列出的适用值,并将这些适用值放在工程发布文件中。
1.6钢板厚度比(接触点焊)
关于钢板厚度比限制,按具体客户要求执行(焊接设计考虑和要求)。
1.7焊接强度
关于焊接强度,按具体客户要求执行(焊接设计考虑和要求)。
1.8焊接设置
关于无镀层的(裸露的)钢板、镀锌的(热浸锌镀层)钢板、锌镀层退火处理的(锌铁合金镀层)钢板和电镀锌的(锌或锌铁合金镀层)钢板的接触点焊设置建议请参见表5、表6、表7和表8。
表9、表10、表11和表12包含同种钢板的接触点焊设置建议,但是仅在根据工程发布文件需要选择更大的焊核直径时才适用。
这些焊接设置仅作为指导,只能用于帮助制造工厂设置他们的焊接设备和对设备进行维护。
这些设置对中频直流电(MFDC焊接或其它形式的直流电焊接并不适用。
当锌镀层退火处理的钢板(锌铁合金镀层)互相焊接时,应当使用表5、表7、表9或表11中列出的建议焊接时间和电流的较高值。
当电镀锌的(锌或锌铁合金镀层)钢板互相焊接或与镀锌的(热浸锌镀层)钢板焊接时,或当镀锌的(热浸锌镀层)钢板互相焊接时,应当使用表6、表8、表10或表12中列出的建议焊接时间和电流的较高值。
当无镀层的(裸露的)高强度钢板互相焊接或锌镀层退火处理的(锌铁合金镀层)高强度钢板互相焊接时,表5、表7、表9或表11中的电极力应当增加10%。
当无镀层的(裸露的)高强度钢板或锌镀层退火处理的(锌铁合金镀层)高强度钢板与低碳钢板焊接时,表5、表7、表9或表11中的电极力应当增加5%。
焊接层压钢板时,考虑将由层压钢板制成的2个层压板变成一个实心板。
这个实心板可以是一个双层钢所列焊接设置不相同的设置。
1.8.1持续时间设置
对于所有焊接设置而言,应当增加至少2次循环的最低持续时间,以使焊核凝固。
焊接较厚的材料时,要增加循环次数,最高为10次。
1.8.2脉动设置
脉动设置是单脉冲焊接设置的变形。
单脉冲和双脉冲焊接设置请参见图1。
在单脉冲设置中,对焊接施加单位时间的电流。
单脉冲设置可以最大程度降低循环时间,且较脉动设置而言通常能提供更长的电极寿命。
而焊接较厚的材料时,或零件装配非常重要时,使用脉动设置可以有助于阻止溢出和扩大焊接电流范围。
进行脉动设置时,将单个热脉冲分为两个(必须时,可以更多)脉冲,各脉冲间有一定的“冷却”时间。
焊接界面的热量缓慢上升,同时冷却时间可以防止电极表面过热。
总的来说,进行双脉冲设置时,选择单脉冲设置70%至80%的脉冲时间作为双脉冲设置每次脉冲的开始时间。
冷却时间应当在两次循环时开始,此后随着材料厚度的增加而增加。
但是,冷却时间不能长到使焊接件过度冷硬,因为这样会使第二次脉冲不能产生足够的热量来完成焊接。
2、工序
2.1钢板条件
在进行焊接时,钢零件表面应当没有水垢、铁锈、油漆和其它可能影响焊接质量的污染物。
焊接前,应当去除随着时间的增长会逐渐变硬的拉拔用润滑剂、防锈剂、轧钢机机油或其它润滑剂。
接触点焊工序可以和用于焊接的可焊透底漆、粘接剂、密封剂、轧钢机机油、防锈剂、润滑剂或磷酸盐一起使用。
2.2零件装配
元件零件装配不当会影响焊接质量,且可能会导致严重的金属溢出和比较差的表面外观。
要保证配件、仪表和夹具的精确性,装配结束时应当使配件在最多使用10%建议电极力的情况下相互接触和排列整齐。
冲压件的焊接凸缘应该有规定的宽度,且所有区域应当没有卷曲的或折叠的金属。
在必须要使用卷曲的或折叠的金属时,应当使用适当的补救方法(调整焊接电流、焊接时间或焊接压力)。
2.3电极
应当保持电极端的几何形状。
图2说明了保持电极端几何形状的重要性,以及扁圆形电极对电流密度和焊接压力的不良影响。
电极端几何形状、端直径或端几何形状的变化可能会改变焊接设置,应当在发生此类变化后对焊接设置进行检查。
在与待焊接零件的接触点位置,电极表面应当保持相互平行,且电极表面应当排列整齐。
不允许电极通过夹具或零件侧围使焊接电流分流。
通过[15.9毫米(5/8英寸)柄直径]焊接电极或焊帽的最低水流率应当为2.3升/分钟(0.6加仑/分钟)。
水流率为3.8升/分钟(1加仑/分钟)或更高会增加电极寿命。
最大水流率不应当超过4.5升/分钟(1.2加仑/分钟),一旦超过可能会引起空化,从而降低电极冷却的效率。
因此,应当调整通过更小或更大的电极/焊帽的水流。
2.4焊接方式
接触点焊的数量、位置和间距应该在工程发布文件中进行规定。
最大焊接间距变化范围请参见本标准2.7.1.7。
2.5质量检查
应当根据以下规定进行质量检查。
2.5.1设备设置鉴定
对接触点焊原型或试验零件进行设备设置鉴定时,应当参考具体客户标准要求进行。
应该在对焊接设备进行主要维护后,设置改动结束后,且在更改钢板供应商或钢板类型(在临时取代规定的钢板时可能有这种情况)后,对首批机械设置进行设备设置鉴定。
应当对焊接设置进行调整以在鉴定中提供完全电极表面直径焊接。
对首批机械设置进行的设置鉴定应该基于剥裂试验。
在对焊接设备进行主要维护后,在设置改动结束后,或更改钢板供应商或钢板类型后进行的设置鉴定应该考虑以下任一种方法:
-剥裂试验(请参见2.7.4.1)
-根据客户标准进行超声波无损试验。
需要注意的是,只有根据客户的要求获得认证的操作员才能进行这项操作。
-在对焊接设备进行主要维护之前重新确定有效的焊接电流、焊接压力和焊接时间。
应该不使用一个校正过的RMS测流计对焊接电流进行检查。
应该使用一个校正过的测力计(建议使用数字测力计)对焊接压力进行检查。
如果在对焊接设备进行主要维护期间电极或焊帽发生了变化或调整,那么在使用新的或调整过的电极或焊帽时应该重新设置到正确的电流上。
如果选择了这种设置鉴定方法,工厂应该事先记录和跟踪所有设置变化,可以用这些设置变化重新进行设置(在对焊接设备进行主要维护之前,这些设置一直有效)。
2.5.2工序中质量保证
负责的工厂部门应该进行工序中质量保证。
工序中质量保证应该包括破坏性试验以决定点焊焊核直径或剥裂的按钮直径,以及对焊接区进行目测检查看看是否有偏差之处。
注意:
无损试验(请参见2.7.3)允许减少破坏性试验的频率。
在对焊接设备进行主要维护后,还可以利用无损试验帮助进行设备设置鉴定(请参见2.5.1和2.7.3)。
2.6焊接要求
应该根据2.6.1中的焊接熔接规定以及2.7中列出的检查要求,决定生产过程中的接触点焊是否合格。
在因剥裂试验或无损试验方法均未能确定熔接是否充分这一熔接特性发生争议时,应该利用2.8中关于焊接界面金相检验的规定解决这一争议。
负责的工厂部门应该规定工序中质量保证试验的间隔时间。
2.6.1熔接要求
根据点焊焊核直径测量出来的熔接值应该不低于表1或表2中关于特定的,正在焊接中的镀层(镀锌的、锌镀层退火处理的或电镀锌的)或无镀层钢板厚度的熔接值。
如果设计机构需要更大的焊核直径,应该参考表3或表4。
在工程发布文件中应该说明更大的焊核直径。
双层焊接的最小点焊焊核直径应该基于正在焊接的两块钢板中较薄的那一块。
三层焊接件的最小点焊焊核直径应该基于正在焊接的三块钢板中间的那一块。
应该使用这一调节金属层(GMT)和适当的表格(表2或表4)决定所需要的焊核直径。
在图3的例子中,调节金属层是1.8毫米的钢板,其位于层叠钢板外侧。
如果“焊接按钮”大于或等于所需要的点焊焊核直径,则其就是合格的。
应该使用带口的游标卡尺以及一个标度盘指示器或类似仪器对焊接按钮进行测量。
(建议使用数字游标卡尺。
)测量出来的数值应该与两层钢板接触面的焊接值尽量接近。
如图4所示,对畸形焊接件进行测量。
应该通过大直径和小直径对这些焊接件进行测量(测量点不需要互相垂直),然后再把测量值除以2即可。
如果获得的测量值大于或等于所需要的最小点焊焊核直径,则此焊接件是合格的。
因为破坏性地将两层钢板撕开可能会在按钮上形成一个“尾巴”,在进行按钮测量时不应该包含这一尾巴。
相反,尽可能多地探测远离钢板的尾巴,然后在尾巴剩余部分的下面滑动游标卡尺的叶片进行测量(请参见图4所示)。
图4底部的图说明,游标卡尺不能旋转至与钢板表面垂直的位置,以对非圆形焊接件的中凹部分进行测量。
2.7检查要求
以下检查程序的主要目的是确保进行了适当的工序控制。
使用的检查方法有目测检查和物理试验。
只有在符合本标准2.7.3.1中的检查要求时,才可以使用无损试验以减少物理破坏性试验的频率。
2.7.1目测检查
因为与工程发布文件不同或因为其它明显的焊接误差,许多偏差焊接可以通过目测就可以检查出来。
在目测检查显示焊接无偏差,但有最终出现偏差的趋势时,应当在焊接出现偏差之前采取纠正行动。
计划使用破坏性试验时,应该在破坏性试验之前进行目测检查。
2.7.1.1裂缝
如果在焊接表面或与焊接相邻的区域出现了无须任何放大装置就能看到的裂缝,该焊接件就不符合本标准的要求。
2.7.1.2表面小孔和透孔
在无须任何放大装置就能看到的表面小孔和透孔不符合本标准的要求。
2.7.1.3表面压痕
当目测检查显示表面压痕可能过多时,应该进行测量。
双层焊接表面压痕(请参见图5、图6、图7、图8和图9)。
任何一个电极端引起的表面压痕(C1或C2)不应该超过金属板厚度(T1或T2)的30%。
除非图纸上对焊接表面精整要求另行规定,应当对焊接设备进行调整以将压痕减少到低于30%。
测量方法1-变形和无变形的面板-卡尺方法(至少应当选择的):
钢板T1表面压痕百分比的计算方法是,将C1除以T1,然后将结果乘以100。
钢板T2表面压痕百分比的计算方法是,将C2除以T2,然后将结果乘以100。
C1的测定方法是,先测量图6左边的焊接边缘L1,然后将图6右边测量出来的总深度减去L1。
测量表面压痕时,注意不要把金属板变形包含在内(请参见图8和图9)。
图8说明了如果测量装置(卡尺或其它测量仪器)过宽,可能会出现的误差。
卡尺的边缘可以在因金属板变形而导致表面压痕测量有误的地方,与金属板接触。
测量方法2-无变形的面板-夹具方法:
可以使用图7所示的测量方法。
这一方法排除了方法1中的焊接边缘和卡尺校正问题。
测量方法3-变形和无变形的面板-套管方法:
图9说明了存在面板变形时,取代方法1的方法。
在这个方法中,一个“套管”取代了扁平面板测量装置的指示器定位夹具(如图7所示)。
套管内直径较待检查的具体焊接件的最大边缘直径稍大一些。
如图9所示,套管外直径尽可能窄,这样可以减少或消除因面板变形带来的误差。
图10说明了在变形非常接近于焊接边缘时可以使用的一个方法(套管方法3A)。
在套管上安装一个减压装置,以使松开的边缘避免与变形区接触。
三层焊接表面压痕:
三层焊接表面压痕的测量方法与双层焊接表面压痕使用的方法一样。
2.7.1.4变形
当目测检查显示变形过多时,应该进行测量且以下内容应该适用:
如果任一一层钢板的移动次数是调节金属层的两倍以上而导致焊接周围的钢板不成直线的话,就出现了焊接误差(请参见图11)。
如果任一一层钢板的移动次数是调节金属层的两倍以上而导致周围的金属不成直线的话,就出现了焊接误差。
原因是与加工件不垂直的电极引起的变形(请参见图12)。
可以利用与2.7.1.3.1中类似的方法进行测量。
2.7.1.5边缘焊缝
如果焊接件的任何一部分超过正在焊接的任何钢板的边缘,则出现了焊接误差(请参见图13)。
2.7.1.6遗漏的焊接
有效焊接的次数不能低于工程发布文件上规定的次数。
2.7.1.7等间距焊接件中宽度为25毫米(1英寸)或更小的凸缘的焊接间距变化范围
当目测检查显示变形过多时,应该进行测量且以下内容应该适用:
对于手工焊接节点,如果相邻焊接之间的距离超过工程发布文件上的平均节距(间距)30%,则说明出现了焊接误差。
对于机械焊接节点,如果相邻焊接之间的距离超过工程发布文件上的平均节距(间距)10%,则说明出现了焊接误差。
注意:
根据客户设计标准的最低要求设置节距时,如果间距小于图纸上列出的间距,有必要抵消制造过程中电流并联效应。
2.7.2焊接试验
焊接试验可以是破坏性试验,也可以是无损试验。
破坏性试验有两种:
旨在破坏性地确定焊接特性的试验,如剥裂试验;以及原本想要不产生破坏但最终超出预先确定的金属变形限制的试验。
无损试验也分为两种:
1)仅能决定焊接是否焊牢的物理试验,如无损弯曲试验或无损楔形试验;2)可以对焊接件进行测量(或基于焊接件测量)的试验,如超声波焊接试验。
2.7.2.1楔形试验和弯曲试验
所有目测检查应该在楔形试验或弯曲试验之前进行。
楔形试验和弯曲试验通常都是无损试验,但是如果出现了过多的金属变形,就会导致对零件的损害。
可接受的弯曲程度由制造焊接件的工厂和他们的客户共同决定。
当零件由于过度金属变形而受损时,不能视此次试验为破坏性试验(请参见2.7.4),除非对焊接按钮进行了测量(根据2.6.1)。
在对安全焊接件进行楔形试验或弯曲试验之前应当就某些限制事宜参考工程发布文件。
楔形试验应该包括在焊接零件之间,靠近焊接的地方推入一个楔子(请参见图14)。
弯曲试验应该包括在直接面向焊接的焊接零件之间推入一个楔子,但是无需将楔子推入焊核(请参见图15)。
2.7.3无损试验
根据客户要求,无损试验可以是物理试验(如无损楔形试验、无损弯曲试验等)或超声波试验。
如果满足2.7.3.1的条件,无损试验可以用来补充损坏性试验。
满足2.7.3.1的条件时,无损试验可以用来减少物理破坏性试验的频率。
进行无损楔形试验和无损弯曲试验是为了检验焊接是否牢固,因此不需要对点焊焊核直径进行测量。
2.7.3.1使用
进行无损试验的同时,应该进行破坏性剥裂试验。
如果剥裂试验或无损试验不能确定焊接熔接情况,应该进行金相试验。
2.7.3.2合格超声波试验的标准
进行超声波试验时应该参考客户工序标准“接触点焊超声波检查”中的无损试验要求。
应该使用表1或表2规定的最小点焊焊核直径来评估焊接质量。
如果规定了更大的焊核直径,可以使用表3或表4。
2.7.3.3合格无损楔形试验或无损弯曲试验的标准
无损楔形试验包括在焊接零件之间,靠近焊接的地方推入一个楔子,但是其与破坏性楔形试验有些不同,即其限制材料的变形程度以使制造工厂质量部门和客户都可以接受(请参见图14)。
两个正在进行试验的焊接件之间的材料应该通过楔子分开。
无损弯曲试验应该包括在直接面向焊接的焊接零件之间推入一个楔子,但是不接触焊接件或使金属变形程度超出制造焊接件的工厂与其客户可接受的限制(请参见图15)。
应该将直接靠近焊接的材料拉到焊接表面上以对焊接楔子提供一个载荷。
如果在拉出按钮之前载荷可以保持的话(两个钢板之间),说明焊接无误差,属于牢固的焊接。
如果在拉出按钮之前载荷不能保持的话,说明焊接有误差。
应当采取措施,在不发生永久变形的情况下稍微分开钢板对焊接楔子提供一个载荷,因为材料弯曲可能会导致按钮跑出母体材料之外,最终导致零件弯曲。
如果发现变形,变形程度必须要在制造工厂质量部门和客户可接受的范围之内(请参见2.7.2.1)。
需要注意的是,使用一种对焊接件施加载荷但又不损坏焊接件的方法可能需要破坏几个零件以发展进行此项试验所需要的技巧。
如果在对焊接边缘施加载荷时有一个按钮开始向外跑,那么这个按钮应该至少等同于2.6.1规定的,所需要的最小焊核直径。
如果对两个以上的金属层进行焊接,应该在每对钢板之间进行检查。
如果在对焊接边缘施加载荷时有一个按钮开始向外跑,那么每对钢板之间的按钮不能小于2.6.1规定的,所需要的最小焊核直径。
2.7.3.4其它无损试验形式
只要符合2.7.3.1中的所有要求,还可以使用其它无损试验形式。
2.7.4物理破坏性试验
所有目测检查应该在任何形式的物理破坏性试验之前进行。
对确定焊接质量来说,物理破坏性试验是最为严格的试验。
在设置期间,应该时刻对零件进行剥裂试验,以确保机械处于适合生产的状态之中,并确保焊接设置是正确的。
剥裂试验是在对焊接设备进行主要维护后可以使用的三种试验之一(请参见2.5.1)。
还可以在生产过程中,通过负责的客户公司质量部门和制造工厂质量部门共同达成共识,定期进行剥裂试验。
剥裂试验的目的是确定焊接熔接的数量,从而对焊接熔接进行测量,并根据本标准要求定为合格还是不合格。
在因剥裂试验未能确定焊接熔接的特性而就熔接是否充分发生争议时,应该利用2.8中关于焊接界面金相检验的规定解决这一争议。
2.7.4.1剥裂试验
剥裂试验包括对经过焊接的总成进行砍凿、撬动或拖拉,并通过测量从正在焊接的钢板上拉出来的按钮尺寸来评估接触点焊的质量。
经过破坏性剥裂试验后表现出以下一个或多个特征的点焊不符合本标准的要求。
“牢固焊接”——牢固焊接在焊接界面上只有很少的熔接迹象或没有熔接迹象,且在焊接附近区域只有很少一点的金属变形或没有金属变形。
这些焊接还缺少焊接渗透,因此不符合本标准的要求。
“不合规格的熔接”——如果熔接的直径小于表1或表2规定的最小焊核直径,则双层或三层金属板的焊接有不合规格的熔接。
如果工程发布文件上规定了更大的焊核直径,可以参考表3或表4。
带有不合规格的熔接的焊接不符合本标准的要求。
2.8焊接界面金相检验
当剥裂试验或无损试验不能确定焊接熔接情况时,应该根据本节列出的焊接金相检验的结果最终解决熔接是否充分的争议(请参见图5)。
2.8.1焊核直径
应该在通过接触点焊中心的经过腐蚀的横截面上对焊核直径进行测量(请参见图5)。
根据2.6.1及表1或表2的规定,熔接应该等于或超过点焊焊核直径。
在工程发布文件中规定了更大的焊核直径时,可以参考表3或表4。
2.8.2渗透性
2.8.2.1双层焊透
如果焊核对钢板的渗透低于原始钢板厚度的20%,则焊接有误差。
钢板T1渗透百分比的计算方法是,用N1除以T1,再把结果乘以100。
钢板T2渗透百分比的计算方法是,用N1除以T2,再把结果乘以100。
2.8.2.2三层焊透
如果焊核对三层钢板中的任何一层的渗透低于原始钢板厚度的20%,则焊接有误差。
三层焊透测量请参见图17、图18和图19。
图17是从钢板1到钢板2直至钢板3的一个焊核。
为了确定渗透情况,用从“a”点到“b”点(在钢板1和钢板2点焊焊核的交叉点)的一条虚线和从“c”点到“d”点的另一条虚线测量P1和P4的距离。
需要注意的是,测量P1和P4距离的箭头既与焊核垂直,也与虚线垂直,然后测量焊核渗透进钢板的最大距离。
焊核对钢板1的渗透百分比可以通过将P1除以T1,再将结果乘以100得到。
焊核对钢板3的渗透百分比可以通过将P4除以T3,再将结果乘以100得到。
焊核对钢板2的渗透百分比为100%。
图18和图19是每组钢板间的各个焊核。
为了确定对钢板1与钢板2之间接合处的渗透情况,在“a”点到“b”点之间绘制一条虚线,然后测量P1和P2的距离。
需要注意的是,测量P1和P2距离的箭头既与焊核垂直,也与虚线垂直,然后测量焊核渗透进钢板的最大距离。
焊核对钢板1的渗透百分比可以通过将P1除以T1,再将结果乘以100得到。
焊核对钢板2的渗透百分比可以通过将P2除以T2,再将结果乘以100得到。
为了确定对钢板2与钢板3之间接合处的渗透情况,在“c”点到“d”点之间绘制一条虚线,然后测量P3和P4的距离。
需要注意的是,测量P3和P4距离的箭头既与焊核垂直,也与虚线垂直,然后测量焊核渗透进钢板的最大距离。
焊核对钢板2的渗透百分比可以通过将P3除以T2,再将结果乘以100得到。
焊核对钢板3的渗透百分比可以通过将P4除以T3,再将结果乘以100得到。
2.8.3裂缝
如果焊接周围的热影响区出现裂缝或在点焊焊核中出现裂缝(从冶金横截面中可以看出),则焊接不符合本标准的要求。
3、定义
误差焊接-不同与本标准要求的一种误差焊接。
尽管这些焊接有所不同,但它们可能有有益的工程特性。
设备设置鉴定-确保设备能够根据本标准的要求进行焊接的一种行为。
镀锌的用来描述钢板表面上非合金锌镀层的一个术语。
可以通过以下描述的工序应用这一镀层:
-电镀锌的-用来描述通过在钢板上进行锌电解沉积而生成锌镀层的一个术语。
-热浸镀锌的-用来描述通过将钢板浸入锌溶液中而生成锌镀层的一个术语。
镀锌的(通过后电镀技术):
-增加了镀锌零件,被认为等同于电镀锌的钢板。
锌镀层退火处理的-用来描述钢板表面上锌铁合金镀层的一个术语。
这一镀层可以通过对非合金锌镀层进行热处理后获得。
-锌铁电镀锌的-用来描述通过在钢板上进行锌和铁电解共沉积而生成锌铁镀层的一个术语。
调节金属层-两层焊接件中较薄的那一层,或三层焊接件中间的那一层(关于“中间厚度”的描述请参见2.6.1和图3)。
热影响区-点焊焊核周围的基体金属部分,其机械性能或微观结构因接触点焊的热量而受到了改变。
层压钢板-通过一个提供充分冲压的粘弹性层进行连接的两块钢板。
有时还称为金属塑性合金(MPM)或三明治钢。
更大的点焊焊核直径-一种点焊焊核直径,约为正在焊接的较薄的钢板的厚度平方根的5至6倍。
接触点焊金相检验-首先在稍微靠近中间的一个点刺穿接触点焊,这样在准备工作(砂纸打磨和抛光)结束后就可以露出焊接件正中间。
然后在热影响区以