普通本科毕业设计方案论证.docx
《普通本科毕业设计方案论证.docx》由会员分享,可在线阅读,更多相关《普通本科毕业设计方案论证.docx(9页珍藏版)》请在冰豆网上搜索。
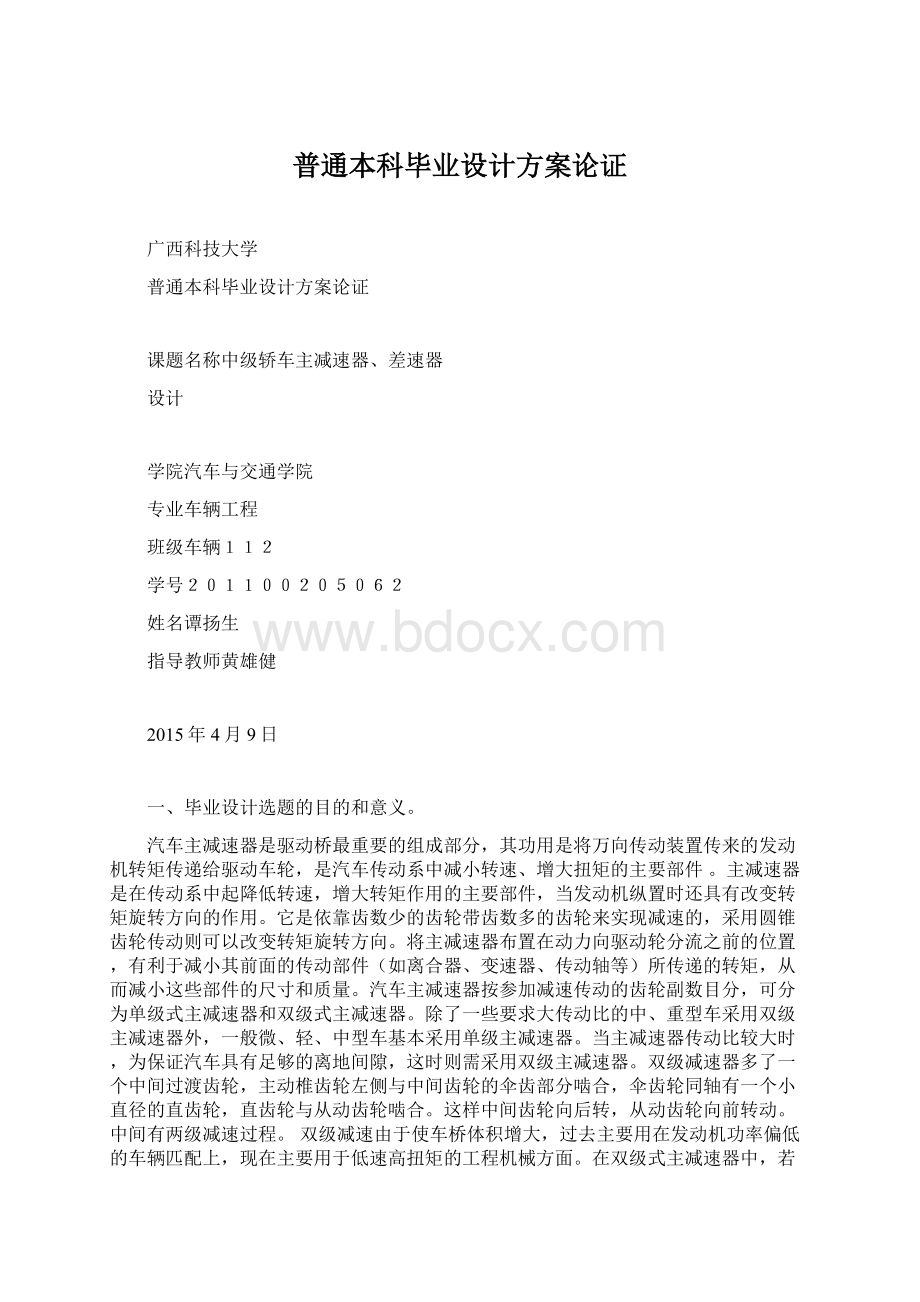
普通本科毕业设计方案论证
广西科技大学
普通本科毕业设计方案论证
课题名称中级轿车主减速器、差速器
设计
学院汽车与交通学院
专业车辆工程
班级车辆112
学号201100205062
姓名谭扬生
指导教师黄雄健
2015年4月9日
一、毕业设计选题的目的和意义。
汽车主减速器是驱动桥最重要的组成部分,其功用是将万向传动装置传来的发动机转矩传递给驱动车轮,是汽车传动系中减小转速、增大扭矩的主要部件。
主减速器是在传动系中起降低转速,增大转矩作用的主要部件,当发动机纵置时还具有改变转矩旋转方向的作用。
它是依靠齿数少的齿轮带齿数多的齿轮来实现减速的,采用圆锥齿轮传动则可以改变转矩旋转方向。
将主减速器布置在动力向驱动轮分流之前的位置,有利于减小其前面的传动部件(如离合器、变速器、传动轴等)所传递的转矩,从而减小这些部件的尺寸和质量。
汽车主减速器按参加减速传动的齿轮副数目分,可分为单级式主减速器和双级式主减速器。
除了一些要求大传动比的中、重型车采用双级主减速器外,一般微、轻、中型车基本采用单级主减速器。
当主减速器传动比较大时,为保证汽车具有足够的离地间隙,这时则需采用双级主减速器。
双级减速器多了一个中间过渡齿轮,主动椎齿轮左侧与中间齿轮的伞齿部分啮合,伞齿轮同轴有一个小直径的直齿轮,直齿轮与从动齿轮啮合。
这样中间齿轮向后转,从动齿轮向前转动。
中间有两级减速过程。
双级减速由于使车桥体积增大,过去主要用在发动机功率偏低的车辆匹配上,现在主要用于低速高扭矩的工程机械方面。
在双级式主减速器中,若第二级减速在车轮附近进行,实际上构成两个车轮处的独立部件,则称为轮边减速器。
这样作的好处是可以减小半轴所传递的转矩,有利于减小半轴的尺寸和质量。
轮边减速器可以是行星齿轮式的,也可以由一对圆柱齿轮副构成。
当采用圆柱齿轮副进行轮边减速时可以通过调节两齿轮的相互位置,改变车轮轴线与半轴之间的上下位置关系。
这种车桥称为门式车桥,常用于对车桥高低位置有特殊要求的汽车。
单级减速器就是一个主动椎齿轮(俗称角齿),和一个从动伞齿轮(俗称盆角齿),主动椎齿轮连接传动轴,顺时针旋转,从动伞齿轮贴在其右侧,啮合点向下转动,与车轮前进方向一致。
由于主动锥齿轮直径小,从动伞齿轮直径大,达到减速的功能。
改革开放以来,中国的汽车工业得到了长足发展,尤其是加入WTO以后,我国的汽车市场对外开发,汽车工业逐渐成为世界汽车整体市场的一个重要组成部分。
同样,车用减速器也随着整车的发展不断成长和成熟起来,一代减速器设计开发的突出特点是:
不仅在产品性能参数上进一步进设计上完全遵从模块化设计原则,产品配套实现车型的平台化,造型和结构更加合理,更宜于组织批量生产,更适应现代工业不断发展,更能应对频繁的车型换代和产品系列化的特点,这些都对基础件产品提出愈来愈高的配套要求,需要在产品设计上不断地进行二次开发和持续改进,以满足快速多变的市场需求。
因此,研究汽车主减速器具有重大意义。
二、毕业设计方案选型
1.本设计车型的主要参数:
外型尺寸(长
宽
高):
4500×1700×1400
前后轮距:
1414/1422mm
总质量:
1590kg
整备质量:
1040kg
满载轴荷分配(前/后)(kg):
742/748
最小离地间隙:
160mm
最高车速:
165km/h
发动机最大扭矩:
145/3500(N.m/r/min)
发动机额定转速下功率:
66kw/5200r/min
变速器速比:
1档3.456,2档1.945,3档1.287,4档0.919,5档0.811倒档3.267
主减速器速比:
4.119
轮辋规格:
3.50B,轮胎类型与规格:
185/70SR13
2.1主减速器的齿轮类型
主减速器的减速型式分为单级减速、双级减速、双速减速、单级贯通、双级贯通、主减速及轮边减速等。
(1)单级主减速器
由于单级主减速器具有结构简单、质量小、尺寸紧凑及制造成本低廉的优点,广泛用在i≤7的各种中、小型汽车上。
单级主减速器都是采用一对螺旋锥齿轮或双曲面齿轮,也有采用蜗轮传动的。
(2)双级减速
由两级齿轮减速器组成,结构复杂、质量加大,制造成本也显著增加,因此仅用于主减速比较大,i一般为7-12,且采用单级减速不能满足既定的主减速比和离地间隙要求的中、重型汽车上。
(3)双速主减速器
双速主减速器用于载荷及道路状况变化大、使用条件非常复杂的重型载货汽车。
会加大驱动桥的质量,提高制造成本,并要增设较复杂的操纵装置。
(4)单级贯通式主减速器、双级贯通式主减速器
单级贯通式主减速器、双级贯通式主减速器用于多桥驱动汽车上。
(5)主减速器附轮边减速器
主减速器附轮边减速器应用于矿山、水利及其他大型工程等所用的重型汽车,工程和军事上用的重型牵引越野汽车及大型公共汽车等。
综上所述,本车采用单级主减速器。
2.2主减速器齿轮类型的选择
在现代汽车驱动桥上,主减速器采用得最广泛的是螺旋锥齿轮和双曲面齿轮。
圆柱齿轮传动应用于发动机横置的前置前驱动乘用车和双级主减速器驱动桥。
在某些公共汽车、无轨电车和超重型汽车的主减速器上,有时也采用蜗轮传动。
(1)螺旋锥齿轮
其主、从动齿轮轴线相交于一点。
交角可以是任意的,但在绝大多数的汽车驱动桥上,主减速齿轮副都是采用90º交角的布置。
由于轮齿端面重叠的影响,至少有两对以上的轮齿同时啮合,因此,螺旋锥齿轮能承受大的负荷。
加之其轮齿不是在齿的全长上同时啮合,而是逐渐地由齿的一端连续而平稳地转向另—端,使得其工作平稳,即使在高速运转时,噪声和振动也是很小的。
(2)双曲面齿轮
其主、从动齿轮轴线不相交而呈空间交叉。
其空间交叉角也都是采用90º。
主动齿轮轴相对于从动齿轮轴有向上或向下的偏移,称为上偏置或下偏置。
这个偏移量称为双曲面齿轮的偏移距。
当偏移距大到一定程度时,可使一个齿轮轴从另一个齿轮轴旁通过。
这样就能在每个齿轮的两边布置尺寸紧凄的支承。
这对于增强支承刚度、保证轮齿正确啮合从而提高齿轮寿命大有好处。
双曲面齿轮的偏移距使得其主动齿轮的螺旋角大于从动齿轮的螺旋角。
因此,双曲面传动齿轮副的法向模数或法向周节虽相等,但端面模数或端面周节是不等的。
主动齿轮的端面模数或端面周节大于从动齿轮的。
这一情况就使得双曲面齿轮传动的主动齿轮比相应的螺旋锥齿轮传动的主动齿轮有更大的直径和更好的强度和刚度。
其增大的程度与偏移距的大小有关。
另外,由于双曲面传动的主动齿轮的直径及螺旋角都较大,所以相啮合齿轮的当量曲率半径较相应的螺旋锥齿轮当量曲率半径为大,从而使齿面间的接触应力降低。
随偏移距的不同,双曲面齿轮与接触应力相当的螺旋锥齿轮比较,负荷可提高至175%。
双曲面主动齿轮的螺旋角较大,则不产生根切的最少齿数可减少,所以可选用较少的齿数,这有利于大传动比传动。
当要求传动比大而轮廓尺寸又有限时,采用双曲面齿轮更为合理。
因为如果保持两种传动的主动齿轮直径一样,则双曲面从动齿轮的直径比螺旋锥齿轮的要小,这对于主减速比i≥4.5的传动有其优越性。
当传动比小于2时,双曲面主动齿轮相对于螺旋锥齿轮主动齿轮就显得过大,这时选用螺旋锥齿轮更合理,因为后者具有较大的差速器可利用空间。
由于双曲面主动齿轮螺旋角的增大,还导致其进入啮合的平均齿数要比螺旋锥齿轮相应的齿数多,因而双曲面齿轮传动比螺旋锥齿轮传动工作得更加平稳、无噪声,强度也高。
双曲面齿轮的偏移距还给汽车的总布置带来方便。
(3)圆柱齿轮传动
一般采用斜齿轮,广泛应用于发动机横置且前置前驱动的轿车驱动桥。
(4)蜗杆传动
与锥齿传动相比,蜗杆传动有如下优点
①在轮廓尺寸和结构质量较小的情况下,可得到较大的传动比(可大于7);
②在任何转速下使用均能工作得非常平稳且无噪声;
③便于汽车的总布置及贯通式多桥驱动的布置;
④能传递大的载荷,使用寿命长。
但是由于蜗轮齿圈要求用高质量的锡青铜制作,故成本较高;另外,传动效率较低。
在此不采用。
像圆柱齿轮传动只在节点处一对齿廓表面为纯滚动接触而在其他啮合点还伴随着沿齿廓的滑动一样,螺旋锥齿轮与双曲面齿轮传动都有这种沿齿廓方向的滑动。
此外,双曲面齿轮传动还具有沿齿长方向的纵向滑动。
这种滑动促使齿轮副沿整个齿面都能较好地啮合,因而更促使其工作平稳和无噪声。
但双曲面齿轮的纵向滑动产生较多的热量,使接触点的温度升高,因而需要用专门的双曲面齿乾油来润滑,且其传动效率比螺旋锥齿轮略低,达96%。
其传动效率与倔移距有关,特别是与所传递的负荷大小及传动比有关。
负荷大时效率高。
螺旋锥齿轮也是一样,其效率可达99%。
两种齿轮在载荷作用下对安装误差的敏感性本质上是相同的。
如果螺旋锥齿轮的螺旋角与相应的双曲面主、从动齿轮螺旋角的平均值相同,则双曲面主动齿轮的螺旋角比螺旋锥齿轮的大,而其从动齿轮的螺旋角则比螺旋锥齿轮的小,因而双曲面主动齿轮的轴向力比螺旋锥齿轮的大,而从动齿轮的轴向力比螺旋锥齿轮的小。
两种齿轮都在同样的机床上加工,加工成本基本相同。
然而双曲面传动的小齿轮较大,所以刀盘刀顶距较大,因而刀刃寿命较长。
综上所述各种齿轮类型的优缺点,本文设计的中级轿车大多用于私家车,应该优先选择驾驶平稳,噪声和振动小传动方式,所以本设计主减速器采用螺旋锥齿轮传动更合理。
2.3主减速器主、从动锥齿轮的支承方案
主减速器中必须保证主、从动齿轮具有良好的啮合状况,才能使它们很好的工作。
齿轮的正确啮合,除与齿轮的加工质量、装配调整及轴承、主减速器壳体的刚度有关以外,与齿轮的支承刚度密切相关。
1)主动锥齿轮的支承方案
主动锥齿轮的支承形式可分为悬臂式支承和跨置式支承两种。
悬臂式支承结构(图2-1a)的特点是在锥齿轮大端一侧采用较长的轴颈,其上安装两个圆锥滚子轴承。
为了减小悬臂长度倪和增加两支承间的距离b,以改善支承刚度,应使两轴承圆锥滚子的大端朝外,使作用在齿轮上离开锥顶的轴向力由靠近齿轮的轴承承受,而反向轴向力则由另一轴承承受。
为了尽可能地增加支承刚度,支承距离b应大于2.5倍的悬臂长度a,且应比齿轮节圆直径的70%还大,另外靠近齿轮的轴径应不小于尺寸a。
为了方便拆装,应使靠近齿轮的轴承的轴径比另一轴承的支承轴径大些。
靠近齿轮的支承轴承有时也采用圆柱滚子轴承,这时另一轴承必须采用能承受双向轴向力的双列圆锥滚子轴承。
支承刚度除了与轴承形式、轴径大小、支承间距离和悬臂长度有关以外,还与轴承与轴及轴承与座孔之间的配合紧度有关。
a)主动锥齿轮悬臂式b)主动锥齿轮跨置式 c)从动锥齿轮
图2-1主减速器锥齿轮的支承形式
悬臂式支承结构简单,支承刚度较差,用于传递转矩较小的轿车、轻型货车的单级主减速器及许多双级主减速器中。
跨置式支承结构(图2-1b)的特点是在锥齿轮的两端均有轴承支承,这样可大大增加支承刚度,又使轴承负荷减小,齿轮啮合条件改善,因此齿轮的承载能力高于悬臂式。
此外,由于齿轮大端一侧轴颈上的两个相对安装的圆锥滚子轴承之间的距离很小,可以缩短主动齿轮轴的长度,使布置更紧凑,并可减小传动轴夹角,有利于整车布置。
但是跨置式支承必须在主减速器壳体上有支承导向轴承所需要的轴承座,从而使主减速器壳体结构复杂,加工成本提高。
另外,因主、从动齿轮之间的空间很小,致使主动齿轮的导向轴承尺寸受到限制,有时甚至布置不下或使齿轮拆装困难。
跨置式支承中的导向轴承都为圆柱滚子轴承,并且内外圈可以分离或根本不带内圈。
它仅承受径向力,尺寸根据布置位置而定,是易损坏的一个轴承。
参考所选车型属于中级轿车,一般用作私家车,传递最大扭矩不是很大,因此主减速器主动锥齿轮采用悬臂式支承。
2)从动锥齿轮的支承选择
从动锥齿轮的支承(图2-1c),其支承刚度与轴承的形式、支承间的距离及轴承之间的分布比例有关。
从动锥齿轮多用圆锥滚子轴承支承。
为了增加支承刚度,两轴承的圆锥滚子大端应向内,以减小尺寸c+d。
为了使从动锥齿轮背面的差速器壳体处有足够的位置设置加强肋以增强支承稳定性,c+d应不小于从动锥齿轮大端分度圆直径的70%。
为了使载荷能尽量均匀分配在两轴承上,应尽量使尺寸c等于或大于尺寸d。
在具有大的主传动比和径向尺寸较大的从动锥齿轮的主减速器中,为了限制从动锥齿轮因受轴向力作用而产生偏移,在从动锥齿轮的外缘背面加设辅助支承。
辅助支承与从动锥齿轮背面之间的间隙,应保证偏移量达到允许极限时能制止从动锥齿轮继续变形.
3.1差速器结构形式的选择
汽车在行驶过程中左,右车轮在同一时间内所滚过的路程往往不等。
例如,转弯时内、外两侧车轮行程显然不同,即外侧车轮滚过的距离大于内侧的车轮;汽车在不平路面上行驶时,由于路面波形不同也会造成两侧车轮滚过的路程不等;即使在平直路面上行驶,由于轮胎气压、轮胎负荷、胎面磨损程度不同以及制造误差等因素的影响,也会引起左、右车轮因滚动半径的不同而使左、右车轮行程不等。
如果驱动桥的左、右车轮刚性连接,则行驶时不可避免地会产生驱动轮在路面上的滑移或滑转。
这不仅会加剧轮胎的磨损与功率和燃料的消耗,而且可能导致转向和操纵性能恶化。
为了防止这些现象的发生,汽车左、右驱动轮间都装有轮间差速器,从而保证了驱动桥两侧车轮在行程不等时具有不同的旋转角速度,满足了汽车行驶运动学要求。
差速器用来在两输出轴间分配转矩,并保证两输出轴有可能以不同的角速度转动。
差速器主要有以下几种形式。
(1)对称式圆锥行星齿轮差速器
图3-1普通的对称式圆锥行星齿轮差速器
图3-1所示,普通的对称式圆锥行星齿轮差速器由差速器左、右壳,2个半轴齿轮,4个行星齿轮(少数汽车采用3个行星齿轮,小型、微型汽车多采用2个行星齿轮),行星齿轮轴(不少装4个行星齿轮的差逮器采用十字轴结构),半轴齿轮及行星齿轮垫片等组成。
由于其结构简单、工作平稳、制造方便、用在公路汽车上也很可靠等优点,最广泛地用在轿车、客车和各种公路用载货汽车上.有些越野汽车也采用了这种结构,但用到越野汽车上需要采取防滑措施。
例如加进摩擦元件以增大其内摩擦,提高其锁紧系数;或加装可操纵的、能强制锁住差速器的装置——差速锁等。
由于整速器壳是装在主减速器从动齿轮上,故在确定主减速界从动齿轮尺寸时,应考虑差速器的安装。
差速器壳的轮廓尺寸也受到从动齿轮及主动齿轮导向轴承支座的限制。
(2)强制锁止式防滑差速器
图3-2强制锁止式防滑差速器
如图3-2所示,强制锁止式防滑差速器就是在普通的圆锥齿轮差速器上加装差速锁,必要时将差速器锁住。
此时左、右驱动车轮可以传递由附着力决定的全部转矩。
当汽车驶入较好的路面时,差速器的锁止机构应即时松开,否则将产生与无差速器时一样的问题,例如使转弯困难、轮胎加速磨损、使传动系零件过载和消耗过多的功率等。
(3)自锁式差速器
为了充分利用汽车的牵引力,保证转矩在驱动车轮间的不等分配以提高抗滑能力,并避免上述强制锁止式差速器的缺点,创造了各种类型的自锁式差速器。
用以评价自锁式差速器性能的主要参数,是它的锁紧系数。
为了提高汽车的通过性,似乎是锁紧系数愈大愈好,但是过大的锁紧系数如前所述,不但对汽车转向操纵的轻便灵活性、行驶的稳定性、传动系的载荷、轮胎磨损和燃料消耗等,有不同程度的不良影响,而且无助于进一步提高驱动车轮抗滑能力。
因此设计高通过性汽车差速器时,应正确选择锁紧系数值。
因为本车属于中级轿车,主要在较好的路面上行驶,所以采用成本低廉、结构简单的对称式圆锥行星齿轮差速器。
本设计方案如下:
设计车型:
中级轿车
驱动形式:
前置前驱
主减速器:
单级主减速器
齿轮传动方式:
螺旋锥齿轮
主动锥齿轮支承方式:
悬臂式
从动锥齿轮支承方式:
跨置式
差速器:
普通对称式圆锥行星齿轮(2个)
其简图如下:
三、毕业设计主要内容和重点
本设计师在给定变速器输出转矩,转速及最高车速,最大爬坡度等条件下,独立设计出符合要求的主减速器和差速器。
着重设计计算齿轮结构参数及对其进行校核计算。
在对各种结构件进行了分析计算后,绘制出主减速器装配图及主要零件图。
四、毕业设计工作进度计划
第四周:
进行方案论证。
第五周:
查找相关车型的设计数据,对主减速器、差速器零部件进行设计计算。
第六、七周:
确定零部件主要参数,设计、计算校核以及论证。
第八、九、十周:
完成三维设计数模及设计图纸。
第十一、、十二、十三周:
整理完成说明书;进行外文翻译;检查图纸及设计说明书,订正错误。
为答辩做好充分准备
五、主要参考文献目录
刘惟信.汽车车桥设计.北京:
清华大学出版社,2006年5月
杨华骥等主编.齿轮手册2000版.北京:
机械工业出版社,2005年
刘惟信.汽车齿轮.北京:
人民交通出版社,1980年12月
黄华梁彭文生.机械设计基础.北京:
高等教育出版社,2001年6月[
王昆何小柏汪信远.机械设计基础课程设计.北京:
高等教育出版社,1995年12月
陈家瑞.汽车构造(下册).北京:
机械工业出版社,2006年5月
张秀艳.画法几何及机械制图.北京:
高等教育出版社,2005年8月
成大先.机械设计手册.北京.化学工业出版社.1994年4月
王望予汽车设计.北京:
机械工业出版社,2007年5月
刘惟信汽车设计.北京:
清华大学出版社,2004月7月
<<汽车工程手册>>编辑委员会主编.汽车工程手册,北京:
机械工业出版社.2004年8月
吴宗泽.机械零件设计手册.第三版.北京:
机械工业出版社,2003年11月
<<实用机械设计手册>>编委会主编.实用机械设计手册,北京:
机械工业出版社.1984年
余志生汽车理论.北京:
清华大学出版社,2005年3月.
孙桓等机械原理.北京:
高等教育出版社,2006年5月
六、指导教师审查意见
报告内容和形式符合要求。
课题立意比较明确,技术路线可靠,研究内容充实,研究方法有效,设计路线基本可行性,具体实施方案,需在进一步设计中完善。
课题具有一定的研究基础,能达到预期目标,同意开题。
指导教师签字:
年月日