快速成型技术在模具制造中的应用.docx
《快速成型技术在模具制造中的应用.docx》由会员分享,可在线阅读,更多相关《快速成型技术在模具制造中的应用.docx(7页珍藏版)》请在冰豆网上搜索。
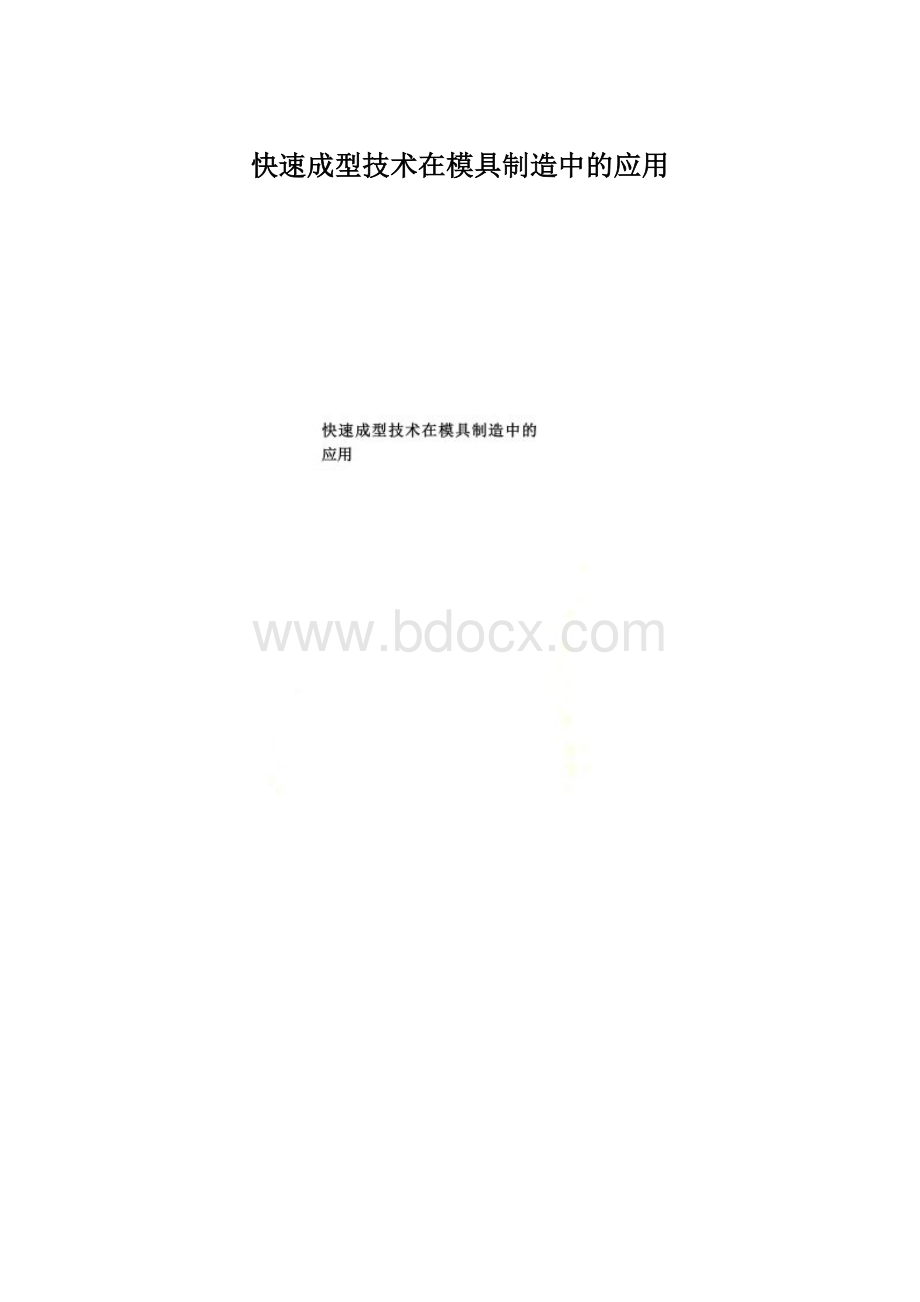
快速成型技术在模具制造中的应用
法。
二基于RP技术的模具制作方法
传统的模具制造方法可分为两种,一种是借助母模翻制模具,另一种就是用数控机床直接制造模具。
在新产品开发过程中,减少模具制造所需成本和时间对缩短整个产品开发时间及降低成本是最有效的步骤,快速成型技术的一个飞跃就是进入模具制造领域,其潜力所在正是能降低模具制造成本并减少模具开发时间。
将快速成型技术引入模具制造过程后的模具开发制造就是快速模具制造。
快速成型技术在模具制造领域的应用主要是用来制作模具设计制造过程中所用的母模,有时也用快速成型技术直接制造模具。
因此可以将基于RP的快速模具制造分为两类,即:
直接制模法和间接制模法。
(一)直接制模法
1SLS激光粉末烧结
一般的工艺流程为:
先在基底上铺上一层粉末,压辊压实后,用激光有选择的烧结一个层面。
然后新的一层粉末通达铺粉装置铺在上面,进行下一层烧结,反复进行直至得到最终的零件。
目前主要有两种商品化的SLS工艺:
一是美国DTM公司的RapidTool工艺;另一种是德国EOS公司的DirectTool工艺[1]。
RapidTool工艺
该工艺采用激光烧结包覆有粘结剂的钢粉,由计算机控制激光束的扫描路径,加热融化后的粘结剂将金属粉末粘结在一起,生成约有45%孔隙率的零件,干燥后,放入高温炉膛内进行烧结、渗铜,生成表面密实的零件,此时零件中上材料成分为65%的钢和35%的铜。
经过打磨等后处理工序后,得到最终的模具。
DirectTool工艺
通过烧结过程使低熔点金属向基体金属粉末中渗透来增大粉末间隙,产生尺寸膨胀抵消烧结收缩,使最终的收缩率几乎为零。
23DPrinting
由MIT开发的3DP技术已发展成可利用喷头有选择地向金属粉末喷射粘结剂,利用粘结剂使金属粉末成型。
这种低密度的(约为50%)成型件也要经过去除粘结剂和渗铜处理,最终得到密度达92%以上的模件。
其成型厚度为0.17mm,因而其尺寸精度只达到±0.1mm的水平。
这种方法的优点是可以制造的材料多种多样,这种多样性既可体现在不同模件上,也可体现在同一个模件上,其尺寸也可以比较大,几何形状任意,过程简单,是一种比较看好的技术。
3光固化法制作注射成型模具
这是一种以环氧树脂基的光敏树脂为原料在SL设备上成型的方法。
它用密集激光束过量扫描待成型表面,即激光束扫描间距很小,甚至部分重合,同时照射非常均匀。
该法制作的快速成型件的精度和表面光洁度在目前所有RP方法中是最好的,因此常用它来制作模具制造中所用的母模。
用此种方法直接制作注射模的型腔或型芯,也达到了非常好的效果,可用于注射多种热塑性的塑料,甚至可注射研磨性的塑料,寿命达200件,价格适中,制作时间一般在2星期左右。
需要注意的是环氧树脂导热性差,虽然带来了可用较小压力注射的好处,也要考虑注射周期问题。
4LOM法
与一般的LOM不同的是,它直接在成型机上进行金属薄板的叠层制造,根据CAD模型,采用激光或水射流方法形成轮廓。
采用扩散粘结将切割的薄板叠全起来,形成伪金属实体零件,由于板村的厚度较大,会产生台阶效应,因此需要精加工处理。
(二)间接制模法
直接制模法根据要求,能够在不同部位采用不同材料。
然而,直接制模法受到工艺本身限制,制造的模具在表面及尺寸精度、大小规格、形状自由度等方面尚不能满足高精度金属模具的要求。
具有竞争力的快速制模方法主要是将快速成型与铸造、喷涂、电镀、粉末成型等传统成型工艺相结合的间接制模法。
间接制模法主要有以下几种方法。
1硅胶模
硅胶模应用非常广泛。
首先用RP法制作出“正”的与待成型件相同的母模,然后在母模周围浇满硅橡胶。
固化后,沿所要求的分型面将硅橡胶切开,取出母模后就制成了硅胶模。
为了保证硅胶模的质量,要求母模表面经过抛光处理,因为模具翻制过程中会将母模表面的几乎所有特征哪怕手印复制到硅胶模成型面上进而复制到零部件上。
硅胶模具有制作速度极快,可以浇铸多种热固性塑料,成型件具有较好精度,价格非常便宜等优点,但硅胶模不能制作精度要求很高的零件,寿命短,通常只能浇铸25~30件。
2环氧树脂模具
制作过程类似硅胶模生产过程,只是将硅胶换成了掺有铝粉的环氧树脂。
整个模具需分两次浇铸制成,因为环氧树脂不能象硅胶那样用刀切分型。
环氧树脂在固化过程中伴有少量收缩,因此母模常会损坏。
环氧树脂的导热性极差,用纯环氧树脂制作的模具进行注塑成型时的热量难以散出,解决的办法就是制作环氧树脂的模具特征表面,背后充填导热性好的材料。
这样制作的模具具有很好的抗压强度,完全可以用于象注塑成型那样的压力成型,具有研磨性的材料也可以注塑,寿命达数千件。
3表面喷涂金属的模具
在RP制作的母模外喷涂一层雾化了的熔化金属,待液态金属固化后形成金属表面。
受喷涂设备和母模受温限制,通常所用金属材料是低熔点金属,如铅锡合金、锌合金和镍等,常用的喷涂方法是电弧喷涂。
如果母模能够耐受高温,也可以喷涂高熔点金属如不锈钢。
此种模具用于注射成型的寿命可达2500件左右,与纯金属模具相比不能用更大的夹持力。
研究成果表明,若在母模表面喷涂镍可进一步提高模具使用寿命,因其具有较高表面硬度(HV=5400N/mm2)和耐磨性,抗腐蚀性好,开模后注射成型件容易取出。
这样的模具在不到两天时间内就可制作完成。
注意这类模具的使用温度不能超过300℃。
4镍和陶瓷混合物模具制造技术
此法利用塑料RP模型作为母型,在母型上用电镀的方法镀上一层镍金属,制造出一个镍金属薄壳,这个薄壳与母型接触的那个表面完全反映了待注射成型零件的表面形状及尺寸特征。
由于薄壳的强度低,因此在薄壳的非成型面以高强度陶瓷粉充填,要求陶瓷材料具有很小的收缩系数和合适的热物理性能。
这种复合材料模具非常适合制造尺寸较大零件(大于250mm×250mm×250mm),如若母型用立体光造型(SL)方法制作,则此法的尺寸精度将不低于SL件的精度,用于塑料注射成型时其寿命至少为5000件。
53DKeltool模具
Keltool是目前被认为是最有发展前景的由一种快速制造金属模具的方法。
它首先用RP母模型制造出精度较高等的硅胶模,再往硅胶模中注入精细粉状的A6工具钢(或不锈钢)与颗粒更加细小的碳化钨的混合物(注意粉末颗粒的大小是控制模具最终质量的一个非常重要的因素)。
然后再向混合物中加入环氧树脂类的粘结剂,从而使金属粉末混合物在硅胶模中形成绿件。
开模后把绿件在炉中加热从而使粘结剂挥发,同时使金属粉末混合物烧结成型,这时的模件中仍有30%的空隙,所以还需做最后渗铜处理,最终得到可用于大批量生产(达百万件)的硬模具。
其尺寸精度每250mm误差为±0.04mm。
不足的是这种方法所能制造的最大模具尺寸目前仅为127mm。
一般用此法可在十多天内完成模具型腔或型芯的制作,与传统CNC机床加工制作相比节约25%~40%的成本。
6铸造法
a)陶瓷型精密铸造法[2]
在单件生产或小批量生产钢模时,可采用此法。
其工艺过程为:
RP原型作母模→浸挂陶瓷沙浆→在烤炉里固化模壳→烧去母模→预热模壳→烧铸钢(铁)型腔→抛光→加入烧注、冷却系统→制成生产用注塑模。
其优点在于工艺装备简单,所得铸型具有极好的复印性和极好的表面光洁度以及较高的尺寸精度。
工程塑料可以高温气化,没有残渣,适用于熔模制造。
b)砂型铸造法
用RP原型作模型来制作砂型,再铸钢而得到模具的工作部分,如果浇钢的性能得到大幅提高,用此法几乎可以制造各种模具,且模具寿命不会有大的降低。
ABS材料的高强度特性,适合制造大的坚固实心模型。
c)石蜡精密铸造法
在批量生产金属模具时可采用此法。
先利用RP原型或根据翻制的硅橡胶、金属树脂复合材料或聚氨脂制成蜡模的成型模,然后利用该成型模生产蜡模,再用石蜡精铸工艺制成钢(铁)模具来。
另外,在单件生产复杂模具时,亦可直接用RP原型代替蜡模。
若用SL法,可将原型制成疏松多孔的蜂窝状结构以便快速浇损,在氧气充足的条件下,树脂原型可在980℃左右分解成水气和CO2。
d)石膏铸造法
利用RP原型翻制成石膏铸型,然后在真空下浇铸铝、锌等非铁合金模,它可小批量生产注塑产品。
用RP原型作模型浇注低熔合金,作成低熔合金模,可用来压制铸造用的砂芯。
7利用RP原型制作电火花加工用的电极
EDM方法在模具制造领域应用非常广泛,它可用来加工形状极其复杂的型腔和型芯,它可以加工硬度极高的用CNC机床无法加工的材料,它还可以加工热处理后的材料,从而避免加工后热处理造成的热变形。
EDM电极的质量是影响加工件质量的关键因素,电极本身的费用占EDM加工过程费用的50%~80%。
目前多用石墨或铜电极,其使用寿命极短,有时为加工一个型腔需更换多个电极,严重影响EDM的加工效率。
用RP方法就可快速制造任意形状的EDM电极,可以弥补这个不足。
a)石墨电极成形法。
利用RP原型翻制石墨电极研具,再利用研具采用平动研磨法制造石墨电极,然后用电火花加工金属模具。
b)电铸铜电极法。
它是在RP原形表面喷涂一层导电介质,然后电铸法在RP原型的表面沉淀一层一定厚度的铜得到电镀铜电极,再利用电极电火花加工模具。
电极成形法的优点在于随着模具型腔复杂程度的提高,批量的增大,其优越性就越能得到体现。
三基于RP的快速模具制造需解决的问题
利用RP技术发展快速模具制造技术还存在以下主要问题需要解决或者说需要进一
步提高[3]。
(1)表面质量如何满足模具的要求,否则无法承受如注射成型这样的高压。
分层制造法不可避免会产生台阶,斜面时更严重,后处理是目前通用的作法。
(2)尺寸精度如何满足模具制造的要求,尤其是制造较大模具时,尺寸更不稳定。
(3)用作母模时的强度,耐热和耐腐蚀性,形状和尺寸的时效问题。
(4)塑料或树脂类模具的导热性很差,导热差虽然带来了可用较低注射压力的好处,但生产周期太长也必须考虑。
(5)多数所谓金属模具都需要最后渗铜,这就造成这种金属模具的使用温度不可太高,可能超过500℃就不行了。
(6)使用寿命的进一步延长和使用成本的进一步降低。
(7)目前所能制造的模具的体积都很小,怎样制造大型模具?
(8)受不可缺少的后处理工序的限制,目前还不能制造具有很小细节特征的模具,尤其是具有内凹形状的模具。
(9)目前快速成型方法所能成型的材料种类及其有限,需要开发新型材料。
结束语
快速成型技术的应用已从原型制造发展到模具制造,使传统的模具制造技术焕发出新的活力,同时快速成型技术在快速模具制造领域的成功应用无疑会给快速成型技术的进一步发展注入新的生命力。
需要注意的是
A如今快速成型制造工艺过程的费用相对于传统机械制造还是比较高的,不要寄希望于用快速成型的方法代替传统大批量生产的方法,即使将来有一天快速成型技术的制造成本和时间数值减少到现有数值的1%,它也无论如何不能与注射成型方法相比。
B随着快速成型技术的进一步发展,它在小批量生产和单体复制领域还是大有可为的。
C快速成型技术对模具制造的贡献,虽然现阶段制作的快速模具质量和寿命还不太尽人意,实践证明仍然可以应用于中小批量的注塑成型和模压铸造,相信快速模具制造技术会在短期内有很大突破。
参考文献
[1]赖耀平,刘美坚基于RP的快速制模技术模具制造2003第18期
[2]邓明,彭成允RP技术在模具制造中的应用锻压技术1999第6期
[3]焦向东,邓双成,张沛等基于快速成型原理的模具制造技术石汕化工高等学校学报2002第1期