实践报告.docx
《实践报告.docx》由会员分享,可在线阅读,更多相关《实践报告.docx(21页珍藏版)》请在冰豆网上搜索。
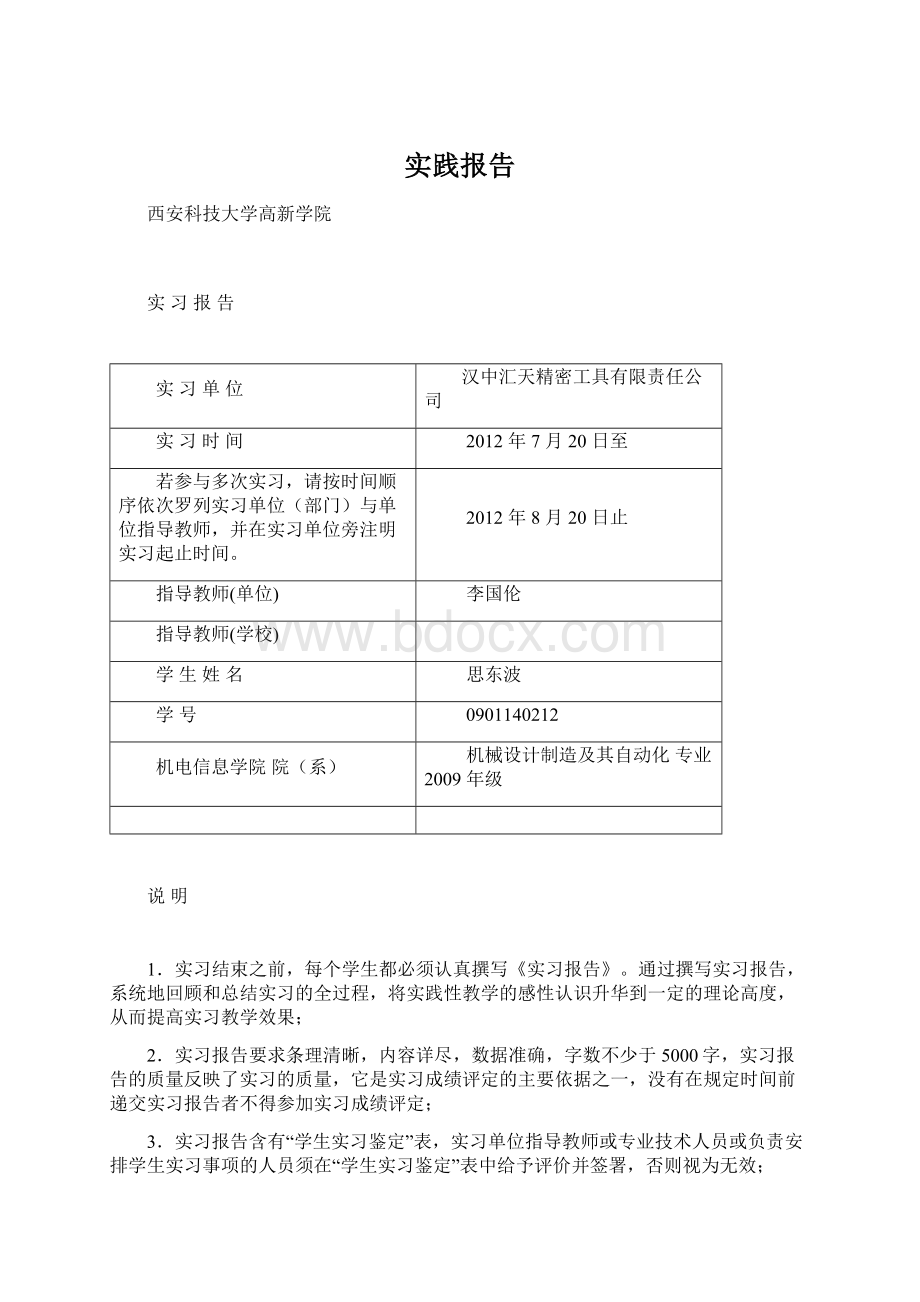
实践报告
西安科技大学高新学院
实习报告
实习单位
汉中汇天精密工具有限责任公司
实习时间
2012年7月20日至
若参与多次实习,请按时间顺序依次罗列实习单位(部门)与单位指导教师,并在实习单位旁注明实习起止时间。
2012年8月20日止
指导教师(单位)
李国伦
指导教师(学校)
学生姓名
思东波
学号
0901140212
机电信息学院院(系)
机械设计制造及其自动化专业2009年级
说明
1.实习结束之前,每个学生都必须认真撰写《实习报告》。
通过撰写实习报告,系统地回顾和总结实习的全过程,将实践性教学的感性认识升华到一定的理论高度,从而提高实习教学效果;
2.实习报告要求条理清晰,内容详尽,数据准确,字数不少于5000字,实习报告的质量反映了实习的质量,它是实习成绩评定的主要依据之一,没有在规定时间前递交实习报告者不得参加实习成绩评定;
3.实习报告含有“学生实习鉴定”表,实习单位指导教师或专业技术人员或负责安排学生实习事项的人员须在“学生实习鉴定”表中给予评价并签署,否则视为无效;
4.封面中的“实习单位”必须写单位的全名,实习单位配指导教师或专业技术人员时应写清姓名;
5.若在不同的单位或部门实习,须分别撰写相应的实习报告(重起目录),由不同实习单位\部门的指导教师填写“学生实习鉴定”表,并将其装订在一起。
只要填写一个封面,实习单位与单位指导教师分别按实习时间顺序罗列出;
6.“前言”部分:
“实习背景”可简介实习目的、学院有关实习的要求、通过何种方式到此单位实习、实习起止时间等内容;“实习环境”可包括实习单位全称(中英文)、地址、实习单位性质、规模、简介、所在部门、该部门主要工作、指导教师安排等内容;
7.“实习内容”部分:
属报告的主要部分。
“实习过程”概述实习各阶段所从事的主要工作等;“实习内容”包括项目介绍、本人从事的工作、软硬件平台和技术等;“实习成果”应具体列出自己所完成的主要成果及实际应用情况等;
8.“总结”部分:
其中“其它意见”可对学院课程设置、教学内容、实习安排等方面提出自己的意见或建议,也可对实习单位的各个方面提出自己的意见;
9.“谢辞”部分:
主要指对实习单位、实习单位指导教师,以及合作者的感谢;
10.实习指导教师批阅意见,由实习指导教师根据实习大纲要求及完成情况对实习报告进行评阅,按百分制给出成绩。
目录
1前言4
1.1实习背景4
1.2实习环境4
2实习内容5
2.1实习过程5
2.2实习内容5
2.3主要成果5
3总结6
3.1实习体会6
3.2其它意见6
谢辞7
学生实习鉴定8
实习指导教师评阅9
1前言
1.1实习背景
造精品利刃,建和谐汇天。
汇天精密工具有限责任公司可为汽车、摩托车、电梯、冶金、矿山、工程机械、石油机械、重型机械、机床、船舶、机车车辆、航天航空等行业提供高精度、高效率、高可靠性、专用化的金属切削刀具。
热忱欢迎海内外朋友光临惠顾。
汇天精密工具有限责任公司是中国机床工具行业大型重点骨干企业,国家大型精密复杂刀具的重要制造基地。
公司拥有进出口自营权。
陕西省大型复杂刀具研究所设在公司内,可承担各类金属切削刀具的开发与制造。
公司金属切削刀具,以其高精度、高效率、高可靠性的特点在中国工具行业和广大顾客中树立起良好的品牌形象,深受广大顾客的信赖。
公司主要产品有:
齿轮刀具、拉削刀具、螺纹刀具和钻、铣、铰……
1.2实习环境
公司位于陕西南部汉中市高新技术产业开发区,占地面积12000平方米年产值2000万元人民币。
公司拥有各类机械加工设备及拉削刀具制造专用机床40余台,大型精密检测仪器5台,是中国拉削刀具专业生产企业。
公司以雄厚的生产能力和高精的检测手段使“智海精密”品牌的产品销往全国各地区,以及欧、美市场。
在汽车、机械、航空、冶金、电子等行业,智海精密品牌得到广大用户的好评。
智海精密机械工具有限责任公司现拥有一批现代化企业管理和高精刀具设计制造的专业人才,现有高级管理人员6名,工程技术人员6名,技师8名,中级技术工人30名。
公司已全面通过了ISO9001质量管理体系认证,获得产品进出口经营权。
质量管理活动在各小组广泛开展,使产品从投入到成品,有一个完整的质量保证体系。
我公司已获得企业产品进出口经营权。
公司按照“以人为本,质量第一,服务至上”的宗旨,将智海精密拉削刀具打造成为中国第一品牌。
2实习内容
2.1实习过程
进入车间见习才是我真正意义上开始接触溶模制造。
对我来说一切都是新鲜的,在车间,许多很简单的问题对于我来说,都有可能成为难点,但这不是解决不了的理由,是谁都需要经历的一个过程。
在不断的学习中,不断的摸索中,去培养自己的自主学习能力,思考问题能力。
我首先了解了生产制作流程,然后又逐步了解了熔模铸造工艺及各工序控制要点,以及溶模铸造的基本知识。
制造部主要包括型壳、浇注、后处理、热处理、机加工几大车间。
产品的一般生产流程为:
压蜡→蜡检→修蜡→组树→制壳→浇铸→光谱检→切割、初抛→清理→初检→焊修→中检→热处理→热处理检→加工浇口→整形→中整检→咬酸、抛丸、喷砂→酸洗→酸检→整形、清洗→酸整检→表面处理→表面检→毛坯库→内、外部加工→外抛光→加工检→内、外部热处理→整形装配→装配检→内、外部表面终处理→表面终检→成品库。
每道工序都安排有师傅,在师傅的细心辅导下,我对每道工序应该注意的。
1,型壳车间:
压蜡:
此工序与产品模具直接接触,与研发课工作联系密切。
整个型壳车间是产品的最初阶段,也是最关键的阶段。
万事开头难,蜡模的质量直接关系到产品表面尺寸和质量的好坏。
操作时注意射蜡湿度、压力、流速、保压时间,以及产生各种缺陷(如:
凹陷、气泡、缩孔、蜡模破裂、油温冷叠、射不满)的原因以及对后序产品的影响。
作为研发人员还要特别注意,不同结构产品模具的设计方法、模具型腔尺寸与蜡模尺寸的差异等。
修蜡:
则主要是将冷却后的蜡模表面合模线、飞边、射蜡口修补过渡圆顺;凹陷填平、气泡挑破补平,油纹擦净等。
一切表面缺陷修补完好。
这道工序要求操作者要集中精力,以防不小心用修蜡刀把蜡件划伤。
组树:
本工序主要与工艺课的关系紧密,它直接反映工艺出品率。
组数时注意树上的蜡模上表面距浇口杯上边缘>90mm,蜡模间距>9mm,蜡模放置角度要利于脱蜡,内浇口长度12~25mm利于切割。
焊接处无凹陷、无缝隙、无尖边、无蜡片粘符。
组树还要注意的一个原则是尽量保证工件在脱蜡时蜡能全部排出。
制壳:
所需要的材料有碱性硅溶胶、锆英粉(用来配制面层涂料)、锆英砂(用于面层撒砂)、煤矸石粉(用于配制背层涂料)、煤矸石砂(是制背层型壳的撒砂)。
制壳的工序比较复杂,所需要注意的地方如:
各种材料的混合比例、温度、湿度、干燥时间的控制等。
型壳质量的好坏直接在铸件表面体现出来,比如铸件表面的毛刺、裂纹、跑火、剥落、回溶、壳裂、鼓胀、夹砂等缺陷,都和浆料的配制、搅拌时间以及浆料的粘度、干燥过程中的温度和湿度有着及大的关系。
脱蜡和蜡处理:
要注意的就是温度、压力、时间、以及脱蜡釜、脱蜡用水分蒸发器、除水桶、静置桶、保温箱操作规程等。
脱蜡过程要迅速,从带蜡模壳推进脱蜡釜至达到0.56Mpa压力时间<14S,才能实现瞬间脱蜡,减小因蜡模膨胀造成的模壳损坏。
压力控制在0.8~0.9Mpa持续9~18分钟,保证脱蜡完全。
通过在型壳车间的见习,我不但对在型壳车间的各工序进行学习并参与实践操作,更重要的是对铸造用的蜡型模具有了初步认识,对蜡和硅溶胶制壳体的性质和特性也有了一定了解。
如产品在设计过程中,有些地方模具无法实现,有些地方制壳无法实现或反映在蜡模上会出现各种缺陷。
这对我以后的工作将会有很大的帮助。
2,浇注车间浇注主要有焙烧、熔炼、浇注、振壳、切割、初抛等工序。
需要注意的是焙烧、熔炼、浇注的温度、时间,还有炉前的经济配料。
以及产生各种缺陷的分类和原因。
铸造过程中熔炼是一个十分重要的环节。
它除了对材质、熔炼温度、熔炼时间以及脱氧剂的添加量有严格的控制以外。
还需要求熔炼师傅们具有专业的技术知识及丰富的工作经验,才能熔炼出合格的钢液。
在浇铸、振壳、切割这些工序中最要注意的是安全。
要严格遵守安全制度,严守纪律,确保安全第一!
浇铸后的铸件经冷却后,方可转入振壳工序。
振壳分机械振壳和人工振壳。
对于一些用横模头组合的铸件树要用人工振壳,人工振壳比较慢、效率低。
但一些用竖模头来组合的铸件树就可以用机振了,省时省力,效率也高。
为了进一步清除铸件表面残留的型壳。
在切割以前要进行悬挂抛丸。
就是在悬挂式抛丸机内用喷射铸铁砂丸的方式将整棵铸件树上的残壳清除掉。
但也不是所有的铸件都要先抛丸再切割,有一些结构简单、内浇口处残留型壳较少的产品,也可以直接进行切割。
切割时不可以切伤铸件本体,但也不可以留有太长的内浇口,大概有1—2mm即可。
通过在浇铸车间的见习,我对浇铸车间的各工序有了更直观的认识。
对壳体的性质有了更深的了解,
3,后处理车间后处理主要是对产品表面质量和整体形状进行处理。
它的工序最为复杂,包括抛丸、喷砂、咬酸、酸洗、粗磨、精磨、整形、焊修、电抛光、研磨等工序。
它与质检车间毛坯检的联系紧密,产品在它们两者之间不停的流动,直到合格入毛坯库。
在后处理工序中,产品没有固定的工艺流程,通常根据产品结构和现场的工作安排来协调加工流程。
如在清理过程中,抛丸、喷砂、粗磨就没有先后顺序可以根据现场情况协调。
有需要咬酸的清理过程中在咬完酸后进行抛丸再喷砂,根据产品结构和质量要求选择咬酸时机。
对于表面质量要求比较高的产品。
要进行喷砂处理。
喷砂是以压缩空气为动力,通过喷枪将砂轮速喷击铸件表面,以清除残留在铸件外表和内孔中的残砂及氧化皮。
工艺对喷砂使用的砂的种类、粗细以及喷砂压力都有明确要求。
因为压力过大容易造成产品表面损伤。
操作时还要注意不要把铸件正对喷枪口摆放。
以防喷伤铸件。
喷砂后的产品表面比抛丸后的产品表面细腻得多。
粗磨是用砂布带将内浇口磨低,磨至离铸件表面高度小于1mm.然后精磨,根据不同表面质量要求的产品,选用不同粗细的砂布带进行精磨。
精磨时必须精力集中,以防磨伤产品表面从检验车间转到焊修车间的都是表面有缺陷的产品。
一般来说产品的表面缺陷可分为两大类:
凸出类和凹陷类。
凸出类缺陷有:
飞边、毛刺、钢豆或较明显的合模线等。
凹陷类缺陷有:
气孔、缩坑、切伤、磨伤等。
修磨和焊补即是分别针对表面这两大缺陷的修补方式。
修磨主要就是利用气动风枪、绞磨机等修磨工具,装上不同型号和类型的磨头。
把产品表面的凸出类缺陷修平、磨平。
修产品大表面上的凸出类缺陷的时候会选择砂磨头,比较快。
但是有一些孔、沟、槽等砂磨头修不到的地方就会用到钢磨头。
因为钢磨头比较细,修那些比较小的地方会更便捷。
焊补则是针对凹类缺陷的修复方式,比如:
气孔、缩坑、切伤、磨伤等。
焊修师傅根据铸件选择同材质的焊条。
利用高超的专业技术将铸件修补平。
和修磨有异曲同工之处。
整形和焊修的目的相同。
就是通过不同方式修复产品不同类型的缺陷,使不合格的产品合格。
它主要是针对形状变形产品的校正。
一般容易变形的都是一些造型简单、壁厚较薄的产品。
至于那些壁厚较厚、而结构又复杂的产品则比较不易变形。
对于一些可预见的变形,一般都会在压蜡工序中采取冷却工装、合理摆放等措施来进行预防以减少变形率、返修率。
虽然车间里有两台校正液压机,但利用率很低,只有一些简单而又规则的产品才用得到。
大部分产品都是人工修整。
利用材质硬度较低的金属棒、工装、量具等用具,用击打的方式来使产品平整、圆顺、垂直等。
以使产品恢复原始形状,达到工艺要求。
保证尺寸精度。
咬酸是为了彻底清除残壳和软化铸件表面的氧化皮,咬酸常用的酸有硝酸和氢氟酸。
酸洗一般都是指洗混合酸,是硝酸和氢氟酸按一定比例配制而成的。
咬酸和酸洗都对时间和温度有一定的要求。
咬酸或酸洗时要注意观察铸件,以防咬酸或酸洗过度。
酸洗后铸件表面呈银白色。
特别要注意的是碳钢不可以酸洗。
电抛光是工件做阳极,铅板做阴极,在硫酸、磷酸,乙甘油等组成的电解液内,通过电解反应使金属表面抛出光泽。
研磨作业则通过流动式光饰机带动磨料研磨工件表面,通过震动式光饰机上光,上光剂有石子,玉米芯等。
4,热处理车间热处理有热处理和爆碱两部分,我着重学习的是热处理工艺的生产过程。
钢在加热和冷却时组织转变的机理;各种热处理的具体工艺过程;钢在加热和冷却过程中产生的缺陷;钢在加热时组织转变的过程中及影响因素;各种热处理的定义、目的、组织转变过程,性能变化,用途和适用的钢种,零件的范围。
通过这三个月的实习,学到了不少专业的知识,但我深深地知道理论上的精通不是真正意义上的对技术的精通,技术最终要应用于生产,就避免不了在实践中遇到各种问题,只有在实践中不断的发现和解决问题。
才能让自己掌握的知识得到真正的成长也只有通过不断的实践中的经验积累才能达到的真正意义上的对技术的精通。
2.2实习内容
1型壳车间:
压蜡:
此工序与产品模具直接接触,与研发课工作联系密切。
整个型壳车间是产品的最初阶段,也是最关键的阶段。
万事开头难,蜡模的质量直接关系到产品表面尺寸和质量的好坏。
操作时注意射蜡湿度、压力、流速、保压时间,以及产生各种缺陷(如:
凹陷、气泡、缩孔、蜡模破裂、油温冷叠、射不满)的原因以及对后序产品的影响。
作为研发人员还要特别注意,不同结构产品模具的设计方法、模具型腔尺寸与蜡模尺寸的差异等。
修蜡:
则主要是将冷却后的蜡模表面合模线、飞边、射蜡口修补过渡圆顺;凹陷填平、气泡挑破补平,油纹擦净等。
一切表面缺陷修补完好。
这道工序要求操作者要集中精力,以防不小心用修蜡刀把蜡件划伤。
组树:
本工序主要与工艺课的关系紧密,它直接反映工艺出品率。
组数时注意树上的蜡模上表面距浇口杯上边缘>90mm,蜡模间距>9mm,蜡模放置角度要利于脱蜡,内浇口长度12~25mm利于切割。
焊接处无凹陷、无缝隙、无尖边、无蜡片粘符。
组树还要注意的一个原则是尽量保证工件在脱蜡时蜡能全部排出。
制壳:
所需要的材料有碱性硅溶胶、锆英粉(用来配制面层涂料)、锆英砂(用于面层撒砂)、煤矸石粉(用于配制背层涂料)、煤矸石砂(是制背层型壳的撒砂)。
制壳的工序比较复杂,所需要注意的地方如:
各种材料的混合比例、温度、湿度、干燥时间的控制等。
型壳质量的好坏直接在铸件表面体现出来,比如铸件表面的毛刺、裂纹、跑火、剥落、回溶、壳裂、鼓胀、夹砂等缺陷,都和浆料的配制、搅拌时间以及浆料的粘度、干燥过程中的温度和湿度有着及大的关系。
脱蜡和蜡处理:
要注意的就是温度、压力、时间、以及脱蜡釜、脱蜡用水分蒸发器、除水桶、静置桶、保温箱操作规程等。
脱蜡过程要迅速,从带蜡模壳推进脱蜡釜至达到0.56Mpa压力时间<14S,才能实现瞬间脱蜡,减小因蜡模膨胀造成的模壳损坏。
压力控制在0.8~0.9Mpa持续9~18分钟,保证脱蜡完全。
通过在型壳车间的见习,我不但对在型壳车间的各工序进行学习并参与实践操作,更重要的是对铸造用的蜡型模具有了初步认识,对蜡和硅溶胶制壳体的性质和特性也有了一定了解。
如产品在设计过程中,有些地方模具无法实现,有些地方制壳无法实现或反映在蜡模上会出现各种缺陷。
这对我以后的工作将会有很大的帮助。
2,浇注车间浇注主要有焙烧、熔炼、浇注、振壳、切割、初抛等工序。
需要注意的是焙烧、熔炼、浇注的温度、时间,还有炉前的经济配料。
以及产生各种缺陷的分类和原因。
铸造过程中熔炼是一个十分重要的环节。
它除了对材质、熔炼温度、熔炼时间以及脱氧剂的添加量有严格的控制以外。
还需要求熔炼师傅们具有专业的技术知识及丰富的工作经验,才能熔炼出合格的钢液。
在浇铸、振壳、切割这些工序中最要注意的是安全。
要严格遵守安全制度,严守纪律,确保安全第一!
浇铸后的铸件经冷却后,方可转入振壳工序。
振壳分机械振壳和人工振壳。
对于一些用横模头组合的铸件树要用人工振壳,人工振壳比较慢、效率低。
但一些用竖模头来组合的铸件树就可以用机振了,省时省力,效率也高。
为了进一步清除铸件表面残留的型壳。
在切割以前要进行悬挂抛丸。
就是在悬挂式抛丸机内用喷射铸铁砂丸的方式将整棵铸件树上的残壳清除掉。
但也不是所有的铸件都要先抛丸再切割,有一些结构简单、内浇口处残留型壳较少的产品,也可以直接进行切割。
切割时不可以切伤铸件本体,但也不可以留有太长的内浇口,大概有1—2mm即可。
通过在浇铸车间的见习,我对浇铸车间的各工序有了更直观的认识。
对壳体的性质有了更深的了解,如壳体高温高强透气性好,低温强度低等性质。
3,后处理车间后处理主要是对产品表面质量和整体形状进行处理。
它的工序最为复杂,包括抛丸、喷砂、咬酸、酸洗、粗磨、精磨、整形、焊修、电抛光、研磨等工序。
它与质检车间毛坯检的联系紧密,产品在它们两者之间不停的流动,直到合格入毛坯库。
在后处理工序中,产品没有固定的工艺流程,通常根据产品结构和现场的工作安排来协调加工流程。
如在清理过程中,抛丸、喷砂、粗磨就没有先后顺序可以根据现场情况协调。
有需要咬酸的清理过程中在咬完酸后进行抛丸再喷砂,根据产品结构和质量要求选择咬酸时机。
对于表面质量要求比较高的产品。
要进行喷砂处理。
喷砂是以压缩空气为动力,通过喷枪将砂料高速喷击铸件表面,以清除残留在铸件外表和内孔中的残砂及氧化皮。
工艺对喷砂使用的砂的种类、粗细以及喷砂压力都有明确要求。
因为压力过大容易造成产品表面损伤。
操作时还要注意不要把铸件正对喷枪口摆放。
以防喷伤铸件。
喷砂后的产品表面比抛丸后的产品表面细腻得多。
粗磨是用砂布带将内浇口磨低,磨至离铸件表面高度小于1mm.然后精磨,根据不同表面质量要求的产品,选用不同粗细的砂布带进行精磨。
精磨时必须精力集中,以防磨伤产品表面从检验车间转到焊修车间的都是表面有缺陷的产品。
一般来说产品的表面缺陷可分为两大类:
凸出类和凹陷类。
凸出类缺陷有:
飞边、毛刺、钢豆或较明显的合模线等。
凹陷类缺陷有:
气孔、缩坑、切伤、磨伤等。
修磨和焊补即是分别针对表面这两大缺陷的修补方式。
修磨主要就是利用气动风枪、绞磨机等修磨工具,装上不同型号和类型的磨头。
把产品表面的凸出类缺陷修平、磨平。
修产品大表面上的凸出类缺陷的时候会选择砂磨头,比较快。
但是有一些孔、沟、槽等砂磨头修不到的地方就会用到钢磨头。
因为钢磨头比较细,修那些比较小的地方会更便捷。
焊补则是针对凹类缺陷的修复方式,比如:
气孔、缩坑、切伤、磨伤等。
焊修师傅根据铸件选择同材质的焊条。
利用高超的专业技术将铸件修补平。
和修磨有异曲同工之处。
整形和焊修的目的相同。
就是通过不同方式修复产品不同类型的缺陷,使不合格的产品合格。
它主要是针对形状变形产品的校正。
一般容易变形的都是一些造型简单、壁厚较薄的产品。
至于那些壁厚较厚、而结构又复杂的产品则比较不易变形。
对于一些可预见的变形,一般都会在压蜡工序中采取冷却工装、合理摆放等措施来进行预防以减少变形率、返修率。
虽然车间里有两台校正液压机,但利用率很低,只有一些简单而又规则的产品才用得到。
大部分产品都是人工修整。
利用材质硬度较低的金属棒、工装、量具等用具,用击打的方式来使产品平整、圆顺、垂直等。
以使产品恢复原始形状,达到工艺要求。
保证尺寸精度。
咬酸是为了彻底清除残壳和软化铸件表面的氧化皮,咬酸常用的酸有硝酸和氢氟酸。
酸洗一般都是指洗混合酸,是硝酸和氢氟酸按一定比例配制而成的。
咬酸和酸洗都对时间和温度有一定的要求。
咬酸或酸洗时要注意观察铸件,以防咬酸或酸洗过度。
酸洗后铸件表面呈银白色。
特别要注意的是碳钢不可以酸洗。
电抛光是工件做阳极,铅板做阴极,在硫酸、磷酸,乙甘油等组成的电解液内,通过电解反应使金属表面抛出光泽。
研磨作业则通过流动式光饰机带动磨料研磨工件表面,通过震动式光饰机上光,上光剂有石子,玉米芯等。
4,热处理车间热处理有热处理和爆碱两部分,我着重学习的是热处理工艺的生产过程。
钢在加热和冷却时组织转变的机理;各种热处理的具体工艺过程;钢在加热和冷却过程中产生的缺陷;钢在加热时组织转变的过程中及影响因素;各种热处理的定义、目的、组织转变过程,性能变化,用途和适用的钢种,零件的范围。
通过这三个月的实习,学到了不少专业的知识,但我深深地知道理论上的精通不是真正意义上的对技术的精通,技术最终要应用于生产,就避免不了在实践中遇到各种问题,只有在实践中不断的发现和解决问题。
才能让自己掌握的知识得到真正的成长也只有通过不断的实践中的经验积累才能达到的真正意义上的对技术的精通。
2.3主要成果
进入车间见习才是我真正意义上开始接触溶模制造。
对我来说一切都是新鲜的,在车间,许多很简单的问题对于我来说,都有可能成为难点,但这不是解决不了的理由,是谁都需要经历的一个过程。
在不断的学习中,不断的摸索中,去培养自己的自主学习能力,思考问题能力。
我首先了解了生产制作流程,然后又逐步了解了熔模铸造工艺及各工序控制要点,以及溶模铸造的基本知识。
制造部主要包括型壳、浇注、后处理、热处理、机加工几大车间。
产品的一般生产流程为:
压蜡→蜡检→修蜡→组树→制壳→浇铸→光谱检→切割、初抛→清理→初检→焊修→中检→热处理→热处理检→加工浇口→整形→中整检→咬酸、抛丸、喷砂→酸洗→酸检→整形、清洗→酸整检→表面处理→表面检→毛坯库→内、外部加工→外抛光→加工检→内、外部热处理→整形装配→装配检→内、外部表面终处理→表面终检→成品库。
每道工序都安排有师傅,在师傅的细心辅导下,我对每道工序应该注意的地方和容易造成的产品缺陷,以及导致这些缺陷的原因等有了一定了解。
1,型壳车间:
压蜡:
此工序与产品模具直接接触,与研发课工作联系密切。
整个型壳车间是产品的最初阶段,也是最关键的阶段。
万事开头难,蜡模的质量直接关系到产品表面尺寸和质量的好坏。
操作时注意射蜡湿度、压力、流速、保压时间,以及产生各种缺陷(如:
凹陷、气泡、缩孔、蜡模破裂、油温冷叠、射不满)的原因以及对后序产品的影响。
作为研发人员还要特别注意,不同结构产品模具的设计方法、模具型腔尺寸与蜡模尺寸的差异等。
修蜡:
则主要是将冷却后的蜡模表面合模线、飞边、射蜡口修补过渡圆顺;凹陷填平、气泡挑破补平,油纹擦净等。
一切表面缺陷修补完好。
这道工序要求操作者要集中精力,以防不小心用修蜡刀把蜡件划伤。
组树:
本工序主要与工艺课的关系紧密,它直接反映工艺出品率。
组数时注意树上的蜡模上表面距浇口杯上边缘>90mm,蜡模间距>9mm,蜡模放置角度要利于脱蜡,内浇口长度12~25mm利于切割。
焊接处无凹陷、无缝隙、无尖边、无蜡片粘符。
组树还要注意的一个原则是尽量保证工件在脱蜡时蜡能全部排出。
制壳:
所需要的材料有碱性硅溶胶、锆英粉(用来配制面层涂料)、锆英砂(用于面层撒砂)、煤矸石粉(用于配制背层涂料)、煤矸石砂(是制背层型壳的撒砂)。
制壳的工序比较复杂,所需要注意的地方如:
各种材料的混合比例、温度、湿度、干燥时间的控制等。
型壳质量的好坏直接在铸件表面体现出来,比如铸件表面的毛刺、裂纹、跑火、剥落、回溶、壳裂、鼓胀、夹砂等缺陷,都和浆料的配制、搅拌时间以及浆料的粘度、干燥过程中的温度和湿度有着及大的关系。
脱蜡和蜡处理:
要注意的就是温度、压力、时间、以及脱蜡釜、脱蜡用水分蒸发器、除水桶、静置桶、保温箱操作规程等。
脱蜡过程要迅速,从带蜡模壳推进脱蜡釜至达到0.5