重催装置操作规程汇总辩析.docx
《重催装置操作规程汇总辩析.docx》由会员分享,可在线阅读,更多相关《重催装置操作规程汇总辩析.docx(133页珍藏版)》请在冰豆网上搜索。
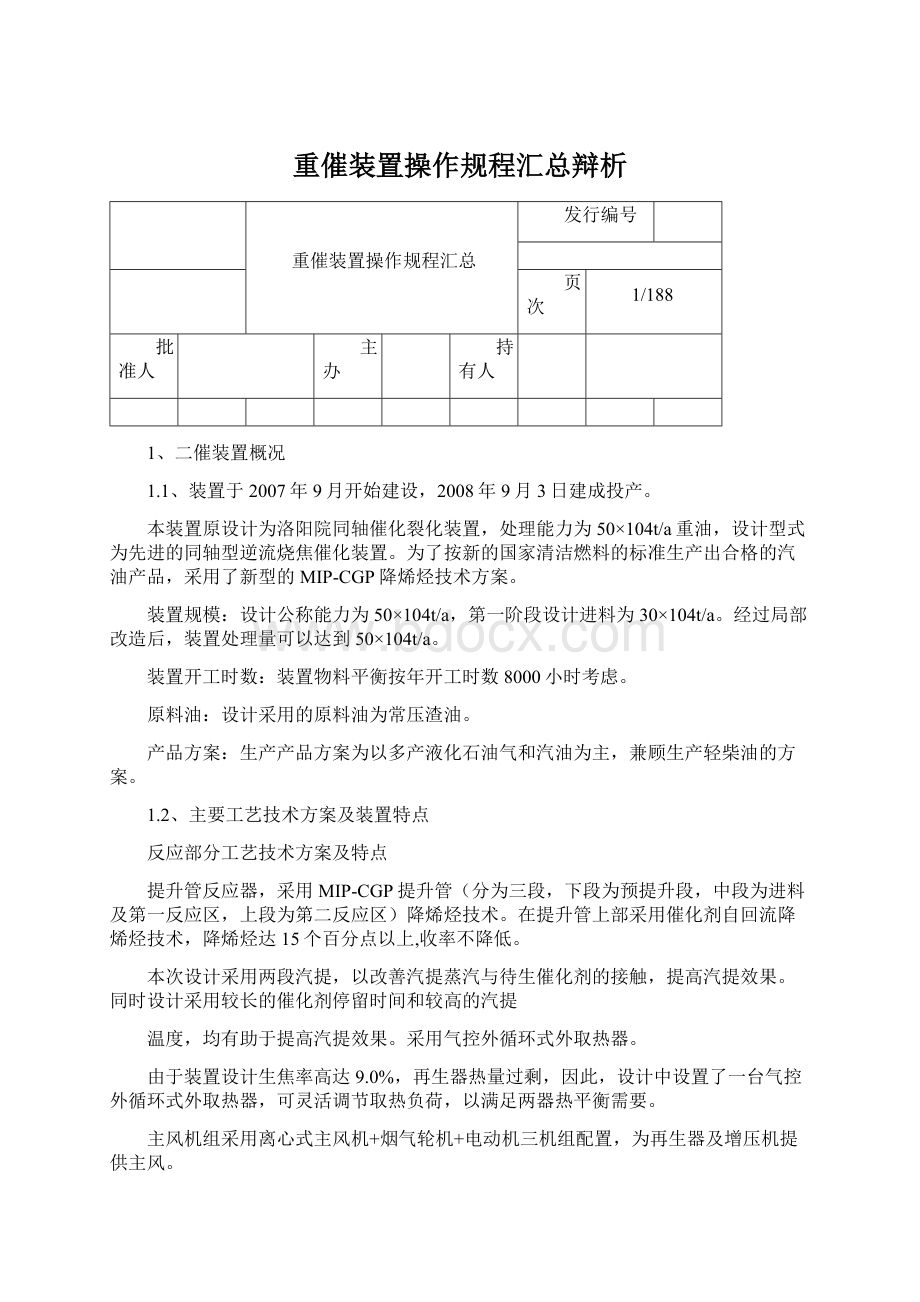
重催装置操作规程汇总辩析
重催装置操作规程汇总
发行编号
页次
1/188
批准人
主办
持有人
1、二催装置概况
1.1、装置于2007年9月开始建设,2008年9月3日建成投产。
本装置原设计为洛阳院同轴催化裂化装置,处理能力为50×104t/a重油,设计型式为先进的同轴型逆流烧焦催化装置。
为了按新的国家清洁燃料的标准生产出合格的汽油产品,采用了新型的MIP-CGP降烯烃技术方案。
装置规模:
设计公称能力为50×104t/a,第一阶段设计进料为30×104t/a。
经过局部改造后,装置处理量可以达到50×104t/a。
装置开工时数:
装置物料平衡按年开工时数8000小时考虑。
原料油:
设计采用的原料油为常压渣油。
产品方案:
生产产品方案为以多产液化石油气和汽油为主,兼顾生产轻柴油的方案。
1.2、主要工艺技术方案及装置特点
反应部分工艺技术方案及特点
提升管反应器,采用MIP-CGP提升管(分为三段,下段为预提升段,中段为进料及第一反应区,上段为第二反应区)降烯烃技术。
在提升管上部采用催化剂自回流降烯烃技术,降烯烃达15个百分点以上,收率不降低。
本次设计采用两段汽提,以改善汽提蒸汽与待生催化剂的接触,提高汽提效果。
同时设计采用较长的催化剂停留时间和较高的汽提
温度,均有助于提高汽提效果。
采用气控外循环式外取热器。
由于装置设计生焦率高达9.0%,再生器热量过剩,因此,设计中设置了一台气控外循环式外取热器,可灵活调节取热负荷,以满足两器热平衡需要。
主风机组采用离心式主风机+烟气轮机+电动机三机组配置,为再生器及增压机提供主风。
备用主风机采用离心式主风机+电机二机组配置,作为本装置的备机。
增压机采用增压机+电机二机组配置,一开一备,该机为外取热器、外取热器返回管及待生套筒供风。
气压机组采用气压机+背压式透平二机组配置。
采用余热锅炉+补燃的灵活方案
1.3装置物料平衡的设计数据如下:
项目
年处理量
(万吨)
日处理量
(吨)
时处理量
(吨)
百分比
(%)
原料
30-50
900-1500
37.5-62.5
100
常压渣油
40
1200
50
80
减压蜡油
10
300
12.5
20
产品
100
干气
1.5-2.5
45-75
1.875-3.125
5
液化气
5.7-9.5
171-285
7.125-11.9
19
汽油
12.6-21
379-631
15.8-26.3
42
柴油
6.3-10.5
189-314
7.9-13.1
21
油浆
1.05-1.75
31.5-52.3
1.32-2.18
3.5
焦炭
2.76-4.6
82.8-138
3.45-5.75
9.2
损失
0.15-0.25
4.5-7.5
0.1875-0.313
0.5
轻油收率
82
1.2装置工艺流程简述
1.2.1公用系统:
1.2.1.1燃料系统:
高压瓦斯出自本装置再吸收塔和稳定塔顶油气分离器,进入高压瓦斯管网,高压瓦斯主管网在装置北端可出装置,再吸收塔顶的瓦斯也可做提升管提升介质和直接放火炬。
辅助燃烧室开工用气液化气站引入。
1.2.1.2水系统:
a新鲜水:
新鲜水用于生活用水、机泵冷却、两机润滑油冷却及气压机中冷、废锅水封罐上水等,其中两机润滑油冷却、气压机中冷均可切换成循环水冷却。
为在开停工时进行水冲洗、水试压、洗塔、顶线,在顶循环泵、粗汽油泵、吸收中段泵、稳汽泵、液化气泵、凝缩油泵入口均接有新鲜水线。
b除氧水
装置除氧水来源于动力厂和甲乙酮凝结水。
动力厂来的除氧水分两路进入装置,一路从装置区东头进入装置,与E—310稳汽换热后进入余锅除氧器,做为余热锅炉、E—211油浆蒸气发生器和外取热的上水。
c循环水
循环水作为全部冷疑冷却器的冷却介质循环于装置与凉水塔之间。
循环水自水场经DN800地下管道进入装置,至各冷凝冷却器,而后返回水场凉水塔。
1.2.1.3、蒸汽系统
a1.0MPa级主蒸汽
主蒸汽管网贯穿于全装置,动力厂来的主蒸汽进入装置,分成两路,一路来自气压机的背压蒸汽(1.0MPa)与装置内油浆蒸气发生器产出的1.0MPa级的蒸汽合并进入主蒸气管网分出一支作为消防用蒸汽;另一路经蒸汽分水器脱水后至装置区,用作V101抽真空蒸汽,反应进料雾化,反应器防焦蒸汽,再生稀相喷汽,反应进料事故蒸汽,各单、双动滑阀、膨胀节、烟道等吹扫蒸汽及各扫线蒸汽,主蒸汽末端做为本装置的消防蒸汽和伴热蒸汽。
b3.8MPa过热蒸汽DD
中压过热蒸汽是由外取热器发汽,经余锅产汽过热后,作为本装置汽轮机用蒸汽,中压蒸汽经汽轮机做功(带动气压机)后生成低压蒸汽,供本装置用汽后多余蒸汽送出装置。
中压蒸汽压力用管网中蒸汽补入主蒸汽的办法来控制。
c低压蒸汽
分馏油浆蒸汽发器产生的1.0MPa级的蒸汽,与汽压机低压蒸汽合并后一起进入低压蒸汽管网出装置。
低压蒸汽管网压力用管网中补入(或送出)主蒸汽的办法来控制。
1.2.1.4、风系统
a净化风
净化风自空压站通过DN100管线进入装置区分成二部分,一路进事故风罐作为双动滑阀动力风,提升风自保、主风自保动力风,另一路经脱水、过滤器除尘,作为反应器、再生器测压反吹风,各仪表调节阀的风源,两机仪表用风,最后经事故风罐作为放火炬闸阀动力风。
b非净化风
非净化风自空压站至装置脱水后有如下去向:
去反应——再生区,作为大中小加料输送风,V—3101、V—3102充压风,再生器三次风,再生、待生斜管卸料输送风,斜管松动风,分布管及锥底卸料输送风以及各卸料口的反吹风。
净化风与非净化风间有一条连通线用于互为补充。
1.2.2、催化剂装卸系统
1.2.2.1、新鲜催化剂(或平衡催化剂)自车上卸下后,用非净化风从催化剂料斗送入事先抽真空的(V—101或V—102)中。
1.2.2.2、加催化剂时V—101(或V—102)充压,罐内催化剂或经大型加料线由输送风送入再生器密相下部,或经中、小型加料线用输送风送入再生器密相下部。
1.2.2.3、V—101、V—102设有催化剂倒罐线,其中某一罐中的催化剂均可倒入另一罐中,过滤催化剂时要用到倒罐线。
1.2.2.4、V—101底部设有小型自动加料系统,催化剂进入再生器密相下部。
放空接到V—101顶部。
1.2.2.5、为防止超压,V—101、V—102顶部均设有安全阀。
1.2.2.6、卸催化剂时,用输送风将再生器分布管上、分布管下,再生器外取热底部的催化剂经各卸料线送入事先抽真空的V102中。
1.2.2.7、V—101、V—102顶部设有放空、撤压管线和抽真空系统。
1.2.2.8、CO助燃剂自助燃剂加料斗用输送风经小型加料送入再生器密相中部。
1.2.3、反应系统
提升管反应进料。
常压渣油进入提升管下部进料集合管,通过四组喷咀,用主蒸汽进行雾化,用以分散成与催化剂料径相近的微粒,与来自再生器的再生催化剂(约700℃)接触,立即汽化并反应,产生的反应油气携带催化剂沿提升管向上流动,在出口处通过粗旋风分离器,使催化剂与油气迅速分离,以减少二次反应,夹带的催化剂油气经两组单级旋风分离器分离,分离出来的油气去分馏塔,回收下来的大部分催化剂经料腿流入汽提段。
其底部通入两段汽提蒸汽,汽提段内设有4层环形挡板和4层锥形挡板,使沉积有焦炭并吸附一定量油气的催化剂与蒸汽逆流接触,除去催化剂中所吸附的油气。
提升管在进料喷咀上部有两组回炼油回炼喷咀。
沉降器的压力由汽轮机即气体压缩机转速来控制,反应温度由再生斜管单动滑阀的开度控制催化剂循环量来调节,沉降器内汽提段催化剂料位由待生立管塞阀的开度控制。
提升管为新型的降烯烃工艺下部设有预提升器的MIP提升管。
1.2.4、再生系统
经汽提后的催化剂沿待生立管、待生塞阀、待生催化剂分配器,使待生催化剂分布于密相床上部,与来自外取热器的再生催化剂混合,并进入再生器密相床层,与经分布管进入的空气逆向充分接触烧去催化剂上的积炭,夹带催化剂的烟气在再生器稀相段经过沉降分离后,烟气进入三组一、二级旋风分离器,进一步分离催化剂,与烟气分离后的催化剂沿料腿落入再生器密相床层。
再生催化剂分两路流出,第一路经再生器底部进入淹流管,再生斜管流入提升管底部的预提升器,然后去提升管反应器,预提升器使催化剂流动处于稳定状态;第二路经循环斜管去外取热器,床层温度由外取热器下部外循环管输送风阀的开度来控制,也可由调节外取热器流化风量的大不上来控制。
再生器顶部压力为0.17MPa,由烟机入口蝶阀或双动滑阀的开度来控制。
1.2.5、外取热系统
掺炼渣油后裂化反应过程中产生的焦炭,燃烧放出的热量除供给反应需要的热量外,尚有多余热量需要取出,为此设置了外取热器。
由再生器密相应层来的高温催化剂(700℃)自流入外取热器后,经取热列管间隙自上而下流动,取热管浸没于流化床内、管内走水,取热器底部通入流化风以维持良好流化,形成流化床催化剂对直立浸没管的良好传热。
经换热后,催化剂通过斜管输送风阀控制循环量返回到再生器相床。
外取热用的除氧水从动力反渗透来经余锅除氧器除氧后由中压水泵直接进入汽包,并与外取热换热出来的汽——水混合物混合、传热,在汽包中进行汽液分离,产生的中压蒸汽到余锅过热并入蒸汽管网,汽包内的饱和水自循环进入外取热器20组取热管,为使进入取热管的水分配均匀,每组均装有集合分配管,汽包设有压力控制及液位控制系统。
1.2.6、原料系统
原料由自油品罐区来进入原料油缓冲罐(V—201),然后经原料泵(P—201/A、B)增压之至换热器E—204A/B分馏顶循环回流、E—205A/B轻柴油、E—210循环油浆回流换热后,去反应提升管进料喷咀。
1.2.7、分馏系统
1.2.7.1、反应器顶出来的油气,经过油气大管进入分馏塔盘圆形挡板下,经8层挡板,洗涤所携带的催化剂和脱除过热状态后,再经过29层浮阀塔盘,被依次分割成相应的馏份。
最后汽油及气体组分从塔顶油气出口出来,经过E—201A—D4台油气空冷器、2台塔顶冷凝冷却器,冷凝冷却后到V—202塔顶油气分离罐进行气液分离,分馏塔顶油气线上设有蝶阀,以备低负荷时调节反应器压力。
分离后的气体经富气线到气压机,水从脱水包由仪表控制油水界面,将水送出装置,分离出来的汽油称之为粗汽油,3路,分成一路去吸收稳定,一路返回分馏塔作塔顶回流,一路去提升管打终止剂。
1.2.7.2、为更好的利用分馏塔顶的热量,在分馏塔上部设有分馏顶循环系统,顶循环油自分馏塔第4层塔板下集油箱抽出,经E—204A、B;E—203A、B被原料油和空气冷却后,与粗汽油合并返回分馏塔顶。
1.2.7.3、催化轻柴油自塔第十一或十三层流入汽提塔,经4层条阀塔盘与由下而上的过热蒸汽接触,轻的油气经塔顶挥发线返回分馏塔10层下,汽提过的轻柴油由P—205A、B抽出,经E—205原料油换热;E—215A、B富吸收油换热;E—206;E—207冷却后大部分去T—303再吸收塔,小部分作为产品出装置。
轻柴油和冲洗油总线设有连通线,汽提塔出入口有连通线,轻柴油可以不经过汽提塔,直接出装置,汽提塔本身设有液面指示及控制系统。
1.2.7.4、分馏一中段回流自分馏十七层塔盘抽出,由P—206A、B送至循环油浆——分馏一中段油换热器(E—208),稳定塔底重沸器(E—309),解吸塔底重沸器(E—306),分馏一中段冷却器(E—209)冷却到190℃返回分馏塔第十四层上以保证柴油质量。
1.2.7.5、回炼油从分馏塔自压流入回炼油罐,经P—207A、B分成二路。
第一路做反应的原料;第二路直接返塔作内回流。
1.2.7.6、分馏塔油浆自塔底由P-—208抽出后,经过循环油浆——分馏一中段油换热器(E—208),循环油浆——原料换热器(E—210),油浆蒸汽发生器(E—211A、B)后返塔做循环回流来脱除分馏塔进料油气的过热状态和洗掉进料油气中所携带的催化剂,这部分油浆进塔口共有两个,一个是返盘圆形挡板上,一个返盘圆形挡板下,通过调节油浆返盘圆形挡板下的流量来控制塔底温度。
油浆冷却水箱将外甩油浆温度降至90℃送到装置外。
1.2.7.7、冷后轻柴油除出装置外送外,一部分返回装置进封油罐V—206做各冲洗点的冲洗油和泵的封油及开工燃烧油用,用封油泵将V—206柴油抽出,一路自身循环,系统压力由回罐量控制,各用冲洗油点从循环系统引出,另一路至泵各密封点,由控制阀控制封油压力。
1.2.8、吸收稳定系统
1.2.8.1粗汽油自P—203A、B来可有2个走向:
正常生产时进T—301吸收塔,不合格或停吸收稳定时直接出装置。
1.2.8.2气压机出口富气经E—301空冷和E—302冷凝冷却后直接进入凝缩油罐。
经V—302凝缩油罐分离后的富气组分自压进入吸收塔下部。
凝缩油罐中的凝缩油经泵P—301A、B进入解吸塔顶。
1.2.8.3吸收塔顶贫气进入T—303再吸收塔下部,经再吸收后自塔顶进入高压瓦斯管网。
1.2.8.4吸收塔设有中段循环回流,即中段油经E—303冷却后返回其下一层塔板。
1.2.8.5吸收塔底油经吸收塔底泵(P—302A、B)升压,进入E302冷却后压入V302气压机出口凝缩油罐。
1.2.8.6T—3302解吸塔顶气体自压进入E—302压缩富气后冷器,而后进入凝缩油罐。
1.2.8.7解吸塔底油进入E—306重沸器壳程被分馏中段油加热后,油气混合物共同返回塔板下,两相分离后气相上升成为解吸塔热源,液相(脱乙烷油)落入塔底经解底泵升压与稳汽换热后进入稳定塔。
脱乙烷油进T—304稳定塔有三个进料口,可根据需要选择使用。
1.2.8.8稳定塔顶油气冷却后进入V—303稳定塔顶回流罐。
罐内未冷凝下来的轻组分自不凝气线进入高压瓦斯管网,或富气管网。
罐内液相组分经P—305液态烃泵分成两路,一路做T—304稳定塔顶回流;一路出装置。
1.2.8.9稳定塔底的油品,落入E—309重沸器壳程,被分馏中段油加热后的气体返回塔板下,做为T—304稳定塔热源,液相即为稳定汽油。
1.2.8.10稳定汽油冷却后一部分经稳汽泵打回T—301吸收塔顶做补充吸收剂;另一部分自压进精制系统,精制后出装置。
1.2.8.11高压瓦斯管网压力超高可排入低压瓦斯放火炬。
1.2.8.12吸收稳定系统故障需撤压时,可由再吸收塔压控前直接排入低压瓦斯放火炬。
2、反应岗位操作法
反应系统是催化裂化装置的核心,是平衡生产的关键,反应系统各操作参数的变化不但会引起其它系统操作参数的变化,而且会波及到有关装置的生产。
而其它系统操作参数的变化也会反过来影响反应的操作。
为此要求,掌握好反应系统的物料平衡、热量平衡和压力平衡,选择适宜的操作条件以获得较高的轻质油收率,实现低能耗的安全平稳生产。
由于反应系统内各参数变化快,互相影响大,要求发现及时、判断准确、处理果断、迅速、准确,操作中要求加强对各参数的检查、分析,以保证装置的正常安全平稳运行。
2.1反应系统正常操作法
2.1.1反应温度(提升管出口温度)
2.1.1.1、影响因素:
a催化剂循环量增加,反应温度上升。
b再生温度上升,反应温度上升。
c总进料增加,反应温度下降。
d进料组成变重,再生温度上升,反应温度上升。
e原料变轻或带水,反应温度下降。
f预提升介质流量增加,催化剂循环量增加,反应温度上升。
g蒸汽带水,反应温度下降。
h启用汽油终止剂,反应温度下降。
i催化剂加料速度快,引起再生温度下降,反应温度下降。
2.1.1.2、调节方法:
a正常生产中,反应温度控制是由给定反应温度来自动控制再
生单动滑阀开度,即调节催化剂循环量来实现的。
再生单动滑阀一旦失灵,应立即改手动控制。
b调节再生温度,见第(七)条。
c调整总进料量,见第(三)条。
d预提升蒸汽一般不用做调节,反应汽油回炼、终止剂不用做正常调节反应温度的手段。
e正常操作时,进料事故蒸汽不启用。
f加料速度适中,避免由其引起各参数波动。
2.1.2反应压力(沉降器顶部压力)
2.1.2.1、影响因素:
a气压机工况变化(如转数、蒸汽压力)反应压力改变,正常
情况下是转数下降,压力上升。
b气压机入口放火炬闸阀开度增加,反应压力下降。
c气压机反飞动量增加或排量减少,反应压力上升。
d原料油组分变轻或带水,反应压力上升。
e提升管反应温度升高,反应深度增加,反应压力上升。
f提升管进料量增大,反应压力上升。
g催化剂受污染选择性变差,产气量增加,反应压力上升。
h原料油预热温度升高,压力上升。
i反应汽提蒸汽量或预提升蒸汽量增大,反应压力上升。
j蒸汽带水或注入量增加,反应压力上升。
k启用事故蒸汽,反应压力变化。
l启用终止剂,反应压力上升。
m分馏塔底液面超高,淹没油汽大管入口,反应压力上升。
n分馏塔塔盘有结盐或异物堵塞现象,反应压力上升。
o分馏塔回流量增大,反应压力上升。
p分顶蝶阀开度变小,反应压力上升。
q分顶冷凝冷却器冷却效果变差,冷后温度上升,反应压力上升。
r分馏塔顶油气分离器液面超高,反应压力上升。
s油浆泵或其它回流泵抽空,反应压力上升。
t低压瓦斯线内存油或水,或放火炬线凝缩油罐满,放火炬时阻力增大,反应压力上升。
u轻柴汽提塔满或溢流,反应压力上升。
v向V202压油量过大或压空,反应压力上升。
w再吸收塔压空,反应压力急剧上升。
2.1.2.2、调节方法:
a正常生产中,反应压力是由汽压机转数或反飞动量来控制。
b在反应压力超高,气压机无调节余地时,可用改变气压机入
口放火炬量来作为反应压力的辅助控制手段。
c反应压力低,汽压机飞动时,可由汽压机岗位适当增大反飞
动量,汽压机停时,反应压力可用分顶蝶阀和放火炬蝶阀调节,在放火炬蝶阀有调节余地时,不得使用分顶蝶阀,正常操作时,分顶蝶阀开度不得低于30%。
d调整汽压机反飞动量。
e改变进料组成,通知有关岗位和车间改善原料油品质。
f选择适当的操作条件,控制反应深度。
g调节总进料量。
见第(三)条。
h置换催化剂。
I调整汽提蒸汽和预提升蒸汽量。
j检查蒸汽品质,及时联系有关岗位和车间改善蒸汽品质。
k分馏压降大时,及时通知分馏和班长,改善操作状态。
沉降器压力超限时,可降低处理量。
l反应压力升高,应观察汽压机入口压力及出口富气量变化情
况,分馏塔压力变化情况,及时判定压力升高的原因,是反应还是分馏引起的?
然后酌情予以迅速处理。
m反应压力突然大幅度升高时,马上用汽压机入口放火炬蝶阀
来撤压,但要注意机入口压力变化情况(特别是当机入口压力及分馏塔顶压力和富气量同时下降时,在汽压机运行时,要防止因汽压机入口压力撤的过快,富气量太小而导致气压机飞动),在生产中应保持放火炬瓦斯线畅通和汽压机入口放火炬阀灵活好用,尤其是在冬季更应特别注意防冻防凝及凝缩油太多堵塞管路。
n反应压力升高而撤压困难时,可降低进料量,切断进料,以
保证设备安全。
o启用终止剂要缓慢,不可过快。
p其他岗位或单位压油时,应注意观察,加强联系,发现问题及时处理。
q吸收稳定要注意稳住再吸收塔液面,必要时甩掉再吸收塔。
2.1.2反应进料
2.1.2.1影响因素
a原料油罐液位低换罐不及时,或机泵抽空,导致反应进料量降低。
b回炼油或油浆回炼控制阀失灵,进料量大幅度变化。
c进料自保,滑阀压降自保或主风自保动作或失灵引起进料波动。
d回炼油泵抽空,进料量大幅度波动。
e开大喷咀预热线,或事故旁通付线手阀,进料量减少。
f原料油轻或带水,及预热温度高进料量大幅度波动。
g油浆回炼控制阀失灵或油浆泵抽空,进料量波动。
2.1.2.2调节方法
a正常操作时,根据生产计划控制进料量,根据反应情况和分馏要求,控制回炼油回炼量和油浆回炼量。
b当仪表指示出现变化时,应同时观察各路进料和总进料情况,判断是否真变化和仪表假信号,若仪表控制失灵,应根据总进料指示改手动或根据就地指示仪表改付线控制。
c当由于机泵抽空影响进料时,应及时开起备用泵,同时赶快联系处理抽空泵。
d当进料量很低,而须维持正常操作时,改用事故旁通付线阀或预热线阀控制反应进料量,同时适当开启事故蒸汽付线帮助流化。
2.1.4汽提蒸汽量
2.1.4.1影响因素:
a过热蒸汽管网压力波动,从而使汽提蒸汽量波动。
b汽提蒸汽流量调节器失灵。
c汽提蒸汽喷嘴堵塞。
2.1.4.2调节方法
a正常情况下,汽提蒸汽量由其流量调节器自动控制。
b过热蒸汽压力低时,应开大其流量控制阀付线阀,以保证有足
够的汽提蒸汽量。
同时联系调度提低压蒸汽压力。
c注意检查分析过热蒸汽压力、温度的变化情况及时与有关车间
和岗位联系。
d若仪表失灵应及时联系处理。
e过热蒸汽压力过低不能维持时,可用主蒸汽代替。
2.1.5催化剂循环量
2.1.5.1影响因素:
a待生塞阀和再生单动滑阀的开度增加,循环量增加。
b提升风量增加,循环量增加。
c总进料量增加,循环量增加。
d预提升介质量增加,循环量增加。
e两器差压改变,循环量变化。
f主风量增加,循环量增加。
g汽提蒸汽量增加,循环量降低。
h斜管松动介质压力或品质变化,循环量变化。
i启用加料或增加料速度大,增加系统藏量,循环量增加。
g提高或降低反应温度,催化剂循环量增加或减小。
k再生温度上升,循环量降低;反之,则增加。
2.1.5.2调节方法
a正常情况下,由反应温度控制再生单动滑阀开度来调节催化剂
的循环量。
b及时调节两器压力,保持两器差压稳定,保证催化剂的正常循
环。
c正常操作中应经常观察并记住各单动滑阀的开度,当循环量出
现大幅度波动时,应首先将塞阀、滑阀改手动或手摇,稳定两阀开度,再寻找导致循环量波动的原因进行处理,调节时应注意滑阀开度控制在滑阀压降允许的范围内。
d经常检查总进料,进料温度,主风量,提升风量,预提升蒸汽
量,汽提蒸汽量,松动介质压力等使之平衡,以保证催化剂循环量不发生大的变化。
e加料速度适中,以不影响平衡为宜。
f调节再生温度平稳参见(七)。
2.1.6汽提段藏量(沉降器)
2.1.6.1影响因素:
a待生塞阀开度增加,藏量减少。
b再生滑阀开度增加,藏量增加。
c两器差压变化时,正差压增加,料位下降,藏量下降。
d汽提蒸汽量增加,密度降低,藏量增加。
e仪表失灵,滑阀失灵引起藏量变化。
2.1.6.2调节方法:
a严禁汽提段藏量压空,正常时用待生塞阀的开度自动调节沉降
器汽提段藏量,但要注意待生塞阀压降不能超限。
b一般情况下,再生滑阀主要用来调节反应温度,不用来调节反
应沉降器和汽提段的藏量,一旦作为调节手段时,要保证反应温度和系统压力的变化在指标范围之内。
c及时调节两器压力,保持两器差压稳定。
d稳定汽提蒸汽量。
e当仪表故障时,立即将滑阀改手动或手摇,保持一定的藏量并
及时联系仪表处理。
2.1.7再生温度
2.1.7.1影响因素
a取热催化剂循环量增加,再生温度下降。
b外取热器内流化风量增加,外取热器内催化剂流化改善,取热量增加,再生温度下降。
c取热器内,循环热水量降低,再生温度上升。
d再生、待生催化剂循环增加,再生温度下降。
e待生催化剂含炭量增加,再生温度上升。
f再生压力上升,再生温度上升。
g喷燃烧油或增大喷