犁刀变速齿轮箱体钻孔攻丝双工位组合机床双侧4m8毕业设计说明书全套cad图纸.docx
《犁刀变速齿轮箱体钻孔攻丝双工位组合机床双侧4m8毕业设计说明书全套cad图纸.docx》由会员分享,可在线阅读,更多相关《犁刀变速齿轮箱体钻孔攻丝双工位组合机床双侧4m8毕业设计说明书全套cad图纸.docx(50页珍藏版)》请在冰豆网上搜索。
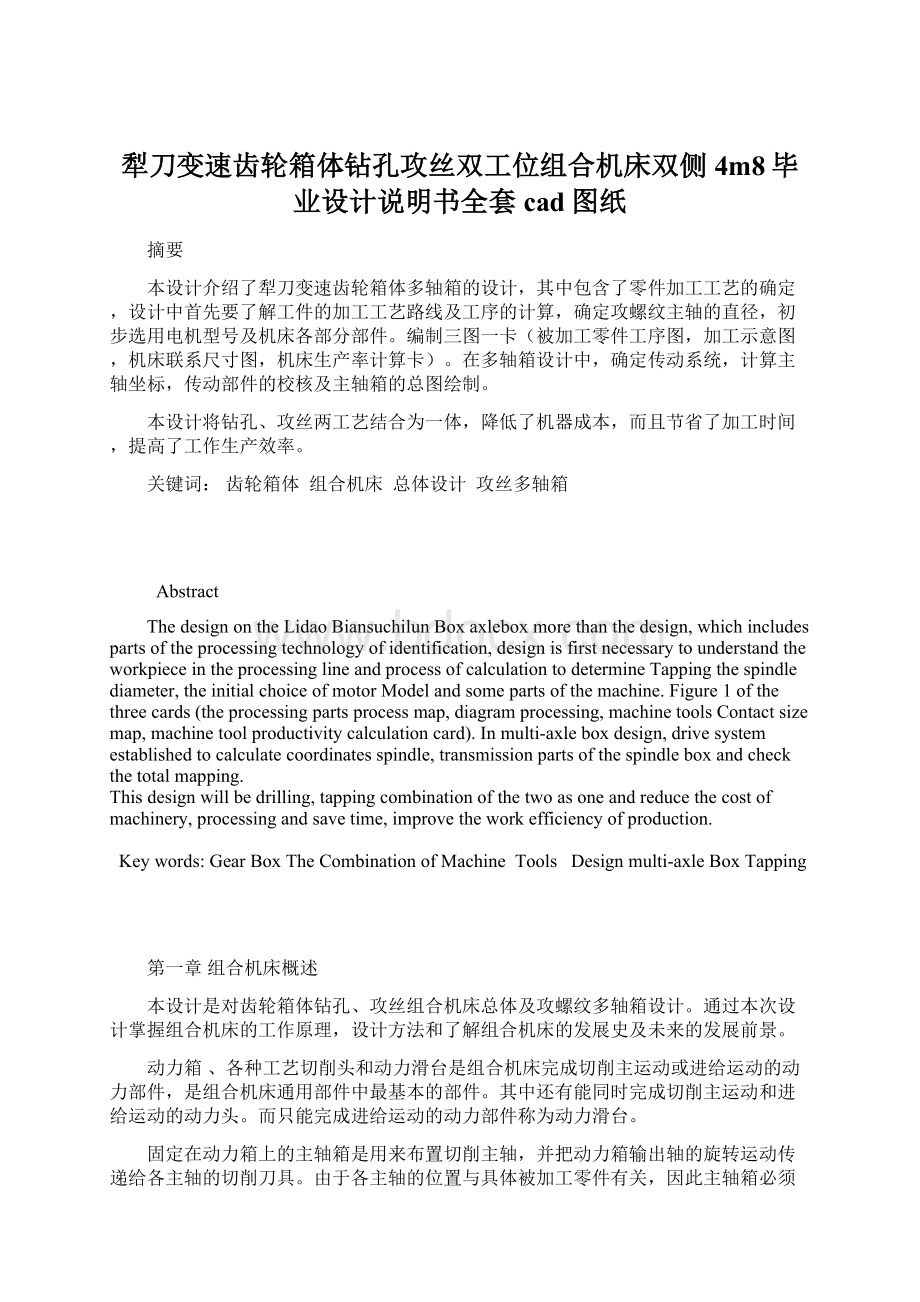
犁刀变速齿轮箱体钻孔攻丝双工位组合机床双侧4m8毕业设计说明书全套cad图纸
摘要
本设计介绍了犁刀变速齿轮箱体多轴箱的设计,其中包含了零件加工工艺的确定,设计中首先要了解工件的加工工艺路线及工序的计算,确定攻螺纹主轴的直径,初步选用电机型号及机床各部分部件。
编制三图一卡(被加工零件工序图,加工示意图,机床联系尺寸图,机床生产率计算卡)。
在多轴箱设计中,确定传动系统,计算主轴坐标,传动部件的校核及主轴箱的总图绘制。
本设计将钻孔、攻丝两工艺结合为一体,降低了机器成本,而且节省了加工时间,提高了工作生产效率。
关键词:
齿轮箱体组合机床总体设计攻丝多轴箱
Abstract
ThedesignontheLidaoBiansuchilunBoxaxleboxmorethanthedesign,whichincludespartsoftheprocessingtechnologyofidentification,designisfirstnecessarytounderstandtheworkpieceintheprocessinglineandprocessofcalculationtodetermineTappingthespindlediameter,theinitialchoiceofmotorModelandsomepartsofthemachine.Figure1ofthethreecards(theprocessingpartsprocessmap,diagramprocessing,machinetoolsContactsizemap,machinetoolproductivitycalculationcard).Inmulti-axleboxdesign,drivesystemestablishedtocalculatecoordinatesspindle,transmissionpartsofthespindleboxandcheckthetotalmapping.
Thisdesignwillbedrilling,tappingcombinationofthetwoasoneandreducethecostofmachinery,processingandsavetime,improvetheworkefficiencyofproduction.
Keywords:
GearBoxTheCombinationofMachineToolsDesignmulti-axleBoxTapping
第一章组合机床概述
本设计是对齿轮箱体钻孔、攻丝组合机床总体及攻螺纹多轴箱设计。
通过本次设计掌握组合机床的工作原理,设计方法和了解组合机床的发展史及未来的发展前景。
动力箱、各种工艺切削头和动力滑台是组合机床完成切削主运动或进给运动的动力部件,是组合机床通用部件中最基本的部件。
其中还有能同时完成切削主运动和进给运动的动力头。
而只能完成进给运动的动力部件称为动力滑台。
固定在动力箱上的主轴箱是用来布置切削主轴,并把动力箱输出轴的旋转运动传递给各主轴的切削刀具。
由于各主轴的位置与具体被加工零件有关,因此主轴箱必须根据被加工零件进行设计。
不能制造成完全通用的部件,但其中很多零件(如主轴、中间轴齿轮和箱体等)是通用的。
组合机床在目前被广泛应用。
组合机床是根据工件加工需要,以大量通用部件为基础,配以少量专用部件组成的一种高效专用机床,它能够对工件进行多刀,多轴,多面,多工位同时加工。
在组合机床上可以完成钻孔,攻丝,铰孔,车削,镗削,磨削及液压等工序。
组合机床结构稳定,工作可靠,使用和维修方便,有可重新改装的优越性。
其通用零部件可以多次重复使用。
它可以同时从几个方向采用多把道具,对几个工件进加工,大大提高了生产率,而且他还具有设计制造周期短,占地面积小等特点。
所以组合机床越来越广泛的被广泛的被应用到各行各业。
组合机床一般采用多轴、多刀、多工序、多面或多工位同时加工的方式,生产效率比通用机床高几倍至几十倍。
由于通用部件已经标准化和系列化,可根据需要灵活配置,能缩短设计和制造周期。
组合机床的通用部件有:
床身(侧底座)、底座(包括中间底座和立柱底座)、立柱、动力箱、动力滑台、各种工艺切削头等。
对于一些按顺序加工的多工位组合机床,还具有移动工作台和回转工作台。
因此,组合机床兼有低成本和高效率的优点,在大批、大量生产中得到广泛应用,并可用以组成自动生产线。
图1-1为各种组合机床配置方案示意图
图1-1各种组合机床配置方案示意图
组合机床一般用于加工箱体类或特殊形状的零件。
加工时,工件一般不旋转,由刀具的旋转运动和刀具与工件的相对进给运动,来实现钻孔、扩孔、锪孔、铰孔、镗孔、铣削平面、切削内外螺纹以及加工外圆和端面等。
有的组合机床采用车削头夹持工件使之旋转,由刀具作进给运动,也可实现某些回转体类零件(如飞轮、汽车后桥半轴等)的外圆和端面加工。
近年来组合机床的主要用户汽车制造厂为了提高产品质量和加强竞争力,对加工设备提出了一些新的要求,如高生产率、缩小加工尺寸的分散度、高可靠性、高利用率和柔性化;此外要求组合机床价格低,交货期短,售后服务好。
这对组合机床行业是一种新的挑战,其中有一些要求相当苛刻的。
在不断革新和采用新技术以及一些有关工业及配套件厂的共同努力下,有不少要求已得到满足,在技术上取得了一些新的进展。
例如,在对组合机床高生产率方面,要求单线(不采用并联线)加工大件(指缸体、缸盖、变速箱体、变速器壳)的生产率达到120-182件/h(100%负荷时),也就是节拍时间为20-30s或更短。
又如,车削活塞变椭圆裙部的数控专门化车床,转速高达5000r/min,生产率可达500件/h。
它采用了新颖的往复运动刀架(直线伺服电动机驱动、采用计算机磁盘驱动和定位原理,以及滚动导轨铝质套筒形密封结构)和高抗振性聚合物人造花岗岩床身等新技术;其加工的外圆公差可达0.0013mm,仅为图纸要求公差的1/2,可以不必再分组的办法进行选择装备,便可做到互换装配,从而减少零件的库存量和分组、保管、配对等手续和管理上的麻烦,更加便于实现“准时制生产”。
对于组合机床来说达到完全互换装配的加工精度尚有些距离,如精镗汽缸孔的精度目前还只能达到0.02mm,如能达到0.012-0.015mm就可以达到完全互换装配了,在高可靠性和利用率方面,部分组合机床自动线可达到三班制常年生产(利用班休间隔进行换刀)。
当前不但有一个国家内各组合机床制造厂之间存在着竞争,同时还在各国著名机床厂之间也出现了竞争。
如美国较著名的组合机床厂Cross公司及其参加的KearneyCross联营公司由于连年亏损,于1991年被GiddingsLcwis公司收购而消失了。
美国是汽车工业发达、需要组合机床及其自动线较多的国家。
近年来,德国、意大利的几个较著名的组合机床制造厂纷纷打入美国市场,1991、1992两年输入美国的组合机床及其自动线价钱金额达2.8亿美元。
由于柔性制造设备和技术的发展和广泛应用,特别是加工箱体件柔性制造单元和柔性制造系统的应用,取代了一部分单一品种生产用的组合机床及其自动线,预计90年代组合机床在机床市场中所占的比例将继续降低。
一份1990年发表的美国机床市场调查及预测报告(表1-1)表明,组合机床在机床市场中所占的份额(金额计算),从80年代中期的平均占15%,将到989年的9.3%,预计90年代前半期还将继续下降到7.7%。
而加工中心所占比例将上升3个百分点(由18%升至21%)。
另一份报告(美国ManufacturingEninineering.1991.102.No1:
18)指出,1990-1997年美国柔性制造系统和柔性制造单元的产值将从7.69亿美元增至17亿美元。
美国组合机床市场会进一步缩小,也是一种必然的趋势。
各国情况不同,但适应市场对产品多样化的要求,利用柔性较大的设备进行多品种生产和易于实现产品的更新换代则是一种必然的趋势,虽然组合机床也在向柔性化发展,但其柔性毕竟不及柔性制造系统,其应用总是受到一定限制,组合机床市场的缩小将会程度不同地出现。
美国组合机床(其包括内容与我国比较接近)的产值在金切机床产值中占的比例较高,大多数年份都在20%以上,表明美国组合机床行业是比较发达的。
从单台(条)的平均价值金额看,美国较高,表明美国组合机床自动线的产量较多。
意、法两国组合机床的产量和产值虽然较少,但其在金切机床年产值中的比例却高于德国和日本,表明这两国重视组合机床的生产。
美国组合机床的常量很少,所占比例较低,未受重视。
表1-1美国金属切削机床市场情况及预测
组合机床的更新情况,可以每隔几年一次机床拥有量普查中有关各类机床役龄的统计及其所占百分比的数据中推算出来。
美国是机床普查工作进行得比较好的国家,其分类及役龄统计都比较完整。
美国1968-1989年进行了5次机床普查。
组合机床(包括自动线)的拥有量、构成比及役龄的百分比表明组合机床的构成比有些变化,但变化不大;70年代后期构成比最大,80年代又逐渐减少,可以认为70年代后期组合机床在美国的应用达到高潮。
从役龄的百分比来分析组合机床的更新情况是,1983年和1989年的0-4年役龄的各占16%和14%,而调查是每五年进行一次,大约每年有3%的新组合机床投入使用,总量变化不大,可以认为其更新率约为3%。
从其他几个役龄上看,5-9年役龄的增加了10%,20年以上役龄的减少了16%,组合机床的役龄是更年轻化了。
这种情况可以认为有比较普遍的意义。
第二章犁刀变速齿轮箱体工艺分析
2.1被加工零件的功用
箱体的功用箱体零件是机械制造中加工工序较多,劳动量较大的,精度要求高的典型零件。
变速箱体是专用机床的关键零件,箱体的质量直接影响到机床的使用功能,箱体内装有许多零件,所以箱体上相应部件作为零件的装配部件的基础,它们之间的相对位置基本上是由箱体来保证的,所以箱体的加工表面的尺寸、形状、位精度都有非常严格的要求。
2.2编制工艺规程及分析
2.2.1被加工零件的技术要求
犁刀变速齿轮箱体材料为HT200。
该材料有较高的强度、耐磨性、耐热性及减振性,适用承受教大应力、要求耐磨的零件。
该零件主要加工表面为N面、R面、Q面和2-Φ80H7孔。
N面的平面度为0.05mm,直接影响旋耕机与拖拉机变速箱的接触精度及密封。
2-Φ80H孔的同轴度Φ0.04mm,与N面的平行度0.07mm,与R面及Q面的垂直度φ0.1mm以及R面相对Q面的平行度0.005mm,直接影响犁刀传动对N面的平行度及犁刀传动齿轮的啮合精度、左臂壳及右臂壳体孔轴线的同轴度。
因此,再加工他们时,最好能在一次装夹下将两孔或两面同时加工出来。
2-Φ10F9孔的两孔距尺寸精度(14
0.05)mm以及(14
0.05)mm对R面及N面的平行度0.06mm,影响旋耕机与变速箱连接时的正确定位,从而影响犁刀与变速箱倒挡齿轮的啮合精度。
2.2.2计算生产纲领
犁刀变速齿轮箱体,该产品年生产量为50000件,设其备品率为16%,机械加工废品率为2%,现制定该零件的机加工工艺规程技术要求:
(1)铸件消除内应力。
(2)未注明铸造圆角为R2~R3。
(3)铸件表面不得有粘砂、多肉、裂纹等缺陷。
(4)允许有非聚集的孔眼存在,其直径不大于5mm,深度不大于3mm,相距不小于30mm,整个铸件孔眼不多于10个。
(5)未注明倒角为0.5×45°。
(6)所有螺孔锪90锥孔至螺纹外径。
(7)去毛刺,锐边倒角。
(8)同一加工平面上允许有直径不大3mm,深度不大于15mm,总数不超过5个孔眼,两孔之间不小于3mm。
(9)涂漆按NJ226-31执行。
计算犁刀变速齿轮箱体年产量N:
N=Qn(1+a%+b%)=50000×1×1+16%+2%)(2-1)
=59000件/年
该零件的质量为7kg。
根据生产类型与生产纲领的关系。
查表3-3
生产类型可确定为大量生产。
2.2.3毛坯的选用
根据零件材料HT200确定毛坯为铸件,又已知零件生产纲领为59000件/年,该零件约为7kg,可知,其生产类型为大批量生产。
毛坯的制造方法选用砂型机器造型。
又由于箱替零件的内腔及2-Φ80mm的孔须铸出。
故还应安放型芯。
此外,为消除残余应力,铸造后安排人工时效。
(1)铸件尺寸公差分为16级,由于是大量生产,毛坯制造方法采用砂型机器造型。
由工艺人员手册查得,铸件尺寸公差等级为CT10级,选取铸件箱值为1.0mm。
(2)铸件机械加工余量
对成批大量的铸件加工余量由工艺人员手册
查得,选取MA为G级,各表的总余量见表2-1。
由工艺人员手册可查得铸件主要尺寸公差见表2-2。
表2-1各加工表面总余量/mm
加工表面
基本尺寸
加工余量等级
加工余量数值
说明
R面
Q面
N面
凸台面
孔2-φ80
168
168
168
106
80
G
H
G
G
H
4
5
5
4
3
底面,双侧加工(取下行数据)
顶面降一级,双侧加工
侧面,单侧加工(取上行数据)
侧面单侧加工
孔降一级,双侧加工
表2-2主要毛坯尺寸及公差/mm
主要面尺寸
零件尺寸
总余量
毛坯尺寸
公差CT
N面轮廓尺寸
N面轮廓尺寸
N面距孔Φ80中心尺寸
凸台面距孔Φ80中心尺寸
孔2-Φ80
168
168
46
100+6
Φ80
—
4+5
5
4
3+3
168
177
51
110
Φ70
4
4
2.8
3.6
3.2
2.3零件加工工艺路线的拟定
2.3.1工件定位
工件在夹具中定位的主要任务是:
使同一工序中的一批工件都能在夹具中占据正确的位置。
工件位置的正确与否,用加工要求来衡量。
能满足加工要求的为正确,反之不正确。
一批工件逐个在夹具上定位时,各个工件在夹具中占据的位置不可能完全一致,也不必要求其完全一致,但各个工件的位置变动量必须控制在加工要求所允许的范围内。
工件定位定则(六点定则):
在空间直角坐标系中,工件可以沿X、Y、Z轴有不同的位置,称工件沿XYZ轴的位置自由度,用
、
、
表示;也可以绕X、Y、Z轴有不动的位置,称工件绕X、Y、Z轴的角度自由度,用
、
、
表示。
用于描述工件不确定性的
,称为工件的六个自由度。
用于限制工件自由度的固定点,称为定位支承点,简称支承点。
用合理分布的六个支承点限制工件六个自由度的法则,称为六点法则。
对六个自由度的限制可分为以下几类定位:
(1)工件在夹具中定位,若六个自由度都被限制时,称为完全定位。
(2)工件在夹具中定位,若六个自由度没有被全部限制时,称为部分定位(不完全定位)。
在工件定位时,以下情况允许不完全定位:
①加工通孔或通槽时,沿贯通的位置自由度可不限制。
②毛坯(本工序加工前)是轴对称时,绕对称轴的角度自由度可不限制。
③加工贯通的平面时,除可不限制沿两个贯通的位置自由度外,还可不限制绕垂直加工表面的角度自由度
(3)工件在夹具中定位时,若实际定位支撑点或实际限制的自由度个数少于工序加工要求应予限制的自由度个数,则工件定位不足,称为欠定位。
(4)工件在夹具中定位,若几个支撑点重复限制同一个或几个自由度时,称为重复定位。
2.3.2定位基准的选择
(1)精基准的选择。
犁刀变速齿轮箱体的N面和2-Φ10F9孔既是装配基准,又是设计基准,用它们作为精基准,能使加工遵循“基准重合”原则,实现箱体零件“一孔二面”的典型定位方式;其余各面和孔的加工也能用它定位,这样工艺路线遵循了“基准统一”的原则。
此外,N面的面积较大,定位比较稳定、加紧方案也比较简单、可靠,操作方便。
(2)粗基准的选择。
考虑到以下几点要求,选择箱体零件的重要孔(2-Φ80mm孔)的与箱体内壁作为粗基准
①保证各加工表面均有加工余量的情况下,使重要孔的加工余量尽量均匀;
②装入箱内的旋转零件(如齿轮、轴套等)与箱体内壁有足够的间隙;
③能保证定位夹紧可靠。
2.3.3工序的集中和分散
(1)集中工序的特点:
①减少设备的数量,减少了操作工人和生产面积。
②减少工序的数目,减少运输工作量,简化了生产计划工序缩短了生产
周期。
③减少装夹次数不仅有利于提高生产率,而且由于在一次装夹加工许多表面,也易于保证这些表面间的位置精度。
④因为采用的专用设备和专用工艺装备数量多而复杂,因此机床的工艺
装备的调整维修也很费事,生产准备工作量很大。
(2)分散的特点:
①采用比较简单的机床和工艺装备,调整容易。
②对工人的技术要求低或只经过较短时间的训练。
③生产准备工作量小,易于变换产品。
④设备数量多,生产面积大。
综上所述攻箱体螺纹可采用集中攻螺纹,即箱体上大量螺纹工序集中在一台机床上加工,并与钻床工序分开。
这样便于考虑统一的润滑、简化多轴箱传动
2.3.4加工工序的设计
确定工序尺寸的一般方法是,由于加工表面的最后工序往前推算,最后工序的尺寸只与工序的加工余量有关。
有基准转换时,工序尺寸用工艺尺寸链解算。
2.3.5热处理的安排
变速箱体是形状复杂的铸件,必须消除内应力,防止加工和装配以后产生变形,必须合理安排时效处理工序,采用自然或人工时效处理。
2.3.6初步拟定工艺规程
工艺规程:
把工艺过程的操作方法按一定的格式用文件的形式规定下来。
通过对箱体的工艺分析和箱体的技术要求来制定箱体的加工路线,由于箱体的年产量为59000台/年,为大批量生产,尽量选用专用机床加工,提高生产率。
拟订的加工工艺:
序号
工序内容
简要说明
铸造
时效
消除内应力
涂底漆
防止生锈
10
粗铣N面
先加工基准面
20
钻扩铰2-Φ10F9至2-Φ9F7,孔口倒角1×45°。
钻孔4-Φ13
留精铰余量
30
粗铣R面及Q面
先加工面
40
铣凸台面
50
精镗孔2-Φ80,孔口倒角1×45°
后加工孔粗加工结束
60
精铣N面
精加工开始
70
精铰孔2-Φ10F9至2-Φ10F7(工艺要求)
提高工艺精准度
80
精铣R面及Q面
先加工面
90
精铰孔2-Φ80H7
后加工孔
100
钻Φ20。
扩铰球形孔SΦ30H9,钻4-M16螺纹底孔,孔口倒角1×45°,攻螺纹4-M6-6H
次要加工面在后面加工
110
锪平面4-φ22
120
钻8-M12螺纹底孔,空口倒角1×45°,钻铰孔2-Φ8N8,孔口倒角1×45°
130
攻螺纹8-M12-6H
工序分散平衡节拍
140
检验
150
入库
2.4攻丝切削用量的选择
查《机械加工工艺手册》
选取所需刀具,选用M12细柄机用丝锥。
攻螺纹切削转矩:
T-切削转矩(Nmm)
D-主轴直径(mm)
-工件螺距(mm)
由已知得螺纹直径D=12mm,取
=1.75mm
则
=14600Nmm
切削功率P=
(2-2)
T─切削转矩(N·mm)
V─切削速度(m/min)
由螺纹直径和螺距查《机械制造工艺设计手册》表3-63得切削速度V=8.88m/min
转速
。
查《机床设计手册》表6-19知:
高速钢丝锥攻螺纹切削速度为4~8m/min(加工材料为铸铁),即转速较大,取实际转速n=200r/min,则实际切削速度v=n
d/1000=7.54m/min
P=
×1000=0.3KW
第三章钻孔、攻丝组合机床的结构设计
3.1组合机床的配置形式的选择
本设计是对犁刀齿轮箱体钻孔、攻丝的组合机床设计。
根据犁刀齿轮箱体结构和大批量生产采用双面加工的组合机床和液压自动加紧结构以便提高生产效率。
图3-1机床总体布置图
其总体布置如图3-1所示。
3.2动力部件的选择
动力部件的选择主要是确定动力箱和动力滑台。
已经确定为卧式双面齿轮传动组合机床,选用配套的动力箱驱动多轴箱攻螺纹主轴。
动力箱规格要与滑台匹配,其驱动功率主要依据多轴箱所传递的切削功率来选用。
P
=
(3-1)
P
─消耗主轴的切削功率总和
η─多轴箱的传动功率
机床共有四根主轴加工工件,故P
=P×4
=0.3×4=1.2kw
传动功率η加工黑色金属时取0.8~0.9,加工有色金属时取0.7~0.8;主轴传动复杂时取小值,反之取大值。
故本设计取η=0.8。
P
=
=1.5kw
据《组合机床简明手册》
表5-39选用动力箱:
1TD32-IV电动机型号Y100L-6,电动机功率1.5kw电动机转速n=940r/min,输出转速n=470r/min,L
=320mm。
3.3通用部件选择
选择通用部件,主要是确定动力部件的驱动方式和规格(即大小),其他如床身、立柱、挡铁等部件根据动力部件的规格,按通用部件配套表选用
3.3.1主轴箱的轮廓尺寸的确定
标准通用钻、镗类多轴箱的厚度是一定的、卧式为325mm,立式为340mm。
因此,确定多轴箱尺寸的宽度B和高度H及最低主轴高度h1。
如图3-2所示:
图3-2多轴箱尺寸确定
被加工零件轮廓以点画线表示,多轴箱尺寸用实线表示,多轴箱宽度B、高度H的大小主要与被加工零件孔的分布有关,多轴箱轮的宽度B和高度H通常按下式确定:
B=b1+b+b2(3-2)
H=h+h1+h2(3-3)
b1=100mm,b2=100mm,b=156.3mm
h1=124.5mm,h2=160mm,h=131.1mm
B=100+156.3+100=256.3mm
H=124.5+160+131.1=415.6mm
b—工件在宽度方向相距最远的两孔距离
b1、b2—最边缘主轴中心至箱体外壁距离
h—工件在高度方向相距最远的两孔距离
h1—最低主轴高度
h2—最低孔高度
B和h为已知尺寸。
为保证多轴箱内有足够安排齿轮的空间,推荐
>70-100mm。
多轴箱最低主轴高度
必须考虑与工件最低孔位置
、机床装料高度H、滑台总高度
、侧底座高度
等尺寸之间的关系而确定。
实例中
==24.4mm,H=1000mm,查表5-3知滑台高度
=280mm,侧底座高度
=560mm。
实例
、B、H的计算如下:
=
+H-(0.5+
+
)=[24.4+1000-(0.5+280+560+5)]mm=138.9mm
取
=100mm,则可求出多轴箱的轮廓尺寸:
H=h+
+
=131.1+138.9+100=370mm
B=b+2
=156.3+2×100=365.3mm
上述计算值,按通用箱体系列尺寸标准,最后确定多轴箱轮廓尺寸为B
H=500×500mm。
3.3.2液压滑台选择
液压滑台的结构特点是:
①采用双矩型导轨结构型式,以单导轨两侧面导向,导向的长宽比较大,导向性好。
②滑座体为箱形框架纳构,滑座底面中间增加了结合面,结构刚度高。
③导轨淬火,硬度高