脱硝系统运行规程试用汇总.docx
《脱硝系统运行规程试用汇总.docx》由会员分享,可在线阅读,更多相关《脱硝系统运行规程试用汇总.docx(26页珍藏版)》请在冰豆网上搜索。
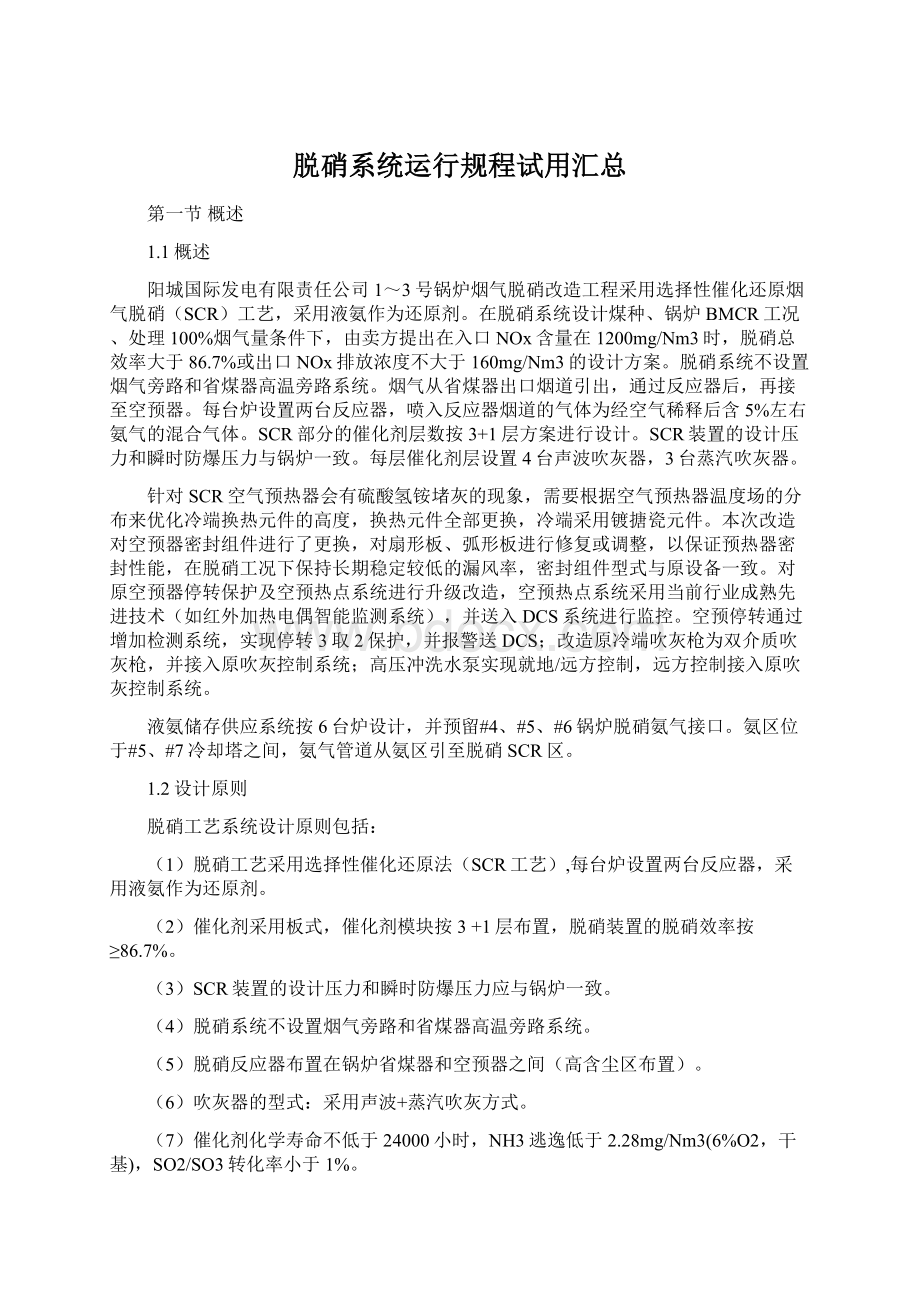
脱硝系统运行规程试用汇总
第一节概述
1.1概述
阳城国际发电有限责任公司1~3号锅炉烟气脱硝改造工程采用选择性催化还原烟气脱硝(SCR)工艺,采用液氨作为还原剂。
在脱硝系统设计煤种、锅炉BMCR工况、处理100%烟气量条件下,由卖方提出在入口NOx含量在1200mg/Nm3时,脱硝总效率大于86.7%或出口NOx排放浓度不大于160mg/Nm3的设计方案。
脱硝系统不设置烟气旁路和省煤器高温旁路系统。
烟气从省煤器出口烟道引出,通过反应器后,再接至空预器。
每台炉设置两台反应器,喷入反应器烟道的气体为经空气稀释后含5%左右氨气的混合气体。
SCR部分的催化剂层数按3+1层方案进行设计。
SCR装置的设计压力和瞬时防爆压力与锅炉一致。
每层催化剂层设置4台声波吹灰器,3台蒸汽吹灰器。
针对SCR空气预热器会有硫酸氢铵堵灰的现象,需要根据空气预热器温度场的分布来优化冷端换热元件的高度,换热元件全部更换,冷端采用镀搪瓷元件。
本次改造对空预器密封组件进行了更换,对扇形板、弧形板进行修复或调整,以保证预热器密封性能,在脱硝工况下保持长期稳定较低的漏风率,密封组件型式与原设备一致。
对原空预器停转保护及空预热点系统进行升级改造,空预热点系统采用当前行业成熟先进技术(如红外加热电偶智能监测系统),并送入DCS系统进行监控。
空预停转通过增加检测系统,实现停转3取2保护,并报警送DCS;改造原冷端吹灰枪为双介质吹灰枪,并接入原吹灰控制系统;高压冲洗水泵实现就地/远方控制,远方控制接入原吹灰控制系统。
液氨储存供应系统按6台炉设计,并预留#4、#5、#6锅炉脱硝氨气接口。
氨区位于#5、#7冷却塔之间,氨气管道从氨区引至脱硝SCR区。
1.2设计原则
脱硝工艺系统设计原则包括:
(1)脱硝工艺采用选择性催化还原法(SCR工艺),每台炉设置两台反应器,采用液氨作为还原剂。
(2)催化剂采用板式,催化剂模块按3+1层布置,脱硝装置的脱硝效率按≥86.7%。
(3)SCR装置的设计压力和瞬时防爆压力应与锅炉一致。
(4)脱硝系统不设置烟气旁路和省煤器高温旁路系统。
(5)脱硝反应器布置在锅炉省煤器和空预器之间(高含尘区布置)。
(6)吹灰器的型式:
采用声波+蒸汽吹灰方式。
(7)催化剂化学寿命不低于24000小时,NH3逃逸低于2.28mg/Nm3(6%O2,干基),SO2/SO3转化率小于1%。
(8)脱硝设备年利用小时按5500小时考虑,投运时间按8000小时考虑。
(9)脱硝装置可用率不小于99%。
1.3设计条件
1.烟气条件
本脱硝改造工程按下表中烟气参数设计:
项目
内容
单位
数据
备注
ECO出口烟风参数
机组负荷
MW
350
额定负荷
O2
%
1.45
湿基
CO2
%
16.49
湿基
湿度
%
6.38
湿基
N2
%
75.68
湿基
湿烟气量
Nm3/h
1010698
湿基
烟气温度
℃
400
最高423℃
静压
Pa
-535
污染物浓度
基准NOx排放浓度
mg/Nm3
1200
SO2@6%O2,干基
mg/Nm3
7278
煤中硫含量2.8%
SO3@6%O2,干基
mg/Nm3
73
炉内SO2/SO3转化率约0.8%
飞灰浓度
g/Nm3
45
考虑煤质的变化留裕量
锅炉最大连续负荷(BMCR)工况下空预器入口主要设计技术参数:
工况
单位
BMCR(设计煤种)
进口烟气量
Nm3/h
1097329
进口一次风量
kg/s
60.35
进口二次风量
kg/s
347
进口烟温
℃
392
进口一次风温
℃
11.7
进口二次风温
℃
11.7
2.液氨品质参数
指标名称
单位
合格品
备注
氨含量
%
≥99.6
残留物含量
%
≤0.4
重量法
密度
kg/L
0.66
25℃时
1.4性能保证值
序号
项目
单位
数据
1
脱硝设备年运行小时数
h
5500
2
装置可用率
%
99
3
NOx脱除率,性能验收期间
%
86.7
4
脱硝系统入口烟气量(实际氧,湿基)
Nm3/h
1010698
5
脱硝系统入口NOx浓度(6%O2,标态,干基)
mg/Nm3
1200
6
出口NOx浓度(6%O2,标态,干基,75%脱硝效率)
mg/Nm3
159.6
7
氨逃逸率
μL/L
≤3
8
SO2/SO3转化率
%
<1
9
脱硝装置压降(加装附加催化剂前)
Pa
600
10
脱硝装置压降(加装附加催化剂后)
Pa
800
11
消耗品
11.1
-液氨
kg/h
485
11.2
-工业水(间断)
m3/h
1
11.3
-合计耗电
kW
107
11.4
-仪用压缩空气
Nm3/h
21
11.5
-杂用压缩空气
Nm3/h
110
11.6
-蒸汽(蒸汽吹灰)
t/h
1.2
1.5工艺系统及主要设备
1.脱硝反应器
本工程设计烟气灰浓度为40mg/Nm3,烟气灰浓度比较低,结合场地条件,反应器截面尺寸设计为11.2m×8.3m,催化剂模块采用4x11布置,模块尺寸按1882×954×1420mm设计,可满足各厂家板式或蜂窝催化剂的尺寸要求。
本工程每台锅炉配置2台脱硝反应器,每台脱硝反应器设计成3+1层催化剂布置方式,其中上层为预留层。
反应器入口采用三角结构型式设计,并在顶层催化剂层上方设置气流整流装置。
反应器主要由催化剂支撑梁、反应器壳体、密封板等组成。
反应器设计压力为±5800Pa(同锅炉设计压力),设计温度400℃,材质采用Q345。
2.催化剂
根据烟气灰浓度,本工程催化剂选用采用板式催化剂。
催化剂技术数据如下:
序号
技术参数
单位
数据
1
机组描述
1.1
机组容量
MW
350
1.2
锅炉数量
台
3
1.3
每台锅炉反应器数量
台
2
2
烟气参数(BMCR)
2.1
烟气量(wet,actualO2)
Nm3/hr
1010698
2.2
CO2
Vol%
16.49
2.3
O2
Vol%
1.45
2.4
N2
Vol%
75.68
2.5
H2O
Vol%
6.38
2.6
烟尘浓度
g/Nm3
≤45
2.10
NOxInlet(以NO2计,干基,6%O2)
mg/Nm3
≤1200
2.8
Cl(干基,6%O2)
mg/Nm3
-
2.9
F(干基,6%O2)
mg/Nm3
-
2.10
SO2(干基,6%O2)
mg/Nm3
7278
2.11
SO3(干基,6%O2)
mg/Nm3
73
3
设计要求
3.1
脱硝效率
初始效率(性能测试时,初装4400小时内)
%
≥86.7
24000小时内
%
≥86.7
3.2
NOxOutlet
初始效率(性能测试时,初装4400小时内)
mg/Nm3
<160
24000小时内
mg/Nm3
<160
3.3
NH3逃逸率
mg/Nm3/ppmvd
<2.28/3
3.4
SO2/SO3转化率
%
<1
3.5
催化剂化学寿命(从首次通烟气开始)
H
24000
3.6
催化剂机械寿命(从首次通烟气开始)
年
10
4
催化剂参数
4.1
制造商
大唐南京环保科技有限责任公司
4.2
型式
板式
4.3
型号
4.4
基材
不锈钢网
4.5
活性化学成份
TiO2、V2O5,MoO3
4.6
催化剂单元孔数
-
4.7
节距(pitch)
Mm
7
4.8
孔径
Mm
7.1
4.9
壁厚
外壁厚t1
Mm
0.8
内壁厚t2
Mm
4.10
催化剂空隙率
%
87
4.11
催化剂比表面积
m2/m3
291.8
4.12
前端硬化长度
mm
20
4.13
催化剂单元尺寸(长×宽×高)
mm×mm×mm
464×464×600
4.14
初始催化剂体积
(单个反应器/单机组)
m3/m3
266.5/532.8
4.15
3台锅炉催化剂体积总用量
m3
1598.4
5
催化剂模块参数
5.1
每个模块包含单元数量
个
16
5.2
每一单元尺寸
mm×mm×mm
464×464×600
5.3
每个模块的尺寸(长×宽×高)
mm×mm×mm
1882×954×1420
5.4
每个模块的重量
Kg
~1110
5.5
模块外壳材料
碳钢
6
反应器参数
6.1
每台锅炉反应器数量
2
6.2
催化剂层数
层
3(初装)+1(预留)
6.3
催化剂模块布置方式
块
4x11*
6.4
每层催化剂模块数量(单台反应器)
块
44
6.5
每个反应器模块数量
块
132
6.6
每台锅炉催化剂模块数量
块
396
7
设计保证值
7.1
初始脱硝效率
%
≥86.7
7.2
24000h(3年)后脱硝效率
%
≥86.7
7.3
NOxOutlet
mg/Nm3
<160
7.4
NH3逃逸率
ppmvdc
<3
7.5
SO2/SO3转化率
%
<1
7.6
每层催化剂的压降
Pa
156.7
7.7
催化剂总压降
Pa
470
7.8
催化剂化学使用寿命
小时
24000
7.9
催化剂机械寿命
年
10
7.10
烟气线速度
催化剂入口处
m/s
5.0
催化剂通道内
m/s
5.7
7.14
烟气空间速度SV
1/hour
1897
7.15
面积速度AV
Nm/hour
6.5
7.16
测试块
类型
平板催化剂每片单板均可作测试块
数量(每层/单反应器/机组)
8
设计温度参数
8.1
设计使用温度
℃
400
8.2
允许使用温度范围(min/max)
℃/℃
333/420
8.3
允许最高使用温度(连续运行5小时)
℃
450
8.4
运行温度变化速率
℃/min
<=20℃/min,温度低于150℃时;
<=50℃/min,温度高于150℃时
9
SCR入口分布条件
9.1
速度分布偏差
%
C.V.≤±15%
9.2
温度分布偏差
℃
±5℃
9.3
NH3/NOx摩尔比分布偏差
%
C.V.≤±5%
9.4
烟气入射催化剂模块角度(与垂直方向的夹角)
±10°
9.5
飞灰分布偏差:
%
<20%
3.烟气系统
烟道设计压力为±5800Pa(同锅炉设计压力),设计温度400℃,材质采用Q345,烟道壁厚6mm。
烟道内烟气流速按15.0m/s设计。
SCR入口烟道截面尺寸为2300×11000mm,SCR出口烟道截面尺寸为2300×11000mm。
在外削角急转弯头、变截面收缩急转弯头处,设置导流板,导流板材质为Q345。
烟道补偿器:
在反应器入口、反应器出口及SCR出口分别设置补偿器,吸收轴向和径向位移,补偿器采用非金属补偿器。
4.稀释风机
利用稀释风机供应的空气将气氨稀释成氨体积含量小于5%的混合气体,经由氨喷射装置进入烟道参与脱硝反应。
稀释风机出力按稀释氨气到5%浓度所需空气量设计,并留有10%的余量。
压头根据稀释风系统阻力选取,并留有20%的余量。
稀释风机选用离心风机,每台炉设置3台稀释风机,两用一备。
流量6546Nm3/h,全压7000Pa。
具体参数如下:
序号
项目
单位
参数
备注
1
风机型号
9-26№5.4A离心式
2
数量
台
3
每台机组二运一备
3
流量
Nm3/h
6546
4
全压升
Pa
7000
5
轴功率
KW
18
6
电机型号
Y180M-2
7
电机功率
KW
22
8
电机转速
r/min
2900
9
防护等级
IP55
10
电机转动方向
从电机向风机方向看
5.氨/空气混合器
氨/空气混合器采用隔板式,在混合器内部设置有5片隔板,可确保氨气和空气混合均匀。
氨/空气混合器的尺寸根据氨气和空气的流量确定,本工程氨/空气混合器选用直径DN500,长度2000mm。
6.氨喷射格栅(AIG)
氨喷射格栅确保氨空混合气均匀喷入烟气的关键装置,采用分区结构型式,由喷射管组成,每根喷射管设置有6个喷嘴,每2根喷射管组成1个区域,每个区域的喷射流量可通过安装在分配管上的手动调节阀控制。
氨喷射格栅布置在垂直烟道上,每台炉设置2套。
氨喷射格栅的关键参数是混合距离(AIG到顶层催化剂的距离,L)和喷嘴间距(6个喷嘴组成区域的当量直径,D),要确保L/D大于20。
在氨喷射格栅设置一排混合管,混合管间距同喷嘴间距。
混合管可促进氨气和烟气混合均匀。
7.吹灰系统
吹灰系统采用声波+蒸汽吹灰模式。
每层催化剂层设置4台声波吹灰器,每台反应器共设置12台声波吹灰器,每台炉设置24台声波吹灰器。
每台声波吹灰器每10分钟吹灰10秒,每小时吹灰12次。
每台声波吹灰器用压缩空气2.28Nm3/min(连续喷吹),每层2台声波吹灰器同时吹,瞬时最大耗气量为4.56Nm3/min,单台炉平均耗气量为1.22Nm3/min(含预留层)。
为了稳定压力,每台炉设置杂用压缩空气储罐1台,储罐容积2m3。
每层催化剂层设置3台蒸汽吹灰器,每台反应器共设置9台蒸汽吹灰器,每台炉设置18台蒸汽吹灰器。
单台炉蒸汽吹灰瞬时最大消耗量为7t/h,平均消耗量为1.2t/h。
声波吹灰器设备参数如下:
序号
项目名称
数据
1
吹灰器本体
1.1
吹灰器型式
声波吹灰器
1.2
吹灰器型号
DC-75
1.3
声波频率
75HZ
1.4
声波强度
147dB(距离喇叭口1米处测)
1.5
每层催化剂吹灰器数
4
1.6
吹灰器数(每个机组/三个机组)
24/72
1.7
一台声波吹灰器的吹灰范围(设计值)
横向3-4.5米,轴向≤12m(超过该范围,请与GE或其分销商北京光耀环境工程有限公司核准)
1.8
喇叭材质
A、B段为铸铁,C段为不锈钢,发生头为碳钢。
1.9
膜片材质
钛金属
1.10
声波吹灰器到催化剂表面的距离,mm
610
1.11
声波吹灰器入口压缩空气压力,bar
4.83~6.21
1.12
单台工作时间,s
10s
1.13
有效吹扫时间,s
10s
1.14
间隔时间,s
590
1.15
每次吹扫运行台数
两台
1.16
空气耗量,L/s(单个吹灰器)
19-38
1.17
瞬时最大空气耗量,Nm3/s
0.076(2台同时发生的瞬间流量)
1.18
平均耗气量,Nm3/h(单台炉)
72.96(三层)
109.44(四层)
2
管路系统
2.1
阀门
普通气路承压阀门(设计压力不小于1.0MPa)
2.2
管道
普通气路承压管道
(设计压力不小于1.0MPa)
3
电控系统
脱硝DCS
杂用空气罐参数如下:
序号
项目
单位
技术参数
备注
1
型式
圆筒立式
2
设备台数
台
3
3
设备直径
mm
1200
4
设计年限
年
30
5
腐蚀余量
mm
2.0
6
桶体壁厚
mm
8
7
封头壁厚
mm
8
8
设计压力
MPa
1
9
工作压力
MPa
0.7
10
设计温度
℃
50
11
工作温度
℃
环境温度
12
筒体高度
mm
1400
13
储存介质
空气
14
介质密度
Kg/m3
15
设计容积
m3
2
16
设备荷重
kg
680
17
总高度
mm
2525
18
设备本体材质
Q345R
19
保温厚度
mm
80
蒸汽吹灰器设备参数如下:
序号
项目名称
数据
1
吹灰器本体
蒸汽吹灰器
1.1
吹灰器型式
半伸缩耙式
1.2
吹灰器型号
HXP-5
1.3
每层催化剂吹灰器数
3
1.4
靶子数(单台吹灰器)
3
1.5
靶子宽度
3480mm
1.6
吹灰母管管径及材质
¢108X5,材质20#
1.7
靶子行程长度,m
2.7
1.8
喷嘴数/每耙
27
1.9
喷嘴
1.9.1
尺寸,mm
φ5
1.9.2
喷嘴材质
1Cr18Ni9Ti
1.9.3
喷嘴型式
文丘里
1.9.4
喷嘴供货厂家
湖北华信
1.9.5
单个喷嘴覆盖面积,m2
0.015166
1.10
吹灰器到催化剂表面的距离,mm
500
1.11
喷嘴出口蒸汽压力,barg
~5
1.12
催化剂表面蒸汽压力,barg
4.5~4.7
1.13
行进速度,m/min
0.9
1.14
转速,rpm
不旋转
1.15
单台工作时间,s
375
1.16
有效吹扫时间,s
355
1.17
有效吹扫范围,m2
垂直向下1.5M
1.18
蒸汽耗量,Kg/s(单个喷嘴)
0.013
1.19
蒸汽耗量,Kg/s(单台吹灰器)
1.054
1.20
吹灰方式
单台逐个吹扫
2
电机型号
Y90L-4
3
电机生产厂家
广东江晟
4
电机轴功率
5
电机功率
1.5KW,380V
6
管路系统
见管道清单
7
空气清扫系统
空气阀进气负压
第二节稀释风机
2.1稀释风机启动前的检查和准备
1.检查稀释风机及其系统检修工作结束,临时安全措施拆除,现场清洁无杂物,有关工作票已终结。
2.检查稀释风机、轴承座、电机地脚螺栓紧固无松动,联轴器防护罩完整牢固。
3.检查各轴承油位在1/2~2/3之间,油质清澈,无乳化、渗漏。
4.检查稀释风机入口滤网清洁无杂物,完整无缺损。
5.检查稀释风机电机电源接线牢固、无松动,外壳接地线良好,无断线、松脱现象。
6.检查稀释风机入口挡板操作灵活无卡涩,就地与画面开度显示一致。
7.检查稀释风机系统各种测量仪表、控制系统投入正常且显示正确。
8.检查气氨与空气混合器完整无损,气氨喷射格栅手动蝶阀开度在预定位。
9.检查仪用压缩空气压力在0.5~0.8MPa之间。
2.2稀释风机的启动(以A稀释风机为例)
1.稀释风机应在启动风烟系统之前投入运行。
2.脱硝稀释风机允许启动条件:
A稀释风机(20HSG11AN001)无故障信号。
3.当A稀释风机启动条件满足后,在稀释风机画面上点出A稀释风机(20HSG11AN001)电机操作块,点击启动按钮,启动稀释风机(20HSG11AN001)。
4.开启A稀释风机(20HSG11AN001)出口挡板(20HSG11AA002)。
5.开启稀释风机入口挡板(20HSG11AA101),检查稀释风压>6KPa,稀释风流量>4000Nm3/h(6400~6900Nm3/h)。
2.3稀释风机的正常运行维护
1.正常情况下,A、C稀释风机运行,B稀释风机备用良好。
2.检查运行稀释风机出口挡板全开,运行声音平稳且无异音;各地脚螺丝牢固无松动;联轴器防护罩完整牢固;电机外壳接地线连接牢固,无松脱、断线现象。
3.检查稀释风机各轴承油位在1/2~2/3之间,油质清澈,无乳化、渗漏现象。
4.检查稀释风机入口滤网清洁无杂物,完整无破损。
5.检查运行稀释风机电流稳定,在33~36A之间。
6.正常运行时,稀释风压大于6KPa,稀释流量>4000Nm3/h(6400~6900Nm3/h),确保气氨稀释后的浓度<5%。
7.检查备用稀释风机出口逆止门关闭,风机无倒转现象。
2.4稀释风机停运(以A稀释风机为例)
1.当脱硝系统气氨停止喷射后,待风烟系统停运后,可将稀释风机停运。
2.锅炉运行期间,停止气氨喷射时,无异常情况应继续保持稀释风机运行。
3.停运时,应先停止气氨喷射,继续吹扫5min。
解除B稀释风机联锁子回路,关闭A稀释风机入口挡板(20HSG11AA101),点出A稀释风机(20HSG11AN001)电机操作块,点击停止按钮,停运A稀释风机(20HSG11AN001)。
4.当稀释风机停运后,关闭A稀释风机出口挡板(20HSG11AA002)。
2.5稀释风机的联锁保护
1.A稀释风机(20HSG11AN001)自动停:
(OR)
1)稀释风机A故障;或
2)稀释空气流量低低(21HSG10CF101、22HSG10CF101)<3600m3/h(AND)稀释风机B已运行。
2.B稀释风机(20HSG12AN001)自动停:
(OR)
1)稀释风机B故障;或
2)稀释空气流量低低(21HSG10CF101、22HSG10CF101)<3600m3/h(AND)稀释风机A\C已运行。
3.C稀释风机(20HSG13AN001)自动停:
(OR)
1)稀释风机C故障;或
2)稀释空气流量低低(21HSG10CF101、22HSG10CF101)<3600m3/h(AND)稀释风机B已运行。
第三节SCR脱硝吹灰系统
3.1SCR脱硝吹灰系统投运前的检查
1.检查吹灰系统的检修工作结束,临时安全措施已拆除,现场清洁无杂物,工作票已终结。
2.各吹灰器外壳护罩完整,枪管完好无变形、无破损,跑道清洁无积灰,驱动齿轮与传动齿啮合紧密,阀门开启机构连接牢固可靠。
3.各电动门、气动门及减压阀试验正常,安全阀已校验合格,吹灰管路各阀门位置正确。
4.检查各吹灰器驱动电机完好,电缆完好无破损。
5.检查系统各测量管线、仪表一次门开启,显示正确。
6.检查控制盘电源正常,各仪表、指示灯投入且指示正确。
7.检查吹灰画面系统各参数显示正常,与就地相符,无异常报警。
8.吹灰器各项保护正常并投入,各热工报警和机械定值经校验合格。
9.就地检查各手动门已开启,电动门已送电、气动门仪用压缩空气投入,压力0.5~0.8MPa,声波吹灰杂用压缩空气罐压力为0.62~0.8MPa。
3.2吹灰系统的运行原则
1.脱硝吹灰系统有蒸汽吹灰枪和声波吹灰器两种设备,采用以上设备吹灰时顺序都应按烟气流动的方向进行,即先吹上层再吹下层。
2.正常情况下,声波吹灰器采用连续吹灰方式,蒸汽吹灰枪根据积灰等情况投入运行。