基于数字PID的电阻炉温度控制系统设计课程设计任务书 精品.docx
《基于数字PID的电阻炉温度控制系统设计课程设计任务书 精品.docx》由会员分享,可在线阅读,更多相关《基于数字PID的电阻炉温度控制系统设计课程设计任务书 精品.docx(29页珍藏版)》请在冰豆网上搜索。
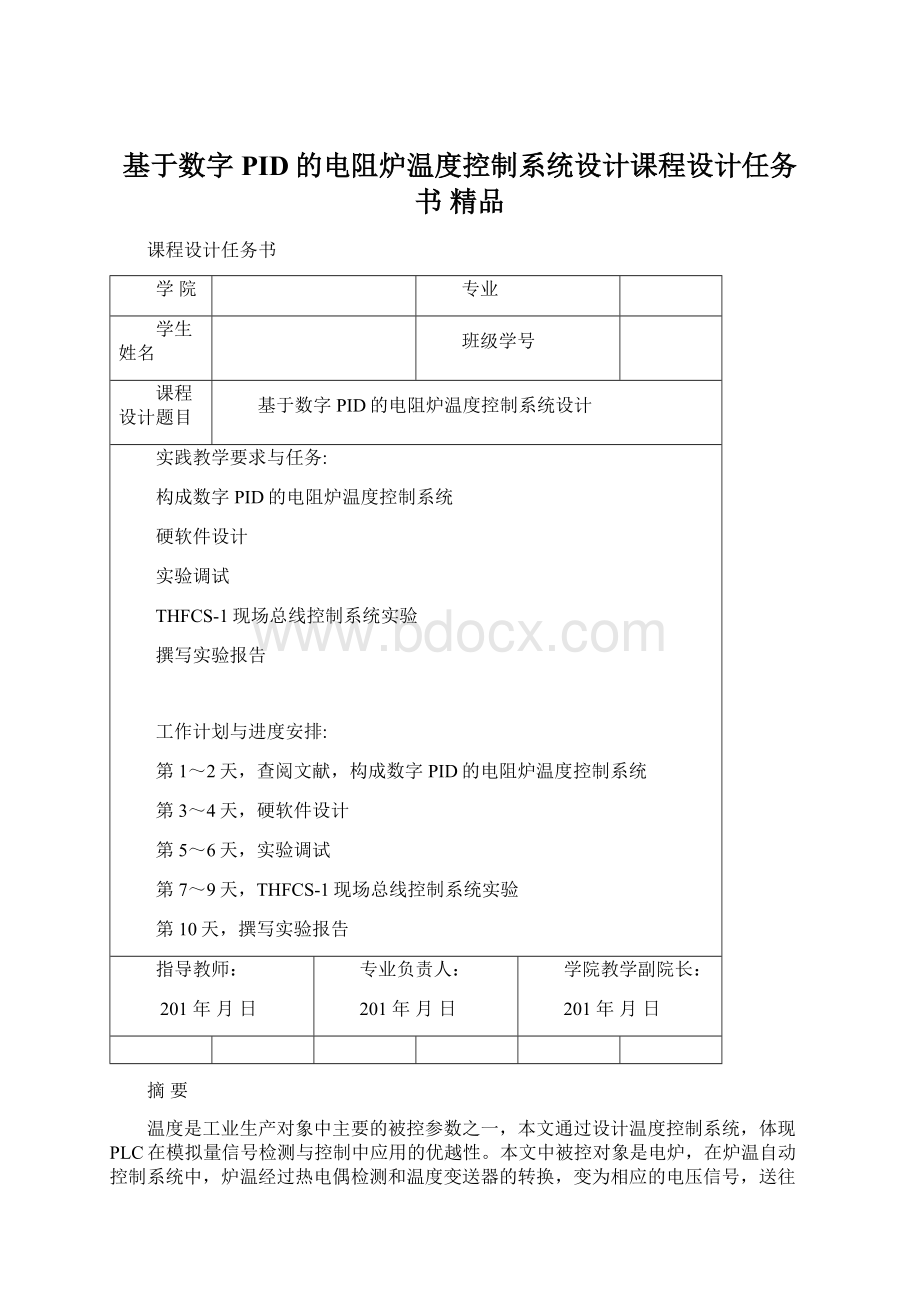
基于数字PID的电阻炉温度控制系统设计课程设计任务书精品
课程设计任务书
学院
专业
学生姓名
班级学号
课程设计题目
基于数字PID的电阻炉温度控制系统设计
实践教学要求与任务:
构成数字PID的电阻炉温度控制系统
硬软件设计
实验调试
THFCS-1现场总线控制系统实验
撰写实验报告
工作计划与进度安排:
第1~2天,查阅文献,构成数字PID的电阻炉温度控制系统
第3~4天,硬软件设计
第5~6天,实验调试
第7~9天,THFCS-1现场总线控制系统实验
第10天,撰写实验报告
指导教师:
201年月日
专业负责人:
201年月日
学院教学副院长:
201年月日
摘要
温度是工业生产对象中主要的被控参数之一,本文通过设计温度控制系统,体现PLC在模拟量信号检测与控制中应用的优越性。
本文中被控对象是电炉,在炉温自动控制系统中,炉温经过热电偶检测和温度变送器的转换,变为相应的电压信号,送往PLC控制器,再经过模拟量输入/输出模块(A/D)转换为数字量,并由程序将给定的温度值与测量值比较,然后根据偏差大小按比例调节规律,计算出校正量。
通过模拟量输入/输出模块的输出控制作用,消除炉温的偏差,从而使炉温达到并稳定在给定的数值
关键字PLC;温度控制;比例调节
Abstract
Temperatureisoneofthemainobjectofindustrialproductioncontrolledparameters,thispaperdesigntemperaturecontrolsystem,andreflectthesuperiorityofthePLCanalogsignaldetectionandcontrolapplications.Controlledobjectinthisarticleistheelectricfurnace,thefurnacetemperatureautomaticcontrolsystem,thefurnacetemperatureafterthermocoupledetectionandtemperaturetransmittersconvertintoacorrespondingvoltagesignalsenttothePLCcontroller,andthenaftertheanaloginput/outputthemodule(a/D)conversiontodigital,byprogramagiventemperaturevalueandthemeasuredvalue,andthenaccordingtothedeviationsizeproportionallyregulatingrule,thecalculatedcorrectionamount.Theoutputoftheanaloginput/outputmodulescontrolroleinremovingthefurnacetemperaturedeviation,sothatthefurnacetemperaturereachedandstabilizedatagivenvalue
KeywordPLC;temperaturecontrol;ratioadjustment
1绪论
1.1课题背景及研究目的和意义
电阻炉的应用领域相当广泛,电阻炉的性能优劣决定了产品的质量好坏。
目前电阻炉的控制系统大都采用以微处理器为核心的计算机控制技术,既提高设备的自动化程度又提高设备的控制精度。
PLC的快速发展发生在上世纪80年代至90年代中期。
在这时期,PLC在处理模拟量能力、数字运算能力、人机接口能力和网络能力得到了很大的提高和发展。
PLC逐渐进入过程控制领域,在某些应用上取代了在过程控制领域处于统治地位的DCS系统。
PLC具有通用性强、使用方便、适应面广、可靠性高、抗干扰能力强、编程简单等特点。
电阻炉是机电一体化的产品,可将电能直接转化成热能,具有效率高,体积小,无污染,运行安全可靠,供热稳定,自动化程度高的优点,是理想的节能环保的供暖设备。
加上目前人们的环保意识的提高,电阻炉越来越受人们的重视,在工业生产中应用越来越普及。
电阻炉在机械工业中用于金属锻压前加热、金属热处理加热、钎焊、粉末冶金烧结、玻璃陶瓷焙烧和退火、低熔点金属熔化、砂型和油漆膜层的干燥等PID控制是迄今为止最通用的控制方法之一。
因为其可靠性高、算法简单、鲁棒性好,所以被广泛应用于过程控制中,尤其适用于可建立精确数学模型的确定性系统。
PID控制的效果完全取决于其四个参数,即采样周期ts、比例系数Kp、积分系数Ki、微分系数Kd。
因而,PID参数的整定与优化一直是自动控制领域研究的重要课题。
PID在工业过程控制中的应用已有近百年的历史,在此期间虽然有许多控制算法问世,但由于PID算法以它自身的特点,再加上人们在长期使用中积累了丰富经验,使之在工业控制中得到广泛应用。
在PID算法中,针对P、I、D三个参数的整定和优化的问题成为关键问题。
1.2国内外研究现状
自70年代以来,由于工业过程控制的需要,特别是微电子技术和计算机技术的迅猛发展以及自动控制理论和设计方法发展的推动下,国内外温度控制系统的发展迅速,并在智能化,自适应、参数整定等方面取得成果,在这方面,以日本、美国、德国、瑞典等国技术领先,都生产出了一批商品化的、性能优异的温度控制器及仪器仪表,并在各行各业广泛应用。
随温度控制系统在国内各行各业的应用虽然应用很广泛,但从国内生产的温度控制器来讲,总体发展水平仍然不高,同日本、美国、德国等先进国家相比仍然有着较大的差距。
目前,我国在这方面总体水平处于20世纪80年代中后期的水平,成熟产品主要以“点位”控制及常规的PID控制器为主,它只能适用于一般的温度系统的控制,难以控制滞后、复杂、时变温度系统控制。
能适应于较高的控制场合的智能化、自适应控制仪表,国内还不十分成熟。
随着科学技术的不断发展,人们对温度控制系统的要求越来越高,因此,高精度、智能化、人性化的温度控制系统是国内外必然发展的趋势。
1.3项目研究内容
以炉为被控对象,以炉温为主被控参数,以加热炉电阻丝电压为控制参数,以PLC为控制器,构成温度控制系统;采用PID算法,运用PLC梯形图编程语言进行编程,实现温度的自动控制。
可编程逻辑控制器(PLC)是集计算机技术、自动控制技术和通信技术为一体的新型自动控制装置。
其性能优越,已被广泛的应用于工业控制的各个领域,并已经成为工业自动化的三大支柱(PLC、工业机器人、CAD/CAM)之一。
PLC技术在温度监控系统上的应用从整体上分析和研究了控制系统的硬件配置、电路图的设计、程序设计,控制对象数学模型的建立、控制算法的选择和参数的整定等。
论文通过对德国西门子公司的S7-200系列PLC控制器,温度传感器将检测到的实际炉温转化为电压信号,经过模拟量输入模块转换成数字信号送到PLC中进行PID调节,PID控制器输出转化为0-10mA的电流信号输入控制可控硅电压调整器或触发板改变可控硅管导通角的大小来调节输出功率。
2可编程控制器(PLC)概况
2.1可编程控制器的概述
可编程序控制器(ProgrammableController)通常也可简称为可编程控制器,英文缩写为PC或PLC,是以微处理器为基础,综合了计算机技术、自动控制技术和通信技术发展起来的一种通用的工业自动控制装置。
它具有体积小、功能强、程序设计简单、灵活通用、维护方便的一系列的优点,特别是它的高可靠性和较强的适应恶劣工作环境的能力,更是得到了用户的好评,因而在冶金、能源、化工、交通、电力等领域中的到了越来越广泛的应用,成为了现代工业控制的三大支柱(PLC、机器人、CAD/CAM)
2.2PLC的基本组成及各部分作用
PLC是一种通用的工业控制装置,其组成与一般的微机系统基本相同。
按结构形式的不同,PLC可分为整体式和组合式两类。
整体式PLC是将中央处理单元(CPU)、存储器、输入单元、输出单元、电源、通信接口等组装成一体,构成主机。
另外还有独立的1/0扩展单元与主机配合使用。
主机中,CPU是PLC的核心,1/0单元是连接CPU与现场设备之间的接口电路,通信接口用于PLC与编程器和上位机等外部设备的连接。
组合式PLC将CPU单元、输入单元、输出单元、智能1/0单元、通信单元等分别做成相应的电路板或模块,各模块插在底板上,模块之间通过底板上的总线相互联系。
装有CPU单元的底板称为CPU底板,其它称为扩展底板。
CPU底板与扩展底板之间通过电缆连接,距离一般不超过10m.无论哪种结构类型的PLC,都可以根据需要进行配置与组合。
2.2.1中央处理单元(CPU)
CPU在PLC中的作用类似于人体的神经中枢,它是PLC的运算、控制中心。
它按照系统程序所赋予的功能,完成以下任务:
接收并存储从编程器输入的用户程序和数据;
诊断电源、PLC内部电路的工作状态和编程的语法错误;
用扫描的方式接收输入信号,送入PLC的数据寄存器保存起来;
PLC进入运行状态后,根据存放的先后顺序逐条读取用户程序,进行解释和执行,完成用户程序中规定的各种操作;
将用户程序的执行结果送至输出端。
2.2.2存储器
根据存储器在系统中的作用,可以把它们分为以下3种:
系统程序存储器:
和各种计算机一样,PLC也有其固定的监控程序、解释程序,它们决定了PLC的功能,称为系统程序,系统程序存储器就是用来存放这部分程序的。
系统程序是不能由用户更改的,故所使用的存储器为只读存储器ROM或EPROM.
用户程序存储器:
用户根据控制功能要求而编制的应用程序称为用户程序,用户程序存放在用户程序存储器中。
由于用户程序需要经常改动、调试,故用户程序存储器多为可随时读写的RAM。
由于RAM掉电会丢失数据,因此使用RAM作用户程序存储器的PLC,都有后备电池(铿电池)保护RAM,以免电源掉电时,丢失用户程序。
当用户程序调试修改完毕,不希望被随意改动时,可将用户程序写入EPROM.目前较先进的PLC(如欧姆龙公司的CPMIA型PLC)采用快闪存储器作用户程序存储器,快闪存储器可随时读写,掉电时数据不会丢失,不需用后备电池保护。
工作数据存储器:
工作数据是经常变化、经常存取的一些数据。
这部分数据存储在RAM中,以适应随机存取的要求。
在PLC的工作数据存储区,开辟有元件映象寄存器和数据表。
元件映象寄存器用来存储PLC的开关量输入/输出和定时器、计数器、辅助继电器等内部继电器的ON/OFF状态。
数据表用来存放各种数据,它的标准格式是每一个数据占一个字。
它存储用户程序执行时的某些可变参数值,如定时器和计数器的当前值和设定值。
它还用来存放A/0转换得到的数字和数学运算的结果等。
根据需要,部分数据在停电时用后备电池维持其当前值,在停电时可保持数据的存储器区域称为数据保持区。
2.2.3I/0单元
I/0单元也称为I/0模块。
PLC通过I/0单元与工业生产过程现场相联系。
输入单元接收用户设备的各种控制信号,如限位开关、操作按钮、选择开关、行程开关以及其他一些传感器的信号。
通过接口电路将这些信号转换成中央处理器能够识别和处理的信号,并存到输入映像寄存器。
运行时CPU从输入映像寄存器读取输入信息并进行处理,将处理结果放到输出映像寄存器。
输出映像寄存器由输出点对应的触发器组成,输出接口电路将其由弱电控制信号转换成现场需要的强电信号输出,以驱动电磁阀、接触器、指示灯被控设备的执行元件.
2.2.4电源部分
PLC一般使用220V的交流电源,内部的开关电源为PLC的中央处理器、存储器等电路提供5V,+12V,+24V的直流电源,使PLC能正常工作。
电源部件的位置形式可有多种,对于整体式结构的CPU,通常电源封装到机壳内部;对于模块式PLC,有的采用单独电源模块,有的将电源与CPU封装到一个模块中。
2.2.5扩展接口
扩展接口用于将扩展单元以及功能模块与基本单元相连,使PLC的配置更加灵活以满足不同控制系统的需要。
2.2.6通信接口
为了实现“人一机”或“机一机”之间的对话,PLC配有多种通信接口。
PLC通过这些通信接口可以与监视器、打印机和其他的PLC或计算机相连。
当PLC与打印机相连时,可将过程信息、系统参数等输出打印;当与监视器相连时.可将过程图像显示出来;当与其他PLC相连时,可以组成多机系统或连成网路,实现更大规模的控制;当与计算机相连时,可以组成多级控制系统,实现控制与管理相结合的综合性控制。
3模块方案的选择与论证
3.1总体方案的选择
方案一:
此方案采用传统的模拟控制方法,选用模拟电路,用电位器设定给定值,反馈的温度值与给定的温度值比较后,决定加热或不加热。
本方案的特点是电路简单,易容易实现,但系统所得结果的精度不高并且调节动作频繁,系统静差大,不稳定。
系统受环境的影响大,不能实现复杂的控制算法,而且不易实现对系统的控制及对温度的显示,人机交换性能差。
方案二:
采用PLC来作为整机的控制单元,系统的工作中,经过温度检测及变换电路把被测对象的温度转换成电压信号,该电压信号经过D/A转换器转换为数字信号后送入PLC中,与给定的对应所要控制的多组温度值进行比较,找出现温度值所在范围,根据PLC中设置的参数,转化为占空比,控制功率转换器件,带动被控对象,并且把被控对象的温度经过变换电路和D/A转换器反馈到PLC中,与输出的初值进行比较,其偏差被PID程序计算出后重新输出,在规定的时间内循环。
对于欠温度,控制加速功率。
对于过温度,控制吹风冷却装置。
方案三:
采用AP89S52来作为整机的控制单元。
他是一个功耗,高性能CMOS8位微控制器,经过信号采集,数据转换,数据处理来控制温度。
此方案比方案一简单,比方案二复杂。
比较以上三种方案的优缺点,方案二简单、灵活、可扩展性好,具有电路设计简单、精确度高、控制效果好等优点,能达到题目设计要求,因此采用方案二实现本设计.
图1.1PLC的组成框图
本系统的基本工作原理:
假定实际炉温等于给定炉温,这时
,反馈值与给定值相同,电炉处于规定的恒温状态。
如果增加工件,电炉负荷加大,给定值暂时不变,炉温就要下降,使得给出温度
下降,则有
,经过温度检测以及变换电路把对侧对象转换成电压信号,该电压信号经D/A变换器转换为数字信号后送入PLC中,与给定的对应所要控制的多组温度值进行比较,得知系统处于欠温度状态。
此时系统会加大占空比信号,控制加热功率,从而使炉温回升,直到重新等于给定值(即
)为止。
如果负荷减小,则炉温升高。
u(t)随之加大,使得
。
经过温度检测及变换电路把被测对象的温度转换成电压信号,该电压信号经D/A变换器转换为数字信号后送入PLC中,与给定的对应所要控制的多组温度值进行比较,得知系统处于过温度状态。
此时系统会启动风扇,控制吹风冷却装置,从而使炉温下降,知道重新等于给定值为止。
由此看出系统是通过热电偶测量被控量,并反馈到系统的输入端,从而形成了闭合回路,此反馈信号通过比较线路与给定值进行加法或减法运算,获得偏差信号,系统再根据偏差信号的大小和方向进行调节。
所以,炉温控制系统是一个按偏差调节的闭环系统。
3.2各独立模块方案论证
3.2.1温度检测模块
采用西门子S7-200,它集成14个输入/10输出共24个数字量I/O点。
可连接7个扩展模块,最大扩展至168路数字量I/O点或35路模拟量I/O点。
16K字节程序和数据存储空间。
5个独立的30kHz高速计数器,2路独立的20kHz高速脉冲输出,具有PID控制器。
1个R5485通讯编程口,具有PPI通讯协议,MPI通讯协议和自由方式通讯能力,I/O端能容易的整体拆卸。
具有较强的控制力。
使用西门子S7-200,其提供一个4点12位模拟量输入和温度传感输入模块,输入为DC-5~+5v和0~20mA电压或电流。
3.2.2主控模块PLC
S7-200cup224集成14输入/10输出共24个数字量I/O点。
可连续7个扩展模块,最大扩展至168路数字量I/O点或35路模拟量I/O点,16K字节程序和数据存储空间。
6个独立的30kHz高速计数器,2路独立的20kHz高速脉冲输出,具有PID控制器。
1个R5485通讯/编程口,具有PPI通讯协议,MPI通讯协议和自由方式通讯能力。
I/O端子排可很容易地整体拆卸。
是具有较强控制能力的控制器。
图3.1CUP224模块接线图
图3.2CPU224AC/DC/继电器
输入接线型式简图
图3.324VDC输入图3.4继电器输出图3.524VDC输出
3.2.3功率输出电路及其控制原理的分析
加热丝输出功率大小的调节,可以使用移相调压电路,也可以采用占空比开关电路进行控制。
在采用移想调压电路时,即将计算到的控制量经D/A变换,控制可控硅的移相触发电路,实现输出电压的无极调节。
由于电压输出波形的不完整,含有高次谐波分量,对电网有一定的干扰。
采用占空比开关电路控制,即考虑可控硅控制电压和被控的交流电压之间以及电热丝产生的热量和所家的电压之间的非线性,通过调节周期时间内的通电时间来调节输出功率的大小,可以避免D/A转换和信号放大造成的不必要的误差,也可以通过可控硅的过零触发电路避免对电网的谐波干扰。
在本系统中采用占空比开关电路控制,功率输出电路设计如图3.6。
图3.6功率输出图
3.2.4温度调节模块
本系统中风扇的作用是,当炉温过高时控制风扇对其进行降温。
当系统处于过温度状态,此时系统会启动风扇,控制吹风冷却装置,从而使炉温下降,知道重新等于给定值为止。
本系统中热电阻的作用是,当炉温过低时,控制热电阻对其进行加热。
当系统处于欠温状态时系统会启动热电阻,控制加热功率,从而使炉温回升,直到重新等于给定值为止。
4系统软件设计
4.1主要的工作流程
本系统采用PLC作为核心处理器件,把经过温度检测电路现场实时采集到的温度数据,存入PLC的内部数据存储器,送LED显示,并与预先设定值进行比较,然后由PLC输出信号去控制加热器。
进行温度控制程序的设计应考虑如下几个问题:
实时采集温度、温度显示、与上位PLC通信程序、警告和处理。
软件设计主要有:
主程序、初值设定子程序、温度读取子程序、显示子程序和输出控制子程序等。
初值设定子程序完成对温度初值的设定及数据保存;温度读子程序完成对温度传感器数据的读取、并通过液晶显示子程序显示温度值等等。
4.2数字PID的数学建模
典型的数字P1D控制系统如图3所示,图中SP(t)是给定值PV(t)为反馈量,C(t)为输出值,PID控制器的输入输出关系可表示为:
式4.1
在PLC控制系统中,系统通过PID控制指令实现的。
进入PLC的连续时间信号,必须经过采样和整量化后,变成数字量,方能进入存储器和寄存器,而在PLC中的计算和处理,不论是积分还是微分,只能用数值计算去逼近。
当采样周期相当短时,用求和代替积分,用差商代替微商,使PID算法离散化,将描述连续时间PID算法的微分方程,变为描述连续时间PID算法的差分方程。
PID的子程序流程图如图3所示,根据实际检测到得温度值和设定温度比较,求出相应的温度偏差值E,根据E与a的比较判断采用PID算法或是PD算法,随后进行算法处理,求出控制值。
在计算机控制系统中使用的是数字PID调节,就是对式1.1离散化,离散化时,令
,
式中T是采样周期,显然,上述周期T必须足够短,才能保证有足够的精度。
因此数字PID调节器,表达式如下:
式4.2
由控制理论可知:
离散化采样频率越高,采样后失去的信息越少,相应的控制性能也越好。
其主要采用主程序调用子程序通过中断返回采样值,循环调用进行,程序框图如图3.8
5.系统介绍
5.1现场总线控制系统(FCS)介绍
5.1.1系统简介
本现场总线控制系统是基于PROFIBUS和工业以太网通讯协议、在传统过程控制实验装置的基础上升级而成的新一代过程控制系统。
整个实验装置分为上位控制系统和控制对象两部分,上位控制系统流程图如图5.1所示:
图5.1上位控制系统
5.1.2系统组成
本实验装置由被控对象和上位控制系统两部分组成。
系统动力支路分两路:
一路由三相(380V交流)磁力驱动泵、气动调节阀、直流电磁阀、PA电磁流量计及手动调节阀组成;另一路由变频器、三相磁力驱动泵(220V变频)、涡轮流量计及手动调节阀组成。
1、被控对象
被控对象由不锈钢储水箱、圆筒形有机玻璃水箱和敷塑不锈钢管路组成。
水箱:
包括上水箱和储水箱。
上水箱采用淡蓝色圆筒型有机玻璃,不但坚实耐用,而且透明度高,便于学生直能接观察到液位的变化和记录结果。
上水箱尺寸为:
d=25cm,h=20cm; 水箱有三个槽,分别是缓冲槽,工作槽,出水槽。
储水箱尺寸为:
长×宽×高=68cm×52㎝×43㎝。
储水箱内部有两个椭圆形塑料过滤网罩,防止两套动力支路进水时有杂物进入泵中。
管道:
整个系统管道采用敷塑不锈钢管组成,所有的水阀采用优质球阀,彻底避免了管道系统生锈的可能性。
有效提高了实验装置的使用年限。
其中储水箱底有一个出水阀,当水箱需要更换水时,将球阀打开让水直接排出。
2、检测装置
压力传感器、变送器:
采用SIEMENS带PROFIBUS-PA通讯协议的压力传感器和工业用的扩散硅压力变送器,扩散硅压力变送器含不锈钢隔离膜片,同时采用信号隔离技术,对传感器温度漂移跟随补偿。
压力传感器用来对上水箱的液位进行检测,其精度为0.5级,因为为二线制,故工作时需串接24V直流电源。
3.执行机构
调节阀:
采用SIEMENS带PROFIBUS-PA通讯协议的气动调节阀,用来进行控制回路流量的调节。
它具有精度高、体积小、重量轻、推动力大、耗气量少、可靠性高、操作方便等优点。
由CPU直接发送的数字信号控制阀门的开度,本气动调节阀自动进行零点校正,使用和校正都非常方便。
变频器:
本装置采用SIEMENS带PROFIBUS-DP通讯接口模块的变频器,其输入电压为单相AC220V,输出为三相AC220V。
水泵:
本装置采用磁力驱动泵,型号为16CQ-8P,流量为32升/分,扬程为8米,功率为180W。
泵体完全采用不锈钢材料,以防止生锈,使用寿命长。
其中一只为三相380V恒压驱动,另一只为三相变频220V输出驱动。
可移相SCR调压装置:
采用可控硅移相触发装置,输入控制信号为4~20mA标准电流信号。
输出电压用来控制加热器加热,从而控制锅炉的温度。
电磁阀:
在本装置中作为气动调节阀的旁路,起到阶跃干扰的作用。
电磁阀型号为:
2W-160-25;工作压力:
最小压力为0Kg/㎝2,最大压力为7Kg/㎝2;工作温度:
-5~80℃。
4.控制器
控制器采用SIEMENS公司的S7300CPU,型号为315-2DP,本CPU既具有能进行多点通讯功能的MPI接口,又具有PROFIBUS-DP通讯功能的DP通讯接口。
5、空气压缩机
用于给气动调节阀提供气源,电动机的动力通过三角胶带传带动空压机曲轴旋转,经连杆带动活塞做往复运动,使汽缸、活塞、阀组所组成的密闭空间容积产生周期变化,完成吸气、压缩、排气的空气压缩过程,压