磷在钢中的存在形式通常认为是以磷化物.docx
《磷在钢中的存在形式通常认为是以磷化物.docx》由会员分享,可在线阅读,更多相关《磷在钢中的存在形式通常认为是以磷化物.docx(22页珍藏版)》请在冰豆网上搜索。
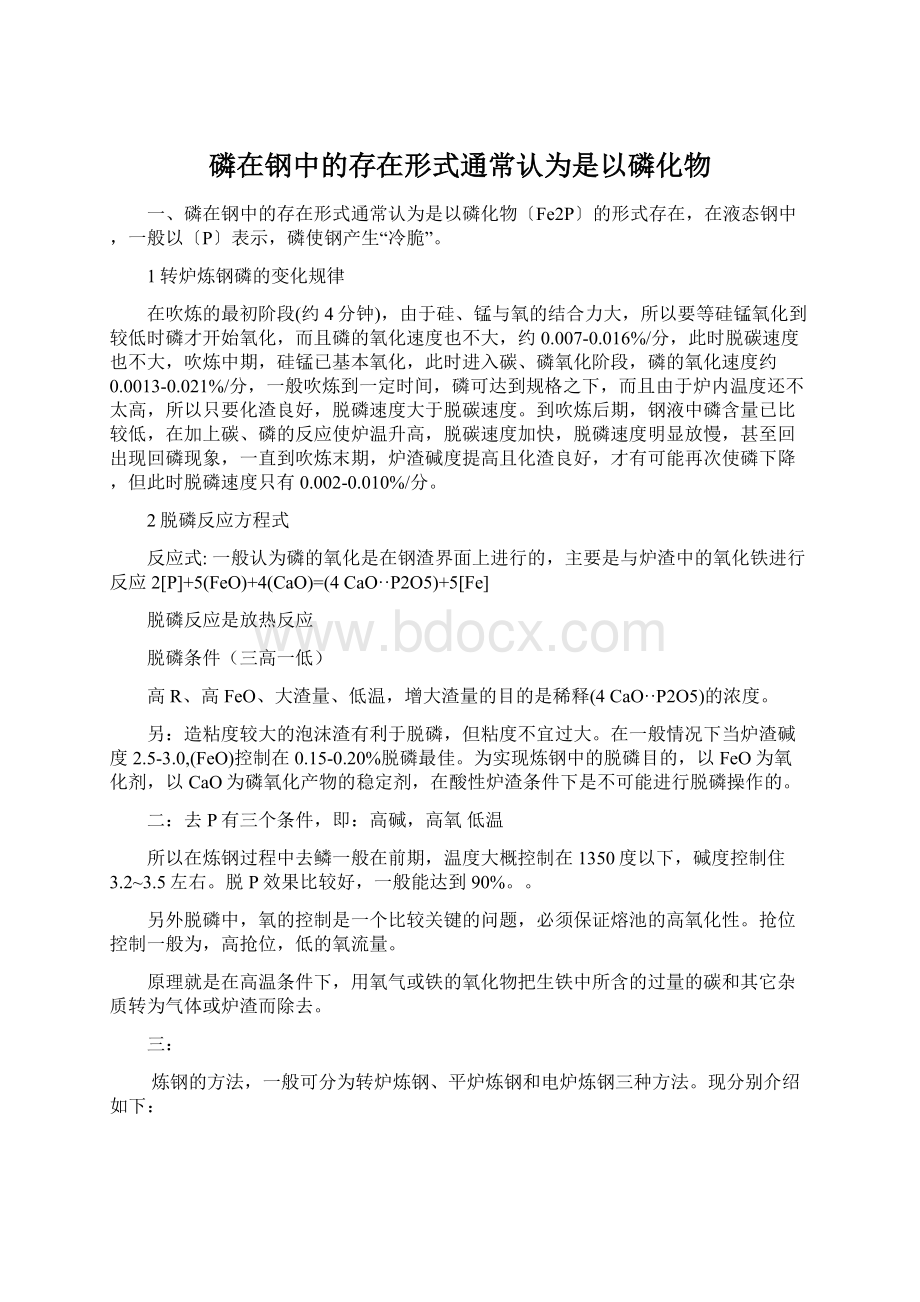
磷在钢中的存在形式通常认为是以磷化物
一、磷在钢中的存在形式通常认为是以磷化物〔Fe2P〕的形式存在,在液态钢中,一般以〔P〕表示,磷使钢产生“冷脆”。
1转炉炼钢磷的变化规律
在吹炼的最初阶段(约4分钟),由于硅、锰与氧的结合力大,所以要等硅锰氧化到较低时磷才开始氧化,而且磷的氧化速度也不大,约0.007-0.016%/分,此时脱碳速度也不大,吹炼中期,硅锰已基本氧化,此时进入碳、磷氧化阶段,磷的氧化速度约0.0013-0.021%/分,一般吹炼到一定时间,磷可达到规格之下,而且由于炉内温度还不太高,所以只要化渣良好,脱磷速度大于脱碳速度。
到吹炼后期,钢液中磷含量已比较低,在加上碳、磷的反应使炉温升高,脱碳速度加快,脱磷速度明显放慢,甚至回出现回磷现象,一直到吹炼末期,炉渣碱度提高且化渣良好,才有可能再次使磷下降,但此时脱磷速度只有0.002-0.010%/分。
2脱磷反应方程式
反应式:
一般认为磷的氧化是在钢渣界面上进行的,主要是与炉渣中的氧化铁进行反应2[P]+5(FeO)+4(CaO)=(4CaO··P2O5)+5[Fe]
脱磷反应是放热反应
脱磷条件(三高一低)
高R、高FeO、大渣量、低温,增大渣量的目的是稀释(4CaO··P2O5)的浓度。
另:
造粘度较大的泡沫渣有利于脱磷,但粘度不宜过大。
在一般情况下当炉渣碱度2.5-3.0,(FeO)控制在0.15-0.20%脱磷最佳。
为实现炼钢中的脱磷目的,以FeO为氧化剂,以CaO为磷氧化产物的稳定剂,在酸性炉渣条件下是不可能进行脱磷操作的。
二:
去P有三个条件,即:
高碱,高氧低温
所以在炼钢过程中去鳞一般在前期,温度大概控制在1350度以下,碱度控制住3.2~3.5左右。
脱P效果比较好,一般能达到90%。
。
另外脱磷中,氧的控制是一个比较关键的问题,必须保证熔池的高氧化性。
抢位控制一般为,高抢位,低的氧流量。
原理就是在高温条件下,用氧气或铁的氧化物把生铁中所含的过量的碳和其它杂质转为气体或炉渣而除去。
三:
炼钢的方法,一般可分为转炉炼钢、平炉炼钢和电炉炼钢三种方法。
现分别介绍如下:
1.转炉炼钢法:
这种炼钢法使用的氧化剂是氧气。
把空气鼓入熔融的生铁里,使杂质硅、锰等氧化。
在氧化的过程中放出大量的热量(含1%的硅可使生铁的温度升高200摄氏度),可使炉内达到足够高的温度。
因此转炉炼钢不需要另外使用燃料。
转炉炼钢是在转炉里进行。
转炉的外形就像个梨,内壁有耐火砖,炉侧有许多小孔(风口),压缩空气从这些小孔里吹炉内,又叫做侧吹转炉。
开始时,转炉处于水平,向内注入1300摄氏度的液态生铁,并加入一定量的生石灰,然后鼓入空气并转动转炉使它直立起来。
这时液态生铁表面剧烈的反应,使铁、硅、锰氧化(FeO,SiO2,MnO,)生成炉渣,利用熔化的钢铁和炉渣的对流作用,使反应遍及整个炉内。
几分钟后,当钢液中只剩下少量的硅与锰时,碳开始氧化,生成一氧化碳(放热)使钢液剧烈沸腾。
炉口由于溢出的一氧化炭的燃烧而出现巨大的火焰。
最后,磷也发生氧化并进一步生成磷酸亚铁。
磷酸亚铁再跟生石灰反应生成稳定的磷酸钙和硫化钙,一起成为炉渣。
当磷于硫逐渐减少,火焰退落,炉口出现四氧化三铁的褐色蒸汽时,表明钢已炼成。
这时应立即停止鼓风,并把转炉转到水平位置,把钢水倾至钢水包里,再加脱氧剂进行脱氧。
整个过程只需15分钟左右。
如果空气是从炉低吹入,那就是低吹转炉。
随着制氧技术的发展,现在已普遍使用氧气顶吹转炉(也有侧吹转炉)。
这种转炉吹如的是高压工业纯氧,反应更为剧烈,能进一步提高生产效率和钢的质量。
四:
炼钢:
1、反应原理
高温下,用氧化剂把生铁里过多的碳和其它杂质氧化成气体或炉渣而除去。
2、目的:
降碳、调硅锰、去硫磷。
3主要反应(分三个阶段)
(1)氧化造渣
2Fe+O2=2FeO+Q
2FeO+Si=SiO2+2Fe+Q
FeO+Mn=Fe+MnO+Q
FeO+C=CO+Fe-Q
生成的二氧化硅、氧化锰与造渣材料生石灰相互作用成为炉渣。
(2)去硫、磷
FeS+CaO=FeO+CaS
2P+5FeO+3CaO=5Fe+Ca3(PO4)2
(3)脱氧
用硅铁、锰铁或金属铝来还原钢水中含有的少量FeO
2FeO+Si=SiO2+2Fe
3FeO+2Al=3Fe+Al2O3
FeO+Mn=Fe+MnO
生成的二氧化硅等大部分形成炉渣而除去,部分的硅、锰等留在钢里以调整钢的成分。
钢水合格后,可以浇成钢的铸件或钢锭,钢锭可以再轧成各种钢材。
五:
氧气顶吹转炉炼钢法
(1)转炉的构造
(2)原料:
生铁(液态)、氧气、适量的造渣材料(如生石灰等)、脱氧剂。
(3)热源:
依靠熔融铁水中的杂质等被氧气氧化所放出的热量,不需要燃料。
炉渣中碱性氧化物的质量分数总和与酸性氧化物的质量分数总和之比,常用炉渣中的氧化钙含量与二氧化硅含量之比表示,符号R=CaO/SiO2
一般情况下,转炉吹氧开始之后就开始加料,那么炉渣就开始化了,只不过比较缓慢而已。
但是前期的炉渣基本化起来是没有问题的。
中期随着炉温的上升,碳氧反应开始激烈,会消耗大量的氧,于是炉渣中的氧化铁开始减少,会造成炉渣结坨的现象,叫做返干,这时需要提高枪位、加入助溶剂来化渣。
到终点前,炉渣化好的情况下,基本上如果吹氧时间12分钟的化,到10分钟多就应该降枪拉碳了。
氧化反应应该在前,转炉吹炼前期主要为硅锰氧化期,硅锰氧化结束后进入碳氧反应期。
实际顶吹氧气转炉炉内脱碳反应速度的变化将炼钢过程分为前、中、后三个阶段。
前期因铁水中的硅含量很高.而铁水温度较低,所以以硅的氧化为主,而脱碳反应受到抑制。
硅的氧化速度由快变馒.而脱破速度由慢到快,最后达到最大值。
中期钢水温度上升,钢水中的碳以极大速度转移到点火区,供给的氧气几乎消耗于脱碳,因此脱碳速度始终保持最高水平。
后期脱碳反应继续进行,但钢水中的碳的浓度已很低,脱碳速度随着钢水碳含量的减少不断下降。
转炉炼钢过程中留渣操作是什么意思?
意思是出完钢溅完渣后,留下一部分或全部渣子做为下一炉的初渣使用,好处是可以提高金属收得率,使初渣早化,坏处是会增加渣量,造成喷溅,还会对炉衬造成一定的损伤。
所谓粘度高就是钢渣的成分是高熔点物质。
在炼钢温度下没有完全变为液体,故流动性差。
有一条基本规律:
碱度高,粘度肯定高。
碱度=氧化钙/二氧化硅。
加的石灰多了碱度肯定高,渣子肯定很黏。
转炉炼钢最后要脱氧,用的脱氧剂常常是硅铁合金,其中的硅和氧化亚铁反应生成二氧化硅,之后再给转炉中加入熔剂碳酸钙,碳酸钙分解生成氧化钙,生成的氧化钙与二氧化硅反应生成硅酸钙,硅酸钙为炉渣,使得钢中的二氧化硅减少。
1、转炉炼钢法的分类转炉是以铁水为主要原料的现代炼钢方法。
该种炼钢炉由圆台型炉帽、圆柱型炉身和球缺型炉底组成。
炉身设有可绕之旋转的耳轴,以满足装料和出钢、倒渣操作,故而得名。
酸性空气底吹转炉——贝塞麦炉(英国1856年)空气转炉{碱性空气底吹转炉——托马斯炉(德国1878年)碱性空气侧吹转炉(中国1952年)转炉{氧气顶吹转炉——LD(奥地利1952年)氧气转炉{氧气底吹转炉——OBM(德国1967年)顶底复吹转炉(法国1975年)2、氧气顶吹转炉炼钢法简介
(1)诞生的背景及简称现代炼钢生产首先是一个氧化精炼过程,最初的贝氏炉和托马斯炉之所以采用空气吹炼正是利用其中的氧。
二次世界大战以后,工业制氧机在美国问世,使利用纯氧炼钢成为可能,但原来的底吹方式炉底及喷枪极易烧坏。
美国联合碳化物公司于1947年在实验室进行氧气顶吹转炉的实验并获成功,命名为BOF。
奥地利闻之即派有关专家前往参观学习,回来后于1949年在2吨的转炉上进行半工业性实验并获成功,1952年、1953年30吨氧气顶吹转炉分别在Linz和Donawitz建成投产,故常简称LD。
1967年12月德国与加拿大合作发明了氧气底吹转炉,使用双层套管喷嘴并通以气态碳氢化合物进行冷却。
1975年法国研发了顶底复吹转炉,综合了LD和OBM的优点,77年在世界年会上发表。
(2)氧气顶吹转炉的特点1)优点氧气顶吹转炉一经问世就显示出了极大的优越性,世界各国竟相发展,目前成为最主要的炼钢法。
其优点主要表现在:
(1)熔炼速度快,生产率高(一炉钢只需20分钟);
(2)热效率高,冶炼中不需外来热源,且可配用10%~30%的废钢;(3)钢的品种多,质量好(高低碳钢都能炼,S、P、H、N、O及夹杂含量低);(4)便于开展综合利用和实现生产过程计算机控制。
2)缺点当然,LD尚存在一些问题,如吹损较高(10%,)、所炼钢种仍受一定限制(冶炼含大量难熔元素和易氧化元素的高合金钢有一定的困难)等。
3氧气转炉的发展趋势对于氧气顶吹转炉的推广和普及首推日本迅速,且引导了LD的发展趋势:
(1)容量大型化(相对投资较小);
(2)配加炉外精炼以增加品种,提高质量(理论上可炼任何钢种);(3)引入底吹技术,实施复合吹炼(减少喷溅,降低吹损);(5)实现冶炼过程计算机控制。
1转炉炼钢的原材料引言转炉炼钢所用原材料可分为金属料和非金属料两大类。
原材料质量的好坏,不仅关系到吹炼操作的难易,而且会影响钢的产量、质量和生产成本。
1.1金属料转炉炼钢的金属料主要是铁水、废钢和铁合金。
作用:
转炉炼钢的主原料,一般占装入量的70%以上。
2要求铁水应符合一定要求,以简化和稳定操作并获得良好技术经济指标。
1)温度≥1250℃而且稳定铁水温度的高低,标志着其物理热的多少。
较高的铁水温度,不仅能保证转炉吹炼顺利进行,同时还能增加废钢的配加量,降低生产成本。
因此,希望铁水的温度尽量高些,一般应保证入炉时仍在1250℃~1300℃以上。
另外,还希望铁水温度相对稳定,以利于冶炼操作和生产调度。
2)成分合适而且波动小转炉炼钢的适应性较强,可将各种成分的铁水吹炼成钢。
但是,为了方便转炉操作及降低生产成本,铁水的成分应该合适而稳定。
(1)铁水的含磷量≤0.4%:
磷会使钢产生“冷脆”现象,是钢中的有害元素之一。
转炉单渣法冶炼时的脱磷效果为85%~95%,普碳钢的含磷量通常要求≤0.04%,因此,国标规定铁水的含磷量小于0.4%。
需要指出的是,高炉内不能去磷,如果铁水的含磷量超过0.4%,或者吹炼低磷钢,则需采用双渣法冶炼或对铁水进行预脱磷处理。
(2)铁水的含硫量≤0.07%:
硫会使钢产生“热脆”现象,也是钢中的有害元素。
转炉的脱硫效果不理想,单渣法冶炼时的脱硫率仅为30%~35%,而通常要求钢液的含硫量在0.05%以下,因此国标规定铁水含硫量≤0.07%。
如果铁水含硫量超过0.07%或吹炼低硫钢,则需采用双渣法冶炼或对铁水进行预脱硫处理。
(3)铁水的含硅量:
铁水中的硅是转炉炼钢的主要发热元素之一,含硅量每增加0.1%,废钢比可增加1.3%~1.5%。
对于大、中型转炉,铁水含硅量以0.5%~0.8%为宜。
小型转炉的热损较大,铁水的含硅量可以高些。
若含硅量低于0.5%,铁水的化学热不足,会导致废钢比下降,小容量转炉甚至不能正常吹炼;反之,如果铁水含硅量高于0.8%,不仅会增加造渣材料的消耗,而且使炉内的渣量偏大,过多的渣量容易引起喷溅,增加金属损失。
另外,铁水含硅量高时,初期渣子的碱度低,对炉衬的侵蚀作用加剧;同时,初期渣中的二氧化硅含量高,这会使渣中的FeO、MnO含量相对降低,容易在石灰块表面生成一层熔点为2130℃的2CaO•SiO2外壳,阻碍石灰熔化,降低成渣速度,不利于早期的去磷。
应该指出的是,一些钢厂铁水的含硅量超过了1.2%,个别的甚至达到了1.5%,对此应进行预脱硅处理,以减轻转炉的负担。
(4)铁水的含锰量:
铁水中的锰是一种有益元素,主要体现在锰氧化后生成的氧化锰能促使石灰溶解,有利于提高炉龄和减轻氧枪粘钢。
我国大多数钢铁厂所用铁水的含锰量都不高,多为0.2%~0.4%。
提高铁水含锰量的方法主要是向高炉的原料中配加锰矿石,但这将会使炼铁生产的焦比升高和高炉的生产率下降。
对于铁水增锰的合理性还需要做详细的技术经济对比,因此,目前对铁水含锰量不提硬性要求。
(5)铁水的含碳量:
碳也是转炉炼钢的主要发热元素,≥3.5%的含碳量即可满足冶炼要求,而通常铁水含碳4%左右,故一般不做要求。
国内一些转炉炼钢厂对铁水成分的控制见表(6)1-1。
3)带渣量≤0.5%高炉渣中含有大量的S、SiO2,因此希望兑入转炉的铁水尽量少带渣,以减轻脱硫任务和减少渣量,通常要求带渣量不得超过0.5%。
3铁水的预处理定义:
铁水在兑入转炉之前进行的脱硫、脱磷或脱硅操作叫做铁水预处理。
目的:
减轻高炉、转炉的负担,提高生产率。
1)铁水炉外脱硫铁水脱硫的条件比钢水优越(铁水中碳、硅、磷等元素的含量高,硫的活度系数大,同时铁水中的氧含量低),脱硫效率比钢水脱硫高4~6倍,经济上比转炉双渣法合算,因此铁水预脱硫技术已被国内外广泛采用。
基本思路:
向铁水中加入脱硫剂使之化合入渣。
(1)脱硫剂及其特点:
目前常用的铁水预脱硫剂主要有以下四种。
①电石粉(CaC2)脱硫反应:
CaC2(S)+[S]=CaS(S)+2[C]特点:
脱硫能力强,但脱硫过程中有少量CO和C2H2逸出,并带出电石粉,污染环境,因而必须安装除尘装置;价格较贵。
②石灰粉(CaO)脱硫反应:
2CaO(S)+[S]+1/2[Si]=CaS(S)+1/22CaO•SiO2(S)特点:
价格便宜,脱硫成本低,但单独使用时脱硫能力差,而且石灰表面会出现C2S,阻碍脱硫反应继续进行,降低脱硫速度和效率,为此,常配加适量的铝或苏打粉避免C2S的生成:
CaO(S)+[S]+2/3[Al]=CaS(S)+1/3Al2O3(S)使脱硫速度和效率明显提高,如8图1-1。
③苏打粉(Na2CO3)脱硫反应:
Na2CO3(l)+[S]+[Si]=Na2S(l)+SiO2(S)+{CO}特点:
脱硫能力很强,且产生的气体具有搅拌作用,脱硫速度快,但价格贵且污染严重,现已很少使用,有时与其它粉剂配成复合脱硫剂。
④金属镁脱硫反应:
金属镁的沸点仅为1107℃,铁水温度下为气体,故脱硫反应为:
{Mg}+[S]=MgS(S)特点:
金属镁直接加入铁水时,会发生爆发式气化反应,不仅导致镁的利用率大大降低,而且还会引起铁水喷溅而造成事故,因此不能单独使用,常与其它粉剂组成复合脱硫剂。
在相同的铁水条件下,各脱硫剂的能力强弱顺序为:
Na2CO3、CaC2、Mg、CaO,见9表1-3。
以上脱硫剂有的可单独使用,但多为几种配合使用,如电石粉+石灰粉、金属镁+电石粉、石灰粉+苏打粉、金属镁+石灰粉等,其脱硫能力有较大差别。
(2)脱硫的方法及效果:
铁水预脱硫的基本工艺是向铁水中加入脱硫剂并使之混合而发生脱硫反应,目前使用最广泛的是机械搅拌法和喷吹法。
①机械搅拌法混合方式:
将脱硫剂加入铁水罐中,用耐火材料制成的搅拌器插入铁水搅拌,使之与脱硫剂充分混合。
特点:
脱硫效果与搅拌器的转速及脱硫剂的种类有关,见(10)图1-3、1-4。
此法有多种形式,具有代表性的是日本的KR法(电石粉为主),武钢二炼79年引进,经消化改造使用以石灰粉为主的脱硫剂。
②喷吹法混合方式:
它是以空气或惰性气体为载体,利用喷枪将粉状脱硫剂喷射到铁水中,使铁水与脱硫剂充分混合。
宝钢80年代由日本引进的叫DTS法,喷吹电石粉。
各种脱硫剂在喷射法中的应用效果见图1-6。
实际生产中,各厂应根据要求达到的脱硫程度、铁水的热损和铁损、脱硫设备费用、环境污染等问题,选用最适合的脱硫剂和脱硫方法。
2)铁水预脱硅基本思路:
向铁水中加入氧化性的脱硅剂,使之氧化成SiO2进入炉渣。
(1)脱硅剂:
常用的脱硅剂是以氧化铁皮和烧结矿粉为主,配加少量石灰和萤石以降低渣子的黏度。
各厂家所用配比也不完全一样:
日本福山氧化铁皮70~100%,石灰0~20%,萤石0~10%;日本水岛烧结矿粉75%,石灰25%。
脱硅剂用量约为15~30kg/t。
(2)脱硅方法:
常用的炉外脱硅方法有投入法和顶喷法两种。
投入法是在高炉出铁时,将脱硅剂投到铁水沟中,借助铁水流入铁水罐的冲击搅拌作用使之充分混合、反应。
这是最早的一种脱硅方法,效率较低,通常在50%左右。
顶喷法是用0.2~0.3MPa压力的空气通过喷枪从(铁沟或流入铁水灌的铁水流)铁水液面以上一定高度将脱硅剂喷入,使之混合、反应。
由于该方式使铁水与脱硅剂两次混合,所以脱硅效率高达70~80%,铁水含硅可达0.1~0.15%以下。
3)铁水预脱磷转炉炼钢的脱磷效率较高,双渣法冶炼尤其如此,但会增加造渣材料消耗,并延长冶炼时间,生产成本增大。
近年来,铁水的炉外脱磷研究有了较大的发展,已用于工业生产。
基本思路:
向铁水中加入脱磷剂使其中的磷氧化并固定在渣中。
(1)脱磷剂:
目前广泛使用的是苏打系和石灰系两类。
苏打系脱磷剂:
2[P]+5[O]+3Na2CO3(S)=(Na2O•P2O5)+3{CO}石灰系脱磷剂:
2[P]+5[O]+4CaO(S)=(4CaO•P2O5),其中常配有一定的氧化铁皮或烧结矿粉和萤石粉助熔剂。
(2)脱硅处理:
由于磷与氧的亲和力小于硅与氧的亲和力,而且铁水中总含有一定的硅,因此,欲要脱磷需先进行脱硅处理。
使用苏打系脱磷时要求[Si]<0.1%,使用石灰系处理时要求[Si]<0.15%。
(3)铁水炉外脱磷方法及效果:
目前,铁水脱磷方法主要喷吹法,它是以气体作载体将脱磷剂喷吹到铁水包中,使之充分混合,快速脱磷。
日本新日铁以氩气喷吹45kg/t,时间20min,脱磷率达90%左右。
3)铁水同时脱硫和脱磷从上所述,苏打和石灰既是脱硫剂也是脱磷剂,因此铁水同时进行脱硫和脱磷不仅成本低而且生产率高。
目前,已在工业上应用的同脱工艺有以下两种。
(1)SARP法:
即日本住友的碱性精炼工艺,它是将铁水首先进行脱硅处理,当[Si]<0.1%后扒出炉渣,然后喷吹19kg/t苏打粉,脱硫率可达96%,脱磷率可达95%。
该法的特点是,脱硫磷效率高,但处理成本高、耐火材料侵蚀严重,同时有气体(CO)污染。
(2)ORP法:
也是先进行脱硅处理,当[Si]<0.15%后扒出炉渣,然后喷吹52kg/t石灰基粉料,脱硫率可达80%,脱磷率可达88%。
该法的特点是,处理成本低,但渣量大而铁损多(TFe=20~30%)。
作用:
废钢是转炉炼钢的另一种金属炉料,其作用是冷却熔池。
氧气顶吹转炉炼钢中,主原料铁水的物理热和化学热足以把熔池的温度从1250℃~1300℃加热到1600℃左右的炼钢温度,且有富余热量,废钢就是被用来消耗这些富余热量,以调控熔池的温度。
2要求
(1)清洁、少锈,无混杂,不含有色金属;
(2)最大长度不得超过炉口直径的二分之一,最大截面积要小于炉口面积的五分之一。
3废钢的加工和预热1)废钢的加工转炉炼钢所用废钢多为外购废钢。
其来源广泛,大小悬殊,外形各异,且多有混杂,应针对所购废钢的特点进行相应的加工处理如切割、打包、火烧、挑拣、水洗等,以满足转炉炼钢对入炉废钢的基本要求。
2)废钢的预热目的:
提高废钢比(见17表1-8),降低生产成本。
方法及效果:
利用铁水罐余热和燃料燃烧加热。
(首钢)将废钢装入铁水罐中,置于煤气烘烤器下烘烤30~40min,然后接铁水一并倒入转炉,废钢比提高10%。
,根据常炼钢种不同还可能有Fe-Cr、Fe-W、Fe-Mo、Ni等合金。
要求:
成分准确、块度合适(5~40mm)、用前烘烤。
思考题1简述氧气转炉的发展趋势。
2转炉炼钢对铁水有哪些要求?
3常用的脱硫剂有哪些?
它们的脱硫能力如何?
4铁水炉外预脱硫方法有哪些?
影响机械搅拌法脱硫效果的因素是什么?
5简述SARP法同时脱硫脱磷工艺过程。
6炼钢用石灰应满足哪些要求?
2.2底吹气体射流,实验用氮气从底部吹入水或水银中,并用高速摄影机拍摄其流出情况,发现气体通过浸没式喷嘴流出时在熔池中的行为有两种:
(1)鼓泡流速较小时,气体在喷嘴出口鼓起而形成气泡并逐渐长大,当气泡长大一定程度(浮力大于粘滞力)后则脱离孔口上浮,这一现象称为鼓泡。
(2)形成射流流速较大时,气体在孔口上形成连续的气流射入液体中,这种现象称为浸没式射流。
实验发现,由流量计算的表观马赫数Ma/增加到1以上时,从喷嘴流出的气体由鼓泡转变成射流,即表观马赫数Ma/等于1的速度为临界流速,如(32)图2-12。
表观马赫数Ma/用2-9式计算:
Ma/=υ/a=Q/aA式中υ——气体出口速度,m/s;a——室温的音速,m/s;A——喷嘴截面积,m2;Q——气体流量,m3/s。
电除尘的工作原理、控制和影响除尘效果等因素的探讨
目前,氧气转炉炼钢的煤气净化回收主要有两种方法,一是采用煤气湿法(OG法)净化回收系统,二是采用煤气干法(LT法)净化回收系统。
干法(LT法)除尘系统主要由蒸发冷却器、静电除尘器和煤气冷却器组成。
与老式的除尘系统(OG)法相比,LT法的主要优点是:
除尘净化效率高,通过电除尘器可直接将粉尘浓度降至10mg/Nm3以下,对于粒径小于0.1um的微细粉尘,仍有较高的除尘效率;该系统全部采用干法处理,不存在二次污染和污水处理的系统;系统阻损小,煤气回收热值高,回收粉尘可直接利用,节约了能源;系统优化,减少占地面积,便于管理和维护。
因此,干法除尘技术比湿法除尘技术具有更高的经济效益和环境效益。
干法(LT法)技术在国际上已被认定为今后的发展方向。
由于所回收的煤气可以再利用,太钢的转炉炼钢过程已经实现负能炼钢。
经电除尘器(ESP)处理过的铁含量较高的粉尘灰,经压块系统处理后,可以当废钢继续使用。
另外,在环境保护和能源方面比较,由于湿法(OG)净化回收系统存在着能耗高(比如:
水,电等资源是LT法的5倍消耗)、二次污染的缺点,湿法(OG)系统将随着社会的发展而逐渐被干法(LT法)除尘系统所取代,它将成为冶金工业可持续发展的先决条件。
该技术已获得全世界的普遍重视和采用,到目前为止,中国已有宝钢、莱钢、包钢、太钢等钢厂从德国引进该技术,并得到了应用,其应用总数已达18套以上,其中太钢的LT系统除尘效果在国内钢厂中达到领先水平。
此外,天津铁厂新引进的LT系统也已于2007年4月28日进行了热试。
LT系统的工艺流程
下图为LT系统的工艺流程的介绍
图1太钢LT系统工艺流程图
静电除尘器(ESP)的工作原理
图2ESP(电除尘器)本体工艺流程图
静电除尘器的功能是除去转炉煤气的灰尘。
在LT工艺中,由于转炉特殊的操作方式,煤气冷却系统和ESP除尘系统必须交替处理含O2和含CO的煤气。
为此,整个LT系统按优化流体动力设计,如:
对整个气体管路进行密封,防止形成气体爆炸性混合物和产生燃烧;此外,炼钢过程中煤气气流的成分随着转炉操作阶段的改变而改变,而流体的动力设计可以防止混合煤气气流的缓冲压力。
在转炉吹氧过程中,烟气燃烧是不可避免的,水平电除尘器的设计能抵抗压力波动,并且在出口和入口安装有选择德国进口的卸压阀,这些阀的关闭位置分别由三个光电开关监控,以此来保证系统的安全性能。
静电除尘器分别由平行布置的电极组成。
这些电极通过ESP壳体接地,准备被除尘的气体依次流经电极间通道、煤气通道的分布板以及放电电极。
放电电极为高压负电的条形带刺电极,由绝缘子支撑,由于在放电电极周围的高磁场密度,形成了放电电晕,从而形成了带负电的煤气电离子。
在高压静电磁场的作用下,煤气负电离子流向阳极板,在正电极板上形成了电流,部分负极煤气离子附着在灰尘上,如同放电给电极一样,将带电离子转给灰尘,灰尘则吸附在阳极板(CE)上。
从干煤气中收集到的灰尘沉积到电极上,通过CE振打周期性的排出。
负离子灰尘则吸附在阳极收尘板上。
3静电除尘器(ESP)的配置
LT炼钢工艺中的静电除尘器包括一个柱形钢罩,除下部区域外,这个钢罩整体有绝热防护罩,在这个罩子里,安装有4个串联的高压静电场,每个静电场有几个并联的大暗煤气通道。
如前所述,煤气通道由接地集电极形成,其中布置有高压放电电极——阴极线(DE)。
集电极包括立式阳极板,沿煤气流向一个挨一个布置。
一个静电场的集电极包括若干根阴极线组成的阴极框,