飞锤支架工艺夹具设计.docx
《飞锤支架工艺夹具设计.docx》由会员分享,可在线阅读,更多相关《飞锤支架工艺夹具设计.docx(15页珍藏版)》请在冰豆网上搜索。
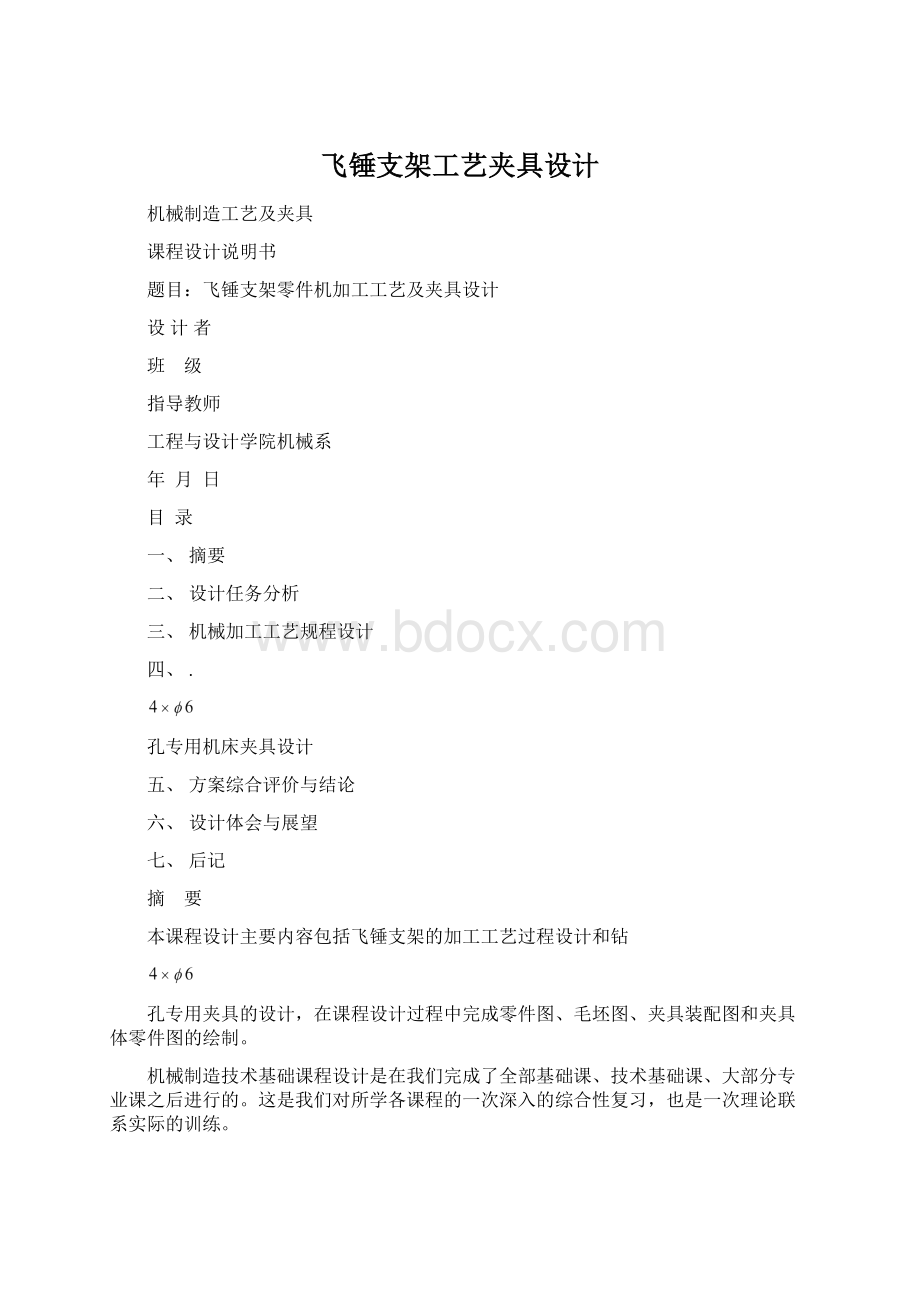
飞锤支架工艺夹具设计
机械制造工艺及夹具
课程设计说明书
题目:
飞锤支架零件机加工工艺及夹具设计
设计者
班 级
指导教师
工程与设计学院机械系
年 月 日
目 录
一、摘要
二、设计任务分析
三、机械加工工艺规程设计
四、.
孔专用机床夹具设计
五、方案综合评价与结论
六、设计体会与展望
七、后记
摘 要
本课程设计主要内容包括飞锤支架的加工工艺过程设计和钻
孔专用夹具的设计,在课程设计过程中完成零件图、毛坯图、夹具装配图和夹具体零件图的绘制。
机械制造技术基础课程设计是在我们完成了全部基础课、技术基础课、大部分专业课之后进行的。
这是我们对所学各课程的一次深入的综合性复习,也是一次理论联系实际的训练。
能够顺利完成这次课程设计,首先得益于朱晓虹老师的悉心指导,同学们的耐心解答。
在设计过程中,缺乏实际的生产经验,导致在设计中碰到了许多问题。
但在同学们的帮助下,通过请教老师,翻阅资料、查工具书,解决设计中的一个又一个问题。
在此,十分感谢朱晓虹老师的细心指导,感谢同学们的帮助。
1.零件工艺性分析
1.1零件的用途
飞锤支架为盘类零件,主要用于柴油发动机上。
用于安装柴油发动机减速器的飞锤,便于发动机进行调速。
1.2零件的技术要求
飞锤支架属于盘类零件,材料为QT600-2,毛坯制造完成后需要进行时效处理,硬度要求为250-300HBW。
其全部技术要求如下表
表1飞锤支架的技术要求
加工表面
尺寸及偏差
/mm
公差/mm
及精度等级
表面粗糙度
/
形位公差
/mm
飞锤支架右端面
33
0.062,IT9
3.2
右圆台面
0.027,IT8
1.6
19mm圆柱面
19
0.033,IT8
1.6
15mm圆柱面
15
0.18,IT12
12.5
11mm圆柱面
11
0.043,IT9
6.3
7mm孔
7
0.036,IT8
1.6
左凹槽底面
5
0.030,IT9
6.3
左凹槽侧面
18
0.70,IT12
12.5
6mm孔
6
0.030,IT9
6.3
6.5mm螺栓孔
6.5
0.18,IT12
12.5
2.零件毛坯的确定
2.1零件的生产类型
零件的生产类型是指企业(或车间、工段、班组、工作地等)生产专业化程度的分类,它对工艺规程的制订具有决定性的影响。
生产类型一般可分为大量生产、成批生产和单件生产三种类型,不同的生产类型有着完全不同的工艺特性。
零件的生产类型是按零件的年生产纲领和产品特征来确定的。
生产纲领是指企业在计划期内应当生产的产品产量和进度计划。
年生产纲领是包括备品和废品在内的某产品的年产量。
零件的年生产纲领N可按下式计算
其中
——是零件的生产纲领(件/年);
——产品的年产量(台、辆/年);
——每台(辆)产品中该零件的数量(件/台、辆);
——备品率,一般取
;
——废品率,一般取
;
根据上式结合题目给定数据,即可算出飞锤支架的生产纲领,进而确定出其生产类型。
取飞锤支架的生产类型中批量生产
2.2毛坯的种类和制造方法
飞锤支架的材料在产品设计时已经确定,在制订零件机械加工工艺规程时,毛坯的选择主要是选定毛坯的制造方法。
用于铸造的材料有灰铸铁、可锻铸铁、球墨铸铁、合金铸铁、铸钢、有色金属合金等。
由于飞锤支架选用QT600-2作为材料,加之零件形态以外圆为主,为了减少加工余量,提高劳动生产率,决定毛坯采用铸件。
熔模造型生产率较高、铸件精度高、表面质量与机械性能均好,使用于中批量生产。
该飞锤支架的生产类型为中批量生产,所以在铸件造型上采用熔模造型。
2.3零件个表面的加工方法
工件上的加工表面往往需要通过粗加工、半精加工、精加工等才能逐步达到质量要求,加工方法的选择一般应根据每个表面的精度要求,先选择能够保证该要求的最终加工方法,然后再选择前面一系列预备工序的加工方法和顺序。
通过对飞锤支架各加工表面的分析,根据表1-6至1-11选择各表面的加工方法。
表2各表面加工方法
加工表面
粗糙度要求
加工方法
飞锤支架右端面
3.2
粗铣—精铣
19mm圆柱面
1.6
粗车—半精车—精车
15mm圆柱面
12.5
粗车
11mm圆柱面
6.3
粗车—半精车
7mm孔
1.6
钻—粗铰—精铰
右圆台面
1.6
粗车—半精车—精车
左凹槽底面
6.3
粗铣—半精铣
左凹槽侧面
12.5
粗铣
6mm孔
6.3
钻—铰
6.5mm螺栓孔
12.5
锪
2.4各工序间加工余量
根据表1-6至1-11和2-15至2-40,将各加工表面的工艺路线、工序(或工步)余量,工序(或工步)尺寸及其公差、表面粗糙度填入表3中。
表3各工序间加工余量
加工表面
工步名称
工步余量
基本尺寸
公差等级
精度公差
工步偏差
粗糙度
19mm圆柱面
精车
0.9
IT8
0.033
1.6
半精车
0.5
IT10
0.052
6.3
粗车
0.9
IT12
0.21
12.5
毛坯
1.6
0.29
15mm圆柱面
粗车
0,9
IT12
0.18
12.5
毛坯
1.6
0.29
11mm圆柱面
半精车
0.7
IT10
0.043
6.3
粗车
0.9
IT12
0.18
12.5
毛坯
1.6
12.6
0.27
7mm孔
精铰
0.04
IT9
0.036
1.6
粗铰
0.16
IT10
0.058
6.3
钻
0.2
IT12
0.15
12.5
毛坯
实心
18通槽
粗铣
2
18
IT12
0.70
12.5
毛坯
1.6
16.4
4
2.4
6mm孔
铰
0.2
6
IT9
0.030
6.3
钻
5.8
5.8
IT12
0.12
12.5
毛坯
实心
6.5mm螺栓孔
锪
6.5
IT12
0.18
12.5
毛坯
实心
11mm端面
半精车
0.6
IT9
0.043
3.2
粗车
0.8
IT12
0.18
12.5
毛坯
1.6
12.6
2.2
2.5确定毛坯图尺寸
根据表3,得出毛坯尺寸。
利用电子图板绘出毛坯图,毛坯尺寸详见毛坯图
3.机械加工工艺规程设计
3.1拟定工艺路线
工艺路线的拟定包括:
定位基准的选择;各表面加工方法的确定;加工阶段的划分;工序集中程度的确定;工序顺序的安排。
考虑到实际经验的缺乏,加之时间的限制,主要进行了定位基准的选择、各表面加工方法的确定和工序顺序的安排工作
3.1.1定位基准的选择
拟定工艺路线的第一步是选择定位基准,为使所选的定位基准能保证整个机械加工工艺过程顺利进行,通常应先考虑如何选择精基准来加工各个表面,然后考虑如何选择粗基准把作为精基准的表面先加工出来。
飞锤支架的未加工面只有左面的凸台面,所以应先以左凸台面为粗基准加工右圆台面和右端面,然后以右圆台面加工
三个外圆面,钻孔
,粗铣通槽。
粗加工完成后,进一步进行半精加工和精加工。
3.1.2工序顺序的安排
根据表2各加工表面的加工方法和表3各工序间加工余量,考虑加工过程中定位基准的选择原则,确定工序顺序。
在工序顺序安排中,不仅要考虑机械加工工序,还应考虑热处理和辅助工序,遵循先基准后其他、先粗后精、先主后次、先面后孔的原则,最终确定的工序顺序详见表4,以此为依据,填写机械加工工艺过程卡片。
表4飞锤支架的加工工序
工序
工序名
供需内容
1
铸造毛坯
2
去锐边,尖角毛刺
3
备料热处理
4
车
粗车外圆面
至
,外圆面
至
,外圆面
至
5
铣
粗铣通槽至18
7
车
粗车右圆台面至11.7,半精车右圆台面至11
8
车
半精车
孔至
,精车
孔至
,半精车
孔至
10
钻
钻孔
至
,粗铰孔
至
,精铰孔至
11
钻
钻孔
至
,铰孔
至
12
锪
锪孔
至
,
至
13
钳工
却毛刺,尖角,锐边
14
检验
检验各尺寸
3.2
孔切削用量的计算
3.2.1钻孔工步切削用量的计算
背吃刀量的确定,取
=5.8mm。
进给量的确定,由表5-22,选取该工步每转的进给量f=0.05mm/s。
切削速度的确定,由表5-22,工件材料为铸铁、硬度度HBS=600的条件选择,切削速度可取为v=8m/min.由公式(5-1)n=1000v/πd可求得该工序钻头转速为n=493.3r/min,参照表4-9所列Z525型立式钻床的主轴转速,取转速n=545r/min。
再将此转速代入公式5-1,可求出实际转速v=nπd/000=545*3.14*5.8/1000=9.93m/min。
3.2.2铰孔工步切削用量的计算
背吃刀量的确定,取
。
进给量的确定,由表5-31,选取该工步每转的进给量f=0.30mm/r。
切削速度的计算,由表5-31,切削速度可取为v=4m/min。
由公式5-1,可求得该工序钻头的转速为n=212.3r/min。
参照表4-9所列Z525型立式钻床的主轴转速,取转速n=272r/min。
再将此转速代入公式5-1,可求出实际转速v=nπd/1000=272*3.14*6/1000=5.12m/min
3.3
孔基本工时的计算
3.3.1基本时间
的计算
钻孔工步,根据表5-41钻孔的基本时间可由公式:
求得。
式中l=6mm,
f=0.05m/s,n=545r/min。
将上述结果代入公式,则该工序的基本时间
。
铰孔工步,根据表5-41,铰圆柱孔基本时间公式:
求得。
式中的
由表5-42按
的条件查得
,而l=6mm,f=0.3mm/r,n=272r/min.将上述结果代入公式中计算出该工序的基本时间
3.3.2辅助时间
的计算
根据第五章第二节所述,辅助时间
与基本时间
之间的关系为
,可取
=0.15
,则各工序的辅助时间分别为:
钻孔工步的辅助时间:
铰孔工步的辅助时间:
。
3.3.3其他时间的计算
除了作业时间以外,每道工序的单件时间还包括布置工作的时间、休息与生理需要时间