工厂成本管理与控制资料大全.docx
《工厂成本管理与控制资料大全.docx》由会员分享,可在线阅读,更多相关《工厂成本管理与控制资料大全.docx(41页珍藏版)》请在冰豆网上搜索。
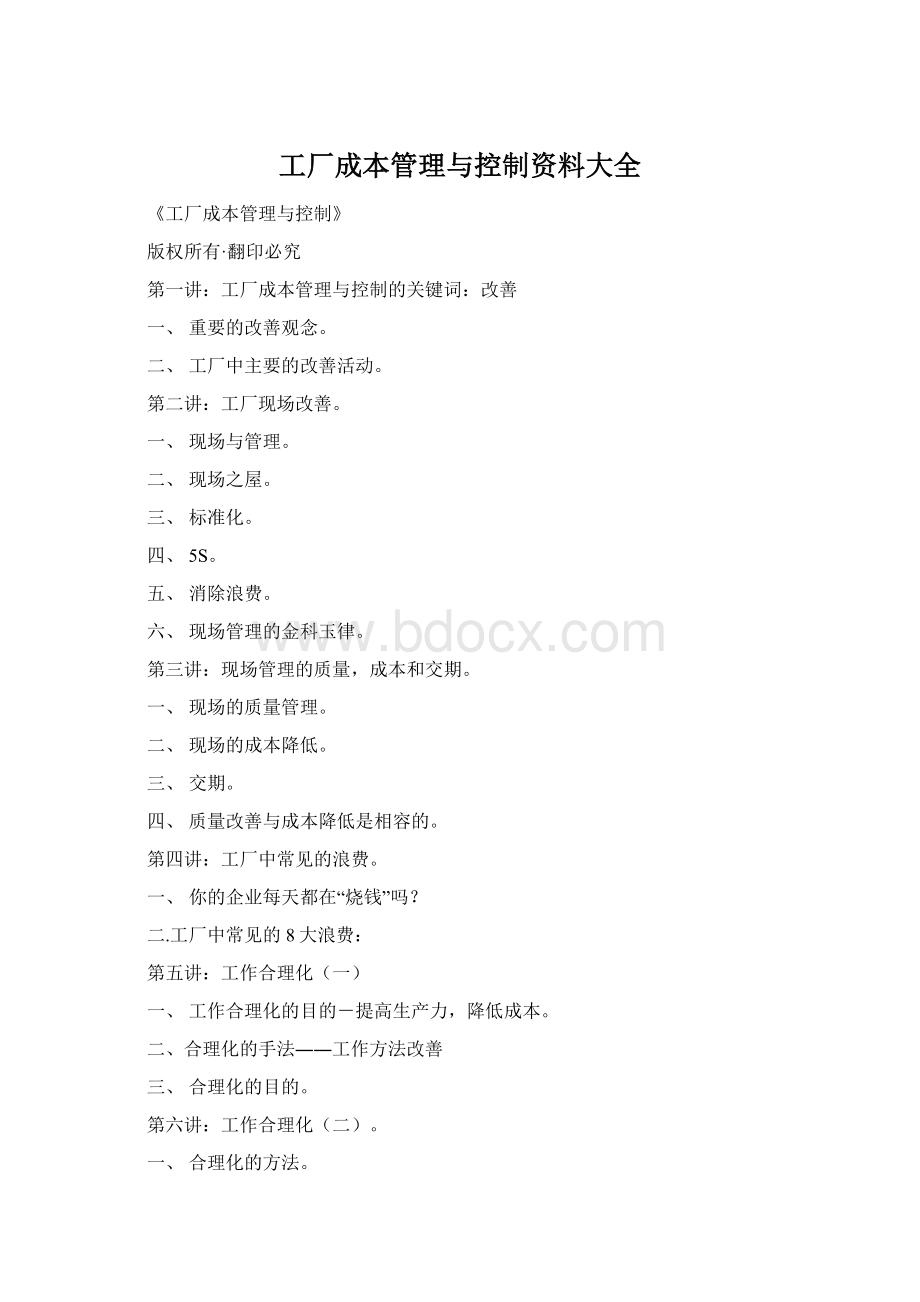
工厂成本管理与控制资料大全
《工厂成本管理与控制》
版权所有·翻印必究
第一讲:
工厂成本管理与控制的关键词:
改善
一、重要的改善观念。
二、工厂中主要的改善活动。
第二讲:
工厂现场改善。
一、现场与管理。
二、现场之屋。
三、标准化。
四、5S。
五、消除浪费。
六、现场管理的金科玉律。
第三讲:
现场管理的质量,成本和交期。
一、现场的质量管理。
二、现场的成本降低。
三、交期。
四、质量改善与成本降低是相容的。
第四讲:
工厂中常见的浪费。
一、你的企业每天都在“烧钱”吗?
二.工厂中常见的8大浪费:
第五讲:
工作合理化
(一)
一、工作合理化的目的-提高生产力,降低成本。
二、合理化的手法――工作方法改善
三、合理化的目的。
第六讲:
工作合理化
(二)。
一、合理化的方法。
二、合理化的内容。
三、合理化流程作业。
四、合理化组立线规划。
第七讲:
工作简化
(一)。
一、工作简化之意义。
二、工作简化之基本原则。
三、工作简化与生产力之关系。
第八讲:
工作简化
(二)
一、工作改善具体方法。
第九讲:
IE(工业工程)
(一)。
一、IE(IndustrialEngineering)的概念。
二、流程分析。
第十讲:
IE(工业工程)
(二)。
一、动作分析。
二、动作的经济原则。
第十一讲:
成本控制之库存管理。
一、库存的ABC分析及重点管理。
二、“零库存”的追求和意义。
第十二讲:
成本控制之采购管理。
一、准时制采购。
二、消除采购人员的“灰色收入”
第一讲:
工厂成本管理与控制的关键词:
改善
问题一、何为改善?
工厂中有哪些主要的改善活动?
一、主要的改善观念。
1、改善与管理。
“维持”是指从事于保持现有技术、管理及作业上标准活动,以及支持这些标准所需的训练和纪律。
在“维持”的功能下,管理部门要执行工作的指派,使每一个人都能依照标准的作业程序来工作;而“改进”则是以改进现有标准为目标的活动。
因此可以浓缩为一句箴言来表示:
维持和改进标准。
创新
改善
维持
改进
维持
高层管理高层管理
中层管理中层管理
督导管理督导管理
作业人员作业人员
管理的工作职能改进分为创新和改善
改进可再区分为“改善”和“创新”。
“改善”,是由于持续不断的努力,所产生的诸多的小步伐改进,而逐次累积而成。
“创新”则是借助大笔资源投资于新技术或设备,而产生戏剧性的变化的改进。
2、改善注意过程。
“改善”是着重在“过程为导向”的思考模式上,这是因为要改进“结果”,必须先改进“过程”。
预期的计划成果未能达成,表示其“过程”是失败的。
管理部门必须确认及改正这种“过程面”的错误。
“改善”是着重在“人际面”上的努力。
许多公司改善活动失败的原因,就在于轻“过程”。
在“改善”的过程中,最关键性的就是最高管理部门的承诺和参与。
3、PDCA/SDCA循环
在“改善的过程”中,第一个步骤就是要建立:
计划(PLAN)——执行(DO)——核查(CHECK)——处置(ACTION)——PDCA的循环,以PDCA循环作为“改善”持续运作的工具,以达成“维持标准”和“改进标准”的目标。
任何一个新的工作流程,在初期都是呈不稳定的状态。
开始进行PDCA改善时,必须先将任何现有的流程稳定下来。
此一稳定的过程称之为:
标准化(Standardize)→执行(DO)→查核(Check)→处置(Action)SDCA的循环:
见图
改进
改进
处置计划处置标准化
查核执行查核执行
计划→执行→查核→处置标准化→执行→查核→处置
PDCA循环SDCA循环
4、品质第一
就质量、成本和交期的主要目标而言,要经常将质量视为最优先的目标。
不管价格和交期的条件,对顾客具有多大的吸引力,若是产品或服务缺少了质量,仍无法竞争。
5、用数据说话
“改善”是一种解决问题的过程。
为了能正确地了解及解决问题,首先必须收集及分析相关的资料,以确定问题的真象。
没有确实的资料,就去尝试解决一个问题,与凭借感觉及预感是没什么两样的,这并不是科学或客观的方法。
6、下一流程就是顾客
所有的产品与工作,都是经历一连串的加工流程来完成,而每一道流程都有供应商及顾客。
流程A(供应商)提供材料或信息,供流程B(本流程)生产加工用,完成之后就送往下一流程C(顾客),继续加工下去。
要时常将下一流程视为顾客。
此一信念中的顾客,包含了两种形态的顾客:
内部的顾客(在公司内的)及外部的顾客(在外面的市场)。
二、工厂中主要的改善活动
1、TQC/TQM
●TQC为全面质量控制(TotalQualityContrll);
●TQM为全面质量管理(TotalQualityManagement)。
在TQC/TQM中,Q表示质量,具有其优先性,但仍含有其他的目标----即成本与交期。
T在TQC/TQM中,意味着“全面的”,包含组织内的每一个人,从最高阶层经中间管理阶层、现场督导人员,以及现场的作业人员,更进一步延伸至供应商、经销商及批发商。
T也意含着最高管理部门的领导及绩效,是TQC/TQM推行成功的要素。
2、及时生产方式(JIT)
JIT生产方式奠基于如下的观念:
产距时间(TaktTime,生产一个产品的目标时间)与周期时间(CycleTime)、一个流(One-PieceFlow)、后拉式生产(PullProduction)、自动化(Autonomation)、U型细胞式生产线及缩短换模时间。
要实现理想的及时生产方式,必须持续不断地实施一系列的改善活动,以消除现场中没有附加价值的工作。
3、全员生产保全(TPM)
全员生产保全(TotalProductiveMaintenance),TQM强调总体管理绩效及质量的改进,TPM则着重于设备质量的改进。
TPM是通过总体的预防保养制度,来延长设备的寿命,以追求设备效率的最大化。
就如TQM涵盖了公司内的每一个人,TPM也涵盖了工厂内的每一个人。
厂房环境维持的5S活动,是现场里另一主要的活动,也可视为TPM的前奏活动。
4、提案建议制度
是属于“个人导向”改善活动的一种,它的功能着重在激励员工的参与来提高士气。
其方法是鼓励员工多提出建议,无论他们的建议有多少。
5、小集团活动
在工作现场的环境里,在公司内以非正式、自愿性质组成团体,去执行特定工工作任务。
小集团活动最普遍的形态就是质量圈。
其成立的活动宗旨,不公限于质量方面的课题,而且也包含了成本、安全及生产力方面的课题。
质量圈是一种“团队导向”的改善活动。
第二讲工厂现场改善
问题二何为“走动管理”?
何为“三现主义”?
一、现场与管理
现场不仅是所有改善活动的场所,也是所有信息的来源。
不论管理阶层提供什么样的协助,都应是源自现场的特定需求。
一旦管理阶层不尊重、不珍视现场时,便会经常下达一些不适当的指示、要求和其他支援服务给现场,完全忽略了现场的实际需求。
这两种不同的现场观点:
一种管理阶层的角色在于提供支持给现场,现场位于管理结构的顶层(倒三角形),另一种管理阶层的角色在于提供政策和资源给现场,现场置于管理结构的底层(正三角形);就“现场-管理”的关系而言,具是具同等效用。
“现场”与“管理”共同分享同等的重要性。
“现场”通过提供产品或服务来满足顾客,而“管量”则是通过策略的设定和方针展开,以达成在现场的目标。
因此,改善的动力应是“由下而上”和“由上而下”,两者兼具。
二、
利润管理
现场之屋
质量及
安全管理成本管理物流管理
工人的产品及
作业情报设备材料
标准化
5S(良好的厂房环境维持)
消除浪费
团队合作士气强化自律
可视管理质量圈提案建议
现场管理之屋
三、标准化
每次一有问题或不正常现象发生时,管理人员须先加以调查,确定原因和修正现行标准,或实行新标准,防止问题再度发生。
标准化已成为现场改善不可或缺的一部分,而且也可作为日常改善的基准。
在现场,标准化指的是,将工程师所规定技术上和工程上的条件,转换成作业员天天所需要的作业标准。
这样的转换过程并不需要科技能力或高度的智慧能力,仅需要由管理部门拟定一个清晰的计划,依逻辑步骤展开下去即可。
四、5S
整理(SEIRI)
将工作场所的任何物品区分为有必要与没有必要的,除了有必要的留下来以外,其它的都清除掉;
目的:
●腾出空间,空间活用;
●防止误用、误送;
●塑造清爽的工作场所;
注意:
要有决心,不必要的物品应断然地加以处置,这是5S的第一步。
整顿(SEITON)
把留下来的必要用的物品依规定位置摆放,并放置整齐,加以标示。
目的:
●工作场所一目了然;
●消除找寻物品的时间;
●整整齐齐的工作环境;
●消除过多的积压物品。
注意:
这是提高效率的基础。
清扫(SEISO)
将工作场所内看得见与看不见的地方清扫干净,保持工作场所干净、亮丽。
目的:
●稳定品质
●减少工业伤害
清洁(SEIKETSU)
维持上面3S的成果
素养(SHITSUKE)
每位成员养成良好的习惯,并遵守规则做事,培养主动积极的精神。
目的:
●培养好习惯,遵守规则的员工;
●营造团队精神。
五、消除浪费
任何事情或活动,不会产生附加价值的均称为浪费。
在现场,仅有两种活动在进行:
“有附加价值的”和“没有附加价值的”。
当工人注视一部正在动作的自动机器时,并无任何附加价值产生。
一位维修工程师手上拿着工具,走了一段长距离的路,他也是在做没有附加价值的动作。
只有使用工具修理、保养或安装机器的动作,才算是有附加价值的。
六、现场管理的金科玉律
1、●问题(异常)发生时,要先去现场。
●检查现物(有关的物件)。
●当场采取暂行处置措施。
●发掘真正原因并将之排除。
●标准化以防止再发生。
2、走动管理
到工作现场去,在工作现场来回走动,发现问题,解决问题的管理方式。
工厂的现场管理一定是走动管理。
3、“三现主义”现时、现场(地)、现物(象)
当事情发生时,立即(现时)去现场,看现物(象)。
4、问5次为什么?
挖掘问题方法。
●“为何你将铁屑洒在地面上?
”
●“因为地面有点滑,不安全。
”
●“为什么会滑,不安全”
●“因为那儿有油渍。
”
●“为什么会有油渍?
”
●“因为机器在滴油。
”
●“为什么会滴油?
”
●“因为油是从联结器泄漏出来的。
”
●“为什么会泄漏?
”
●“因为联结器内的橡胶油封已经磨损了。
”
第三讲现场管理的质量、成本和交期
问题三现场管理的成本如何管理与控制
一、现场的质量管理
为了减少变异,管理部门必须建立标准,促使员工养成守纪律、遵守标准以及确保不良品不会流到下一位顾客。
大部分的质量问题可以用现场----现物的原则,以低成本、常识性的方法来解决。
“一下流程就是顾客”,指在同一公司内的内部顾客,绝不应把不合格品送至下一流程的顾客,以免造成他们的不便。
在现场,这样的想法有时就写成为“不接受、不制造、不流出”,当每一个人都能认同实现这个理念时,一个良好质量保证体系就能存在了。
二、现场的成本降低
1、改进质量
改进质量,事实上会带动成本降低。
质量在此系指管理人员及员工的工作过程的质量。
改进了工作过程的质量,其结果会使错误更少,不合格更少以及重工更少,缩短交期时间以及减少资源耗用,因而降低了营运总成本。
质量改进也是提高合格率的同义词。
2、改进生产力以降低成本
当以较少的(资源)“投入”,生产出相同的产品“产出”,或以相同的“投入”,生产出较多的“产出”时,生产力就改进了。
在此所称的“投入”系指像这些项目如人力资源、设施和材料。
“产出”意指像这些项目如产品、服务、收