锥齿轮减速器下箱体设计.docx
《锥齿轮减速器下箱体设计.docx》由会员分享,可在线阅读,更多相关《锥齿轮减速器下箱体设计.docx(32页珍藏版)》请在冰豆网上搜索。
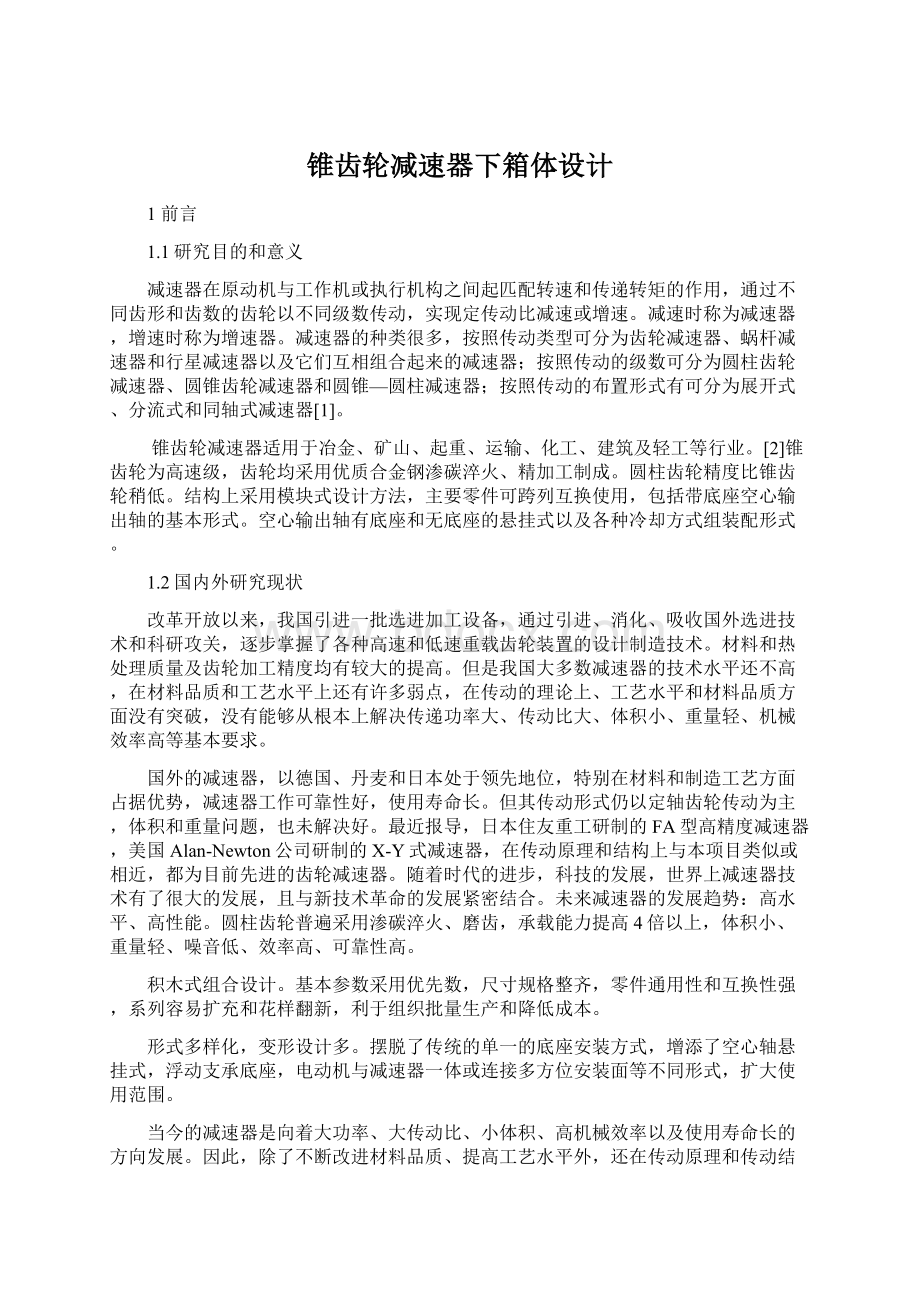
锥齿轮减速器下箱体设计
1前言
1.1研究目的和意义
减速器在原动机与工作机或执行机构之间起匹配转速和传递转矩的作用,通过不同齿形和齿数的齿轮以不同级数传动,实现定传动比减速或增速。
减速时称为减速器,增速时称为增速器。
减速器的种类很多,按照传动类型可分为齿轮减速器、蜗杆减速器和行星减速器以及它们互相组合起来的减速器;按照传动的级数可分为圆柱齿轮减速器、圆锥齿轮减速器和圆锥—圆柱减速器;按照传动的布置形式有可分为展开式、分流式和同轴式减速器[1]。
锥齿轮减速器适用于冶金、矿山、起重、运输、化工、建筑及轻工等行业。
[2]锥齿轮为高速级,齿轮均采用优质合金钢渗碳淬火、精加工制成。
圆柱齿轮精度比锥齿轮稍低。
结构上采用模块式设计方法,主要零件可跨列互换使用,包括带底座空心输出轴的基本形式。
空心输出轴有底座和无底座的悬挂式以及各种冷却方式组装配形式。
1.2国内外研究现状
改革开放以来,我国引进一批选进加工设备,通过引进、消化、吸收国外选进技术和科研攻关,逐步掌握了各种高速和低速重载齿轮装置的设计制造技术。
材料和热处理质量及齿轮加工精度均有较大的提高。
但是我国大多数减速器的技术水平还不高,在材料品质和工艺水平上还有许多弱点,在传动的理论上、工艺水平和材料品质方面没有突破,没有能够从根本上解决传递功率大、传动比大、体积小、重量轻、机械效率高等基本要求。
国外的减速器,以德国、丹麦和日本处于领先地位,特别在材料和制造工艺方面占据优势,减速器工作可靠性好,使用寿命长。
但其传动形式仍以定轴齿轮传动为主,体积和重量问题,也未解决好。
最近报导,日本住友重工研制的FA型高精度减速器,美国Alan-Newton公司研制的X-Y式减速器,在传动原理和结构上与本项目类似或相近,都为目前先进的齿轮减速器。
随着时代的进步,科技的发展,世界上减速器技术有了很大的发展,且与新技术革命的发展紧密结合。
未来减速器的发展趋势:
高水平、高性能。
圆柱齿轮普遍采用渗碳淬火、磨齿,承载能力提高4倍以上,体积小、重量轻、噪音低、效率高、可靠性高。
积木式组合设计。
基本参数采用优先数,尺寸规格整齐,零件通用性和互换性强,系列容易扩充和花样翻新,利于组织批量生产和降低成本。
形式多样化,变形设计多。
摆脱了传统的单一的底座安装方式,增添了空心轴悬挂式,浮动支承底座,电动机与减速器一体或连接多方位安装面等不同形式,扩大使用范围。
当今的减速器是向着大功率、大传动比、小体积、高机械效率以及使用寿命长的方向发展。
因此,除了不断改进材料品质、提高工艺水平外,还在传动原理和传动结构上深入探讨和创新,平动齿轮传动原理的出现就是一例。
减速器与电动机的连体结构,也是大力开拓的形式,并已生产多种结构形式和多种功率型号的产品。
目前,超小型的减速器的研究成果尚不明显。
在医疗、生物工程、机器人等领域中,微型发动机已基本研制成功,美国和荷兰近期研制的分子发动机的尺寸在纳米级范围,如能辅以纳米级的减速器,则应用前景远大。
1.3研究内容和方法
对于箱体的工艺规程设计应遵循一下原则:
可靠的保留零件图样上的所有技术要求的实现。
必须满足生产纲领的要求。
在满足技术要求和生产纲领要求的前提下,一般要求工艺成本最低。
尽量满足减轻工人的劳动强度,保证生产安全。
在查阅相关加工锥齿轮减速器下机体的书籍、期刊等资料,结合自己学过的金属工艺学、几何量公差与检测、机械设计等知识,并参考一些机械加工工艺人员所用的手册和资料,以在济南机床厂学习安排工艺规程的基础上,本着保证质量、降低成本的原则,根据零件的特点,设计出锥齿轮减速器下机体的工艺规程。
此锥齿轮减速器生产量较少,属小批量生产,因此机体本身采用焊接工艺加工制造。
在编制中,参考大重厂现行工艺,查阅资料,分析加工方法,制定出新的工艺规程:
包括加工工序安排,工序图,各工序使用的机床、夹具、刀具及切削用量和加工时间,并且绘制出零件图、工艺规程流程图,编写出设计说明书。
2工艺路线的确定
2.1毛坯的选择
下机体毛坯的选择是各零件的材料是Q235-A,由于是钢件,因此这些零件的毛坯是可以通过铸造加工出来的,而其他组成箱体壳部分可以直接用钢板焊接工艺完成。
熔炼金属,制造铸型,并将熔融金属浇入铸型,凝固后获得一定形状和性能的铸件的成形方法称为铸造。
[5]通过铸造能获得形状相当复杂的铸件,不仅可以获得十分复杂的外形,而且能获得一般机械加工难以加工的复杂内腔。
用较少的投资、较短的时间、较方便的工艺方法制造大批量的铸件,铸造的批量不限,从单件、小批,直到大量生产。
由于一般铸件金属组织比较粗大,容易产生缩孔、气孔、夹渣、裂纹等各种铸造缺陷,其力学性能比锻件低,承受动载荷和冲击载荷的能力较差,而且其生产过程中工序多,一些工艺过程不易控制,铸件质量不易稳定,另外铸造的生产条件差,劳动强度高。
Q235代表碳素结构钢,A表示质量等级。
碳素结构钢原称普通碳素钢结构钢,但1988年国家标准修订后,增加了C、D质量等级的优质钢。
碳素结构钢含碳量底(0.06%—0.38%),硫、磷含量较高。
选用这类钢通常在热轧空冷状态下使用,不但其塑性高,韧性和焊接性能好,而且市场价格较低,性能能够满足减速器箱体的使用要求,其使用状态下的组织为铁素体加珠光体。
碳素结构钢常以热轧板、带、棒及型钢使用,用量约占钢材总量的70%,适合于焊接、铆接、栓接等。
2.2工艺路线的确定
在一定的生产条件下,在保证质量和快速响应市场需求的前提下,获得最好的经济效益是制定工艺规程的基本原则。
制定工艺规程时,应追求技术上的先进性,经济上的合理性,生产的安全性,并积极推行绿色制造工艺。
2.2.1零件机加工工序顺序的确定:
1.加工阶段的划分:
机械加工工艺过程一般可分为粗加工、半精加工和精加工三个阶段。
有些零件表面要求有很高的精度要求时,需要光整加工阶段。
2.加工顺序的安排:
遵循先粗后精、先主后次、先基面后其他的原则。
对于箱体零件,遵循先面后孔的加工原则,即:
先加工平面后加工孔。
安排加工顺序还要考虑到车间设备的布置情况。
设备成机群布置时,应尽量把相同工种的工序安排在一起,避免工件在车间内往返流动。
3.热处理工序的安排:
为了消除内应力的热处理安排在粗加工后,精加工之前。
4.辅助工序:
划线工序一般应安排在机械加工前。
内、外表面粗加工及时效处理后即可安排清理型砂、毛刺。
零件加工后,最终检验前应安排清洗工序。
(一)下机体的零件加工工艺路线
01轴承座Ⅰ
(1)铸造
(2)粗铣侧面(3)铣缺口
02下料钢板
03下料钢板
04轴承座Ⅱ
(1)铸造
(2)粗铣侧面(3)铣缺口
05下料钢板
06下料钢板
07下料钢板
08轴承座Ⅲ
(1)铸造
(2)粗铣侧面(3)铣缺口
09连接板
(1)切割
(2)铣缺口
10下料钢板
11下料钢板
12下料钢板
13下料钢板
14下料钢板
15下料钢板
(二)下机体焊后整体加工工艺路线
16下料
17焊下机体并进行渗漏检验
18热处理(去应力退火)
19划线
20粗铣下机体
21粗镗下机体
22实效处理
23划线
24精铣下机体
25上、下机体合钻孔
26钳(将上、下机体把合,锥销打入锥销孔)
27划线
28半精镗轴承孔
29精镗轴承孔
30倒所有角
31精铣侧面和φ220孔端面
32精铣下机体右侧加工面
33划线:
划机体上其余各孔线
34钳工去毛刺
35检验
36渗漏试验
由于减速器箱体经过焊接加工工艺以后,箱体的焊接部位的组织结构等发生变化。
采用热处理的目的是为了改变刚的内部组织结构,消除铸件、锻件、焊接件及机械加工工件中的残余应力,以提高尺寸稳定性,防止工件变形和开裂,延长机器使用寿命的一种热处理方法。
在精加工或淬火前使用的热处理工艺方法,可以达到的:
1)降低硬度,以利于切削加工或其它种类加工;2)细化晶粒,提高钢的塑性和韧性;3)消除内应力,并为淬火工序做好准备。
3设计计算
3.1下机体的零件设计
1.轴承座ⅠTY6308.02-1材料:
Q235-A数量:
1单重:
19.33Kg总重:
19.33Kg
(1)铸造
重量19.33Kg≤80Kg由于是小批量生产精度等级为3重量偏差8%
确定加工余量
底面及侧面加工余量为5
(2)粗铣侧面
确定加工余量z=4.5确定切深ap=4.5
确定铣床:
龙门铣床X2010C(主轴转速n为50—630公比1.26)
确定铣刀:
不重磨硬质合金套式面铣刀
D=400B=80d=60z=16(v=175s=0.12t=6试刀)
材料:
YT15硬质合金
切削宽度:
B=0.6*D=240
切削速度:
v=
(3.1)
T耐磨时间t切削深度D铣刀直径B铣削宽度每齿进给量z铣刀齿数Sz
每齿进给量:
Sz=0.12
计算:
v=253m/min
n计=1000×v/(π×D)=253000/(3.14*400)=201n/min所以取n=252n/min
v实=π×D×n/1000=3.14*400*252/1000=316.5m/min
确定加工时间:
L1=0.5(D-22BD−)=40L2=5f=
×z=1.92mm/n
T基=(L+L1+L2)×i/(f×n)=(440+40+5)/(1.92*252)=1.0
T辅T基=1/4=0.25min
T服=3%(T基+T辅)=0.025min
T休=2%(T基+T辅)=0.038min
T单=T基+T辅+T服+T休=1.313min
(3)铣缺口
确定加工余量:
缺口深度为20确定切深ap=20
确定铣床:
X61W万能铣床(n为65-1800公比1.26)
确定铣刀:
凸半圆铣刀
D=85d=27B=20R=10z=10
刀片材料:
YT15
进给量:
Sz=0.1
计算:
V=
(3.2)
T耐磨时间t切削深度D铣刀直径B铣削宽度每齿进给量z铣刀齿数Sz
计算得出:
v=255.8m/min
n计=1000×v/(π×D)=958n/min取n=1015n/min
v实=π×D×n/1000=270m/min
确定加工时间:
按轮廓或仿形铣削:
L1=t+(0.5~2)取L1=22
非封闭轮廓铣削:
L2=1铣削轮廓的实际长度:
L=66
f=Sz×z=1
T基=(L+L1+L2)/(f×n)=0.088min
T辅=T基/4=0.022min
T服=3%(T基+T辅)=0.0033min
T休=2%(T基+T辅)=0.0022min
T单=T辅+T基+T休+T服=0.1155min
2.下料钢板10×50×155材料:
Q235-A数量:
1单重:
0.46Kg总重:
0.46Kg
3.下料钢板10×235×306材料:
Q235-A数量:
1单重:
4.6Kg总重:
4.6Kg
4.轴承座ⅡTY6308.02-2材料:
Q235-A数量:
1单重:
33.19Kg总重:
33.19Kg
(1)铸造
重量33.19Kg≤80Kg由于是小批量生产精度等级为3重量偏差8%
确定加工余量
底面及侧面加工余量为5
(2)粗铣侧面
确定加工余量z=4.5确定切深ap=4.5
确定铣床:
龙门铣床X2010C(主轴转速n为50—630公比1.26)
确定铣刀:
不重磨硬质合金套式面铣刀
D=400B=80d=60z=16(v=175s=0.12t=6试刀)
材料:
YT15硬质合金
切削宽度:
B=0.6*D=240
切削速度:
v=
(3.1)
T耐磨时间t切削深度D铣刀直径B铣削宽度每齿进给量z铣刀齿数Sz
每齿进给量:
Sz=0.12mm
计算:
v=253m/min
n计=1000×v/(π×D)=253000/(3.14*400)=201n/min所以取n=252n/min
v实=π×D×n/1000=3.14*400*252/1000=316.5m/min
确定加工时间L1=0.5(D-22BD−)=40L2=5
Sz=f×z=1.92mm/n
T基=(L+L1+L2)×i/(f×n)=(815+40+5)/(1.92*252)=1.8min
T辅=T基/4==0.45min0.068min
T服=3%(T基+T辅)=0.045min
T单=T基+T辅+T服+T休=2.36min
(3)铣缺口
确定加工余量:
缺口深度为20确定切深ap=20
确定铣床:
X61W万能铣床(n为65-1800公比1.26)
确定铣刀:
凸半圆铣刀
D=85d=27B=20R=10z=10
刀片材料:
YT15
进给量:
Sz=0.1mm
计算:
V=
(3.2)
T耐磨时间t切削深度D铣刀直径B铣削宽度每齿进给量z铣刀齿数Sz
计算得出:
v=255.8m/min
n计=1000×v/(π×D)=958n/minn取=1015n/min
v实=π×D×n/1000=270m/min
确定加工时间:
按轮廓或仿形铣削:
L1=t+(0.5~2)取L1=22
非封闭轮廓铣削:
L2=1铣削轮廓的实际长度:
L=66
f=Sz×z=1mm/n
T基=(L+L1+L2)/(f×n)=0.088min
T辅=基T/4=0.022min
T服=3%(T基+T辅)=0.0033min
T休=2%(T基+T辅=0.0022min
T单=T基+T辅+T服+T休=0.1155min
5.下料钢板10×70×180材料:
Q235-A数量:
2单重:
0.99Kg总重:
0.99Kg
6.下料钢板10×290×895材料:
Q235-A数量:
2单重:
12.6Kg总重:
12.6Kg
7.下料钢板10×70×135材料:
Q235-A数量:
2单重:
0.74Kg总重:
0.74Kg
8.轴承座ⅢTY6308.03-3材料:
Q235-A数量:
1单重:
33.19Kg总重:
33.19Kg
(1)铸造
重量33.19Kg≤80Kg由于是小批量生产精度等级为3重量偏差8%确定加工余量底面及侧面加工余量为5
(2)粗铣侧面
确定加工余量z=4.5确定切深ap=4.5
确定铣床:
龙门铣床X2010C(主轴转速n为50—630公比1.26)确定铣刀:
不重磨硬质合金套式面铣刀
D=400B=80d=60z=16(v=175s=0.12t=6试刀)
材料:
YT15硬质合金切削宽度:
B=0.6*D=240mm
切削速度:
v=
(3.1)
T耐磨时间t切削深度D铣刀直径B铣削宽度每齿进给量z铣刀齿数Sz
每齿进给量:
Sz=0.12mm计算:
v=253m/min
n计=1000×v/(π×D)=253000/(3.14*400)=201n/min所以取n=252n/min
v实=π×D×n/1000=3.14*400*252/1000=316.5m/min
确定加工时间L1=0.5(D-22BD−)=40L2=5f=Sz×z=1.92mm/n
T基=(L+L1+L2)×i/(f×n)=(815+40+5)/(1.92*252)=1.8min
T基=(L+L1+L2)×i/(f×n)=0.45min
T服=3%(T基+T辅)=0.068min
T休=2%(T基+T辅)=0.045min
T单=T基+T辅+T服+T休=2.36min
(3)铣缺口
确定加工余量:
缺口深度为20确定切深ap=20
确定铣床:
X61W万能铣床(n为65-1800公比1.26)
确定铣刀:
凸半圆铣刀D=85d=27B=20R=10z=10刀片材料:
YT15
进给量:
Sz=0.1mm
V=
(3.2)
T耐磨时间t切削深度D铣刀直径B铣削宽度每齿进给量z铣刀齿数Sz
计算得出:
v=255.8m/min
n计=1000×v/(π×D)=958n/min取n=1015n/min
v实=π×D×n/1000=270m/min
确定加工时间:
按轮廓或仿形铣削:
L1=t+(0.5~2)取L1=22
非封闭轮廓铣削:
L2=1铣削轮廓的实际长度:
L=66
f=Sz×z=1mm/n
T基=(L+L1+L2)/(f×n)=0.088min
T辅=T基/4=0.022min
T服=3%(T基+T辅)=0.0033min
T休=2%(T基+T辅)=0.0022min
T单=T基+T辅+T服+T休=0.1155min
9.连接板TY6308.03-4材料:
Q235-A数量:
1单重:
8.16Kg总重:
8.16Kg
(1)仿行切割加工出样料
(2)铣缺口
确定加工余量:
缺口深度为15确定切深ap=15
确定铣床:
X61W万能铣床(n为65-1800公比1.26)
确定铣刀:
凸半圆铣刀
D=85d=27B=20R=10z=10
刀片材料:
YT15
进给量:
Sz=0.1mm
计算:
V=
(3.2)
T耐磨时间t切削深度D铣刀直径B铣削宽度每齿进给量z铣刀齿数Sz
计算得出:
v=276m/min
n计=1000×v/(π×D)=1034n/min取n=1431n/min
v实=π×D×n/1000=382m/min
确定加工时间:
按轮廓或仿形铣削:
L1=t+(0.5~2)取L1=22
非封闭轮廓铣削:
L2=1铣削轮廓的实际长度:
L=23
f=Sz×z=1mm/n
T基=(L+L1+L2)/(f×n)=0.04min
T辅=T基/4=0.01min
T服=3%(T基+T辅)=0.0015min
T休=2%(T基+T辅)=0.001min
T单=T基+T辅+T服+T休=0.0525min
10.下料钢板10×290×306材料:
Q235-A数量:
1单重:
12.6Kg总重:
12.6Kg
11.下料钢板20×φ70材料:
Q235-A.F数量:
1单重:
0.32Kg总重:
0.32Kg
12.下料钢板18×40×120材料:
Q235-A.F数量:
1单重:
0.68Kg总重:
0.68Kg
13.下料钢板25×100×915材料:
Q235-A数量:
1单重:
18.35Kg总重:
18.35Kg
14.下料钢板10×260×915材料:
Q235-A数量:
1单重:
19Kg总重:
19Kg
15.下料钢板25×100×915材料:
Q235-A数量:
1单重:
18.35Kg总重:
18.35Kg
3.2下机体焊后整体精加工
下机体TY6336.04数量:
1单重:
204.58Kg总重:
204.58Kg
01.下料
02.焊下机体并进行渗漏检验
03.热处理(去应力退火)
04.划线
05.粗铣下机体
(1)粗铣底面
确定加工余量:
z=2
确定切深:
ap=2
确定铣床:
选用龙门铣床X2010C(主轴转n为50—630公比1.26)
确定铣刀:
选用不重磨硬质合金套式面铣刀
D=400B=80d=60z=16(v=175S=0.12t=6试刀)
确定刀片材料:
YT15切削宽度:
B=0.6×D=240
计算v=
(3.1)
T耐磨时间t切削深度D铣刀直径B铣削宽度每齿进给量z铣刀齿数Sz
铣刀每齿进给量:
Sz=0.1mm计算得出:
v=230m/min
n计=1000×v/(π×D)=230000/(3.14×250)=293n/min所以取n=318n/min
v实=π×D×n/1000=3.14×250×318/1000=250m/min
确定加工时间:
L1=0.5(D-22BD−)=25L2=4
f=Sz×z=1.92mm/n
T基=(L+L1+L2)×i/(f×n)=1.55min
T辅=T基/4=0.39min
T服=3%(T基+T辅)=0.058min
T休=2%(T基+T辅)=0.039min
T单=T基+T辅+T服+T休=2.037min
(2)粗铣接合面
确定加工余量:
z=3确定切深:
ap=3
确定铣床:
选用龙门铣床X2010C(主轴转n为50—630公比1.26)
确定铣刀:
选用不重磨硬质合金套式面铣刀
D=250B=63d=60z=12确定刀片材料:
YT15切削宽度:
B=0.6×D=150
计算:
v=
(3.1)
T耐磨时间t切削深度D铣刀直径B铣削宽度每齿进给量z铣刀齿数Sz
铣刀每齿进给量:
Sz=0.16mm计算得出:
v=230m/min
n计=1000×v/(π×D)=230000/(3.14×250)=293n/min所以取n=318n/min
v实=π×D×n/1000=3.14×250×318/1000=250m/min
确定加工时间:
L1=0.5(D-22BD−)=25L2=4
F=Sz×z=1.92mm/n
T基=(L+L1+L2)×i/(f×n)=1.70min
T辅=T基/4=0.42min
T服=3%(T基+T辅)=0.063min
T休=2%(T基+T辅)=0.0424min
T单=T基+T辅+T服+T休=2.225min
06.粗镗下机体
(1)粗镗φ180孔
确定加工余量:
z=5
确定切深:
ap=2.5镗至φ175
确定镗床:
T68卧式镗床(主轴转速n为20—1000公比1.26)
确定镗刀:
45º镗刀(镗通孔)镗刀材料:
W18Gr4V
确定进给量:
f=0.4mm/n
确定切削速度:
v=25m/min加冷却液
n计=1000×v/(π×D)=25000/(3.14×175)=46n/min所以取n=51n/min
v实=π×D×n/1000=3.14×175×51/1000=28m/min
确定加工时间:
L1=3L2=2采用游标卡尺测量L3=5
T基=(L+L1+L2)×i/(f×n)=8.4min
T辅=T基/4=2.1min
T服=3%(T基+T辅)=0.315min
T休=2%(T基+T辅)=0.21min
T单=T基+T辅+T服+T休=11.025min
(2)粗镗φ280孔
确定加工余量:
z=6确定切深:
ap=3镗至φ274
确定镗床: