模具制造工艺学.docx
《模具制造工艺学.docx》由会员分享,可在线阅读,更多相关《模具制造工艺学.docx(12页珍藏版)》请在冰豆网上搜索。
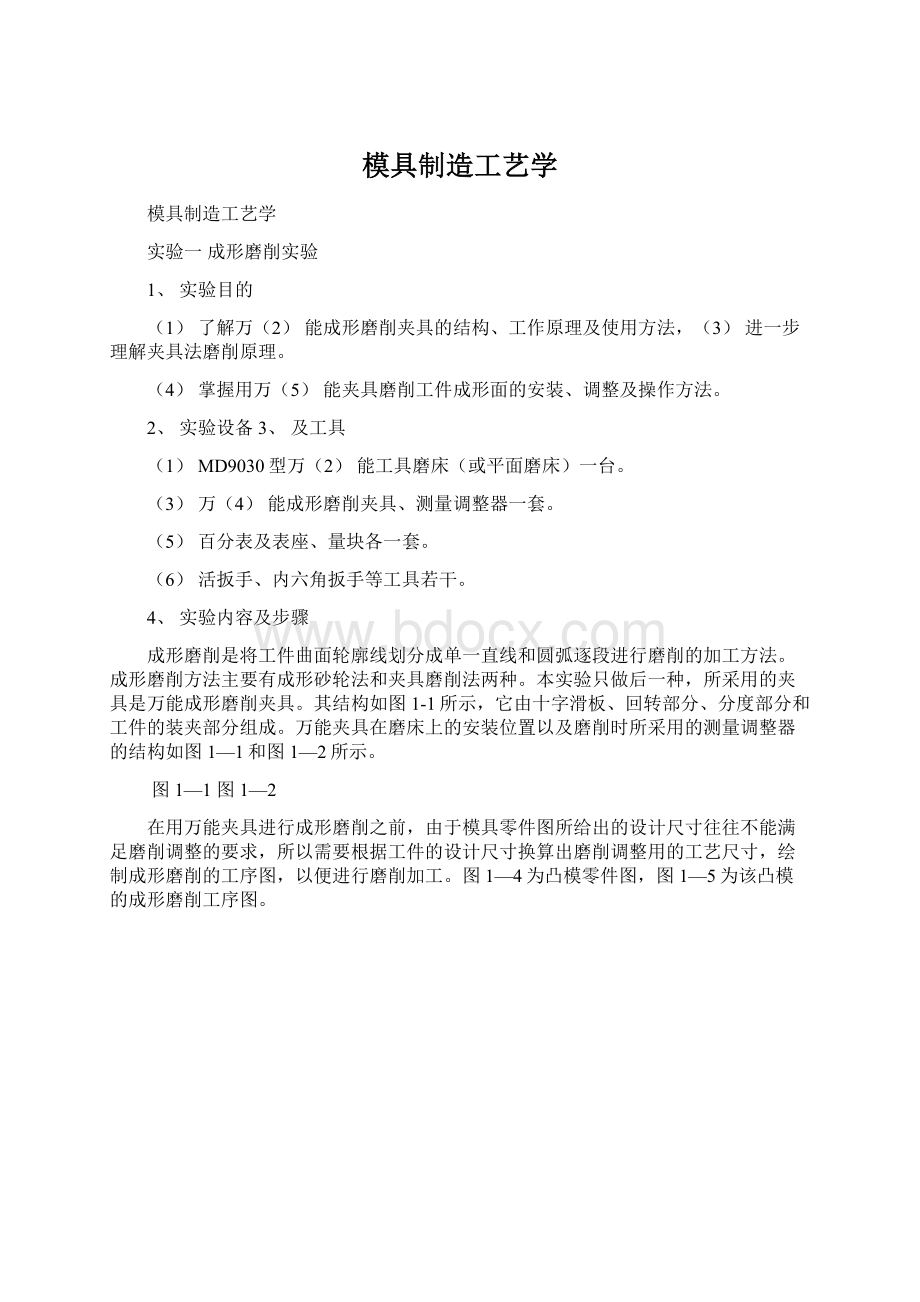
模具制造工艺学
模具制造工艺学
实验一成形磨削实验
1、实验目的
(1)了解万
(2)能成形磨削夹具的结构、工作原理及使用方法,(3)进一步理解夹具法磨削原理。
(4)掌握用万(5)能夹具磨削工件成形面的安装、调整及操作方法。
2、实验设备3、及工具
(1)MD9030型万
(2)能工具磨床(或平面磨床)一台。
(3)万(4)能成形磨削夹具、测量调整器一套。
(5)百分表及表座、量块各一套。
(6)活扳手、内六角扳手等工具若干。
4、实验内容及步骤
成形磨削是将工件曲面轮廓线划分成单一直线和圆弧逐段进行磨削的加工方法。
成形磨削方法主要有成形砂轮法和夹具磨削法两种。
本实验只做后一种,所采用的夹具是万能成形磨削夹具。
其结构如图1-1所示,它由十字滑板、回转部分、分度部分和工件的装夹部分组成。
万能夹具在磨床上的安装位置以及磨削时所采用的测量调整器的结构如图1—1和图1—2所示。
图1—1图1—2
在用万能夹具进行成形磨削之前,由于模具零件图所给出的设计尺寸往往不能满足磨削调整的要求,所以需要根据工件的设计尺寸换算出磨削调整用的工艺尺寸,绘制成形磨削的工序图,以便进行磨削加工。
图1—4为凸模零件图,图1—5为该凸模的成形磨削工序图。
图1—3图1—4
模具零件在进行成型磨削之前,应先用其它加工方法完成定位基面(上、下平面)的精加工,成型面的粗加工、半精加工、成型面周边均匀留0.08mm的磨削量。
对于图1—4所示的凸模,为了便于成形磨削时的安装,还需在端面钻、攻两个直径为M8mm、深为10mm的螺孔,然后在实验教师的指导下,按下列步骤进行磨削:
1.装夹工件
利用凸模端面上两个螺孔,用螺钉和垫套将凸模装夹在装件盘上。
按图1-6校正工件,是工件的工艺坐标轴与十字滑板导轨方向平行,调好后将凸模紧固在装件盘上。
然后移动十字滑板,使各工艺中心依次与分度转盘的回转轴线重合,用百分表和测量调整器检查各处的磨削余量是否足够,如图1-7a所示,在测量调整器上放置尺寸为50mm+44.985mm的量块,使百分表在量块上面对“0”,然后将百分表移至工件的被测表面“1”上,调整工件使其读数等于磨削余量;再将工件顺时针旋转90°,使平面“2”处于水平位置(图1-7b),降低量块高度到50mm—28.015mm,以此调整好工艺中心O2的位置;转动工件,用百分表和测量调整器检查R15.985mm、R65.985mm及斜面“3”是否有足够的磨削余量。
图1—6图1—7
以平面“1”“2”为测量基准,把工艺中心O1、O3依次调到分度盘回转轴线上,用百分表和测量调整器检查其余各表面的磨削余量是否足够、均匀,若工件上某些部位无余量或余量不均匀,还需作补充调整,直至各处余量调匀为止。
2.磨削加工
(1)磨削基准面“1”、“2”和R16.015mm的凹圆弧面:
将工艺中心O1调至分度盘的回转轴线上,先后使平面“1”、“2”处于水平位置,磨削两平面至规定尺寸,如图1-8a、b所示。
磨平面“2”时,在离与凹圆弧的切点2~3mm处停止磨削,留作磨削切点处余量。
将砂轮修整成半径小于工件凹圆弧半径的圆弧面,用回转法磨R16.015mm的凹圆弧至规定尺寸(图1-8c)。
在磨削中,当平面“2”转至水平位置时,停止转动,水平移动十字滑板,磨掉切点余量,使切点处连接平滑。
(2)磨削R65、985mm、R15.985mm的圆弧面和斜面“3”:
将工艺中心O2调至分度盘的回转轴线上,重新将砂轮修平,用回转法磨R65.985mm的圆弧面至规定尺寸,如图1-8a所示。
使平面“3”处于水平位置,磨削平面“3”至规定尺寸,如图5—15b所示。
控制转角α=21°6′时,垫在分度盘圆柱下的量块尺寸为:
h1=h—(D/2)sin21°6′—d/2
用回转法磨削R15.985mm的圆弧至规定位置尺寸,如图1-8c所示。
为防止磨坏相邻面,在磨削时需要控制回转角α1和α2。
控制转角α1和α2时,垫在分度盘圆柱下的量块尺寸为
图1—8
h1=h—(D/2)sin(α1—90°)
h2=h+(D/2)sin(90°—α2)
(3)磨削R16mm的凸圆弧面:
将工艺中心O3调至分度盘回转轴线上,用回转法磨削R16mm圆弧面至规定尺寸,如图1-9所示。
为了防止磨坏相邻面,需要控制磨削回转角α3和α4。
控制转角α3和α4所用量块的尺寸为
h1=h—(D/2)sin21°6′—d/2
h2=h+(D/2)sin21°6′—d/2
以上式中h—夹具主轴中心至量块支承面的距离;
D—正弦圆柱中心所在圆的直径;
d—正弦圆柱的直径。
3.整理实验现场
图1—9
成形磨削完成后,卸下工件,收存量块、百分表及测量调整器,清理工作场所,关闭机床。
四、实验报告
(1)确定计算坐标
(2)系(用简图表示),(3)并标(4)注各圆弧的圆心代号及各角度代号。
(5)计算确定各处磨削所需要的加工调整参数(移动坐标(6)系X、Y值、各角度值)。
实验二数控线切割编程及加工实验
一、实验目的
(1)了解数控线切
(2)割机床的结构、工作原理及操作方法。
(3)掌握数控编程的基本方法;学会使用穿孔机进行纸带程序穿孔;并在线切(4)割机床上验证所编零件线切(5)割加工程序是否正确。
(6)了解工件的装夹过程及找正方法。
(7)了解线切(8)割加工工件的工艺性。
二、实验设备、工具及毛坯
(1)DK7725型数控线切
(2)割机床一台。
(3)BDZ—3型纸带穿孔机一台。
(4)标(5)准五孔程序纸带一卷。
(6)活扳手、游标(7)卡尺各一把。
(8)毛坯(材料:
T10,(9)尺寸:
100mm×50mm×4mm)一块。
三、实验内容及步骤
首先由实验教师介绍数控线切割机床的主要部件的结构及作用,机床各按键和旋钮的功用,工件的装夹方法以及加工的操作过程。
然后在实验教师的指导下,学生按下列步骤进行实验:
(1)接通电源、给控制柜和机床供电;把工件放到机床工作台上,
(2)找正加工位置,(3)并将其夹紧;装好电极丝(钼丝)。
(4)将预先编好的工件线切(5)割加工程序,(6)在穿孔机上进行纸带穿孔,(7)并把穿好孔的纸带放在光电读入机上进行程序检验(对于封闭曲线轮廓,(8)全曲线程序运行完毕应回零位,(9)即回零检验)。
然后将线切(10)割加工程序存入控制柜,(11)也可在机床控制柜的键盘上,(12)将切(13)割程序直接输入。
(14)根据加工工件的材料、结构特点及技术要求,(15)预选一组电规准(工作电压、脉冲电流、脉冲宽度、脉冲频率等),(16)并调好并调好相应玄钮的档位。
(17)起动走丝电动机,(18)接通脉冲电源,(19)找正钼丝起切(20)点的位置,(21)然后记下滑板进给(X、Y方向)手柄上刻度的初始值。
(22)开动切(23)削液泵,(24)按下执行键,(25)开始切(26)割加工。
加工时,(27)要注意观察各项电参数是否正常,(28)并通过相应的调整旋钮进行调节,(29)使加工过程趋于稳定,(30)但要防止调节量过大,(31)以免造成断丝。
对于切割中途需要换丝或装丝时(当断丝或改变起切点位置时)不要用手动进给方式移动工作台,而应采用程序控制的机动快速进给来完成,以保持切割程序运行的连续性。
(32)切(33)割完毕,(34)按操作要求关闭机床。
(35)检测工件。
(36)整理实验现场,(37)填写实验报告。
四、实验报告
1.工件图
2.加工条件记录
工件材料:
坯料尺寸:
钼丝直径:
单边放电间隙:
电规准:
工作电压:
工作电流:
脉冲宽度:
脉冲频率:
3.分析计算结点坐标
(1)计算补偿量,确定钼丝中心运动轨迹。
补偿量:
(2)确定计算坐标系,并标注在图上。
(3)标注结点名称,计算结点坐标值;标注各圆弧圆心(用O1、O2、O3代表)并计算其坐标值;将各结点及圆心坐标值填入表5—15中。
表2—1结点、圆心计算坐标值
点
X
Y
点
X
Y
A
H
B
I
C
J
D
K
E
O1
F
O2
G
O3
(4)编写线切割加工程序,并填入表2—2中(学生应在实验前完成编程工作)。
表2—2线切割程序单
序号
线段
各线段对应的程序
备注
1
2
3
4
5
6
7
8
9
10
11
12
13
14
15
16
17
18
19
20
5.根据现场观察,画出能够反映机床总体构成和加工原理的示意图。
实验三电火花成形加工实验
一、实验目的
(1)了解电火花成形机床的组成、工作原理及操作方法。
(2)了解平动头的作用及工作原理;掌握平动量的调整方法。
(3)验证极性效应特性。
(4)了解轴向放电间隙的控制方法。
(5)了解电规准变化对加工质量及加工速度的影响。
(6)了解不同(7)电极材料的电火花加工工艺性。
二、实验设备及工具
(1)D6140A—1型电火花成型机床一台。
(2)工具电极(尺寸为φ10mm×100mm的紫铜电极、石墨电极、钢电极)各一根。
(3)加工试件(材料为Cr12,(4)尺寸为90mm×30mm×10mm上、下平面的表面粗糙度Rα为3.2μm)一块。
(5)游标(6)卡尺和活动扳手各一把。
三、实验内容及步骤
首先由实验教师介绍电火花加工机床的主要构成,机床和控制柜上各旋钮及按键的功用,工件的装夹,平动量的调节以及加工的操作过程。
然后由学生在实验教师的指导下,按下列步骤进行实验。
(1)将试件和工具电极分别安装在工作台和主轴头(或平动头)上,按要求找正它们之间的位置关系,再将控制柜的两脉冲电源分别接到试件和工具电极上(或接到与它们相连的其它导电零件上)。
(2)起动介质循环系统,使介质液面高于加工面,达到规定高度(按机床说明书规定),然后开启脉冲电源,根据加工条件选择电规准,并调整好相应旋钮的档位,按下加工执行键,用手动缓慢下移工具电极,使之进入加工区,待发现有火花出现时转入电极进给的自动控制,加工即可开始。
加工时注意观察主轴头、加工区和控制柜上各显示仪表的工作情况及彼此之间变化的关系,记下加工参数,填入表中。
(3)三根直径相同但材料不同的工具电极在同样的电规准条件下,对同一块钢板的三处依次进行电火花加工,主轴垂直进给距离均为5mm(以工具电极端面刚与工件表面接触开始,用百分表读数)。
观察它们的加工状况有何不同,待加工结束之后,分别观察三个工具电极的耗损情况及表面粗糙度的变化情况,并测量试件的型孔直径和深度,将观察和测量的结果记入表中。
(4)将平动头安装在主轴上,再将工具电极装在平动头上,找正加工位置,开动平动电动机,观察电极在平动头上的运动情况,旋转调节手柄逐渐改变平动量,学会平动量的调节方法。
将平动量调整为零,先用紫铜电极对试件进行型孔的粗加工(电规准按粗规准选择),然后将粗规准变换到精规准,开启平动机构,并慢慢地增加平动量,直至有火花出现为止,继而转入平动法精加工型孔,记下此时的规准转换量和平动量,填入表中。
(5)用一根石墨电极,在粗、中、精三种不同电规准的加工条件下,分别在同一块试件上进行三处进行电火花加工,主轴垂直进给距离为5mm,待加工完后,分别观察粗、中、精加工试件表面粗糙度并测量其尺寸,记入表中。
(7)关闭机床,(8)清理实验现场,(9)整理实验记录,(10)填写实验报告。
四、实验报告
(1)在同
(2)一电规准条件下,(3)不同(4)电极材料电加工性能的测试记录见书中表。
表3—1试件及工具电极电加工表面及尺寸测量
工作电压U/V
工作电流I/A
脉冲宽度t/μs
工作频率f/Hz
测试电极
电极测量
工件测量
表面粗糙度
加工时间t/min
直径d/mm
高度h/mm
直径d1/mm
高度h1/mm
(大、中、小)
钢
紫铜
石墨
(5)平动法加工型孔的电规准及平动量选择见书中表。
表3—2电规准与平动量关系
工作电压U/V
工作电流I/A
脉冲宽度t/μs
工作频率f/Hz
平动量△/mm
粗规准
精规准
(3)同一电极材料在不同电规准条件下的电火花加工性能测试记录见书中表。
表3—35试件电加工表面及尺寸测试
规准
工作压力U/V
工作电流I/A
脉冲宽度t/μs
工作频率f/Hz
试件测量
表面粗糙度
直径d1/mm
高度h1/mm
大、中、小
粗
中
精