操作窑外分解窑系统的若干体会.docx
《操作窑外分解窑系统的若干体会.docx》由会员分享,可在线阅读,更多相关《操作窑外分解窑系统的若干体会.docx(6页珍藏版)》请在冰豆网上搜索。
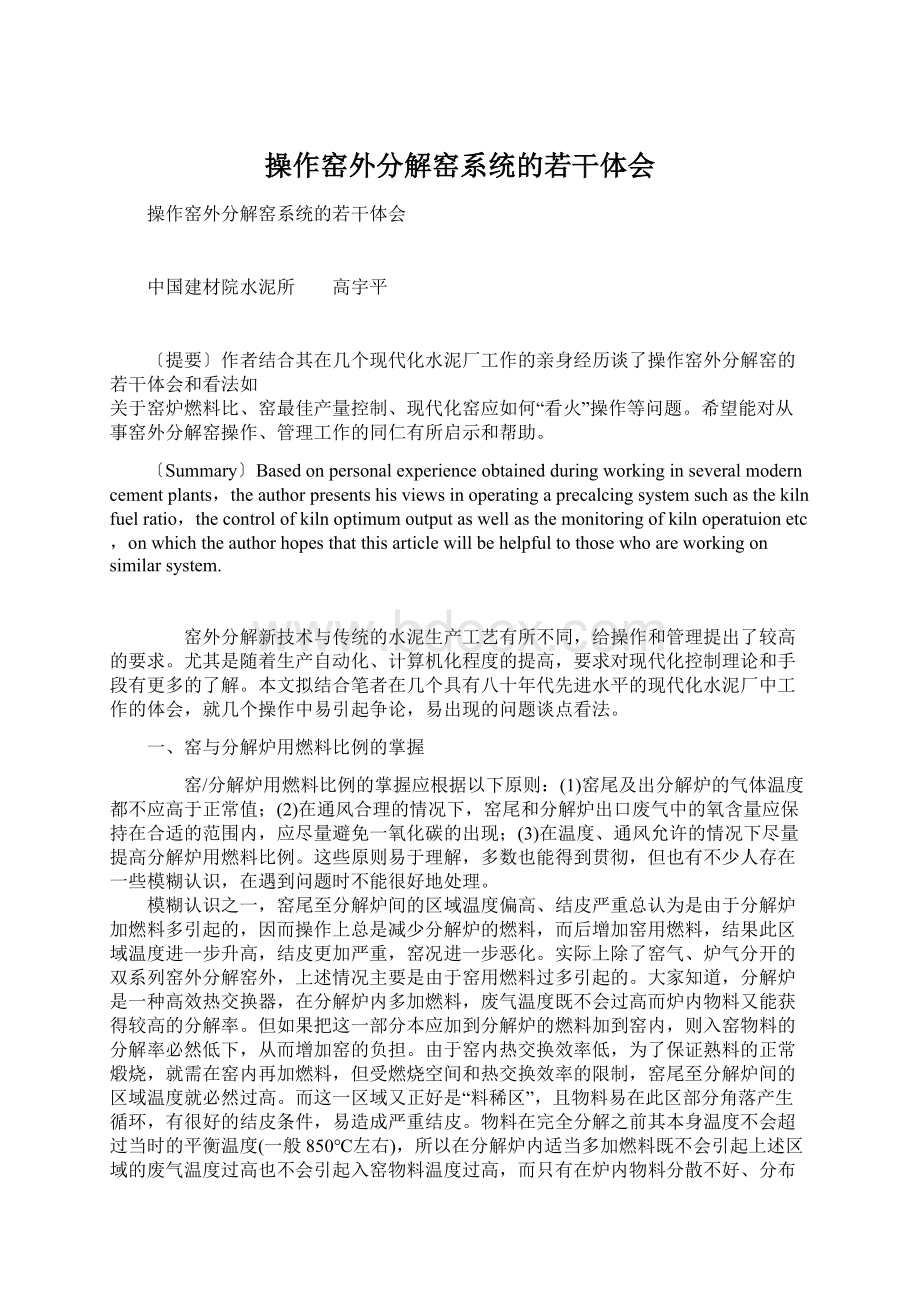
操作窑外分解窑系统的若干体会
操作窑外分解窑系统的若干体会
中国建材院水泥所 高宇平
〔提要〕作者结合其在几个现代化水泥厂工作的亲身经历谈了操作窑外分解窑的若干体会和看法如
关于窑炉燃料比、窑最佳产量控制、现代化窑应如何“看火”操作等问题。
希望能对从事窑外分解窑操作、管理工作的同仁有所启示和帮助。
〔Summary〕Basedonpersonalexperienceobtainedduringworkinginseveralmoderncementplants,theauthorpresentshisviewsinoperatingaprecalcingsystemsuchasthekilnfuelratio,thecontrolofkilnoptimumoutputaswellasthemonitoringofkilnoperatuionetc,onwhich theauthorhopesthatthis article will be helpfultothosewhoareworkingonsimilarsystem.
窑外分解新技术与传统的水泥生产工艺有所不同,给操作和管理提出了较高的要求。
尤其是随着生产自动化、计算机化程度的提高,要求对现代化控制理论和手段有更多的了解。
本文拟结合笔者在几个具有八十年代先进水平的现代化水泥厂中工作的体会,就几个操作中易引起争论,易出现的问题谈点看法。
一、窑与分解炉用燃料比例的掌握
窑/分解炉用燃料比例的掌握应根据以下原则:
(1)窑尾及出分解炉的气体温度都不应高于正常值;
(2)在通风合理的情况下,窑尾和分解炉出口废气中的氧含量应保持在合适的范围内,应尽量避免一氧化碳的出现;(3)在温度、通风允许的情况下尽量提高分解炉用燃料比例。
这些原则易于理解,多数也能得到贯彻,但也有不少人存在一些模糊认识,在遇到问题时不能很好地处理。
模糊认识之一,窑尾至分解炉间的区域温度偏高、结皮严重总认为是由于分解炉加燃料多引起的,因而操作上总是减少分解炉的燃料,而后增加窑用燃料,结果此区域温度进一步升高,结皮更加严重,窑况进一步恶化。
实际上除了窑气、炉气分开的双系列窑外分解窑外,上述情况主要是由于窑用燃料过多引起的。
大家知道,分解炉是一种高效热交换器,在分解炉内多加燃料,废气温度既不会过高而炉内物料又能获得较高的分解率。
但如果把这一部分本应加到分解炉的燃料加到窑内,则入窑物料的分解率必然低下,从而增加窑的负担。
由于窑内热交换效率低,为了保证熟料的正常煅烧,就需在窑内再加燃料,但受燃烧空间和热交换效率的限制,窑尾至分解炉间的区域温度就必然过高。
而这一区域又正好是“料稀区”,且物料易在此区部分角落产生循环,有很好的结皮条件,易造成严重结皮。
物料在完全分解之前其本身温度不会超过当时的平衡温度(一般850℃左右),所以在分解炉内适当多加燃料既不会引起上述区域的废气温度过高也不会引起入窑物料温度过高,而只有在炉内物料分散不好、分布不均的情况下才会造成炉内及其出口废气温度高。
因此,当窑尾及其上升管道温度高时,不能轻易认为是分解炉燃料加多了,而应认真分析原因,采取正确操作方法。
通常只要逐步减少些窑用燃料同时将其减少量的一部分增加到分解炉内,情况就会逐渐好转。
模糊认识之二,烧成温度低熟料欠烧总认为是窑用燃料少造成的。
即使当窑的燃烧能力已到极限时,仍增加窑燃料用量,结果造成窑头温度进一步降低,窑尾系统温度则过高。
这一错误的操作方法还会引起窑内还原气氛,造成系统结皮严重、结长厚窑皮甚至结圈。
窑内通风及燃烧能力是有一定限度的,在燃烧空气无富余的情况下,增加燃料窑头温度不仅不会提高反而会降低。
这一道理一般都懂,但有一部分人一遇到窑头温度低却总是增加窑头燃料,尤其是在喂料量并不多,燃烧空气并不富余的情况下,仍往窑内多加燃料。
笔者认为窑用燃料的增加有一个最简单的原则,即只要窑尾废气中有一氧化碳存在,则在调整系统状态使一氧化碳消失之前,不应该增加窑用燃料。
所以如遇到窑头温度低的情况,应该首先分析其原因,如燃烧空气不足,应设法增加通风量;如风机已开到极限,则应分析是否下料量大了,是否三次风闸板没调整好,是否窑内结圈,并进行适当的调整和处理:
如是入窑分解率低,则应增加分解炉燃料而非窑头燃料;如是冷却机效率低二次风温低,则应对冷却机进行处理。
总之要具体情况具体分析,而不能一味增加窑头用燃料,结果适得其反。
二、系统通风的控制和调节
在窑、炉燃料用量及喂料量合理的情况下给燃料提供适当的燃烧空气是系统通风的控制原则。
一般是以窑尾、分解炉和预热器出口的废气分析为主要依据对系统通风进行控制,这三个部位的氧含量一般应分别控制在2%、2%~3%、3%~4%,同时应尽量避免一氧化碳的出现。
控制方法主要有调节主排风机转速(或风门开度)、调节三次风闸板开度等。
靠调节一次风量、冷却机鼓、排风量和旁路风量等也可调整系统通风情况。
笔者发现,当操作有旁路系统的窑外分解窑时,有相当一部分操作员在旁路废气中有CO,需降低其含量时,不是增加旁路量而是相反,结果造成窑尾废气中CO进一步增加,窑内还原气氛进一步加剧,窑况进一步恶化。
旁路内的CO一般来自窑尾(只有当分解炉烧油而油嘴又结焦滴油时或烧煤而煤由于喂入不均塌料时旁路CO才会来自分解炉),而且由于旁路废气取样装置一般都安装在旁路混合室之后,所以其CO含量值比起窑尾中的要小得多。
当旁路废气中有CO存在时说明窑尾CO更多,这时应采取包括增加旁路放风量在内的调整措施而绝不应该减少旁路放风量。
三、窑外分解窑绝不是产量越低越好烧
窑外分解窑的分解炉、窑尾上升管道、各级预热器及其连接管道等都是按一定的气流速度设计的,以保证物料能处于悬浮状态、能随气流运动并有较高的分离效率等。
在设备规格已定的情况下,各处风速取决于系统用风量和喂料量。
对应于系统各处最佳风速有一个相应的最佳喂料量。
从这个意义上讲,窑的产量低于或高于这一最佳产量都不好。
产量过高,强制煅烧的害处是众所周知的,而产量过低,则会由于风速低产生下列后果:
1.物料易在系统内堆积并在适当条件下塌落
当各处风速低时,物料易在预热器、分解炉内部的一些小平台、角度小的锥体等部位堆积,堆积到一定程度当系统风速有所变化时,积料就会失去稳定,塌入气流中。
由于风速低,这些大大超过正常量的物料不可能均匀地分散于气流中,而是在没有进行适当热交换的情况下塌入窑内并很快窜入烧成带。
这一过程尽管时间短但却会严重干扰窑的热工制度,带来烧成温度突然降低,熟料短期内生烧;窑内瞬间通风不畅,出现还原气氛;窑内各带的长度和部位发生变化,引起火砖、窑皮受损;放热反应带突然前移,产生后结圈等严重后果。
在带有旁路放风系统的窑上,由于塌料一般都经过旁路引出口,所以塌料时还会引起旁路灰量增加、效率下降。
一般刚开窑时或因其它原因窑产量低时,窑况容易波动。
表现为负压表上下波动频繁、窑传动电流(或扭矩)无法稳定,烧成温度忽高忽低等。
这些现象就是由塌料引起的。
2.物料分散情况不好
在预热器风管和分解炉中物料均匀地分散悬浮于气流之中,传热效率才高,但如果喂料量低,系统通风量少,风速低,则各处的分散效果都不会好,从而造成系统热效率低、易堆积和塌料。
窑在低产量时热耗高除了单位熟料的散热比例大外,另一个原因就是物料分散不好,热量没有得到充分的利用。
3.物料易过热,预热器易堵塞
在喂料量低时,由于系统吸热体少,平衡温度易向高的方向发展。
尤其当系统出现积料时,悬浮于热气流中的物料量少于当时与燃料平衡的量,从而物料易过热,易粘附于预热器或下料管等处形成结皮。
低喂料量时为了对付窑况波动,燃料加入量都高于正常需量,所以系统就更易过热、结皮甚至堵塞。
预热器的堵塞易发生在窑低产时,原因就在于此。
所以,窑产量应有一个最佳值它随物料的易烧性、旁路量、燃烧质量等情况而变化,应在操作中体会决定。
窑在开窑加料初期应逐步增加喂料量,但应尽量避免拖长低喂料量阶段。
只要很好地掌握好燃料、喂料、风量的关系,使系统达到合理的热平衡,即使规模很大的窑在一个小时之内也能加到最佳产量(有时是最高产量)。
笔者操作的日产3400吨的窑,在已有正常窑皮的情况下从开始加料到最高产量可在40分钟内完成,系统无异常情况发生。
笔者还发现,一般当到最高产量的70%时,窑况就已变得容易稳定。
如日产3400吨的窑当喂料量大于180吨/时时,就基本上不发生塌料现象了。
因此,操作这样的窑应尽量避免在此产量以下运转。
四、不是所有结皮都有害
窑尾、分解炉、预热器及它们的各连接管道内在过热和有害成分含量高的情况下可产生结皮。
结皮可缩小物料、气流的有效通过空间,阻碍物料流动甚至引起堵塞;结皮还可引起物料入窑处的通道不畅,造成物料飞扬、在上升管道循环、加剧结皮、增加系统通风阻力。
但笔者认为,并不是所有结皮都有害,而是大部分结皮有害,一部分结皮无害,有的结皮还可能有利。
一般在本应光滑的表面上、在原已狭窄的通道内的结皮都是有害结皮。
如下料管、预热器锥体、分解炉燃烧区域及其上部、窑尾斜坡及窑尾缩口等处的结皮。
这些地方的结皮阻碍物料和气流的流动甚至可引起堵塞;减少了燃烧和热交换空间。
而一些部位的结皮,如方形管道内四角上并不十分大的结皮、各气体管道中气流流动死区内的结皮等都是无害结皮。
这些结皮对气体和物料流动没有多大影响。
而以下两种结皮属于有益结皮:
第一种,如果某部位没有结皮则气流易在该区域形成涡流,增加阻力损失,则该部位的结皮是有益结皮;第二种,如某部位设计过大,使该部位风速过低,则该部位的结皮也是有益结皮。
例如笔者曾操作过的某窑,有一次上升管道内衬料产生了裂缝,热气体进入了衬料与外壳之间的空间。
为了窑继续运转,决定暂不清理该处的结皮,意在用结皮堵住裂缝,防止热气体继续渗透造成外壳变形、衬料鼓出。
后来该处结皮逐渐增厚,挡住了三分之一的截面积,窑反而达到了少有的高产与稳定。
后来结皮掉了,窑也随之失去了那一段“黄金”时期。
分析其原因很简单,该部位在管道分解炉之下,物料在其上部入炉,平时由于该处风速稍低物料易从该处“短路”入窑,造成窑况波动、产量不高。
而一旦该处结皮厚了,风速高了物料不再“短路”,入窑分解率提高,从而窑况稳定,窑产增高。
因此,对于结皮有一个该清不该清的问题。
有害结皮要不断被清理掉;无害结皮则不见得要清理,而有益结皮就根本不应清理。
五、关于“看火”问题
现代化水泥厂中,窑操作员是在中央控制室靠各参数的显示仪表、PID控制器甚至计算机来了解、判断和控制窑系统各参数和设备的。
传统上所说的“看火”在这种现代化水泥厂的操作中有了新的内涵。
在现代化水泥窑的操作过程中,烧成温度、熟料升重和游离钙、窑尾温度、NOx含量等都是分析和判断窑内状况的重要依据,但本文只打算谈一谈窑传动电流(有的工厂使用窑传动扭矩)这一最重要、最有效的依据。
窑传动电流(或扭矩)是窑转速、喂料量、窑皮状况、窑内热量和物料中液相量及其液相粘度的函数,它反映了窑的综合情况,比其它任何参数代表的意义都多都大。
下面列举几种传动电流(或扭矩)变化形态所代表的窑况。
1.窑传动电流(或扭矩)很平稳、所描绘出的轨迹很平。
表明窑系统根平稳、热工制度很稳定。
2.窑传动电流(或扭矩)所描绘出的轨迹很细,说明窑内窑皮平整或虽不平整但在窑转动过程中所施加给窑的扭矩是平衡的。
3.窑传动电流(或扭矩)描绘出的轨迹很粗,说明窑皮不平整,在转动过程中,窑皮所产生的扭矩呈周期性变化。
4.窑传动电流(或扭矩)突然升高然后逐渐下降,说明窑内有窑皮或窑圈垮落。
升高幅度越大,则垮落的窑皮或窑圈越多。
大部分垮落发生在窑口与烧成带之间。
发生这种情况时要根据曲线上升的幅度马上降低窑速(如窑传动电流或扭矩上升20%左右,则窑速要降低30%左右),同时适当减少喂料量及分解炉燃料,然后再根据曲线下滑的速率采取进一步的措施。
这时冷却机也要作增加篦板速度等调整。
在曲线出现转折后再逐步增加窑速、喂料量、分解炉燃料等,使窑转入正常。
如遇这种情况时处理不当,则会出现物料生烧、冷却机过载和温度过高使篦板受损等不良后果。
5.窑传动电流(或扭矩)居高不下
有四种情况可造成这种结果。
第一,窑内过热、烧成带长、物料在窑内被带得很高。
如是这样,要减少系统燃料或增加喂料量。
第二,窑长了窑口圈、窑内物料填充率高,由此引起物料结粒不好、从冷却机返回窑内的粉尘增加。
在这种情况下要适当减少喂料量并采取措施烧掉前圈。
第三,物料结粒性能差。
由于各种原因熟料粘散,物料由翻滚变为滑动,使窑转动困难。
第四,窑皮厚、窑皮长。
这时要缩短火焰、压短烧成带。
6.窑传动电流(或扭矩)很低
有三种情况可造成这种结果。
第一,窑内欠烧严重,近于跑生料。
一般操作发现传动电流(或扭矩)低于正常值且有下降趋势时就应采取措施防止进一步下降。
第二,窑内有后结圈,物料在圈后积聚到一定程度后通过结圈冲入烧成带,造成烧成带短、料急烧,易结大块。
熟料多黄心,游离钙也高(有时可达10%之多)。
出现这种情况时由于烧成带细料少,仪表显示的烧成温度一般都很高。
遇到这种情况要减料运行,把后结圈处理掉。
第三,窑皮薄、短。
这时要伸长火焰,适当延长烧成带。
7.窑传动电流(或扭矩)逐渐增加
这一情况产生的原因有以下三种可能。
其一,窑内向温度高的方向发展。
如原来熟料欠烧,则表示窑正在趋于正常;如原来窑内烧成正常,则表明窑内正在趋于过热,应采取加料或减少燃料的措施加以调整。
其二,窑开始长窑口圈,物料填充率在逐步增加,烧成带的粘散料在增加。
第三,长、厚窑皮正在形成。
8.窑传动电流(或扭矩)逐渐降低
这种情况产生原因有二。
其一,窑内向温度变低的方向发展。
加料或减少燃料都可产生这种结果。
其二,如前所述,窑皮或前圈垮落之后卸料量增加也可出现这种情况。
9.窑传动电流(或扭矩)突然下降
这种情况也有两种原因。
第一,预热器、分解炉系统塌料,大量未经预热好的物料突然涌入窑内造成各带前移、窑前逼烧,弄不好还会跑生料。
这时要采取降低窑速、适当减少喂料量的措施,逐步恢复正常。
第二,大块结皮掉在窑尾斜坡上,阻塞物料,积到一定程度后突然大量入窑,产生与第一种情况同样的影响。
同时大块结皮也阻碍通风,燃料燃烧不好,系统温度低,也会使窑传动电流(或扭矩)低。
依靠窑传动电流(或扭矩)来操作窑有信息清楚、及时、可靠等优点,尤其与烧成温度、窑尾温度、系统负压、废气分析等参数结合起来判断窑内状况及变化更能做到准确无误。
而单独依靠其它任何参数都不可能如此全面准确地反映窑况。
比如烧成带温度这个参数只能反映烧成带的情况,而且极易受粉尘和火焰的影响。
而窑电流(或扭矩)却可及时地反映出烧成带后的情况,预告大约半小时后烧成带的情况,提示操作员进行必要的调整。
六、用计算机操作窑的体会
许多现代化水泥厂都配备了计算机操作窑所需要的设备和软件。
计算机操作窑就是把从现场采集到的各参数的信号送入计算机,计算机经过比较和分析从而按一定程序输出相应的信号给现场的执行器来完成操作任务。
象传统的PID控制回路一样,计算机对窑的控制也靠若干个控制回路来完成,不同的是控制回路之间可以有许多联系,而且能包含多个PID控制回路的功能。
比如用于窑头和分解炉喂煤的PID控制回路是两个独立的回路,操作员在自动控制时分别设定窑头和分解炉的燃料用量,而计算机控制时则可把上面两个回路并为一个,可对窑头和分解炉的燃料按一定比例同时进行调节。
调节的依据一般是窑传动电流(或扭矩)、窑烧成温度。
窑烧成温度的目标值是由计算机根据几个小时之内测得并输入计算机的熟料升重和游离钙的数值而定的。
计算机操作过程中各回路之间的联系可用下面的例子说明。
当窑内发生小规模的垮落窑皮、冷却机篦下压力增加较快、窑传动电流(或扭矩)下降时,计算机会根据这些情况逐步增加篦板速度、同时逐步降低窑速、适当减少喂料量和分解炉燃料。
由于燃料量的变化,系统废气中的气体成分也发生了变化,计算机会根据这些变化进一步调节主风机转速、风门开度或三次风闸板开度。
计算机操作窑有其省事、及时、不易失误等优点。
但就目前水平而言,运用计算机操作窑还有许多局限性,一个好的、责任心强的操作员只会比计算机操作得好而不会坏。
下面就谈谈计算机操作窑的局限性。
1.计算机分析现场来的信号是靠输入的软件程序来完成的,而实际生产中的情况变化多端,不可能总是符合程序中特定的模式,故有其局限性。
尤其是对一些不真实的信号(如热电偶被结皮包裹后测得的温度信号等)计算机是判断不出来的,而操作员则可以判断出来并加以调整。
窑系统各参数之间相互影响、关系复杂,很少直线关系,甚至连规则的曲线关系也没有。
这样设计软件时就很难完美,使计算机的综合分析能力较差。
2.在开窑加料初期和准备停窑操作等阶段,由于系统情况变化大,无法采用计算机操作。
3.窑在大波动的情况下(如窑口圈掉了),由于机内设计的PID参数只适应小范围的波动,所以也不能用计算机操作,否则会因反映慢而贻误调节时机,造成严重后果。
4.一次信号不可靠的回路不宜投入计算机操作。
比如测窑尾温度的热电偶被结皮包裹,测不到真实温度时,又如窑尾气体分析取样管堵塞或漏入空气,检测结果不准确时,则靠这些信号进行控制的回路都不宜用计算机操作。
5.信号多变、需频繁调节的回路不宜用计算机操作。
因计算机的输出信号送到现场需经过中间继电器,每改变一次输出信号继电器就跳动几次,信号变化频繁时继电器易失效,从而造成计算机只输出信号而执行器不动作的情况,使窑的操作出现失误。