最新fmea规定.docx
《最新fmea规定.docx》由会员分享,可在线阅读,更多相关《最新fmea规定.docx(15页珍藏版)》请在冰豆网上搜索。
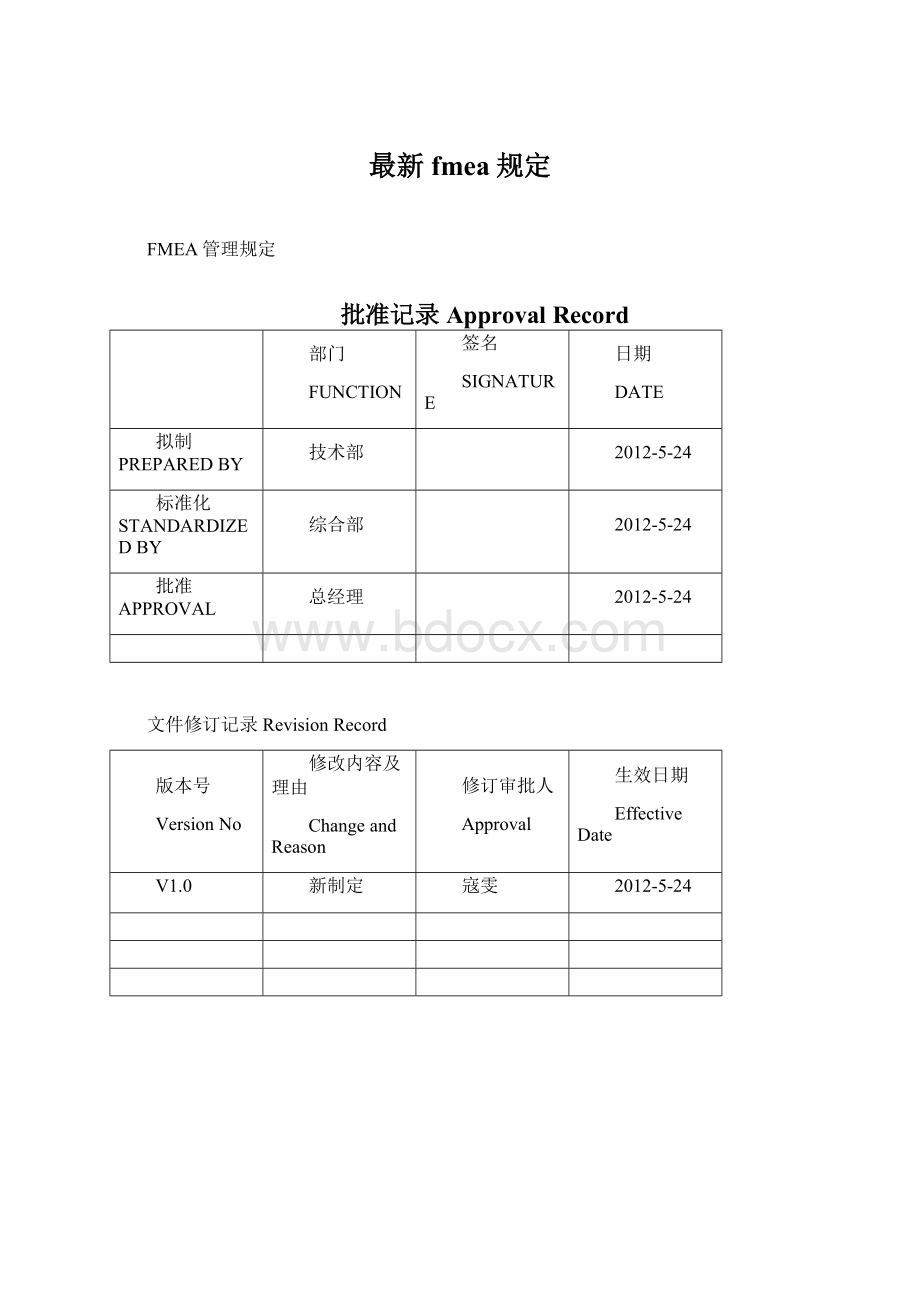
最新fmea规定
FMEA管理规定
批准记录ApprovalRecord
部门
FUNCTION
签名
SIGNATURE
日期
DATE
拟制PREPAREDBY
技术部
2012-5-24
标准化STANDARDIZEDBY
综合部
2012-5-24
批准APPROVAL
总经理
2012-5-24
文件修订记录RevisionRecord
版本号
VersionNo
修改内容及理由
ChangeandReason
修订审批人
Approval
生效日期
EffectiveDate
V1.0
新制定
寇雯
2012-5-24
1目的
通过设计前、量产前的FMEA分析,规范和减少设计及制程中已知和潜在的不良模式并针对不良模式,在设计及量产前提出预防措施,以提高设计之稳定性,可靠性,提高制程品质和制程能力。
2范围
设计管制活动、设计变更前/后、制程标准订定及变更前/后的潜在失效模式之作业。
3定义
FMEA(FailureModeEffectsAnalysis)失效模式与效应分析。
为一系列统化的分析技术,用以评估某一可能缺点的发生机率,及其发生后造成的影响。
而且针对高风险(RPN,RiskPriorityNumber)项目,事先评估其制程能力,制订适当的制程管制。
4职责
3.1技术部:
3.1.1FMEA会议召开,产品保证计划,新产品流程草案主导拟定,FMEA作业制定,主导FMEA会议。
3.1.2召集组成跨功能小组,小组成员可包括技术、品保、生产及相关人员(必要时可会同客户或供货商),协同进行研讨。
3.2生产部:
流程的讨论确认,潜在不良模式收集,潜在不良原因分析,预防措施的拟定、确认、实施。
3.3品管部:
FMEA作业所需之相似制程之统计数据的提供,预防措施的监督执行。
3.3管理代表:
FMEA文件的核准。
5适用时期
5.1开发初期。
5.2产品投产前期。
5.3整体材料变更时。
5.4制程设备、模/治具大幅变更或购置时。
5.5客户要求时。
5.6以上由技术部主管视情况裁决,是否实施实效模式与效应分析作业。
6作业流程:
责权单位
流程
说明
相关表单
FMEA核心小组
由技术部主导选定所要执行FMEA的型号规格
FMEA会议记录
FMEA核心小组
由技术部绘制制程/设计流程图
《设计/制程流程图》
FMEA核心小组
由技术部主导根据产品或部件实际机能,选定重要制程
《产品或部件特性测试报告》
FMEA核心小组
由技术部主导根据产品特性及实际经验,对产品品质进行预测
FMEA会议记录
PFMEA报告
DFMEA报告
FMEA核心小组
由技术部主导根据产品特性及实际经验,对产品品质进行分析
FMEA会议记录
PFMEA报告
DFMEA报告
FMEA核心小组
技术主导对产品风险系数评估;对改善后的风险系数评估
FMEA会议记录
PFMEA报告
DFMEA报告
FMEA核心小组
对风险系数大于100或偏大的,需拟定对策并重新评估
FMEA会议记录
PFMEA报告
DFMEA报告
相关单位
相关单位执行重新拟定的对策
FMEA会议记录
PFMEA报告
DFMEA报告
FMEA核心小组
确认新的对策是否有效,无效若则重新评估
FMEA会议记录
PFMEA报告
DFMEA报告
技术部
效果OK后整理存档
PFMEA报告
DFMEA报告
流程说明:
从制程流程图中,小组成员以脑力激荡后决定欲分析的制程等,用失效模式分析表进行后续的分析.
7作业内容:
7.1失效模式分析表使用方法:
7.1.1文件编号:
文件号码编号用于做追踪管控。
7.1.2项目:
填入须分析的产品、部件或零组件的名称、编号。
7.1.3制程/设计责任:
填入部门和小组,如果需要,还要包括供货商的名称。
7.1.4编制者:
负责FMEA工程师的姓名、部门。
7.1.5完成日期:
填入本FMEA的预定完成日,此日期不得迟于计划量产的日期。
7.1.6生效日期:
填入编制FMEA原始稿的日期及最后修改版的日期。
7.1.7FMEA小组:
列出有权认可及执行工作的责任部门及个人名称。
7.1.8项目/功能:
将被分析项目或制程功能及要求注意事项,用简明文字说明。
7.1.9潜在失效模式:
说明可能发生的失效。
所谓「潜在失效」系指「可能发生,但是不一定发生」的失效而言。
负责制程的工程人员应先检讨过去类似项目的FMEA分析品质、耐用性及可靠性等方面的问题,以为判断的依据。
(如漏件、松动、插不到位…等)
7.1.10潜在失效效应:
潜在失效效应是指对客户的冲击,发生此种失效时,会造成功能或组装或其他方面的效用产生。
A对最终使用者来说:
失效的潜在效应一律用产品或系统的性能来描述,例如:
无连接、无功能、不对码、性能不稳定、外观划伤、无震动等。
B如果顾客是下一工站,失效潜在影响应用制程工站性能(功能)来描述,例如:
合不严、卡键、接触不良、锁不紧、作业不便、损坏设备或危害作业者等。
7.1.11严重度:
估计缺点发生对客户使用或生产制程的影响程度,以1~10分的尺度计分。
所谓影响度,系指某项失效发生后,对客户或生产制程可能产生的影响情况。
(见附表1――严重性评定表)
7.1.12级别:
是用来对需要附加制程/设计控制的零组件、部件或产品本身的一些特殊
特性进行分级(如关键、主要、重要、重点)。
7.1.13潜在失效原因:
将各项失效说明其可能的发生原因。
注意应将一切可能的原因尽量列出。
7.1.14发生度:
指某项失效的发生机率。
估计发生度时,系假定产品经检查前,有关失效发
生的机率。
填入该项失效出现的机率,用1~10尺度为评估标准。
(见表7-2―――发生率评分表)
7.1.15现行制程/设计管制方式:
A.现行制程控制应描述防止失效模式发生或侦测将发生失效模式的控制;
B.现行设计控制应列出预防措施,设计确认/验证或其它活动,以保证该设计对于所考虑的失效模式或机理是充分的。
C.现行制程/设计管制可以考虑预防、侦测两种类型.
7.1.16难检度:
已发生的失效而言。
难检度用1~10的尺度表示。
因此,处理时应确认失效原因已经查出。
并确保相关控制均属有效,以防止将失效成品运出厂外。
见表7-3――难检度评分表(PFMEA)和表7-4――难检度评分表(DFMEA)
7.1.17风险顺序数(RPN)Riskprioritynumber:
发生度/严重度及难检度等三项数字的乘积,为一项目的失效综合指针。
应优先择取风险顺序数高的部份先采取矫正措施。
但无论RPN的结果如何,当严重度(S)高时,就应引起特别注意。
7.1.18矫正优先度:
凡RPN≥100分以上或是严重度>8以上时,应优先考虑实施改善措施。
7.1.19改善建议措施:
A建议采取的具体改善措施。
凡有关单位应必须重视各项建议措施,务须追踪改善。
(改善措施,通常皆属设计或制程方面)。
B依据矫正优先度,应对首先对排列在最前面问题和最关键问题进行矫正措施并予以标准化。
C如果某一特定原因无建议措施,该栏必须写『无』,予以明确。
D若失效潜在影响会危害制造/作业员,就应采取矫正措施。
或明确规定适当操作人员保护措施。
7.1.20责任担当与完成日:
填入改善措施负责单位/人员以及应完成期限。
7.1.21对策实施:
填入矫正对策及其生效日期。
7.1.22措施后结果:
完成改善措施后,再于本栏填入各项修正计分,将PRN重新算出。
并判定是否低于100,考量是否需要更进一步的措施,重点应该随时放在持续改善上。
7.1.23跟催:
小组成员担当职责的工程师应负责保证所有的建议措施已被实施或已妥善地落实。
8.相关记录
8.1《设计潜在失效模式及影响分析表》
附表1:
严重性评定分表
效应
判定准则:
效应的严重性
这个级别导致当一个潜在的失效模式发生后造成了在最终顾客或制造、组装工厂缺陷,应该随时考虑到最终顾客。
如果在两者都发生缺陷,则采取较高两级的严重性
(顾客影响)
判定准则:
效应的严重性
这个级别导致当一个潜在的失效模式发生后造成了在最终顾客或生产组装中的缺陷,应该随时考虑到最终顾客。
如果在两者都发生缺陷,则采取较高两级的严重性
(制造、组装影响)
严重性级别
无警告的严重危害
严重程度很高。
潜在失效模式影响用户安全或包含政府法规情形失效发生时无警告
可能危及作业员(机器或组装),没有警告
10
有警告的
严重危害
严重程度很高。
潜在失效模式影响用户安全或包含政府法规情形,失效发生时无警告
可能危及作业员(机器或组装),但有警告
9
很高
产品无法正常使用(基本功能丧失)
产品基本功能丧失或根本达不到客户要求,需要进行难度较大的修
8
高
产品功能正常,但性能下降。
顾客非常不满意
产品基本功能正常,但使用性能下降,可能必须要筛选,或要进行一般修理
7
中等
产品功能、性能正常,但舒适性、方便性项目失效。
顾客不满意
产品功能正常,但外观达不到客人要求
6
低
产品功能、性能正常,但舒适性、方便性项目运行性能下降
产品功能正常,但外观有轻微缺陷
5
很低
装配完工后出现尖响声、喀嗒响声或外观缺陷等项目令人不舒服,大多数顾客能发现有缺陷(大于75%)
产品功能正常,但使用时有轻微不适(75%以上的顾客能发现
4
轻微
装配完工后出现尖响声、喀嗒响声或外观缺陷等项目令人不舒服,50%的顾客能发现有缺陷
产品功能正常,但使用时有轻微不适(50%的顾客能发现)
3
很轻微
装配完工后出现尖响声、喀嗒响声或外观缺陷等项目令人不舒服,少数顾客能发现有缺陷(少于25%)
产品功能正常,但使用时有轻微不适(25%的顾客能发现)
2
无
没有可识别的影响
轻微或作业不方便,或没影响
1
附表2:
发生率评分表
失效发生的可能性
可能的失效率A
可能的失效率B
评分等级
很高:
持续性发生的失效
≧100件/每千件
≧100pcs/1000pcs
10
50件/每千件
50pcs/1000pcs
9
高:
反复发生的失效
20件/每千件
20pcs/1000pcs
8
10件/每千件
10pcs/1000pcs
7
中等:
偶尔发生的失效
5件/每千件
5pcs/1000pcs
6
2件/每千件
2pcs/1000pcs
5
1件/每千件
1pcs/1000pcs
4
低:
很少有很少有相关或相似的失效
0.5件/每千件
0.5pcs/1000pcs
3
0.1件/每千件
0.1pcs/1000pcs
2
极低:
失效不太可能发生
≦0.010件/每千件
≦0.010pcs/1000pcs
1
注:
设计失效模式与效应分析(DFMEA)仅需考虑“可能的失效率A”;
制程失效模式与效应分析(PFMEA)仅需考虑“可能的失效率B”。
附表3:
难检度评分表(PFMEA)
难检度
评分标准A
评分标准B
检出度评分
几乎不可能
确定绝对无法检出
100%不能检出
10
很微小
现行的控制方法不能检出
现行的控制方法100%不能检出
9
微小
现行的控制方法只有很小机会能检出
现行的控制方法85%不能检出
8
很小
现行的控制方法只有很小机会能检出
现行的控制方法70%不能检出
7
小
现行的控制方法可能可以检出
现行的控制方法35%不能检出
6
中等
现行的控制方法可能可以检出
现行的控制方法20%不能检出
5
中上
现行的控制方法有很好的机会检出
现行的控制方法5%不能检出
4
高
现行的控制方法有很好的机会检出
现行的控制方法98%以上能检出
3
很高
现行的控制方法几乎确定可以检出
现行的控制方法99%以上能检出
2
几乎肯定
现行的控制方法肯定可以检出
现行的控制方法100%以上能检出
1
附表4:
难检度评分表(DPFMEA)
难检度
评价准则:
被设计控制检出的可能性
级别
绝对不肯定
设计控制将不能/或不可能找出潜在的起因/机理及后续的失效模式;或根本没有设计控制
10
很极少
设计控制只有很极少的机会能够找出潜在的起因/机理及后续的失效模式
9
极少
设计控制只有极少的机会能够找出潜在的起因/机理及后续的失效模式
8
很少
设计控制只有很少的机会能够找出潜在的起因/机理及后续的失效模式
7
少
设计控制只有较少的机会能够找出潜在的起因/机理及后续的失效模式
6
中等
设计控制只有中等机会能够找出潜在的起因/机理及后续的失效模式
5
中上
设计控制只有中上机会能够找出潜在的起因/机理及后续的失效模式
4
多
计控制只有较多机会能够找出潜在的起因/机理及后续的失效模式
3
很多
设计控制只有很多机会能够找出潜在的起因/机理及后续的失效模式
2
几乎肯定
设计控制几乎肯定能够找出潜在的起因/机理及后续的失效模式
1