架空供热管道维修施工方案.docx
《架空供热管道维修施工方案.docx》由会员分享,可在线阅读,更多相关《架空供热管道维修施工方案.docx(12页珍藏版)》请在冰豆网上搜索。
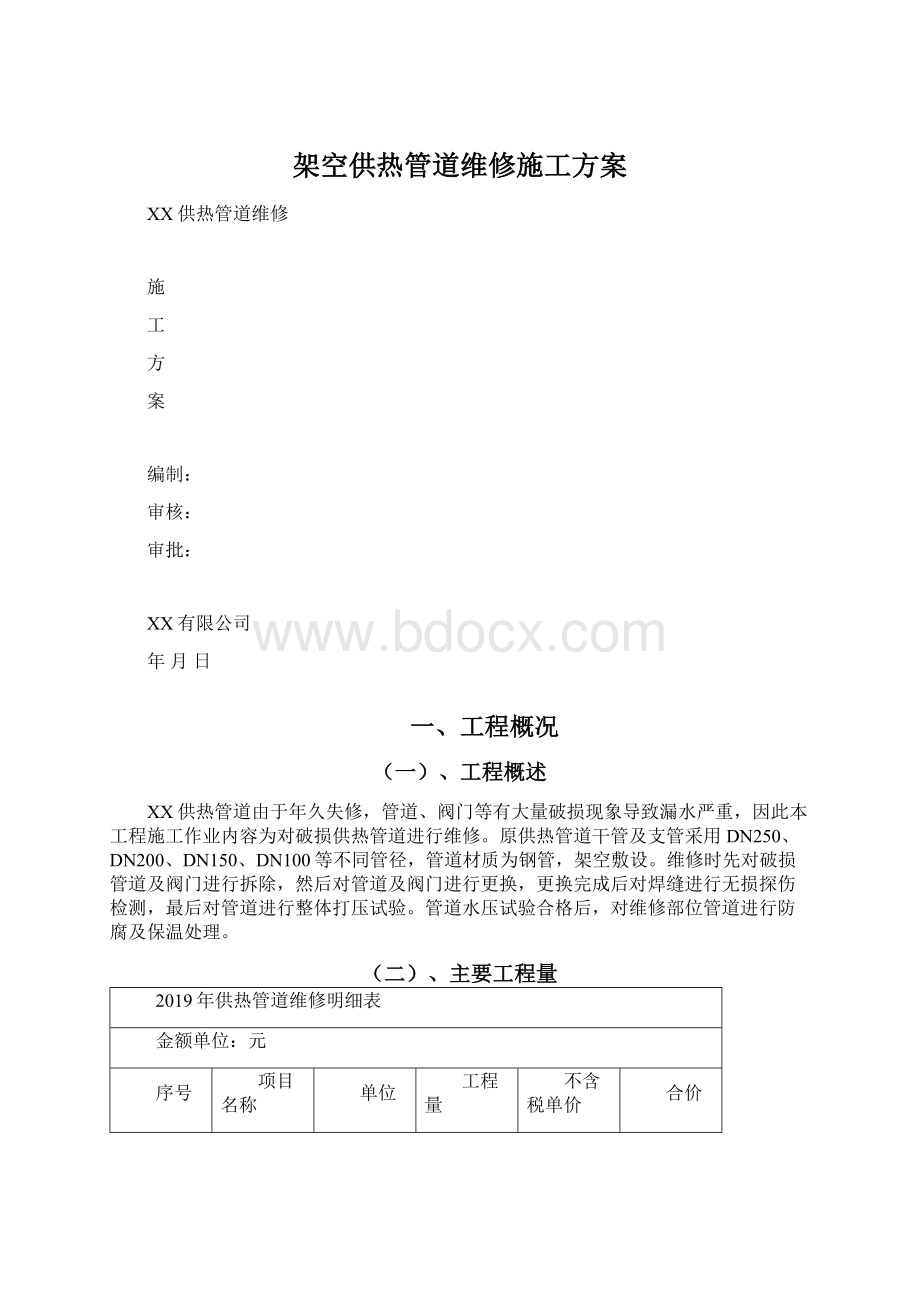
架空供热管道维修施工方案
XX供热管道维修
施
工
方
案
编制:
审核:
审批:
XX有限公司
年月日
一、工程概况
(一)、工程概述
XX供热管道由于年久失修,管道、阀门等有大量破损现象导致漏水严重,因此本工程施工作业内容为对破损供热管道进行维修。
原供热管道干管及支管采用DN250、DN200、DN150、DN100等不同管径,管道材质为钢管,架空敷设。
维修时先对破损管道及阀门进行拆除,然后对管道及阀门进行更换,更换完成后对焊缝进行无损探伤检测,最后对管道进行整体打压试验。
管道水压试验合格后,对维修部位管道进行防腐及保温处理。
(二)、主要工程量
2019年供热管道维修明细表
金额单位:
元
序号
项目名称
单位
工程量
不含税单价
合价
1
拆换支管阀门
个
221
54.09
11954
2
DN50闸阀安装
个
35
365.66
12798
3
DN50截止阀安装
个
45
319.78
14390
4
DN65闸阀安装
个
7
421
2947
5
DN65截止阀安装
个
2
397
794
6
DN80闸阀安装
个
2
516
1032
7
DN40截止阀安装
个
38
227
8626
8
DN50蝶阀安装
个
20
370.75
7415
9
DN50截止阀安装
个
48
319.77
15349
10
DN65闸阀安装
个
10
421
4210
11
DN65截止阀安装
个
3
397
1191
12
DN65蝶阀安装
个
1
402
402
13
DN80闸阀安装
个
10
516.1
5161
14
DN250供暖钢管拆除
m
210
23.34
4901
15
DN200供暖钢管拆除
m
519
17.95
9315
16
DN150供暖钢管拆除
m
300
17.95
5385
17
DN100供暖钢管拆除
m
50
14.36
718
18
DN200室外焊管安装
m
300
339.03
101710
19
DN150室外焊管安装
m
300
238.57
71572
20
DN250室外焊管安装
m
210
416.29
87421
21
DN200室外焊管安装
m
219
339.03
74248
22
DN100室外焊管安装
m
50
166.54
8327
23
DN50供暖保温处理
m
97.5
62.42
6086
24
DN65供暖管保温处理
m
59.8
65.95
3944
25
DN80供暖保温处理
m
10.4
69.23
720
26
DN100供暖保温处理
m
5
71.2
356
27
DN40供暖管保温处理
m
52
61.69
3208
28
DN50供暖保温处理
m
65
62.42
4057
29
DN100供暖管保温处理
m
4
71
284
30
安居小区DN40供暖管保温处理
m
59.8
61.67
3688
31
DN50供暖管保温处理
m
208
62.43
12985
32
DN65供暖管保温处理
m
59.8
65.95
3944
33
DN80供暖管保温处理
m
10.4
69.23
720
34
DN100供暖管保温处理
m
6.5
71.08
462
35
DN250焊缝超声波探伤
口
35
55.91
1957
36
DN200焊接超声波探伤
口
86
31.13
2677
37
DN150寒风超声波探伤
口
50
31.12
1556
38
DN100焊缝超声波探伤
口
8
31.13
249
39
采暖工程系统调试
系统
1
12762
12762
40
措施费
项
1
138584
138584
小计
648105
增值税
9%
58329
含税总计
706435
如上表所示,主要工程量为DN250、DN200、DN150、DN100管道拆除及安装,管道拆除及安装工程汇总如下表:
保温管道拆除安装统计表
管材型号
合计
DN250
210
0
210
DN200
219
300
519
DN150
0
300
300
DN100
100
0
100
总计
1129
DN250管道拆除及安装量59.8+74.2+76=210m,位置如下图:
建工DN200管道拆除及安装量53+95+21+50=219m,位置如下图:
建工DN100管道拆除及安装量50+35+15=100m,位置如下图:
DN200管道拆除及安装工程量50+45+30+50+40+15+30+40=300m,位置如下图所示:
DN150管道拆除及安装工程量116+100+84=300m,位置如下图所示:
一、施工准备
(一)、技术准备
1、施工方案完成,并与相关专业讨论确定实施。
2、施工相关工具准备完毕,检查合格。
3、作业前已对参加该项作业的相关人员进行施工安全、技术交底,交底人与被交底履行签字手续。
4、作业场地清理干净,无杂物。
夜间施工照明充足。
高处作业平台、步道畅通,安全围栏、警示牌齐全。
5、所有施工人员身体健康,无妨碍工作的病症,从事登高作业的人员血压正常,无心脏病,无恐高症与精神障碍等。
(二)、材料准备
1、管材:
管材应有产品合格证,管材不得弯曲、无锈蚀、无飞刺、重皮及凹凸不平等缺陷。
2、各类阀门有出厂合格证,规格、型号、强度和严密性试验符合设计要求。
丝扣无损伤,铸造无毛刺、无裂纹,开关灵活严密,手轮无损伤。
3、附属装置:
减压阀、疏水器、过滤器、补偿器、法兰等应符
合设计要求,应有产品合格证及说明书。
(三)、施工组织及人员准备
1、施工组织应保证重点,统筹安排;
2、采用先进技术,推进施工标准化、机械化;
3、科学地安排施工计划,保证连续均衡举进行施工;
4、保证工程质量,做到安全施工;
5、讲究经济效益,努力降低工程成本;
6、应配备有较高业务水平的管道技术人员、土建技术人员;
7、应配备满足施工需要的技术工人,如管道工、电焊工、气焊工油漆工、起重工、泥瓦工等。
三、施工方案
(一)、拆除方案
1、拆除工艺流程
2、施工方法
根据架空管道位置(如上图)和距离现状自然地面的高度,原管道每3m/段进行切除,管道切除位置增设钢支架进行原管道加固。
全线搭设宽度4米,平均高度5米满堂脚手架。
脚手架、临时支架拆除过程中自上向下,逐层逐段进行拆除,不得垂直交叉作业。
脚手架及操作平台平均高度5m,水平撑不大于2m/道,架设双向剪刀撑,搭设坡道,设防护网。
3、施工机具
100KW柴油发电机1台(提供现场用电),50T吊车2台(用于拆除管道),8T吊车2台(用于搭设拆除临时支架),300挖掘机1台(用于基础、道路平整处理和吊车不能到达处管道拆除),板车2辆(用于材料及拆除管道运输),气割4套,电焊机4台,磨光机4台,打夯机2台(用于基础、道路平整处理)。
4、施工人员组织
管理人员
施工安全负责人:
1人
施工技术负责人:
1人
施工现场负责人:
1人
施工人员
焊工(持证):
6人负责管道切割、临时支架焊接
电工(持证):
1人负责现场临时用电
吊车司机:
4人负责管道吊装、临时支架吊装、管道装卸车
信号工:
4人配合吊车指挥信号
货车司机;2人材料、管道转运
架子工:
4人负责搭设拆除脚手架、安全网、脚手板。
普工:
10人负责拆除保温、配合吊车、配合专业人员操作、转运材料。
5、管线拆除
a、根据系统流程图查清每根管线的流程走向;
b、与甲方取得联系,确认每根管线的切断点位置,并作出断点标志和编号。
c、管线、阀门拆除:
(1)管线拆除从上至下开始,拆除时注意保持管道支架的稳定,防止向一侧偏斜,发生倒塌事故;
(2)拆除阀门法兰螺栓,大型阀门用倒链将其吊至地面,阀门两端管口应做好加固。
(3)按一定的长度将管线截断,用倒链将截断管线吊至地面,摆放在指定位置;
(4)拆除管线支吊架;并对管道支吊架进行标注。
(5)拆除管道,应先清理管道内部残留的物质,所有的工作人员要佩戴必要的劳保用品。
(6)部分管道上带有防腐保温材料,根据现场实际情况考虑基本上不能利旧,因此不考虑保护性拆除,只考虑管道拆除方便即可。
(7)从法兰连接处进行拆除时,由于连接的螺栓多锈蚀,因此在拆除前应至少提前4个小时在螺栓连接处喷除锈剂,这样螺栓就比较容易拆除。
拆下来的螺栓如果可以再次利用的话,在管道拆除后应挂到连接法兰上以防丢失。
对碳钢、合金钢管道可采用火焰切割,对不锈钢管道采取砂轮机切割。
(8)管道拆除,需要起重工和管工的密切配合。
由于是拆除,可以考虑局部整体进行拆除,拆除时需要用吊车或者相关吊具对管道进行悬吊配合,防止发生管道倾倒、滑落等砸人事故,对于使用的吊车、吊具必须具有相应的吊装能力。
(9)拆除后的管道,尽量立即拉走,不能运走的在现场设置一个临时集中堆放点,便于集中管理,有利于清点和运输。
(10)管道切割位置原则上从安装焊口出切割,并控制每段管子的重量不超过起重设备额定负荷的90%。
6、拆除作业安全措施
(1)施工人员必须经过安全教育培训,合格后方准上岗。
(2)落实各级安全施工责任制,抓生产必须同时抓安全。
施工人员必须严格遵守安全生产规章制度和安全操作规程,施工技术员做好技术交底工作,做到不交底不开工,交底不全不开工。
(3)每天开工前应划施工区域和界限,班组长以上人员应该知道现场作业面的分布情况,施工过程中各班组须相互照应和通气,班组人员在施工时不得随意增加施工项目和施工点。
(4)特殊工种(电工、焊工、架子工、起重工)必须经过培训,并考试合格,取得劳动部门颁发的上岗操作证,持证上岗,严禁无证操作。
其他施工人员施工前进行安全教育培训,考核合格后,方可持证上岗。
(5)参加高处作业人员应进行体格检查,经医生诊断患有不宜从事高处作业病症的人员不得参加高处作业。
(6)所有参加人员必须熟知本措施内容,施工期间必须安全帽。
(7)高空作业人员必须系好安全带。
(8)施工前必须规定办理动火审批手续。
(9)所有施工人员必须听从指挥,互相配合,不得乱发指令。
(10)施工前要仔细检查气割设备。
氧气、乙炔瓶必须有合格证,检查减压器、割枪、胶管是否漏气,若有漏气不得使用,氧气乙炔压力表是否完好,工作使用的氧气胶管为黑色,乙炔管为红色,二者不得互换使用,不得用其它胶管代替。
(11)乙炔瓶和氧气瓶在搬运过程中要轻拿轻放,严禁有剧烈的碰撞现象。
(12)施工前,要将氧气瓶、乙炔瓶之间的距离保持在10m以上距离,并一定要放置平稳,且有专人看管。
气体不使用时,要及时关闭氧气瓶和乙炔瓶阀门。
(13)每处工作地点要备至少2个完好的灭火器和2个水桶,2个水桶必须灌满水,并设防火挡板。
(二)、安装方案
1、管道安装工艺流程
2、施工技术措施
2.1、材料的验收检验工作,管道用的钢管材、管件阀门等,必须经质量技术监督行政主管部门的安全认可证书或受理证书,同时还需如产品质量证明书。
2.2、管道的焊接工作﹐必须有持相应证书的焊工担任﹐且在有效期内。
焊后经焊接检验员检测合格后方可进行探伤检测。
2.3、管道水压试验,试验压力按照设计及规范要求执行﹐稳压30min,压力不下降,无渗漏为合格﹔
2.4、管道水压试验结束后,按照规范要求应进行水冲洗等。
3、管道焊接工艺
3.1、架空热力管道施工﹐焊接是重要的工艺之一,焊接质量的好坏关系到管网的正常运行寿命及安全可靠性,因此焊接质量控制是质量控制的中心环节,围绕焊接质量控制和影响焊接质量因素,必须为确保焊接质量提供必要的保证。
根据管道的技术要求和设备、人员、现场环境要求等条件﹐采用手工电弧焊的焊接工艺方法。
对接接头的坡口形式为V型;强调按工艺要求开坡口以保证焊透。
3.2、焊前准备
1)、坡口加工和清理除锈
坡口加工要求采用坡口机加工出坡口,并留出适当的钝边,如1mm左右坡口的清理用角向砂轮机,将坡口面和坡口附近20mm范围内﹐打磨漏出金属光泽。
除锈、去油﹐除去污物﹐要求当天清理干净,当天焊接完毕,不允许隔夜焊接。
2)、焊接设备及工具
a、要求使用直流电焊机﹐配好电流、电压表,手工电弧焊时,采用直流反接法﹔
b、管子组对时﹐应采用专用工具组对﹐避免强力组对焊口;
c、对焊接部位﹐应采用临时挡风措施﹐并注意将管子―头堵死﹐以防止穿堂风的影响;
准备好焊条烘箱和焊条保温筒﹔
d、拖焊的环境条件符合通用工艺要求,阴雨天和湿度过大的天气,应停止焊接(或采取措拖后焊接);
e、焊工每人应配齐角向磨光机﹐以便及时打磨层间和接头等部位。
3.3、焊材的选择:
焊条、管材等主要材料都应有材质证明书和质量合格证并经检验、验收符合国家标准或其它有关标准方可使用。
3.4、焊接质量控制措施
1)焊前控制项目:
材质证明书﹐焊工资格﹐坡口尺寸和加工质量,坡口清理除锈,坡口组对间隙﹐焊接工艺评定试验及工艺文件﹐焊机完好情况、电流表、电压表配备等等。
2)焊接过程控制项目:
焊条烘干和保温筒的使用,焊接工艺纪律执行情况,焊接规范参数的控制和记录,定位焊缝﹐焊缝接头的质量,焊缝打底和层间焊接质量,清渣情况等等。
3)焊后控制项目∶
焊缝表面清渣﹐清除飞溅﹐焊缝外观自检﹐质量记录,无损探伤检查,焊接缺陷返修等等。
4、强度试验
管线施工完成后,经检查除现场组装的连接部位(如:
焊接连接、法兰连接等)外,其余均符合设计文件和相关标准的规定后,方可以进行强度试验。
强度试验应在试验段内的管道接口防腐、保温施工及设备安装前进行,试验介质为洁净水,环境温度在5℃以上,试验压力为设计压力的1.5倍,充水时应排净系统内的气体,在试验压力下稳压10min,检查无渗漏、无压力降后降至设计压力,在设计压力下稳压30min,检查无渗漏、无异常声响、无压力降为合格。
当管道系统存在较大高差时,试验压力以最高点压力为准,同时最低点的压力不得超过管道及设备的承受压力。
当试验过程中发现渗漏时,严禁带压处理。
消除缺陷后,应重新进行试验。
试验结束后,应及时拆除试验用临时加固装置﹐排净管内积水。
排水时应防止形成负压,严禁随地排放。
5、严密性试验
严密性试验应在试验范围内的管道全部安装完成后进行。
严密性试验压力为设计压力的1.25倍,且不小于0.6MPa。
一级管网稳压1h内压力降不大于0.05MPa;二级管网稳压30min内压力降不大于0.05MPa,且管道、焊缝、管路附件及设备无渗漏,固定支架无明显变形的为合格。
钢外护管焊缝的严密性试验应在工作管压力试验合格后进行。
试验介质为空气,试验压力为0.2MPa。
试验时,压力应逐级缓慢上升,至试验压力后,稳压10min,然后在焊缝上涂刷中性发泡剂并巡回检查所有焊缝,无渗漏为合格。