氮化优点及常见缺陷原因分析工艺制定资料.docx
《氮化优点及常见缺陷原因分析工艺制定资料.docx》由会员分享,可在线阅读,更多相关《氮化优点及常见缺陷原因分析工艺制定资料.docx(6页珍藏版)》请在冰豆网上搜索。
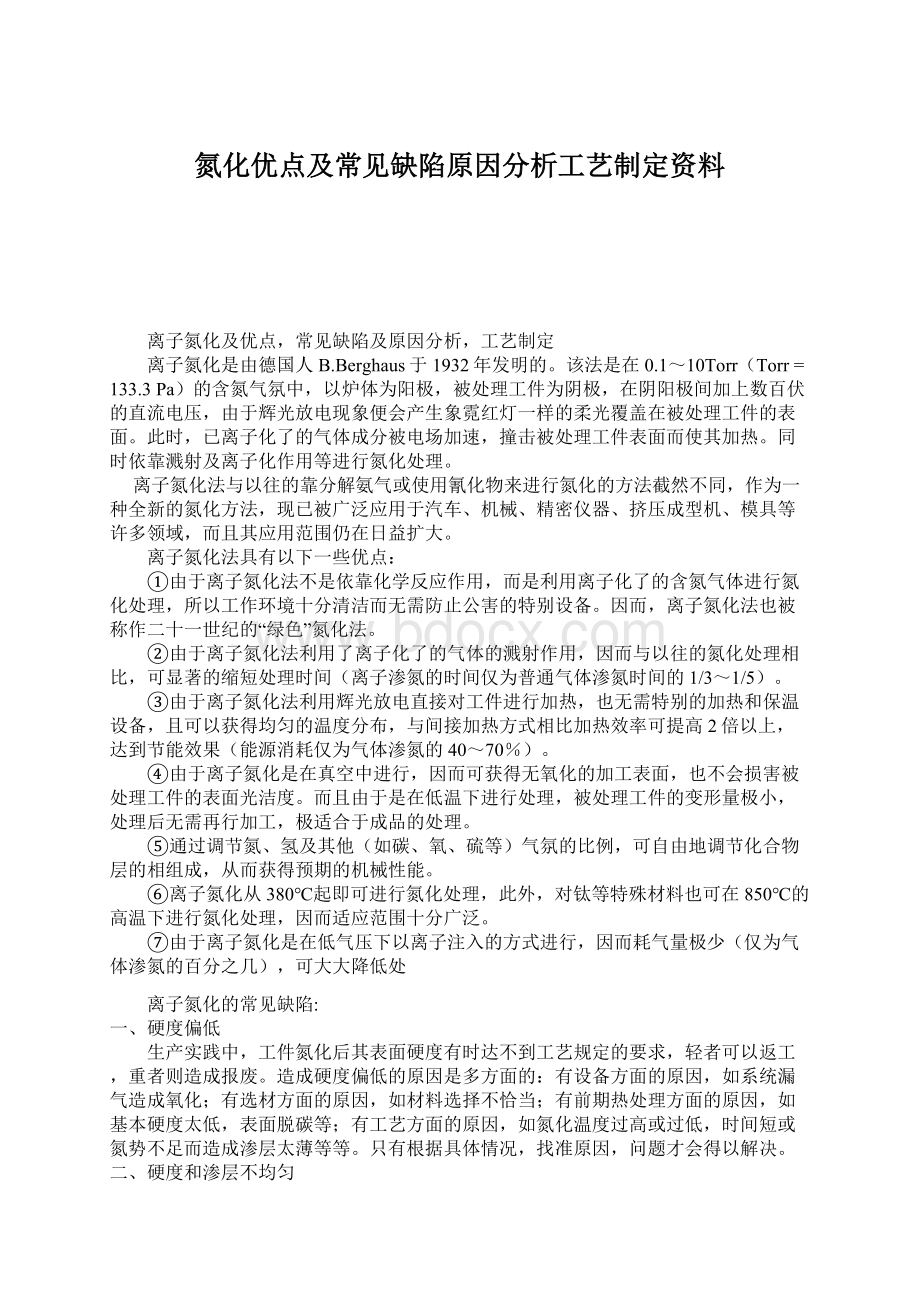
氮化优点及常见缺陷原因分析工艺制定资料
离子氮化及优点,常见缺陷及原因分析,工艺制定
离子氮化是由德国人B.Berghaus于1932年发明的。
该法是在0.1~10Torr(Torr=133.3Pa)的含氮气氛中,以炉体为阳极,被处理工件为阴极,在阴阳极间加上数百伏的直流电压,由于辉光放电现象便会产生象霓红灯一样的柔光覆盖在被处理工件的表面。
此时,已离子化了的气体成分被电场加速,撞击被处理工件表面而使其加热。
同时依靠溅射及离子化作用等进行氮化处理。
离子氮化法与以往的靠分解氨气或使用氰化物来进行氮化的方法截然不同,作为一种全新的氮化方法,现已被广泛应用于汽车、机械、精密仪器、挤压成型机、模具等许多领域,而且其应用范围仍在日益扩大。
离子氮化法具有以下一些优点:
①由于离子氮化法不是依靠化学反应作用,而是利用离子化了的含氮气体进行氮化处理,所以工作环境十分清洁而无需防止公害的特别设备。
因而,离子氮化法也被称作二十一世纪的“绿色”氮化法。
②由于离子氮化法利用了离子化了的气体的溅射作用,因而与以往的氮化处理相比,可显著的缩短处理时间(离子渗氮的时间仅为普通气体渗氮时间的1/3~1/5)。
③由于离子氮化法利用辉光放电直接对工件进行加热,也无需特别的加热和保温设备,且可以获得均匀的温度分布,与间接加热方式相比加热效率可提高2倍以上,达到节能效果(能源消耗仅为气体渗氮的40~70%)。
④由于离子氮化是在真空中进行,因而可获得无氧化的加工表面,也不会损害被处理工件的表面光洁度。
而且由于是在低温下进行处理,被处理工件的变形量极小,处理后无需再行加工,极适合于成品的处理。
⑤通过调节氮、氢及其他(如碳、氧、硫等)气氛的比例,可自由地调节化合物层的相组成,从而获得预期的机械性能。
⑥离子氮化从380℃起即可进行氮化处理,此外,对钛等特殊材料也可在850℃的高温下进行氮化处理,因而适应范围十分广泛。
⑦由于离子氮化是在低气压下以离子注入的方式进行,因而耗气量极少(仅为气体渗氮的百分之几),可大大降低处
离子氮化的常见缺陷:
一、硬度偏低
生产实践中,工件氮化后其表面硬度有时达不到工艺规定的要求,轻者可以返工,重者则造成报废。
造成硬度偏低的原因是多方面的:
有设备方面的原因,如系统漏气造成氧化;有选材方面的原因,如材料选择不恰当;有前期热处理方面的原因,如基本硬度太低,表面脱碳等;有工艺方面的原因,如氮化温度过高或过低,时间短或氮势不足而造成渗层太薄等等。
只有根据具体情况,找准原因,问题才会得以解决。
二、硬度和渗层不均匀
装炉方式不当,气压调节不当(如供气量过大),温度不均,小孔、窄缝未屏蔽造成局面过热等均会造成硬度和渗层不均匀。
三、变形超差
变形是难以杜绝的,对易变形件,采取以下措施,有利于减小变形。
氮化前应进行稳定化处理(处理次数可以是几次)直至将氮化前的变形量控制在很小的范围内(一般不应超过氮化后允许变形量的50%);氮化过程中的升、降温速度应缓慢;保温阶段尽量使工件各处的温度均匀一致。
对变形要求严格的工件,如果工艺许可,尽可能采用较低的氮化温度。
四、处观质量差
氮化件出炉后首先用肉眼检查外观质量,钢铁零件经氮化处理后表面通常呈银灰色或暗灰色(不同材质的工件,离子氮化后其表面颜色略有区别),钛及钛合金件表面应呈金黄色。
离子渗氮后工件表面不应有明显的电弧烧伤和剥落等缺陷,这些要求在正常情况下是完全可以达到的。
不正常的氮化颜色有以下一些情况:
1、表面电弧烧伤:
主要是由于工件表面、工件上的小孔中或焊接件的空腔内及组合件的接合面上存在含油杂质,引起强烈弧光放电所致。
2、表面剥落起皮:
产生起皮的机理还不十分清楚,但在生产实践中,工件表面清理不净、脱碳或气份中含氧量过多、氮化温度过高等有时会产生起皮。
3、表面发蓝或呈紫蓝色
这是氧化造成的,如果氧化是在氮化结束后停炉过程中产生的,则仅影响外观质量,对渗层硬度、深度无影响。
如果氧化是在氮化过程中产生的,则将不仅影响到产品外观,而且将直接影响到渗层硬度和深度。
表面发蓝的原因可能有:
炉子系统漏气,气氛中含水及含氧量过多;工件各处的温度不均匀,温度过低的部位由于渗氮较弱而呈绿色;冷却时工件各部位冷速不一致,冷得慢的部位可能呈蓝色。
4、表面发黑
这对将氮化作为最后一道工序的零件将影响外观,但一般不影响渗层硬度和深度。
产生这种现象的原因可能是:
炉子系统漏气,气氛中含水量及含氧量过高;温度过高;工件上的油污及氧化皮未去净等。
五、脉状氮化物
脉状氮化物通常又俗称脉状组织,是指扩散层中与表面平行走向呈白色波纹状的氮化物。
其形成机理尚无论,一般认为与合金元素的晶界偏聚及氮原子的扩散有关。
因此,控制合金元素偏聚的措施均有利于减轻脉状氮化物的形成。
工艺参数方面,氮化温度越高,保温时间越长,越易促进脉状组织的形成,如工件的棱角处,因氮化温度相对较高,脉状组织比其它部位严重得
离子氮化后零件的“肿胀”现象及防治对策
一、“肿胀”的本质
离子氮化后零件的“肿胀”实际上是零件尺寸变化的一种表现形式。
尺寸变化是由于氮化时工件表面吸收了大量的氮原子,生成各种氮化物或工件表层原始组织的晶格常数增大所致,宏观上则表现为表层体积的略微增加。
氮化后零件的“肿胀”是一种普遍现象。
各种氮化方法(气体氮化、液体氮化和离子氮化)处理后的零件或多或少总会存在一定的“肿胀”。
但应该说明的是:
离子氮化后零件的“肿胀量”较其它氮化方法要小。
这是因为:
离子氮化中的“阴极溅射”有使尺寸缩小的作用,因而抵消了一部分氮化“肿胀量”。
二、影响“肿胀”的因素
氮化后尺寸的胀大量取决于零件表层的吸氮量。
因而,影响吸氮量的因素均是影响“肿胀”的因素。
影响“肿胀”的因素主要有:
材料中合金元素的含量、氮化温度、氮化时间、氮化气氛中的氮势等。
材料中合金元素含量越高,零件氮化后的“肿胀”越大。
氮化温度愈高、氮化时间愈长,零件氮化后的“肿胀”愈大。
氮化气氛的氮势越高,零件氮化后的“肿胀”愈大。
三、“肿胀”的防治办法
前以述及,“肿胀”是氮化过程中一种必然的现象,因此要彻底杜绝“肿胀”是不现实的。
我们此处所说的“防治”主要有两种含义:
一是尽可能减小“肿胀”量;二是在“肿胀”不可避免的情况下,掌握“肿胀”规律,省去氮化后的再次加工。
1、减小“肿胀”的方法
①根据工件的服役条件,正确选用材料。
避免因追求工件性能而盲目使用“好”材料(高合金钢)的现象。
②根据工件的服役条件,提出合理的氮化要求,避免片面追求氮化层深度和硬度的现象。
③正确做好氮化前的预先热处理工作和“稳定化”处理,预先热处理工艺参数的制定必须正确,操作必须合理。
对形状复杂的零件,在最终精加工前必须进行一次或几次“稳定化”处理。
④在工艺允许的前提下,适当降低氮化温度,缩短氮化时间。
⑤在保证氮化层性能的前提下,调整氮化气氛。
⑥合理装炉,确保同炉工件温度的均匀性。
2、“肿胀”规律,省去氮化后的再次加工
一般说来,在选材、工艺制定正确的前提下,如能合理装炉,正确操作,则工件的“肿胀”是有一定规律的。
掌握了“肿胀”的规律后,即可在氮化处理前的最后一道加工工序中根据“肿胀”量使工件尺寸处于负偏差,工件经氮化处理后尺寸可正好处于要求的尺寸公差范围内,因而可省去氮化后的再次加工。
离子氮化脉冲电源的优点:
脉冲电源离子氮化技术的特点与直流离子氮化相比,脉冲电源使离子氮化工艺得到了进一步的发展,并在直流离子氮化技术基础上拓宽了应用范围。
脉冲电源离子氮化技术具有如下一些特点:
1、工艺参数独立可调,脉冲电源的优点之一是工艺参数与物理参数独立可调。
这是因为在直流电源条件下,既要满足零件表面的电流密度要求,又要满足零件保温电流密度的要求,两者相互影响。
而在脉冲电源条件下,电流密度由峰值电流满足,保温电流由平均电流满足,可由两个独立参数分别调节。
因此,工艺参数可在较大范围内变动。
2、打弧速度快,脉冲电源的输出特性,自身就有抑制电弧迅速发展的特点,由于IGBT开关响应速度极快,这更利于我们一旦发现弧光放电就立即关断电源,然后重新点燃电源,这些工作均在几十微秒内完成。
3、无需堵孔,由于脉冲电源对弧光放电的抑制作用,因此对于很多零件无需堵孔,这样给生产操作带来很大的方便。
例如处理曲轴时就不需堵孔,而当曲轴上存在有一些为提高零件性能的工艺孔时,这种优点就显得更为突出。
4、处理质量好、变形小,利于提高层深 ,由于脉冲电源对弧光发电的抑制作用,弧光在零件表面作用的时间极短,可获得高质量的表面,绝无灼伤。
并且提高了工件温度的均匀性,零件变形小。
由于其改善了工艺条件,在相同的时间内或者不利于氮化的条件下,能提高层深。
5、能提高设备的利用率,在直流电源的条件下,由于工艺参数和物理参数的相互影响,在保温时电压的调节范围通常在650V左右,而采用脉冲电源,电压调节范围将提高,例如在处理狭缝时可将电压提高到900V,增加了电源的有效输出。
6、有利于深孔、窄缝、微孔的渗氮,由于脉冲电源对空心阴极效应的抑制作用,可在深孔、窄缝、微孔内实现氮化。
例如可在型腔≥0.6mm的铝型材挤压模和Ф4×80(Ф32×1030)的深孔内实现氮化。
7、节能,由于脉冲电源可有效地抑制空心阴极效应的产生,避免小孔、窄缝处打死弧,取消了堵孔等工序,省去了不必要的辅助工时,缩短了工艺周期,节省了大量的人力物力,提高了设备的综合使用效率。
此外脉冲电源中限流电阻的减小,也可节省部分能量,因此脉冲电源较直流电源更加节能。
离子氮化前预先热处理工艺的制订原则:
为了保证氮化件心部具有必要的力学性能(也称机械性能),消除加工过程中的内应力,减少氮化变形,为获得良好的氮化层组织性能提供必要的原始组织,并为机械加工提供条件,零件氮化前必须进行不同的预先热处理。
1、氮化工艺参数对预先热处理工艺的要求
预先热处理中最后一道工序的加热温度至少要比氮化温度高20~40℃。
否则,零件在氮化过程中其心部组织及力学性能将发生变化,零件的变形无规律,变形量将无法控制。
2、常用的预先热处理工艺
常用的预先热处理工艺有调质、淬火+回火、正火及退火。
调质是结构钢常用的预先热处理工艺,调质的回火温度至少要比氮化温度高20~40℃。
回火温度越高,工件硬度越低,基体组织中碳化物弥散度愈小,氮化时氮原子易渗入,氮化层厚度也愈厚,但渗层硬度也愈低。
因此,回火温度应根据对基体性能和渗层性能的要求综合确定。
调质后理想的组织是细小均匀分布的索氏体组织,不允许存在粗大的索氏体组织,也不允许有较多的游离铁素体存在。
调质引起的脱碳对渗层脆性和硬度影响很大,所以调质前的工件应留有足够的加工余量,以保证机械加工时能将脱碳层全部切除。
对氮化后要求变形很小的工件,在精加工前(如精磨)还应进行一次或多次稳定化处理,处理温度应低于调质温度而高于氮化温度。
调质后,若工件的硬度或金相组织不合格,允许返工。
工、模具钢氮化前的预先热处理一般采用淬火+回火处理。
不锈钢氮化前的预先热处理一般采用淬火+回火,目的是为了消除加工应力和改善组织。
对硬度要求不高的工件可采用退火处理。
奥氏体不锈钢通常采用固溶处理。
正火预先热处理只适用于对心部强度和韧性要求不高的氮化件,正火时冷却速度不宜过慢。
尺寸较大的零件不宜采用正火处理,因正火时过慢的冷却速度会产生粗大组织,氮化后表面硬度低且不均匀。
正火后不合格的工件允许返工。
球铁的预先热处理多采用正火处理。
退火处理在钛合金中运用较多,结构钢中极少采用退火处理。
38CrMoAl钢不允许采用退火处理,否则渗层组织中易出现针状氮化物。
对于经过变形(如冲压、锻造、机加工等)的零件,应进行去应力退火处理,以减少氮化变形。
还需说明的是,细小的原始组织比粗大的原始组织氮化后有更高的表面硬度及良好的硬度梯度,因此,正火时冷却速度不易过慢,调质时回火温度不应过高,保温时间不应太长。
截面尺寸大的零件不易用正火态,而应调质处理。
离子氮化炉在曲轴生产线的工艺序号
1、毛胚检验
2、写编号
3、钻两端面中心孔
4、车大头外圆及端面
5、粗车主轴颈及小头
6、打编号
7、粗车主轴颈、大小头及小头倒角
8、铣定位面
9、精洗连杆颈
10、车大头工艺外圆及平衡块外圆
11、粗磨连杆颈
12、钻横油孔
13、钻斜油孔
14、斜油孔攻丝及油孔倒角
15、打磨棱角毛刺
16、平小头端面,精车小头并攻丝
17、粗车大头孔
18、半精磨主轴颈及大头外圆
19、精车轴承孔
20、半精磨连杆颈
21、精磨连杆颈
22、钻法兰孔并攻丝
23、精磨小头
24、铣键槽
25、动平衡、去重
26、精磨大头外圆及端面
27、油孔口倒角并研磨
28、清洗
29、打热处理批号
30、离子氮化热处理
31、检查跳动量
32、手攻丝
33、油孔口抛光
34、轴颈抛光
35、探伤。
36、清洗。
37、检验。
38、清洗。
39、涂蚀、包装