多膛炉活性炭再生工艺.docx
《多膛炉活性炭再生工艺.docx》由会员分享,可在线阅读,更多相关《多膛炉活性炭再生工艺.docx(16页珍藏版)》请在冰豆网上搜索。
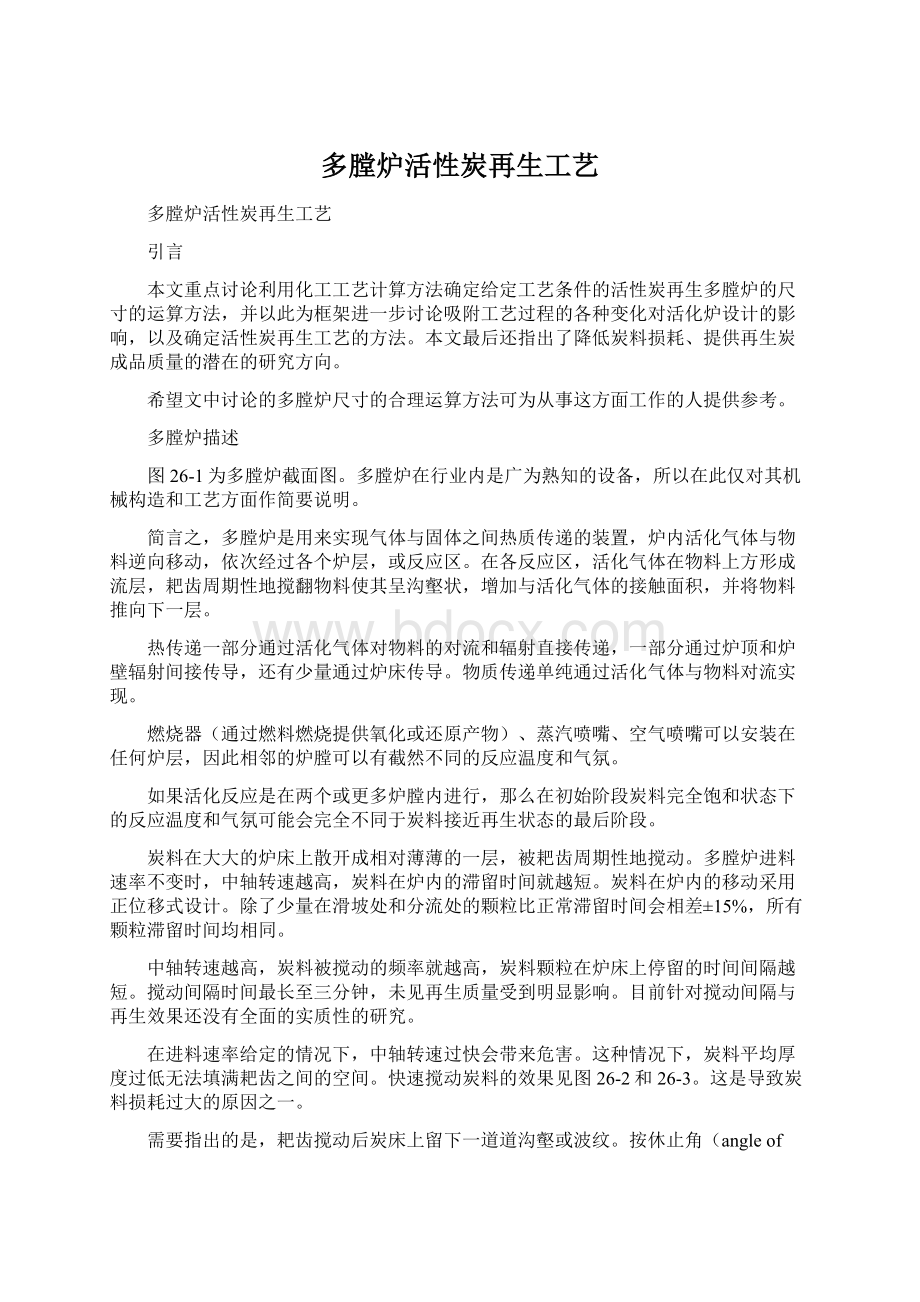
多膛炉活性炭再生工艺
多膛炉活性炭再生工艺
引言
本文重点讨论利用化工工艺计算方法确定给定工艺条件的活性炭再生多膛炉的尺寸的运算方法,并以此为框架进一步讨论吸附工艺过程的各种变化对活化炉设计的影响,以及确定活性炭再生工艺的方法。
本文最后还指出了降低炭料损耗、提供再生炭成品质量的潜在的研究方向。
希望文中讨论的多膛炉尺寸的合理运算方法可为从事这方面工作的人提供参考。
多膛炉描述
图26-1为多膛炉截面图。
多膛炉在行业内是广为熟知的设备,所以在此仅对其机械构造和工艺方面作简要说明。
简言之,多膛炉是用来实现气体与固体之间热质传递的装置,炉内活化气体与物料逆向移动,依次经过各个炉层,或反应区。
在各反应区,活化气体在物料上方形成流层,耙齿周期性地搅翻物料使其呈沟壑状,增加与活化气体的接触面积,并将物料推向下一层。
热传递一部分通过活化气体对物料的对流和辐射直接传递,一部分通过炉顶和炉壁辐射间接传导,还有少量通过炉床传导。
物质传递单纯通过活化气体与物料对流实现。
燃烧器(通过燃料燃烧提供氧化或还原产物)、蒸汽喷嘴、空气喷嘴可以安装在任何炉层,因此相邻的炉膛可以有截然不同的反应温度和气氛。
如果活化反应是在两个或更多炉膛内进行,那么在初始阶段炭料完全饱和状态下的反应温度和气氛可能会完全不同于炭料接近再生状态的最后阶段。
炭料在大大的炉床上散开成相对薄薄的一层,被耙齿周期性地搅动。
多膛炉进料速率不变时,中轴转速越高,炭料在炉内的滞留时间就越短。
炭料在炉内的移动采用正位移式设计。
除了少量在滑坡处和分流处的颗粒比正常滞留时间会相差±15%,所有颗粒滞留时间均相同。
中轴转速越高,炭料被搅动的频率就越高,炭料颗粒在炉床上停留的时间间隔越短。
搅动间隔时间最长至三分钟,未见再生质量受到明显影响。
目前针对搅动间隔与再生效果还没有全面的实质性的研究。
在进料速率给定的情况下,中轴转速过快会带来危害。
这种情况下,炭料平均厚度过低无法填满耙齿之间的空间。
快速搅动炭料的效果见图26-2和26-3。
这是导致炭料损耗过大的原因之一。
需要指出的是,耙齿搅动后炭床上留下一道道沟壑或波纹。
按休止角(angleof
Repose)为30-45°计算,炭料与活化气体的接触面积是公称或平面炉床面积的1.2-1.4倍,而接触面积是影响再生能力的决定性因素。
值得注意的是,耙齿搅翻炭料的力度十分轻柔。
在粉状活性炭再生装置测试中,少量较小的炭料结块随进料一起加入系统,穿过六个炉床后进入落料槽,此时仍可见到炭料结块,只是已经非常脆弱,不能用两指夹起,需要用勺子将其盛出送检。
几年前有位客户曾不辞辛苦用冷炉作骨炭磨损值试验。
测试使用的多膛炉外径为14”3’,共八层,骨炭进料速率以吨/时计算,采用斗式提升机将出料复送入系统,共进行30个作业周期。
骨炭与一般活性炭在标准NBS磨损测试中的表现相差无几。
客户试验得出的结果是每作业循环磨损率(消失以及生成的60目颗粒)为0.3%。
这个结果令人质疑通常所说的5%的活性炭磨损率是怎么得出的。
由一个炉床落入下一炉床的活性炭的数量是不变的,在颗粒活性炭应用中,热量质量传递的面积可以忽略不计。
炉床公称面积为175ft2,实际沟壑表面积227ft2,炉床高4ft,每层落下的物料质量始终为1/3磅。
按平均粒度30目计算,总的颗粒面积将为12.5ft2,但下落时颗粒很紧密,没有完全散落在活化气体中,这样大约有1-2ft2的面积与活化气体接触。
以上这样的情况是很幸运的,因为单个颗粒与活化气体接触时会全方位的吸收热量。
炉膛上层活化气体中反应物浓度高,此时活化气体还原性极强。
气化反应发生仅在颗粒表面,而不会深入到孔隙内。
即便是炉床最上面一层的活性炭也仅能够一面受热,即一半的比表面积受热,而且热量会从朝下的一面传导出去。
在活化区,由于受到层流和炭床表面停滞膜的影响,活性炭周围的烟气成分与炭床上方活化气体流中的烟气成分差别很大。
活化工艺–反应区划分和影响反应区尺寸的因素
通常认为利用热再生法还原活性炭的温度在1500-1850℉,参加反应的有水蒸汽和/或二氧化碳,残余吸附质,以及作为吸附剂的炭。
当然反应不会在没有达到反应温度时发生,加热反应不会在炭料干燥前开始。
在最好的设计和运行条件下,活性炭再生需要经过三个反应阶段,分别在多膛炉的三个区域独立进行,互不重叠。
反应区按照活化气体的流动方向、反应的重要程度而不是反应顺序由多膛炉底部往上依次为活化区、加热区和干燥区。
炉内发生的化学反应有:
C+H2OCO+H2
1700℉平衡常数K=47.8
C+CO22CO
1700℉平衡常数K=52.5
CO2+H2CO+H2O
1700℉平衡常数K=0.73
*假定炭为石墨炭,而参与再生反应的为无定形炭的同素异形体。
即便是在1500℉,在充分反应的情况下,不考虑动能率限制,前两个反应的平衡常数依然很高(接近10)。
考虑到炭料层内发生的气化反应受到动能率和反应速率限制,反应区域大小可能取决于耙动后的炭床的体积,但实际上,反应区域大小由炉床面积决定。
活化气体接触到的物料面积决定了气相到炭料(固相)的质量传递,及吸热反应所需的热传递。
炭床表面和下层都会产生反应,但是随着深度增加,反应速率会逐渐降低,因为靠近炭床表面的炭料对热传递和反应物起到阻隔作用。
如前文讨论的,在炭床厚度的正常范围内,炭料气化反应速率不会因为这些因素变化而改变,比如:
搅拌频率、滞留时间或炭床厚度超出覆盖整个炉床面积要求的最低标准。
如果认为活化区由炭床体积决定,需要先假定一个有效反应厚度,比如约为0.5英寸,这样反应体积将具体表示为炉床面积乘以一个常数。
活化区炉床面积可这样得出,每小时需要气化的炭的质量除以气化反应速率(单位表示为磅固定碳/时*平方英尺)。
活化区尺寸设计就成了确定每磅炭料中需要气化的炭的质量,及反应速率的问题(将在后文中进行详细讨论)。
活化区条件确立后,就可以确定由活化区进入热解区的烟气的温度、体积、质量和组成。
如果热解区与活化区不重叠,那么热解区的反应条件就可以调整成不同于烟气由活化区进入热解区后形成的反应条件。
可通过注入蒸汽降低炉温,注入空气升温,(空气与活化气体中的CO和H2反应)或通过燃料燃烧升温。
通常,根据多膛炉的设计和运行,以及吸附质的不同特性,热解区逐渐过渡到活化区或与其有部分重叠。
随着吸附质热降解反应放缓,水蒸汽与二氧化碳反应速率增加,完成缓慢过度。
热解区及其上方干燥区炉膛尺寸的确定,仅是一个关于炭料、吸附质和水在炭床上进行热交换所需面积的问题。
在此区域内传递热量以供蒸发水分,加热炭料和热分解吸附质。
通过提高活化气体温度,增加温差产生热传递很可能会减少反应区面积。
通过燃烧CO或H2或燃烧吸附质炭化时排放出的有机挥发物会可以减少燃料。
详细的计算方法将在后文中举例说明。
当前情况下我们暂认为在一般工艺条件下干燥炭料这道准备工序并不对炭料损失率和质量造成影响。
在详细计算反应区尺寸之前,需要确认影响产品质量、炭料损失及炉子尺寸的因素。
计算反应区尺寸所需的基本要素
干燥区
计算干燥区尺寸时最主要的是知道需要蒸发脱除的水分的质量。
这部分水分是随着饱和活性炭进入再生炉的,流量以磅/时计。
通常,再生炉上游设置泥浆脱水装置,用于控制进料的含水百分比。
过去普遍的做法是在固定床脱色柱中直接用热水洗涤炭料,靠重力作用使炭料脱水,或向立柱内吹入压缩空气快速脱水。
这样方式脱水后炭料含水量在37-45%范围。
最近,更常见的做法是通过向上倾斜的螺旋输送机输送炭浆,让水流至输送机较低的一端,与炭料输送相反。
采用这种方式脱水,炭料中水分可控制在45-55%范围。
不管采用两者之中哪种方式脱水,炭料水分含量范围都会很大,这是因为除了脱水设备,还受其他因素影响炭料水分含量。
在静止容器内对炭料脱水,最后一道洗涤水的温度,压缩空气使用与否,还有脱水时间长短都影响脱水效果。
若利用脱水螺旋输送机,脱水效果主要取决于炭料粒度,以及是否定期清理了螺旋叶片和输送机壳之间的炭粉和霉菌,使排水不受阻碍。
当活性炭上吸附质负荷相对较高时,孔隙容积主要被吸附质占据,而留给水分的容积很小。
因此在前面提到的较低的范围时,可以预测出水分含量。
每磅饱和活性炭含吸附质0.3-0.5磅视为相对较高的吸附质负荷。
不论是采用哪种脱水设备,必须要说明水分含量是“按接收量”表示,水量除以水、活性炭及其吸附质总和。
因此需要知道单位质量活性炭中吸附质的含量来计算给定活性炭再生率条件下水分的蒸发速率,以磅/时计。
活性炭脱水远不如当前油价受到的关注多,因为“按接收量”表示水分含量不准确可靠。
水分含量40%表示干基活性炭1磅,水分2/3磅,水分含量50%表示干基活性炭1磅,水分1磅。
需要蒸发的水分不是10%,也不是25%,而是50%。
热解区
正确计算热解中的热传递,应知道单位质量活性炭中吸附质的质量,以及降解吸附质所需要的热量。
热解区尺寸设计通常并不需要知道以上两点的确切数值,因为假定的每磅炭料携带半磅吸附质(已知的最大负荷)和250Btu/lb吸热反应所需热量,并不会明显影响多膛炉整体尺寸。
未遇见吸附质热解所需热量或吸附质的质量不同于以上假定值而产生问题的情况。
相比于热解区尺寸,单位原始活性炭所含吸附质的质量对于确定干燥区尺寸以及确定有机挥发物的热值具有更重要的意义。
有机挥发物可作为干燥区“免费的”热量来源。
再生反应所需要的是在热解反应中尽可能多地去除吸附质,因为吸附质去除的越多,在接下来活化反应中需要与水和二氧化碳反应分解的炭化物就会越少。
活性炭孔隙直径在30Å或以下通过活化反应并不能完全去除炭化物。
活化反应去掉炭化物时,通常伴随着活性炭粒度变小,大孔隙扩大。
大孔隙不仅会使炭颗粒重量减轻,还会使其硬度降低,并且增加随后环节中的炭料损失。
尽管需要通过热解反应尽可能完全地去除吸附质,但不能通过增加热解反应中炭化物温度来实现。
在1600℉,炭化物会石墨化,较为适宜的做法是尽量保持炭化物的化学活性,使其优先于原始碳结构发生反应。
原始碳结构在生产过程中已经过高温去除活性成分使其化学活性减弱。
Goos在木炭研究中发现迅速升温越快,产生的炭化物越少。
他在报告中指出,热解反应时间从几天缩减到几秒,可使木炭产量由35%降低至14%。
如果确实如此,多膛炉则是进行这一反应的最理想的设备,因为饱和炭干燥后,炭颗粒在被翻搅至炭床表面后,可在几秒钟内升温到气化温度的100℉上下。
热解反应区活化气体的温度通常在1500-1800℉范围.
如后文中所介绍的多膛炉的设计和运行条件都是专为活性炭再生工艺精心制定的,物料在很小的区域内,从200℉升温至1500℉,根据中轴转速的不同滞留时间在5至20分钟不等。
流化床的应用效果会更好,但是如果热解区不独立会带来其他问题。
建议在热解阶段避免过度加热或缓慢焙烧。
为避免过度加热,建议热解时的活化气体保持较高的H2O含量,降低CO和H2含量。
在1500℉,发生吸热反应,随着温度提高,反应速率加快,防止炭料循环利用活化气体温度。
活化气体的温度应控制在大约1700℉。
在低于设计产能的情况下,为了避免缓慢焙烧,再生炉内的反应的有效面积可以缩小,做法是将活化区上移,并在底部炉膛改用蒸汽净化,或者可以通过在干燥区急剧降温,使炭料在进入活化反应前处于潮湿状态。
在设计计算中,倾向于通过提高热解区热传递速率,减少热解区面积,缩短热解时间。
活化区
目的是通过活化反应去除所有吸附质热解后残留的炭化物,同时避免原始活性炭结构参与活化反应。
吸附质热解炭化物
热解产生炭化物的质量是首先需要知道的设计数据。
吸附质的重量通过利用水银置换仪测量新鲜状态和饱和后的活性炭颗粒密度计算得出。
饱和活性炭颗粒密度与新鲜活性炭颗粒密度之比再减去1可得出每磅活性炭中吸附质的质量(磅)。
饱和活性炭应在封盖的坩埚中,在1740℉时,加热7.5分钟,除去挥发成分。
饱和、热解颗粒密度与新鲜活性炭密度之比,等于每磅原始活性炭形成炭化物的质量(磅)。
当然,炭化物数值需要根据灰分从新鲜状态到热解状态的增益和损失进行校准。
比较这两种比值,了解每磅吸附质生成炭化物的质量具有学术意义,积累这方面的经验可帮助设计工程师预测不同种类化合物热解反应后的结果,并有助于研究各种热解反应条件。
如果未能取得水银密度仪,也可通过平均体积密度(ABD)获得几乎同样的结果。
平均体积密度相对于颗粒密度的优点之一就是,同样一份炭样可用于新鲜炭密度测定,饱和干燥后能用于饱和密度测定,在一个或多个坩埚中热解后,还能用于热解密度测定。
而采用水银颗粒密度时,炭样经过吸附和热解后即作废,这种方法带来的问题是需要准备三份一模一样的炭样。
在准备以上炭样时需要非常仔细,精心筛选与等分。
不同时间,不同批次,甚至同一袋子顶部和底部的炭样,其颗粒密度和平均体积密度都会有很大差别,随意取样后进行饱和炭热解的结果会大不相同。
通常料液生产线未建成的情况下,确定炭化物气化反应条件会产生困难。
以上操作可直接利用实验用装置或在工作台上进行,制成模拟废料液。
水银置换法测定颗粒密度,只需使用20g活性炭放入料液中至饱和。
如果没有设计吸附系统,不确定炭料与进入吸附工序的液体流接触后是否会达到饱和平衡状态,最保险的做法是依据炭料完全饱和后的数据进行再生炉设计。
炭样在吸附过程中可能逐渐将吸附质中较轻的成分置换成较重的,较重的成分通常会形成更多的炭化物,从两方面看—最大负荷和吸附质形成最多炭化物,依此数据设计的炉子的尺寸会是安全尺寸。
按以上方式确定吸附质负荷和热解反应形成的炭化物含量要好于在脱色柱中取样计算吸附质负荷。
后一种方法经常忽视活性炭已经吸附却未被检测出的料液中的成分,因为不是有意将这些成分从产品流中去除,而是这些成分与活性炭接触后发生生物氧化,不会出现在活化阶段。
料液成分的测量结果通常以BOD、COD、TOC或色值表示,而这些无法直接精确转换成每磅原始活性炭中所含吸附质的质量。
最重要的是,料液成分变化测量结果(streamchangemeasurements)让设计师根据经验猜测有多少吸附质能通过简单或有破坏力的蒸馏方式被轻松去除,又有多少会残留并经热解反应后生成难以去除的炭化物。
这不仅影响到多膛炉尺寸设计还影响到活性炭的损耗值。
炭本体结构以外的炭的气化反应,反应条件,反应速率
吸附质热解形成炭化物的质量经确定后,在合理计算炉子尺寸之前,还需要解决以下两个问题:
炭料反应速率,单位表示为lb/hr/ft2炉床面积。
按照这样的速率,参与气化反应的炭料有多少?
炭结构整体的气化反应。
原始炭结构会与吸附质生成的炭化物互相竞争与H2O和CO2反应。
即使所有活性炭本体结构全部被吸附质形成的炭化物所覆盖(这种情况可能永远不会出现),结构外层和扩散式大孔隙内的炭化物会先反应,然后才是吸附孔隙中的炭化物参与反应。
这些大孔隙是H2O和CO2通往吸附孔隙的通路。
Juhola指出粗大孔隙的活性炭比细小孔隙的活性炭反应速率更高,恰恰证明了这一点。
活化工艺要求的不是与固定炭发生反应,而是与热解形成的质地较软的炭化物发生反应,新生成的炭化物中可能还含有少量氢、氮、硫或其他原子,此时反应很可能带有选择性,新生成的炭化物就会比活性炭本体结构更容易发生反应。
关于这个假设的初步研究将在后文简单阐述,当然相关证据还不充足,仅希望今后能有更深入的研究。
笔者建议,如果没有更好的数据,多膛炉的设计参数可以参考在封盖好的坩埚中,1740℉条件下,气化比例为0.25lb原始碳结构/lb热解炭化物。
某糖加厂的数据显示,用骨炭对糖浆进行脱色作业后,再用颗粒活性炭对脱色溶液进行最终精细加工,每作业循环的炭料补充量不到1%。
在这种加工条件下,每磅活性炭中所含吸附质的数量较低。
蔗糖溶液中吸附质热解后形成的固定碳含量极低。
业内常见的做法是用动物骨炭吸附这些色素物质,然后在密封的整流罐内900℉下热解。
除非吸附质的负荷非常高,一般经过200次再生循环后,未见有固定碳堆积问题。
以上数据证实了在设计合理和运行正常的再生系统中,机械操作或其他机械原因造成的炭料损失的可能性极小。
笔者的经验是,吸附质负荷越高,形成的固定碳的含量就越高,吸附作业时所需的炭料补给量就越高。
对于那些采用间歇式作业,生产率低,再生炉设计和运行都不太理想的工厂,按照气化炭化物1磅,损失0.25磅原始炭,来计算活性炭补给量不会与测试结果有较大差异。
Juhola的研究结果显示炭料经过活化后平均体积会降低1.8%。
焙烧和活化后平均体积密度的总重量损失将达到20%左右,在1700℉含有氮的条件下焙烧,仅40%吸附质仍为炭化物。
这就表示,原始炭占炭样质量的80%,热解形成炭化物的质量占10%。
损失率1.8%就意味着气化热解形成1磅的炭化物,就会损失0.18磅原始炭。
实验室结果与笔者对商业应用粗略推测正好吻合。
活化区反应条件。
业内的惯例是通过选取活化区反应条件,使一定产能要求下反应速率最大化,炉型尺寸最小化。
对于细小孔隙活性炭采用固定碳气化率0.2lb/hr/ft2是已证实安全可靠的。
气化粗大孔隙活性炭的经验较少,但固定碳气化率按1.2lb/hr/ft2是经实验室和实际加工条件下可达到的。
曾有一种活性炭表现出更高的气化速率,但是经过三个作业周期后,速率出现下降。
因此孔隙结构影响化气化反应速率的说法或许不成立。
起到催化作用的矿物质成分或其他原因都可影响气化反应速率。
只有在希望通过利用固定碳最大反应速率确定再生炉最小尺寸时才可参考0.6或1.2lb/hr这两个值。
但是,通过提高反应速率可以减少炭化物与原始炭结构反应性能的区别。
提高温度、提高H2O与CO2的比例可以提高气化反应速率。
Mizushima指出活性炭最低在1650℉,并且最短在三分钟之内即可出现石墨化。
他使用的炭样从1300℉开始焙烧,并且假定这种条件下炭料没有出现石墨化。
活化区气相温度应控制在1700℉(炭料温度1600℉),这样做一方面可以保留炭化物与原始炭结构气化反应性的区别,另一方面可以在控制不当的情况下,允许一部分碳化的吸附质在下一个活化作业中去除。
根据观测,反应气体浓度、温度较高可造成气化反应速率高,这样产品活性炭的糖蜜值与碘值之比倾向于偏高。
似乎只有粗大孔隙被清理干净或者扩大,细小孔隙没有改变。
本文最后提到的初步实验的结果显示,反应温度越低,炭化物相对于原始碳结构的热解反应速率越高。
至少在水蒸汽容积为40%时情况如此。
科罗拉多大学西部分校的怀俄明州煤炭活化实验报告指出,当活化气体中仅有CO2和氮气时,只有大孔隙结构参加气化反应(孔隙大于28Å),小孔隙结构不发生反应。
文中还对其他实验结果做了比较研究,有趣的是在其他试验中,使用H2O和氮气作为活化气体时,均显示小孔隙参与活化反应,而活化气体有CO2和无H2O时未见到。
在Juhola的实验中,在未使用HClleeching的测试中,在原有焙烧形成的碘值基础上很少有碘值增加。
在个别测试中,活化阶段还出现碘值下降。
在未使用HClLeeching,但碘值出现增加的测试中,其共同特征是蒸汽与CO2含量比例3:
1。
使用HClleeching的情况下,蒸汽与CO2含量比例较高时,活化阶段碘值会高于焙烧阶段的碘值。
综上所述可以得出以下两点:
1.如果要求吸附用活性炭的碘值最大化,则再生工艺中需要较高的蒸汽与CO2比例。
如果仅需要使活性炭糖蜜值较高,则可以忽略此点。
2.低于1800℉的活化气体温度,且保证最高的气化速率,是理想的反应温度。
这样条件下,热解形成的炭化物比原始碳结构更容易发生气化反应。
在本章结尾所阐述的实验中,温度降低,反应速率将急剧下降,因此需要权衡避免反应区炉床面积过大。
以上气化反应速率的2/3范围,特别是对于小孔隙活性炭,固定碳气化速率为0.4lb/hr/ft2可作为降低炭料补充率的建议反应速率。
如果按以上方式实现炭料损失率降低1%,增加50%的炉床面积,仅反应区面积,可以取得较好的经济收益。
炉床面积及炉体尺寸计算
考虑以上因素,针对最小设备尺寸、反应条件的灵活性和最小损失率做实验并确定设计重点后,既可以计算出每个反应区的炉床面积和再生炉的炉床总面积。
炉体计算应从底部炉层开始,沿着活化气体流动的方向进行。
活化气体与被耙动的炭床之间的热传递可通过以下公式计算:
q=UA(LMDT)
U=热传递经验系数,Btu/hr/ft2/℉
A=公称炉床面积
(LMDT)=同一炉层中气相液相对数平均温差
给定炉层的活化气体温度是恒定不变的,等同于热电偶感应,等同于活化气体完成热传递后离开炉层时的温度,气体传递的热量用于加热蒸汽,补偿设备热损失。
在200-500℉的低温条件下,经验系数U大约为3,在1700-1800℉条件下,U约为20,在这个范围内,系数变化与温度成线性关系。
以下列数据为例,
原始炭料,作为吸附剂的用量2000lb/hr
吸附质负荷,0.3lb/lb原始炭600lb/hr
吸附质炭化物,吸附质的40%240lb/hr
气化反应条件:
保留小孔隙
1700℉
H2O=3xH2O
H2O+H2O=或>40%体积
以上条件下,气相反应速率为0.4lb/hr/ft2(见实验数据)
燃料、天然气CH4约1000Btu/ft3
吸附质热值---10,000Btu/lb
进料水分–40%收到基
以上仅列出计算公式及计算时应考虑的原则和因素,气体组成和炉膛温度的最终计算结果在图26-4中标出(H2O+C和CO2+C的反应热与等重的C+H2O反应热平衡——用于运算的简要说明)。
活化区
炉床面积计算
反应区炉床面积计算如下:
240lb/hrx1.25/0.4lb/hr/ft2=750ft2
吸附质焦碳乘以系数1.25来包括过量气化的碳。
原始炭损失率可表示为240磅/时炭化物的25%,即损失量为60磅/时,原始炭的3%。
根据以上计算,炉床面积可以有以下几种选择:
2个内径为23.5英尺的炉膛,3个内径为20英尺的炉膛或4个内径16.5英尺的炉膛。
活化区尺寸需要等其他反应区域尺寸确定后做最终决定。
本示例中选择了4个内径16.5英尺的炉膛。
燃料流、空气流、蒸汽流的确定
在必要时活化区四个炉层中的每一层内都会通过注入蒸汽、空气,还可能注入燃料来控制气化反应的气氛及反应温度。
内径16.5英尺的底部炉膛的炉床面积为200ft2,比其顶部炉层的面积要大,因为需要从直径16.5英尺的圆形面积中减去一个落料口和中轴所占面积。
按气化反应速率0.4lb/hr/ft2计算,可得出底部炉膛参加反应的炭的质量为80磅,即62/3摩尔。
试验A–蒸汽和空气,不加燃料,最大反应速率,温度1700℉
如果在本层中只注入蒸汽和空气,燃烧80磅炭可释放热量1,126,000Btu/hr;注入12,000scfh空气与烟气反应时需要消耗300,000Btu/hr。
加热12,375scfh蒸汽消耗432,000Btu。
离开本层时,活化气体中含有:
H2O
12,375scfh
CO2
2,520scfh
N2
9,480scfh
合计
24,381scfh
水蒸汽几乎是CO2含量的6倍,约占活化气体总体积的50%。
气相下的实际反应为H2O和CO2与碳反应生成H2和CO。
在活化气体中含有过量O2的情况下,可见到炉床上笼罩着一层CO燃烧而产生的蓝色。
在炭床上方漂浮着一层CO和H2混合气体层,O2无法穿过这层气体与炭料发生反应。
除非直接向炭料中注入空气。
笔者曾在以上工艺条件下实际操作多膛炉,未见对产品质量和炭料损失率有严重影响。
但个人认为在1700℉,最大反应速率,H2O含量60%,无CO和H2的条件下进行活化反应很可能不可行。
试验B-