毕业设计 数控机加工零件剖析.docx
《毕业设计 数控机加工零件剖析.docx》由会员分享,可在线阅读,更多相关《毕业设计 数控机加工零件剖析.docx(28页珍藏版)》请在冰豆网上搜索。
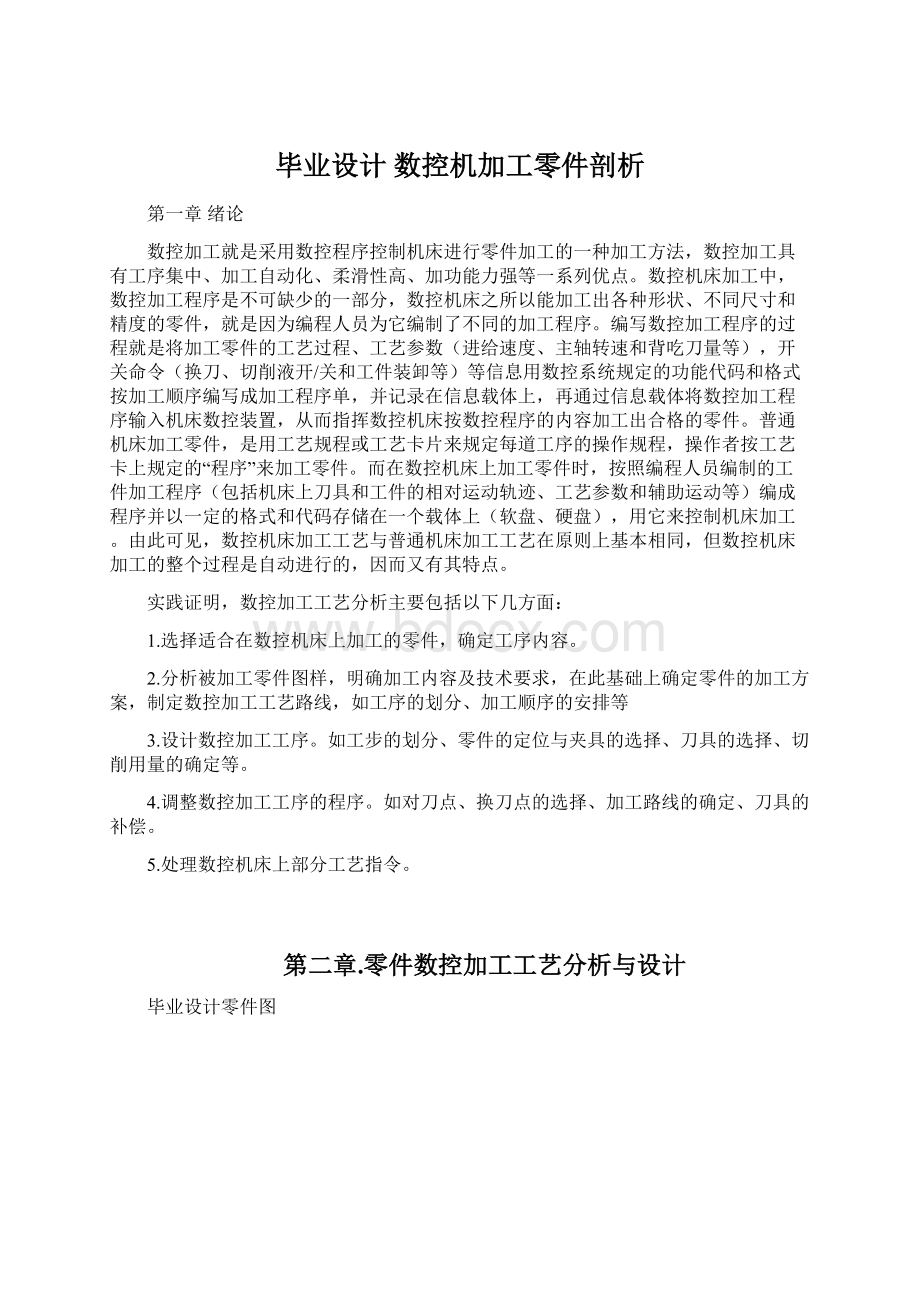
毕业设计数控机加工零件剖析
第一章绪论
数控加工就是采用数控程序控制机床进行零件加工的一种加工方法,数控加工具有工序集中、加工自动化、柔滑性高、加功能力强等一系列优点。
数控机床加工中,数控加工程序是不可缺少的一部分,数控机床之所以能加工出各种形状、不同尺寸和精度的零件,就是因为编程人员为它编制了不同的加工程序。
编写数控加工程序的过程就是将加工零件的工艺过程、工艺参数(进给速度、主轴转速和背吃刀量等),开关命令(换刀、切削液开/关和工件装卸等)等信息用数控系统规定的功能代码和格式按加工顺序编写成加工程序单,并记录在信息载体上,再通过信息载体将数控加工程序输入机床数控装置,从而指挥数控机床按数控程序的内容加工出合格的零件。
普通机床加工零件,是用工艺规程或工艺卡片来规定每道工序的操作规程,操作者按工艺卡上规定的“程序”来加工零件。
而在数控机床上加工零件时,按照编程人员编制的工件加工程序(包括机床上刀具和工件的相对运动轨迹、工艺参数和辅助运动等)编成程序并以一定的格式和代码存储在一个载体上(软盘、硬盘),用它来控制机床加工。
由此可见,数控机床加工工艺与普通机床加工工艺在原则上基本相同,但数控机床加工的整个过程是自动进行的,因而又有其特点。
实践证明,数控加工工艺分析主要包括以下几方面:
1.选择适合在数控机床上加工的零件,确定工序内容。
2.分析被加工零件图样,明确加工内容及技术要求,在此基础上确定零件的加工方案,制定数控加工工艺路线,如工序的划分、加工顺序的安排等
3.设计数控加工工序。
如工步的划分、零件的定位与夹具的选择、刀具的选择、切削用量的确定等。
4.调整数控加工工序的程序。
如对刀点、换刀点的选择、加工路线的确定、刀具的补偿。
5.处理数控机床上部分工艺指令。
第二章.零件数控加工工艺分析与设计
毕业设计零件图
图2
图1
2.1零件工艺性分析
如图所示的典型轴类零件,有支承传动零件,传递扭距,承受载荷的作用,它属于轴零件,由圆柱、不规则圆球、导角、螺纹、孔、锥面、螺尾退到槽。
锥面的作用是使零件装配时配合面易与配合;螺纹用于安装锁紧螺母和调整螺母。
根据工作性能和条件该图规定了轴套内、外圆表面的尺寸和表面粗糙度值。
这些技术要求必须在加工中得以保证。
该轴套的关键工序是φ46mm的外圆柱面,φ24mm,φ20mm和φ29.7mm内圆柱面的加工,同时内孔深22.5mm和25mm也是重要的加工尺寸。
该零件的整个加工过程中车端面、外圆、钻孔、镗孔、倒角、锥面、螺纹、割槽、内(外)螺纹
2.2确定毛坯
该零件属于中、小轴套,45钢因其机械性能好、易切削,广泛用于机械制造,查《机制制造工艺设计简明手册》见表格,故选用φ50mm的热轧圆钢作为毛坯。
2.3确定主要表面的加工方法
该轴套大都是回转表面,并且精度要求不是很高,主要采用车削成形。
外圆的表面加工方案可为:
粗车→精车
内圆的表面加工方案可为:
钻孔→粗镗→精镗
2.4确定定位基准
正确合理地选择定位基准是制定机械加工工艺规程的一项重要工作。
在零件机械加工的第一道工序里,使用毛坯上未经加工的表面来定位,又由于它是空心轴,所以粗基准采用热轧圆钢的毛坯外圆,可以保证零件的技术要求。
中心孔加工采用三爪自定心卡盘装夹热轧圆钢的毛坯外圆,车端面,钻中心孔。
然后以已车过的外圆作为基准,采用三爪自定心卡盘装夹,车另一端面,外圆及钻孔。
轴套的定位基准的确定也是一样的。
2.5工艺路线的制定
综合上述分析,按照先右后左,先外后内,先粗后细的原则确定轴套配合零件的工艺路线如下:
(Ⅰ)下料→车右端面→粗车外圆→精车外圆→切槽→切螺纹→卸下掉头装夹→车端面→钻孔→粗车外圆→精车外圆→粗镗孔→精镗孔→检验。
(Ⅱ)下料→车右端面→钻孔→粗车外圆→精车外圆→粗镗孔→精镗孔→切螺纹→检验。
在上边的工艺路线的制定中:
(Ⅰ)中,工序8不能和前面的工序颠倒,,因为当零件上有平面可以作为定位基准时,总是先加工平面,再以平面定位加工孔,保证孔和平面之间的位置精度,这样定位比较稳定,装夹也方便。
同时若在毛坯表面上钻孔,钻头容易引偏,所以从保证加工孔的加工精度出发,也应该当加工平面在加工该平面上的孔。
(Ⅱ)中,工序3不能和后面的工序颠倒,因为孔加工属于粗加工,余量大,发热多,变形也大,会使得加工精度难以保持。
2.6切削用量确定
背吃刀量根据机床、工件和刀具的刚度来决定,在刚度允许的条件下,应尽可能使背吃刀量等于工件的加工余量,这样可以减少走刀次数,提高生产效率。
为了保证加工表面质量,可留少量精加工余量,一般0.2一0.5mm。
总之,切削用量的具体数值应根据机床性能、相关的手册并结合实际经验用类比方法确定。
所以,合理的切削用量,能提高加工零件的表面质量,减少刀具的磨损。
同时,建立一张切削用量表,主要是为了防止遗忘和方便编程.
2.7夹具的选择与装夹方案的确定
该图为典型轴类零件,属于轴类零件的加工,形状规则,所以夹具用三爪自定心卡盘装夹就可以了。
而且三爪自定心卡盘结构简单,零件易装夹。
2.8加工设备的选用
根据图形的形状、结构特点、外形和加工精度,选用西门子数控系统的CK6140型数控车床。
2.9加工与工步的划分
该零件加工工序依次装夹次数划分,可分为三道工序,即工序1为装夹零件左端加工零件右端内外型面,工序2掉头装夹零件右端加工零件左端内外型面和工序3装夹零件左端加工零件右端内外型面。
具体工序、工步分布如下:
(1)装夹零件左端加工零件右端内外型面
1)下料,用切割机切Φ50的45#热轧圆钢,长度为100mm。
2)装夹毛坯左端,加工右端,棒料伸出卡盘外约80mm,找正后夹紧。
3)用1号刀车平端面。
4)用1号刀采用G95循环加工右端轮廓
5)用3号刀进行切槽加工
6)用5号刀采用G97进行螺纹加工循环。
(2)掉头装夹零件左端加工零件右端内外型面
1)卸下工件用铜皮包住已加工过的Φ36的外圆,帮料伸出卡盘外约40mm,找正后加紧。
2)用1号刀车车端面并控制总长在97±05mm内。
3)把Φ20锥柄麻花钻装入尾座,移动尾架接近端面后锁紧,主轴以400r/min,转动尾座手轮钻Φ20的孔,转5圈多一些(尾架螺纹导程为5mm)使孔深大于25小于26。
然后通过车端面来控制孔深25。
(钻孔时需开切削液)
4)用1号刀采用G95循环进行零件左端面循环的轮廓粗加工。
用粗加工完用1号刀采用G95循环进行零件左端面的轮廓循环精加工。
5)用2刀采用G95进行零件内孔的粗、精镗循环加工,X轴的精加工余量应为负值。
(3)装夹零件左端加工零件右端内外型面。
1)下料,用切割机切Φ50的45#热轧圆钢,长度为70mm。
2)装夹毛坯左端,加工右端,棒料伸出卡盘外约50mm,找正后夹紧。
3)用1号刀车平端面。
4)把Φ22锥柄麻花钻装入尾座,移动尾架接近端面后锁紧,主轴以400r/min,转动尾座手轮钻Φ20的孔,转5圈多一些(尾架螺纹导程为5mm)使孔深大于46小于47。
然后通过车端面来控制孔深46。
(钻孔时需开切削液)
5)用1号刀采用G95进行零件右端面的轮廓循环粗加工。
用粗加工完用1号刀采用G95进行零件右端面的轮廓循环精加工。
6)用2刀采用G95进行零件内孔的粗镗循环加工,X轴的精加工余量应为负值。
粗加工完用2号刀采用G95进行零件内孔的精镗循环加工。
7)4号刀采用G97进行螺纹加工循环。
(主轴转速为350r/min)
8)掉头加工左端的端面和圆弧倒角
第三章.零件数控加工工艺分析与设计
3.1零件工艺性分析
如图1所示的典型轴类零件,有支承传动零件,传递扭距,承受载荷的作用,它属于轴零件,由圆柱、不规则圆球、导角、螺纹、孔、锥面、螺尾退到槽。
锥面的作用是使零件装配时配合面易与配合;螺纹用于安装锁紧螺母和调整螺母。
根据工作性能和条件该图规定了轴套内、外圆表面的尺寸和表面粗糙度值。
这些技术要求必须在加工中得以保证。
该轴套的关键工序是φ46mm的外圆柱面,φ24mm,φ20mm和φ29.7mm内圆柱面的加工,同时内孔深22.5mm和25mm也是重要的加工尺寸。
该零件的整个加工过程中车端面、外圆、钻孔、镗孔、倒角、锥面、螺纹、割槽、内(外)螺纹
3.2确定毛坯
该零件属于中、小轴套,45钢因其机械性能好、易切削,广泛用于机械制造,查《机制制造工艺设计简明手册》见表格,故选用φ50mm的热轧圆钢作为毛坯。
3.3确定主要表面的加工方法
该轴套大都是回转表面,并且精度要求不是很高,主要采用车削成形。
外圆的表面加工方案可为:
粗车→精车
内圆的表面加工方案可为:
钻孔→粗镗→精镗
3.4确定定位基准
正确合理地选择定位基准是制定机械加工工艺规程的一项重要工作。
在零件机械加工的第一道工序里,使用毛坯上未经加工的表面来定位,又由于它是空心轴,所以粗基准采用热轧圆钢的毛坯外圆,可以保证零件的技术要求。
中心孔加工采用三爪自定心卡盘装夹热轧圆钢的毛坯外圆,车端面,钻中心孔。
然后以已车过的外圆作为基准,采用三爪自定心卡盘装夹,车另一端面,外圆及钻孔。
轴套的定位基准的确定也是一样的。
3.5工艺路线的制定
综合上述分析,按照先右后左,先外后内,先粗后细的原则确定轴套配合零件的工艺路线如下:
(Ⅰ)下料→车右端面→粗车外圆→精车外圆→切槽→切螺纹→卸下掉头装夹→车端面→钻孔→粗车外圆→精车外圆→粗镗孔→精镗孔→检验。
(Ⅱ)下料→车右端面→钻孔→粗车外圆→精车外圆→粗镗孔→精镗孔→切螺纹→检验。
在上边的工艺路线的制定中:
(Ⅰ)中,工序8不能和前面的工序颠倒,,因为当零件上有平面可以作为定位基准时,总是先加工平面,再以平面定位加工孔,保证孔和平面之间的位置精度,这样定位比较稳定,装夹也方便。
同时若在毛坯表面上钻孔,钻头容易引偏,所以从保证加工孔的加工精度出发,也应该当加工平面在加工该平面上的孔。
(Ⅱ)中,工序3不能和后面的工序颠倒,因为孔加工属于粗加工,余量大,发热多,变形也大,会使得加工精度难以保持。
3.6切削用量确定
随着数控机床在生产实际中的广泛应用,数控编程已经成为数控加工中的关键问题之一。
在数控程序的编制过程中,确定切削用量也显得十分重要。
因此,编程人员必须熟悉切削用量的确定原则,数控编程时,编程人员必须确定每道工序的切削用量,并以指令的形式写人程序中。
切削用量包括主轴转速、背吃刀量及进给速度等。
背吃刀量根据机床、工件和刀具的刚度来决定,在刚度允许的条件下,应尽可能使背吃刀量等于工件的加工余量,这样可以减少走刀次数,提高生产效率。
为了保证加工表面质量,可留少量精加工余量,一般0.2一0.5mm。
总之,切削用量的具体数值应根据机床性能、相关的手册并结合实际经验用类比方法确定。
所以,合理的切削用量,能提高加工零件的表面质量,减少刀具的磨损。
同时,建立一张切削用量表,主要是为了防止遗忘和方便编程。
该零件切削用量的选择,主要参照《金属切削工艺设计用量》选取,具体选取数值参看零件数控加工工艺卡片。
3.7夹具的选择与装夹方案的确定
该图为典型轴类零件,属于轴类零件的加工,形状规则,所以夹具用三爪自定心卡盘装夹就可以了。
而且三爪自定心卡盘结构简单,零件易装夹。
3.8加工设备的选用
根据图形的形状、结构特点、外形和加工精度,选用西门子数控系统的CK6140型数控车床。
3.9加工与工步的划分
该零件加工工序依次装夹次数划分,可分为三道工序,即工序1为装夹零件左端加工零件右端内外型面,工序2掉头装夹零件右端加工零件左端内外型面和工序3装夹零件左端加工零件右端内外型面。
具体工序、工步分布如下:
(1)装夹零件左端加工零件右端内外型面
1)下料,用切割机切Φ50的45#热轧圆钢,长度为100mm。
2)装夹毛坯左端,加工右端,棒料伸出卡盘外约80mm,找正后夹紧。
3)用1号刀车平端面。
4)用1号刀采用G95循环加工右端轮廓
5)用3号刀进行切槽加工
6)用5号刀采用G97进行螺纹加工循环。
(2)掉头装夹零件左端加工零件右端内外型面
1)卸下工件用铜皮包住已加工过的Φ36的外圆,帮料伸出卡盘外约40mm,找正后加紧。
2)用1号刀车车端面并控制总长在97±05mm内。
3)把Φ20锥柄麻花钻装入尾座,移动尾架接近端面后锁紧,主轴以400r/min,转动尾座手轮钻Φ20的孔,转5圈多一些(尾架螺纹导程为5mm)使孔深大于25小于26。
然后通过车端面来控制孔深25。
(钻孔时需开切削液)
4)用1号刀采用G95循环进行零件左端面循环的轮廓粗加工。
用粗加工完用1号刀采用G95循环进行零件左端面的轮廓循环精加工。
5)用2刀采用G95进行零件内孔的粗、精镗循环加工,X轴的精加工余量应为负值。
(3)装夹零件左端加工零件右端内外型面。
1)下料,用切割机切Φ50的45#热轧圆钢,长度为70mm。
2)装夹毛坯左端,加工右端,棒料伸出卡盘外约50mm,找正后夹紧。
3)用1号刀车平端面。
4)把Φ22锥柄麻花钻装入尾座,移动尾架接近端面后锁紧,主轴以400r/min,转动尾座手轮钻Φ20的孔,转5圈多一些(尾架螺纹导程为5mm)使孔深大于46小于47。
然后通过车端面来控制孔深46。
(钻孔时需开切削液)
5)用1号刀采用G95进行零件右端面的轮廓循环粗加工。
用粗加工完用1号刀采用G95进行零件右端面的轮廓循环精加工。
6)用2刀采用G95进行零件内孔的粗镗循环加工,X轴的精加工余量应为负值。
粗加工完用2号刀采用G95进行零件内孔的精镗循环加工。
7)4号刀采用G97进行螺纹加工循环。
(主轴转速为350r/min)
8)掉头加工左端的端面和圆弧倒角
4.0刀具的卡片
工件1
工步号
刀具号
刀具名称
加工部位
1
T1
外圆车刀
粗精加工右端面
2
T2
切槽刀
割槽
3
T3
外螺纹车刀
外螺纹
4
T1
外圆车刀
粗精加工右端面
5
T5
钻头
钻20的内孔Φ
6
T1
外圆车刀
粗精加工右轮廓
7
T6
镗刀
粗精加工左内轮廓
工件2
工步号
刀具号
刀具名称
加工部位
1
T1
外援车刀
右端面
2
T5
钻头
钻22的孔
3
T1
外圆车刀
粗精加工外圆轮廓
4
T3
外螺纹车刀
外螺纹
5
T6
镗刀
粗精加工内轮廓
6
T7
倒角刀
车倒角
5.0工艺卡片
江苏信息职业技术
零件号
1
工序号
工序名称
夹具
刀具
名称
规格
名称
规格
1
装夹零件左端加工零件右端内外型面
专用车夹具
2
用切割机切Φ50的45#热轧圆钢,长度为100mm。
3
装夹毛坯左端,加工右端,棒料伸出卡盘外约80mm,找正后夹紧
专用车夹具
4
用1号刀车平端面
专用车夹具
外圆车刀
45号钢
5
用1号刀采用G95循环加工右端轮廓
专用车夹具
外圆车刀
45号钢
6
用2号刀进行切槽加工
专用车夹具
割槽刀
5MM
7
用3号刀采用G97进行螺纹加工循环
专用车夹具
外螺纹刀
8
夹零件左端加工零件右端内外型面
9
下工件用铜皮包住已加工过的Φ36的外圆,帮料伸出卡盘外约40mm
专用车夹具
10
用1号刀车车端面并控制总长在97±05mm内
专用车夹具
外圆车刀
45号钢
11
把Φ20锥柄麻花钻装入尾座
专用车夹具
麻花钻
12
1号刀采用G95循环进行零件左端面循环的轮廓粗加工
专用车夹具
外圆车刀
45号钢
13
用6刀采用G95进行零件内孔的粗、精镗循环加工,X轴的精加工余量应为负值。
专用车夹具
镗刀
40Cr
江苏信息职业技术
零件号
2
工序号
工序名称
夹具
刀具
名称
规格
名称
规格
1
装夹零件左端加工零件右端内外型面
专用车夹具
2
切割机切Φ50的45#热轧圆钢,长度为70mm
专用车夹具
3
用1号刀车平端面
专用车夹具
外圆车刀
45号钢
4
钻Φ20的孔
专用车夹具
麻花钻
5
用1号刀采用G95进行零件右端面的轮廓循环粗加工
专用车夹具
外圆车刀
45号钢
6
用1号刀采用G95进行零件右端面的轮廓循环精加工
专用车夹具
外圆车刀
45号钢
7
6刀采用G95进行零件内孔的粗镗循环加工
专用车夹具
镗刀
40Cr
8
用6号刀采用G95进行零件内孔的精镗循环加工
专用车夹具
镗刀
40Cr
9
3号刀采用G97进行螺纹加工循环
专用车夹具
外螺纹刀
10
掉头加工左端的端面和圆弧倒角
专用车夹具
倒角刀
45号钢
第四章主要加工步骤及加工程序
1.确定编程原点,车床上编程坐标原点的位置是任意的,它是编程人员在编制程序时根据零件的特点选定的,为了编程方便,一般要根据工件的形状和标注尺寸的基准及计算最方便的原则来确定工件上某一个为编程坐标原点
2.编程坐标原点应尽量在精度的精度表面,以提高被加工精度。
3.对称的零件,编程坐标原点应设在对称中心上
4.Z轴方向的零件一般设在工作表面
本设计选择零件⊙20圆的圆心为工件编程X、Z轴的工作坐标原点
5.基础参数的设定
CYCLE95指令
参数
含义及数字范围
参数
含义及数字范围
R105
加工方式:
数值1~12
R110
粗加工退刀量
R106
精加工余量,无符号
R111
粗加工进给量
R108
背吃刀量
R112
精加工进给量
R109
粗加工切入角
R105为加工方式参数,纵向加工时,进刀方向沿着Z轴方向进行;横向加工时,进刀方向则沿着X轴方向进行,见下表:
数值
纵向∕横向
外部∕内部
粗加工∕精加工∕综合加工
1
纵向
外部
粗加工
2
横向
外部
粗加工
3
纵向
内部
粗加工
4
横向
内部
粗加工
5
纵向
外部
精加工
6
横向
外部
精加工
7
纵向
内部
精加工
8
横向
内部
精加工
9
纵向
外部
综合加工
10
横向
内部
综合加工
11
纵向
内部
综合加工
12
横向
外部
综合加工
CYCLE97螺纹切削循环参数
参数
含义及数值范围
参数
含义及数值范围
R100
螺纹起始点直径(X向)
R109
空刀导入量,无符号
R101
螺纹起始点直径(Z向)
R110
空刀退出量,无符号
R102
螺纹终点直径(X向)
R111
螺纹深度,无符号
R103
螺纹纵向终点坐标(Z向)
R112
起始点偏移,无符号
R104
螺纹导程值,无符号
R113
粗切削次数,无符号
R105
加工类型:
数值1(外螺纹),数值2(内螺纹)
R114
螺纹线数,无符号
R106
精加工余量,无符号
6.加工程序
一1.车工件1右端面
2.粗、精加工件右端面轮廓至尺寸要求
M03S600F100T1D1
G00X54Z10(起刀点,也是循环切削的起点)
---chen=“FC1”
R105=1R106=0.5R108=2.5(1代表纵外部粗加工)
R109=0R110=100R112=50(具体的含义参见LCYC95参数)
G00X60Z150(回到换刀点)
M04(主轴停住,程序结束,检查粗加工后尺寸是否达到21mm,然后通过刀具补偿确保精加工0.5*2mm)
M00
M03S800F50T01(精加工开始)
G0X35(回到循环起点)
Z2
CYCLE95
子程序为:
FC1(子程序名)
G01X0Z2(准备加工零件)
R1=0(通过Z变量,即Z=0,到坐标原点)
CH1:
G01X=2*R1Z=-(R1*R1/10)(抛物线的变量表达式)
IFR1≤10GOTOBCH1(条件句,如果满足,跳出此程序,执行下一个程序语句加工,不然返回加工语句CH1继续加工)
G01Z-26.5(加工⊙20mm的圆柱)
X23.8(6g=0.236)(为后工序加工螺纹做准备,C1.5倒角的起点)
X26.8Z-28(倒角C1.5的终点)
Z-49.5(加工⊙27mm的圆柱为下步
槽做准备)
X32(到R2圆角的起点)
N70G03X36Z-51.5CR=2(车圆倒角R2)
N80G01Z-64.5(加工⊙36mm的圆柱)
X43(⊙46mm倒边的C1.5的起点)
X46Z-66(倒边的终点)
X50
N90M17(子程序结束)
IF---条件语句表示有条件跳转,其程序格式为:
IF(条件) GOTOF(标记符);向前跳转
或IF(条件)GOTOB(标记符);向后跳转
条件语句程序
G00X0Z2快速进刀
G01X0Z0工件椭圆零点
R1=25椭圆长轴25
N40LQ2:
R3=2*16*SQRT(1-R1*R1/25/25)椭圆X轴变了表达式
N50G01X=R3Z=-(25-R1)用直线插补拟合椭圆曲线
N60R1=R1-0.5椭圆长轴Z轴变量每次减0.5mm
IFR3>40-R8*2GOTOFLQ3
如果刀具在X向超过毛坯直径,返回椭圆加工起始点,以减少空刀量
IFR1<0GOTOFLQ3如果Z变量小于0,椭圆未加工完毕,往下跳转至LQ3标记,返回起始点
IFR1<=25GOTOBLQ2如果Z变量小于等于25,椭圆未加工完毕,返回LQ2标记处再粗加工
LQ3:
G91GOOX2X方向退刀2mm
G90G00Z2返回椭圆加工起始点
M17子程序结
3.切槽5×⊙23至尺寸要求
M03S350F35T2D2
G00X38.8(与下步一块定位切槽刀的起点)
Z-49.5
G01X23.3(工进,留有0.3mm的精加工量,故加工23.3mm)
X38
Z-47(从新定位,待加工倒角C1.5mm)
X27(刀具靠近工件)
X24Z-48.5(加工出倒角C1.5mm)
X23(刀宽4mm,槽5mm,加工余下的1mm)
Z-49.5(加工余下0.3mm×5mm的裕量降低工件的粗糙度)
X60(回到换刀点)
Z150
4.粗、精加工件I的螺纹至尺寸要求
M03S500T3D3
GOOX27Z-10(起刀点,循环起点)
R100=27R101=-26.5R102=27R103=-39R104=1.5R105=1
R106=0.5R109=6R110=2R111=0.974R112=0R113=6
R114=1
CYCLE97
加工后2维图
5.车件Ⅰ左端面至长度尺寸要求
M03S600F100T1D1
G00X54