高压溶出设备安装方案.docx
《高压溶出设备安装方案.docx》由会员分享,可在线阅读,更多相关《高压溶出设备安装方案.docx(26页珍藏版)》请在冰豆网上搜索。
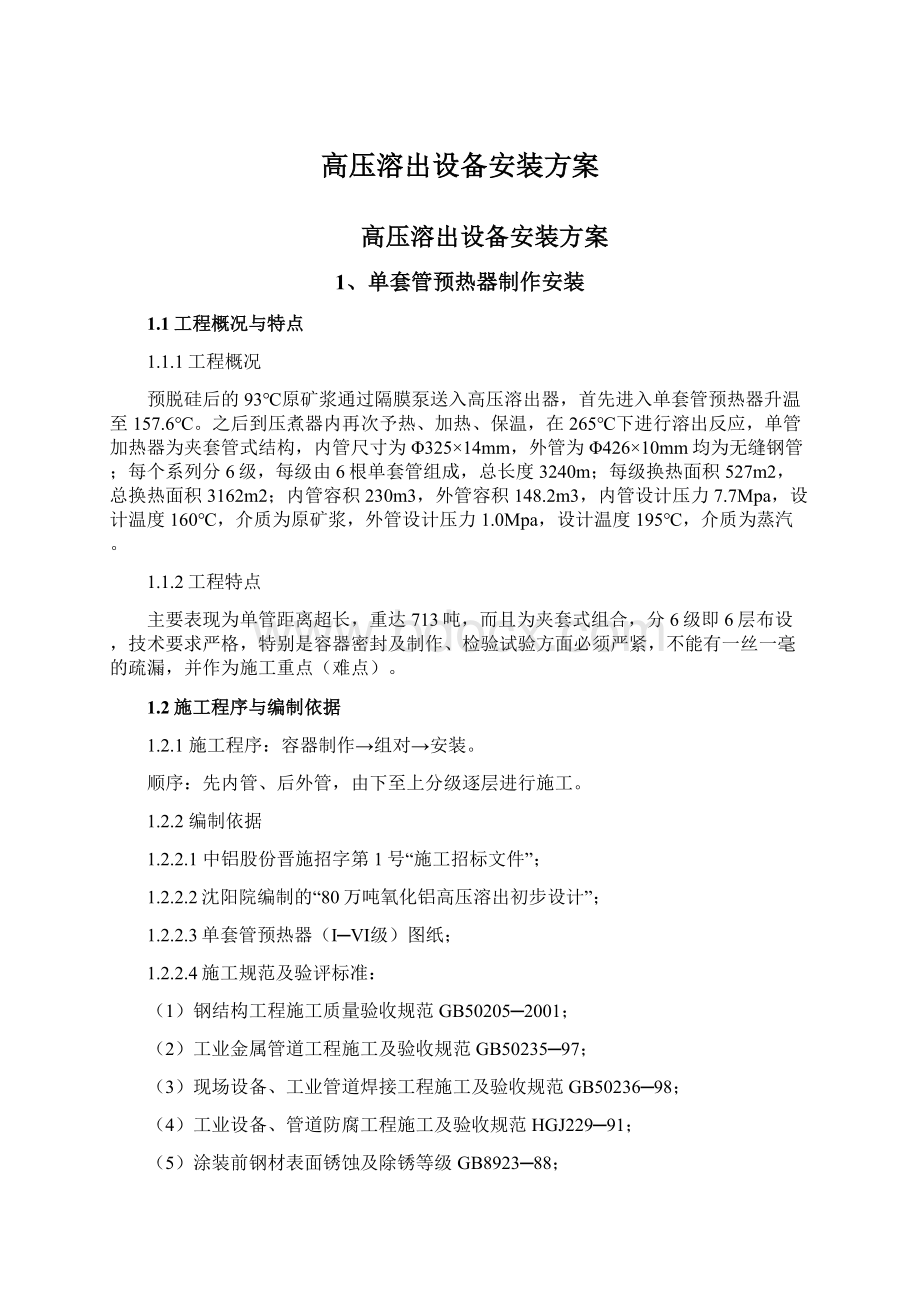
高压溶出设备安装方案
高压溶出设备安装方案
1、单套管预热器制作安装
1.1工程概况与特点
1.1.1工程概况
预脱硅后的93℃原矿浆通过隔膜泵送入高压溶出器,首先进入单套管预热器升温至157.6℃。
之后到压煮器内再次予热、加热、保温,在265℃下进行溶出反应,单管加热器为夹套管式结构,内管尺寸为Φ325×14mm,外管为Φ426×10mm均为无缝钢管;每个系列分6级,每级由6根单套管组成,总长度3240m;每级换热面积527m2,总换热面积3162m2;内管容积230m3,外管容积148.2m3,内管设计压力7.7Mpa,设计温度160℃,介质为原矿浆,外管设计压力1.0Mpa,设计温度195℃,介质为蒸汽。
1.1.2工程特点
主要表现为单管距离超长,重达713吨,而且为夹套式组合,分6级即6层布设,技术要求严格,特别是容器密封及制作、检验试验方面必须严紧,不能有一丝一毫的疏漏,并作为施工重点(难点)。
1.2施工程序与编制依据
1.2.1施工程序:
容器制作→组对→安装。
顺序:
先内管、后外管,由下至上分级逐层进行施工。
1.2.2编制依据
1.2.2.1中铝股份晋施招字第1号“施工招标文件”;
1.2.2.2沈阳院编制的“80万吨氧化铝高压溶出初步设计”;
1.2.2.3单套管预热器(Ⅰ─Ⅵ级)图纸;
1.2.2.4施工规范及验评标准:
(1)钢结构工程施工质量验收规范GB50205─2001;
(2)工业金属管道工程施工及验收规范GB50235─97;
(3)现场设备、工业管道焊接工程施工及验收规范GB50236─98;
(4)工业设备、管道防腐工程施工及验收规范HGJ229─91;
(5)涂装前钢材表面锈蚀及除锈等级GB8923─88;
(6)钢结构制作安装施工规程YB9254─95;
(7)钢制压力容器GB150─1998;
(8)钢制焊接常压容器JB/T4735─1997;
(9)压力容器无损检测JB4730─94;
(10)工业安装工程质量检验评定统一标准GB50252─94;
(11)工业金属管道工程质量检验评定标准GB50184─93;
(12)山西铝建设工程质量验收评定统一标准;
(13)工业设备及管道绝热工程施工及验收规范;
(14)工业设备及管道绝热工程设计规范等。
1.非标设备吊装方法
吊装设备分级吊装采用不同规格的汽车起重机(16t-40t),由底层往上根据高度变化而改变吊车的起重吨位,依据现场实际情况,可以同时增加吊车数量,以满足施工需要;吊车布置:
沿容器长度方向两侧分布,按工程需要充分发挥汽车吊的机动灵活特点,同时使用龙门架(自制)作为吊装配合设施,共同完成单套管预热器这条长龙的全过程施工吊装任务。
1.4施工方法与质量技术控制
1.4.1基础交验和支架安装
按设计和规范规定对单管预热器的基础施工进行验收和办理工序交接手续,对基础表面的平整度、标高及外形尺寸进行现场检测验收,同时划出容器的中心线及容器支架的中心线和位置线,作出明显的标记,给下步管架安装创造条件。
工作第一步为预热器支架安装、基础条件已具备,架的位置也已确定,接着就是现场组对、安装型钢结构支架,先安装两侧钢结构立柱,安装技术要求:
排柱中心线和单柱中心线偏差±5mm,横向两柱中心线偏差±3mm,各柱安装标高±3mm,最大偏差不超过8mm,柱安装垂直度1‰,且全高≯5mm,对角线长度差≯10mm,使用钢尺及磁力线坠现场检测同时作好容器支架安装技术记录。
安装立柱之后,先装下部第一层支架梁等构件,按设计要求确定梁上平面标高,允许偏差±2mm,以确保套管位置的准确性,同时安装柱间支撑和第一层梁间加固构件,确保支架整体稳定,最后用仪器检测作好施工记录;当下部一级套管完成后再安装第二层支持梁→再制作安装二级预热器套管,然后装第三层支持梁→三级套管,以此类推,直至六级全部完成,与此同时,支架也全部完工。
在整个支架分层安装时,也要分层实行仪器检测,确保各层及整架的安装达到规范要求及公司内部钢结构验评标准。
1.4.2夹套管制作、组装
施工顺序为分级进行,由下至上逐层展开的施工方法。
1.4.2.1材料检验:
每级(层)套管先制作内管即325×14mm无缝管,在制作前对所用管材履行检验程序,管材、管件须具有制造单位的质量证明书或合格证,且质量不得低于国家现行标准,具体:
无缝钢管应符合GB8163-92规定,且库前验收合格,外观质量合乎要求,表面无裂纹、缩孔、夹渣、折叠、重皮等缺陷;其锈蚀、凹陷、机械损伤深度等不应超过规定,尺寸偏差:
外径允偏±1.0%,壁厚允偏:
+15%~10%范围之内;当对实物有异议时,宜进行必要的无损检测、化学分析、力学性能实验,结果应当合格,否则不予使用。
设备所用锻件(带颈法兰)应符合JB4726-94“压力容器用碳素钢和低合金钢锻件”规定的Ⅲ级标准;法兰所用垫片按设计要求采用SU型钢带,材质为316L/Graflex的标准。
1.4.2.2施工方法与技术控制
(1)管道加工预制、组装程序
a单级套管施工程序
管材核对标识→检查调直→坡口加工→煨弯→内直管组对焊接→焊缝检验→水压试验→应力退火热处理→装配外管组焊→焊接法兰→外管空气吹扫→内外管封焊→焊缝检验→外管水压试验→外管焊缝消应热处理→内管空气吹扫→单级内管封连
bⅠ-Ⅵ级施工程序
c程序Ⅰ-Ⅵ级分级作完→级间连接→内管作全级水压试验→设备涂漆
总的说,分级进行由低到高分6级完成的顺序安排及作业施工,管道调直及坡口加工,煨制弯管及外管除锈涂第一道底漆等工序,可在加工厂预制完成,其他施工工序应在安装现场进行。
(2)夹套管加工
预制时应预留调整段余量50~100mm,外管在能保证套进内管的情况下,尽量接长并对口焊连,焊缝经射线照相检验合格再套入内管。
内外管相配前,依设计规定焊接支承块,以确保内外管间隙均匀,但应注意支承块不得妨碍管道胀缩。
a管子切割:
预热器每级两头管段应按实际长度进行切割,采用机械切割法,确保切口质量,切口端面倾斜偏差不大于管子外径的1%,且≯2mm;
b坡口加工:
内、外管接头处均应加工坡口,坡口尺寸形式,应采用60度单V形坡口,坡口加工表面粗糙度为12.5um,加工采用机械切削法在专用坡口机上进行,使用样板检测加工质量;
c弯管制作:
内管之间各级段连接及各级相互连接,均用180度弯管通过法兰连接,弯管制作时应挑选最好质量、壁厚正公差最大的直管段,在高频煨管机上成形,弯曲半径执行图纸规定,弯管质量控制:
不得有裂纹、皱纹,表面应光滑,弧度准确,加热煨管温度应控制在800~1000℃。
d管子对口:
在距接口中心200mm处测量平直度(下图)允许偏差1.5mm,且全长允偏≯5mm,采用对口器安装,确保管道平直度。
e管道除锈涂装
在喷砂抛丸房内集中采用机械方法除锈(对外管),除锈等级达到Sa2
级,进行非常彻底的除锈。
涂漆执行JB2536-80规定,先在容器(外管)外表面除锈后4小时之内喷涂第一遍底漆,焊口处50mm范围内暂留不涂,待焊接检验合格后补作。
(3)套管组对焊接
a焊接:
管段两环缝中心之间距离应大于200mm,焊缝距离弯管起弯点大于100mm,且不小于管外径,不得在焊缝上开孔,焊工必须持有中压钢管焊接合格证,并在有效使用期内;
焊缝质量控制措施:
对输送溶融介质管道的内表面焊缝应平整光滑,不得有突出的焊瘤,其质量应符合设计文件规定;针对本工程量大单一的特点,对内管、外管分别采取单独焊接试验的办法,以此选定最佳施焊方案和确定焊接工艺。
编制施工及焊接作业指导书,规范单套管预热器的施工程序、标准、技术要求及检验方法;焊接方法:
采用氩弧焊打底、手工焊封面和CO2气体保护焊,手工焊条型号为E4315,焊前烘干350~400℃,1~2小时,冷至200℃时放入保温筒(箱)内以备使用。
焊丝为H08Mn2si表面保持清洁无污染,坡口经过机械加工,对口时间隙大小由焊接试验确定最佳尺寸;层间清理:
坡口和每层焊道上的锈皮及焊渣,在下一步焊前应作彻底清涂,必要时使用砂轮和角向磨光机打磨显露金属表面,施焊时应填足焊层,盖面后完成焊缝的横断面应在整个焊口上均匀一致,焊缝表面不低于管子外表面,相邻焊层引弧点应相互错开,焊缝表面宽度应大于坡口表面宽度,焊接完成后将焊缝表面彻底清理干净。
焊工在自己完成的焊接管段上,打上钢印,以具有可追溯性,焊缝要求熔合、熔透、无裂纹、气孔、夹渣、电弧擦伤等缺陷,达到一级焊缝标准。
b每一级内管组对完成后,对焊缝进行无损射线检测及单根管作封闭式水压试验须确认合格;外管对口焊接完全与内管相同,不再重述,对外管上的进出料口、蒸汽入口、冷凝水口、不凝汽口、测温口等按设计位置先行开好,开口位置应避开焊缝,然后清除管内熔渣及一切杂物,确认管内清洁无物再套入内管,在保证套入情况下,外管预制尽量长些,此时内管表面已焊接支承块,以保两管之间隙。
夹套管内外管装配后同心度偏差≯2.5mm,装焊支承块时应给予保证。
c法兰焊接:
带颈凹凸法兰执行规范标准为:
JB/T4709-2000及GB/T9115.2;两坡口检查合格,法兰端面与管垂直,其偏差≤0.8mm,焊接工艺要求同上所述。
内管连接法兰和管口法兰均采用同一标准,与管体焊接。
1.4.3焊缝检验试验
1.4.3.1外观检验:
对所有焊缝进行100%外观检验,执行标准为Q/ZB74-78并填写质检表,合格率100%。
焊缝感观良好,焊波均匀,成形好,焊缝过渡平滑,表面清洁,焊缝余高+1.5~+0.5mm,凹值为0,错边值<0.1t,且≯2.0mm(t—壁厚),同时填写验评表。
1.4.3.2射线照相检验
内管及外管的对接焊接接头按设计要求应进行100%射线检测,执行标准为GB4730-94不低于Ⅱ级为合格,其他焊缝进行磁粉探伤,按JB4730-94规定I级为合格。
对于不合格缝返工处理,彻底清根后重焊,直至全部通过射线检测及磁粉探伤,检验后应出据全部检验报告和附照相底片。
1.4.3.3水压试验
应有专项试压方案并执行。
按设计规定,内管进行10Mpa水压试验,外管作1.3Mpa水压试验,内外管水压试验逐根与全级进行,具体操作:
水压进行时应缓慢升压,当升至工作压力时,暂停检查一下有无情况,正常无异时连续升压至试验压力,停压保持10分钟,然后降至设计压力,保压30分钟无渗漏为合格,当出现泄漏时压力降零泄水对泄漏处即速处理,然后重新试压直至合格;
外管打压同上进行,最后作I-Ⅵ级全级内管水压试验。
水压试验表按规定格式填写,同时办理会签手续。
1.4.4消除应力热处理
按设计要求设备制造完毕后进行消除应力热处理。
目的是为了降低或消除焊缝焊后的残余应力,防止焊缝及热影响区产生裂纹和应力腐蚀,“消应”处理应具备:
焊接工作已全部完成;焊缝无损检测合格;采用“电热法”消除应力,具体执行“消应”工艺方案及消应工艺规程SY/T4088-95及GB50236-98,GB/T7232-1999。
1.4.5套管吹扫
1.4.5.1内管吹扫:
拆下连接弯管,然后分级逐根进行压缩空气吹扫,空气流速不宜小于20m/s,当耙板上无铁锈、尘土、水分及其他杂物时,即为合格。
吹扫后填写专项记录。
1.4.5.2外管单根吹扫,打开所有管口,按如上所述,进行空气吹扫。
吹扫完毕进行单级封闭连接。
1.4.6夹套管安装
1.4.6.1安装方法:
安装Ⅰ—Ⅵ级分级进行,同时和夹套管的制作组对施工相结合同步进行的方法。
1.4.6.2安装程序:
由下层→上层逐级安装
1.4.6.3安装工艺:
(1)在每级(层)支持梁板平面上按设计尺寸划线或弹线,即每条夹套管的中心线和外形位置线并打洋锪眼和油漆显示,防止线被抹掉后看不清。
(2)当每条管按工艺程序施工结束后,按应处位置分别调整安装就位,为防止错位可以临时焊接限位块,同时按施工图作好的支、托架也安装入位,当每层6条管全部位置安装检查确认后,连接内管上180度弯管,使每级流程贯通。
(3)按照
(2)条内容对Ⅰ—Ⅵ级(层)逐级安装。
(4)技术偏差控制:
管中心线偏差±3mm,上下级相对应管中心线重合度偏差≯5mm,用吊线坠方法检查确认。
(5)管口连接:
测温口6个应放在每级出口处,法兰连接时,两面保持平行,允偏1‰,法兰两相邻螺栓孔应跨中安装,允偏±1mm;法兰密封垫片统一采用SU型钢带,Grafiex密封材料为30crMOA(应出示质量证明书),连接时使用专用扳手,按扭矩值进行对称紧固。
1.4.7预热器涂漆
管道预制时,外管及管件已在喷砂房,对设备外表面进行专门喷砂除锈和涂过第一道底漆,预热器安装后对外表面焊缝处先作补漆,涂漆前对预留段及焊缝进行表面彻底清理,必要时用角向机打磨光滑,然后进行涂漆;全部干燥后再对外表面进行全面的第二道涂漆,涂漆质量:
要求涂层表面均匀、无漏涂、无流挂等缺陷,涂层厚度用测厚仪测量,达到设计要求。
1.5质保措施
1.5.1建立本工程质保体系和管理控制体系,特别对单套管预热容器施工设立专门质保小组和预控机构,聘设专业技术负责人和专业技术责任工程师,如质保、材料、钢结构、容器、焊接工艺方面的责任工程师各负其责,各示其职,责任分明,从技术质量管理机构和技术力量配备上作好质量技术保证工作,求得施工高质量确保投产以后的安全。
1.5.2材料责任工程师主管并负责材料的供应质量,特别是所用钢材、钢件和焊材的验收,保管、供应发放等层层把关,并肩负直接责任。
1.5.3在总的施工方案指导下,编制施工技术交底书和主要控制过程作业指导书,同时根据施工进度提前编制焊接工艺、夹套管制作组装,容器检验试验、消应热处理等主要环节单项实施技术方案,对施工过程进行指导和监控,明确提出预防和纠正措施。
1.5.4制作安装每一工序单例技术专表,明确技术要求、技术标准及预控技术措施,明确提出单项技术质量主控单位及主控责任人及相关单位人,使技术质量工作具体化,并实行责任负责制,同时对主要工序同步实行技术质量记录表格化,对全施工过程、技术质量具备可追溯性,不折不扣的执行ISO9002质量贯标文件及质量程序文件,多、快、好、省地完成单套管预热器的制安工程。
2、溶出器、溶出自蒸发器和脉冲缓冲器安装
2.1设备概况与特点:
2.1.1溶出器(又称压煮器)按其功能分为预热、加热、保温三种溶出器,具体情况附下表:
溶出器简况附表(一个系列)
符号
溶出器名称
外径×高度(m)
面积F(㎡)
台数
单重(T)
总重(T)
传动装置电机(KW)
S-2
预热溶出器
φ2.8×16.081
F=540
6
115
690
45
S-3
加热溶出器
φ2.8×16.081
F=450
13
112
1456
45
S-4
保温溶出器
φ2.8×16.081
F=100
4
105
420
45
S-5
保温溶出器
φ2.8×16.081
1
95
95
45
工艺流程:
由单套管预热器出来的157.6℃原矿浆进入预热溶出器继续间接加热,升温至212.5℃(热源来自闪蒸槽的二次蒸汽),然后进入加热溶出器继续间接加热升至265℃,(热源来自高压饱和蒸汽,压力6.42Mpa,汽温280℃)最后进入保温溶出器,在265℃上保温50分钟,使矿浆进行充分的溶出化学反应(热源同加热溶出器热源)。
容器特点:
溶出器属压力溶器,内部介质温度和压力比较高,容器应具备可靠的安全性能,溶出器本身尺寸大,直径2.8m,高度16m,自重95T~115T,总重2661T,安装过程中应时刻保护设备的安全杜绝意外发生,施工要求具有可行的安全可靠的吊装方案及安全技术措施,很显然,设备吊装是施工重点(难点)。
2.1.2溶出自蒸发器和脉冲缓冲器:
溶出自蒸发器(又称闪蒸槽)由溶出器送来的265℃溶出料浆在11级溶出自蒸发器内进行逐级闪蒸降温,最后出口料浆温度已降至125℃,然后进入下台容器稀释槽。
两台脉冲缓冲器,料浆在容器内进行脉冲缓冲和控制料位,内部工作压力比较高,65~75bar,具体情况见附表:
设备附表
符号
溶器名称
直径×高度尺寸(m)
数量(台)
重量(T)
备注
S-6
溶出一级自蒸发器
φ3.6×9.7
2
110
2台重量220t
S-7
溶出二级自蒸发器
φ3.6×9.7
1
60
S-8
溶出三级自蒸发器
φ3.8×9.7
1
50
S-9
溶出四级自蒸发器
φ3.8×9.7
1
50
S-10
溶出五级自蒸发器
φ4.0×9.7
1
35
S-11
溶出六级自蒸发器
φ4.0×9.7
1
35
S-12
溶出七级自蒸发器
φ4.2×9.7
1
27
S-13
溶出八级自蒸发器
φ4.2×9.7
1
27
S-14
溶出九级自蒸发器
φ4.4×9.7
1
25
S-15
溶出十级自蒸发器
φ4.4×9.7
1
25
S-16
溶出十一级自蒸发器
φ4.4×9.7
1
25
S-38
脉冲缓冲器
φ2.5×9.35
1
55
容积8m3,,压力75bar
S-39
脉冲缓冲器
φ2.5×9.36
1
47
容积3m3,压力65bar
溶出自蒸器11级12台总重量579T,脉冲缓冲器2台总重102T,以上两种均为园柱形容器,单重由25T~110T,直径由2.5~4.4m,高度近10m,缓冲器安装位置标高在+7m层。
总的看设备特点仍是尺寸大,自重大,设计分布密集紧凑,间距小施工吊装场地不宽裕,需要动脑筋巧设计,使吊装设施、机具作到合理布置,设备吊装仍是工作重点,人身与设备的施工安全同样作为重点。
2.1.3高压溶出系列其他设备附表:
符号
容器名称
直径×高度尺寸(m)
数量(台)
重量(T)
备注
S-17
水封罐
φ0.8×1.79
2
0.7
S-18
1级冷凝水自蒸发器
φ0.8×1.79
1
0.7
S-19
2级冷凝水自蒸发器
φ0.8×1.79
1
0.7
S-20
3级冷凝水自蒸发器
φ1.0×1.9
1
0.8
S-21
4级冷凝水自蒸发器
φ1.0×1.9
1
0.8
S-22
5级冷凝水自蒸发器
φ1.0×1.9
1
0.8
S-23
6级冷凝水自蒸发器
φ1.2×2.09
1
1.2
S-24
7级冷凝水自蒸发器
φ1.2×2.09
1
1.2
S-25
8级冷凝水自蒸发器
φ1.2×2.09
1
1.2
S-26
9级冷凝水自蒸发器
φ1.4×2.19
1
1.5
S-27
10级冷凝水自蒸发器
φ1.4×2.19
1
1.5
S-28
11级冷凝水自蒸发器
φ1.4×2.19
1
1.5
S-29
二次汽冷凝水泵
2
0.251
2台0.502T,电机45KW
S-30-
新蒸汽冷凝水罐
φ1.4×2.4
6
5
6台30T
S-31
新蒸汽冷凝水闪蒸槽
φ4×7.9
2
30
2台60T
S-32
新蒸汽冷凝水泵
2
0.45
2台0.9T,电机15KW
S-33
稀释槽
φ6×8
2
22
2台44T
S-34
稀释泵
2
4.15
2台8.3T,电机185kw
S-35
洗水加热器
φ1.5×7.5
1
4.5
S-36
污水槽
φ3×3
3
3.43
3台10.28T,容积21m3
S-37
污水泵
3
0.69
3台2.07T,电机37KW
S-40
电动单梁桥式起重机
5t
1
3.43
S-41
电动单梁桥式起重机
5t
1
1.99
闪蒸槽用
S-42
出料吊车
1
3
闪蒸槽用
S-43
排风机
1
0.274
S-44
燃烧装置
3
1.2
两系列共用
合计
42
185.36
其它设备42台,186T,其中回转设备10台,吊车3台,燃烧设备3台,槽罐26台,冷凝水闪蒸槽φ4×7.9m,重30T;稀释槽φ6×8m,重22T,作为设备吊装重点项目。
2.2施工程序与编制依据
2.2.1施工程序:
2.2.1.1系列设备安装顺序:
压煮器① 溶出自蒸发器②
脉冲缓冲器③新蒸汽冷凝水闪蒸槽④
稀释槽⑤ 其他设备⑥
说明:
溶出压煮器①、溶出自蒸发器②、新蒸汽冷凝水闪蒸槽③、稀释槽④在设备基础完成以后具备安装条件在厂房钢结构未施工之前,进行吊装就位;具体见平面布置图。
对于脉冲缓冲器③和其他设备⑥可以在厂房各层施工之后,具备条件了,再进行设备安装。
2.2.1.2吊装程序:
吊装准备 设备吊装 就位找正;施工时可以逐台吊装,也可以两列设备同时进行安装。
⑴设备安装条件:
设备基础施工完,厂房钢结构尚未安装之前;
⑵设备安装顺序:
压煮器①24台 溶出自蒸发器②12台 冷凝水闪蒸槽④2台 稀释槽⑤2台;
⑶其他设备:
在厂房钢架及设备所在层施工之后再进行安装,先装2台脉冲缓冲器然后安装其他设备:
2.2.2方案编制主要依据:
2.2.2.1中铝山西企业80万吨氧化铝工程招标第一号文件;(压煮溶出工程)
2.2.2.2沈阳院设计:
“压煮溶出器工程初步设计”;单套管预热器装配图;
2.2.2.3执行的主要施工规范、验评标准、技术规程:
起重设备安装工程施工及验收规范GB50278-98;
机械设备安装工程施工及验收通用规范GB50231-98;
压缩机、风机、泵安装工程施工及验收规范GB50275-98;
工业金属管道工程施工及验收规范GB50235-97;
现场设备、工业管道焊接工程施工及验收规范GB50236-98;
钢制压力容器GB150-1998;
工业安装工程质量检验评定统一标准GB50252-94;
有色金属工业建设工程机械设备安装质量检验评定标准;
轻金属冶炼机械设备安装工程施工及验收规范YSJ412;
山西铝建设工程质量验收评定统一标准;
晋铝建设公司内部施工规程、标准;
2.3主要设备施工方法
2.3.1压煮溶出器安装及溶出自蒸发器安装
2.3.1.1设备基础验收:
对基础的几何尺寸、标高、预埋地脚螺栓和预埋垫板铁件进行检查,验收之后办理土建、安装交接手续;然后进行基础划线;设备中心线,基础相连部分的位置线以及方位、标高完后检查逐一确认,应有明显标记,以满足设备安装需要。
2.3.1.2溶出器本体的管束组配
⑴由于本体与管束分开到货,容器不是整体出厂而是分解发运。
根据这种情况,其施工程序应是先装配后吊装,依据制作装配一体原则,现场装配应由厂家负责完成,倘若施工单位组配,其施工方法如下:
a参加工程施工人员首先应深入仔细学习随机文件、说明书、设备图纸,特别是装配程序、工艺及装配技术与安全要求,充分结合部件的结构特点,掌握装配工作要领和重点。
设备安装责任工程师负责编制组装施工方案,经厂方、业主、监理审批后实施执行。
b根据方案要求,作好装配的准备工作,主要是所用的机具和材料准备、装配技术准备。
在组织上成立溶出器装配专业班组,配备工作经验丰富的精兵强将和专业技术人员,完成装配、安装的全部施工任务。
c配方法:
先拆下封头、孔盖和其它应拆部件,在吊装地点将容器本体端