电磁铸造概论.docx
《电磁铸造概论.docx》由会员分享,可在线阅读,更多相关《电磁铸造概论.docx(11页珍藏版)》请在冰豆网上搜索。
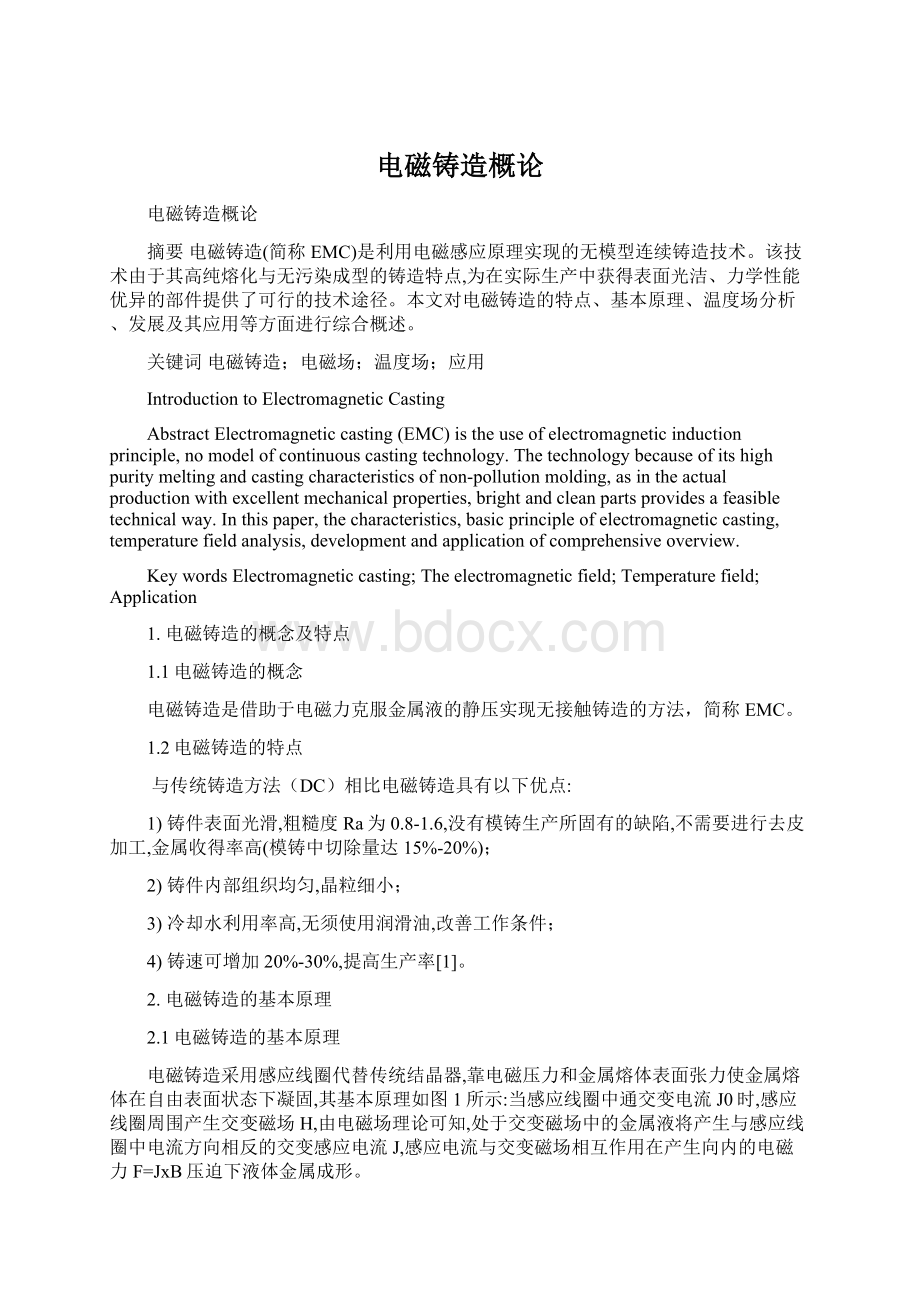
电磁铸造概论
电磁铸造概论
摘要电磁铸造(简称EMC)是利用电磁感应原理实现的无模型连续铸造技术。
该技术由于其高纯熔化与无污染成型的铸造特点,为在实际生产中获得表面光洁、力学性能优异的部件提供了可行的技术途径。
本文对电磁铸造的特点、基本原理、温度场分析、发展及其应用等方面进行综合概述。
关键词电磁铸造;电磁场;温度场;应用
IntroductiontoElectromagneticCasting
AbstractElectromagneticcasting(EMC)istheuseofelectromagneticinductionprinciple,nomodelofcontinuouscastingtechnology.Thetechnologybecauseofitshighpuritymeltingandcastingcharacteristicsofnon-pollutionmolding,asintheactualproductionwithexcellentmechanicalproperties,brightandcleanpartsprovidesafeasibletechnicalway.Inthispaper,thecharacteristics,basicprincipleofelectromagneticcasting,temperaturefieldanalysis,developmentandapplicationofcomprehensiveoverview.
KeywordsElectromagneticcasting;Theelectromagneticfield;Temperaturefield;Application
1.电磁铸造的概念及特点
1.1电磁铸造的概念
电磁铸造是借助于电磁力克服金属液的静压实现无接触铸造的方法,简称EMC。
1.2电磁铸造的特点
与传统铸造方法(DC)相比电磁铸造具有以下优点:
1)铸件表面光滑,粗糙度Ra为0.8-1.6,没有模铸生产所固有的缺陷,不需要进行去皮加工,金属收得率高(模铸中切除量达15%-20%);
2)铸件内部组织均匀,晶粒细小;
3)冷却水利用率高,无须使用润滑油,改善工作条件;
4)铸速可增加20%-30%,提高生产率[1]。
2.电磁铸造的基本原理
2.1电磁铸造的基本原理
电磁铸造采用感应线圈代替传统结晶器,靠电磁压力和金属熔体表面张力使金属熔体在自由表面状态下凝固,其基本原理如图1所示:
当感应线圈中通交变电流J0时,感应线圈周围产生交变磁场H,由电磁场理论可知,处于交变磁场中的金属液将产生与感应线圈中电流方向相反的交变感应电流J,感应电流与交变磁场相互作用在产生向内的电磁力F=JxB压迫下液体金属成形。
为使液柱侧面保持垂直,磁压力在液柱高度方向的分布必须与液柱静压力的分布一致,如图b所示,即满足Pm+Ps=ρgh,式中,Pm为磁压力,Ps为表面张力压力,ρ为熔体密度,g为重力加速度,h为液柱高度。
为达此目的,在液柱上方设置一屏蔽罩,它同时起抑制熔体流动以稳定液柱的作用。
冷却水在感应器下部喷向铸锭使液体金属凝固,铸机拖动底模向下运动,形成连铸过程[2]。
图1电磁铸造原理图
由上可知,电磁铸造技术彻底摆脱了传统的铸造概念,液体金属不与铸模接触,完全在电磁成形系统产生的电磁力下成形,并且在保持自由表面的状态下凝固,其表面接近镜面,又由于它受到较强磁场的电磁搅拌作用,金属内部组织得到改善,因此可获得优异的铸锭性能,实现了真正的无模铸造。
2.2电磁铸造中的温度场分析
为确定电磁铸造过程的各项工艺参数,保证铸锭的质量,温度场的分析是十分必要的。
电磁铸造过程中的温度场与普通连铸法相比有其特殊性,主要为:
1)液态金属由电磁力加以约束,无模壁与之接触,因此不存在由模壁向外传热的过程;
2)液相区存在着强烈的电磁搅拌作用,使得液相区内温差减少。
液相区内温度变化很小,几乎看不出有过热度,液穴形状明显比DC法平坦。
这主要是由于强烈的电磁搅拌作用使液相区内温度趋于一致,凝固界面拉平。
此外,由于电磁感应的边部加热作用,促进边部的固液界面下移。
还有冷却水直接喷在铸锭上,形成强烈的轴向冷却,造成近似定向凝固的传热方式,使液穴变平;
3)受强电磁场作用,液柱以及铸锭的表面层受到强烈的感应加热作用,在外部冷却条件较差的情况下,这一加热作用甚至可使铸锭升温;
4)冷却水直接喷在铸锭表面上,具有很高的冷却强度;
5)存在对EMC过程影响很大的非稳态过渡区,即温度场是运动的。
可以看出由于感应加热、电磁搅拌、强烈水冷、有一定铸速等特点的存在且它们之间又相互影响,从而使得EMC的传热过程非常复杂[3]。
2.3电磁铸造材料的宏观组织形成机理
电磁铸造材料的宏观组织一般为均匀、细小的等轴晶组织[4]。
2.3.1等轴晶组织的形成机理
一般从热力学角度解释为枝晶机械断裂或熔断转变为新的晶核,在过冷度较大的情况下,晶核不易长大而生长为细小的等轴晶。
常规铸造过程可看做是相对静止的,而EMC铸造过程由于磁场的作用一直处于强烈的对流传热传质过程,温度场、溶质场、流速场无时不在变化,因此说EMC过程是一个动态过程。
在这种情况下,没有哪一个方向更占优势,因此也就决定了晶粒不会在某一方向上优先生长,整体趋于各向同性,最终形成等轴晶。
2.3.2柱状晶形成的可能
金属熔体凝固、晶粒长大方式,是EMC凝固过程中的一种趋势。
然而,由于合金成分或某方面工艺因素的变化,会对凝固组织的形成产生一定的影响。
除形成等轴晶组织之外,如强化某一特殊工艺因素(在感应圈中通入高频电流、增大液柱高度、降低液-固界面在反应圈中的位置,)还有可能形成柱状晶[5]。
3.电磁铸造工艺及设备
3.1电磁铸造的工艺
电磁铸造工艺过程如下:
1)调整电磁感应器、屏蔽罩、冷却水套和底模等的水平和相对位置;
2)将底模升入感应器中,使其顶面位于磁场强度最大位置;
3)通入冷却水,启动中频电源,调整功率、频率和感应器电流等至规定值;
4)浇注液体金属于底模中,当形成的半悬浮液柱接近规定的高度时放入浮漂漏斗;
5)喷水冷却,启动拉坯系统,使铸速按一定模式逐渐过渡到正常值;
6)当铸造过程进入稳定阶段后,铸造速度基本恒定,严格控制流槽中的液位,保持静压头和液位恒定,直至铸造过程完毕[3]。
3.2电磁铸造设备
电磁铸造可分为立式电磁铸造和水平电磁铸造。
立式电磁铸造又可分为上拉式即与下引式。
目前国外投入大规模工业生产的电磁铸造属于下引式。
它主要由中频电源、结晶器、底模、铸机、熔铝炉等组成。
此处将以下引式电磁铸造设备为例进行介绍[6]。
3.2.1结晶器
电磁铸造结晶器由感应线圈、屏蔽罩和冷却水系统组成,如图2所示。
结晶器形状决定了所铸铸件的形状,如圆锭、扁锭、薄板、棒材等。
图2电磁铸造装置示意图
1—感应器;2—屏蔽罩;3—铸锭;4—底座;
5—流槽;6—冷却水套
1)感应线圈电磁铸造用感应线圈为单匝线圈。
目前工业生产采用的感应器分为“Russia”直边式与“Kaiser”斜边式两种,如图3所示。
其中,“Russia”直边感应器在液柱上部产生的磁场较强,使得液柱成为“山”形,故需引入屏蔽罩。
“Kaiser”斜边感应器在上部被截去一部分,主要是为了减弱上部磁场,起到屏蔽罩的作用。
图3电磁铸造所采用的两种电磁感应器结构
感应线圈一般由紫铜制作,有时为了得到合适的磁场分布,将线圈加工成与水平方向成某一角度,即感应器上部的直径大于下部直径。
感应器的中部通常在铸坯周边凝固线附近。
此时感应线圈能向凝固线处的液态金属提供最大的推力。
凝固线偏上时,易产生冷隔,偏下时,易产生偏件瘤。
除上述两种结晶器外,瑞士Haller还设计了一种尺寸可调的结晶器。
它具有可移动的端面模壁,在侧壁和端壁之间有1.58-12.7mm的小间隙便于移动端壁。
用它可生产多种尺寸的铸锭,在扁锭的铸造中,为使铸锭角部曲率半径尽量小,感应器角部被加工成凸形。
有时为了得到所需的磁场分布还采用组合感应线圈。
感应线圈的各个部分或不同线圈可通以位相或频率不同的电流。
2)屏蔽罩使用“Russia”式结晶器需引入屏蔽罩。
屏蔽罩的基本作用是使电磁推力与金属液的静压力由下向上逐点保持平衡,并使液穴内的流动不至于过分剧烈,以免造成液面动影响铸锭质量。
屏蔽罩横截面一般是从下向上逐渐增大。
屏蔽罩下口的锥度由铸锭的逆向导热距离和线圈结构及所铸合金性质决定。
屏蔽罩材料的选择必须考虑以下两个方面:
a.屏蔽罩要起到减弱磁场的作用,但又不能完全消除磁场。
b.尽量减少整个系统的能量消耗,即屏蔽罩材料的电阻要尽量小。
在中频条件下(1-10kHz),铜和铝的穿透深度均为0.2-2mm。
用铜和铝作屏蔽罩将基本消除磁场。
不锈钢的穿透深度为4-13mm,因此一般地选为屏蔽罩材料。
但由于电阻较大,其消耗的能量约占整个系统能量消耗的10-30%。
为了节能,有人提出可在铜质或铝质屏蔽罩中通以与感应器中电流反相的中频电流,或设法增大系统的阻抗使屏蔽体中感应电流减小,有时屏蔽罩还可以作为冷却水套的一部分。
3)冷却水套冷却水套必须使冷却水均匀、合理地喷射到铸锭的表面。
一方面提供一定的流量,另一方面要使冷却水保持一定的角度和流动形态。
对于矩形扁锭,由于窄边与角部冷却较快,因此喷水孔较稀,这样可使整个铸锭断面冷却均匀。
冷却水套的设计比较灵活,既可单排冷却水,也可多排冷却水;有直喷,也有带角度的;有组装的,也有分离的,视具体情况而定。
冷却水的强度及见水点决定着凝固带的位置,决定着逆流导热距离。
见水点上移,冷却强度增加,凝固线下降;见水点下移,冷却强度减少,凝固线上升。
冷却强度必须与铸造速度相匹配。
冷却强度随铸速增加而增加。
冷却强度太小,有可能拉漏;冷却强度太大,液柱高度变小,容易产生纵向波浪等缺陷。
由于冷却水直接喷到铸锭表面,这种强烈的冷却有时将导致铸锭产生裂纹。
为降低生成裂纹的趋势,需提高铸件已凝固部分的温度,提高铸件的温度通常有以下方法:
CO2法、脉冲式冷却法和“刮水器”法,刮水器法就是在着水点下方某一距离处增设橡皮挡水板阻止冷却水直接喷到铸锭上,利用余热起到热处理作用,消除应力。
综上所述:
结晶器的设计要基本满足以下三个条件:
1)保证电磁推力与一定高度的金属液的静压力处处平衡。
2)使液穴内的流动不至于过分剧烈。
3)冷却水均匀合理地分布。
3.2.2底模
底模的结构对铸造起动以及铸锭质量均起着重要作用。
铸造开始时,铸锭下面与底模接触处的凝固层较薄,而周边的凝固层变厚,并由于周边的凝固及冷却作用,使铸锭下面薄凝固层发生弯曲变形,从而与底模的接触面减少,严重时容易拉漏。
若周边收缩不均匀,将引起铸锭的中垂线偏离垂直方向,引起铸锭的摇晃,金属液就有可能从侧面溢出。
且铸锭下部在铸造开始时就产生弯曲,喷射于铸件表面的冷却水将流入底模和铸锭间的空隙内,冷却水在此汽化,加剧铸锭的摇晃。
为使铸造正常进行,需要对底模进行以下改进:
a.选择导热性能较好的材料制作底模。
这样当冷却水直接喷到铸锭上时,不致引起冷却速率的较大变化,有利于铸造过程稳定。
b.为防止铸锭底部翘曲,底模的形状要做成“凹膛”式结构,并开有扁形沟槽与排气孔。
铸造时底模上还可放置金属垫片或纯铝垫底。
底模结构的设计要尽量消除弯曲变形,拉速,尤其是起动段的拉速要与设定值拟合。
铸造温度、电流、频率、功率、液位、水压等工艺参数要稳定在工艺给定值。
4.电磁铸造的发展及应用
4.1电磁铸造的发展
4.1.1国外电磁铸造的发展
1960年年中苏联Getselev发明了电磁铸造法(EMC)。
1966年用EMC制得了第一个铸锭,1969年在工业上铸造了直径为200-500毫米的铸锭。
后来,由于它也适于铸造方锭,实际上用于铸造300x(1250-1550)mm2的铸锭,在捷克斯洛伐克、匈牙利、东德等东欧各国进行了普及。
在西方各国,1973年美国Kaiser公司引进了专利,同年Alusuisse公司也引进了该技术,此外,Alcoa、Reynolds、Pechiney等公司的大型铝厂也都在同时期引进了该技术。
日本的三菱化成公司在1972年10月也引进了该技术。
从苏联引进的EMC技术,单块铸造技术是基本的,距离西欧各国对多块铸造技术或大断面铸锭连续铸造技术的要求相差很远,引进之后,各公司还必须发展这种技术。
Alusuisse公司1975年在美国的分公司Comalco开始装备了实用的成套设备,投产了铸锭尺寸为500x1300mm2的4块连续铸造设备。
Kaiser公司1981年完成了500x1300mm2的5块连续铸造设备。
现在,在引进EMC技术过程中,达到工业实用化的只有Kaiser及Alusuisse二个公司,它们都是在引进基本技术后经过数年才达到实用化。
在EMC实用化方面不可缺少的是电算机控制的铸造自动化。
目前,EMC可以说是变成了技术水平高的铸造方法[7]。
4.1.2国内电磁铸造的发展
我国的电磁铸造技术研究起步也较早,70年代中期,东北轻合金加工厂就开始这方面的研究,并于1982年试制出铝合金圆锭。
但因缺乏基础理论和配套设备的系统研究,工艺操作难度较大,没有实现自动控制,致使这一技术实际上被搁置起来,未能在生产中发挥应有作用。
“七五”期间,中国有色金属工业总公司主持将铝合金方锭的电磁铸造方法列入国家攻关计划,组织大连理工大学、西南铝加工厂、北方工业大学、东北轻合金加工厂共同进行开发研究,并取得了一系列成果。
近年来,大连理工大学电磁铸造实验室在国家自然科学基金和辽宁省科技基金的支持下,建立了电磁铸造中试基地,进行了铝合金电磁铸造的中试实验;优化设计出电磁感应器系统结构,确定了成型控制参数;铸造出多种优质铝合金铸锭,并对EMC温度场、应力场进行了实验与数值模拟的研究。
4.2电磁铸造的应用
EMC技术自20世纪60年代问世以来,倍受关注并获得迅速发展。
除开发了水平的、立式的不同方向的EMC技术外,还研究了不同金属及其合金电磁铸造的可能性,铝、铜、钢、镁、锌、铋等都成为电磁铸造的实验和研究对象。
目前,铝及其合金的电磁铸造已大规模投人工业性生产,铜、钢的电磁铸造也正成为人们研究的热点。
日本已有钢的电磁铸造用于工业性试生产的报道。
至于EMC的研究方法、手段也不断更新、现代化,尤其是高速、大容量计算机的出现为高精度、高效率的数值计算提供了可行条件,也为解决各种场的藕合问题奠定了基础。
5.电磁铸造技术的研究方向及新进展
5.1电磁铸造技术的研究方向
电磁铸造技术应用于生产,仅仅30多年的时间,但在工艺、设备等诸方面都取得了新的进展和突破,主要研究方向集中在以下几个方面:
1)多流化、盒形化;
2)可调节的电磁模和无接触液位检测;
3)异型铸坯;
4)不同材料的开发应用[8]。
5.2电磁铸造技术的新进展
5.2.1铸造各种形状的铸锭
美国Olin公司发明了一种生产透平机叶片的电磁铸造法,其结晶器可由一齿轮带动旋转,感应线圈做成透平机叶片的截面形状。
在电磁铸造过程中,调节外加电流的大小可以改变铸锭的截尺寸,齿轮缓缓转动,使拉出的铸锭成为螺旋状。
此外,还有生产管棒材,薄板的电磁铸造技术报到。
图4为美国GE公司开发出的一种专门用于生产管棒材的GELC法原理图。
该装置巧妙地利用行波磁场向上的推力抵消重力,环形线圈向轴线方向的挤压力使液态金属脱离结晶器壁后凝固,工艺过程稳定且便于调整[9]。
图4CELE装置示意图
5.2.2不同材料的电磁铸造
电磁铸造应用于铝及铝合金已经很普遍了,最近几年它的应用范围不断扩大,如硅、锗、镁等棒材及铝合金的管材。
美国Olin公司开发铜和铜合金的电磁铸造技术,并成功地将其应用于大截面铜坯和薄铜带的生产中。
目前,最引人注目的是钢的电磁铸造的开发和应用。
钢的产量巨大,如果实现无模电磁铸造将大大改善钢坯的表面质量,消除轧制中产生的各种缺陷,显著提高组织和机械性能又由于无模取消了复杂的润滑和振动系统以及检测、控制系统,可大大简化工艺及装备,降低劳动强度。
因此,实现钢的电磁铸造意义重大。
但是,钢的电磁铸造受以下因素的困扰:
1)钢的密度大,约是铝的三倍,若要形成与铝相同高度的液柱,磁感应强度则需铝的1.7倍。
表1列出了几种合金电磁铸造的特性参数。
2)钢的电导率低,仅为铝的1/6,而且趋肤深度大,在相同电源参数下钢表面形成的感应电流密度小,电磁推力也小。
表1电磁铸造在铝、铜及钢中应用比较(频率3000HZ,液体金属高度5cm)
综合上述因素,可推知钢电磁铸造应满足的电流条件为20000A。
俄罗斯学者用250KW的电源制造出直径为300mm的圆钢坯,能耗接近于铝合金的10倍,这在实际生产中是无法接受的。
3)钢的熔点高,难于凝固。
因此,目前尚无实用的钢电磁铸造技术获得成功,此外,用电磁铸造法生产钢坯在经济上的合理性,还缺乏充分的论证[10]。
图5钢电磁铸造示意图
5.2.3水平电磁铸造技术
浅井滋生首先开发了静磁场中通以直流电的水平电磁铸造装置如图6所示
图6直流水平电磁铸造装置原理图
随后日本住友公司和美国能源部,先后也申报了水平电磁铸造薄板的专利。
其中美国能源部的专利对设备说明相当详细,其原理如图7所示。
被铸金属位于铁芯中间,在上线圈与被铸金属之间放有一金属导板。
导板一边与液态金属熔池连接,另一边通过引导辊与被铸金属连接,形成导电闭合回路。
在上下两个线圈产生的交变磁场作用下,闭合回路中产生感应电流。
受磁场作用,导板受压力向下,被铸金属受浮力向上。
由于上层导板被固定,所以下层被铸金属受浮力悬浮。
冷却剂从上下两面喷出使金属在悬浮段凝固,引导辊引导被铸金属板运动形成连铸过程。
当被铸金属受干扰向下偏离时,闭合回路面积加大,感应电流增加而使浮力增加,使被铸金属回到原位。
反之亦然。
因此这一装置具有自动稳定的功能。
两侧两个小凸缘可使磁路形成小闭环,产生侧面向内的压力[10]。
图7交流水平电磁铸造原理
5.2.4铝合金薄板的电磁铸造
电磁铸造主要用于铝合金圆锭和厚大扁锭的生产,其产品需经过二十多个道次的热轧和冷轧制成不同规格的板、带和箔材。
电磁铸造对铸锭组织和性能的改善主要在表层30-40mm范围内,而内部与DC法生产的铸坯相差不大。
Evans在阐述电磁铸造技术时,认为用电磁铸造法直接制取厚10mm以下的铝薄板,以便省去热轧而直接冷轧,从而可大大降低设备投资和能耗,减少工序。
所以,铝薄板电磁铸造技术的研究具有重要意义,因而己成为当前电磁铸造的研究热点之一。
Cook等首先用有限元法计算了电磁铸造铝薄板时液一固界面的位置,然后数值模拟了电磁场,确定了在较高铸速下可以支撑半悬浮金属液柱成型的电磁场和电磁力,为成型系统的设计提供依据。
叶谷等用电磁铸造法进行了150x(10-20)mm铝合金薄板的工艺试验并获得成功。
他们采用10匝的电磁线圈,工作电流为710A,可产生0.08-0.1T的磁通密度以维持140mm高液柱的静压力。
他们研究了不同的冷却水量(16-20L/min)、铸造速度(360-600mm/min)以及底模厚度(10-20mm)对铸造工艺和薄板质量的影响。
铸造的铝薄板样品直接进行冷轧,压下率达80%时仍无表面缺陷,机械性能高于DC法生产的经过热轧和冷轧的样品,完全符合日本JIS标准要求。
但是,叶谷等制备的铝薄板样品尺寸较小,而且截面形状不甚理想。
大连理工大学从1996年开始铝薄板电磁铸造的研究并取得有意义的结果[3]。
参考文献
[1]郭景杰,张铁军,苏彦庆,丁宏升,贾均.电磁技术在铸造中的研究与应用[J].特种铸造及有色合金,2003(3):
37.
[2]浩海,金俊泽,张兴国.电磁铸造中的感应热研究[J].铸造,1999(8):
5-6.
[3]张兴国.电磁铸造技术的研究[D].大连:
大连理工大学材料工程系,2001.
[4]董杰,崔建忠,赵志浩.低频电磁铸造超高强高韧铝合金元素晶内固溶度和力学性能研究[J].航空材料学报,2003,23
(1):
16-19.
[5]卞之.电磁铸造及其材料宏观组织的形成机制[J].铸造技术,2003,25(7):
496-497.
[6]曹志强,张兴国,金俊泽.电磁铸造设备与工艺[J].轻金属,1995(8):
56-58.
[7]吉田政博.电磁铸造法的现状和未来[M].高革,译.哈尔滨:
中国有色金属加工工业协会轻金属分会,1989.
[8]张维平.电磁铸造技术的发展及应用[J].鞍钢技术,1991(3):
17-19.
[9]寇宏超,李金山,张丰收等.钢的电磁铸造及其研究进展[J].铸造技术,2001(3):
46-48.
[10]曹志强,张兴国,金俊泽.电磁铸造技术及其发展[J].轻金属,1995(10):
51-53.