精品铁芯制造工艺新全.docx
《精品铁芯制造工艺新全.docx》由会员分享,可在线阅读,更多相关《精品铁芯制造工艺新全.docx(12页珍藏版)》请在冰豆网上搜索。
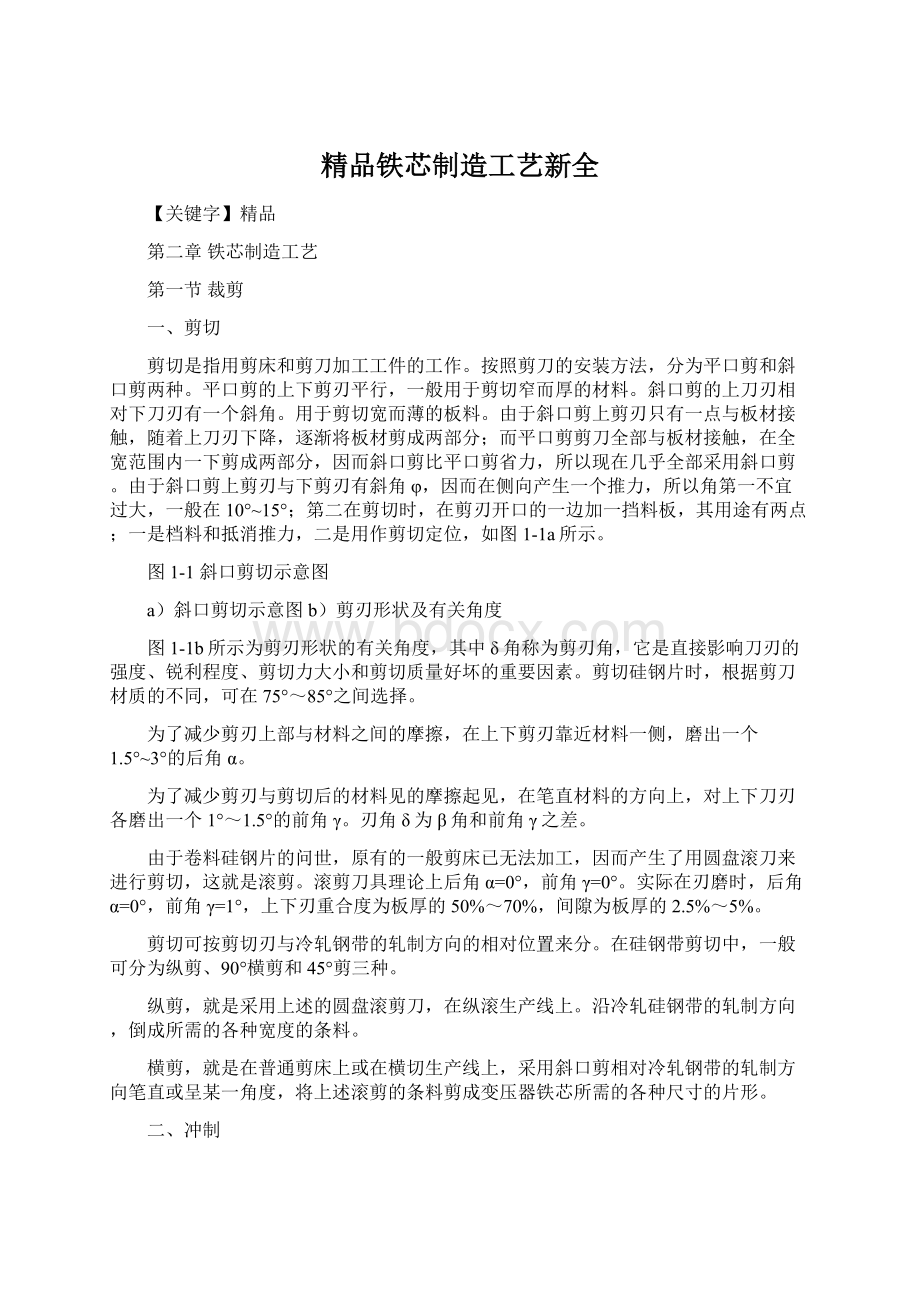
精品铁芯制造工艺新全
【关键字】精品
第二章铁芯制造工艺
第一节裁剪
一、剪切
剪切是指用剪床和剪刀加工工件的工作。
按照剪刀的安装方法,分为平口剪和斜口剪两种。
平口剪的上下剪刃平行,一般用于剪切窄而厚的材料。
斜口剪的上刀刃相对下刀刃有一个斜角。
用于剪切宽而薄的板料。
由于斜口剪上剪刃只有一点与板材接触,随着上刀刃下降,逐渐将板材剪成两部分;而平口剪剪刀全部与板材接触,在全宽范围内一下剪成两部分,因而斜口剪比平口剪省力,所以现在几乎全部采用斜口剪。
由于斜口剪上剪刃与下剪刃有斜角φ,因而在侧向产生一个推力,所以角第一不宜过大,一般在10°~15°;第二在剪切时,在剪刃开口的一边加一挡料板,其用途有两点;一是档料和抵消推力,二是用作剪切定位,如图1-1a所示。
图1-1斜口剪切示意图
a)斜口剪切示意图b)剪刃形状及有关角度
图1-1b所示为剪刃形状的有关角度,其中δ角称为剪刃角,它是直接影响刀刃的强度、锐利程度、剪切力大小和剪切质量好坏的重要因素。
剪切硅钢片时,根据剪刀材质的不同,可在75°~85°之间选择。
为了减少剪刃上部与材料之间的摩擦,在上下剪刃靠近材料一侧,磨出一个1.5°~3°的后角α。
为了减少剪刃与剪切后的材料见的摩擦起见,在笔直材料的方向上,对上下刀刃各磨出一个1°~1.5°的前角γ。
刃角δ为β角和前角γ之差。
由于卷料硅钢片的问世,原有的一般剪床已无法加工,因而产生了用圆盘滚刀来进行剪切,这就是滚剪。
滚剪刀具理论上后角α=0°,前角γ=0°。
实际在刃磨时,后角α=0°,前角γ=1°,上下刃重合度为板厚的50%~70%,间隙为板厚的2.5%~5%。
剪切可按剪切刃与冷轧钢带的轧制方向的相对位置来分。
在硅钢带剪切中,一般可分为纵剪、90°横剪和45°剪三种。
纵剪,就是采用上述的圆盘滚剪刀,在纵滚生产线上。
沿冷轧硅钢带的轧制方向,倒成所需的各种宽度的条料。
横剪,就是在普通剪床上或在横切生产线上,采用斜口剪相对冷轧钢带的轧制方向笔直或呈某一角度,将上述滚剪的条料剪成变压器铁芯所需的各种尺寸的片形。
二、冲制
冲制是指在冲床上利用模具进行冲载,冲孔,冲槽等工作,其过程和原理与剪切相似,只不过是用凸凹摸代替了上下剪刃而已。
冲模也有平口和斜口两种,如图1-2所示,图a为平口冲模;图b为斜口冲模,斜度φ约为1°~6°,一般取φ=4°。
冲制时,凸凹模之间也有一个间隙和重合度问题,它们同样是影响冲制力、冲制质量和模具使用寿命的重要因素。
一般间隙取板厚的7%~10%。
对于0.35mm厚的硅钢板,单向间隙一般取0.015~0.02mm。
至于上下刀具重合度,理论上与剪切一样,只要板厚的50%~70%即可。
但是实际上由于冲制是还要考虑落料排出及凹模刃磨寿命等原因,重合度往往大于片厚好几陪。
冲制模具由于加工的性质不同,可分为;落料模、冲孔模、剪切模和修边模等。
其结构可分为敞开式和导柱式两种。
在变压器铁芯片冲制过程中,由于零件尺寸大,只能用敞开式;但是对于较小零件,冲制精度要求高,毛刺要求特别小时,由于冲床精度难以保证上述要求,应采用有导向的导柱式冲模。
第二节硅钢片的压毛、涂漆和烘干
一、硅钢片压毛
1.压毛目的
由于铁芯片毛刺直接影响变压器性能,因此规定毛刺高度大于0.03mm的铁芯片,在涂漆之前必须压毛。
2.压毛工艺方法
压毛是采用双锟压毛机进行。
将双锟压毛机的下压锟位置固定。
上压锟采用压缩弹簧加压,其压力大小由弹簧压紧装置上的顶丝调节。
上下锟必须平行且沿压锟表面均匀接触。
试车时,可先用塞尺检查上下锟于接触是否均匀,然后用毛刺高度超过0.03mm的硅钢片试压,并对毛刺高度进行测定。
如果毛刺高度经压毛后小于0.02mm,片子又无瓢曲、过碾等现象,则视为试车完毕。
然后试压一部分片子,经检验合格后即可投入生产,生产过程中应按规定进行检验。
3.压毛抽检方法
抽取有孔且毛刺较大的片子三片,用千分尺测量刃口处厚度,每片测五点。
每点均不得超过近旁边厚0.02mm。
如果孔处毛刺大,可以从孔处切开测量孔处毛刺,
二、硅钢片涂漆
1.涂漆目的
铁芯片涂漆,是在铁芯片表面涂盖一层坚实的,具有一定绝缘电阻的,耐热耐抽的薄漆膜。
铁芯片涂漆不仅可以减少铁芯涡流和边缘泄漏电流引起的附加损耗,而且可使铁芯片表面与空气中的氧气及腐蚀粒子隔绝,可避免金属表面氧化或腐蚀而影响铁芯的电磁性能。
2.涂漆的工艺方法
铁芯片涂漆有喷涂法和滚涂法两种。
前者通常用于喷涂硅钢片刃口,以防生锈;后者用于整张片子的表面涂漆(包括刃口涂漆)。
三、硅钢片涂漆后的烘干
1.烘干目的
硅钢片上所涂的漆需要在一定温度下进行烘干,才能固化成坚硬、牢固、绝缘强度大和表面光滑平整的漆膜。
然后转入下道工序供铁芯叠装。
2.烘干工艺
烘干一般分为前、中、后三区加热,这样可以使漆膜中气体排出和充分固化,从而获得内表一样坚固的漆膜。
对于1611漆来说
前区加热温度一般为150°~250°
中区加热温度一般为350°~550°
后区加热温度一般为200°~350°
上述温度是由烘干炉上的三个热电偶和毫伏表或电位差计进行监视和控制。
对于不同的漆种和不同的进料速度,其温度高低及分布方法可适当改变。
可用白手套在热状态下擦拭漆膜,如漆膜上不出现印痕,不粘手,则视为干透。
也可通过观察漆膜颜色来判断,例如1611漆
一次涂漆为棕色或深棕色
二次涂漆为褐色或深褐色
三次涂漆为更深的褐色
根据上诉方法判断后,操作工人可适当降低或提高某区温度,或进行全线调整速度和温度,边试边调,直至调到满意为止。
第三节铁芯片的叠片形式和叠片图
一、铁芯的叠片形式
1.对接和搭接
铁芯的叠片形式是按心柱和铁轭的接缝是否在一个平面内而分类,各个接合处的接缝在同一笔直平面内的称为对接;接缝在两个或多个笔直平面内的称为搭接。
由图5-1可见,对接式的心柱片与铁轭片间可能短路,需要垫绝缘垫,且在机械上没有联系,夹紧结构的可靠性要求高。
搭接式的心柱与铁轭的铁芯片的一部分交替地搭接在一起,使接缝交替遮盖从而避免了对接式的缺点。
2.搭接的接缝结构
铁芯在厚度方向是由铁芯片叠积而成。
接缝形式决定了铁芯的电磁性能、材料利用率和加工的难易程度。
当接缝与硅钢片的轧制方向平行或垂直时称为直接缝。
否则称为斜接缝。
3.阶梯接缝
为了减少接缝处铁损过分集中而造成局部过热,国外已在铁芯上采用阶梯接缝,又称为步进接缝即把各层之间的叠片接缝向纵向或横向错开,避免铁芯某一个剖面上接缝集中。
4.每层叠片的数量
铁芯叠装时,每层叠片的数量一般为1~3片。
数量越多,接缝处气隙的截面越大,接缝处引起的磁通密度畸变也越大,如图5-2所示。
由于磁通密度畸变,使接缝处部分硅钢片磁通密度增大引起铁芯损耗增加,从图5-3可以看出每层的数量对铁损的影响。
从理论上讲,采用一张片一叠最好,对于小容量的铁芯有可能做到。
但对于大容量的铁芯,考虑到插装上轭铁的工艺要求有可能插装不到位,反而使空载电流和损耗增加,故一般采用两张片一叠。
混合叠片是近年来在国外对中等容量配电变压器铁芯采用一种新方法。
即对铁芯总厚度约1/3的中心部分(主级)一张片一叠,接下来的1/3是两张片一叠,最靠外的1/3采用三张片一叠,总的叠装工作量并不增加多少,但可取得显著降低铁损和空载电流的效果,表5-3是模型试验的结果。
磁通密度B/T
每层叠不同片数的铁损/W
-
每层叠不同片数的I。
A
-
1片
2片
混合
%
1片
2片
混合
%
1.40
83.0
86.0
84.02.3
2.3
2.55
2.82
2.62
7.1
1.50
100.5
104.5
102.0
2.5
3.60
4.00
3.65
8.5
1.60
123.5
129.0
125.5
2.7
5.19
5.61
5.15
7.2
1.67
143.4
150.0
145.6
2.9
6.70
7.35
6.86
6.7
1.70
153.5
160.9
156.1
3.0
7.85
8.60
8.07
6.2
实践证明,铁芯中心的磁通密度分布并不是均匀的中心部分的磁通密度低于额定值,中间和边缘的磁通密度要高于额定值,越靠外侧磁通密度越高。
降低铁损的方法之一就是使铁芯各部分的磁通密度分布均匀。
采用=变更每叠片数的方法,可调节磁路的磁阻,从而调节磁通密度的分布。
中间部分磁通密度偏低,采用一张一叠后磁阻降低,使磁通密度增加:
外侧磁通密度偏高,采用三张片一叠磁阻增加,使磁通密度减小。
如前所述,如果全部采用一张片一叠节约效果当然会大,这样却增加了铁芯叠装的工作量。
二、铁心叠片图
反映铁芯中每层叠片的分布和排列方式的图称为铁心叠片图。
在叠片图中,规定了叠片的接缝结构、叠片的形状、尺寸和数量。
下面是几种常见的铁芯叠片图:
单相二柱式铁心叠片图如图5-4所示。
三相三柱式铁心叠片图如图5-5~图5-8所示。
三相五柱式铁心叠片图如图5-9所示。
对于小型铁芯,为了增加机械强度采用不断轭铁芯片;为了剪切方便,可采用标准斜接缝的(出尖角)结构为了减少废料,可采用5/7接缝形式(属半直半斜接缝结构)。
大型铁芯,均采用断轭的全斜接缝的结构形式,如图5-7~图5-9所示。
第四节铁芯片的预叠
一铁芯选片
铁芯选片,是按铁芯柱及铁轭柱截面形状,将各级铁片按顺序准备好,以供叠装使用,对于中小型变压器,可将铁心柱或铁轭的各级叠片,按截面形状在料板上叠成一个“圆柱”,分别供铁心柱或铁轭叠装时使用。
对于大型变压器,由于一个完整的“圆柱”叠片重量太大,超出料板的承受能力,不便于吊运,因此常叠片成两个半“圆柱”分别放在两个料板上,如图5-23所示,为了保证吊运时的稳定性,料板(图b)最下一、二级叠片因宽度较小,可以并列平放,以增加底层料的面积。
叠装时先用图a料板中的片,待叠装完后再用图b板中的片,对于容量更大的变压器,有时可以将以个“圆柱”叠片分成三部分,即第一板放置按圆柱总厚度的上部的1/3,第二板中间的1/3(即最宽的主级),第三板放置下部的1/3。
叠装时,从第一板开始,依次取料。
选片工作,主要靠人工操作,对于硅钢片的搬运可借助于电磁铁及简单的吊运设施,操作时应轻拿轻放,避免摔打碰撞,否则会使叠片受到不应有的应力影响,从而使铁损增加,为保证叠装时取料方便,各级叠片应堆放整齐。
二厚度保证
预叠是铁芯加工过程中承上启下的一个工序,是铁芯片加工和叠装的中间环节,通过预叠保证铁芯叠装时每级厚度和总厚度。
纵剪工作是按材料长度来控制的,横剪工作是按剪切的片数来控制的,叠片时要保证图样所要求的每级厚度和总厚度,所以预叠的另一项工作就是把铁芯片的片数和叠装的厚度联系起来。
一般要求每一台铁芯预叠时,先根据每级厚度和片厚度计算每级所需片数,选叠一个心柱,按叠装的顺序逐级叠好,用卡尺测量每级的厚度是否符合工艺要求。
所以级叠完,模拟叠铁时的夹紧方式,上好三个卡子,检验总厚度是否符合要求,如果吧符合要求,则要调整片数直到符合要求为止,这样的一个心柱就叫标准柱。
以标准柱的每级片数为准,再预叠其他铁芯片,每级都要用卡尺测量级厚,如果有的片型级厚度误差大,要用加减级片数来进行调节,并做好记录,以供叠铁时增减本片型每级铁每一层的片数,保证叠铁时层数相同,级厚度也符合标准。
三边柱的预叠
从叠片图中可以看出,边柱(或旁轭)的片型常有方向性,因为叠片时不允许纵向翻片(片弯曲后将引起铁芯片的磁性能下降和铁损增加),所以预叠时要把带有方向的边柱片配套跺好,具体操作过程见图-5-24和图5-25
假设A板是剪切好的边柱片,先从A板上分出一半片横向翻转180度放在B板上,然后将B板吊起来旋转180度放在C办的另一侧。
根据每层叠片的片数,从A.B两板上一层接一层的顺次发那个在C板上叠成塔形或倒塔形,注意按吊车的吊运能力分板
当边柱最大片宽不超过500mm时,可选宽度大于或等于1000mm的料板按图5-25所示预叠即可。
四防尘防锈
预叠后的板料通常要存放和运输才能叠装,所以要注意防尘防锈
防尘主要用塑料布覆盖并用胶带封好,在预f叠过程中叶要注意,每次工作完后都要用塑料布盖好。
操作过程中要杜绝磕碰、摔打等野蛮操作,尤其的宽片、长片要少拿轻放。
如果一次拿片太多太重,就有可能造成料边相互摩擦极易形成很多的毛刺,这是不允许的,它会对产品的性能和安全产生不良影响。
在铁芯制造过程中为了防锈,在铁芯片刀口处喷涂或刷涂防锈剂。
每次要根据喷涂或刷涂的面积倒出适量的防锈剂,搅拌均匀,最好一次用完,以免存放失效。
喷刷时,要掌握量少而均匀,以免大量渗入片间深处,使叠片时不好揪片,并使叠片系数下降。
第五节铁芯的叠装
一、10千伏小型变压器铁芯叠装
铁芯叠装首先要准备好图样、工装设备、工卡量具等,然后调平叠装基准面,也就是简易装配台,装配台由数根纵横槽钢搭成槽钢架,如图5-26所示。
然后按照操作规程,放好夹件、夹件绝缘、垫木等。
放时要平行,距离要准确,使其成为一平面,力求平稳牢靠。
为使叠装时操作方便预叠好的铁芯柱和轭铁片的位置要摆放适当。
叠装时按铁芯叠片图,两片一叠。
由下往上逐级叠装,根据铁芯大小,可一级一靠打,也可15~20mm厚度打齐一次,使接缝达到最小,但不得有搭头、卷边、漏片错片现象。
首级要注意找正,铁芯对角线尺寸应相等,宽度较小的级,厚度公差多采用负公差。
宽度大的级(主级)可采用正公差,但必须注意铁芯叠面的对称性,这样可保证总厚度不变的情况下铁芯截面积较大,以较少铁芯损耗。
叠到最后2~3级时需要测量铁芯叠装的总厚度尺寸,按铁芯叠装的质量标准,控制铁芯的总厚度尺寸。
铁芯全部叠完,经全面检查校正后,进行铁芯零部件的装配。
放好绝缘件、接地片压紧上、下铁轭夹件,装好垫脚。
需绑扎粘带的铁芯,画好绑扎位置标记,在布带间隔区域用心柱临时夹具紧固。
铁芯起立前装好拉螺杆,或用工装将上下夹件夹好,用钢丝绳挂在上夹件两端,由专人指挥吊车,起立时速度要快。
铁芯起立后,放在平坦的地面上。
起吊、着地时应慢、轻、平稳。
校正铁芯垂直度后,按要求需绑扎环氧玻璃粘带或用钢带绑扎,按其绑扎工艺进行绑扎然后将铁芯送入烘干炉内烘干。
出炉后,卸去铁芯临时夹具。
铁芯装配完毕,由专人对铁芯按检查规范进行检查。
(图4-11)。
全斜接无孔绑扎的三相铁芯采用过内四角定位和外四角定位法工艺复杂。
现改用中柱定位法,定位简单。
中柱定位法是先叠中柱,后叠上、下铁轭和边柱的分步叠装法。
其操作过程如下:
1)在平台上,按铁芯尺寸,放置一侧夹件、夹件绝缘和心柱的临时支撑;
2)先叠装中柱用W形定位件定位,中柱完成后适当紧固;
3)以中柱为基准,先插叠上、下铁轭,然后排放边柱片,如图5-27所示;
4)边叠装、边整理,用纯铜纯或尼龙纯打严接缝。
叠装厚度采用卡尺检测,垂直度采用直角尺检测,直至叠完。
在平台上叠装铁芯,首先要摆放好上、下夹件,在铁芯柱应绑扎环氧粘带的位置上放好临时支撑,使铁芯柱的叠片与夹件处于同一水平面上。
第一级叠片(最窄的一级)的对准至关重要,它将决定以后叠装尺寸的正确性。
碟装的过程中“敲齐”禁用金属块,应选用有一定任性的尼龙块而且要轻敲轻打。
跌装中要注意级块尺寸边缘距离的测量,如图5-28中A、B、C、D……G以保证不发生级块偏移而使直径超差。
对于各级的厚度T1、T2、T3……T8,尽管在选片时已经测量过,在叠装过程中仍需逐级严格测量,当叠装玩最宽的一级(主级)后往上各级是逐级变窄,容易用目测判定是否有级块偏移。
当小容量变压器生产量很大时,可采用铁心柱单独叠装,然后插好下轭送去套绕组,最后在插上轭的方式,即不叠装上铁轭工艺。
中柱的叠装利用W形定位件(见图5-27)
先将中柱叠装好并夹紧。
边柱的叠装比较简单,如图5-29所示。
除图示挡板外,还可采用简单的辅助挡板,以保证各级块的位置正确,采用铁芯柱单独叠装方式时,必须具备可翻转的铁芯装备台,如图5-30所示将预先叠好的的三个心柱A、B、C固定在翻转台的可调基板上,基板上有定位夹具可保证三个心柱的位置和平行度,然后通过调整手柄H,取得要求窗口距离Mo,这时松开翻转轴(操动K)使铁芯柱处于直立位置,插上上端的轭片并装上下部的夹件,然后再松开K,使工作台翻转180°,将插好的铁轭处于下方,松开夹具,取下铁芯,即可送去套绕组。
套好后就地插上轭。
简易平台也可实现不叠铁轭工艺,即采取外侧五点定位法,如图5-31所示。
下铁轭两角外侧定位与四角定位相同,而心柱上端则不同。
两边柱上端采用45°定位件定位:
中柱上端单独采用W形定位件定位。
由于中柱各级片的片形上下一致,所以定位件的高度要大于铁芯的叠厚,而且在开始叠片前调整一次定位即可,以后无需在调整。
四角定位件的高度应大于主级厚度,其位置每当叠完一级需要调整一次。
叠片顺序为先叠下铁轭片,再叠中柱片,最后叠两边柱片,一次反复叠装。
如果第一次两张轭片靠左下角定位件的两个基准面,则第二次两张轭片就要靠右下角定位件的两个基准面。
叠中柱片时,上端要靠紧W形定位件的定位面,下端要对准下轭片的三角槽口,每叠片组均可得到可靠的限位。
两边柱片的位置不同于中柱片,叠片方向不变,但上下接缝处每个叠片组(两张片)之间互相错开一定的距离,下端受到定位件两个面和与轭片接缝处的可靠定位,而上端未能完全实现定位。
左边柱第一次两张片上端两个面受到限位,位置准确又不会移位,第二次叠放时的两张片只有一个面受到限位,45°斜边面没有受到限位。
右边柱第一次叠放的两张45°斜边面未受到限位,而第二次叠放的两张片上端两个面均受到限位。
因此,在叠装边柱时,上端45°斜边面没有受到限位的片上放片时,要注意,严防下面的片受冲击而位移。
用钢槽夹紧梁,将铁芯的三个柱横向夹紧,可以保持较好的整体刚性。
小铁芯夹紧方法如图5-32所示。
需要注意的是铁心柱夹紧梁的拉螺杆数目,应保证三个铁心柱均能得到平均夹紧力。
为保证铁芯在吊起过程中铁芯柱不产生位移,吊车吊绳应挂在下面第二个夹紧梁上。
第六节铁心叠装的质量和检验方法
1、铁心叠装完毕要进行全面质量检查,检查内容如下:
1)铁心片叠装是否整齐、叠片最大缝隙、接缝搭头和叠片参差不齐程度,可用硅钢片离缝间隙量具,参照表5—4中标准值,测量铁轭可见处,判断是否合格。
对于大型铁心来说,不允许有搭头。
表5—4叠片缝隙、接缝搭头和叠片参差不齐标准
容量
/kVA
叠片最大缝隙
/ram
接缝搭头
/nlm
叠片参差不齐
/ram
直接及半斜
全斜
直接及半斜
全斜
直接及半斜
全斜
630以及下
1
1.5
1
1.5
1
1.5
800以及上
1.5
2
1.5
2
1.5
Z
2)高、低压下夹件对装后,两肢板应在同一平面上。
可用钢直尺和塞尺测量下夹件肢板对装部位。
小型变压器允差不大于2mm:
大型变压器允差不大于4mm。
3)主极叠厚尺寸公差、总叠厚度尺寸公差、直径尺寸公差,可参照表5-5中标准规定,用’外卡钳和钢直尺测量。
表5.5叠厚尺寸公差
容量/kVA
主摄叠厚尺寸公差
/mm
总叠厚尺寸公差
/mm
直径尺寸公差
/mm
630及以下
+1.5
—0.5
士1
士1
800及以上
+2
—1
+1
—2(大型:
)
+2
一I(大型:
+6)
2、容量在8000kVA及以上的中型变压器的铁心叠装
容量在8000kVA及以上的中型变压器的叠装方法,与前面所介绍的基本相同。
由于铁心容量的增大而使重量增大,其装配和起立需采用专用设备——滚转台。
在该设备上叠装铁心的工艺过程如下:
根据铁心图样要求,调整滚转台两边可移动垫梁,使其中心线距离符合铁心柱中心距尺寸。
把铁心的上、下夹件放好,并保证上、下两夹件平行,下夹件底边线要和滚转台立臂平面平行。
按铁心柱的玻璃粘带绑扎间距要求,摆好心柱支撑,放入夹件绝缘、心柱护板(或拉板),使夹件的绝缘、心柱护板处于一个水平面上,如图5—33所示。
开始叠装第一级铁心片,测量好对角线和叠片位置尺寸并敲打对齐,如果上、下轭片有
孔时,要放置铁轭定位棒,以后逐级进行叠装。
对于有冷却油道的产品,需按照图样要求放好油道后再继续进行叠片。
在叠最大级铁心片前,要放好下铁轭木垫脚。
在叠至最后3个级时,要对已叠装完的铁心片测量一次总厚度,根据需要,对最后3个级的片数进行调整。
全部叠片叠完后,用铁心柱临时夹具卡紧每个心柱的中间部位,进行最后总厚度和心柱直径的测量。
在确定尺寸无误后,再摆好上面的夹件绝缘和心柱护板。
在环氧玻璃粘带绑扎位置的间隔处,用临时夹具卡紧心柱。
放好上、下铁轭两端的方铁和枕木,摆好上、下夹件、取出定位棒,插进绝缘管和双头螺杆,并装好垫圈和螺母,最后装配下铁轭垫脚。
铁心接地片的安放位置和插入深度,要按工艺要求做到准确无误。
上好铁心与滚转台连接临时保护绳。
夹紧过程中需要注意是放好夹件和拉板后,要检查最窄级叠片是否有移位。
如果有位移,要及时处理,然后才能上紧夹紧心柱的卡子。
上紧的顺序是从柱中间开始向上下两边逐个拧紧,一般需要重复拧紧2~3次。
这是为防止上紧卡子顺序不对而产生拱片现象,或铁心起立后使铁心柱局部弯曲影响垂直度。
轭铁夹紧要采用专用压梁装置,使夹件均匀受压后才能拧紧拉带和夹紧螺杆,操作时也是按照先中间后两边的顺序,最后才装垫脚、撑板(上梁)和侧梁等。
夹紧件装完后,需检查铁心片受力是否均匀。
如果有弓片或弯曲等现象产生,说明铁心片受力不均匀,应及时修理。
如果铁心有绝缘油道或层间纸板,在叠装过程中需要测量其绝缘电阻的数值,应符合工艺要求,否则要查明原因予以处理。
总之,在铁心起立前,应仔细检查各种数据是否正常,以免铁心起立后发现问题再去修理就很困难了。
起立前,要将上铁轭连同上夹件一起用尼龙绳或绑扎带与滚转台横梁l临时绑牢,防止铁心起立时发生意外。
指挥吊车,应使吊钩对准滚转台中心线,挂好吊绳,并开始翻转,当滚转台翻到垂直位置时,吊车应立即停止升起。
两侧支脚自动转出,用销子锁紧。
放下吊绳后,将铁心从滚转台上吊走,然后重复滚转台起立时相反操作程序,使滚转台回到原来的位置。
此文档是由网络收集并进行重新排版整理.word可编辑版本!