板料折弯冲剪机液压传动系统设计论文.docx
《板料折弯冲剪机液压传动系统设计论文.docx》由会员分享,可在线阅读,更多相关《板料折弯冲剪机液压传动系统设计论文.docx(32页珍藏版)》请在冰豆网上搜索。
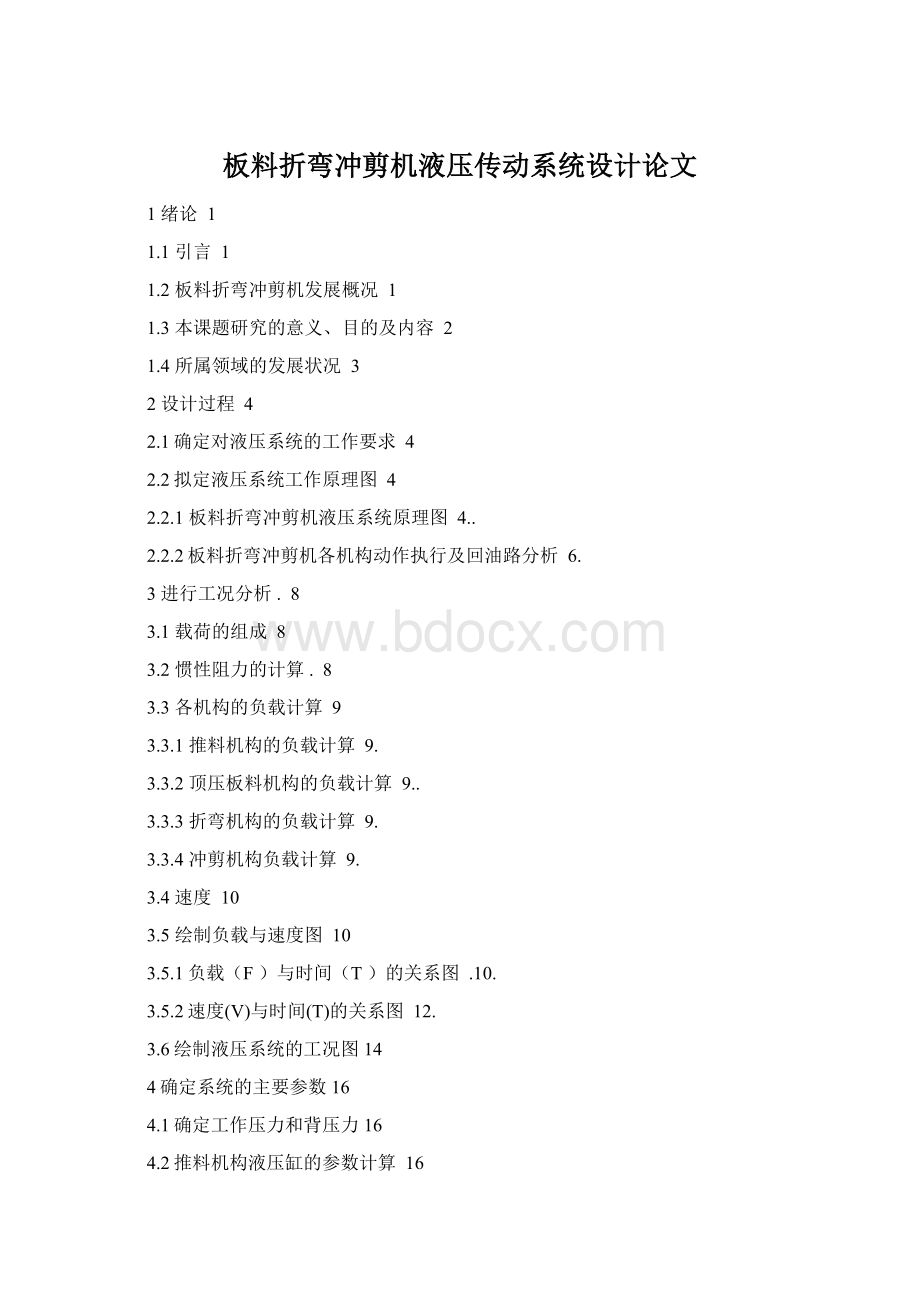
板料折弯冲剪机液压传动系统设计论文
1绪论1
1.1引言1
1.2板料折弯冲剪机发展概况1
1.3本课题研究的意义、目的及内容2
1.4所属领域的发展状况3
2设计过程4
2.1确定对液压系统的工作要求4
2.2拟定液压系统工作原理图4
2.2.1板料折弯冲剪机液压系统原理图4..
2.2.2板料折弯冲剪机各机构动作执行及回油路分析6.
3进行工况分析.8
3.1载荷的组成8
3.2惯性阻力的计算.8
3.3各机构的负载计算9
3.3.1推料机构的负载计算9.
3.3.2顶压板料机构的负载计算9..
3.3.3折弯机构的负载计算9.
3.3.4冲剪机构负载计算9.
3.4速度10
3.5绘制负载与速度图10
3.5.1负载(F)与时间(T)的关系图.10.
3.5.2速度(V)与时间(T)的关系图12.
3.6绘制液压系统的工况图14
4确定系统的主要参数16
4.1确定工作压力和背压力16
4.2推料机构液压缸的参数计算16
4.2.1推料机构液压缸的内径D1的计算16.
4.2.2推料缸活塞杆直径d1的计算17.
4.3夹紧机构液压缸的参数计算18
4.3.1夹紧机构液压缸的内径D2的计算.18.
4.3.2夹紧缸活塞杆直径d2的计算19.
4.4折弯机构液压缸的参数20
4.4.1折弯机构液压缸的内径D3的计算20.
4.4.2折弯缸活塞杆直径d3的计算20..
4.5冲剪机构液压缸的参数计算21
4.5.1冲剪机构液压缸的内径D4的计算21.
4.5.2冲剪缸活塞杆直径d4的计算22.
4.6各机构中各液压缸的外径、缸壁厚度、油口直径的计算.......23
5液压元件的选择25
5.1液压泵参数计算25
5.2电动机的选择25
5.3其他元件26
5.4油管的选择26
5.4.1管道内径的计算26...
5.4.2壁厚的计算26...
5.5油箱容积的确定27
5.6蓄能器的选择28
5.7执行元件的选择28
参考文献29
1绪论
1.1引言
传统机械切削加工方法包括车削、铣削、刨削、磨削、铿削、插削、钻削、冲削、锯切、剪切、锉削、刮削、攻丝和套扣等常用工艺,它们基本上是通过单台设备来完成一种切削加工方法。
而一个零件的加工往往需要多个工艺才能完成其加工过程,因此一个完整的加工车间大多必须安置以上各种功能单一的切削工艺的设备,这样不仅投资大,占用厂房,而且常常导致设备利用率低、维修维护费用高;另一方面,随着国民经济的发展,行业对设备的功能要求越来越高,尤其是近年来,众多新兴企业钢架厂房的修建,对多功能型材加工设备机床,尤其是运用于多种型材剪切、多角度剪切和冲孔工艺的快速加工多功能机床需求越来越大;联合冲剪机床就是在上述需求下诞生的。
1.2板料折弯冲剪机发展概况
联合冲剪机是一种被广泛应用的金属剪断分离设备,它不仅可以对金属板、型材(包括圆钢、方钢、角钢、槽钢及其他异形钢材等)进行剪断分离加工,还可以在板材和型材的平面部分进行冲孔和切口。
由于能完成的剪切工艺形式较多,所以称作联合冲剪机[1]。
按照所设置的工作机构及所能完成的相应剪切功能,联合冲剪机可以分为:
1).冲孔与型材剪切机2).板材和型材剪切机
3).联合冲剪机4).带模剪联合冲剪机
由于这类设备带有通用性质,工艺范围广,辅助装置少,供提高剪切质量的调节机构少,剪切部位的压料装置简单等原因,致使加工精度较低,尺寸误差较大,断裂面粗糙度较高,所以大多应用于桥梁、锅炉、造船等金属结构件较多的精度要求不高的板材、型材加工车间和一些修理部门中。
国外,美国、苏联、英国很早就已经开始研制并应用到生产实际中且性能较好,我国早期生产的联合冲剪机多为仿制原苏联产品,采用机械传动,体积庞大,操作不便,且有较大振动
和噪声,刀具寿命低。
由于联合冲剪机的生产工艺简单,且产品利润高,所以有目前国内有很多联合冲剪机的生产厂家。
但是国内的联合冲剪机主要是仿国外制造。
这类产品的传动系统采用大部分采用液压传动;在控制方面,有些采用手动
控制,有些采用单片机控制,以适用于各种不同的场地,性能上比老式机械传动产品有较大提高。
至今已经生产出了许多种类型的联合冲剪机,性能上优于以前。
1.3本课题研究的意义、目的及内容
液压传动的基本原理是在密闭的容器内,利用有压力的油液作为工作介质来实现能量转换和传递动力的。
其中的液体称为工作介质,一般为矿物油,它的作用和机械传动中的皮带、链条和齿轮等传动元件相类似。
在液压传动中,液压缸就是一个最简单而又比较完整的液压传动系统,分析它的
工作过程,可以清楚的了解液压传动的基本原理.
液压传动系统的组成[2]:
液压系统主要由:
动力元件(油泵)、执行元件(油缸或液压马达)、控制元件(各种阀)、辅助元件和工作介质等五部分组成。
1)动力元件(油泵)它的作用是把液体利用原动机的机械能转换成液压能;是液压传动中的动力部分。
2)执行元件(油缸、液压马达)它是将液体的液压能转换成机械能。
其中,油缸做直线运动,马达做旋转运动。
3)控制元件包括压力阀、流量阀和方向阀等。
它们的作用是根据需要无级调节液动机的速度,并对液压系统中工作液体的压力、流量和流向进行调节控制。
4)辅助元件除上述三部分以外的其它元件,包括压力表、滤油器、蓄能装置、冷却器、管件及油箱等,它们同样十分重要。
5)工作介质工作介质是指各类液压传动中的液压油或乳化液,它经过油泵
和液压机实现能量转换
1.4所属领域的发展状况
液压传动相对于机械传动来说,是一门发展较晚的技术。
自18世纪末英国制成世界上第一台水压机算起,液压传动技术只有二三百年的历史。
直到20世纪30年代它才较普遍地用于起重机、机床及工程机械。
在第二次世界大战期间,由于战争需要,出现了由响应迅速、精度高的液压控制机构所装备的各种军事武器。
第二次世界大战结束后,战后液压技术迅速转向民用工业,液压技术不断应用于各种自动机及自动生产线,从而使它在机械制
造、工程机械、农业机械、汽车制造等行业得到推广应用。
20世纪60年代以来,液压技术随着原子能、空间技术、计算机技术的发展而迅速发展,并渗透到各个工业领域中。
液压技术开始向高速、高压、大功率、高效率、低噪声、经久耐用、高度集成化的方向发展。
同时,新型液压元件和液压系统的计算机辅助设计(CAD)、计算机辅助测试(CAT)、计算机直接控制(CDC)、机电一体化技术、可靠
性技术等方面也是当前液压传动及控制技术发展和研究的方向[3]。
我国的液压工业开始于20世纪50年代,最初只应用于机床和锻压设备上,后来又用于拖拉机和工程机械。
现在,我国的液压元件随着从国外引进一些液压元件、生产技术以及进行自行设计,现已形成了系列,并在各种机械设备上得到了广泛的使用。
尽管如此,我国的液压元件与国外先进的同类产品相比,在性能
上,在种类上、在规格上仍存在着较大的差距。
我国已瞄准世界发展主流的液压元件系列型谱,有计划地引进、消化、吸收国外最先进的液压技术和产品,大力开展产品国产化工作。
我国的液压技术在21世纪必将获得更快的发展。
2设计过程
2.1确定对液压系统的工作要求
根据设计要求,此次设计可以分为送料机构、夹紧机构、折弯机构、冲剪机构这四大机构来对这个系统进行分析。
同时,也要对各机构的里的各个动作顺序进行分析,设计他们应当如何控制来达到目的。
此系统包含的动作可分为送料一工件夹紧一快速下降一慢速下压一定形一快速上升一快速冲剪一退升一恢复这几个动作,下面是对他们进行一一的分析:
送料机构的动作分析:
送料机构的动作有送料,送料机构恢复。
为了达到这个目的,首先,要接一个溢流阀,其作用是防止系统压力过载和保持系统压力恒力。
要接一个三位四通换向阀,其作用是用来实现液压油路的换向、顺序动作、及卸荷等。
在送料和送料机构恢复的过程中各接一个单向节流阀,其作用是正向
流动时起节流阀作用;反向流动时起单向阀作用,这时由于有部分油液可在环形缝隙中流动可以清除节流口上的沉淀物。
工件循环拟定采用液压传动方式来实现,故决定选取油缸做执行机构。
夹紧机构的动作分析:
夹紧的机构的动作夹紧和松夹,首先,要接一个溢流阀,其作用是防止系统压力过载和保持系统压力恒力。
要接一个三位四通换向阀,其作用是用来实现液压油路的换向、顺序动作、及卸荷等。
在夹紧的过程中要接一个在考虑到进给系统传动功率不大,且要求低速稳定性好,以及滑台的速度调节,故拟定选用调速阀,单向阀组成的节流阀调速方式。
2.2拟定液压系统工作原理图
2.2.1板料折弯冲剪机液压系统原理图
图2-1为板料折弯冲剪机液压系统原理图,整个液压系统图由拟定好的控制回路及液压源组合而成。
各回路组合时要去掉重复多余的元件,力求系统结构简单。
注意各元件间的连锁关系,避免错误动作发生。
要尽量减少能量损失环节。
提高系统的工作效率。
同时,为了便于液压系统的维护和监测,在系统中的主要回路上装设有必要的检测的元件〈如压力表、温度计等〉。
图2-1系统原理图
图2-2为动作顺序执行表,整个液压各执行机构的顺序动作,根据设备类型不同,有的按固定程序运行,有的则是随机的或人为的。
工程机械的操纵机构多为手动,一般用手动的多路换向阀控制。
加工机械的各执行机构的顺序动作多采用行程控制,当工作部件移动到一定的位置时,通过行程开关发出的电信号给电磁铁推动电磁阀或直接压下行程阀来控制连续的动作。
行程开关安装比较方便,而用行程阀需连接相应的油路,因此只适用于管路联接比较方便的场合。
另外还有时间控制、压力控制等。
例如液压泵无载启动,经过一段时间,当泵正常运转后,延时继电器发出电信号卸荷阀关闭,建立起正常的工作压力。
压力控制多用在带有液压夹具的机床,挤压机、压力机等。
当某一执行元件完成预定动作时,回路中的压力达到一定的数值,通过压力继电器发出电信号或打开顺序阀使压力油通过,来启动下一个动作。
C'T
5DT
ST
ViT
CT
tr
IT
U
a
U
41
11
IJ
11
■
1風
—11
+
—
—
+
—
—
+
—
■
3晌
+
—
—
+
+
—
+
—
-
—
—
+
—
-
—
+
1
J.
■
1
1
+
—
—
—
—
-
—
—
—
--
+
—
-
—
—
—
4
卜
+
+
十
—
—
+
—
卜
—
—
-
—
—
十
—
+
8勵t
—
4
+
—
+
+
—
—
十
—
-
7耳入专Fl
十
十
-L
|
+
ll'Jaa
1
T
图2-2动作执行表
2.2.2板料折弯冲剪机各机构动作执行及回油路分析
1推送板料
三位四通电磁换向阀1DT得电,由泵2输出的压力油经过电磁换向阀4、单向节流阀5流入推料缸7上腔,液压缸移至1J。
元件4电磁换向阀1DT得电,由泵2输出的压力油经过电磁换向阀4、单向节流阀5流入推料缸7上腔,再经过单向节流阀6流回油箱,液压缸移动至1J。
2夹紧并推料机构返回
三位四通电磁换向阀2DT3DT得电,三位四通电磁换向阀8接通,由泵2输出的压力油经过溢流阀、电磁换向阀&减压阀9流入夹紧缸上腔。
同时推料缸液压缸右腔回油一单向节流阀一电磁换向阀4左端一油箱,液压缸移动至2J、
3J。
3快速下降
三位四通电磁换向阀5DT得电得电,三位四通电磁换向阀12左端接通;主油路进油路:
过滤器1—泵一三位四通电磁换向阀12左端一调速阀13—单向调
速阀。
液压缸移动至5J
4慢速下压
三位四通电磁换向阀12得电,三位四通电磁换向阀12左端接通;主油路进油路:
过滤器1—泵一三位四通电磁换向阀12左端一调速阀13—单向调速阀16,然后经过压力继电器一折弯机构压力缸上腔,液压缸移动至6J。
5定形
三位四通电磁换向阀12得电,三位四通电磁换向阀12右端接通,油路经拉折缸下腔一单向调速阀15-电磁换向阀12-油箱。
6快速上升
三位四通电磁换向阀12得电,三位四通电磁换向阀12右端接通,油路z经拉折缸下腔-单向调速阀15-电磁换向阀12-油箱,液压缸移动至7J。
7夹紧
三位四通电磁换向阀2DT得电,三位四通电磁换向阀8接通,由泵2输出的压力油经过溢流阀、电磁换向阀8、减压阀9流入夹紧缸上腔。
8快速冲剪
三位四通电磁换向阀25电磁换向阀9DT得电,由泵2输出的压力油经过二位二通换向阀21,经电磁换向阀过单向阀22,达到冲剪机构液压缸的上腔,液压缸移动至8J。
9剪头退升
三位四通电磁换向阀25电磁换向阀10DT得电,冲剪缸下腔-单向节流阀26—电磁换向阀25—单向阀22—二位二通电磁换向阀21,回油箱液压缸移动至2J。
10松夹
三位四通电磁换向阀8得电,电磁阀右端4DT通电,滑台松开工件。
3进行工况分析
3.1载荷的组成
1.最大折弯力Fi=1.7X104(N)
2•冲剪时薄板顶压力F2=5.8X104(N)
3
3.最大冲剪力Fa=2.7X10(N)
4.推料时的推力F50.8103(N)
3.2惯性阻力的计算
负载分析中,暂不考虑回油腔的背压力,液压缸的密封装置产生的摩擦阻力在机构效率中加以考虑。
因工作部件是卧式放置,重力的水平分力为零,这样需要考虑的力有:
导轨的摩擦力和惯性力。
可查[4]P230的计算公式见<3—1>、<3
—2>、<3—3>及<3—4>。
Fm1
m
f8
000.11
88N
<3-
-1>
3
Fm2
M
V5
2.410
4
60
1.2
103N
<3-
2>
g
t
10
0.1
104
93
Fm3
M
V4
V52.4
60
2.4
103N<3
—3:
g
t1
0
0.1
12
Fm4
M
Vl
2.4104
60
4.8
3
10N
<3
—4
g
t
10
0.1
3.3各机构的负载计算
331推料机构的负载计算
1•推送板料hi888N
2•退回F120N
3.3.2顶压板料机构的负载计算
1•工进顶压F210N
2•顶压板料F225.8104N
3•退回F230N
3.3.3折弯机构的负载计算
1•加速下降f31
M
FM2
2?
4104
4
0.1210
2.28
104N
2•快速下降F32
M
2.4
104
N
3.由快速变慢速下降
1
Z33M
F
m32.410
44
0.2410
2.64104N
4.慢速下降F34
M
2.4
104
N
5.定形F35M
F1
2.4
104
1.7
104
0.7
104N
6.反向加速上升F36
M
Fm4
2.4
104
0.48
104
4
2.8810N
7.制动F37M
Fm42
:
..4
104
0.48
104
1.92104N
3.3.4冲剪机构负载计算
1•快速工进F410N
2•剪切板料F422.7103N
3.
退升
F430N
3.4速度
V1
4m/min
V28m/min
V35.5m/min
V4
9m/min
V53m/minV6
6m/min
V7
12m/min
V810m/minV9
13.5m/min
3.5绘制负载与速度图
综上,根据负载计算结果和已知的各阶段的速度,可绘出负载图,见图3-1、图3-2、图3-3、图3-4和速度图,见图3-5、图3-6、图3-7、图3-8。
横坐标以上为液压缸活塞前进时的曲线,以下为液压缸活塞退回时的曲线。
3.5.1负载(F)与时间(T)的关系图
如下图所示;图3-1表示的是送料机构负载(F)与时间(T)的关系图,图3-2表示的是夹紧机构负载(F)与时间(T)的关系图,图3-3表示的是折弯机构负载(F)与时间(T)的关系图,图3-4表示的是冲剪机构负载(F)与时间
(T)的关系图。
F(103M)I
20
0,00
a科
11
B■V11j
tlts±4
tetstiotn
L
T
raa3N)
图3-2夹紧机构负载(F)与时间(T)的关系图
图3-3折弯机构负载(F)与时间(T)的关系图
rClO^N)A
30
5.7
己7
JfaJ|
i1
j]
liE
t]t3til
tet?
±st?
i
;IDt]l
L
T
3.5.2速度(V)与时间(T)的关系图
如下图所示;图3-5表示的是送料机构速度(V)与时间(T)的关系图,图
3-6表示的是夹紧机构速度(V)与时间(T)的关系图,图3-7表示的是折弯机构速度(V)与时间(T)的关系图,图3-8表示的是冲剪机构速度(V)与时间
(T)的关系图。
7
4
i斗
1I1111i1
一
■i
r
;i+f七3t*±3"ti±7'
於t
ior
-T
-
5.5
图3-5送料机构速度(V)与时间(T)的关系图
V(n/nlri>
图3-7折弯机构速度(V)与时间(T)的关系图
14
g
r
c
-ir~-^L
-10
七[七E~t3T-1~t5~t&~t7~t毎T5
IV彳Ll
10
图3-8冲剪机构速度(V)与时间(T)的关系图
图3-1
图3-5的说明:
0tio推送板料
tiotii退回
图3-2
图3-6的说明:
0ti顶压机构工进
tit2顶压机构顶压板料
t2
t3顶压机构退回
t6
t7顶压机构工进
t7
t9顶压板料
t9
tio退回
图3-3
图3-7
的说明:
ti
t2弯析机构快速下降
t2
t4弯折机构慢速下降及弯折
t4
t5定形
t5
t6弯折机构退回
图3-4
图3-8
的说明:
t7
t8冲剪机构冲剪材料
t8
t9退回
3.6绘制液压系统的工况图
工况图包括压力循环图、流量循环图和功率循环图。
它们是调整系统参数、
选择液压泵、阀等元件的依据。
见图3-9表示的是折弯机构工况图(F)与时间
(T)的工况图,图3-10表示的是冲剪机构工况图(F)与时间(T)的工况图。
图3-9折弯机构工况图(F)与时间(T)的工况图
FC103N)p
图3-10冲剪机构工况图(F)与时间(T)的工况图
4确定系统的主要参数
4.1确定工作压力和背压力
压力的选择要根据载荷大小和设备类型而定。
还要考虑执行元件的装配空间、经济条件及元件供应情况等的限制。
在载荷一定的情况下,工作压力低,势必要加大执行元件的结构尺寸,对某些设备来说,尺寸要受到限制,从材料消耗角度看也不经济;反之,压力选得太高,对泵、缸、阀等元件的材质、密封、制造精度也要求很高,必然要提高设备成本。
一般来说,对于固定的尺寸不太受限的设备,压力可以选低一些,行走机械重载设备压力要选高一些。
具体选择可查
[5]P420表4.1-1和表4.1-2。
表4.1-1按载荷选择工作压力
载荷/KN
<5
5-10
10-20
20-30
30-50
50
工作压力
/MPa
<0.8-1
1.5-2
2.5-3
3-4
4-5
5
表4.1-2执行元件背压力
系统类型
背压力/MPa
简单系统或轻载节流调速系统
0.2-0.5
回油路带调速阀系统
0.4-0.6
回油路设置有背压阀系统
0.5-1.5
用补油泵的闭式回路
0.8-1.5
回油路较复杂的工程机械
1.2-3
回油路较短,且直接回油箱
可忽略不计
4.2推料机构液压缸的参数计算
4.2.1推料机构液压缸的内径D1的计算
因为m=800N<5000h查表4.1-1初选工作压力为R0.3MPa,可查
⑹P23191的内径计算公式见<4—1>:
D13.57102Fl<4—1>
Pi
则代入数值得
2Jo82
D13.57105.8102m58mm
0.3
可查⑹P23173液压缸内径尺寸系列表,取标准系列值D163mm
4.2.2推料缸活塞杆直径d1的计算
查⑹P23191,活塞杆直径的计算,根据速度比的要求来计算活塞杆直径d.
公式见<4—2>:
d1j——<